
книги из ГПНТБ / Электрометаллургия стали и ферросплавов учебное пособие
..pdfДля более глубокого раскисления сталь во время обработки шла ком дополнительно раскисляют кремнием, а после обработки алюми нием, присаживаемыми в металл в небольших количествах. Вслед ствие высокого содержания А120 3 в шлаке и низкого содержания FeO алюминий мало окисляется, а иногда даже немного восстанавли вается. Поэтому усвоение присаживаемого в металл алюминия до стигает 100% и более.
Обработка стали в ковше восстановительным известково-глино земистым шлаком, обеспечивающая раскисление и десульфурацию стали, позволяет существенно сократить восстановительный период плавки или по существу отказаться от него.
ОКНСНЫЕ НЕМЕТАЛЛИЧЕСКИЕ ВКЛЮЧЕНИЯ В СТАЛИ
Частицы окислов в большей или меньшей мере остаются в ме талле и, как и сульфиды и нитриды, образуют в стали отдельную фазу неметаллических включений. По происхождению окисные включения можно разделить на экзогенные и эндогенные.
Экзогенные включения вносятся в сталь извне в результате меха нического воздействия металла на футеровку. Так как такие вклю чения обычно бывают крупными, они быстро всплывают в металле и .среди остающихся в стали включений их доля не велика (до
5— 15%).
Основную часть окисных включений в стали составляют эндо генные включения, образующиеся в самом металле в результате из менения термодинамических условий и развития ряда физико-хими ческих процессов, а именно:
1)окисления примесей в окислительный период плавки;
2)раскисления;
3)изменения условий (констант) равновесия с понижением тем пературы;
4)уменьшения растворимости при охлаждении;
5)повышения концентрации в растворе в результате ликвации. Окисные включения, образовавшиеся в результате окисления
примесей, как и попавшие в металл из шихты и футеровки, в окисли тельный период в значительной мере удаляются в шлак и лишь не большая часть их остается в металле. В конце окислительного пери ода содержание окисных включений (А120 3 и S i0 2) обычно не пре вышает 0,002—0,004%.
Основная часть окисных включений в стали образуется в резуль тате раскисления. Следует отметить, что и другие причины образо вания окисных включений в спокойной стали (изменение условий равновесия — уменьшение констант равновесия, растворимости, лик вации) также вызывают взаимодействие кислорода с раскислителями, т. е. образование продуктов раскисления. Следовательно, рас кисление стали происходит не только во время присадки раскислителей, но и после этого вплоть до кристаллизации и на всех стадиях от присадки раскислителей до кристаллизации образуются окисные включения продуктов раскисления.
201
Первичные продукты раскисления образуются вовремя присадки раскпслптелей сообразно с подробно рассмотренными условиями.
Вторичные продукты раскисления образуются во время охлажде ния стали при выпуске, выдержке в ковше и разливке вследствие условий равновесия — изменения констант равновесия и уменьше ния произведения равновесных концентраций раскислителя и кисло рода. Важную роль в образовании окисных включений в этот период играет вторичное окисление стали при контактировании струи с воздухом во время выпуска и разливки.
Третичные продукты раскисления образуются во время кристал лизации, т. е. охлаждения металла в двухфазном состоянии, соответ ствующем области, расположенной на диаграмме состояния между линиями ликвидуса и солпдуса. Причинами их образования яв ляются понижение температуры и соответственно изменение условий (констант) равновесия и, главное, развитие ликвациопиых процес сов, преимущественно кислорода.
Удаление третичных продуктов раскисления вследствие запуты вания их в растущих кристаллах затруднено, а при образовании в междендритных пространствах почти невозможно. Более благо приятны условия удаления первичных и вторичных продуктов рас кисления, образующихся в гомогенной жидкой среде. Но и они частично остаются в металле.
Обычно содержание окисных неметаллических включений в спо
койной стали составляет 0,01—0,03%. В их состав входит 60—90% |
|
А1,03; 2—30% S i0 2; 1— |
10% FeO; 1— 10% МпО. Кроме этих окис |
лов, встречаются Сг20 3, |
MgO и др. |
Обычно окисные включения находятся в твердой стали в виде соединений разных окислов: силикатов, шпинелей и др. В виде чистого окисла часто встречается лишь корунд.
Корунд является «-модификацией глинозема А120 3. На металло графических шлифах при рассмотрении под микроскопом в отражен ном свете кристаллы корунда имеют обычно вид зерен неопределен ной формы или шестиугольников, чаще неправильной формы
(рис. 89, а).
Включения корунда обычно располагаются в виде отдельных дезориентированных гроздьев мелких, не сомкнутых между собой кристаллов. В катаной или кованой стали эти гроздья вытягиваются в направлении деформации металла, образуя строчки (рис. 89, б).
Всвязи с очень высокими твердостью (9 единиц по десятичной шкале)
итемпературой плавления включения корунда при обработке дав лением не деформируются.
Кроме корунда, в стали, раскисленной алюминием, имеются включения шпинели -на основе А120 3. Наиболее часто встречаются включения железной шпинели — герцинита (Fe0-Al20 3) и марган цевой шпинели-галаксита (Мп0-А120 3), образующие непрерывный ряд твердых растворов, а также другие включения систем FeO—
А120 3 и МпО—А120 3. На металлографических шлифах эти вклю чения имеют вид прямоугольных кристаллов правильной кубической формы (рис. 90, а) или треугольников.
202
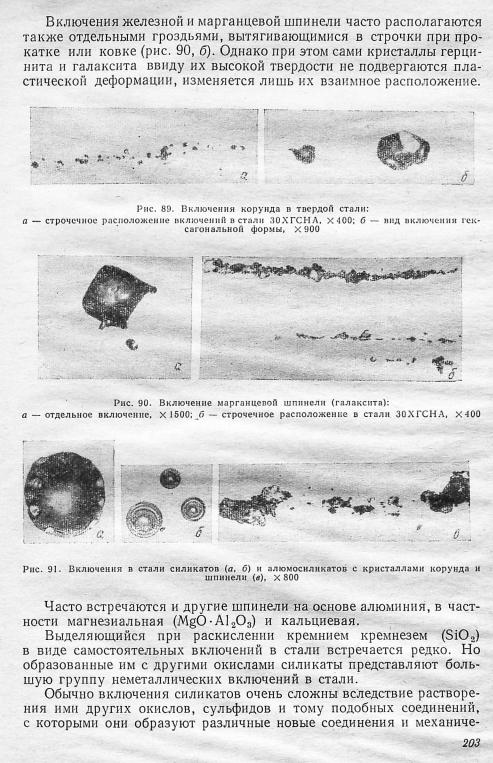
ские смеси. |
Часто |
они имеют в стали вид сложных конгломератов, |
в которых |
можно |
различить ряд минералов. |
Наиболее часто в стали встречаются включения силикатов железа (2Fe0-Si03 — фаялит) и марганца (2MnO-Si02 — тефроит, MnO -Si02 ■— роданит). На металлографических шлифах они имеют вид глобулей с кристаллами других минералов на поверхности (рис. 91, а); иногда же они располагаются в виде сложных скопле нии (рис. 91, б). При температурах горячей обработки давлением они пластичны и во время прокатки или ковки вытягиваются. Часто встречаются также включения алюмосиликатов, в частности мул лита (ЗА120 3-2S10.,) и силиманита (Al„03-Si02) ромбической и оваль ной формы. Располагаются они преимущественно группами (рис. 91, в). Эти включения непластичны и они не деформируются.
В легированных сталях соответственно наличию тех или иных элементов в состав неметаллических включений могут входить окислы хрома, титана, ванадия и др.
Окпсиые включения оказывают отрицательное влияние на неко торые свойства стали. При обработке давлением скопления окисных включений, а часто и сами включения вытягиваются в направлении течения металла и поэтому оказывают существенное влияние на свойства в поперечном направлении течению металла при ковке пли прокатке. Влияние это является следствием нарушения однород ного напряженного состояния металла и концентрации напряжений возле включений, играющих роль надрезов, особенно при угловатой форме или острых краях. Так как концентрация напряжений вызы вает возникновение объемного напряженного состояния, включения ухудшают свойства металла, характеризующие его пластичность (относительное удлинение и относительное сужение) и ударную вяз кость. Наиболее сильно влияние включений обычно проявляется на ударной вязкости, особо чувствительной к надрезам металла и кон центраторам напряжений. Понижение ударной вязкости, например при наличии строчечных включений в плоскости излома, может до стигать 30—70%.
Строчечные включения могут вызывать расслаивание металла под действием внешних нагрузок. Это вызывает быстрый износ п забраковывание стальных изделий.
Глобулярные окисные включения, расположенные на контактной поверхности, понижают износостойкость и усталостную прочность стали. В условиях быстро меняющихся нагрузок включения выкра шиваются, вызывая откалывание и усиленный износ подшипников, а также их разрушение вследствие резкого падения усталостной проч ности при наличии дефектов поверхности, возле которых концентри руются напряжения и начинается усталостное разрушение.
Окисные включения вызывают возникновение в стали ряда спе
цифических дефектов — пористость, точечную неоднородность, воло совины и др.
Глава |
13 |
ГАЗЫ В |
СТАЛИ |
ВОДОРОД |
В СТАЛИ |
Р а с т в о р и м о с т ь в о д о р о д а в ж е л е з е и в л и я н и е е г о н а с в о й с т в а с т а л и . Водород растворяется в же лезе и его сплавах в атомарном (ионном) состоянии. Атомы (ионы) водорода благодаря своим малым размерам распределяются в про межутках между атомами железа, образуя растворы внедрения.
4 |
зо |
|
|
|
4 |
20 |
|
|
|
Is |
|
|
|
|
К'" |
|
|
|
|
I'5 |
0 |
|
|
|
5 |
700 900 |
ноо |
1500 /500 1700 |
|
|
500 |
|||
|
|
Температура, °С |
||
Рис. 92. Растворимость водорода в железе при |
||||
парциальном |
давлении |
водорода |
10,233 кН/м2 |
|
-• |
|
(760 мм |
рт. ст.) |
|
Растворимость водорода в железе может быть описана уравне ниями
2 [Н] = ТЬ (г); |
|
Кн = Ры./ Ш ]2, |
(74) |
отсюда
[Н] — /Сн У Рн, >
где К и = 1/|'/ Ан-
Следовательно, растворимость пропорциональна корню квадрат ному из величины его давления. Эта закономерность была установ лена Сивертсом и затем подтверждена экспериментально М. М. Кар науховыми А. Н. Морозовым, В. И. Явойским и другими исследова телями. Было вместе с тем найдено, что растворимость водорода зависит от температуры и скачкообразно изменяется при аллотропи ческих превращениях (изменяется величина Кн).
Результаты исследований, приведенные в виде изобары на рис. 92, показывают *, что при повышении температуры растворимость во дорода в общем повышается. При превращении a -железа в у-железо,
атакже в точке плавления растворимость водорода скачкообразно
*Концентрацию водорода в железе обычно выражают в см3 на 100 г металла, которая равна [% Н] 22400/2.
205
увеличивается. При переходе железа из модификации у в модифи
кацию б она несколько понижается.
Другие элементы влияют на растворимость водорода в жидком железе. Это влияние характеризуется параметрами взаимодействия,
которые, по данным разных |
авторов, при 1600° С равны: |
=3,7; |
ен = 0,027; б» = 0,06; eft = — 0,081 |
|
|
Следовательно, кислород, |
кремний и углерод понижают раствори |
мость водорода в жидком железе, причем особенно сильно в этом направлении действует кислород. Титан, напротив, повышает рас творимость водорода в жидком железе. Влияние других элементов (Ni, Al, Сг и др.) незначительно.
Особое значение |
имеет резкое понижение растворимости водорода |
|
при |
затвердевании |
и дальнейшем понижении температуры. Из |
рис. |
92 видно, что |
при температуре 1600° С и р ц„ = 10,223 кН/м2 |
(760 мм рт. ст.) растворимость водорода в жидком железе равна примерно 28 см3 на 100 г, а в твердом железе при комнатной темпера туре она равна практически нулю. Вследствие этого во время кри сталлизации водород в значительной мере переходит в маточный раствор, что вызывает его сильную зональную ликвацию в слитке, а после затвердевания полностью выделяется из раствора в металле.
Выделение водорода происходит в пустоты металла и дефектные места решетки. Здесь атомы водорода соединяются в молекулы и он переходит в газообразное состояние.
Если объем пустот достаточно велик, как это бывает в литом ме талле, давление водорода в них не велико и он не влияет на свойства стали. Если же объем пустот небольшой (например в катаном и ко ваном металле), водород переходит лишь в микропустоты и дефект ные места решетки, где возникает высокое давление (до 1 кН/м2, или 100 кгс/мм2), отрицательно влияющее на свойства стали.
Ввиду узко локального характера высокое давление водорода, даже если оно превышает предел прочности стали, само по себе не может вызвать разрушение металла, так как упруго передается на слои, следующие за микропустотой. Однако в случае приложения внешнего усилия возле микрообъемов с высоким давлением водо рода возникает объемное напряженное состояние, вызывающее рез кое понижение пластичности стали — водородную хрупкость. Про является она в виде понижения относительных сужения и удлине ния, а иногда и ударной вязкости при содержании водорода более
2 см3 на 100 г и в |
тем большей степени, чем больше это содер |
жание. |
|
Под действием |
давления водорода металл может разрушиться |
в том случае, если |
это давление суммируется с внутренними напря |
жениями (структурными, термическими, от остаточных дефор маций). В этом случае в стали образуются внутренние разрывы— флокены.
Флокены представляют собой внутренние трещины, имеющие в продольном направлении излома (относительно течения металла при горячей обработке давлением) вид округлых хлопьев диаметром
206

щее влияние на содержание водорода в электростали оказывает не влажность воздуха, а влажность шлакообразующих материалов. При введении этих материалов в печь вода растворяется в шлаке и вызы вает повышение содержания в нем водорода.
В шлаке водород, по-видимому, находится в виде гидроксила (ОН- ). Соответственно этому растворение влаги в шлаке можно записать реакцией Н 20(Г) + (О2-) = 2 (ОН- ). Такой записи реак ции соответствует установленная В. И. Явойским и подтвержден ная затем другими исследователями квадратичная зависимость между концентрацией водорода в шлаке и парциальным давлением водяных паров в равновесной с ним газовой фазе:
(Н) = /С(Н) Г' Р н ..о ,
а также увеличение растворимости водорода в шлаке с увеличением активности ионов кислорода (яо-2)> происходящей с повышением содержания (СаО) и увеличением основности шлака.
В общем растворимость водорода в основных шлаках не велика и, по некоторым данным, в окислительный период она составляет 0,0007—0,0015%. В кислых шлаках она еще меньше. Но и такая растворимость водорода оказывается достаточно высокой для того, чтобы вызвать интенсивное поступление его в металл. Переход водо рода из шлака в металл может быть записан уравнением
2 (ОН") = 2 [Hi + (О] + (О2-),
К = 1Н|; |0 |< Г > . |
(75) |
(аон-) |
|
Согласно уравнению (75), в условиях равновесия содержание водорода в металле понижается с увеличением активности ионов кислорода в шлаке, т. е. повышением его основности. Равновесное распределение водорода между шлаком и металлом не достигается, но отмеченное влияние основности шлака в некоторой мере прояв ляется. Существенное значение при этом имеет увеличение вязкости шлака, вызывающее уменьшение интенсивности массопереноса водо рода из шлака в металл.
Однако решающее значение в уменьшении интенсивности поступ ления водорода в металл при плавке стали в дуговых электропечах имеет уменьшение влажности шлакообразующих материалов (при менение свежеобожженной извести, отказ от применения боксита в восстановительный период, прокаливание материалов, присажи ваемых после прекращения кипения ванны).
Удаление водорода из металла происходит в окислительный пе риод плавки в результате экстрагирования его пузырьками окиси углерода. Это экстрагирование является следствием стремления водо рода к равновесному распределению его между металлом и пузырь ками окиси углерода, в которых при их образовании парциоиальное давление водорода равно нулю.
208
Увеличение интенсивности выделения пузырьков окиси угле рода по ходу окислительного периода вызывает увеличение интен сивности удаления водорода. Следовательно, повышению скорости удаления водорода способствует повышение скорости обезуглерожи вания металла. Это было показано теоретически и экспериментально Н. М. Чуйко.
При теоретическом рассмотрении он принял, что в процессе кипения металла объемы выделяющихся водорода Кн„ и окиси угле рода Vco пропорциональны их парциальным давлениям:
V |
_ Рн. _ |
[НР/Сс |
^ с о |
Р с о |
[С] [О] |
Исходя из^этого он показал, что скорость удаления водорода из металла ( У н ) в процессе кипения связана со скоростью окисления углерода (vc) соотношением
(76)
Вусловиях плавки равновесное распределение водорода между металлом и пузырьками окиси углерода, как это принял Н. М. Чуйко, видимо, не достигается, но, по крайней мере, качественно установ ленная им закономерность подтверждается.
Вусловиях электроплавки стали обычно подтверждается и общее уравнение скорости изменения содержания водорода в металле (уц)
сучетом и скорости его поступления ( у'н ):
Рн = Ун — Ун = K V[Н]2 — DH([Нр] — [Н]) |
(77) |
где Dн — коэффициент массопереноса водорода через |
шлак в ме- |
талл; |
|
[Нр] — равновесное содержание водорода в металле.
Это объясняется тем, что при электроплавке парциальное давление водяных паров в печной атмосфере бывает низким и водород обычно не поступает в металл из газовой фазы. Поэтому коэффициент D для данной печи является величиной постоянной. В случае поступления водорода в металл через шлак из печной атмосферы (например, при мартеновской плавке) увеличение величины Ус вызывает увеличение массопереноса водорода, т. е. увеличение величины Он, что очень трудно учесть.
Таким образом, основными методами понижения содержания водорода в металле в процессе плавки служит уменьшение влаж ности шлакообразующих материалов, особенно присаживаемых в восстановительный период, легирующих и увеличение интенсив ности окисления углерода.
Для более быстрого и полного удаления водорода из металла уве личивают количество подаваемых в ванну в единицу времени же лезной руды или газообразного кислорода. Второй метод более эф фективный, если кислород не содержит значительного количества влаги (более 0,1—0,5 г/м3).
14 Зак. 824 |
209 |
Так как по уравнениям (76) и (77) скорость удаления водорода из металла увеличивается не только с увеличением скорости обез углероживания, но и с повышением его исходного содержания, кон центрация водорода в стали в конце окислительного периода не за висит от той, которая была в начале периода. К концу окислитель ного периода даже при очень интенсивной продувке ванны кислоро дом не удается получить содержание водорода в металле менее 2,7— 3,0 см3 на 100 г, да и такое содержание получается редко.
При наведении после интенсивного окислительного периода вос становительного шлака содержание водорода в металле вновь воз растает даже в случае применения хорошо просушенных материалов и свежеобожженной извести. Поэтому па некоторых заводах для понижения содержания водорода в стали осуществляют короткую продувку металла кислородом сразу после наведения известкового шлака.
Обычно при ведении плавки с интенсивным окислительным периодом и применением хорошо просушенных материалов содержа ние водорода в среднелегированной стали во время выпуска из дуго вой печи составляет 4—9 см3 на 100 г. В высоколегированной аусте нитной стали оно может достигать 10— И см3 на 100 г.
АЗОТ В СТАЛИ
Р а с т в о р и м о с т ь а з о т а е г о н а с в о й с т в а с т а л и .
может быть описана |
уравнениями |
|||
2 [NJ = N-j (г); К |
N |
Р а . |
||
[N]2 ’ |
||||
|
|
|
||
•откуда |
|
|
|
|
[N] = |
К а У Pn2> |
|
|
|
где Kn = |
U V К n - |
|
|
в ж е л е з е и в л и я н и е Растворимость азота в железе
(78)
Рис. 04. Растворимость азота п железе при парциальном давлении азота
10,223 кПа/м2 (7G0 мм т. ст.)
Следовательно, и растворимость азота, в соответствии с правилом Сивертса, пропорциональна корню квадратному из величины его давления. Так как Ка меняется с температурой и различно для разных фазовых состояний, растворимость азота зависит от тем
270