
книги из ГПНТБ / Бушуев, В. М. Химическая индустрия в свете решений XXIV съезда КПСС
.pdfБольшое значение для роста выпуска товаров народного по требления, а также для обеспечения автомобильной, авиацион ной и судостроительной промышленности отделочными материа лами имело развитие производства искусственной кожи. В част ности, производство мягкой кожи увеличилось с 88 млн. м2 в 1960 г. до 151 млн. м2 в 1970 г. За этот же период возрос вы пуск подошвенной резины со 178 до 274 тыс. т, обувного картона с 41,7 до 65,6 тыс. т. Одновременно совершенствовался ассорти мент и повышалось качество этой продукции, прежде всего ка чество искусственных жестких кож, обувных резин и картонов. В истекшем десятилетии организовано производство кожеподоб ной пористой резины «кожволон», подошвы из которой приме няются практически во всех видах обуви; термостойкого кожволокна для подошв обуви, изготовляемой на поточных линиях клеевым методом; пористой формованной подошвы; резины «Стиронип» и «Траиспорент» для обуви весенне-осеннего ассортимента. Использование новых полимеров (высокостирольных и других каучуков, термореактивных смол), а также более активных на полнителей позволило значительно повысить физико-механиче ские показатели обувных резин и снизить на 25% их расход за счет уменьшения толщины деталей.
Освоено массовое производство кожевенно-целлюлозных кар тонов. В частности, организован выпуск стелечного целлюлоз ного материала, который по своим показателям не уступает луч шим зарубежным образцам, значительно увеличен выпуск гото вых формованных деталей из картонов.
Выпуск искусственной мягкой кожи увеличился в основном за счет быстрого развития производства кожи с поливинилхло ридным покрытием. В 1970 г. такой кожи выработано 80,7 млн. м2, что составляет 53% от общего выпуска искусственных кож (в 1960 'г. кожи с поливинилхлоридным покрытием производилось 28,6 млн. м2). Большим достижением является организация опыт но-промышленного производства синтетической кожи с полиуре тановым покрытием, которая по санитарно-гигиеническим свой ствам приближается к натуральной коже, а по ряду эксплуата ционных свойств выгодно отличается от нее: обладает водооттал кивающей способностью, не требует особого ухода; обувь, изго тавливаемая из нее, в процессе носки хорошо сохраняет цвет и форму.
Значительно повысился и технический уровень промышлен ности искусственных кож. Многие предприятия оснащены за этот период современным технологическим оборудованием; резиносмесителями, вулканизаторами, смесителями непрерывного дей ствия, коническими мельницами, высокопроизводительными по
52
точными линиями по производству поливинилхлоридных пленок, котировальными, литьевыми и отливными машинами.
Народнохозяйственная эффективность быстрого развития про изводства искусственной кожи видна из следующих данных. Для того чтобы заменить использованную в 1970 г. в производстве обуви искусственную кожу натуральной потребовалось бы до полнительно заготовить 39 млн. шкур крупного рогатого скота, что составляет 65% всего заготовленного в этом году кожсырья.
Рост производства химических волокон и синтетической кожи значительно расширил сырьевую базу для выпуска товаров на родного потребления., В общем потреблении текстильного сырья доля химических волокон возросла до 22% в 1970 г.'против 11,7% в 1960 г. В последнем году восьмой пятилетки с применением хи мических волокон было произведено более 30% от общего коли чества всех выработанных тканей, при этом шерстяных — 8 6 %, шелковых — 97%, около 45% бельевого и свыше 30% верхнего трикотажа. Более 60% общего прироста обуви достигнуто на основе применения синтетических материалов.
Экономия от снижения себестоимости продукции за счет при
менения |
химических |
волокон |
в |
1961—1970 гг. |
превысила |
5,3 млрд. руб. |
|
|
|
|
|
Коренные изменения произошли и в промышленности синте |
|||||
тического каучука. Выпуск синтетических каучуков |
увеличился |
||||
за 10 лет |
в 2,7 раза. |
В структуре |
производства синтетических |
||
каучуков произошли коренные сдвиги (табл. 5). |
|
||||
Создание крупнотоннажного |
производства стереорегулярных |
||||
каучуков — полиизопренового и |
полибутадиенового — является |
крупным достижением отечественной науки и техники. Экономи
ческое и оборонное |
значение организации |
выпуска |
указанных |
|
|
|
|
|
ТАБЛИЦА 5 |
|
I960 г. |
1970 г. |
|
|
Каучуки и латексы |
Уд. вес |
Уд. вес |
1970 г. |
к I960 г. |
%%
В с е г о |
100,0 |
100,0 |
в 2,7 |
раза |
Стереорегуляриые |
— |
29,5 |
— |
|
Бутадиен-стирольные и бу- |
37,1 |
47,5 |
в 3,5 |
раза |
тадиен-метилстирольные |
|
|
_ |
|
СКВ |
50,5 |
9,2 |
|
|
Вутадиен-нитрильные |
1.2 |
2,5 |
в 5,8 |
раза |
Хлоропреновые |
8,0 |
7,7 |
в 2,6 |
раза |
53
каучуков, полноценно заменяющих натуральный каучук практи чески во всех изделиях из резины, трудно переоценить.
Значительно расширен ассортимент сополпмерных каучуков общего назначения. Так, число марок бутадиен-стирольных и бутадиен-метилстирольных каучуков увеличилось с 5 до 12; организовано производство каучуков этого типа для нужд легкой и электрокабельной промышленности, для производства высоко качественных покрышек, камер и резиновых технических изде лий. Ассортимент бутадиен-нитрильных каучуков расширился с 3 до 9 марок за счет выпуска мягких и легкообрабатываемых кау чуков, а также нетоксичных каучуков для изделий, соприкасаю щихся с пищевыми продуктами.
В опытном масштабе создано производство одного из наибо лее перспективных каучуков общего назначения — этиленпропиленового. Этот каучук обладает неплохими физико-механиче скими свойствами, стоек к воздействию атмосферных влияний и при крупных масштабах производства будет самым дешевым каучуком, так как мономерами для него служат такие доступные продукты, как этилен и пропилен.
Намного увеличился ассортимент каучуков немассового на значения. Организовано, например, промышленное производство десятков новых марок силоксановых каучуков, резиновых сме сей, компаундов и герметиков на их основе. Налажен выпуск ряда марок тиокола и уретановых каучуков. Ведутся большие исследовательские и опытно-промышленные работы по многим новым видам каучуков, которые призваны обеспечить самые разнообразные нужды современной техники.
Один из цехов завода синтетического каучука показан на рис. 8 .
Серьезные качественные изменения произошли в производ стве мономеров. Одно из них—'получение бутадиена из нефтехи мического сырья (бутана и фракций С4 пиролиза бензина) вме сто этилового спирта. В результате использования для этой цели более дешевого нефтяного сырья, за счет снижения эксплуата ционных затрат за 10 лет было сэкономлено около 250 млн. руб.
Большое значение имело также освоение крупномасштабного производства изопрена двумя методами: из изобутана и мета нола и из изопентана, что создало твердую основу для дальней шего быстрого развития производства этого каучука в девятой пятилетке.
Повышение технического уровня промышленности синтетиче ского каучука осуществлялась также путем внедрения новых технологических процессов и высокопроизводительного оборудо вания. Во вновь построенных производствах установлены агре-
54
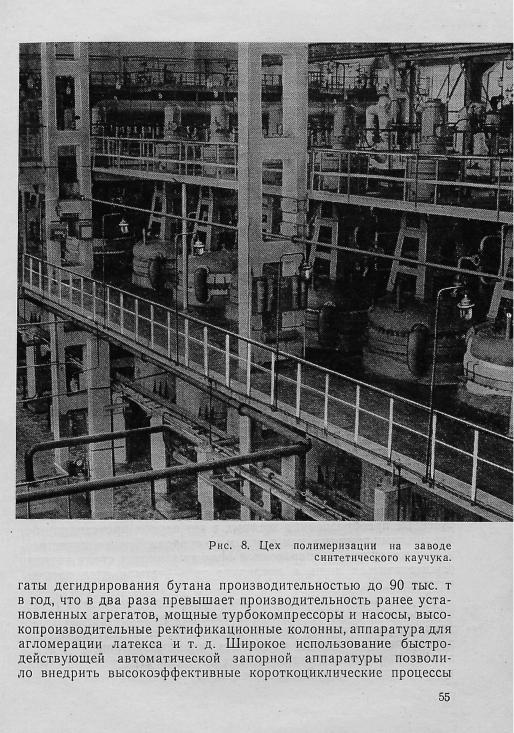
получения бутадиена и изопрена. Для разделения мономеров применены системы экстрактивной дистилляции взамен устарев ших систем хемосорбции.
Разработаны и нашли применение в промышленности ориги нальные конструкции полимеризаторов со скребковыми мешал ками, что дало возможность создать высокопроизводительные линии 'полимеризации в растворах для производства етереорегулярных каучуков. Начато внедрение механических методов выде ления влагги из каучуков с помощью шнековых агрегатов высокой производительности. Такие методы дают возможность суще ственно снизить энергетические затраты, улучшить качество кау чука, увеличить производительность труда и в значительной сте пени оздоровить воздушные бассейны в районе расположения заводов.
Большим достижением является практически полная ликви дация ручного труда на предприятиях отрасли в результате ши рокого применения упаковочных машин, подъемников и средств малой механизации (транспортеров, конвейеров и др.).
Все эти мероприятия позволили значительно улучшить техни ко-экономические показатели работы промышленности синтети ческого каучука. Производительность труда на одного работаю щего возросла за 10 лет более чем на 70% •
Очень важно, что в годы восьмой пятилетки научно-исследо вательскими организациями и коллективами предприятий был выполнен большой объем поисковых, научно-исследовательских и опытных работ по совершенствованию применяемых технологи ческих процессов и созданию новых методов производства для успешного развития промышленности в девятой пятилетке на базе оригинальных отечественных разработок.
Определенное развитие получила в 1961—1970 гг. и лакокра сочная промышленность. Однако она относится к тем немногим подотраслям химической индустрии, количественные и каче ственные преобразования которых в тот период происходили бо лее низкими темпами, чем в целом по отрасли. Точнее, качествен ные изменения в лакокрасочной промышленности стали активно осуществляться лишь в последние три — четыре года восьмой пятилетки.
За десять лет производство лакокрасочных материалов увели чилось с 1212 до 2377 тыс. т, т. е. почти в 2 раза. Более быстрыми темпами увеличивался выпуск материалов на основе синтетиче ских смол: эпоксидных, акриловых, кремнийорганических и по лиэфирных, а также синтетических латексов. Изменения в струк туре производства показаны в табл. 6,
56
|
|
|
|
I960 г. |
1970 г. |
||
Лакокрасочные материалы |
Произ |
Уд. вес |
Произ |
Уд. вес |
|||
|
|
|
|
водство |
% |
водство |
|
|
|
|
» |
тыс. т |
|
тыс. т |
|
В с е г о |
|
|
|
1212 |
100,0 |
2377 |
100,0 |
Прогрессивные |
|
521 |
43,0 |
1152 |
48,5 |
||
лаки |
и |
эмали |
на |
339,1 |
28,0 |
681 |
28,6 |
основе |
|
конденса |
|
|
|
|
|
ционных смол * |
|
|
|
|
|
||
лаки |
и |
эмали |
на |
158 |
13,0 |
345 |
14,5 |
основе эфиров цел |
|
|
|
|
|||
люлозы * |
|
|
|
|
|
||
лаки |
и |
эмали |
на |
23 |
1,9 |
84 |
3,6 |
основе полимериза- |
|
|
|
|
|||
циоиных смол* |
|
|
|
|
|
||
водоразбавляемые |
1,4 |
0,1 |
42 |
1,8 |
|||
краски |
|
на основе |
|
|
|
|
|
латексов |
и водных |
|
|
|
|
||
дисперсий |
|
|
|
|
|
||
Тертые масляные крас |
348 |
28,7 |
725 |
30,5 |
|||
ки |
|
|
|
|
|
|
|
Олифы |
|
|
|
336 |
. 27,7 |
492 |
20,7 |
Прочие |
|
|
|
7 |
0,6 |
8 |
0,3 |
* С р а с т в о р и т е л я м и .
ТАБЛИЦА 6
1970 г.
к1960 г.
в1,96 раза
в2,2 раза
в2 раза
в2,2 раза
в3,7 раза
в30 раз
в2,1 раза
в1,5 раза
Как видно из таблицы, доля прогрессивных лакокрасочных материалов (вырабатываемых на основе синтетических смол) возросла за десять лет с 43 до 48,5%. Внедрены в производство новые виды синтетического сырья, что позволило улучшить ка чество лаков, красок и эмалей, увеличить срок их службы, по высить устойчивость к агрессивным средам и высоким темпера турам, придать хороший внешний вид. Промышленностью раз работано и освоено 76 новых лакокрасочных материалов. Пущены производства таких ценных материалов, как водоразбавляемые краски на основе бутадиен-стирольного латекса и поливинилацетатной дисперсии, водорастворимые автомобильные грунты, наносимые методом электрофореза, полиэфирные лаки для ме бели, светоотражающие пленки для дорожных знаков. Освоен
57
выпуск новых стойких к агрессивным средам эмалей на основе эпоксидных и акриловых смол, хлоркаучука, сополимеров винил хлорида с винилацетатом, а также термостойких лаков и эмалей на основе кремнийорганических соединений.
Наряду с этим технический прогресс в подотрасли осуще ствлялся 'путем концентрации производства и развития действую щих заводов в крупные 'предприятия с прогрессивной техноло гией и комплексной механизацией технологических процессов.
Вновь построенные и реконструированные цехи по единичной мощности реакторов, системам обогрева и управления, уровню механизации и автоматизации технологических процессов не уступают передовым заводам зарубежных фирм и по своему тех ническому оснащению способны производить высококачествен ные лакокрасочные материалы.
В промышленности лакокрасочных материалов внедрялись передовые технологические процессы. В производстве алкидных смол и лаков, например, преобладающее распространение полу чил синтез смол с азеотропной отгонкой реакционной воды. В производстве эмалей широко применяются такие высокопро изводительные и эффективные виды оборудования для дисперги рования пигментов, как бисерные мельницы и скоростные сме сители. Началось выполнение большой программы развития производства высококачественного белого пигмента— двуокиси титана.
Однако, несмотря на эти меры, народное хозяйство до сих пор ощущает острый дефицит в лакокрасочной продукции, да и по качеству она зачастую уступает продукции ведущих зарубежных фирм; многие отечественные лакокрасочные материалы хуже аналогичных зарубежных образцов по блеску, чистоте цвета и некоторым другим показателям.
Следует отметить две основные причины такого отставания. Во-первых, все еще низкий удельный вес передовых технологи ческих процессов и, во-вторых, недостаточный объем производ ства многих компонентов (полимеризациониых смол, растворите лей, многоатомных спиртов, ангидридов фталевой и малеиновой кислот, пигментов и др.) и неудовлетворительное качество мно гих видов сырья. Растительные масла, как правило, не рафини руются должным образом. Перхлорвиннловая смола имеет плохую растворимость. Не выпускается ряд необходимых раство рителей, полиспиртов, микроизмельченных наполнителей (мик рокальцит, микродоломит, микробарит и др.).
При разработке пятилетнего плана развития химической индустрии центральные плановые органы и Министерство хими ческой промышленности обратили серьезное внимание на разра
58
ботку мер по устранению недостатков в развитии лакокрасочной промышленности.
В соответствии с потребностями народного хозяйства в седь мой и восьмой пятилетках значительными темпами развивалось производство содопродуктов. Выпуск каустической соды за де сятилетие возрос с 704 до 1783 тыс. т, т. е. более чем в 2,5 раза. Следует отметить, что наряду с потребностью народного хо зяйства в самой каустической соде в этот период стал про являться второй фактор, способствующий развитию этой подот расли— быстро растущая потребность в хлоропродуктах.
Серьезные изменения произошли в техническом уровне про изводства каустической соды. Хотя к началу восьмой пятилетки каустик получался в основном диафрагменным методом, значи тельно возрос удельный вес производства его в ваннах с ртут ным катодом, где без дополнительного упаривания и очистки Получается 40—50%-ный едкий натр достаточной чистоты. Сни зилась доля производства каустической соды устаревшим хими ческим способом. Изменения в структуре производства каусти ческой соды показаны в табл. 7.
До 1960 г. хлорная промышленность была оснащена в основ ном маломощными электролизерами диафрагменного типа с на грузкой по току 5 ка. На таких электролизерах производилось около 90% всего количества каустической соды. В седьмой пяти летке новые и реконструируемые заводы оснащались более мощ ными отечественными электролизерами с нагрузкой 25 ка, а позд нее— электролизерами с нагрузкой 50 ка. К 1970 г. на новых электролизерах вырабатывалось уже около 60% каустика, про изводимого диафрагменным методом. Одновременно велись ра боты по усовершенствованию и интенсификации электролизеров
(без изменения |
их габаритов) путем |
увеличения |
электродных |
поверхностей и повышения плотностд тока. |
в основном |
||
Ртутный электролиз до 1965 г. был оснащен |
|||
электролизерами |
небольшой мощности |
с нагрузкой 15—30 ка. |
|
|
|
|
ТАБЛИЦА 7 |
|
Удельный вес, % |
|
|
Метод получения |
|
|
|
каустика |
I960 г. |
1965 г. |
1970 г. |
|
|||
Ртутный |
13,8 |
18,2 |
29,4 |
Диафрагменный |
65,7 |
67,1 |
59,0 |
Химический |
20,5 |
14,7 |
11,6 |
.59
В восьмой пятилетке осуществлено коренное перевооружение ртутного электролизного парка — в производство были внедрены новые электролизеры, рассчитанные на нагрузку 100 ка. На этих электролизерах в 1970 г. было выработано 80% каустической соды от общего количества, получаемого по ртутному методу. Мощности производств выросли с 50—60 до 120—150 тыс. т в год.
Преобразовательные подстанции всех цехов электролиза были оснащены полупроводниковыми агрегатами на 25 ка.
Серьезные изменения произошли в технике вспомогательных производственных отделений. Внедрена непрерывная очистка рассола, подземное выщелачивание соли, разработана и освоена схема глубокой осушки хлора, стали применяться мощные цен тробежные турбокомпрессоры (вместо малопроизводительных ротационных компрессоров), а также выпарные системы в про изводстве каустика диафрагменным методом производитель ностью 50—70 тыс. т в год. Созданы цехи сжижения хлора мощ ностью 60—100 тыс. т в год.
Важной особенностью в развитии хлорной промышленности является быстрый рост производства новых хлорорганических продуктов. За истекшее десятилетие была практически создана новая отрасль — промышленность хлорорганического синтеза. Число вырабатываемых ею продуктов возросло за этот период в два с лишним раза. В 1966 г. на производство хлорорганической продукции израсходовано более 70% произведенного хлора.
Созданы крупные производства таких хлорсодержащих про дуктов, как винилхлорид, эпихлоргидрин — полупродукт для производства синтетического глицерина и эпоксидных смол, хлорсульфированный полиэтилен, ряд хлорорганических пести цидов, а также дихлорэтан, трихлорэтилен, метиленхлорид, хлорметил, хлорэтил, четыреххлористый углерод, хлорпарафины и другие химикаты, используемые как растворители и как полу продукты в органическом синтезе. Производство, например, ди
хлорэтана |
за 10 лет возросло |
в 2,6 раза, метиленхлорида — |
в 6,6 раза, |
хлорметила — в 8 раз, трихлорэтилена — в 9,8 раза, |
|
четыреххлористого углерода — в |
2,4 раза. |
Значительно повышен технический уровень производства та ких многотоннажных хлорорганических продуктов, как дихлор этан и винилхлорид.
За истекшие годы было освоено около трех десятков новых технологических процессов хлорорганического синтеза.
Разработан и осуществлен процесс получения метиленхло рида методом хлорирования метана в кипящем слое катализа тора, что позволило существенно увеличить производительность
60
аппаратуры, снизить себестоимость и повысить качество про дукта.
Серьезным достижением является освоение производства син тетического эпихлоргидрина — одного из многотоннажных хлорорганических продуктов, который еще недавно вырабатывался из глицерина, получаемого омылением натуральных жиров. В восьмой пятилетке было пущено производство синтетического глицерина по методу хлорирования пропилена. На одной из ста дий этого процесса получается синтетический эпихлоргидрии, который значительно дешевле «жирового» эпихлоргидрина.
Важное значение имела организация производства сульфоиола и сульфоната — поверхностно-активных веществ, являю щихся основой для получения синтетических моющих средств. Сульфонол и сульфонат не содержат хлора, но он в больших ко личествах потребляется в процессах их производства. В 1970 г. производство сульфонола составило 58,2 тыс. т, а выпуск суль фоната, получаемого методом фотохимического сульфохлорйро- вания /-/-парафинов, — 7 тыс. т.
Развитие производства синтетических моющих средств, син тетических жирных кислот, применяемых для выработки мыла, лакокрасочной продукции и других химикатов позволяет не только обеспечить потребности народного хозяйства в высокока чественных продуктах и материалах, но и высвободить большое количество растительных и животных жиров из промышленного потребления. В 1961-—1970 гг. за счет выпуска указанных хими ческих продуктов было высвобождено из промышленного потреб ления около 1800 тыс. т жиров.
Общеизвестно значение кальцинированной соды. Выпуск этого продукта в 1961—1970 гг. увеличился с 1793 до 3485 тыс. т,т. е.
в1,9 раза; по объему его производства СССР занимает второе место в мире. Выработка соды на одного работающего за этот период возросла в среднем на 70%, а на передовых предприя тиях— почти в 2,5 раза. По концентрации производства соды
СССР находится впереди зарубежных стран. Самым крупным содовым заводом в мире является Стерлитамакский содово цементный комбинат, мощность которого около 1800 тыс. т соды
вгод, в то время как максимальная мощность наибольшего аме риканского завода, работающего по аммиачному способу, — не многим больше 900 тыс. т в год.
Рост производства кальцинированной соды был достигнут за счет расширения и модернизации действующих заводов путем применения оборудования большей мощности. Внедрены эле
менты адсорбции — дистилляции мощностью 630 т (вместо 470 т) в сутки, карбонизационные колонны мощностью до 250 т (вместо
61