
1495
.pdfНа кинетику процесса растворения оксида кальция в воде влияют также примеси исходного сырья. Так, сесквиоксид железа, диоксид титана и сесквиоксид хрома замедляют процесс гидратации, а добав ка 5% оксида магния снижает скорость реакции на 33%. Существен но замедляет процесс и сульфат кальция. Ускоряет процесс присутст вие в системе электролитов (рис. 1.36).
Согласно технологической схеме (рис. 1.37), процесс растворения оксида кальция с получением водной суспензии оксида и гидроксида кальция осуществляют следующим образом.
Исходный оксид кальция (известь) из бункера 1 дозируется бара банным питателем 2 во вращающийся барабанный гаситель 3, в ко торый непрерывно поступает подогретая в эжекционном водоподог- ревателе-конденсаторе 4 вода (обычно для этого используют очищенную хозяйственно-фекальную воду, осветленную часть дистиллерной жидкости, маточные растворы дистилляции слабой жидко сти и слабую известковую суспензию, полученную в процессе помо ла и промывки мелких отходов гашения). Подогретая в конденсаторе 4 вода после смешения в коллекторе подается в гаситель 3 и на про мывку мелких отходов гашения в шаровую мельницу 6. В конце га сителя 3 смонтирован барабан 7, который имеет вытяжную трубу 8 для выхода паров из системы.
Выходящая из гасителя 3 суспензия распределяется в сортировоч ном барабане 7 на три фракции: крепкую известковую суспензию, содержащую инертные примеси и недиспергировавшиеся зерна окси да кальция, мелкие и крупные отходы гашения. Крепкая суспензия оксида кальция проходит через сито первой по ходу материала сек ции сортировочного барабана 7 и после тонкой очистки на вибраци-
Рис. 1.36. Кинетика процесса седиментации гидроксида кальция с применением электролитов:
7 — 1%-ный раствор NaCl; 2 — Н20; 2 — дистиллерная жидкость, очищенная от SOj~; 4 — 1%-ный раствор Na2S04; 5 — дистиллерная жидкость
Рис. 1.37. Схема процесса приготовления суспензии оксида и гидроксида кальция:
/ — бункер; 2 — барабанный |
питатель; 3 — гаситель оксида кальция; 4 — эжекционный водоподог- |
||
реватель-конденсатор; 5 — коллектор горячей воды; 6 — шаровая мельница; 7 — сортировочный |
ба |
||
рабан; 8 — вытяжная труба; |
9 — вибрационные сита; 10 — сборник; 11 — насос; 12 — ленточный |
||
конвейер; 13 — скребковый транспортер; |
14 — односпиральный классификатор; 15 — сборник |
сла |
|
бой |
известковой |
суспензии; 16 — сборник шлама |
|
онном сите 9 поступает в сборник 10, оборудованный мешалкой, от куда насосом 11 перекачивается в отделение дистилляции. Твердый остаток поступает во вторую секцию вибрационного сита 9, где его промывают подаваемой в сортировочный барабан 7 горячей водой. Частицы оксида кальция менее 15 мм (мелкие отходы гашения) про ходят сквозь сито 9, а крупные куски недокала и топлива, отмытые от известковой суспензии, направляются ленточным конвейером 12 на склад сырья и топлива.
Мелкие отходы гашения отделяют на вибросите 9 от слабой из вестковой суспензии и по распределительному желобу подают в сборник, снабженный перемешивающим устройством, затем скребко вым транспортером 13 направляют в шаровую мельницу 6 мокрого помола. Для разбавления шлама используют горячую воду или дистиллерную жидкость. Слабую известковую суспензию, получаемую в процессе размола, гашения и диспергирования оксида кальция, очи щают на классификаторах 14 и подают через распределительный же лоб в сборник 15. Шлам из классификатора 14 в сборнике шлама 16
72
репульпируют дистиллерной жидкостью и откачивают на стадию пе рекачки промстоков или на фильтрацию, где смешивают со шламом после дистилляции.
В табл. 1.14 приведен аналитический состав водной суспензии смеси оксида и гидроксида кальция.
Т а б л и ц а 1.14. Аналитический состав водной суспензии смеси оксида и
гидроксида кальция
|
Суспензия СаО и Са(ОН)2 |
Шлам из классифиКрупные отходы, % |
|||
|
% (масс.) |
н.д. |
кагора, % (масс.) |
(масс.) |
|
СаО |
(акт) |
23,5 |
215,0 |
25,0 |
2,0 |
СаО |
(неакт) |
1,5 |
13,7 |
14,0 |
7,0 |
M gO |
0,3 |
3,8 |
0,8 |
0,3 |
|
СаСОз |
2,0 |
11,8 |
23,2 |
83,0 |
|
R20 3 |
0,2 |
— |
3,0 |
1,0 |
|
Si02 + Н.О/ |
1,7 |
— |
4,0 |
4,5 |
|
СаС12 |
2,2 |
10,1 |
— |
— |
|
NaCl |
U |
4,8 |
— |
— |
|
Н20 |
67,5 |
952,1 |
30,0 |
1,0 |
|
*Н.О.— нерастворимый |
остаток. |
|
|
|
|
А м м о н и з а ц и я |
р а с с о л а . |
Исходное сырье — рассол до |
насыщения диоксидом углерода в карбонизационных колоннах в от делении адсорбции насыщают аммиаком и частично диоксидом угле рода из парогазовой смеси отделений дистилляции, карбонизации и газовоздушной смеси вакуум-фильтров.
Основной задачей отделения абсорбции является получение ам монизированного рассола с передачей его в отделение карбонизации
рассолов следующего |
состава: |
|
Содержание, |
н.д.: |
|
аммиака................. |
100—106 |
|
хлорид-ионов........ |
не менее 89 |
|
Температура, |
°С...... |
28—32 |
Кроме того, отделение адсорбции должно обеспечивать поглоще ние аммиака из выхлопных газов производства карбоната натрия.
Для насыщения рассола применяют парогазовую смесь, поступаю щую из отделения дистилляции (свыше 80% от всей массы) и содержа щую аммиак и пары воды. Количество последних зависит от темпера туры смеси. Обычно в производстве температуру смеси поддерживают не ниже 58° С. При более низких температурах происходит процесс
73
кристаллизации карбонатов аммония NH4HCO3 и (NH^CCb, образую' щихся по схеме:
NH3 + Н20 + C02^NH4HC03
2NH3 + Н20 + C02-)-(NH4)2C03
Однако в опубликованных в последние годы работах утверждают, что основной реакцией, протекающей в процессе аммонизации, счи тается реакция аммиака с диоксидом углерода по уравнению
2NH3 + С02 <± NH2COONH4
Образование карбамата аммония создает более благоприятные условия в процессе абсорбции аммиака и диоксида углерода в резу льтате снижения равновесного давления NH3 и С 02 над раствором. Растворы охлаждают, так как процесс поглощения аммиака рассолом сопровождается выделением теплоты.
Процесс абсорбции диоксида идет значительно медленнее, чем аммиака. В связи с этим аппаратуру рассчитывают так, чтобы обес печивать поглощение заданного количества аммиака и максимально возможного количества диоксида углерода, которое кроме темпера турного режима определяется присутствием аммиака в рассоле по всей поверхности аппаратов.
Согласно схеме процесса абсорбции, приведенной на рис. 1.38, очищенный рассол из отделения рассолоочистки поступает в напорную емкость 3, откуда самотеком поступает в аппараты абсорбции. Около 75—80% рассола из емкости 3 поступает в промыватель воздуха фильтров (ПВФЛ) 4, где поглощается аммиак из воздуха, проходящего через фильтрующую ткань вакуум-фильтров и содержащего около 0,5— 1,0% (масс.) аммиака. Из ПВФЛ рассол поступает во второй про мыватель газа колонн (ПГКЛ-2) 7, где абсорбируется аммиак из отхо дящих газов отделения карбонизации, содержащих до 10% NH3. Ос тальные 20—25% очищенного рассола из напорной емкости 3 поступают в промыватель газа абсорбции (ПГАБ) 1, в котором абсор бируется аммиак из отходящих газов отделения абсорбции, содержа щих до 5% NH3. Одновременно поглощается некоторое количество ди оксида углерода, содержащегося в выхлопных газах. Газ из ПВФЛ поступает на вакуум-насос 5, создающий разрежение на вакуум-фильт рах, и выбрасывается в атмосферу. Газ из ПГАБ, содержащий не менее 75% С 02, поступает в вакуум-насос 2, откуда он передается на смеше ние с диоксидом углерода из содовых печей (в ПГСП), а затем — на карбонизацию. Выхлопные же газы из ПГКЛ-2 выбрасываются в атмо сферу. Газ из ПГАБ, содержащий не менее 75% С02, вакуум-насосом 74
Рис. 1.38. Схема процесса абсорбции:
^ — промыватель газа абсорбции; 2, 5 — вакуум-насосы; 3 — напорная емкость; 4 — промываггель воздуха фильтров; б — холодильник газа дистилляции; 7 — второй промыватель газа колонн; ^ — сепаратор-брызгоуловитель; 9 — сборник аммонизированного рассола; 10, 12 — оросительные холодильники; 11 — постамент-резервуар; 13 — второй абсорбер; 14 — первый абсорбер
передается на смешение с диоксидом углерода содовых печей (6 ПГСЩ а затем на процесс карбонизации. Выхлопные газы из ППЩ-2 выбрасываются в атмосферу. /
Рассол после промывки выхлопных газов из ПГКЛ-2 и ПГАБ по ступает на основную операцию — абсорбцию аммиака из газа дистил ляции, осуществляемую в две ступени — в первом абсорбере (АБ- Г) 14 н во втором абсорбере (АБ-2) 13. Две ступени абсорбции диктуются необходимостью в промежуточном охлаждении рассола, нагревающе гося в процессах растворения и взаимодействия аммиака с диоксидом углерода в конденсацией водяного пара, поступающего с газом дистил ляции. После первого абсорбера нагретый до 60—65° С рассол охлаж дают до 28—32° С в оросительном холодильнике 12, после чего он по ступает во второй абсорбер, где также нагревается до 65° С, и поэтому, до поступления в сборник аммонизированного рассола (САР), вторич но охлаждается в оросительном холодильнике 10. С целью обеспече ния самотека рассола на оросительный холодильник второй абсорбер и стоящие на нем аппараты расположены на постаменте-резервуаре 11.
Газ из отделения дистилляции охлаждается и осушается в холо дильнике газа дистилляции (ХГДС) 6 охлаждающей водой, а затем, пройдя сепаратор-брызгруловитель 8, противотоком к рассолу прохо дит последовательно второй и первый абсорберы, где аммиак погло щается практически полностью. Вместе с аммиаком из газа поглоща ется значительная часть диоксида углерода. Неабсорбированная часть газов идет в ПГАБ 1. В процессе охлаждения газа дистилляции в XIДС водяные газы конденсируются, образуя конденсат, содержащий до 150—200 н.д. аммиака и диоксида углерода. Аммиак из таких жидкостей, называемых «слабыми», регенерирует на отдельной уста новке. Получаемый же при этом газ, содержащий аммиак, диоксид углерода н водяные пары, после охлаждения до 58—60° С поступает в первый абсорбер.
Во всех аппаратах отделения абсорбции жидкости и газы дви жутся по принципу противотока, что обеспечивает наиболее полное
извлечение абсорбируемых компонентов из газа. |
|
|
К а р б о н и з а ц и я |
а м м о н и з и р о в а н н о г о |
р а с с о - |
л а. Процесс насыщения |
аммонизированного рассола диоксидом угле |
рода, в результате которого образуется гидрокарбонат натрия, является основным процессом в производстве карбоната натрия. Образование гидрокарбоиата натрия идет по реакции
NaCI + NH, + С 02 + Н20 £ NaHCOj + NH4CI
Процесс ведут ступенчато. В начале процесса аммонизированный рассол, частично обработанный в отделении абсорбции диоксидом углерода, обрабатывают отходящим из известковых печей газом в ко-
76
лонне предварительной карбонизации (КЛПК), затем в первом промывателе газа колонн (ПГКЛ-1) — газами, отходящими из осадитель ных колонн, и, наконец, в осадительных колоннах (КЛ), в нижнюю часть которых вводят смешанный газ (65—75% С02), а в среднюю часть — газ известково-обжигательных печей.
На первой стадии карбонизации большая часть диоксида углерода реагирует с аммиаком:
2Ш 3 + С02 -> NH2COONH4
Образующийся карбамат аммония гидролизуется
NH2COONH4 + Н20 NH4HCO3 +NH3
с образованием перенасыщенного по НСО3 раствора. Из пересыщен ного раствора кристаллизуется гидрокарбонат натрия:
NH4HCO3 + NaCl NaHC03 + NH4C1
Отделение карбонизации (рис. 1.39) комплектуется сериями ко лонн. В состав серии входят осадительные карбонизационные колон ны 5, первый промыватель газа колонн 3 и теплообменник 2. Перио дически каждую из осадительных карбонизационных колонн (КЛ) ставят на промывку, тогда она выполняет функции колонны предва рительной карбонизации 1.
Аммонизированный рассол из сборника аммонизированного рас сола (САР) поступает в колонну предварительной карбонизации (КЛПК). Одновременно в колонну подается газ известковых печей, содержащий 38—40% (масс.) С02. В КЛПК параллельно осуществля ется промывка колонны от гидрокарбоната натрия, осаждающегося на внутренних поверхностях аппарата, и предварительная карбониза ция аммонизированного рассола. Из КЛПК раствор, содержащий 55—60 н.д. диоксида углерода с температурой 42—46° С, подается в первый промыватель газа колонн (ПГКЛ-1). Одновременно в промы ватель поступает газ из КЛПК и осадительных колонн. В ПГКЛ-1 улавливается аммиак, отдутый карбонизующим газом из КЛПК. Основное назначение аппарата — более глубокое, чем в КЛ, извлече ние диоксида углерода из карбонизующего газа. Это наравне с повы шением общей степени использования диоксида углерода в процессе способствует снижению выдувания из КЛ аммиака. Более полному выполнению ПГКЛ-1 своих технологических функций способствует снижение температуры жидкости. При этом снижается равновесное давление NH3 и С02 над жидкостью, что повышает эффективность процесса их абсорбции. Поэтому в некоторых технологических схе-
77
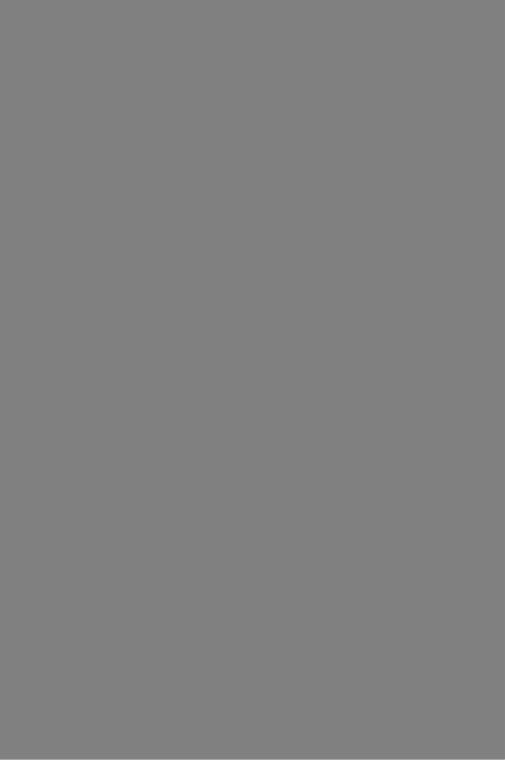
прохода в виде мелких кристаллов через фильтрующую перегородку, а также в результате частичного протекания обратной реакции:
NaHC03 + NH4CI NaCl + NH4HCO3
Потери в процессе фильтрации увеличиваются при повышении температуры промывной воды выше 45° С и ее количества, а также при нарушении целостности фильтрующей перегородки. В табл. 1.15 приведены данные по зависимости выхода карбоната натрия, количе ства испаряемой влаги и расхода теплоты на стадии кальцинации от содержания влаги в гидрокарбонате натрия.
Т а б л и ц а 1.15. Зависимость показателей |
работы |
отделения кальцинации от |
|||||
содержания влаги |
в гидрокарбонате |
натрия |
после <шльтрации |
||||
|
Количество удаляемой |
Относительный расход |
Выход карбоната на |
||||
|
тепла для испарения |
трия* из 100 кг влаж |
|||||
Содержание влаги, % |
влаги, |
кг на 100 кг го |
|||||
воды на стадии кальци |
ного гидрокарбоната |
||||||
|
товой продукции |
|
нации, % |
натрия |
|||
|
|
|
|
||||
22,23 |
|
45,0 |
|
139,7 |
|
49 |
|
20,75 |
|
41,3 |
|
126,1 |
|
50 |
|
19,16 |
|
37,5 |
|
114,7 |
|
51 |
|
17,58 |
|
33,8 |
|
100,0 |
52 |
||
15,99 |
|
30,2 |
|
91,7 |
|
53 |
|
14,31 |
|
26,5 |
|
80,3 |
|
54 |
*Из 100 кг влажного гидрокарбоната натрия теоретически максимальный выход карбоната на трия— 63 кг.
Д и с т и л л я ц и я а м м и а к а и д и о к с и д а у г л е р о д а . В отделении дистилляции карбоната натрия производится полное отде ление аммиака и диоксида углерода из маточного раствора и возвраще ние их в отделение абсорбции. При этом содержание аммиака должно быть 51—53% (масс.), диоксида углерода — 26—28% (масс.). Темпера тура парогазовой смеси поддерживается в пределах 58—60° С.
В процессе дистилляции протекают реакции разложения карбо натных солей аммония за счет нагревания растворов и реакции раз ложения связанного аммония при взаимодействии его с суспензией гидроксида кальция. Образующиеся аммиак и диоксид углерода вы деляют отгонкой из раствора при повышении его температуры.
Процесс десорбции из фильтровой жидкости осуществляют в дистилляционной колонне, состоящей из дистиллера (ДС), теплообменни ка дистилляции (ТДС) и конденсатора-холодильника газа дистилляции (КХДС). Обычно нагрев ведется паром. При 35—40° С начинается раз ложение гидрокарбоната аммония и выделение диоксида углерода:
NH4HC03->NH3 + С02 + Н20
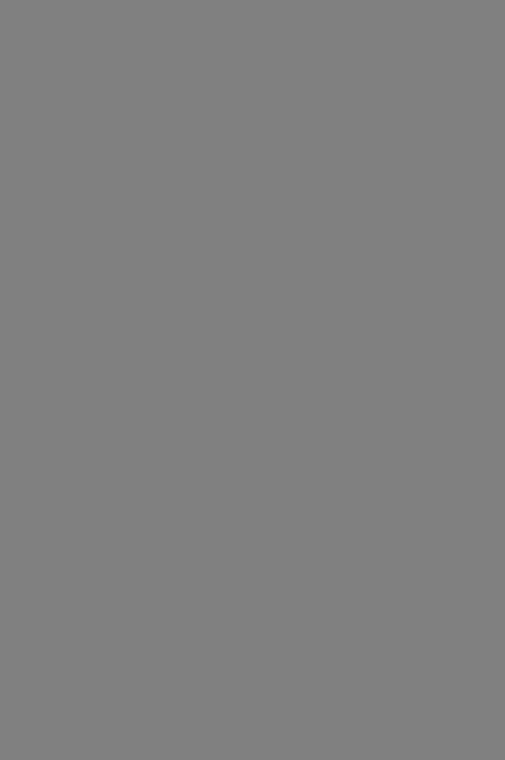