
1236
.pdfпостроена и пущена в эксплуатацию шахтная печь шириной в об ласти фурм 1,6 м при длине 11,7 м. Это позволило превратить печь в высокопроизводительный агрегат, проплавляющий свыше 800 т шихты в сутки. Шахтная печь для свинцовой плавки состоит из трех основных частей: горна, шахты и колошникового шатра.
Шахта печи кессонированна. Кессоны установлены по высоте шахты печи в два или три ряда. Устройство их примерно такое же, как у шахтной печи для медной плавки. Сверху шахта печи рас ширена из-за наклонного расположения первого ряда боковых кессонов. Общая высота шахты от горна загрузочной площадки печи достигает 6—7,5 м. В торцах печи также установлены кес соны, называемые торцовыми; их располагают вертикально. Через торцовые кессоны печи выпускают шлак. Для выпуска расплава торцовые кессоны имеют проемы, в которые устанавливают ма лый водоохлаждаемый выпускной кессон.
Горн печи расположен непосредственно под шахтой печи и яв ляется как бы ее продолжением. Поэтому размеры горна соответ ствуют размерам печи в области фурм, а глубина горна колеб лется в пределах 500—600 мм. Горн устанавливают на бетонный фундамент, на поверхность которого кладут слой глины, а затем стальную плиту толщиной 20 мм.
Горн выкладывают всухую впритирку из огнеупорных изделий в кожухе, изготовленном из листовой стали. Снаружи горн скреп ляют двутавровыми балками. Лещадь горна имеет форму обрат ного свода, что препятствует разрушению кладки просочившимся свинцом. Жидкие продукты плавки собираются в области горна печи и расслаиваются по плотности: черновой свинец собирается в нижней части горна, шлак — в верхней. Черновой свинец из горна выпускают через особый канал сечением 200 X 200 мм, на зываемый сифоном. Сифон работает по принципу сообщающихся сосудов. Когда горн наполняется расплавленной массой, черновой свинец под давлением массы столба и дутья заполняет весь си фон и затем по желобу стекает непрерывно в приемный ковш. При бедной шихте, когда выплавляют меньше свинца, его выпус кают периодически.
Достоинство сифона заключается в том, что в горне всегда есть слой расплавленного свинца, что обеспечивает непрерывный выпуск металла. Уровень свинца в горне регулируют порогом из глины, набиваемым в сифонном желобе. При правильном уровне сифонного порога свинец вытекает через сифон и не уходит вместе со шлаком и штейном. Если сифонный порог поднят выше нормы, то часть свинца уносится со шлаком; если порог спущен ниже нормы, в сифон попадает шлак.
Шлак удаляют из печи через летку выпускного кессона, назы ваемого беби-кессоном, который находится в торцовом кессоне печи ниже фурм. По чугунному желобу шлак поступает в перед ний отстойник. Продукты плавки выпускают из шахтной печи пе риодически по мере накопления. При форсированной работе печи шлак выпускается непрерывно.
Шахтная печь для плавки окисленных никелевых руд
Шахтная печь для плавки окисленных никелевых руд на штейн состоит из тех же элементов, что и другие шахтные печи заводов цветной металлургии. От шахтной печи, применяемой в металлур гии меди, она отличается большими размерами. На рис. 12 пока зана такая печь с наружным горном и кессоном испарительного охлаждения.
Основными частями печи являются фундамент, внутренний горн, шахта, колошник и наружный отстойный горн. Чтобы печь могла работать, требуется еще ряд непосредственно примыкаю щих к ней устройств. Так, печь имеет кольцевой воздухопровод с многочисленными отводами-рукавами для подачи воздуха впечь,
кольцевой водопровод и паропровод для подачи воды в |
кессоны |
и для отвода пароводяной смеси. Наконец,, у колошника |
печи и |
у ее горна имеются рабочие площадки. На первой площадке уло жены узкоколейные пути. По ним движутся загрузочные вагоны (троллейкары) с шихтой. Эта площадка называется колошнико вой. Вторая, нижняя, служит для ухода за горном печи и вы носным горном. Ширина современной шахтной печи в области фурм составляет 1,5—1,7 м, на уровне колошника 1,4—1,5 м; вы сота шахты 4,5—6 м. Площадь сечения печи на уровне фурм 18— 25 м2. Внутренний горн печи монтируют на железобетонном фунда менте.
Горн печи — это открытый сверху прямоугольный ящик, кото рый опирается на два ряда чугунных колонок высотой 500—600 мм, установленных на фундаменте. Собранное этим способом дно горна легко доступно для осмотра, а воздушная прослойка способствует охлаждению дещади горна. Лещадь и боковые стенки горна печи смонтированы из комплекта чугунных плит с залитыми в них хро момагнезитовыми кирпичами. В последнее время в тело чугунных плит заливают также стальные трубчатые змеевики для циркуля ции охлаждающей воды.
Плиты скрепляют между собой болтами, а боковые плиты крепят металлическими стойками, устанавливаемыми на стыках плит. Внутреннюю часть горна футеруют хромомагнезитовыми изделиями. Длина и ширина горна печи соответствуют длине и ширине печи. Высота или глубина ванны горна составляет 0,6— 0,8 м. Расстояние от плоскости фурм до лещади горна колеблется в пределах 1,1—1,2 м. В продольной стенке горна печи делают в за висимости от длины печи по одному-два отверстия для’ присоеди нения наружного горна. На больших печах устанавливают два наружных горна. Один из них — резервный.
Шахта печи состоит из фурменной водоохлаждаемой коробки (кессона) и кессона испарительного охлаждения. Кессоны уста навливают на края облицовочных плит и они образуют шахту, расширяющуюся книзу (угол 85°). Между собой кессоны скреп лены пластинами, приваренными по всей их высоте. Колошник над
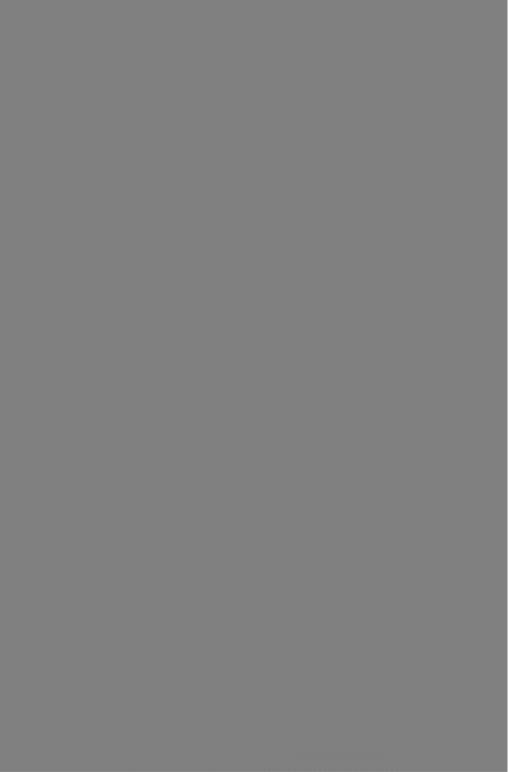
печью состоит из кессонов испарительного охлаждения. По про дольным сторонам колошника расположены загрузочные окна, пе рекрытые вертикально подвешенными на петлях шторами.
Детали шахтных пеней
Кессоны, охлаждаемые водой, имеют форму коробки высотой 5,0— 6,0 м, шириной 0,75—0,90 м и внутренним расстоянием между стенками 100—150 мм. Кессоны сваривают лз листовой сталитолщиной 10—18 мм. Внутреннюю огневую стенку кессона делают толще наружной на 4—6 мм, ,так как она воспринимает нагрузку от давления шихты и подвергается тепловым и механическим воз действиям шихты. Для охлаждения кессона в него бесперебойно подают воду. Вода поступает в нижнюю часть кессона и отводится
Рис. |
13. |
Кессон |
испарительного |
||||
охлаждения: |
|
|
|
|
|
||
/ — подвод |
умягченной |
воды; |
2 — люк |
||||
для очистки кессона; |
3 — фурма; |
4 — |
|||||
кессон |
на |
водяном |
охлаждении; |
5 — |
|||
патрубок |
для |
отвода |
воды; |
6 — кол |
|||
лектор |
нагретой воды; |
7 — толстостен |
|||||
ная труба |
испарительного кессона; |
8 — |
|||||
крепление |
для |
переноски кессона; |
9 — |
коллектор с патрубком отвода паро
водяной |
смеси; 10 — патрубок; |
/ / — |
труба с |
заглушенными концами; |
12 — |
патрубок подвода воды к трубе (испа рительному элементу)
в верхней его части. Температура воды, выходящей из кессона, не должна подниматься выше 50—60 °С.
При водяном охлаждении с водой теряется до 20 % тепла, расходуемого на плавку. Для использования этого тепла в послед ние годы кессоны с водяным охлаждением на шахтных печах частично заменили на кессоны с испарительным охлаждением. Применение этих кессонов позволяет сократить расходы воды при мерно в 20—25 раз и получать пар под давлением до 1,4 МПа для технологических нужд предприятия; охлажденная вода возвраща ется в кессоны. Кессон шахты печи (рис. 13) состоит из фурмен ного кессона, охлаждаемого водой, высотой 0,7 м и шириной 0,9 м, и кессона испарительного охлаждения высотой 5,3 м и шириной
0,9 м. Кессон испарительного охлаждения состоит из восьми сва ренных между собой труб диаметром 108 мм и толщиной стенок 14—16 мм. Для увеличения теплопередающей поверхности в центре каждой, трубы установлена труба меньшего диаметра с заглушен ными концами. Химически очищенная вода поступает в нижнюю часть фурменного кессона, откуда в подогретом состоянии через коллектор и патрубки распределяется по трубчатым элементам кессона испарительного охлаждения. В верхней части этого кес сона расположен коллектор для отвода из трубчатых элементов пароводяной смеси в бак-сепаратор, где происходит отделение пара от воды. Вода собирается в нижней части сепаратора и по ступает снова в кессоны. Пар заполняет верхнюю часть сепара тора и отводится потребителю.
Все боковые кессоны при шахтной плавке медных руд имеют, как правило, по три отверстия для фурм диаметром 100—120 мм, а при плавке окисленных никелевых руд — по одному отверстию диаметром 200 мм. Число и диаметр фурм для шахтных печей выбирают в зависимости от фурменного отношения. Фурменным отношением называется отношение площади поперечного сечения всех фурм к площади сечения печи на уровне фурм, выраженное в процентах. Фурменное отношение зависит главным образом от вида плавки. Так, при плавке медных руд фурменное отношение составляет от 5—6 до 8—10 % площади сечения печи, при плавке окисленных никелевых руд 7,5—10 %.
Выпускной кессон. Для непрерывного выпуска штейна и шлака из шахтной печи медной плавки служит малый медный кессон (рис. 14). В тело кессона залит змеевик для водяного охлажде ния. В нижней части кессона имеется отверстие для выхода рас плавленной массы. Диаметр отверстия зависит от величины печи и ее производительности и составляет 150—200 мм. С наружной стороны кессон имеет прилив для установки желоба. По желобу продукты плавки поступают в наружный передний горн. Желоб также медный, литой, с змеевиком для водяного охлаждения. Же лоб футерован огнеупорами. В передней части его установлен по рог из глины, который создает затвор, предупреждающий выброс газа из печи через выпускное отверстие.
Наружный отстойный горн. При шахтной плавке медных, окис ленных никелевых и свинцовых руд шлак и штейн выпускают из печи вместе в наружный передний горн для отстаивания и разде ления. Штейн, более плотный и тяжелый, опускается в нижнюю часть горна, а шлак, более легкий, занимает верхнюю часть горна и непрерывно стекает в шлаковый ковш или его гранулируют. Грануляция состоит в том, что струя жидкого шлака стекает в же лоб на быструю струю воды, которая разбивает шлак на мелкие кусочки — гранулы. Гранулы по желобу поступают вместе с во дой в грануляционный бассейн, из которого их выбирают грейфер ным краном в вагоны п отвозят в отвал. Штейн выпускают перио дически в зависимости от потребности конвертерного передела^. Отверстия для выпуска штейна, или шпуры, забиты огнеупорной
глиной. Через глиняную пробку пропущен длинный металлический ломок. Для выпуска штейна ломок выбивают.
Для хорошего отделения шлака от штейна при медной плавке важное значение имеет объем горна и соотношение его размеров. Размеры горна зависят от производительности шахтной печи или от площади сечения печи в области фурм. Практика работы на шахтных печах при плавке медных руд показывает, что емкость наружного горна должна составлять 5—9 м3 на каждые 100 т су точного проплава печи.
Рис. |
14. |
Выпускной кессон: |
|
/ — прилив |
для крепления медного жело |
||
ба; |
2 — патрубок для подвода воды; 3 — |
||
тело |
кессона; 4 — змеевик; |
5 — патрубок |
|
для выпуска воды |
|
||
Наружный горн представляет собой большую ванну |
из сталь |
ных листов, футерованную изнутри огнеупорными изделиями. Ко жух горна скреплен с наружной стороны двутавровыми балками, а по верху стянут тягами из круглой стали. В верхней части горна по мере накопления шлака образуется корка из остывшего шлака, предохраняющая горн от промерзания. Штейн выпускают через шпуровые отверстия по желобам в штейновые ковши. Выпускное отверстие для штейна выложено из хромомагиезитового кирпича и укреплено специальными чугунными плитами.
Наружные горны шахтной печи свинцовой плавки делают пе редвижными объемом 2—4 м3 или стационарными (обогреваемые электроотстойники объемом 12—16 м2, мощностью до 2500 кВ-А).
Для отделения шлака от штейна в шахтной печи для плавки окисленных никелевых руд имеется вертикальный цилиндрический передний горн. Ом (см. рис. 12) представляет собой цилиндр из котельной стали с днищем и сводом. Изнутри его футеруют хро момагнезитовыми изделиями с засыпкой между кожухом и клад кой магнезитового порошка. Наружный горн соединен с внутрен ним горном закрытым каналом. Расплавленная масса из внутрен него горна печи поступает по каналу в нижнюю часть наружного горна. В горне штейн отделяется от шлака. Шлак из горна вы пускают непрерывно, а штейн — по мере накопления.
Колошниковое устройство служит для загрузки шихты и от вода газов. Колошник монтируют из кессонов испарительного или водяного охлаждения. Он может быть изготовлен из металличе ского каркаса, заполненного кладкой из шамотного огнеупора.
Обслуживание шахтной печи
Обслуживание шахтной печи сводится в основном к обеспечению набора из бункеров шихты и загрузке ее в печь вместе с коксом, подаче в печь необходимого количества воздуха и выпуску из нее продуктов плавки. Рабочие, обслуживающие печь, должны регу лярно наблюдать за состоянием фурм и через каждые два часа их пробивать ломом, а также следить за циркуляцией воды и па роводяной смеси в охлаждающих элементах и кессонах. Загрузка печи — одна из самых важных операций, определяющих успешную работу печи. В обязанности рабочего-загрузчика входит следующее: точная дозировка материала в соответствии с заданным; загрузка шихты с обеих сторон печи; равномерное распределение материа лов по длине печи; соблюдение установленного порядка загрузки материалов в печь (особенно важно в начале загрузить кокс, бес полезное горение которого на поверхности сыпи печи не допуска ется); загрузка шихты в печь через одинаковые интервалы вре мени и поддержание установленной высоты сыпи.
Наиболее важный показатель работы шахтной печи — удельная производительность (проплав), которую определяют количеством шихты или руды (агломерата) в тоннах без кокса, проплавляемой на 1 м2 сечения печи в области фурм в сутки. Если печь сече нием 20 м2 проплавила 200 т агломерата за 6 ч (за смену), то удельный проплав составит (200 X 4) : 20 = 40 т/(м2-сут). Суточ ный проплав печи составит 40X20 = 800 т агломерата. Согласно практическим данным, удельная производительность при плавке медной шихты составляет 40—120 т/м2, свинцовой 60—80 т/м2, при плавке окисленной никелевой руды 28 т/(м2-сут) или 40 т/м2 агло
мерата.
Зная удельную производительность и количество руды (шихты), проплавляемой в сутки, можно определить необходимую площадь сечения печи в области фурм по формуле F = А/а, где А — задан ная производительность печи по руде (агломерату, шихте), т/сут;
а — удельная |
производительность по руде |
(агломерату, шихте), |
т/(м2*сут). |
|
|
П ри м ер . |
Определим площадь сечения |
печи в области фурм, |
перерабатывающей 560 т/сут окисленной никелевой руды. Исходя из практических данных, примем удельный проплав а для нашего случая равным 28 т/(м2-сут). Определим площадь сечения печи на уровне фурм: F = А : а = 560 : 28 = 20 м2.
Шахтные печи имеют прямоугольное сечение: приняв ширину печи В = 1,6 м, подсчитаем ее длину /: / = F : В = 20 : 1,6 = 12,5 м. Высоту печи и размеры кессонов примем на основании практиче ских данных.
§ 4. Отражательные плавильные печи
Основным способом производства меди до последнего времени яв ляется отражательная плавка (65 % от общего производства в СССР и 53% в США), что объясняется простотой процесса и относительно невысокими капитальными вложениями. За послед-
Рис. 15. Отражательная печь с подвесным сводом для плавки медьсодержащих шихт:
^ — форсуночное окно; 2 — отверстия |
загрузки шихты; 3 — шпуровые отверстия; 4 — |
шлаковое окно; 5 — аптейк |
|
ние годы произошли значительные изменения в конструкции от ражательных печей: увеличилась площадь печи, изменился способ загрузки шихты, внедрена боковая загрузка вместо сводовых во ронок. Наряду с основными торцовыми горелками установлены горелки для плавления шихты в своде печи. Развитие процесса отражательной плавки идет по пути применения подогретого дутья, кислорода и природного газа. Современная отражательная печь
показана на рис. 15. Внутренние размеры отражательных печей следующие: длина 28—32 м, ширина 6—10 м, высота 4 м. Пло щадь пода отражательных печей составляет 200—330 м2.
Конструкция отражательных печей
Фундамент является наиболее ответственной частью отражатель ной печи. Его обычно выполняют из железобетонного пояса-рамы, который заполняют кладкой из бутового камня и кирпича. Фунда мент делают шире печи, чтобы на нем можно было установить вертикальные балки крепления печи. Боковые и торцовые стенки печи возводят из динасового кирпича. Внутреннюю кладку стен на всю высоту ванны печи делают из высокоогнеупорного хромомаг незитового кирпича, хорошо противостоящего разъедающему дей ствию штейна и шлака. Толщина стен в области расплава (штейна и шлака) составляет 1500 мм, а в верхней части 600 мм. Через каждые 3 м в кладке оставляют температурные швы, рассчитан ные на расширение кирпича при нагревании. Стены крепят колон нами, нижние концы которых закрепляют в фундаменте, а верх ние концы противоположных колонн стягивают специальными тя гами.
Под или лещадь печи выкладывают между стенами печи на фундаменте из нескольких рядов динасового или хромомагнезито вого кирпича в виде свода с обратной аркой. Верхнюю часть пода набивают из чистого кварцевого песка (95 % SiC^) с примесью 5—8 % огнеупорной глины слоями по 100 мм специальными трам бовками. Толщина набивного кварцевого пода равна 700 мм. Для придания поду прочности перед пуском печи кварцевую набивку наваривают при 1500—1600 °С.
Современная отражательная печь имеет арочный или подвес ной свод. Он состоит из нескольких секций длиной от 3—4 до 7,5 м. Между секциями оставляют промежутки 60—70 мм, которые за полняют деревянными плитками. При разогреве и работе печи деревянные плитки выгорают и промежутки в результате тепло вого расширения огнеупора закрываются. Пролет свода печи до стигает 10 м, толщина свода 380—520 мм. Особое значение имеет размер стрелы свода. В отражательных печах стрела свода равна
примерно V12 от его пролета.
Арочный свод, выложенный из динасового кирпича, опирается на пятовые кирпичи, которые кладут в швеллерные балки с обеих сторон печи, и удерживается креплением печи. В связи с возрас танием тепловых нагрузок, а также с увеличением ширины печи многие заводы устанавливают на печах подвесные или распорно подвесные своды из термостойкого хромомагнезнтового кирпича. Подвесные своды делают прямыми из магнезитовых или хромо магнезитовых кирпичей, скрепленных металлическими пластинами в пакеты и подвешиваемых к конструкциям крепления печи. В на стоящее время распорно-подвесные своды применяют на многих
заводах. Примером |
может служить свод радиусом 8500 мм, на- |
4 Заказ № 355 |
49 |
бранный дугами из хромомагнезитового кирпича (рис. 16). Между кирпичами одной дуги проложены пластины из листовой стали толщиной 0,8—1,0 мм. Выступающие полосы листовой стали под вешены к уголкам арочной балки, опирающейся на кронштейны, приваренные к вертикальной стойке крепления печи. Срок службы
такого свода составляет почти два года.
Преимуществами распорно-подвесного свода являются: стой кость арки из тяжелого хромомагнезитового кирпича при любой
Рис. 16. Распорно-подвесной свод отражательной печи:
/ — стены |
печи; 2 — арочный свод; |
3 — стоика крепления печи; 4 — тяга; 5 — подвески |
свода |
|
|
ширине |
свода и хорошая |
герметичность. Свод — наиболее уязви |
мая часть отражательной печи, особенно это относится к его пер вому сектору. Стойкость свода определяет кампанию печи. Для печи с динасовым сводом она составляет 6—12 мес.
В современных отражательных печах газоотвод делают наклон ным, плавно переходящим в газоотводный боров печи, называе мый аптейком (см. рис. 15). Газоотвод имеет одинаковую с печью ширину и подвесной плоский свод. По газоотводу и борову газы, отходящие из отражательной печи, поступают в котлы-утилиза торы, где часть тепла газов используется для производства пара. Далее газы подают в пылеуловители и затем в дымовую трубу.
Загрузка шихты и выпуск продуктов плавки
В отражательную печь, как правило, шихту загружают через от верстия в своде, расположенные с двух сторон вдоль боковых стен печи. Всего с каждой стороны делают по 22—25 отверстий диаметром 200—300 мм, в которые вставляются загрузочные ру кава (трубы). Для загрузки используют только часть отверстий. Так, на Красноуральском медеплавильном комбинате 70 % огарка загружают на расстоянии 4—5 м от передней топочной стенки
печи, 25 % — на расстоянии 6—10 м и 5 % — на расстоянии |
12 м. |
Весь фронт загрузки составляет 12 м. Если отражательная |
печь |
работает на |
растянутом факеле горения топлива, в результате |
чего в конце |
печи поддерживается высокая температура, то для |