
2774.Вакуумные технологии
..pdfкак снижение внутреннего трения. Это позволяет получать прессовки из нанопорошков с повышенной плотностью. Причем роль данного эффекта усиливается при уменьшении среднего размера частиц в порошке (т.е. при снижении прессуемости);
благодаря адиабатичности процесса (отсутствию теплообмена) мягкое импульсное прессование характеризуется значительным импульсным нагревом прессуемого порошка, что повышает его деформируемость (за счет роста пластичности), а также стимулирует структурно-фазовые превращения;
за счет малого времени протекания процесса импульсного прессования в ряде случаев удается сохранять метастабильные структурно-фазовые состояния нанопорошков, предпочтительные для формируемого объемного наноматериала.
Созданная в Институте электрофизики экспериментальная установка МИП экономична, допускает автоматизацию процесса. Импульсное прессование нанопорошков может производиться при температурах до 600 °С в условиях вакуума после термической дегазации, обеспечивающей удаление адсорбированных веществ с поверхности частиц.
В имеющихся установках МИП двух типов реализовано прессование с использованием плоских и радиально сходящихся волн сжатия.
Магнитно-импульсное прессование имеет ряд преимуществ: простота оборудования, безопасность, высокий КПД и большие импульсные давления. В отличие от традиционных методов прессования, воздействие импульсных волн сжатия сопровождается интенсивным разогревом порошка за счет быстрого выделения энергии при трении частиц в процессе переупаковки. В определенных условиях варьируя параметры волны сжатия можно реализовать динамическое горячее прессование нанопорошка за счет его высокой поверхностной энергии. При одинаковой величине давления прессования магнитно-импульсный метод позволяет получать более плотные компактные образцы, чем традиционный метод прессования. Так, порошки нитрида алюминия, по-
281
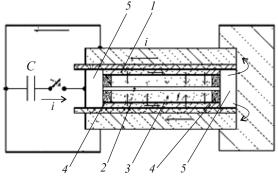
лученные электровзрывом, прессуются магнитно-импульсным методом под давлением 2 ГПа до плотности 95 % от теоретической, а оксида алюминия – до 86 %. Метод может быть использован для получения изделий различной формы, причем в большинстве случаев эти изделия не требуют дополнительной механической обработки. В частности, при проведении работ по прессованию сверхпроводящих оксидных керамических материалов из нанокристаллического порошка диоксида циркония были получены изделия с плотностью более 95 % от теоретической.
Для прессования длинномерных заготовок из нанопорошков в форме труб и стержней отработана техника магнитно-импульс- ного сжатия тонкостенных медных трубчатых оболочек (рис. 12.22). Такая оболочка выполняет функцию радиально сходящегося цилиндрического пуансона. Используется принцип радиального сжатия оболочки под действием давления магнитного поля, генерируемого протекающим вдоль трубы большим импульсным током (схема Z-пинча).
Рис. 12.22. Схема установки для прессования длинномерных заготовок из нанопорошков
Перед прессованием порошок 3 укладывается в трубчатую полость между медной трубой 1 и стержнем 2 из твердого материала, выполняющего функцию формирования канала. После дегазации порошка внутри специального бокса осуществляется
282
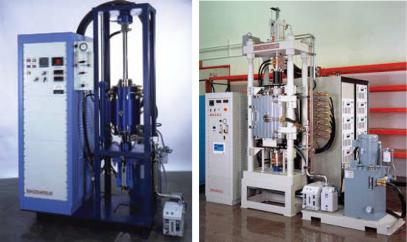
газоплотное |
капсулирование |
пресс-формы in situ (на месте) |
с помощью |
прокладок 4 и 5. |
Это позволяет манипулировать |
с пресс-формой на воздухе, не опасаясь вторичного проникновения в прессуемый порошок адсорбируемых веществ. Подготовленная пресс-форма подключается к генератору импульсных токов с емкостным накопителем энергии С. В ходе прессования большой импульсный ток протекает вдоль медной оболочки и возвращается к генератору по осесимметричной массивной внешней металлической трубе.
Горячее прессование – метод компактирования в условиях повышенных температур, получивший в настоящее время широкое распространение. Горячим называют прессование порошка при температуре, превышающей температуру рекристаллизации основного компонента. Пресс-форма с изделием после ее охлаждения до 500–600 °С (гидравлический пресс) или до 150–200 °С (вакуумный пресс) удаляется из пресса, изделие извлекается и зачищается на шлифовальном станке (рис. 12.23, а).
а |
б |
Рис. 12.23. Вакуумный пресс горячего прессования (а), установка электроискрового спекания (б)
283
В первую очередь горячее прессование применяют для компактирования изделий из нанопорошков тугоплавких металлов. Полученные прессовки из Та и Nb имеют пористость менее 1 %, а прочность на растяжение в 2–2,5 раза выше по сравнению с литым материалом.
Горячим прессованием также получают компактные заготовки из карбида бора, композиций WC-Co нескольких составов. Микротвердость и предел текучести этих прессовок превышают соответствующие значения для материалов из традиционных твердых сплавов. Плотность полученных образцов составляла 97–99 % от теоретической.
Некоторые из защитных составов могут одновременно играть роль смазок, уменьшающих внешнее трение. Кроме того, для предохранения прессуемого материала от окисления применяют защитные газовые среды (восстановительные, инертные) или вакуумирование.
Особым случаем горячего прессования является электро-
разрядное, или электроимпульсное (искровое, плазменно-искро-
вое) спекание: через порошок с помощью электродов-пуансонов, к которым приложено давление, пропускают сильный электрический разряд (рис. 12.23, б).
Плазменно-искровое спекание (SPS) использует высокоточный импульс постоянного тока для быстрого и равномерного распространения энергии плазмы между частицами. Системы плазменно-искрового спекания могут работать с проводниками, диэлектриками, с композитными материалами различной плотности, в том числе полной, с большой гомогенностью, а также с материалами с большой силой связи между частицами.
Процесс плазменно-искрового спекания SPS основан на явлении разряда электрической искры, мощный импульс тока моментально генерирует искровую плазму при высоких локальных температурах (до 10 000 °С) между частицами (рис. 12.24). Энергия искры испаряет примеси и окисную пленку на поверхности частиц до формирования контактных областей. Джоулева тепло-
284
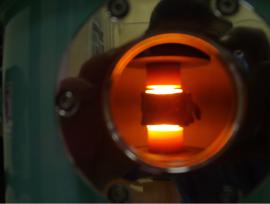
та концентрируется на поверхностях частиц, производя пластическую деформацию и оказывая влияние на высокую плотность получаемого материала. Процесс SPS прессования ведется с усилием до 300 т в зависимости от размеров установки. Процесс осуществляется в вакууме с возможностью использовать инертную атмосферу. Регулирование температуры происходит с использованием термопар и пирометров.
Рис. 12.24. Процесс получения образца оптически прозрачной керамики на основе шпинели методом
SPS на установке Doctor SinterLab
Преимущества плазменно-искрового спекания:
равномерный нагрев по всей длине образца;
не требуется предварительная обработка и сушка;
однородное спекание разнородных веществ;
легкость в использовании;
короткий цикл работы;
выход содержащихся сорбированных газов и газовпримесей в процессе предварительной откачки и спекания;
минимальный рост зерен;
минимальное влияние на микроструктуру;
низкая стоимость эксплуатации.
285
Системы плазменно-искрового спекания включают в себя: 1) удаленную компьютерную станцию управления процес-
сом;
2)сбор и обработку данных;
3)современный очиститель;
4)полностью запрограммированную подачу питания и поддержания температуры и давления;
5)контролируемый сервораспределитель;
6)фронтальную загрузку образцов;
7)прикладываемое усилие 10–250 т;
8)источник питания 3000–60 000 А.
12.3. Нанотехнологические комплексы на базе различных платформ
Группа компаний НТ-МДТ на протяжении многих лет разрабатывала концепцию создания многофункциональных кластерных нанотехнологических комплексов, интегрирующих широкий спектр самого современного научного и технологического оборудования от ведущих мировых производителей.
Платформы НАНОФАБ-25 и НАНОФАБ-100 – модульные технологические платформы для формирования нанотехнологических комплексов (НТК) с кластерной компоновкой, включающих в себя технологические установки с возможностями групповых и нанолокальных методов обработки подложек диаметром 25 и 100 мм соответственно. Платформы представляют собой совокупность кластеров, каждый из которых состоит из нескольких технологических модулей, объединенных общей транспорт- но-распределительной системой (рис. 12.25).
Кластеры могут ориентироваться как на технологии групповой обработки (лазерная абляция, газофазное осаждение, молеку- лярно-пучковая эпитаксия и т.д.), так и на исследования и технологии нанолокальной обработки. К последним относятся модули сканирующей зондовой микроскопии (СЗМ) (вместе с модулями растровой электронной микроскопии (РЭМ), фокусированных
286
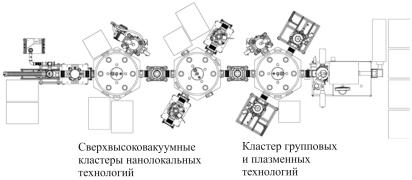
ионных пучков (ФИП), масс-спектрального анализа (МСА) и некоторыми другими). Методы СЗМ используются для оценки качества поступающих пластин (входной контроль), для исследования пластин, прошедших через ту или иную технологию обработки (межоперационный контроль), а также для тестирования свойств готовых наноэлектронных элементов и схем (функциональный контроль). При формировании НТК кластеры объединяются в технологические цепочки через модули межоперационной передачи и складирования образцов. Это позволяет на основе платформ создавать нанофабрики для разработки полнофункциональных наноструктур, а также наноустройств и наносистем.
Рис. 12.25. Пример компоновки 3-кластерного НТК на базе платформы НАНОФАБ-100
Возможности НАНОФАБ реализуются за счет кластерной компоновочной схемы – связь между образующими кластер функционально объединенными технологическими модулями осуществляется с помощью сверхвысоковакуумного радиального робота-раздатчика, обеспечивая минимальное время межоперационной передачи образцов и, следовательно, сохранение совершенно необходимой в нанотехнологии атомарной чистоты поверхности. Наличие модулей передачи подложек с устройствами переворота обеспечивает возможность проведения сложных технологических циклов с включением групповых и нано-
287
локальных процессов, а также проведение необходимых кон- трольно-измерительных и аналитических процедур. Развитая транспортная система с модулями межоперационного хранения подложек позволяет в одном НТК НАНОФАБ реализовать одновременно несколько технологических циклов на нескольких подложках, допуская, таким образом, использование НТК несколькими исследовательскими группами.
Помимо модулей в состав НАНОФАБ входят также и отдельные технологические, контрольные, измерительные, аналитические и другие устройства. Для их использования модули НАНОФАБ снабжены достаточно большим количеством портов, позволяющих расширять при необходимости их возможности. Модули платформы НАНОФАБ могут функционировать как в составе НТК, так
иавтономно, в отдельных случаях с использованием вспомогательных загрузочныхустройств или модулей загрузки.
НАНОФАБ является открытой и постоянно развивающейся
ирасширяющейся платформой – в разработке постоянно находится несколько модулей, использующих новейшие технологии.
Области применения НТК НАНОФАБ покрывают практически все поле нанотехнологических исследований и разработок, связанных с твердотельными наноматериалами, наноструктурами и наноустройствами. Спектр возможностей НАНОФАБ – от проведения фундаментальных исследований до отработки отдельных технологических приемов и моделирования наноэлектронных устройств.
Компоновочные схемы, система управления и развитая транспортная система НТК НАНОФАБ позволяют применять их также и для мелкосерийного производства наноструктур и наноустройств.
Координатно-связанная система позиционирования подложек позволяет создавать сложные многокомпонентные 3D наноустройства путем проведения в различных модулях последовательных нанотехнологических операций с нанометровым разрешением (рис. 12.26).
288
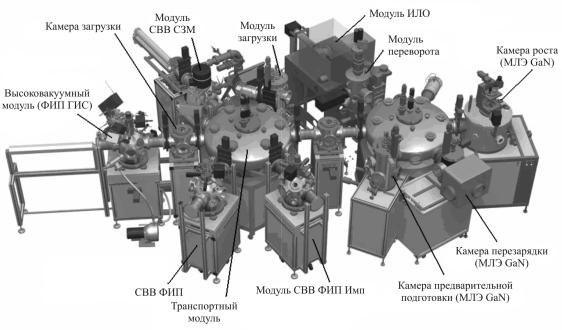
289
Рис. 12.26. Пример компоновкимодулейНТКНАНОФАБ-100 кластерного типа(Таганрогскийтехнологический институт Южного федерального университета): ФИП ГИС – фокусированные ионные пучки с системой газовых инжекторов, CВВ – сверхвысоковакуумный, ИЛО – импульсное лазерное осаждение, МЛЭ – модуль молекулярно-лучевой эпитаксии
Особенно важной является область применения НТК НАНОФАБ для технологических разработок в области современной кремниевой электроники, давно уже вступившей в область реальной наноэлектроники.
Особый интерес представляют собой исследовательские нанотехнологические комплексы, создаваемые при уникальных установках, таких как синхротроны, импульсные лазеры на свободных электронах и др. Разработка специальных аналитических модулей, таких как модули электрофизических измерений, совмещенные с модулями рентгеновской спектроскопии и в особенности высокоразрешающей рентгеновской микроскопией, позволит наряду с высоким пространственным (порядка 10 нм) получать и высокое временное разрешение, что в свою очередь позволит изучать квазиобратимые динамические процессы в наноструктурах с разрешением по времени порядка 0,1 нс на синхротронах и еще на несколько порядков выше – на лазерах на свободных электронах.
Потребность в оснащении вновь разрабатываемого оборудования технологиями, в особенности в такой области, как наноэлектроника, МЭМС и НЭМС требует организации плотной кооперации как с Национальной лабораторией нанотехнологии «Курчатовский институт», так и с головным предприятием по наноэлектронике, в качестве которого определен Зеленоградский научно-исследовательский институт физических проблем (НИИФП) им. Ф.В. Лукина, ставший в настоящее время стратегическим партнером группы НТ-МДТ, в котором силами Института ядерной физики (ИЯФ) СО РАН и группы НТ-МДТ развернуты работы по запуску центра высоких технологий с использованием аналитических и технологических возможностей модифицированного синхротрона серии «Сибирь-2» и уже ведется разработка технологических решений для мощных нанотехнологических комплексов линии НАНОФАБ (рис. 12.27).
290