
1495
.pdfОбразующийся и накапливающийся в системе хлорид магния вы водят из системы с маточными растворами и используют в производ стве металлического магния или других продуктов.
Калимагнезию, полученную конверсией лангбейнита, после обез воживания и сушки выпускают в качестве удобрения, содержащего «31% КгО. Она может быть переработана в сульфат калия по схеме
K2S04 • MgS04 6Н20 + 2КС1 = 2K2S04 + MgCl2 + 6Н20
Переработка лангбейнитовых руд. Приведенная на рис. 2.12 схе ма переработки каинито-лангбейнитовых руд состоит из следующих основных стадий: 1) получение основных продуктов — сульфата ка лия или калимагнезии; 2) флотационное разделение труднораствори мых калийных минералов и галита; 3) регенерация калийных солей
Полиминвральная руда
Рис. 2.12. Принципиальная схема комплексной переработки полиминеральных руд
123
из маточных растворов; 4) получение в качестве полуфабриката ис кусственного карналлита и переработка его в бишофит.
I с т а д и я Исходная руда измельчается до частиц размером 5 мм и поступает на растворение в три последовательно расположен ных горизонтальных растворителя с рамными мешалками по проти- воточно-прямоточной схеме: руда поступает в первый горячий (105— 110° С) раствор — в третий растворитель, в каждом раствори теле руда и раствор передвигаются прямоточно. Твердая фаза из од ного растворителя в другой транспортируется наклонными ковшовы ми элеваторами. Растворитель представляет собой смесь маточного раствора с промывными водами. Перед поступлением в реактор ее подогревают в трубчатых теплообменниках.
В процессе растворения в жидкую фазу переходят легко раство ряющиеся минералы: сильвин, шенит, каинит и карналлит. Не рас творимые в воде полигалит, лангбейнит, галит из последнего раство рителя выводятся на планфильтр. Глинистые шламы в виде тонкодисперсной взвеси выносятся из растворителей с раствором.
Насыщенный раствор первого растворителя отстаивают в отстой- нике-солеотделителе. Образующийся сгущенный солевой шлам на правляют в третий растворитель для повторного выщелачивания. Слив отстойника-солеотделителя отстаивают от глинистого шлама в отстойнике, используя в качестве коагулянта полиакриламид. Сгу щенный глинистый шлам отмывают от солей калия по противоточной схеме промывки и направляют в шламонакопитель.
Отстоенный насыщенный раствор поступает в девятиступенчатую вакуум-кристаллизационную установку, в которой охлаждается от 65 до 32° С. Далее растворы охлаждают до 20° С в шести поверхностных кристаллизаторах, охлаждаемых водой и аммиаком (последний кор пус). В процессе охлаждения раствора происходит кристаллизация шенита. Из последнего корпуса кристаллизатора суспензию кристаллов шенита направляют в сгуститель-солеотделитель, где и осаждается ос новное количество кристаллов шенита. Слив из солеотделителя через дополнительный отстойник выводят на ВКУ, где он подогревается до 45—50° С в поверхностных конденсаторах и разделяется на два пото ка. Первый поток, проходя трубчатые теплообменники, возвращается на растворение руды, а второй направляют на регенерацию калийных солей (III стадия производства).
Сгущенная шенитовая суспензия из солеотделителя и отстойника фильтруется на барабанных вакуум-фильтрах. Полученный продукт сушат и выпускают в качестве калимагнезия или двухстайным разло жением шенита получают сульфат калия.
В последнем случае на первой стадии шенит разлагают в реакто ре водой разбавленным сульфатным раствором, поступающим со вто рой стадии в течение 30—60 мин. При этом получают сульфат калия
124
и концентрированный сульфатный раствор. Его отделяют от шени- то-сульфатной суспензии в сгустителе-солеотделителе, отстойнике и передают на кристаллизацию в ВКУ в смеси с насыщенным раство ром из отделения растворения руды. Сгущенная шенито-сульфатная суспензия в течение 10— 15 мин доразлагается водой на второй ста дии процесса. При этом образуются кристаллы сульфата калия. Кри сталлы освобождают от растворов на барабанных вакуум-фильтрах и направляют на сушку.
II с т а д и я . Нерастворенная часть исходной руды из раствори телей содержит 3,5—4,0% К20. Кроме того, остаток содержит: 17% лангбейнита, 9,2% полигалита, 53,3% галита, 7,4% кизерита, 3,9% каинита, 1,8% ангидрита и 7,3% глины.
С целью дополнительного извлечения калийно-магниевых солей осадок (Ж:Т = 3,5:1) измельчают и подвергают флотации. Во флота ционной машине происходит разделение минеральных составляющих твердой фазы: калийные минералы переходят в пенный продукт, а галит и основная масса глинистого шлама передаются из флотомашины в сгуститель-солеотделитель. Продолжительность процесса флотации составляет 25 мин. После сгущения хвосты обезвоживают на барабанных вакуум-фильтрах и направляют в шламонакопитель.
Пенный продукт после двух перечисток сгущают до соотношения Ж:Т = 1,4-5-1,6, фильтруют и направляют в растворитель, в котором флотационный концентрат растворяется водным раствором сульфата магния. Нерастворившийся полигалитовый остаток после сгущения и фильтрации высушивают в сушилках кипящего слоя и выпускают в виде товарного продукта — калийно-магниевого удобрения, содержа щего до 10— 13% К20.
Насыщенный лангбейнитовый раствор из первого растворителя флотационного концентрата после отделения в отстойнике-осветлите ле глинистых шламов поступает на первую стадию производства кристаллизации шенита.
III с т а д и я . С целью регенерации калийных солей и извлечения хлорида магния, накапливающихся в маточном растворе, все избыточ ные маточные растворы подвергают четырехстадийной вакуум-выпарке с последовательным выделением хлорида натрия и калийно-магниевой соли. Затем растворы нагревают до 95— 100° С и обрабатывают 25%-ным раствором хлорида кальция. При этом ионы SO*' переходят в гипс, осадок которого направляют в шламонакопитель.
IV с т а д и я Растворы из гипсового сгустителя упаривают в аппаратах погружного горения (АПГ) при 120—125° С до их концен трации 31—32% MgCl2. Упаренные растворы охлаждают в поверхно стных кристаллизаторах до 35° С, в которых происходит кристалли зация смеси галита и карналлита. Суспензию сгущают, отделяют
125
смесь на центрифуге, маточные растворы передают в кристаллизато ры, в которых происходит конверсия карналлита в каинит:
KCl MgCb • 6Н20 + MgS04 = КС1 |
MgS04 • 3H20 + MgCl2 + 3H20 |
|||
Слив |
сгустителя — осветленный |
раствор |
карналлита — проходит |
|
четвертую |
стадию |
выпарки при 140—145° С |
до образования плава |
|
бишофита MgCl2 |
6Н20. Плав охлаждают на вальцах и в виде че- |
|||
шуированного продукта направляют |
на склад готовой продукции. |
Существует способ переработки лангбейнитовых руд, богатых хло ридами калия и натрия. Для переработки лангбейнита на сульфат калия исходное сырье измельчается на молотковых дробилках, работающих в замкнутом цикле с вибрационным грохотом, где классифицируется по классу 1,6 мм. Крупный класс репульпируется с холодной водой во вращающемся барабане с целью отмывки галита и обезвоживается в гидроциклоне. Пески гидроциклона смешиваются с классом 1,6 мм и подаются в два последовательно работающих классификатора. Вода для растворения галита подается во второй классификатор, куда посту пает лангбейнит из первого классификатора. Слив первого классифика тора после отделения в гидроциклоне и отстойнике мелких кристаллов сбрасывают. Отмытая руда, выходящая из второго классификатора и содержащая 96—98% лангбейнита, обезвоживается в центрифуге и су шится в барабанных сушилках. Высушенный лангбейнит содержит 22% К20, 18% MgO и не более 2,5% хлора.
Получение сульфата калия из отмытой от хлорида натрия лангбейнитовой руды проводят по схеме
K2S04 2MgS04 + 4КС1t ; 3K2S04 + 2MgCl2
Образующийся хлорид магния выводится из системы в виде кон центрированного раствора в смеси с небольшими количествами хло ридов натрия и калия.
Схема получения сульфата калия из лангбейнита приведена на рис. 2.13, согласно которой измельченная до крупности 0,1 мм лангбейнитовая руда, возвратные смешанные соли и раствор хло рида калия в расчетных количествах вступают в реакцию в каскадно расположенных из пяти взаимосвязанных реакторов 2, осна щенных мешалками. Для поддержания необходимой температуры процесса все реакторы оснащены внешними (водяными) и внут ренними (паровыми) змеевиками. Образующийся в реакторах 2 су льфат калия обезвоживается в центрифугах непрерывного действия 3 и сушится в барабанных вращающихся сушилках 5. Маточные растворы, образующиеся в центрифуге, выпариваются в аппаратах погружного горения 7 до концентрации 67% его первоначальной
126
Рис. 2.13. Схема переработки лангбейнита на сульфат калия:
1 — бункер для лангбейнита; 2 — реактор; 3 — центрифуга; 4 — бункер для сульфата калия; 5 — вращающаяся барабанная сушилка; б — емкость для сульфатного раствора; 7 — аппарат погруж ного горения; 8 — кристаллизатор; 9 — отстойник; 10 — фильтр; 11 — растворитель хлорида калия
массы. Количество испаряемой воды должно быть таким, чтобы в процессе последующего охлаждения раствора до 30° С не наступи ла кристаллизация галита.
В процессе упарки растворов сульфата калия при 70° С и выше происходит кристаллизация лангбейнита и хлорида калия. Горячая суспензия этих солей охлаждается до 30° С в двухкорпусном ваку ум-кристаллизаторе 8. При этом лангбейнит перекристаллизовывается в леонит, а при достаточно высокой концентрации раствора возмож но образование каинита. Выделившиеся в процессе упарки и охлаж дения соли сгущаются в отстойнике Дорра 9, фильтруются на бара банном вакуум-фильтре 10 и направляются на стадию конверсии лангбейнита. Маточные растворы после барабанного вакуум-фильтра направляются в реакторы. По мере накопления хлорида магния в ма точных растворах последние выводятся из системы.
Существует также способ получения сульфата калия восстановле нием лангбейнита. При этом предварительно отмытая от хлорида на трия сырая лангбейнитовая соль смешивается с углем или коксом в барабанном смесителе (92% лангбейнита и 8% угля) и смесь подвер гается термообработке в шахтной печи при 800—900° С:
K2S04 • 2MgS04 + 2С = K2S04 + 2MgO + 2СО + 2S02
Из полученного плава сульфат калия выщелачивают при 95—98° С водой. Оксид магния отделяется на фильтре, а раствор сульфата калия упаривается. Из упаренных растворов выделяют кристаллы.
Сульфат |
калия можно получить из алунита K2S04 • A12(S04)3 • |
4А 1(О Н )з, в |
котором теоретически содержится 23% K2SO4. В про- |
127
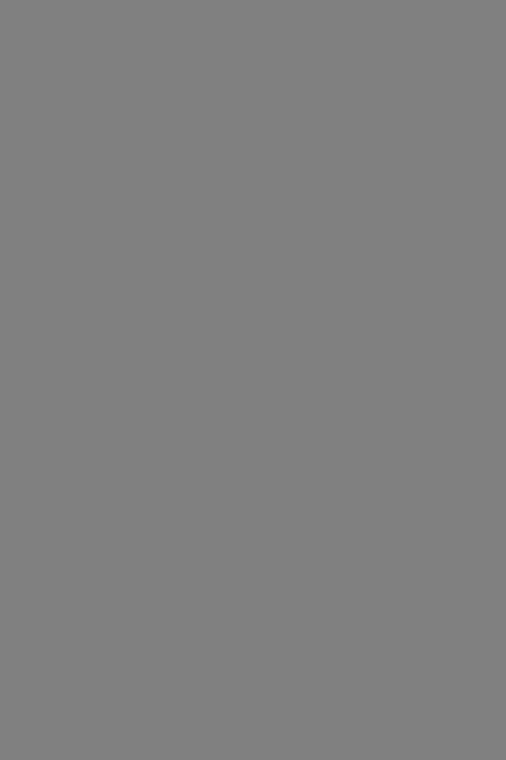
личения индекса по калию разработан способ, сущность которого сводится к следующему: 1) глазерит с пониженным содержанием ка лия обрабатывают раствором А, получаемым при последующем раз ложении его на сульфат калия; 2) получаемый на стадии обогащения глазерита маточный раствор направляется на получение дополнитель ных количеств глазерита.
Глазеритовый раствор (рис. 2.14, точка т) выводится из процесса конверсии. При этом извлечение калия в продукт не превышает 75%. Поэтому с целью повышения выхода калия разработаны варианты утилизации глазеритового раствора: 1) упарка с выделением хлорида натрия; 2) упарка с выделением смеси хлорида натрия и сульфата натрия; 3) упарка глазеритового раствора в смеси с раствором А с выделением из системы смеси солей калия.
На основе изучения диаграммы растворимости взаимной систе мы 2КС1 + Na2SC>4 K2SO4 + 2NaCl при различных температу рах (рис. 2.15) предложен новый метод утилизации глазеритового
раствора. |
Фигуративная |
точка т |
состава глазеритового раствора |
|
при |
0° С |
и ниже находится в поле кристаллизации мирабилита. |
||
При |
этом состав раствора будет изменяться по лучу кристаллиза |
|||
ции |
мирабилита т— 1. |
Мирабилит |
отделяется от раствора и на |
правляется на первую стадию процесса конверсии. Фигуративная
точка 7, |
показывающая состав охлажденного |
раствора, находится |
|||
на изотерме 100° С в поле |
кристаллизации |
галита, |
в результате в |
||
процессе |
упарки раствора в |
твердую фазу |
будет |
переходить хло |
|
рид натрия. Состав жидкой |
фазы при этом |
будет изменяться по |
лучу кристаллизации хлорида натрия до точки 2, где раствор на сыщается хлоридом натрия и глазеритом.
Рис. 2.14. Диаграмма растворимости |
Рис. 2.15. Диаграмма процесса |
солей в системе КС1—Na2S0 4 —Н20 |
переработки глазеритового раствора при |
при 25° С |
охлаждении его до 0° С |
5Химическая технология неорганических веществ, кн. I
Процесс упарки прекращают, раствор отделяют от кристаллов хлорида натрия, а затем раствор охлаждают до 0° С. Поскольку точ ка 2, изображающая состав упаренного раствора, находится в поле глазерита, то в процессе охлаждения раствора в твердую фазу будет переходить глазерит. При этом состав жидкой фазы изменяется по лучу кристаллизации глазерита 2—3. Далее происходит совместная кристаллизация глазерита и хлорида калия, причем состав жидкой фазы изменяется по линии 3—1. После отделения калийных солей, направляемых на конверсию, оставшийся раствор вновь может быть направлен на выпаривание и получение хлорида натрия.
Разработан также вариант схемы переработки глазеритового рас твора, по которому упаренный раствор 2 после отделения хлорида натрия направляется на первую стадию конверсии вместе с мираби литом, полученным в процессе охлаждения глазеритового раствора. Метод позволяет существенно сократить объемы растворов, циркули рующих в системе «охлаждение — выпаривание» в процессе перера ботки глазеритового раствора. На рис. 2.16 изображен ход получения
сульфата калия из мирабилита и хлорида калия с утилизацией гла зеритового раствора.
Рис. 2.16. Схема процесса конверсии мирабилита хлоридом калия с
утилизацией |
глазеритового раствора |
||
охлаждением до 0 °С :------------ |
|
||
изотермы 0° С ; |
--------- изотерма |
100°С: |
|
/- р а с т в о р , образующийся |
после |
охлажде- |
|
ния глазеритовых |
растворов |
и отделения ми- |
рабилита; 2 — упаренный раствор после отделения хлорида натрия; 3 — смесь упаренного раствора 2 с мирабилитом, поступающая на первую стадию конверсии; 4 — смесь хлори да калия с раствором после обогащения гла зерита; А — маточный раствор сульфата ка
лия; G1 — глазерит
Схема получения сульфата калия конверсией сульфата на трия хлоридом калия (рис. 2.17). Хлорид калия и сульфат натрия из бункеров 1 подаются через тарельчатые питатели в реактор конверсии 3 с рамной мешалкой. Одновременно в реактор в рас
четном |
соотношении |
поступают |
|
сульфат |
натрия (мирабилит) и |
||
упаренный |
раствор, |
полученный |
|
на стадии |
утилизации маточных |
растворов, а также серная кисло та для нейтрализации карбоната натрия, содержащегося в исход ном сульфате натрия. Процесс получения глазерита проводится при 20—25° С.
Повышение TeMneoaTVDbl не-
ПОВЫШвНИе тем пературы не
СКОЛЬКО ПОВЫШавТ СКОрОСТЬ ПрО-
цесса, однако при этом существен но увеличивается содержание в растворе глазерита ионов калия и сульфата, что приводит к увеличе-
Рис. 2.17. Схема получения сульфата калия конверсией сульфата натрия хлоридом калия:
1 — бункеры для исходного сырья; 2 — сборник серной кислоты; 3, 6, 9 — реакторы конверсии; 4, 7, 10, 15, 19 — отстойники; 5, 8, 11, 20, 21 — центрифуги; 12, 17 — теплообменники; 13 — поверх ностный кристаллизатор; 14 — холодильная аммиачная установка; 16— вакуум-фильтр; 18 — ВКУ
нию нагрузки на отделение утилизации маточных растворов. Процесс производится непрерывно и продолжается 40—60 мин. Образующую ся в реакторе глазеритовую суспензию направляют в сгуститель Дорра 4, в котором при скорости восходящего потока 1 м/ч суспензия осветляется. Суспензия, сгущенная до соотношения Ж:Т = 0,7:1,2, через промежуточный горизонтальный аппарат с метальным устрой ством поступает на центрифугу 5. Отфильтрованный на центрифуге глазерит направляется на стадию обогащения, где он обрабатывается раствором, полученным на второй стадии конверсии. Процесс обога-
щения глазерита проводится при 20—25° С в течение 60 мин в реак торе 6, аналогичном реактору первой стадии.
Суспензия обогащенного глазерита направляется в отстойник Дорра 7, где она осветляется при скорости восходящего потока 2,5 м/ч. Сгущенная суспензия с соотношением Ж:Т = 0,7:1,0 подается на центрифугу 8. Фильтрат из центрифуги возвращается в отстойник, а осветленный раствор собирается в сборник и затем подается на пер вую стадию конверсии. Отфильтрованный на центрифуге 8 обога щенный глазерит направляется в реактор 9, куда одновременно со второй стадии конверсии поступает 28%-ный раствор хлорида калия. Температура суспензии (смеси) в реакторе поддерживается автомати чески на заданном уровне подачей пара в рубашку аппарата. Про цесс конверсии продолжается 50—60 мин при 20—25° С. Повышение температуры процесса от 25 до 50° С существенно не сказывается на скорости реакции, но при понижении температуры возможна крис таллизация хлорида калия из раствора, что приводит к загрязнению целевого продукта хлоридом калия и глазеритом.
Полученная в реакторе суспензия сульфата калия осветляется в отстойнике Дорра 10. Осветленный раствор направляется на стадию обогащения глазерита, а сгущенная суспензия сульфата калия отжи мается в центрифуге. Кристаллы сульфата калия промываются на центрифуге водой и направляются на сушку.
Для повышения степени извлечения калия и сульфат-иона глазеритовый раствор обессульфачивают и выпаривают. Процесс обессульфачивания раствора проводят охлаждением его до 0—5° С. С этой целью глазеритовый раствор, полученный на первой стадии конвер сии, направляется в теплообменник 12 для предварительного охлаж дения холодным мирабилитовым маточным раствором и далее в кас кад поверхностных кристаллизаторов 13 с аммиачным охлаждением, в которых происходит кристаллизация мирабилита. Образующаяся суспензия сгущается в отстойнике Дорра до соотношения Ж:Т = 3:4 и обезвоживается на дисковом вакуум-фильтре 16. Кек филь тра— мирабилит с незначительными примесями хлоридов калия и натрия — подается на первую стадию конверсии. Осветленный мирабилитовый маточник отдает свой холод исходному глазеритовому раствору в теплообменнике 12, нагревается далее в теплообменнике 17 за счет горячего упаренного раствора и поступает на двухкорпус ную выпарную установку 18.
Суспензия хлорида натрия, получаемая на выпарной установке, сгущается в отстойнике Дорра 19 и центрифугируется. Хлорид на трия поступает на сушку. Осветленный раствор из отстойника Дорра охлаждается в теплообменнике 17 и направляется на первую стадию конверсии.