
2774.Вакуумные технологии
..pdfобработки составляет примерно 15 мин. После ввода раскислителей и легирующих, не нарушая вакуума, дополнительно осуществляют определенное число циклов (4–6), для выравнивания состава и температуры металла в объеме ковша (рис. 2.7).
Остаточное давление в вакуумной камере создается многоступенчатым пароэжекторным насосом и его величина к концу дегазации чаще всего достигает величины около 65 Па. Футеровка вакуумной камеры перед вакуумированием нагревается системой электроподогрева или газокислородными горелками до температуры 1500–1550 °С, что сокращает потерю тепла метал-
лом. |
За время |
вакуумирования его температура |
снижается |
|
на 10–25 °С. |
|
|
|
|
|
Существует мнение, что порционное вакуумирование явля- |
|||
ется |
наиболее |
эффективным средством |
удаления |
водорода |
(по некоторым |
оценкам эффективность |
удаления |
водорода |
вдвое, а азота на 60 % превышает соответствующие показатели циркуляционных вакууматоров). Существует большое количество действующих агрегатов порционного типа, сохраняется потребность в стали с особо низким содержанием водорода, в том числе для роторов цилиндров низкого давления (ЦНД), поэтому остается актуальной задача оптимизации параметров технологического процесса порционного вакуумирования, конструкции и размеров вакуум-камеры.
Циркуляционное вакуумирование стали или процесс RH (Ruhrstahl Heraeus) осуществляют в камере с огнеупорной футеровкой, оснащенной двумя патрубками, которые погружают в жидкий металл. В результате снижения давления в системе и поддувки инертного газа в восходящий погружной патрубок металл подсасывается в вакуумную камеру, где происходят его обезуглероживание и дегазация, а также некоторые другие реакции, связанные с дегазацией (рис. 2.8).
Обработка всей плавки идет быстро за счет циркуляции жидкой стали. Погружение патрубков осуществляют путем
41

опускания самой камеры или подъемом ковша. В целях минимизации времени замены камеры может быть предусмотрена система быстросменных вакуумных камер.
Рис. 2.7. Система внесения |
Рис. 2.8. Схема установки цир- |
||||||
лигатур |
под |
вакуумом с |
куляционного вакуумирования |
||||
двухкамерным |
вакуумным |
типа RH с возможностью про- |
|||||
шлюзом, |
двумя |
вакуумными |
дувки |
кислородом |
сверху: |
||
бункерами и тремя бункерами |
1 |
– устройство |
для |
подачи |
|||
длямикролегирующих добавок |
сыпучих лигатур |
в |
вакуум; |
||||
|
|
|
2 |
– |
кислородная |
фурма; |
|
|
|
|
3 |
– |
крышка |
вакуумной |
|
|
|
|
камеры; 4 – сталеразливочный |
||||
|
|
|
|
ковш; 5 – вакуумная камера |
Металлургические преимущества процесса RH:
оптимальное обезуглероживание до концентрации ниже
15 ppm;
возможность работы с металлом при различном исходном содержании углерода;
42

возможность использования более дешевых легирующих добавок с высоким содержанием углерода;
возможность химического разогрева расплава;
низкое остаточное содержание растворенных газов;
повышение общей степени чистоты стали;
достижение точных запланированных показателейсостава. Вакууматоры типа RH получили наибольшее распростране-
ние вследствие оптимального сочетания производительности, глубины рафинирования и расходов по переделу.
RH-вакууматоры, в свою очередь, по особенностям конструкции и технологии делятся на следующие подтипы:
RH (рис. 2.9–2.11);
RH-TOP/ RH-KTB (Kawasaki Top Blowing);
RH-OB (Oxygen Blowing);
RH-PB (Powder Blowing);
RH-INJ (Injection).
Наиболее широкие рафинирующие возможности, по данным Nippon Steel, имеют вакууматоры подтипов RH-PB и RH-INJ.
Рис. 2.9. Схема реакционной зоны процесса RH
43
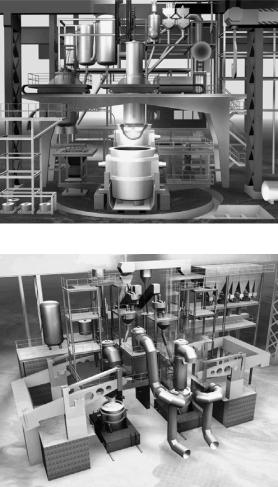
а
б
Рис. 2.10. 260-тонная установка с устройством для быстрой замены вакуум-камеры(подъем ковшаспомощью гидравлического цилиндра)
на заводе фирмыAnshan Iron & Steel Corp., Китай (а); 160-тонная сдвоенная установка RH на Нижнетагильском металлургическом комбинате, Россия (б)
44

Рис. 2.11. Схема однокамерной 85-тонной установки RH с рычажнокоромысловой системой на заводе фирмы SeAH Besteel, Корея
Сравнительная техническая характеристика установок внепечной обработки показывает, что циркуляционный вакууматор, оборудованный системой продувки, позволяет решать наиболее широкий спектр задач (табл. 2.1).
Таблица 2.1
Сравнительная характеристика установок внепечной обработки
Название процесса и схема установки
RHRH- RH- DH CAS KIP VD-OD LF OB PB Inj
Операция
Раскисление |
Есть |
Есть |
Есть Есть |
Есть |
– |
Есть |
– |
|
Обезуглеражива- |
Есть |
Есть |
Есть Есть |
– |
– |
Есть |
Есть |
|
ние |
|
|
|
|
|
|
|
|
Удаление водорода |
Есть |
Есть |
Есть Есть |
– |
– |
Есть |
– |
|
Десульфурация |
– |
Есть |
Есть |
– |
– |
Есть |
Есть |
– |
Нагрев |
Есть |
Есть |
Есть |
– |
Есть |
Есть |
– |
Есть |
Доводка по составу Есть |
Есть |
Есть Есть |
Есть |
Есть |
Есть |
Есть |
||
Удаление включе- |
Есть |
Есть |
Есть Есть |
Есть |
Есть |
Есть |
Есть |
|
ний |
|
|
|
|
|
|
|
|
45
Среди предприятий, использующих в металлургическом цикле систему RH: Voestalpine Stahl, Линц (Австрия); Thyssen Krupp Stahl AG (Beeckerwerth Steelplant, Германия); Sollac Mediterranee, Arcelor Group, Фос-сюр-Мэр (Франция); Maanshan ISCO, Мааншань (Китай); Zhangjiagang Hongfa (ZHF), Цзинфэн Таун (Китай); Arcelor Gent (Sidmar), Гент (Бельгия).
Arcelor Atlantique et Lorraine, Франция (2006 г.) – 270-тонная
RH-OB система с быстрой заменой камер, поворотным стендом, верхнейфурмой для особонизкоуглеродистой стали (ULC).
Dragon Steel Corporation, Тайвань (2006 г.) – 210-тонная
RH-TOP система быстрой замены камер, установка перемешивания в ковше для особонизкоуглеродистой (ULC) стали, высокое содержание кремния, IFстали.
POSCO Pohang Iron & Steel, Корея (2004 г.) – 275-тонная
RH-TOP система быстрой замены камер, тросовая система подъема камеры, особонизкоуглеродистые марки, марки с высоким содержанием кремния.
Вакуумирование стали при помощи REDA-процесса. Nippon Steel – первый японский производитель стали, введший в производственную практику относительно новый способ вакууммирования стали – революционный дегазирующий активатор
(REvolutionary Degassing Activator – REDA), представляющий собой усовершенствованный DH-процесс.
Процесс REDA базируется на том, что скорость гомогенизирующего перемешивания ванны может быть увеличена продувкой металла аргоном через дно ковша. Данный способ вакуумирования развивался как новый способ с 1991 г. на заводе Nippon Steel путем модифицирования 180-тонной установки порционного вакуумирования (N-Slim DH). Установка REDA имеет больший диаметр всасывающего патрубка, чем общепринятый для установки DH. При этом камера не двигается вертикально. Обезуглероживание осуществляется за счет вдувания аргона через дно ковша в вакуум-камеру, с образованием цик-
46

лического потока жидкой стали между камерой и ковшом. Процесс REDA показал преимущества перед DH по обезуглероживающей способности.
Геометрия установки REDA способствует активации перемешивания жидкой стали аргоном на уровне H и более эффективному удалению углерода за счет увеличения общей площади поверхности расплава стали S1 и поверхности контакта стали и аргона S2 в сравнении с установками DH и RH (рис. 2.12). Оптимальный диаметр камеры d для 330-тонной T-REDA установки составляет 2 м – половину внутреннего диаметра ковша D.
Рис. 2.12. Процесс REDA – вдувание аргона через дно ковша в вакуум камеру, с образование циклического потока жидкой стали между камерой и ковшом
В течение 1990–2000 гг. в мире введены в эксплуатацию 119 установок вакуумирования, из них 43 – циркуляционного типа и 76 ковшовых (по преимуществу камерных). Если первый тип установок работает в основном в конвертерных цехах, то половина установок второго типа введена в эксплуатацию в электросталеплавильных цехах.
При этом все большее распространение в технологии дегазации стали в ковше получают вакуумные установки на основе
47
механических насосов, работающих по принципу сухой откачки, что позволяет существенно снизить стоимость эксплуатации, обслуживания и габаритные размеры вакууматора, по сравнению с традиционными жидкостно-кольцевыми и пароэжекторными насосами. Кроме того, высокая скорость и гибкость управления процессом откачки позволяют увеличить производительность сталеплавильного производства. За последние 30 лет в мире введены в строй более 20 вакууматоров с насосной установкой из механических насосов. Наибольшее распространение получили механические откачные комплексы для ковшей с объемом плавки до 50 т. Достигаемая скорость откачки таких систем (по сухому воздуху при нормальных условиях) составляет 96 000 м3/ч (75 кг/ч). Изучение опыта эксплуатации вакууматоров с механическими насосами и совершенствование технологий машиностроения позволили за последние десятилетия осуществить прорыв в область крупнотоннажного производства стали под вакуумом.
Основные процессы вторичной обработки стали: вакуумная дегазация (VD) и вакуумная декарбюдизация (VOD) протекают с выделением большого количества мелкодисперсной пыли. Главной целью этих операций является удаление растворенных в жидкой стали металлургических газов и легких элементов, связанных в форме оксидов. Таким образом, к вакуумным откачным установкам в металлургии предъявляются требования к производительности в условиях значительной пылевой нагрузки.
Основной компонент современных вакуумных систем для дегазации стали, которые принято называть сухими, – большие механические бустерные насосы, сконструированные по принципу воздуходувок Рутса с высокой устойчивостью к пыли. Полностью преимущества сухой откачки проявляются при использовании в качестве первой ступени откачки вакууматора механических насосов (рис. 2.13).
48

Рис. 2.13. Комбинированные установки на основе когтевых насосов серии GV Drystar и насосов Рутса серии EH/HV с производительностью откачки до 120 000 м3/ч, BOC Edwards (используются в производствах компаний: Howmet, Snecma, Rolls-Royce, MTU, Trucast (литейное производство); GM, BMW, Rolls-Royce, Opel, Volvo, Renault, Fiat, ECM, Getrag
(производство двигателей))
Данные системы могут превосходить пароэжекторные комплексы в транспортировке пыли и скорости откачки в диапазоне давлений, при котором начинают протекать большинство металлургических реакций, и при этом занимают заметно меньшие производственные площади.
Компания BOC Edwards (Великобритания) имеет более чем 90-летний опыт разработки и производства пароэжекторных вакуумных систем: от сравнительно простых одноступенчатых насосов до современных эффективных многоступенчатых систем. Эжекторы могут без особых затрат производиться по специаль-
49
ному заказу с целью удовлетворения специфических требований заказчика, они имеют производительность, как правило, в пределах 1,5 · 106 м3/ч. Компания предлагает комбинации паровых эжекторов и жидкостно-кольцевых насосов, в которых жидкостно-кольцевой насос замещает последнюю ступень пароэжекторной системы. Это позволяет обрабатывать более интенсивные потоки газов/паров при низких давлениях, характерных для многоступенчатых эжекторных комплексов, в то же время значительно снижая расход пара и, следовательно, эксплуатационные расходы.
В процессе своей инновационной деятельности компания BOC Edwards разработала и запатентовала захватный механизм когтевого типа и технологию безмасляной откачки на основе насосов серии GV Drystar, имеющую следующие преимущества:
1)минимум технического обслуживания: в связи с отсутствием масла в рабочем объеме насоса нет необходимости в приобретении и замене рабочей жидкости; отсутствует необходимость в производстве и утилизации пара как на пароэжекторных агрегатах; отсутствует масляный выхлоп и протечки масла. Предприятия, эксплуатирующие «сухие» насосы, удовлетворяют экологическим требованиям стандарта ISO 14000;
2)улучшенные технологические условия обработки металла
исплавов, повышающие качество готовой продукции: отсутствие обратного потока паров масла, который является источником загрязнения вакуумной печи; большее допустимое входное давление паров воды, что способствует обезвоживанию новой футеровки печи после технических регламентов; расширенные возможности по инжинирингу и автоматизации вакуумной системы; уменьшаются габаритные размеры установки в целом; насосное
иизмерительное оборудование может быть объединено в единую информационную сеть.
50