
книги из ГПНТБ / Бушуев, В. М. Химическая индустрия в свете решений XXIV съезда КПСС
.pdfботку сжиженных газов с 880 тыс. т до 4,8 млн. т в год и увели чить поставки углеводородного сырья предприятиям химической и нефтехимической промышленности более чем в 8 раз.
Особо важное значение для развития производства многих видов пластических масс, химических волокон, синтетических каучуков, красителей и большого количества других продуктов тонкого органического синтеза имела организация производства бензола, толуола, ксилолов из нефтяного сырья. Рост производ ства некоторых ароматических продуктов за десятилетие харак теризуется следующими данными: бензола — более чем в 2 раза, толуола из нефтяного сырья — в 4,6 раза, ксилолов — в 5,5 раза, в том числе из нефтяного сырья — в 9,5 раза, анилина ■— в 1,9 раза, фенола — в 3,2 раза, в том числе из нефтяного сырья — в 6,3 раза, диметилтерефталата — в 21 раз, фталевого ангидрида— в 4 раза.
Для развития производства бензола решающее значение име ло освоение нефтеперерабатывающей промышленностью метода получения его в процессе каталитического риформинга прямо гонного бензина на ‘платиновом катализаторе при темпе ратуре примерно 500 °С и давлении 25 ат. До седьмой пятилетки основным поставщиком бензола являлась коксохимическая про мышленность. Небольшие количества его вырабатывались пиро лизом керосина, при котором выход составлял всего лишь 3%, а также при термической переработке сланцев. Таким образом, производство бензола лимитировалось масштабами выработки кокса. А это, в свою очередь, сдерживало развитие производства полимерных материалов и большого числа продуктов органиче ского синтеза. Освоение нового метода сняло ограничительные рамки с развития производства бензола и дало возможность по высить его качество и снизить удельные капитальные вложения. Наглядное представление об изменениях в сырьевой базе и ме тодах производства бензола дает рис. 10.
Одним из важнейших продуктов, получаемых из бензола, яв ляется анилин, который используется для производства широкой гаммы анилиновых красителей, фармацевтических препаратов и других продуктов органического синтеза. Рост производства анилина частично осуществлялся за счет интенсификации дей ствующих цехов, вырабатывающих его по старой схеме-— вос становлением нитробензола чугунной стружкой. Новые цехи со оружались по более экономичному методу — непрерывного кон тактно-каталитического восстановления нитробензола водородом. Единичные мощности контактных аппаратов в цехах, введенных в строй в восьмой пятилетке, составляют 5— 6 тыс. т в год.
72
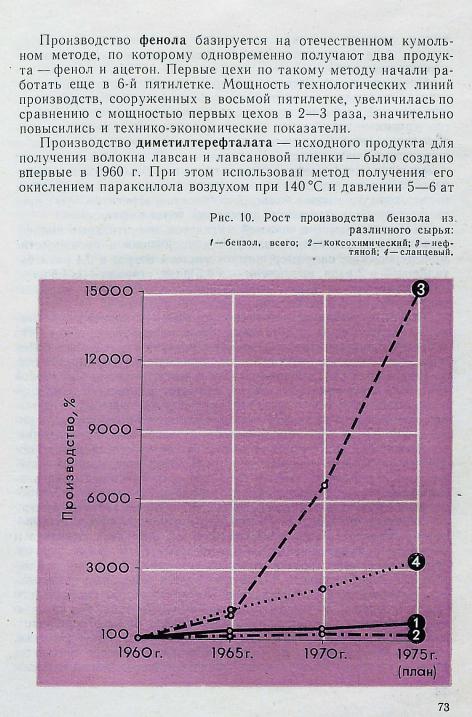
в периодически действующих реакторах. Новые производства основаны па более прогрессивном непрерывном методе окисле ния параксилола.
Производство фталевого ангидрида, необходимого для выпу ска пластификаторов, полиэфирных и глифталевых смол для ла кокрасочной промышленности, лекарственных препаратов и мно гих других продуктов, до второй половины 60-х годов основы валось на окислении паров нафталина кислородом воздуха в
присутствии ванадиевого катализатора. В |
восьмой пятилетке |
с целью экономии дефицитного нафталина |
было создано более |
передовое в техническом отношении производство этого продукта из ортоксилола с вдвое большей мощностью агрегатов, чем в про цессе получения фталевого ангидрида через нафталин.
За годы седьмой и восьмой пятилеток значительные количе ственные и качественные изменения произошли в производстве мономеров. Так, например, выпуск этилена возрос в 5,4 раза, бу тадиена — в 2 раза, пропилена — в 4,5 раза, стирола — в 4,6 раза, капролактама — в 9 раз, винилхлорида — в 6,8 раза, метилме такрилата— в 5,4 раза, винилацетата — в 9,3 раза.
Вопросы, связанные с техническим уровнем производства эти лена, винилхлорида и бутадиена, были рассмотрены выше. Что касается пропилена, то прежде всего следует отметить все более широкое его использование для производства полипропилена, фенола и ацетона, изопропилового спирта, нитрила акриловой кислоты, глицерина. Пропилен получается вместе с этиленом в процессе пиролиза углеводородного сырья, поэтому техниче ский уровень его производства определяется рассмотренным ра нее техническим уровнем процессов пиролиза и газоразделения.
До начала 60-х годов ацетилен в нашей промышленности по лучали карбидным способом, который отличается высокой материало- и энергоемкостью, требует больших удельных капиталь ных затрат и, как следствие, характеризуется высокой себестои мостью продукции. С конца седьмой пятилетки стало быстро развиваться производство ацетилена термоокислительным пиро лизом 'природного газа с использованием агрегатов пиролиза и концентрирования мощностью соответственно 8 и 18 тыс. т в год. Этот способ имеет ряд крупных достоинств. Он основан на ис пользовании доступного и дешевого сырья. Удельные капиталь ные затраты на 1 т ацетилена в два раза, а себестоимость его в полтора раза ниже, чем при карбидном способе. На каждую тонну ацетилена попутно получается такое количество синтезгаза, используемого в качестве сырья для производства аммиака, которое обеспечивает получение 4 т этого ценного продукта; именно . поэтому производства ацетилена термоокислительным
74
пиролизом созданы главным образом на азотно-туковых комби натах.
Быстрое развитие производства этилена и бензола из нефтя ного сырья позволило резко увеличить выпуск стирола — про дукта, широко используемого в производстве пластических масс, синтетических каучуков и латексов, красителей, фармацевтиче ских препаратов. Сырьем для стирола служит этилбензол, полу чаемый алкилированием бензола этиленом. До начала восьмой, пятилетки для алкилирования применяли этилен, содержащийся в коксовом газе. Для получения этилбензола и стирола строи лись специальные цехи на азотных заводах, которые вырабаты вали аммиак из водорода коксового газа. Мощности таких цехов лимитировались объемом производства аммиака и не превышали 10 тыс. т в год. В восьмой пятилетке цехи по производству этил бензола и стирола сооружались уже на нефтехимических пред приятиях. Мощность их по стиролу равна 40 тыс. т в год, производительность одной технологической нитки — 20 тыс. т в год.
Один из важнейших продуктов для производства синтетиче ских волокон — капролактам получается в промышленности по трем схемам: из фенола, из анилина и из бензола. Удельный вес этих способов в общем объеме производства капролактама ви ден из рис. 11.
Производство капролактама из фенола было создано еще в 1949 г. За счет расширения и реконструкции, а также совер шенствования технологического процесса мощность производства за 20 лет возросла почти в 14 раз. Изменилась и его экономика: себестоимость капролактама снизилась примерно на 30%. До оборудование производства установкой дистилляции позволило получать продукт значительно лучшего качества.
Процесс производства капролактама из анилина имеет мень ше технологических стадий й позволяет получать более дешевый продукт. Однако главным направлением в развитии производства
капролактама в нашей промышленности |
стало получение его |
из бензола. Ключевой процесс этого метода — окисление цикло |
|
гексана воздухом. Технологические линии |
первых цехов имели |
мощность 5—5,5 тыс. т, |
сейчас мощность линий достигает |
25 тыс. т. Себестоимость |
1 т продукта на новых производствах |
примерно на 200—250 руб. ниже, чем при получении капролак тама из фенола и анилина.
Резко возросло производство винилацетата, используемого для получения поливинилового спирта, ацеталей на его основе, поливинилацетатной эмульсии и др. Он производится нашей про мышленностью из ацетилена и уксусной кислоты в агрегатах со
75
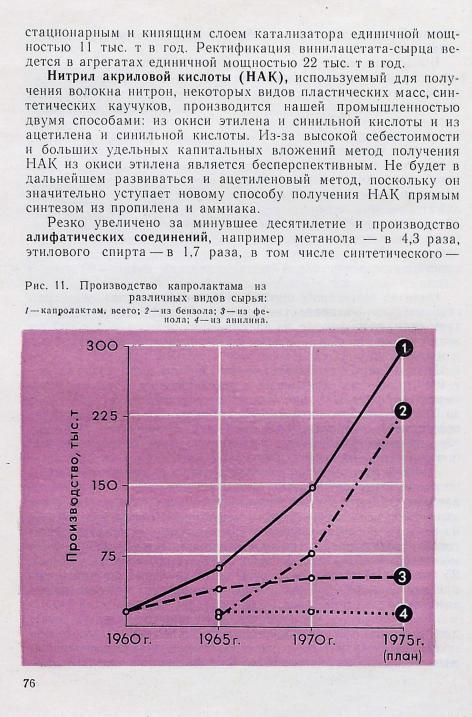
в 2,1 раза, бутилового спирта — в 2,9 раза, высших спиртов С7—Сд — почти в 15 раз, высших спиртов Сю—Сю — в 6,2 раза, ацетальдегида— в 4,4 раза, уксусного ангидрида и уксусной кис лоты— в 3,3 раза, формальдегида — в 4,4 раза, адипиновой и себациновой кислот — в 6,3 раза.
В производстве метанола наиболее существенным изменением за последнее время является перевод его на новое сырье — при родный газ вместо продуктов переработки угля. Это позволило снизить удельные капитальные вложения на 30^40%, а себе стоимость на 25—45%• В 1970 г. уже свыше 97% метанола выра батывалось из продуктов конверсии природного газа. Намного улучшились технические характеристики применяемого обору дования. В конце 60-х годов эксплуатировались агрегаты синтеза метанола мощностью 12—15 тыс. т в год, а в 70-х годах соору жались технологические линии мощностью уже 55 тыс. т. Строя щиеся цехи оснащались более мощными компрессорами, совер шенной технологической аппаратурой для очистки газа и т. д. Получили применение новые катализаторы, что позволило зна чительно снизить давление и температуру синтеза.
Этиловый спирт вырабатывается тремя способами: из пище вого сырья, гидролизным методом при химической переработке древесины и синтезом непосредственно из этилена (синтетиче ский этиловый спирт).
Этиловый спирт из сельскохозяйственных продуктов (карто феля, зерна и т. д.) производят предприятия Министерства пищевой промышленности СССР и предназначается он исключи тельно для пищевых и медицинских целей.
Гидролизный метод в настоящее время самостоятельного зна чения не имеет, его применяют главным образом для утилиза ции отходов производства целлюлозы.
Синтетический спирт получают двумя методами: сернокислот ным (через этилсериую кислоту) и прямой гидратацией этилена. Преимущество этих методов состоит в использовании дешевого сырья, имеющегося в больших количествах, — углеводородных газов нефтепереработки, которые раньше сжигались. Капиталь ные затраты на создание мощности по производству 1 т этило вого спирта при получении его из отходящих газов нефтепере рабатывающих заводов составляют менее 400 руб., а при выра ботке из пищевого сырья с учетом затрат в сельском хозяйстве— свыше 900 руб. Себестоимость 1 т синтетического спирта при мерно в 2 раза ниже себестоимости спирта, вырабатываемого из зерна или картофеля.
Сернокислотный метод требует большого расхода серной кис лоты и кислотостойкой аппаратуры, вследствие чего он не полу
77
чил значительного развития — основным является метод прямой гидратации. За истекшее десятилетие технологические линии, работающие по этому способу, значительно интенсифицированы, их мощность увеличилась с 1 до 2 млн. дкл в год.
Уксусная кислота и уксусный ангидрид используются для получения ацетатов целлюлозы, красителей, лаков, кинопленки, лекарственных препаратов и ряда других веществ. Кислота про изводится двумя методами: каталитическим окислением ацеталь дегида кислородом и окислением бутана или бензина. Уксусный ангидрид получают методом дегидратации в присутствии ката лизаторов. В конце восьмой пятилетки был освоен более эконо мичный метод одновременного получения уксусной кислоты и ангидрида. Производство, основанное на этом методе, исполь зует высокопроизводительное оборудование и полностью авто матизировано.
Формальдегид, применяемый в больших масштабах при изго товлении пластических масс, для синтеза изопрена, красителей, взрывчатых веществ, лекарственных препаратов и других ве ществ получают каталитическим окислением метанола с при менением серебряного катализатора. Единичная мощность кон тактных аппаратов составляет 25—30 тыс. т в год.
Нормальный бутиловый спирт служит исходным сырьем для производства ряда важнейших продуктов: растворителей, пла стификаторов, а изобутнловый спирт применяется в качестве рас творителя лаков, а также как сырье для получения некоторых флотореагентов, ускорителей процесса вулканизации в резино вой промышленности и т. д.
До 1961 г. для синтеза этих спиртов использовался процесс брожения крахмала зерна и картофеля. Кроме того, бутиловый спирт получался в качестве отхода при производстве бутадиена из этилового спирта. В указанном году было организовано про изводство синтетического бутилового спирта из этилового. Однако это — четырехстадийный процесс, осуществляемый в агрегатах малой мощности (2 тыс. т в год) и требующий аппаратуры из высоколегированных материалов.
В восьмой пятилетке начато производство бутилового спирта, основанное на оксосинтезе, в котором используется такое доступ ное сырье, как пропилен, окись углерода и водород. Процесс имеет только две основные стадии; единичная мощность агрега тов доведена до 40 тыс. т в год.'
Спирты С7—Сд, применяемые для получения пластификато ров, до 1960 г..производились в небольших количествах в перио дическом процессе гидрирования кислот С7—Сд или их бутило
78
вых эфиров на стационарном медно-хромокальциевом катали заторе. В 1968 г. вступило в строй предприятие мощностью 2 2 тыс. т в год, работающее по непрерывной технологии с при менением нового более эффективного катализатора.
Спирты Сю—Сю, применяемые в производстве синтетических моющих средств и присадок к маслам, до 1960 г. вырабатыва лись омылением кашалотовых жиров, при этом выход спиртов составлял 35%. В последующие годы была внедрена новая тех нология гидрирования кашалотового жира на стационарном катализаторе с мощностью линии 15 тыс. т; выход спиртов увели чился до 75%. Организовано производство этих спиртов мето дом гидрирования метиловых эфиров синтетических жирных кис лот на суспендированном катализаторе, а также выделением спиртов из вторых неомыляемых фракций, образующихся при синтезе жирных кислот.
Однако наиболее перспективным процессом получения выс ших жирных спиртов в настоящее время является прямое окис ление жидких парафинов по методу, созданному советскими уче ными. Этот метод осуществлен в промышленном масштабе и выгодно отличается от других методов более простой техноло гией и меньшими капитальными вложениями.
Промышленное производство малеинового ангидрида, исполь зуемого для выпуска алкндных и полиэфирных смол, фармацев тических препаратов, пластификаторов, высыхающих масел и т. д., было создано в конце седьмой пятилетки по схеме каталитиче ского окисления бензола кислородом воздуха.
Адипиновая и себациновая кислоты используются для син теза пластификаторов, полиэфирных и полиамидных смол. До восьмой пятилетки адипиновую кислоту получали как побочный продукт при синтезе капролактама, причем качество ее было очень низким. В 1966—1970 гг. создано производство адипиновой кислоты мощностью 3 тыс. т в год по методу окисления циклогексанола 55%-ной азотной кислотой в жидкой фазе. Себациновую кислоту получают перегонкой натриевых солей оксикислот, образующихся при омылении касторового масла едкой ще лочью. Мощность существующих цехов невелика (3 тыс. т в год), процесс неперспективен из-за дефицитности сырья и низкой эко номической эффективности. В настоящее время разрабатываются более эффективные процессы с использованием синтетического
сырья.
Крупные изменения произошли в течение 1961—1970 гг.
вшинной промышленности.
В1970 г. производство шин достигло 34,6 млн. штук, т. е. увеличилось но сравнению с I960 г.-в 2 раза. Выпуск крупнога-
79
бармтных шин возрос в 9,3 раза. Отечественная промышлен ность производит в настоящее время широкий ассортимент шин для различных видов автомобилей, дорожных машин, тракторов и сельскохозяйственных машин, мотоциклов и велосипедов. Вы пускается также значительное количество материалов для вос становительного ремонта шин, который производится сейчас в больших масштабах.
Сдвиги в ассортименте выпускаемых шип (табл. 9), проис шедшие за 10 лет, соответствуют темпам роста производства различных видов автомобилей, тракторов и другой техники, ко торая комплектуется пневматическими шинами.
|
|
|
|
|
ТАБЛИЦА 9 |
|
|
I960 г. |
1970 |
г. |
|
|
|
Групповой ассортимент |
Произ |
Удель |
Произ |
Удель |
1970 г. |
|
шин |
водство |
водство |
к 1960 г. |
|||
|
млн. |
ный вес |
мл н. |
ный вес |
|
|
|
штук |
% |
штук |
% |
|
|
В с е г о шин |
17,2 |
100 |
34,6 |
100,0 |
в 2,0 |
раза |
Грузовые и автобусные |
12,0 |
69,5 |
17,2 |
49,6 |
в 1,4 |
раза |
Легковые |
2,2 |
12,5 |
5,2 |
15,0 |
в 2,4 |
раза |
Тракторные и сельско |
1,5 |
. 9,0 |
6,0 |
17,4 |
в 4 |
раза |
хозяйственные |
|
|
|
|
|
|
Мотоциклетные и мото- |
1,5 |
9,0 |
6,2 |
18,0 |
в 4,1 |
раза |
роллерные |
|
|
|
|
|
|
Огромное значение для обеспечения потребности народного хозяйства в шинах имеет осуществление крупных мероприятий по повышению их качества и ходимости. Как известно, шинная промышленность является очень материалоемкой отраслью. За траты на материалы составляют от 80 до 85% себестоимости шин. Шинное производство, в котором трудится стотысячный коллектив, аккумулирует в себе труд еще более полумиллиона работников смежных производств, поставляющих сырье и ма териалы (синтетический каучук, кордные ткани, металлокорд, проволоку, сажу и другие ингредиенты резиновых смесей). По этому повышение качества продукции является по народно хозяйственной эффективности более предпочтительным путем обеспечения нужд страны в шипах, чем просто увеличение их выпуска. Повышение качества шин осуществлялось по двум направлениям.
Первое направление— повышение ходимости обыкновенных шин (с диагональным расположением нитей корда) путем со
80
вершенствования их конструкции и применения новых более вы сококачественных материалов (синтетического каучука, корд ных тканей, сажи). В 1963 г. научно-исследовательскими инсти тута мш п коллективами шинных заводов были разработаны и частично внедрены в производство новые конструкции и модели диагональных шин с применением материалов более высокого качества для всех массовых автомсбилей. В результате средняя ходимость шин в 1965 г. повысилась на 20—22% по сравнению с 1960 г. Работа по совершенствованию конструкций шин с диа гональным расположением корда продолжалась и в восьмой пятилетке. К 1970 г. удельный вес выпуска шин улучшенных конструкций и моделей (в соответствии с имевшимися ресурса ми высококачественного сырья и материалов) был доведен до 41%. Ходимость этих шин возросла по сравнению с шинами выпуска 1965 г. еще на 20—35%.
Вторым, принципиально новым направлением была разра ботка моделей и освоение производства шин с радиальным рас положением нитей корда и применением металлокорда в брекере (шины типа «Р»), что требовало создания специальных видов оборудования и соответствующей технологии. Ходимость таких шин на 40—70% превышает ходимость шин диагональных конструкций выпуска 1965 г. Кроме того, шины типа «Р» более полно отвечают основным техническим требованиям автомо бильной и тракторной промышленности и по другим показате лям: весу, расходу горючего, теплообразованию, сцеплению с дорожным покрытием. Благодаря этим преимуществам произ водство и эксплуатация шин с радиальным расположением
нитей |
корда дают большой экономический выигрыш. Выпуск |
1 млн. |
шин типа «Р» для грузовых автомобилей и автобусов |
дает экономию народному хозяйству от 20 до 80 млн. руб. (в зависимости от размера шин) по сравнению с усовершенство ванными шинами диагонального построения.
Серийное производство шин типа «Р» для грузовых автомо билей, выпускаемых московским и горьковским автозаводами, было начато в конце 1964 г., однако из-за ограниченности сырьевых ресурсов выпуск шин такой конструкции к 1970 г. со ставил всего лишь 3,1 млн. штук, а удельный вес в общем объ еме производства шин — 9%.
В целом выполненные в седьмой и восьмой пятилетках меро приятия по повышению качества шин существенно сказались на увеличении их фактического среднего пробега. Так, эксплуа
тационный |
пробег |
шин, |
выпущенных в 1970 г., по |
сравнению |
с пробегом шин выпуска |
1960 г. увеличился для грузовых авто |
|||
мобилей на |
62%, |
для легковых автомобилей — на |
38%, для |
0 За к. 316 |
81 |