
2774.Вакуумные технологии
..pdfв нижней части установки и периодически удаляются через сливной вентиль при достижении заданной концентрации.
В химической промышленности ВД широко применяется для изготовления сложных эфиров и восков, в медицине – для изготовления фармацевтических препаратов, в парфюмерии – для изготовления ароматических веществ.
Молекулярная дистилляция (МД), являющаяся разновидно-
стью ВД, – это технологический процесс разделения жидких смесей путем свободного испарения в вакууме (10–1−10–2 Па) при температурах ниже точки их кипения. МД осуществляется на минимально коротком расстоянии между испаряемой поверхностью и холодильником. В современных молекулярных установках процесс испарения протекает в очень тонком слое (пленке) жидкости (в среднем 0,01−0,05 мм), значительно уменьшающем время нахождения вещества на поверхности и, соответственно, опасность его термической деструкции. Конденсация молекул на поверхности холодильника при большой разности температур пара и холодильника (50−100 °С) происходит практически мгновенно.
Молекулярная дистилляция применяется в технологических процессах:
регенерации нефтепродуктов и отработанных минеральных масел из двигателей, редукторов, трансформаторов, турбин (рис. 3.3), деасфальтизации, обессеривания;
производства рабочих жидкостей (масел) для механических и диффузионных вакуумных насосов;
очистки термически нестойких органических веществ – эфиров себациновой, фталевой и некоторых других кислот;
выделения витаминов из рыбьего жира и т.п.
В США разработан метод перегонки в тонком слое в высоком вакууме − молекулярная перегонка вакуумного остатка, позволяющая извлечь дополнительно до 50−60 % тяжелой дистиллятной фракции из остатка, полученного на стандартной установке вакуумной дистилляции (рис. 3.4). Остаток после обессеривания может бытьнаправлен на дальнейшую переработку.
91

Рис. 3.3. Установка ВД смазочных масел производства Pörner Ingenieurgesellschaft GmbH (Австрия), находящаяся
в г. Туркменбаши, Туркменистан
Рис. 3.4. Промышленная установкамолекулярнойвакуумной дистилляции вакуумных масел непрерывного действия, выполненнаяиз нержавеющей стали
92
Новый метод дает возможность на ранней стадии переработки сконцентрировать в небольшом объеме остатка металлы и тяжелые фракции нефти (асфальтены). Полученный дистиллят используется для производства смазочных масел или парафина высокой степени очистки, а также в качестве сырья для каталитического флюид-крекинга.
Установка состоит из газового сепаратора и двух перегонных кубов, в которых при остаточном давлении от 50 до 5 Па происходит процесс разделения в тонком слое. Обогрев кубов производится циркулирующим высокотемпературным теплоносителем. Тяжелый вакуумный дистиллят конденсируется во внутреннем холодильнике. Капли конденсата постоянно отводятся, что способствует снижению до минимума содержания металла и асфальтенов в тяжелом дистилляте.
3.2. Ректификация в вакууме
Технология ректификации − разделение жидкостей и сжиженных газовых смесей, основанное на диффузионном обмене вещества между неравновесными фазами и сопровождаемое межфазным теплообменом. Процесс ректификации проводится в ректификационных колоннах, конструктивно включающих в себя куб-испаритель, колонну с внутренними распределительными устройствами и конденсатор. Пары, образовавшиеся в ку- бе-испарителе, движутся снизу вверх через колонну, контактируя со стекающей жидкостью.
Пар из колонны подается в конденсатор, откуда часть образовавшегося конденсата, называемого флегмой, возвращается в верхнюю часть колонны, а остаток представляет собой конечный продукт процесса – дистиллят.
Флегма стекает вниз по колонне, контактируя с паром, и возвращается в куб-испаритель, где снова испаряется. Внутреннее распределительное устройство, предназначенное для контакта пара и жидкости, представляет собой тарельчатые насадки или сборки различной конструкции. Методом вакуумной ректи-
93

фикации также пользуются в случае разделения термолабильных (неустойчивых к тепловому воздействию) жидкостей.
Вакуумная ректификация применяется в нефтяной промышленности для разделения нефти на бензин, керосин, дизельное топливо, мазут и другие продукты (табл. 3.1), в производстве синтетического каучука, сероуглерода, для разделения изотопов и т.д.
|
|
|
Таблица 3.1 |
|
Материальный баланс атмосферной перегонки |
||||
|
западносибирской нефти |
|
|
|
|
|
|
Выход фракции, |
|
Фракция |
Интервал температуры |
|
||
|
выкипания, ° С |
|
мас. % |
|
Газ |
– |
|
1,1 |
|
Бензиновые фракции |
<62 |
|
4,1 |
|
|
62–85 |
|
2,4 |
|
|
85–120 |
|
4,5 |
|
|
120–140 |
|
3,0 |
|
|
140–180 |
|
6,0 |
|
Керосин |
180–240 |
|
9,5 |
|
Дизельное топливо |
240–350 |
|
19,0 |
|
Мазут |
– |
|
49,4 |
|
Потери |
– |
|
1,0 |
|
Французская фирма Speichim и английская Hays Chemical Distribution Ltd совместно разработали промышленную вакуумную ректификационную установку для очистки сырья, реактивов и растворителей, рекуперации отработанных продуктов с получением высокочистых дистиллятов для фармацевтической и электротехнической промышленности и производства особо чистых реактивов. Установка состоит из 5 колонн из нержавеющей стали, имеющих по 65 тарелок каждая и работающих в диапазоне температур 0−200 °С и давлений от высокого вакуума до 6 атм, а также испарителей, перегонных кубов, конденсаторов и т.д.
94
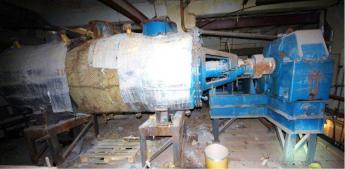
3.3. Вакуумная и сублимационная тепловая сушка
Технология сушки − термический процесс испарения (удаления) влаги из твердых материалов. Выделяют два основных вида – вакуумную тепловую сушку и вакуумную сублимационную сушку материалов в замороженном состоянии.
Сушку в вакууме используют для высокочистых химических продуктов, термочувствительных и взрывоопасных материалов и т.п. ОАО «НИИХиммаш» выпускает вакуумные роторные сушилки моделей PB1, РВ2-4 и ОВК-3 периодического действия для сушки продуктов в жидком, пастообразном и сыпучем состоянии, в том числе токсичных или взрывоопасных
(рис. 3.5).
Рис. 3.5. Роторная вакуумная сушилка модели PB1, ОАО «НИИХиммаш»
Сушилка представляет собой цилиндрический горизонтальный корпус с паровым обогревом, снабженный ротороммешалкой. Специальная конструкция ротора позволяет сушить жидкие, пастообразные и сыпучие продукты с получением агломерированного или порошкообразного сухого материала. В установке отсутствуют газовые выбросы в атмосферу, а испаренная влага конденсируется и возвращается в замкнутый производственный цикл. Давление обогревающего пара составляет 0,5 МПа, остаточное давление в сушилке – 13,3 кПа. Этот тип
95
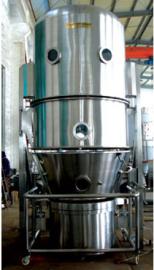
оборудования может быть использован для сушки осадков сточных вод и гальванических шламов.
Вакуумная сушка в псевдоожиженном слое производства
Changzhou Jiafa Granulating Drying Equipment (Китай) предназна-
чена для отгонки органических растворителей при сушке гранул, а также плакирования последних пленками (рис. 3.6). Камера сушилки вмещает 0,005–1,6 м3 исходного материала, который продувается воздухом, нагретым до 80 °С, циркулирующим по замкнутому контуру с расходом 200−15000 м3/ч. В процессе сушки в камере поддерживается остаточное давление в пределах
1,5−40 кПа.
В установках для сублимационной сушки влага удаляется из продукта в замороженном состоянии при остаточном давлении 5−1·102 Па, а требуемое тепло подводится к материалу путем контакта с нагретой поверхностью или излучением от нагретых экранов.
Сушильная установка состоит из цилиндрического сублиматора, снабженного пустотелыми плитами, обогреваемыми горячей водой, на которые устанавливаются поддоны с высушиваемым материалом. Испаренная влага направляется в трубчатый вымораживательконденсатор, присоединенный к вакуумному насосу.
Основным достоинством технологии сублимационной сушки является сохранение после сушки основных биологических параметров материала и малый удельный расход тепла. Сублимационная сушка применяется
96
в пищевой промышленности для сушки продуктов (фрукты, кофе, чай, мясо, дрожжи, яичные и молочные продукты, и др.), а также неустойчивых к нагреву (термолабильных) химических продуктов – белковых препаратов, растительных экстрактов, красителей в фармацевтической промышленности. Сублимационной сушкой также получают большинство лекарственных препаратов (антибиотиков, сывороток, вакцин, плазмы, гормонов, витаминов).
3.4. Фильтрация в вакууме
Технология фильтрации в вакууме применяется для разделения суспензий и в некоторых случаях для разделения коллоидных растворов. Процесс фильтрации осуществляется пропусканием суспензии через фильтроматериал – песок, металлические сетки, пористые керамические плиты и чаще всего через ткань.
Жидкость (или фильтрат) проходит через фильтр и удаляется, твердые частицы отделяются в виде осадка.
В вакуумных фильтровальных установках фильтруют легко фильтрующиеся и в первую очередь кристаллические вещества. Перепад давления в вакуумном фильтре создается откачкой воздуха со стороны пористого фильтрующего слоя, при условии, что суспензия перед фильтром находится под атмосферным или избыточным давлением. Благодаря разности между атмосферным давлением с одной стороны фильтра и вакуумом – с другой, жидкость продавливается сквозь слой фильтрующего материала. Традиционно остаточное давление воздуха под фильтром поддерживается в диапазоне 6,6·102−2,6·104 Па.
Различают два основных типа вакуумных фильтров – непрерывного и периодического действия. Вакуумные фильтры непрерывного действия обычно предназначены для вполне определенного продукта, так как свойства подводимой суспензии должны оставаться неизменными в течение всего процесса. К вакуумным фильтрам непрерывного действия относятся раз-
97

личные модификации барабанных фильтров (рис. 3.7), дисковые, тарельчатые и ленточные фильтры. К вакуумным фильтрам периодического действия относят фильтры с жесткой неподвижной фильтрующей перегородкой, листовые или мешочные фильтры (рис. 3.8) и нутч-фильтры с тканевой перегородкой – наиболее простые по устройству, работающие при давлении под фильтром в диапазоне 5·104−7·104 Па.
Рис. 3.7. Барабанный вакуум-фильтр непрерывного действия: 1 – распределительная головка (золотниковый механизм); 2 – распределитель воды для промывания осадка; 3 – перегородки; 4 – труба для подачи сжатого воздуха; 5 – нож для срезания осадка; 6 – корыто; 7 – барабан; 8, 9 – трубы для откачки отфильтрованной жидкости (8) и промывной
воды (9)
Вакуумные барабанные фильтры, работающие при остаточном давлении 6,5·102 Па, получили широкое распространение в производствах по обогащению руд черных и цветных металлов. Барабанные вакуумные фильтры без центрального золотника применяются в целлюлозно-бумажной промышленности.
98

Рис. 3.8. Мешочныйвакуум-фильтр периодического действия: 1 – решетка; 2 – фильтрующая поверхность (ткань, сетка, пористые керамические плитки); 3 – суспензия; 4 – резервуар; 5 – осадок; 6 – штуцер, соединенный со сборником фильтрата и вакуум-насосом
Наибольшее применение вакуумные фильтры находят в технологических процессах фильтрации пульп с относительно крупными твердыми частицами.
3.5. Выпаривание в вакууме
Техпроцесс выпаривания в вакууме применяется в химическом производстве для повышения концентрации растворов или полного удаления из них растворителей. В процессе выпаривания чаще всего происходит кипение раствора, находящегося в аппарате, и удаление образующегося пара. Выпаривание применяется в основном в тех случаях, когда образующиеся пары не являются ценными по сравнению с остатком. Кроме того, иногда выпаривание служит для выделения растворителя в чистом виде, например, при опреснении воды.
Выпаривание в вакууме осуществляется при пониженной температуре кипения. Для обогрева выпарного аппарата применяется либо отработанный пар, либо пар низкого давления. Процесс выпаривания происходит в однокорпусных или многокорпусных вакуумных установках. В случае, когда количество выпаривае-
99

мой жидкости достаточно велико, применяют многокорпусное выпаривание, при котором тепло для выпаривания используют многократно, путем применения вторичного пара для обогрева. Если выпариваются не водные растворы, то в качестве вторичного пара используют пары растворителя, в котором было растворено концентрируемое вещество.
а |
б |
в |
г |
д |
е |
Рис. 3.9. Схемы вакуумных установок для выпаривания: а – одноступенчатого (теплообмен между холодным слабым раствором
ивозвращающимся сгущенным раствором); б – одноступенчатого (теплообмен между холодным слабым раствором и вторичным паром); в – двухступенчатого (теплообмен между холодным слабым раствором
ивторичным паром); г – со сжатием вторичного пара (теплообмен
между слабым и сгущенным растворами); д – одноступенчатого
впленочном испарителе (теплообмен как в случае с промежуточным охлаждением раствора); е – пленочного (слабый раствор использован
вкачестве конденсирующего агента, промежуточное охлаждение сгущенного раствора). 1 – выпарной аппарат с греющими трубами; 2 – пленочный выпарной аппарат; 3 – поверхностный конденсатор; 4 – вакуумный насос; 5 – теплообменник; 6 – тепловой насос
100