
3229
.pdf
нимают KH = 1,0; для косозубых колес в зависимости от окружной скорости v KH
имеет следующие значения: при v =
10 |
- 20 м/с и 7 - й степени точности |
H |
1,0 – 1,1; при v до |
|
|
|
|
10 |
м/с и 8 - й степени точности KH |
= l,05 - l,15; H - коэф- |
фициент, учитывающий неравномерность распределения нагрузки по ширине зубчатого венца. При проектировании закрытых зубчатых передач типа редукторных принимают зна-
чения |
H |
по табл. 3.1. |
|
|
Таблица 3.1. Ориентировочные значения коэффициента Hдля зубчатых передач редукторов, работающих
при переменной нагрузке
|
Расположение зубчатых |
|
|
Твердость поверхностей зубьев |
|||||||
|
|
|
|
|
|
|
|
|
|
||
|
колес относительно опор |
|
|
|
|
|
|
|
|
|
|
|
|
|
|
|
НB 350 |
|
>НВ 350 |
||||
|
|
|
|
|
|
|
|
|
|||
|
|
|
|
|
|
|
|
|
|||
|
Симметричное |
|
|
|
|
1,0 - 1,15 |
|
1,05 - 1,25 |
|||
|
Несимметричное |
|
|
|
1,10 - 1,25 |
|
1,15 - 1,35 |
||||
|
Консольное |
|
|
|
1,20 - 1,35 |
|
1,25 - 1,45 |
||||
|
|
|
|
|
|
||||||
|
Меньшие значения |
H |
|
принимают для передач с отно- |
|||||||
|
|
|
|
|
|
|
|
|
|
|
|
|
шением |
bd b / d1 0,4 ; при увеличении |
ba до 0,6 для |
||||||||
|
конcольно расположенных колес |
|
ba |
и до 0,8 при несим- |
|||||||
|
|
|
|
|
|
|
|
|
|
|
|
|
метричном расположении колес cледует принимать большие |
||||||||||
|
из указанных в таблице значений |
|
H . |
|
|
||||||
|
При постоянной нагрузке |
H |
= 1 |
|
|
||||||
|
|
|
|
|
|
|
|
|
|
||
|
|
|
|
||||||||
|
При проектировании редукторов обычно задаются вели- |
||||||||||
чиной ba |
b / aw ; для прямозубых передач принимают ba = |
||||||||||
0,125 - 0,25; для косозубых |
|
ba = 0,25 - 0,40; для шевронных |
|||||||||
|
|
|
|
149 |
|
|
|
|
|
|

ba |
= 0,5 - 1,0. Чтобы вычислить |
bd по выбранному значе- |
|
нию |
ba |
следует воспользоваться равенством |
|
|
|
|
|
d1 |
2a /( u 1) тогда bd b / d1 |
0,5b u 1 / a 0,5 ba u 1 . |
Таблица 3.2. Предел контактной выносливости при базовом числе циклов нагружения
Способы термохи- |
Средняя |
|
H lim b , Н/мм2 |
||
мической обработ- |
твердость по- |
Сталь |
|||
ки зубьев |
верхностей |
|
|
||
|
|
|
|
|
|
1. |
Нормализация |
<HB 350 |
|
2 НВ + 70 |
|
или улучшение |
|
||||
|
Углероди- |
|
|||
|
|
|
|
||
|
|
|
стая и леги- |
|
|
2. |
Объемная закал- |
HRC 38 - 50 |
18 HRC+150 |
||
|
|||||
|
|
|
рованная |
|
|
3. |
Поверхностная |
HRC 40 - 50 |
17 HRC + 200 |
||
|
|||||
закалка |
|
||||
|
|
|
|||
|
|
|
|
|
|
4. |
Цементация и |
>HRC 56 |
Легирован- |
23 HRC |
|
нитроцементация |
|||||
|
|
||||
|
ная |
|
|||
5. |
Азотирование |
HV 550 - 750 |
1050 |
||
|
|||||
|
|
|
|
|
Примечание. Базовое число циклов NHO определяют в зависимости от твердости стали: при НВ < 200 принимают NHO = 107; при твердости HB 200 - 500 используют формулу
N |
H 0 |
T 2,4 |
, где T |
- твердость поверхностей зубьев |
|
|
|
|
Динамический коэффициент H, определяют в зависи-
мости от окружной скорости v колес и степени точности их изготовления.
Для прямозубых колес при v до 5 м/с следует назначать 8- ю степень точности по ГОСТ 1643-81; при этом KHv = 1,05 - 1,10.
Для косозубых колес при v до 10 м/с назначают также 8 -ю
150

степень точности, |
H = 1,07 - 1,05. При v от 10 до 20 м/с и 7- |
й степени точности |
H = 1,05 - 1,1. Меньшие из указанных |
значений относятся к колесам с твердостями поверхностей зубьев до НВ 350, большие - при твердостях свыше НВ 350.
При проектном расчете допускаемое контактное напряже-
ние |
H |
определяют по формуле |
|
|
|
||
|
|
|
|
|
|
|
|
|
|
|
H lim b KHL |
. |
(3.10) |
||
|
|
H |
|
||||
|
|
|
n H |
|
|
|
|
|
|
|
|
|
|
|
|
|
Здесь H lim b - предел контактной выносливости при базо- |
||||||
вом числе циклов. Значения |
H lim b |
указаны в табл. 3.2. |
|
||||
|
|
|
|
|
|
|
Для определения - коэффициента долговечности KHL вы-
числяют эквивалентное число циклов перемены напряжений зубьев (циклов нагружения зубьев) NНE колес по формуле
|
|
NHE 60T |
3 |
( ni |
3 |
|
(3.11) |
|
|
|
|
i, j i, j ), |
|
||||
|
|
|
где ni - частота вращения вала |
|||||
|
|
|
рассчитываемого колеса; |
i , j - до- |
||||
|
|
|
ля времени работы колеса с чис- |
|||||
|
|
|
лом оборотов ni от общего време- |
|||||
|
|
|
ни работы колеса Т, в течение ко- |
|||||
|
|
|
торого передача нагружена мо- |
|||||
Рис. 3.3. График загрузки |
ментом |
Mi , j (принято обозначать |
||||||
так, что |
M i ,1 |
M i ,m ax и далее в |
||||||
передачи для некоторого |
||||||||
числа оборотов |
порядке убывания моментов |
|||||||
|
|
|
Mi , j ); |
i , j |
Mi , j / Mном |
(вели- |
||
чины |
i , j |
приводятся на графиках загрузки передачи, для каж- |
||||||
|
|
|
|
|
|
|
дого числа оборотов). Примерный вид графика загрузки передачи приведен на (рис. 3.3)); M ном - номинальный момент нагрузки на передачу.
151
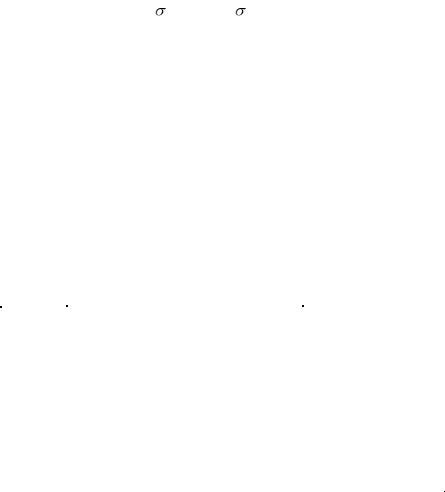
Следует помнить, что для всех колес передачи графики загрузки одинаковы, поскольку отношения моментов на валах передачи определяются передаточными числами.
Таблица 3.3. Механические свойства сталей, применяемых для изготовления зубчатых колес
Марка |
|
Диаметр |
|
Предел |
|
Предел |
Твердость |
Термо- |
||
|
заготов- |
|
прочности |
|
текучести |
НВ |
об- |
|||
стали |
|
|
|
|||||||
|
ки, |
|
B , МПа |
|
T , МПа |
(средняя) |
работка |
|||
|
|
|
|
|||||||
45 |
|
100-500 |
|
570 |
|
|
290 |
|
190 |
Нормли- |
|
|
|
|
|
зация |
|||||
|
|
|
|
|
|
|
|
|
|
|
|
|
До 90 |
|
780 |
|
|
440 |
|
230 |
|
45 |
|
90 - 120 |
|
730 |
|
|
390 |
|
210 |
|
|
|
Св. 130 |
|
690 |
|
|
340 |
|
200 |
|
30ХГС |
|
До 140 |
|
1020 - 930 |
|
840 - 740 |
260 - 250 |
|
||
|
Св. 140 |
|
|
|
||||||
|
|
|
|
|
|
|
|
|
Улучше- |
|
|
|
До 120 |
|
930 |
|
|
690 |
|
270 |
|
|
|
|
|
|
|
ние |
||||
40Х |
|
120 - 160 |
|
880 |
|
|
590 |
|
260 |
|
|
|
|
|
|
|
|||||
|
|
Св. 160 |
|
830 |
|
|
540 |
|
245 |
|
|
|
До 150 |
|
930 |
|
|
690 |
|
280 |
|
40ХН |
140 - 180 |
|
880 |
|
|
590 |
|
265 |
|
|
|
|
Св. 180 |
|
835 |
|
|
540 |
|
250 |
|
40Л |
|
- |
|
520 |
|
|
290 |
|
160 |
Нормли- |
45Л |
|
|
540 |
|
|
310 |
|
180 |
зация |
|
|
|
|
|
|
|
|||||
35ГЛ |
|
- |
|
590 |
|
|
340 |
|
190 |
Улуч- |
35ХГСЛ |
|
790 |
|
|
590 |
|
220 |
шение |
||
|
|
|
|
|
||||||
|
Марка стали |
|
Твердость |
|
Термообработка |
|||||
|
|
|
|
|
|
|
НRC |
|
|
|
ЗОХГС, 35ХМ, 40Х, 40ХН |
|
45 - 55 |
|
Закалка |
||||||
12ХНЗА, 18Х2Н4МА, 20ХМ |
|
50 - 63 |
Цементация и закалка |
|||||||
20ХГМ, 25ХГТ, ЗОХГТ, 35Х |
|
56 - 63 |
|
Нитроцементация |
||||||
ЗОХ2МЮА, 38Х2Ю, 40Х |
|
56 - 63 |
|
Азотирование |
||||||
40Х, 40ХН, 35ХМ |
|
45 - 63 |
Поверхностная закал- |
|||||||
|
|
|
|
|
|
|
|
|
ка ТВЧ |
|
|
|
|
|
152 |
|
|
|

Если частоты вращения валов передачи во время работы почти постоянны, а нагрузка на передачу переменна, то эквивалентное число циклов нагружения определяется по формуле
N |
HE |
60Tn |
3 ( |
3 |
) |
j |
, |
(3.12) |
|
|
|
j |
|
|
|
где n - частота вращения вала рассчитываемого колеса; j - до-
ля времени от общего времени работы передачи Т, в течение которого передача нагружена моментом M j (принято считать
M1 M max ); j M j / Mном ).
Если эквивалентное число циклов нагружения зуба колеса больше базового, то принимают KHL = 1. Именно такой случай типичен для большинства курсовых проектов. В противном
случае, когда NHE меньше NНO, вычисляют KHL |
по формуле |
|||||||
|
|
|
|
|
|
|
|
|
K |
HL |
3 N |
HO |
/ N |
HE |
. |
(3.13) |
|
|
|
|
|
|
|
Если при расчете колее из нормализованной или улучшенной стали получается KHL больше 2,6, то принимают KHL = 2,6; для колее из закаленной стали KHL 1,8 .
Коэффициент безопасности n H для колес из нормализованной и улучшенной стали, а также при объемной закалке принимают n H = 1,1 - 1,2; при поверхностном упрочнении зубьев n H = 1,24 - 1,3.
Для выбора материалов шестерни и колеса можно руководствоваться данными, приведенными в табл. 3.3. Рекомендуется назначать для шестерни и колеса сталь одной и той же марки, но обеспечивать соответствующей термообработкой твердость поверхностей зубьев шестерни на 20 - 30 единиц твердости Бринеля выше, чем колеса.
Для косозубых колес расчетное допускаемое контактное напряжение определяют по формуле
153

H 0,45 |
H 1 |
H 2 , |
(3.14) |
где H 1 и
H 2 - допускаемые контактные напряжения соот-
ветственно для шестерни и колеса; после определения этих величин следует проверить выполнение условия
H 1,23 H min , |
(3.15) |
где H min - минимальное из допускаемых напряжений, как
правило, равно |
H 2 . |
Последовательность проектного расчета
1.Назначают материалы зубчатых колес передачи в соответствии с изложенными выше рекомендациями и данными таблицы 3.3.
2.Определяют базовые NH 0 и эквивалентные NHE числа
циклов нагружения, коэффициенты долговечности колес
KHL .
3.Определяют допускаемые напряжения H 1 и
H 2 .
4.Определяют допускаемое напряжение H .
5.По исходным данным на проектирование определяют M1 или M 2 . Передаточное число и равно отношению чисел
зубьев колеса и шестерни; так как z2 и z1 в начале расчета еще не установлены, то принимают
u |
|
z2 |
|
1 |
|
n1 |
, |
(3.16) |
|
z1 |
2 |
|
n2 |
||||
|
|
|
|
|
||||
где угловые скорости |
1 , |
|
2 или частоты вращения n1 , n2 |
|||||
обусловлены заданием. |
|
|
|
|
|
|
|
|
6. Если условиями проектирования предписано обеспечить стандартное значение u , то следует округлить вычисленное
154

значение и до величины, входящей в стандартные ряды, приведенные в табл. 2.5.
7.Первый ряд следует предпочитать второму.
8.Стандартные значения передаточного числа следует рассматривать как номинальные. В дальнейшем при определении значений zl и z2 в результате расчета, производят уточнение фактической величины и. Величина u не должна отличаться от номинального и больше чем на 2,5% при и < 4,5 и больше чем на 4% при и > 4,5.
9.Определяют прочие величины, входящие в правую часть формулы (3.8) или (3.9) соответственно для прямозубых или косозубых передач.
10. Коэффициенты ширины зубчатого венца колеса ba реко-
мендуется выбирать из ряда: 0,100; 0,125; 0,160; 0,250; 0,315;
0,400; 0,500; 0,630; 0,800; 1,00; 1,25.
11. Для прямозубых колес рекомендуется ограничивать ba < 0,25, иначе увеличивается степень концентрации нагрузки по длине зуба; для косозубых предпочтительно принимать ba = 0,25 до 0,63, проверяя (при ba < 0,4) выполнение условия
ba |
2,5mn |
, |
aw sin |
|
|
|
|
где mn - нормальный модуль зацепления; - угол наклона оси зуба по делительному цилиндру.
12. Определяют межосевое расстояние aw по одной из формул
(3.8) или (3.9)] и округляют его до ближайшего значения стандартного значения (в мм) из следующих рядов:
ряд 1: |
40 |
50 |
63 |
80 |
100 |
125 |
160 |
200 |
250 |
||||||
|
315 |
400 |
500 |
|
630 |
|
800 |
|
1000; |
|
|
|
|
||
ряд 2: |
71 |
90 |
112 |
|
140 |
180 |
224 |
280 |
355 |
450 |
|||||
|
|
|
|
|
|
|
|
155 |
|
|
|
|
|
|

560 710 900.
13.В стандарте указаны значения aw до 2500 мм.
14.Выбирают модуль колес из интервала (0,01 - 0,02) aw, так чтобы его значение совпадало с стандартным значением (в мм) из одного из следующих рядов:
ряд 1: 1 |
1,5 |
2 |
2,5 |
3 |
4 |
5 |
6 |
8 |
10 |
12 |
16 |
20; |
ряд 2: 1,25 1,375 1,75 2,25 2,75 3,5 4,5 5,5 7 9 11 14 18;
(в стандарте регламентированы модули от 0,5 до 100 мм).
15. Для косозубых колес стандартным модулем считают нормальный тп, который равен окружному (торцовому) модулю. Для шевронных колес стандартным может быть как нормальный модуль тт так и окружной (торцовый) mt. Связь модулей задается формулой
|
mn |
mt cos . |
(3.17) |
16. |
Определяют суммарное число зубьев колес z |
z1 z2 . |
|
17. |
Для колес со стандартным окружным модулем (прямозу- |
||
бых, косозубых и шевронных) |
|
||
|
z |
2aw / mt . |
(3.18) |
18. Угол наклона линии зуба принимают для косозубых ко-
лес в интервале = 8 - 15°, для шевронных |
= 25 - 400 (до |
|||
45°). |
|
|
|
|
19. Определяют числа зубьев шестерни и колеса: |
||||
z1 |
z |
|
, z2 z z1 . |
(3.19) |
|
|
|||
u |
|
|||
|
1 |
|
Возможен иной вариант расчета чисел зубьев: задаются числом зубьев шестерни - оно должно быть не меньше
минимального числа зубьев zmin , определенного из усло-
156

вия отсутствия подрезания; для прямозубых колес
zmin 17 , для косозубых и шевронных zmin 17 cos3 . Затем определяют mt 2aw /( z1 z2 ) для прямозубых и шевронных колес или
2a cos mt z1 z2
для косозубых колес, округляют полученные значения до стандартных значений и далее ведут расчет так же, как описано выше.
По округленным значениям z1 и z2 уточняют передаточное число
u z2 / z1 .
Расхождение с принятым ранее номинальным передаточным числом не должно превышать 2,5% при и < 4,5 и 4% при и > 4,5.
После всех указанных округлений необходимо проверить межосевое расстояние: для прямозубых и шевронных колес со стандартным окружным модулем
aw 0,5 z1 z2 mt . |
(3.20) |
Обычно эта проверка подтверждает отсутствие расхождения.
Для косозубых и шевронных колес с нормальным стандартным модулем
mn |
|
aw 0,5 z1 z2 cos . |
(3.21) |
При проверке может обнаружиться несоответствие полученного результата с ранее принятым, стандартным значением aw . В этом случае надо устранить расхождение
157

изменением угла , определив его по формуле:
cos |
0,5 z1 z2 mn / a . |
(3.22) |
Вычисление cos надо выполнять точностью до пяти значащих цифр, чтобы угол
можно было определить с точностью до угловых секунд.
Затем рекомендуется проверить расчеты, определив с точностью до сотых долей миллиметра делительные диаметры зубчатых колес
d1 z1 |
mn |
, d2 |
z2 |
mn |
|
, |
(3.23) |
cos |
cos |
|
|||||
и убедиться, что условие 0,5( d1 |
d2 ) |
aw выполняется. |
Наличие существенного расхождения величин правой и левой частей этого равенства свидетельствует об ошибке в вычислениях.
Кроме того, необходимо определить окружную скорость зубьев, равную скорости точек зубьев, проходящих через полюс зацепления
v n1d1 / 30 n2d2 / 30 , |
(3.24) |
где диаметры d1 и d2 должны быть выражены в метрах, а частоты вращения n1 и n2 колес в об/мин.
§ 3.3. Проверочный расчет цилиндрических передач на контактную выносливость
После определения окончательных размеров шестерни и колеса необходимо проверить величины расчетных контактных напряжений по формуле (3.10), так как после округлений и уточнений размеров колес передачи допускаемое напряжение H и коэффициенты ZM, ZH, Z и KH можно определить
158