
2774.Вакуумные технологии
..pdfспециальные электроизоляционные бумаги и нефтяные минеральные масла или жидкие синтетические диэлектрики. Основу БПИ составляют слои изоляционной бумаги, каждый из которых может быть как сплошным, так и состоять из витков бумажной ленты. В первом случае для создания изоляции используют рулоны шириной до 3,5 м, во втором – ролики из бумажной ленты шириной от 20 до 400 мм. Рулонная БПИ в основном применяется при производстве секций силовых конденсаторов и в электрических вводах (проходных изоляторах), ленточная же – в конструкциях с электродами достаточно сложной конфигурации или в изделиях большой протяженности, например в кабелях.
Изоляция кабелей с бумажной пропитанной изоляцией состоит из лент кабельной бумаги, пропитанной маслоканифольным составом. В кабелях на напряжение 1–10 кВ каждая фаза изолируется отдельно, а затем поверх скрученных изолированных жил накладывается общая – поясная изоляция. Промежутки между изолированными жилами заполняют различными наполнителями.
Кабельные бумаги для силовых кабелей выпускаются из сульфатной целлюлозы с общим диапазоном толщин от 0,08 до 0,24 мм. По назначению их можно разбить на следующие группы: для кабелей на рабочее напряжение до 35 кВ – однослойная и многослойная; для кабелей на 35 кВ и выше – обычная, многослойная и уплотненная (с повышенной плотностью); для кабелей на 110 кВ и выше – обычная и многослойная уплотненная. К бумагам для кабелей на большие напряжения предъявляются повышенные требования. Обычные бумаги имеют плотность 760– 850 кг/м3, уплотненные – 1090–1100 кг/м3 и выше. Кабельные бумаги высокого напряжения отличаются толщиной, плотностью, более жесткими требованиями к механическим, химическим и диэлектрическим показателям.
В настоящее время кабельные бумаги изготавливают исключительно из древесной целлюлозы, полученной путем сульфатной обработки мелкорасщепленной древесной массы.
111
Для изоляции силовых кабелей напряжением до 10 кВ применяют однослойную кабельную бумагу в соответствии с ГОСТ 23436–83 марок К-080, К-120, К-170 (толщиной 0,08; 0,12
и0,17 мм соответственно).
Взависимости от вязкости пропиточного состава кабели с БПИ могут изготавливаться с вязким пропиточным, с обеднен- но-пропиточным и с нестекающим пропиточным составами соответственно.
Кабель с вязким пропиточным составом – это кабель с БПИ, пропитанный маслоканифольным составом марки МП-3, в состав которого входят нефтяное масло (для пропиточного состава применяют нефтяное масло марки КМ-25) в качестве основы, канифоль (7,5±2,5) % и полиэтиленовый воск (3±2) %.
Кабель с обедненно-пропитанной изоляцией – это кабель с вязким пропиточным составом той же марки МП-3, но свободная часть его частично или полностью удалена, т.е. бумажная изоляция освобождена от избытка пропиточного состава. Кабели с обедненно-пропитанной изоляцией выпускают на напряжение до 6 кВ и маркируются добавлением к основной маркировке через дефис буквы В, например ААШв-В. Кабели с обедненнопропитанной изоляцией предназначены для прокладки вертикальных и наклонных трасс с ограниченной разностью уровней.
Кабель с нестекающим пропиточным составом – это кабель с БПИ, пропитанной изоляционным составом, вязкость которого такова, что при рабочих температурах кабеля он не способен к перемещению (стеканию). В качестве такого пропиточного состава используют маслоканифольный состав марки МП-5, содержащий (3±2) % канифоли, (18±1) % полиэтиленового воска, остальное – смесь нефтяного масла и церезина. Бумажная изоляция, пропитанная таким составом, предназначена для прокладки кабелей на вертикальных и наклонных трассах без ограничения разности уровней. Кабели с нестекающим пропиточным составом маркируются индексом Ц, стоящим впереди маркировки кабеля, например ЦААШв.
112
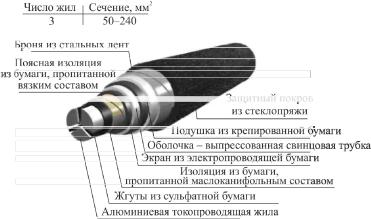
Количество слоев бумажной изоляции (толщина) зависит от рабочего напряжения кабеля и сечения жил. Так, толщина изоляции жил и поясной изоляции (в зависимости от их сечения) для кабелей со свинцовой и алюминиевой оболочками напряжением 1 кВ составляет соответственно 0,75–0,95 и 0,5–0,6 мм, для кабелей напряжением 6 кВ – 2,0 и 0,95 мм, а напряжением 10 кВ – 2,75 и 1,25 мм соответственно. В многожильных кабелях для различия фаз верхние ленты изоляции на каждой жиле имеют разный цвет (на одной жиле – красный, на другой – черный, на третьей – цвета изоляционной бумаги) или полоски различного цвета либо цифры на каждой ленте (на одной – 1, на другой – 2, на третьей – 3).
Стандартная технология изготовления бумажно-пропиточ- ной изоляции состоит в намотке необходимого числа слоев бумаги, последующей вакуумной сушке и пропитке дегазированным маслом или другими жидкими диэлектриками в условиях вакуума (рис. 4.4).
Рис. 4.4. БПИ в кабеле по ГОСТ 18410–73
Так как БПИ является многослойной, то в ней любые дефекты твердого диэлектрика (бумаги) заведомо ограничены пределами одного слоя, который при нанесении многократно пере-
113
крывается другими слоями. Таким образом, в БПИ формируется система узких сообщающихся зазоров между отдельными слоями и большое количество микропор между волокнами самой бумаги. Благодаря наличию зазоров и пор в процессе вакуумной сушки обеспечивается быстрое и полное удаление влаги и воздуха, а при пропитке − гарантированное заполнение зазоров и пор маслом или другими пропиточными жидкостями. Максимальными электрическими и механическими свойствами обладают специальные кабельные и конденсаторные бумаги. Основным же недостатком БПИ являются ее горючесть и невысокие допустимые рабочие температуры.
Цель операций вакуумной сушки и пропитки заключается в увеличении показателя электрической прочности. Заполняющий зазоры между слоями и поры бумаги жидкий диэлектрик имеет значительно более высокую электропрочность, нежели воздух. Температура сушки для конденсаторной бумаги составляет 120–130 °С при остаточном давлении 10–1−10–2 Па, а температура пропитки предварительно высушенным и дегазирован-
ным жидким диэлектриком – от 80 до 90 °С при остаточном давлении 10–1−100 Па.
Особое внимание уделяется процессу сушки и пропитки БПИ силовых кабелей. Пропиточная бумага должна обладать высокими характеристиками механической прочности, электропрочности, сопротивления, низкими диэлектрическими потерями. Большинство свойств изоляционной бумаги значительно зависит от ее газосодержания. При обычной влажности воздуха (70 %) бумага содержит 7−9,5 % воды по массе. Для получения высоких электроизоляционных свойств необходимо снизить влагосодержание бумаги до величины менее чем 0,3 %, а затем пропитать ее сухим дегазированным пропиточным составом на основе минеральных масел.
Даже при длительном нагреве бумажной изоляции до температуры 100−120 °С в условиях атмосферного давления влагосодержание может быть снижено лишь до величины 1,5−2 %.
114
Снижение давления паров над поверхностью бумаги до 10 Па позволяет при той же температуре 120 °С уменьшить влагосодержание уже до 0,1 %.
Для дегазации масел применяются специальные дегазационные котлы, в которых при поддержании температуры в 125 °С создается остаточное давление 2,6·103 Па (для кабелей на напряжение до 10 кВ) и 1,3·103 Па (для кабелей на напряжение 20 и 35 кВ). В процессе дегазации масла, предназначенного для кабелей на 110 кВ и выше, применяется технология капельного распыления масла в дегазационных котлах или технология поверхностного растекания, когда масло свободно протекает через пористое вещество с сильно развитой поверхностью. В этом случае величина остаточного давления поддерживается на уровне 100−101 Па. Длительность процесса дегазации при этом составляет от нескольких десятков до нескольких сотен часов.
При реализации технологического цикла кабель поступает в сушильно-пропиточное отделение уложенным в металлические корзины. Чаще всего в вакуумный сушильно-пропиточный котел загружается по две корзины с кабелем. Каждый котел включается в цеховую систему маслопроводов для подачи в него пропиточного состава. В систему вакуумной откачки котлов входят вакуумные насосы и конденсационные колонки. Также в комплекс технологического оборудования отделения пропитки входят теплообменники и циркуляционные насосы для пропиточного состава.
Технология изготовления маслонаполненных высоковольтных вводов с БПИ также базируется на применении вакуумной техники. Вводы служат для изолирования высоковольтного токоведущего вывода от заземленного силового оборудования. Ввод состоит из токоведущей трубы, изолированной БПИ или элегазом, соединительной втулки и двух фарфоровых крышек. Габариты вводов варьируются по длине от 2,5 м для вводов на 110 кВ до 15 м для вводов на 1150 кВ.
115

На заводе «Изолятор» в технологии изготовления вводов применяются следующие типы вакуумных насосов: водокольцевые ВВН-1,5, форвакуумные НВЗ-150, двухроторные (Рутса) и бустерные. Кроме того, для сушки и дегазации трансформаторного масла, заливаемого во вводы, эксплуатируют как отечественные дегазационные установки ВДУ-3 и ВДУ-10 (рис. 4.5), так и импортные.
Рис. 4.5. Установка ВДУ, выпускаемая Украинским институтом трансформаторостроения, г. Запорожье
Для обеспечения высокой электрической прочности БПИ подвергают термообработке в вакууме, т.е. сушат в индукционных шахтных вакуумных печах при температуре 105 °С и рабочем давлении 102 Па. После прогрева бумажной изоляции до 105 °С, предварительно на 24 ч включают водокольцевые насосы для удаления основной массы водяных паров, выделяющихся из бумажной изоляции, затем – форвакуумный насос, а за ним − бустерный насос.
Результатом применения такой технологии обработки является достижение остаточного давления 10–1 Па в печах и низкое − менее 0,1 % влагосодержание внутри бумажной изоляции, после
116
чего высушенная бумажная изоляция поступает на участок сборки вводов.
После сборки вводы откачивают через отверстие диаметром 6 мм в течение 24−48 ч до остаточного давления 133−400 Па, после чего производят заполнение вводов трансформаторным маслом под вакуумом.
Технология обеспечивает малое (не более 1 %) газосодержание масла в выпускаемых вводах, причем основную долю
вувеличении газосодержания масла составляет газ, оставшийся
вбумажной изоляции после вакуумирования перед операцией заливки масла.
Вмировой практике высоковольтного аппаратостроения на протяжении последних 30 лет коренным образом изменились
взгляды на необходимость глубокого вакуумирования БПИ в процессе ее сушки и пропитки маслом. Раньше считалось, что сушку бумажной изоляции необходимо производить при остаточном давлении не выше 10–1 Па, в настоящее время принято, что величина оптимального давления составляет 10−103 Па, повышение глубины вакуума должно быть произведено непосред-
ственно перед пропиткой бумажной изоляции до величины в пределах 10–1 Па.
Для силовых трансформаторов на рабочие напряжения от 10 до 1150 кВ в качестве основного вида изоляции используется маслобарьерная (МБИ), при изготовлении которой также используются вакуумные технологии.
Основу МБИ составляет минеральное трансформаторное масло, которое гарантированно заполняет изолирующие промежутки между электродами любой сложной формы и, кроме того, обеспечивает интенсивное охлаждение конструкции за счет конвективной или принудительной циркуляции масла. Также достоинством этого типа изоляции является простота конструкции и технологии, достаточное охлаждение активных частей оборудования. Среди заметных недостатков МБИ можно выделить меньшую, чем у БПИ электропрочность, а также пожаро- и взрывоопасность.
117
Типовая технология изготовления МБИ включает в себя сборку конструкции, ее сушку в вакууме и заполнение предварительно дегазированным трансформаторным маслом.
Изоляция силовых трансформаторов представляет собой достаточно сложную систему, состоящую из внешней и внутренней частей, выводов, обмоток и вспомогательных устройств. В процессе производства изоляцию трансформатора подвергают термовакуумной обработке при температуре 110−120 °С и остаточном давлении 102−101 Па, для чего активную часть трансформатора помещают в вакуумный сушильный шкаф. По окончании процесса сушки, при сохранении глубины вакуума температуру в сушильном шкафу снижают до 80−85 °С и в шкаф заливают осушенное дегазированное трансформаторное масло, обладающее электропрочностью не менее 200 кВ/см. После заливки активную часть выдерживают в течение 3−5 ч в шкафу, заполненном маслом при сохранении требуемой глубины вакуума над поверхностью масла, затем масло сливают, после чего сборку выдерживают под вакуумом еще в течение 2 ч.
Благодаря вакуумной сушке перед пропиткой увеличивается теплопроводность обмоток электродвигателей и трансформаторов. При работе обмотки нагреваются протекающим по ним электрическим током по всему объему, а охлаждение происходит только с поверхности. Чем меньше в обмотке воздуха и больше пропиточной смолы или масла, тем лучше ее теплопроводность и, как следствие, меньше разогрев.
Вакуумная технология находит применение не только в производстве конденсаторов и кабелей с БПИ. Одним из типов электрических конденсаторов являются вакуумные конденсаторы, имеющие заметно меньшие диэлектрические потери, чем газовые, малый температурный коэффициент емкости и повышенную устойчивость к вибрациям по сравнению с газонаполненными. Величина пробивного напряжения вакуумных конденсаторов не зависит от атмосферного давления, поэтому они широко используются в авиационной технике.
118
Вакуумная техника также применяется при испытаниях конденсаторов, заполненных элегазом, на герметичность. Испытуемый конденсатор помещается в герметичную камеру, на первом этапе откачиваемую при помощи высопроизводительных вакуумных насосов для удаления адсорбированных газов. На втором этапе камера за короткое время знаполняется осушенным воздухом до давления ниже атмосферного, после чего отбирается проба из смеси воздуха и, в случае негерметичности, элегаза. Датчики давления, встроенные в систему, подключаются к центральному измерительному комплексу.
Важную роль играет вакуумная технология и вакуумное технологическое оборудование в производстве металлопленочных конденсаторов. Одним из методов изготовления тонкопленочных конденсаторов является высокочастотное магнетронное распыление мишеней из титаната бария ВаТiO3. Напыление на кремниевую подложку с температурой от 20 до 700 °С ведется в атмосфере смеси аргона и кислорода. Для практического применения рекомендованы двух- и трехслойные конденсаторы с ВаТiO3 в качестве диэлектрика. Ускоренный метод изготовления намотанных металлопленочных конденсаторов, дающий уменьшение их стоимости и повышение качества и надежности, состоит в следующем: заготовки конденсаторов помещаются в вакуумную камеру для удаления воздуха из пор применяемых материалов, затем проводится заполнение пор газом с высокой электропрочностью (элегазом или хладоном-12) под давлением, что предотвращает возникновение коронного разряда, и на последнем этапе – герметизация полимерными капсулами.
Установки General К5000 и К4000 для вакуумного нанесения электрпроводных слоев из алюминия, цинка, а также слоев алюминий–цинк–алюминий на различные диэлектрики (бумага плотностью 35–90 г/м2 и пленки толщиной от 8 до 120 мкм при ширине рулона 1025–4050 мм) для конденсаторов переменного тока разработаны и производятся английской компанией General Vacuum Equipment (рис. 4.6).
119

Рис. 4.6. Установка General К5000 для вакуумного нанесения алюминия на диэлектрики (бумага и пленки)
Высокопроизводительные диффузные насосы создают в зоне покрытия высокий уровень вакуума. Это позволяет создавать покрытия с хорошими защитными свойствами, которые широко используются при производстве гибкой упаковки для пищевых продуктов.
Используемый в К5000 барабан большого диаметра для нанесения покрытий обеспечивает максимальную в отрасли эффективность при минимальных затратах энергии, алюминия и расходных материалов на 1 м2 произведенной пленки.
Запатентованное устройство для плазменной обработки повышает отражающую способность покрытия, увеличивает адгезивные свойства металла и повышает уровень защиты от проникновения водяного пара и кислорода.
Система намотки с высокоскоростными роликами и точной параллельностью между ними позволяет создавать перемотанные рулоны, качество намотки которых не уступает разматываемым рулонам.
Полимерная подложка обрабатывается плазмой в атмосфере аргона при остаточном давлении 101−10–1 Па. Затем на подложку осаждается тонкая пленка одного из металлов – Au, Ag, Сu, Ni или Sn в количестве 0,1−50 мг/м2, что существенно улучшает адгезию алюминия. После этого поверх созданного подслоя осаждается пленка алюминия. Оптимальная толщина алюминиевой
120