
Лекции - 7 семестр
.pdfТолько одно устойчивое соединение, имеющее фиксированный химический состав, —
гётит.
!
Чистый бурый железняк содержит от 52.2% до 66.1% железа.
!
При добыче — большой выход мелочи (подвергается окускованию).
!
Сидеритовые железные руды.
!
Сидерит (FeCO3) — 48.3% железа — плотная кусковая руда, вредных примесей —
чуть больше, чем нихуя.
!
Силикатные руды.
!
Шамозит и тюрингит — до 42% железа.
!
* * *
!
В металлургии используются следующие дешевые заменители железных руд:
колошниковая пыль, шламы, окалина.
!
Состав колошниковой пыли, выносимой потоком газов через колошник доменной печи и осаждаемой затем из газа в сухих пылеуловителях, приблизительно соответствуют составу проплавляемой в этот момент шихты, но в колошниковой пыли находится еще до 7-9% углерода в виде частиц кокса, что несколько снижает содержание железа в пыли и в то же время — с точки зрения агломерации — является весьма ценным
свойством этого вида сырья.
!
В аглошихте используются шламы доменных и сталеплавильных цехов. Пиритные огарки (состоят из гематита, пустой породы и часто содержат много — до 5-6% — остаточной серы) получают в больших количествах на сернокислотных заводах при обжиге пирита в токе воздуха или кислорода. В физическом смысле пиритные огарки
— достаточно пыльеватый материал.
!
Окалина, удаляемая при прокатке слитков, состоит из гематита и магнетита. При транспортировке окалина загрязняется землей, песком. Окалину вводят в аглошихту,
повышая содержание железа.
!
Значительная часть добываемой руды перед использованием подвергается предварительному обогащению. Только 12% запаса железных руд России можно
использовать без обогащения; 55% — легко обогатимые, 33% — трудно обогатимые.
!
Методом мойки, сухой и мокрой магнитной сепарации, флотации удается получить из бедных руд (25-30% Fe) богатый концентрат (60-65% Fe). Обогащению предшествует
дробление, измельчение руды — разрушаются сростки рудного минерала с пустой
породой.
!
Концентрат оказывается чрезвычайно тонким материалом.
!
!
25. Определение руды. Факторы, определяющие ценность руд. Полезные и
вредные примеси железных руд. Характеристика пустой породы.
!
Железные руды — горные породы, переработка которых экономически выгодна при
современном уровне развития техники.
!
Целесообразность и ценность определяется:
!
1) содержанием в горной породе рудного минерала;
2) полезными и вредными примесями;
3) составом пустой породы;
4) глубиной залегания рудного тела;
5) запасами руды;
6) удаленностью месторождения от дорог и населенных пунктов;
7) многими другими природными, техническими и экономическими факторами.
!
Вредные примеси — элементы, ухудшающие свойства получаемых из металла изделий
или негативно влияющие на эффективность переработки (S, P, As, Zn и Pb).
!
Полезные примеси — ценные элементы, содержащиеся в руде в небольших количествах, которые улучшают свойства металлических изделий, либо могут быть попутно извлечены с повышением общей рентабельности переработки (Mn, Cr, Ni, V,
W, Mo). В частности, природнолегированные руды.
!
Наиболее распространенная примесь — марганец. В обычных условиях плавки марганец вводится в чугун с марганцевой рудой, подаваемой в аглошихту. Наличие
марганца в железной руде позволяет снизить себестоимость чугуна.
!
Пустая порода — сопутствующие (перемешанные с рудными) минералы, не содержащие искомого металла и экономически непригодные для промышленного
потребления.
!
Состав пустой породы влияет на температурный уровень дальнейшей пирометаллургической переработки, а также определяет необходимость
использования тех или иных флюсующих добавок.
!
Руды с кислой пустой породой содержат преимущественно силикаты и
алюмосиликаты. Руды с основной пустой породой — окислы кальция и магния.
!
Если железные руды имеют кремнистую пустую породу, то приходится добавлять в
доменную шихту флюс (известняк), доводя содержание CaO в шлаке до желаемого.
!
Некоторые руды имеют самоплавкую пустую породу (оптимальное соотношение в пустой породе кислых и основных окислов), где основность изменяется от 0.5 до 1.1 — плавка таких руд может производиться с пониженным расходом известняка, что делает
такие руды особенно ценным сырьем для промышленности.
!
!
26. Дробление и измельчение железорудных материалов. Принципы разрушения.
Устройства для дробления и измельчения.
!
Значительная доля руд и флюсов, добытых в карьерах или шахтах, представлена крупными кусками (от 1 метра и более), что затрудняет транспортировку и загрузку в
металлургические агрегаты.
!
Плавка крупнокусковой шихты сопровождается низкими технико-экономическими показателями, поскольку такие материалы из-за малой величины удельной
поверхности медленно восстанавливаются и прогреваются (время — деньги).
!
Для обогащения руду приходится дробить и измельчать до крупности 0.1 мм — в этом случае дробление применяется как вспомогательная операция перед последующим
обогащением.
!
При дроблении и измельчении разрушаются сростки рудного минерала с пустой породой. То есть куски руды необходимо дробить и измельчать до такой степени, чтобы раскрыть зерна рудного минерала, то есть чтобы каждая частичка представляла
собой оксид железа либо пустую породу.
!
Дробить и измельчать, то есть разрушать крупные куски материала на более мелкие,
можно несколькими способами:
!
1) раздавливанием;
2) ударом;
3) раскалыванием;
4) изломом;
5) истиранием;
6) срезанием; и сочетанием этих способов.
!
При дроблении куски руды разделяются на части, при этом преодолевается сила сцепления частиц. Сопротивление, которое руда оказывает дроблению, называют прочностью или крепостью руды. Горные породы по этому свойству делят на четыре
группы:
!
1) мягкие (сопротивление раздавливанию 10 МПа) — глинястые породы;
2) средней твердости (10-50 МПа) — волунчатые руды, богатые бурые железняки; 3) твердые (50-100 МПа) — магнетиты и известняк;
4) весьма твердые (больше 100 МПа) — железистые кварциты.
!
Практикой установлено, что дробить твердые материалы сразу за один прием (присест) от крупных кусков до мелких неэкономично. Эту операцию осуществляют в несколько стадий, используя на каждой из них соответствующее дробильное
устройство.
!
В зависимости от размера кусков до и после дробления выделяют стадии:
!
1) крупное дробление — от 1500 до 300 мм; 2) среднее дробление — от 300 до 20 мм; 3) мелкое дробление — от 20 до 5 мм; 4) измельчение — от 5 до 1 мм;
5) тонкое измельчение — от 1 до 0.05 мм и менее.
!
Таким образом, дробление — это операция уменьшения размера кусков в результате
их разрушения до 5 мм. Разрушение более мелких частиц — измельчение.
!
Дробилки:
!
1) щековая (принцип работы заключается в циклическом сближении и расхождении дробящих плоскостей);
2) конусная (процесс разрушения происходит непрерывно в результате кругового эксцентричного движения внутреннего конуса внутри чаши);
3) валковая (разрушение материала между двумя валками, вращающимися навстречу друг другу);
4) молотковая и роторная (принцип работы схож и основан на ударном разрушении).
!
В горнорудной промышленности измельчение является подготовительной операцией к
обогащению руд и осуществляется в барабанных мельницах.
!
Мельницы:
!
1) шаровая;
2) стержневая;
3) самоизмельчения.
!
Принцип работы всех мельниц схож и основан на воздействии на материал мелющих тел, соответственно — металлических шаров, стержней или крупных кусков руды. Мельница представляет собой вращающийся барабан с полыми цапфами, через которые с одной стороны непрерывно поступает, а с другой непрерывно удаляется
рудный материал.
!
Шаровая мельница — полый барабан с горизонтальной осью вращения, заполненный дробильным материалом и стальными (чугунными) шарами. Благодаря вращению барабана шары и куски материала поднимаются в зависимости от частоты вращения на определенную высоту и затем падают или скатываются, дробя руду под действием ударных и истирающих нагрузок. Данный способ чаще всего применяют с
добавлением воды (пульпа) для исключения пылеобразования.
!
Эффективность или производительность работы шаровых мельниц определяется
следующими факторами:
!
1) частотой вращения;
2) размером кусков загружаемого материала;
3) относительным диаметром шаров;
4) общей их загрузкой.
!
С повышением частоты вращения барабана шары поднимаются на большую высоту и, падая, выполняют большую работу дробления. Однако при превышении определенной
частоты вращения шары перестают падать, и дробление прекращается.
!
С уменьшением исходного размера кусков дробимого материала существенно увеличивается производительность шаровых мельниц. Однако при этом ухудшаются технико-экономические показатели на предыдущих стадиях дробления. С учетом эффективности всех дробильно-измельчительных операций оптимальная крупность
кусков материала, загружаемого в шаровые мельницы, составляет от 5 до 20 мм.
!
В мельницах используются шары диаметром от 25 до 150 мм, оптимально — мельница
заполняется шарами на 40-50%.
!
Основные показатели, характеризующие процессы дробления и измельчения, —
степень дробления (измельчения) и эффективность работы агрегатов.
!
Степень дробления (i) — отношение диаметра куска исходного материала (D) к
диаметру куска продукта дробления (d):
!
i = D / d
!
Эффективность работы агрегатов (Э) — отношение массы дробленного
(измельченного) продукта (Q) к израсходованной энергии (Е):
!
Э = Q / E
!
Величина, обратная эффективности, определяет удельный расход энергии на
дробление:
!
Eуд = E / Q

!
!
27. Принципы усреднения рудного сырья. Схема закладки штабеля и забора руды
из штабеля. Показатели усреднения.
!
Усреднение — операция смешивания больших масс материала для повышения его однородности (в первую очередь по химическому составу). Усреднением обеспечивается стабильность и эффективность любой переработки, поэтому данную
операцию желательно проводить перед каждым этапом металлургического передела.
!
Усреднение кусковых и сыпучих материалов (руд, концентратов, топлива, флюсов) осуществляют на складах либо в бункерах путем перемешивания. Процесс выполняется так: штабель формируется из большого количества тонких горизонтальных слоев материалов; предполагается, что состав каждого отдельного слоя по длине штабеля остается постоянным. Материал забирается с торца штабеля одновременно захватывая все слои по высоте. Усреднение в бункерах же
обеспечивается за счет одновременной и регулируемой выдачи материала из них.
!
Наиболее эффективный способ стабилизации — на складах. Тип склада определяют его форма и схема формирования штабелей, среди которых наибольшее
распространение получили: отвальные, эстакадные и безэстакадные.
!
Способы формирования штабелей на складах:
!
1) шевронные;
2) продольными и поперечными полосами;
3) при непрерывном и шаговом перемещении укладчика;
4) комбинированные.
!
Способы разгрузки складов:
!
1) вертикальные;
2) горизонтальные;
3) обрушением;
4) комбинированные.
!
!
Результаты работы усреднительных установок оцениваются величиной степени усреднения Kуср = σ1/σ2 (где σ1 и σ2 — сигмы — величины стандартных отклонений до и после усреднения).
!
Для складов с рудными грейферными кранами степень усреднения К уср составляет в среднем 1,8-2,2. Степень усреднения возрастает с увеличением размеров штабелей
руды.
!
Если плавка ведется на рудах постоянного состава, то персонал доменного цеха имеет возможность снизить до предела расход кокса, работая без перегрева печей и не опасаясь аварийного похолодания. При этом достигается ровный экономичный ход ДП
с соответствующим повышением производительности.
!
!
28. Грохочение и классификация железорудных материалов. Устройства для
грохочения и классификации, типы и принципы работы.
!
Оптимизация крупности включает также процессы грохочения и классификации.
!
Процесс разделения сыпучих материалов на отдельные классы (фракции) называют
оптимизацией по крупности. Такая оптимизация осуществляется:
!
1)грохочением исходного материала на просеивающих поверхностях с калиброванными отверстиями (колосниковые решетки, сита, решета);
2) |
разделением в жидкой или газообразной среде, в которой взвесь (масса) |
! |
минеральных частиц осаждается с различной скоростью в зависимости от их |
размеров и плотности. |
Для определения крупности применяют ситовый, шламовый, микроскопический
анализы.
!
После дробления и измельчения — грохочение или классификация. Если продукт
крупный, он отправляется обратно на дробление (измельчение).
!
Грохочение — разделение или сортировка материала на классы по крупности при помощи решеток или механических сит. А разделение в воде или в воздухе на основе разности скоростей падения зерен различной крупности — это гидравлическая или
пневматическая классификация.
!
Грохочением обычно разделяют материалы до крупности 1-3 мм, более мелкие —
разделяются классификацией.
!
В практических условиях не удается полностью разделить мелкие и крупные кусочки. Важнейшим технологическим показателем, характеризующим качество грохочения, является эффективность грохочения, представляющая собой отношение массы мелкого класса в подрешетном продукте (q_) к массе этого класса в исходном
материале:
!

ε = 100·q_ / qисх
!
Типы и устройство грохотов:
!
1) колосниковые (неподвижные);
2) подвижные (барабанные, валковые, качающиеся, вибрационные).
!
Колосниковые грохоты (неподвижные грохоты) имеют невысокую эффективность грохочения (50-60%). Подавляющее большинство применяемых грохотов имеют подвижную решетку, благодаря чему у них значительно более высокая эффективность
грохочения.
!
Подвижные грохоты делят на барабанные, валковые, качающиеся, вибрационные.
!
1) Вращающийся барабанный грохот представляет собой цилиндрический или конический барабан с перфорированной поверхностью (решето, сито). Размер ячеек сит возрастает к разгрузочному концу грохота. Для обеспечения перемещения материала от одного конца к другому барабан монтируют под углом к горизонту 5-7 градусов. При вращении барабана материал, находящийся в нем, поднимается на определенную высоту и затем сползает или скатывается вниз. В этот момент мелкие кусочки просыпаются через отверстия. За время пребывания в барабане каждый объем сыпучего материала многократно поднимается и ссыпается вниз, что
существенно повышает эффективность грохочения.
!
1 — опорная рама; 2 — питающая воронка; 3 — барабан; 4 — приводной механизм;
5 — бункер надрешетного продукта; 6 — бункер подрешетного продукта.
!
Барабанные грохоты в зависимости от количества сит могут разделять материал по крупности на 2 и более классов. Барабанные грохоты применяют для промывки и сортировки по крупности глиносодержащих руд (промывочные барабанные грохоты
или скрубберы).
!
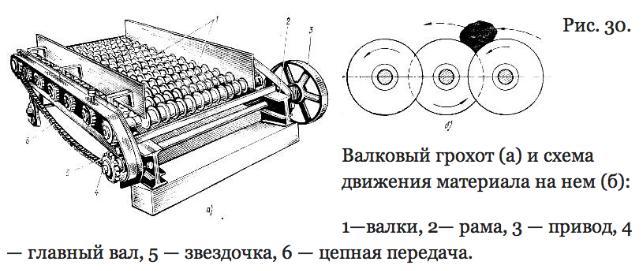
2) Валковый (дисковый, роликовый) грохот имеет рабочую поверхность, образованную дисками, насаженными на ряд валков, вращающихся в направлении
подачи материала.
!
A
!
Валковые грохоты используют для предварительного грохочения угля, известняка и других материалов перед первичным дроблением (чаще всего — в доменном цехе для
сортировки кокса).
!
3) Качающиеся грохоты — плоские грохоты с продольными симметричными
колебаниями просеивающей поверхности.
!
Процесс грохочения характеризуется комплексом технологических показателей и
параметров.
!
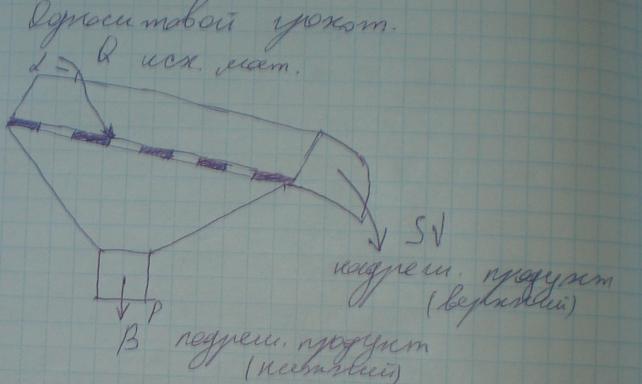
!
1) Выход подрешетного продукта.
!
Q = P + S
!
Уравнение баланса мелкого класса имеет вид: Q = PB + SV,
где , B, V — содержание какого-либо класса соответственно в исходном,
подрешетном и надрешетном продуктах.
!
Q ( — V) = P (B — V)
!
Отсюда выход подрешетного продукта, %:
!
Ɣ = P/Q*100 = ( — V)/(B — V)*100
!
2) Точность отсева.
!
E0 = (Ɣ/ )*100.
!
3) Замельченность надрешетного продукта.
!
V = 100*( — Ɣ)/(100 — Ɣ)
!
Теоретические основы классификации. Падение частиц:
!