
1495
.pdfНа станции карбонизации аммонизированный рассол из сборников 20 центробежным насосом 21 подается в колонну предварительной кар бонизации 24. В нижнюю часть этой колонны компрессором 31 подает ся охлажденный до 30° С и очищенный в электрофильтре 83 диоксид углерода известково-обжигательных печей 89, содержащий 37—39% СС>2. Процесс карбонизации проводят до содержания в растворе 51—53 н.д. СО*'. Температура жидкости при этом достигает 39—40° С.
Выходящий из колонны предварительной карбонизации 24 рас твор самотеком поступает в верхнюю часть первого промывателя га за колонн 25. Аппарат представляет собой заполненный коксом скруббер. В нижнюю часть аппарата поступают хвостовые газы из осадительных карбонизационных колонн 28 с содержанием 8— 10% СОг. Газ в промывателе 25 движется вверх навстречу раствору, отда вая ему часть содержащегося диоксида углерода. После первого про мывателя газа колонн 25 в газе остается 3—4% СОг и вместе с га зом из колонн предварительной карбонизации 24 он поступает на окончательную промывку свежим очищенным рассолом во второй промыватель газа колонн 5.
После этого газ с содержанием 2—3% СОг выбрасывается в ат мосферу.
Раствор из первого промывателя газа колонн 25 с содержанием 58 — 60 н.д. СО*' собирается в сборнике предкарбонизационного рас твора 26, откуда перекачивается центробежным насосом 27 в осади тельные карбонизационные колонны 28. Карбонизационные колонны группируются обычно сериями. В каждую серию входят по четыре осадительных колонны и одна колонна предварительной карбонизации.
Внижнюю часть осадительных карбонизационных колонн пода ется диоксид углерода. При этом газ подается на два входа: в ниж нюю секцию осадительной колонны компрессором 30 подается кон центрированный газ с содержанием 65% СОг, на второй вход (на высоте 7—9м от низа колонны) компрессором 29 подается газ изве стково-обжигательных печей с содержанием 37—39% СОгКонцент рированный газ получается смешением 90%-ного газа содовых печей
и38%-ного газа известково-обжигательных печей.
Внижней части карбонизационных колонн имеется по десять хо лодильных секций, в трубное пространство которых подается охлаж дающая вода, благодаря чему температура выходящего из осадитель
ных колонн раствора снижается до 26—27° С.
Воду на охлаждение подают двумя параллельными потоками в первую и вторую (считая снизу) холодильные секции карбонизацион ной колонны. Один поток охлаждающей воды проходит через все не четные холодильные секции, а второй поток — через все четные хо лодильные секции колонны.
Охлажденный раствор осадительных колонн с температурой 26—27° С, содержащий 70—72 н.д. связанного в NH4 CI аммиака, вместе с выпавшим в осадок гидрокарбонатом натрия непрерывно выдавливается из осадительных колонн 28 в мерники колонн 32 и из расположенного под ними корыта 33 самотеком направляется на вра щающиеся барабанные вакуум-фильтры 34.
На вакуум-фильтрах осадок гидрокарбоната натрия отделяется от маточного раствора и отмывается от хлоридов натрия и аммония. Процесс промывки производится слабым раствором, поступающим из промывателя газа содовых печей 39 в напорную емкость 35, а от туда в промывные устройства вакуум-фильтров. Вакуум на фильтре поддерживается вакуум-насосом.
Фильтровый раствор отделяется от воздуха в сепараторе филь тров и поступает по U-образной трубе в сборник 38, откуда он пода ется на стадию регенерации аммиака. Воздух, отделенный в сепара торе фильтра от маточного раствора, проходит через промыватель воздуха фильтров 7, в которых свежий очищенный рассол улавливает из него аммиак. Из промывателя 7 воздух отсасывается вакуум-насо сом 12 и выбрасывается в атмосферу.
Сырой гидрокарбонат натрия с вакуум-фильтров подается скреб ковыми транспортерами 36 и 64 в вертикальный смеситель 65, рас положенный непосредственно над загрузочными устройствами враща ющихся содовых печей 66. Из вертикального смесителя 65 сырой гидрокарбонат натрия поступает в барабанный ячейковый питатель содовых печей, снабженный метательной лопаткой, вращающейся со скоростью 200 об/мин. Этой лопаткой гидрокарбонат натрия забрасы вается внутрь барабана содовой печи на глубину 6—9 м и смешива ется с находящимся в барабане карбонатом натрия. Барабанная печь вращается со скоростью 4— 5 об/мин. Под передней частью содовой печи (со стороны загрузки гидрокарбоната) расположена топка, в ко торой сжигается топливо. Топочные газы омывают снаружи барабан содовой печи, имеющей обмуровку.
Образующийся в процессе разложения гидрокарбоната натрия в печи карбонат натрия специальными разгрузочными ковшами и вы
грузочным шнеком выводится из содовой печи |
с температурой |
140— 170° С, поступает в собирающий шнековый |
транспортер 62 и |
подается в элеватор 61, а затем в последующие механизмы, транс портирующие его на склад готовой продукции.
Выделяющиеся в процессе разложения гидрокарбоната в содовой печи газы, содержащие диоксид углерода, водяные пары, а также не значительное количество аммиака, удаляются из передней части ба рабанной печи и поступают в циклон 63, в котором улавливается увлеченная газами пыль карбоната натрия. Осевшая в циклоне пыль карбоната натрия расположенными внутри циклона рамной мешалкой
94
и гребками передвигается к выгрузочному отверстию на дне цикло на, закрытому сигнальным клапаном. С приближением гребков к от верстию клапан автоматически открывается, и пыль карбоната натрия по течке возвращается в содовую печь.
Выходящий из циклонов газ поступает в коллектор газа содовых печей, а оттуда в холодильник газа содовых печей 41. С целью лик видации процесса забивания коллектора частично уносимой из цик лона пылью карбоната натрия его орошают слабым раствором с по мощью специальных брызгальных устройств. Раствор подается центробежным насосом 43 из сборника 42, расположенного под хо лодильником газа содовых печей 41.
В холодильнике газа содовых печей 41 газ движется в межтруб ном пространстве сверху вниз. Охлаждающая вода поступает в виде двух параллельных потоков и движется по трубам снизу вверх. С це лью очистки труб холодильника от оседающей на них пыли карбона та натрия и повышения коэффициента теплопередачи межтрубное пространство холодильника орошается слабым раствором карбоната натрия, подаваемым центробежным насосом 43 из сборника 42. Оро шающая жидкость в смеси с конденсатом, образующимся в холоди льнике в результате конденсации водяных паров, возвращается в сборник 42. Собирающийся в сборнике избыток слабых растворов центробежным насосом 43 перекачивается на станцию переработки слабых растворов. В холодильник газа содовых печей 41 подается также газ с концентрацией до 70% СОг, отсасываемый вакуум-насо сом 11 из промывателя газа абсорбции 9.
Завершающая очистка газа содовых печей от пыли карбоната на трия и аммиака производится в промывателе газа содовых печей 39, в нижнюю часть которого поступает газ из холодильника 41. Промыватель газа содовых печей 39 представляет собой скруббер с насад кой, орошаемой водой или слабыми растворами, содержащими кар бонат натрия, из которых аммиак отогнан на станции переработки слабых растворов.
Слабые растворы, содержащие карбонат натрия, направляются из промывателя газа содовых печей 39 в напорную емкость 35 для про мывки гидрокарбоната натрия на вакуум-фильтрах.
После промывателя газа содовых печей 39 газ смешивается с расчетным количеством газа известково-обжигательных печей и по ступает на компрессор 30, которым он нагнетается в нижнюю часть осадительных карбонизационных колонн 28.
Фильтровая жидкость из сборника 38 центробежным насосом 37 перекачивается в напорную емкость фильтровой жидкости 51. Для под держания постоянного уровня в напорном сборнике последний снаб жен поплавковым регулятором 50. Из напорного сборника фильтровая
95
жидкость поступает в конденсатор дистилляции 52. Поток жидкости в конденсаторе регулируется с помощью ограничительной шайбы.
Далее фильтровая жидкость поступает в трубное пространство верхней теплообменной секции конденсатора 52 и последовательно проходит через все теплообменные секции. Поступающий в конденса тор из теплообменника дистилляции 54 газ движется в межтрубном пространстве конденсатора дистилляции снизу вверх противотоком к фильтровой жидкости и подогревает ее от 26—21° С до 72—73° С. При этом содержащиеся в фильтровой жидкости карбонатные соли аммония частично разлагаются. Для отделения жидкости от газа, вы делившегося в процессе разложения этих солей, жидкость после каждой теплообменной секции конденсатора дистилляции поступает в специальный газоотделитель 53, разделенный перегородками соот ветственно числу теплообменных секций конденсатора дистилляции.
Газ из газоотделителя 53 присоединяется к основному потоку газа, выходящему из верхней секции конденсатора дистилляции. В конденсаторе дистилляции температура газа снижается с 83—85°С до 70—71° С.
Дальнейшее охлаждение газа производят в холодильнике газа ди стилляции 8, через который газ проходит по межтрубному простран ству. При этом в трубное пространство подается охлаждающая вода, которая проходит через все секции холодильника. Газ охлаждается до 56—58° С и поступает в нижнюю секцию второго абсорбера 16.
Конденсат, образующийся в межтрубном пространстве конденса тора дистилляции 52 и холодильника газа дистилляции 8 с раство рившимися в нем карбонатными солями аммония, выводят из этих аппаратов и направляют на станцию переработки слабых растворов.
Подогретая в конденсаторе дистилляции 52 фильтровая жидкость поступает самотеком в теплообменник дистилляции 54, расположен ный непосредственно под конденсатором дистилляции. Теплообмен ник дистилляции представляет собой аппарат барботажного типа с двенадцатью барботажными тарелками. Газ поступает в нижнюю секцию теплообменника дистилляции из ее смесителя и движется на встречу потоку жидкости.
В этом аппарате происходит дальнейшее разложение карбонатных солей аммония, содержащихся в фильтровой жидкости. При этом температура раствора повышается до 90—92° С.
Из теплообменника дистилляции 54 фильтровая жидкость, осво божденная от карбонатных солей аммония и содержащая аммиак в основном в виде хлорида аммония, поступает самотеком в смеситель дистилляции 59, снабженный мешальным устройством. Насосом 67 через напорную емкость 60 в смесь вводится водная суспензия окси да— гидроксида кальция. Хлорид аммония разлагается, а выделив-
96
шийся при этом аммиак в большей своей части остается растворен ным в жидкости. Часть аммиака переходит в газообразное состояние и присоединяется к потоку газа и пара, проходящему через газовую (верхнюю) часть смесителя дистилляции 59 при движении из дис тиллера 55 в теплообменник дистилляции 54.
Выходящий из нижней части смесителя дистилляции 59 раствор самотеком поступает в верхнюю барботажную секцию дистиллера 55 и проходит сверху вниз через все двенадцать барботажных секций дистиллера. В нижнюю секцию дистиллера 55 пар подается навстречу жидкости, из-за чего происходит полная отгонка аммиака из раствора. Пользуются обычно отработанным паром турбин и компрессоров.
Дистиллерная жидкость, имеющая после отгонки аммиака темпе ратуру 107— 110° С, поступает в испаритель дистилляции 56, в кото ром за счет снижения давления происходит выделение из раствора значительного количества пара, используемого на станции переработ ки разбавленных растворов.
После испарителя 56 дистиллерную жидкость разбавляют водой, подаваемой для снижения температуры растворов непосредственно в трубопровод. После пескоуловителя 57 жидкость насосом 58 удаляют в отброс.
Содержащийся в слабых растворах аммиак также регенерируют и используют в процессе аммонизации рассола. Поскольку в растворах аммиак находится исключительно в виде карбонатных солей, процесс проводят лишь подогревом паром.
Основными источниками слабых растворов являются:
1.Холодильник 41, в котором происходит конденсация водяных паров, содержащихся в газах содовых печей. Образующийся конден сат содержит растворенные карбонаты аммония и натрия.
2.Конденсат дистилляции 52 и холодильник газа дистилляции 8, в котором конденсируются водяные пары, содержащиеся в газе, выходя щем из теплообменника дистилляции 54. Образующийся в этих аппа ратах конденсат содержит растворенные карбонат аммония и аммиак.
Переработка неконцентрированных растворов осуществляется сле дующим образом. Раствор из напорной емкости 46 поступает в труб ное пространство верхней теплообменной секции конденсатора малой дистилляции 47. Подогрев раствора происходит за счет теплоты газа и пара, поступающих из малого дистиллера 48 и движущихся в меж трубном пространстве снизу вверх. Газ из конденсатора малой дис тилляции 47 поступает в расположенный непосредственно над ним холодильник газа малой дистилляции 45. Газ проходит через межт рубное пространство, а в трубное пространство подается охлаждаю щая вода. Охлажденный до 56—58°С газ направляется в третью (сверху) барботажную секцию первого абсорбера 15.
4 Химическая технология |
^ |
неорганических веществ, кн. |
I |
Подогретый в конденсаторе малой дистилляции 47 неконцент рированный раствор поступает самотеком в малый дистиллер 48, представляющий собой скруббер с деревянной хордовой насадкой. В нижнюю часть аппарата навстречу потоку неконцентрированного раствора поступает пар из испарителя дистилляции 56, к которому добавляется отработанный пар от турбин. Под действием этого происходит полное разложение карбонатно-аммонийных солей, со держащихся в неконцентрированных растворах. Освобожденный от аммиака и диоксида углерода раствор поступает в холодильник жидкости 49, в котором он охлаждается водой, а затем центробеж ным насосом 44 направляется в напорную емкость 40, а далее он поступает в промыватель газа содовых печей 39.
Водный раствор оксида — гидроксида кальция, необходимый для регенерации аммиака из фильтровой жидкости, готовят следующим образом. Добытый в карьере известняк или мел подается по подвес ной канатной дороге в бункер известково-обжигательной печи. Сюда же доставляется кокс или антрацит, который добавляется в каждую вагонетку известняка (мела) в количестве 7,5— 10% от массы загру женного в нее сырья. Количество загруженного топлива зависит от влажности исходного карбонатного сырья и от высоты печи. Шихта загружается в известково-обжигательную печь 89 через центральное загрузочное устройство 84, снабженное двойным затвором. Расчетное количество воздуха для горения топлива подается в печь вентилято ром 88. Образующийся в процессе обжига известняка (мела) диоксид углерода (37—39% COj) поступает с температурой 80— 100° С в скрубберную часть электрофильтра 83, заполненную хордовой насад кой и орошаемую водой. При этом газ охлаждается до 30° С и по ступает в электрофильтр для удаления пыли и брызг воды, увлечен ных из скрубберной части фильтра. Выходящий из электрофильтра газ подводится по газовому коллектору к компрессорам, подающим его в карбонизационные колонны.
Выгрузку образующегося оксида кальция (извести) из печи про водят непрерывно с помощью расположенного в нижней части печи вращающегося пода (улиты) 87, кольцевого транспортера 86 и бара банного ячейкового выгружателя 85.
Оксид кальция поступает непосредственно в приемную воронку пластинчатого или ковшового конвейера 82, которым он доставляется в запасные и расходные бункера 81 гасителей извести. Из расходного бункера 81 оксид кальция с помощью лоткового питателя подается в горизонтальный вращающийся гаситель оксида кальция 76. Процесс гидратации (частичной) оксида кальция производится теплой водой, для чего используется отработанная вода, поступающая в напорную емкость 69, снабженную поплавковым регулятором 70. Перед поступ лением в гаситель извести 76 оксида кальция теплая вода из напор-
98
ного сборника дополнительно подогревается в подогревателе 75 за счет теплоты отходящих из гасителя водяных паров. Уровень жидко сти в подогревателе 75 поддерживается поплавковым регулятором 71. Дозировка воды в гаситель оксида кальция производится с помощью регулятора подачи 78.
Образовавшаяся в гасителе водная суспензия оксида — гидроксида кальция отделяется от крупных кусков недопала во вращающемся сите 73, вмонтированном в торце гасителя извести 76. Отделившиеся в сите крупные куски недопала промываются водой и собираются в приемном бункере 72, откуда они выгружаются в вагонетки, доставляющие недопал к известково-обжигательным печам для повторного обжига.
Окончательная очистка водной суспензии оксида — гидроксида кальция производится на вибрационном сите 74, в котором суспензия очищается от песка и мелких непогасившихся кусков оксида каль ция, представляющих собой в основном перепал. Очищенная на виб рационном сите 74 суспензия оксида — гидроксида кальция с кон центрацией СаО 200 н.д. поступает в сборник 68, снабженный вращающейся мешалкой. Из сборника суспензия насосом 67 переда ется в напорную емкость 60, а оттуда в смеситель дистилляции 59.
Отделившиеся на вибрационном сите 74 мелкие отбросы промы вают водой и подают в шаровую мельницу 77 мокрого помола. По лученный в результате помола осадок поступает в сборник 79, снаб женный вращающейся мешалкой, куда параллельно поступает для разбавления осадка отработанная вода из скрубберной части электро фильтра 83. Разбавленный шлам откачивается из сборника 79 насо сом 80 в шламоотстойник.
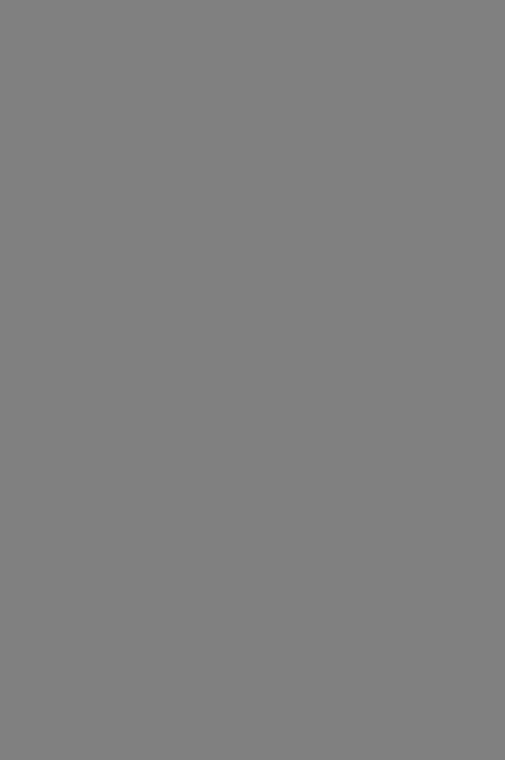
Калий — химически очень активный элемент. Легко взаимодействует с кислородом воздуха, при котором образуются следующие соединения:
4К + 0 2 = 2К20
2К + 0 2 = К20 2
К + 0 2 = К02
При нагревании калия на воздухе он загорается. С водой и раз бавленными кислотами взаимодействует со взрывом и воспламенени ем. В процессе взаимодействия с серной кислотой в зависимости от соотношения исходных реагентов и условий проведения последняя восстанавливается до сероводорода, элементной серы и диоксида се ры, а калий образует различные кислородсодержащие соединения. Азотную кислоту калий разлагает до NO, N20 и N2. При 200—350°С калий реагирует с водородом по следующей схеме:
2К + Н2 = 2КН
Элементный калий в атмосфере фтора воспламеняется, взрывает ся при соприкосновении с бромом и растирании с иодом. Слабо взаимодействует с хлором. С серой, селеном и теллуром калий реа гирует при слабом нагревании:
16К + S8 = 8K2S
2К + Se = K2Se
2К + Те = К2Те
В процессе нагревания с элементным фосфором в атмосфере азо та калий образует соответствующие фосфиды:
12К + Р4 = 4К3Р 8К + 5Р4 = 4К2Р5
С |
графитом при 250—500° С калий образует слоистые соедине |
ния |
состава С8К—С6оК, а с диоксидом углерода реагирует при |
10—30° С. Калий при температуре выше 350—400° С разрушает стекло и платину.
Калий растворяется в жидком аммиаке (35,9 г в 100 мл при -70° С), анилине, этилендиамине, тетрагидрофуране и дигпиме с об разованием растворов с металлической проводимостью. Раствор ка лия в аммиаке имеет темно-синий цвет, а в присутствии платины и
101
следов воды разлагается, образуя KNH2 и Н2. Калий с азотом не реа гирует. В процессе взаимодействия калия с NH4 N3 в жидком аммиа ке образуется азид калия.
Калий не растворяется в жидких литии, магнии, кадмии, цинке, алюминии и галлии и не реагирует с ними. С натрием калий образует интерметаллид KNa2, плавящийся инконгруэнтно при 7°С. С рубидием
ицезием образует твердые растворы, для которых минимальные темпе ратуры плавления составляют соответственно 32,8° С (81,4%, масс. Rb)
и-37,5°С (77,3% Cs). С ртутью калий образует амальгаму, содержа
щую два меркурида — KHg2 и KHg с температурой соответственно 270
и 180° С. С таллием калий образует КТ1 (Тт = 335° С), |
с оло |
вом— K2Sn, KSn, KSn2 и KSn4, со свинцом — КРЬ и фазы |
состава |
К2РЬз, КРЬг и КРЬ4, с сурьмой — КзБЬ и KSb (температура плавления соответственно 812 и 605° С), с висмутом — К3 В1 , K3Bi2 и KBi2 (тем пература плавления соответственно 671, 420 и 553° С).
Калий энергично взаимодействует с оксидами азота, а при высоких температурах — с оксидом и диоксидом углерода. Восстанавливает В2Оз и Si02 соответственно до В и Si, оксиды Al, Hg, Ag, Ni и дру гие — до свободных металлов, сульфаты, сульфиты, нитраты, нитриты, карбонаты и фосфаты металлов — до оксидов или свободных метал лов. Со спиртами калий образует алкоголяты, с галогеналкилами и га-
логенарилами — соответствующие калийалкилы и калийарилы. |
|
В процессе взаимодействия калия с избытком водорода |
при |
300—400° С получают гидрид калия КН, являющийся сильным |
вос |
становителем в неорганических и органических синтезах. КН — бес цветные кристаллы с кубической решеткой (а = 0,570 нм, z = 4, пространственная группа Fm3m); плотность 1,52 г/см3; температура плавления 619° С.
Гидрид калия разлагается при нагревании на элементы, сильный восстановитель. Воспламеняется во влажном воздухе в среде фтора и
хлора. Энергично реагирует с водой: |
|
КН + Н20 = КОН + Н2 |
|
При нагревании с азотом и аммиаком образует KNH2, |
с |
H2S — K2S и Н2, с расплавленной серой — K2S и H2S, с влажным ди |
|
оксидом углерода — НСООК, а с оксидом углерода — НСООК и |
С. |
Металлический калий получают взаимодействием металлического натрия с КОН при 380—450°С или КС1 при 760—890° С. Процесс проводят в атмосфере азота. Взаимодействие жидкого натрия с гид роксидом калия производят противотоком в тарельчатой колонке из никеля. В процессе пары натрия пропускают через расплав КС1. Об разующийся сплав K-Na ректифицируют и получают калий с содер жанием примесей (%, масс.): НО'3 Na и НО"* С1.
102