
2774.Вакуумные технологии
..pdfпленки составляет от 20 до 100 мкм. Коэффициент гладкости полученной поверхности не хуже 10–4. В производстве металлопленочных конденсаторов также используется устройство, обеспечивающее точное расположение затеняющих масок в установке металлизации в процессе нанесения пленки.
Широкую пленку из поликарбоната, полиэфира и некоторых других электроизоляционных материалов металлизируют в вакууме цинком, алюминием или сплавами, содержащими цинк, алюминий и хром. Для получения заготовок конденсаторов из такой пленки в процессе металлизации используют одновременно до 100 лент-масок, которые установлены на две пары приводных роликов и прижимаются к металлизируемой пленке. Перед подачей в узел металлизации ленты-маски проходят через направляющие гребенки из инвара.
Еще одной областью применения вакуумных технологий является формообразование изоляции, при котором разность давлений создает силу, заменяющую механическое воздействие. Так, предложена технологическая система для производства провода с круглой или преимущественно прямоугольной токопроводящей жилой (ТПЖ), которая содержит отдающее и приемное устройства и экструдер, обеспечивающий наложение полимера без растворителя в виде оболочки продольно вокруг ТПЖ, движущейся в направлении от отдающего устройства к приемному. Оболочка из полимера плотно накладывается на поверхность ТПЖ с помощью вакуума, создаваемого внутри оболочки. При этом в системе предусмотрено устройство для контроля скорости движения ТПЖ относительно головки экструдера и таким образом можно точно регулировать толщину экструдируемой электроизоляции при изменении скорости движения ТПЖ.
4.3. Вакуумное электротермическое оборудование
Электрические вакуумные печи сопротивления находят все более широкое применение в промышленности и при проведении научных исследований.
121
Конкурентоспособность и технический уровень отечественных электропечей во многом зависят от применения в них комплектующего вакуумного оборудования. В этих печах находят применение:
механические вакуумные агрегаты и насосы с быстротой откачки от 1 до 5000 л/с;
бустерные и диффузионные паромасляные агрегаты
инасосы с быстротой откачки от 300 до 15000 л/с;
вакуумные клапаны с условным проходом от10 до 100 мм;
вакуумные затворыс условным проходом от100 до630 мм;
термоэлектрические, ионизационные, деформационные блокировочные вакуумметры;
гибкие коммутационные линии (вакуумпроводы) для вакуумной откачки;
вакуумные быстроразъемные соединительные элементы.
Потребность российской промышленности в вакуумном комплектующем оборудовании отечественного производства в настоящее время полностью не удовлетворяется, что сдерживает отечественное производство вакуумных печей.
Электрические вакуумные печи находят широкое применение в металлургии и более подробные сведения о них содержатся в главе 2 настоящего пособия. К неожиданным областям применения вакуумных печей относится вакуумная термообработка медицинских имплантов в стоматологии и ортопедии. Обсуждается возможность и особенности термической обработки в вакуумных электрических печах при производстве искусственных суставов и стоматологических имплантов из современных сплавов.
122
5. ВАКУУМНЫЕ ТЕХНОЛОГИИ В ЭНЕРГЕТИКЕ
Энергетика включает в себя получение, передачу, преобразование и использование различных энергетических ресурсов. Самыми распространенными видами энергетики являются гидроэнергетика, тепловая электроэнергетика и атомная энергетика, включая термоядерную. Несколько особняком стоят генераторы прямого преобразования химической и тепловой энергии в электрическую энергию. Вакуумная техника и вакуумные технологии находят применение практически в каждой из перечисленных областей.
5.1. Сушка и деаэрация
Наиболее часто используемыми являются тепловые электростанции (ТЭС), основой которых служат котельные установки. В рамках подготовительного цикла производится транспортировка, измельчение и подсушивание топлива. Подвод тепла и отвод влаги от топлива производится в специальных сушильных агрегатах. Сушильные агрегаты подразделяются на атмосферные, вакуумные и высоковакуумные − сублимационные по величине давления среды в рабочем пространстве. Малые количества топлива обрабатываются в камерных сушилках, а большие − в туннельных сушилках непрерывного действия. Основной частью любой сушилки является протяженная камера, внутри которой в продольном направлении перемещается высушиваемый материал.
Угольное сырье сушится в барабанных сушилках – вращающихся вокруг оси со скоростью 0,5−8 об/мин горизонтальных либо наклонных цилиндрах или конических барабанах. Процесс сушки проходит в условиях низкого вакуума (рис. 5.1).
Для удаления из воды, питающей котел, растворенных в ней газов на ТЭС устанавливают специальные устройства − деаэраторы. При отсутствии предварительной деаэрации воды, пода-
123
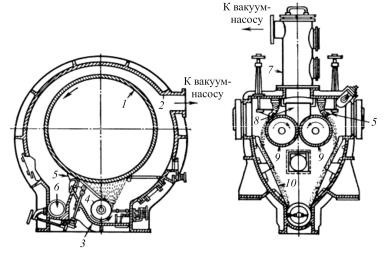
ваемой в парогенераторы ТЭС, газы (кислород и свободная двуокись углерода), растворенные в воде, выделяясь в парогенераторе или тепловых сетях, вызывают повышенную коррозию металла. Среди технических средств деаэрации наибольшее распространение получили вакуумные деаэраторы (рис. 5.2). Принцип действия деаэратора следующий: часть воды в резервуаре подвергается воздействию пониженного давления, в результате чего растворенные в воде воздух и газы удаляются и выводятся через вентиляционный клапан. Удаление газов в современных деаэраторах регистрируется встроенным блоком типа SmartSwitch. Если SmartSwitch ничего не регистрирует в течение 10 мин, это означает, что количество растворенных в жидкости газов достигло минимального уровня. Процесс деаэрации в этом случае автоматически останавливается и снова запускается через предустановленное время.
а |
б |
Рис. 5.1. Вакуум-сушилкидля угля: а– одновальцовая; б– двухвальцовая: 1 – полыйбарабан(валец); 2 – корпус; 3 – корыто; 4 – распределительный валик; 5 – нож; 6 – шнек; 7 – приемныйколпак; 8 – сборник; 9 – вальцы; 10 – наклонные стенки
124
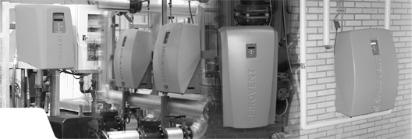
Рис. 5.2. Деаэратор вакуумный Spirovent Air Superior
В Уральском технологическом институте (Екатеринбург) разработана конструкция вакуумного трехкамерного деаэратора (ВТД), который обеспечивает последовательную ступенчатую деаэрацию воды в трех камерах, имеющих различное давление газа и активную вентиляцию паровых пространств.
Работа камеры исключает явление гидростатической депрессии, а следовательно, и недогрев, отрицательно сказывающийся на десорбции таких газов, как О2 и СО2. При расширении воды в струе обеспечивается развитая поверхность контакта пара с водой, что в сочетании с активным вентиляционным потоком, составляющим не менее 5−10 % расхода воды, обеспечивает глубокую деаэрацию воды.
Вакуумная технология нашла свое применение и при производстве турбогенераторов. Компания Chromalloy Gas Turbine Corporation производит нанесение упрочняющих покрытий на детали высокотемпературных турбин. При нанесении покрытий используются вакуумные насосы, которые должны откачивать пары, содержащие хлор и частицы силиката. Начиная с 1990 г. компания начала использовать для откачки вакуумные установки KLRC производства английской фирмы Kinney Vacuum Co. KLRC − двуступенчатая установка, состоящая из двух жидкост- но-кольцевых вакуумных насосов типов 304 и 316 с корпусами из нержавеющей стали 304 и 316 соответственно (рис. 5.3).
125

Рис. 5.3. Водокольцевой вакуумный насос KLRC 300 (Kinney Vacuum Co) для откачки агрессивных сред. Материал корпуса и ротора – нержавеющая сталь
304 или 316
Вкачестве рабочей жидкости насосов используется вода, нейтрализуемая гидроокисью натрия. Ресурс установки KLRC
в2,5−3 раза больше, чем у аналогичных установок с корпусом из чугуна. Создаваемое остаточное давление составляет 4·103 Па, а при использовании жидкости с меньшим давлением насыщен-
ных паров, чем у воды, можно получить остаточное давление до 103 Па.
5.2.Технологии сверхпроводимости и тепловой защиты
Втехнологии турбогенераторостроения вакуумная техника находит свое место в связи с использованием явления сверхпроводимости. Увеличение мощности и размеров турбогенераторов не исключает возникновения технических трудностей при создании крупных энергетических агрегатов. До последнего времени их мощность можно было увеличивать лишь до определенных пределов. Проведенные расчеты показывали, что не удастся перешагнуть верхний предел, ограниченный мощностью турбогенератора в 2500 МВт, ротор которого вращается с частотой
126
3000 об/мин, так как этот предел в первую очередь определяется прочностными характеристиками применяемых материалов: напряжения в механической конструкции машины более высокой мощности возрастают настолько, что действие центробежных сил неизбежно вызовет разрушение ротора.
Немало забот возникает и при транспортировке агрегатов. В свое время для перевозки турбогенератора мощностью 1200 МВт пришлось создать сочлененный транспортер длиной почти 64 м
игрузоподъемностью 500 т. Каждая из двух тележек транспортера опиралась на 16 вагонных осей.
Многие трудности отпадают сами по себе, если использовать при конструировании эффект сверхпроводимости и применить сверхпроводящие материалы (рис. 5.4). В этом случае потери в роторной обмотке можно практически свести к нулю, так как постоянный ток не будет встречать в ней сопротивления. Таким образом, повышается КПД машины, а протекающий по сверхпроводящей (СП) обмотке возбуждения ток большой силы создает столь сильное магнитное поле, что уже нет необходимости применять магнитопровод из стали, традиционный для любой электрической машины. Отказ от стали снизит массу ротора
иего инерционность.
Создание криогенных электрических машин, использующих эффект сверхпроводимости – необходимость, естественное следствие научно-технического прогресса и есть основания утверждать, что уже в начале нашего века сверхпроводящие (СП) турбогенераторы мощностью более 1000 МВт уже будут работать в энергосистемах промышленно развитых стран.
Одной из основных задач при создании сверхпроводящих генераторов является конструирование вакуумной теплозащиты криогенной зоны с расположенными в ней сверхпроводящей обмоткой и системой подачи криоагента.
Применение сверхпроводящих генераторов может начаться уже в ближайшем будущем для парогазовых установок и установок на твердом топливе с мощности в 200 МВт, а для АЭС – мощности в 600−800 МВт.
127
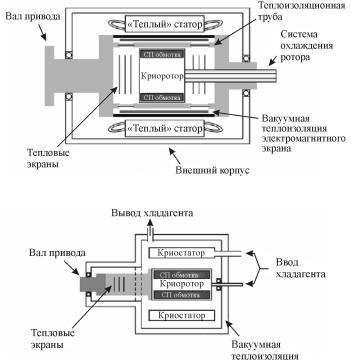
а
б
Рис. 5.4. Схемы классического (а) и полностью сверхпроводникового (б) СП генераторов
Опытные сверхпроводящие турбогенераторы выпускаются в США, Японии, России (Институт электромеханики, ныне ВНИИэлектромаш, ЭМО «Электросила», Энергетический институт им. Кржижановского) с начала 1980-х гг. (рис. 5.5, 5.6).
Современные достижения в области техники сверхпроводимости и криогенной техники позволяют в настоящее время осуществить экономичные и технически более совершенные решения в области получения больших токов. Применение техники низких температур в электротехнических и энергетических установках считается ближайшим будущим криоэнергетики и охватывает следующие области:
128
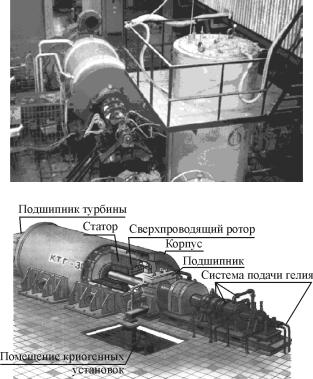
производство электроэнергии: турбогенераторы со сверхпроводящей обмоткой якоря, термоядерные и МГД-генераторы со сверхпроводящими магнитами;
создание накопителей энергии со сверхпроводящими магнитами;
электротранспорт и электроприводы: электромагнитные системы подвеса со сверхпроводящими магнитами (транспорт на магнитной подушке), двигатели с СПобмоткой возбуждения;
передача энергии при помощи сверхпроводящего кабеля.
а
б
Рис. 5.5. СП генераторы: а – КТГ-20 на 20 МВт; б – КТГ-300, СССР, начало 1980-х гг.
129
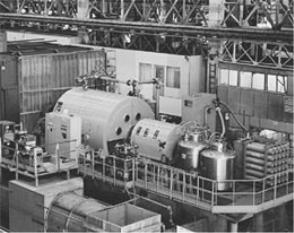
Рис. 5.6. Самый большой в мире СП генератор Hitachi
для NEDO/Super-GM (Japan), 83 МВт (3600 мин–1)
При создании автономных источников энергии небольшой мощности на транспорте: космических летательных аппаратах (КЛА), самолетах, судах и т.д., в настоящее время широко используются электрические генераторы − установки непосредственного преобразования различных видов энергии в электрическую. Суммарная мощность таких генераторов на сегодня превышает мощность всех электростанций вместе взятых.
Вакуумная техника и технология также используется при производстве термоэлектрических, термоэмиссионных генераторов и солнечных батарей (фотовольтаика). Конструкция ТЭмГ представляет собой два электрода, разделенных небольшим промежутком и включенных в цепь с нагрузочным сопротивлением (рис. 5.7, а). Принцип действия термоэмиссионных генераторов (ТЭмГ) основывается на использовании эффекта Ноттингема, когда в результате теплового возбуждения электронов происходит явление термоэмиссии (рис. 5.7, б). Термоэмиссионные генераторы подразделяют на вакуумные и газонаполненные. Для эффективной работы ТЭмГ важно хорошее обезгаживание термо-
130