
1236
.pdf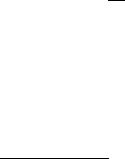
Вследствие неоднородности состава окисленных никелевых руд перед плавкой различные сорта руд смешивают—усредняют. Усредненную руду направляют на грохочение и дробление. Затем руду, предназначенную для плавки, окусковывают брикетирова нием или спеканием (агломерацией). Хорошее окускование обес печивает высокую производительность шахтной печи и низкий расход топлива при плавке.
|
|
Окисленная никелевая руда |
|
||
|
|
|
Усреднение —--------- |
|
|
Сульфидизатор |
|
|
Окускование |
Кокс |
|
|
|
И Г |
|
||
|
|
|
|
|
|
|
|
Шахтная плавка |
|
||
|
|
Штейн |
Отвальный |
Газы |
|
|
|
|
шлак |
Очистка |
|
|
|
|
|
||
|
|
|
|
Пыль |
|
|
|
Конвертирование |
I |
_ |
|
|
|
|
|
||
|
ФайнштейН' |
Газы |
Конвертерный шлак |
|
|
|
|
|
на извлечение |
|
|
Окислительный обжиг |
кобальта и никеля |
|
|||
Закись никеля |
Газы |
|
|
|
|
|
|
Восстановитель |
|
|
|
Восстановительная злектроллавка |
|
|
|
|
|
Огневой |
Электропечной шлак |
|
|
|
|
рикель |
|
I_____________ : |
|
- - - - |
|
Рис. 48. Схема переработки окисленных никелевых руд плавкой на штейн |
|||||
Брикетированием |
называется прессование руды |
или шихты, |
в результате чего полученные брикеты сохраняют приданную им во время прессования форму. Этот процесс основан на свойстве глинистой никелевой руды слипаться под воздействием внешнего давления и сохранять данную форму брикетов. Глину не добав ляют, так как это увеличило бы выход шлака. Перед брикетиро ванием руду подсушивают, измельчают и смешивают с гипсом или пиритом. Сушку руды от первоначальной влажности 25—28 % Д° 12—16 % производят в барабанах-сушилках диаметром 1,9—2,2 м. Производительность сушилки составляет 17—19 т/ч руды при рас ходе топлива 1—2 % от ее массы. После сушки руду сортируют на барабанном грохоте и куски крупностью 25—30 мм направ ляют на плавку, а мелочь — на брикетирование. Брикеты полу-
чают на валковых или других механизированных прессах при давлении до 50 МПа.
Ниже приведена характеристика современных брикетных прес-
сов, изготовляемых на отечественных машиностроительных водах:
Производительность по руде, |
т/ч |
50 |
Диаметр валков, мм . . . . |
|
. 1000 |
Число оборотов валков, об/мин . . . |
8 |
|
Удельное давление прессованияд МПа |
50 |
|
Мощность электродвигателя, |
кВт . |
100 |
Объем брикета, см3 . |
|
90 |
Агломерация. В процессе агломерации шихту нагревают до температуры размягчения или частичного плавления. Нужное для этого тепло получают от горения коксика, вводимого в шихту.
Руда
\
Смешивание различных сортов руд
________Грохочение________
|
-150мм |
|
+150мм |
|
|
|
|
Дробление |
|
|
|
|
5Г |
|
|
|
|
Грохочение |
|
|
|
-35мм |
+35пм |
|
|
Бункера рудб/ |
|
||
Ноксик-дмм |
|
|
|
|
Возврат агломерата |
|
|
Рыло агломерации и шахтных печен |
|
|
Рзиродка |
|
|
|
|
Шихтовка и увлажнение |
|
||
|
|
Г |
|
|
|
Агломерация |
|
||
Газ |
Агломерат |
Пыль |
|
|
В. трубу |
Г |
I |
L |
|
Грохочение |
|
|||
|
|
|||
|
-25мм |
|
Агломерат |
|
|
|
|
+25мм |
|
____________________ Шахтная плавка |
|
|
||
Рис. 49. Схема подготовки руды агломерацией |
|
|||
При. агломерации образующиеся легкоплавкие силикаты |
2FeO X |
|||
X Si02 и магнетит Fe0-Fe20 3 |
связывают мелкие частицы |
шихты |
в прочный пористый пирог-агломерат. Руду подготавливают к аг ломерации по технологической схеме, приведенной на рис. 49.
От схемы подготовки руды к брикетированию она отличается тем, что отпадает сушка руды, получают пористый продукт, не содер жащий влаги, что снижает расход кокса при плавке.
Схема процесса спекания на агломерационной машине (уст ройство машины см. в гл. III) приведена на рис. 50. По мере дви жения паллеты на участке L' зажигается и горит коксик и обра зуется агломерат. Шихта спекается за счет перемещения по вер тикали зоны горения топлива (коксика). По окончании процесса горения топлива на участке L" через готовый агломерат просасы вается холодный воздух, охлаждающий агломерат.
Производительность агломерационной машины и качество аг ломерата зависят от качества шихты и технологического режима спекания. Весьма большое значение для агломерации имеют ми нералогический и гранулометрический состав руды, расход кок-
Рис. 50. Схема агломерации:
1 — зажигательный |
горн; |
2 — слой |
||||||
постели; |
3 — слой |
интенсивного |
го |
|||||
рения |
топлива; |
4 — атмосферное |
||||||
давление; |
5 — вакуум-камеры; |
6 — |
||||||
колосниковая |
решетка; |
h— высота |
||||||
слоя |
шихты; |
L — рабочая |
длина |
|||||
ленты; |
V — зона |
спекания |
агломе |
|||||
рата; |
L" — зона охлаждения |
агло |
мерата
Направление движения аглоленты
Г
I
L
сика, влажность шихты, ее газопроницаемость, высота слоя и раз режение в вакуум-камерах.
Расход коксика определяют опытным путем. Он составляет 8—10 % от массы шихты или 140—160 кг на 1 т агломерата. При его недостатке ухудшается качество агломерата, при избытке за медляется процесс спекания. При неравномерном гранулометри ческом составе шихты во время загрузки на агломерационную машину происходит отделение крупной фракции от мелкой (сегре гация) шихты, что ухудшает газопроницаемость шихты и каче ство агломерата. Для улучшения качества агломерата рекомен дуется крупную руду (+35 мм) отделять перед спеканием и из мельчать до 10—12 мм. Избыток влаги ведет к повышению расхода топлива на ее испарение, и понижается прочность агло мерата. Недостаточно влажная шихта спекается плохо и медленно
из-за низкой газопроницаемости. Оптимальное содержание |
влаги |
в шихте устанавливают опытным путем, и оно составляет |
2 1 — |
23%. |
|
Чтобы обеспечить высокую производительность агломерацион ной машины и получить хороший агломерат, через шихту следует просасывать достаточное количество воздуха. С увеличением га зопроницаемости возрастает его качество, повышается интенсив ность горения коксика и увеличивается скорость спекания.
Скорость движения паллет следует регулировать по виду из лома агломерата на выгрузке в зависимости от полноты пропе-
кания слоя шихты. Обычно она составляет 2 —3,5 м/мин. Агломе рат из окисленных никелевых руд отличается малой прочностью и содержит много мелочи. Мелкий агломерат и часть неспечеииой шихты (—30 мм) отделяют от крупного агломерата, его называют возвратом. Он поступает на спекание с новой порцией руды. Со держание возврата в шихте 20 %.
Машины с полезной площадью спекания 50 м2 перерабатывают в сутки 1500 т шихты. При выходе годного агломерата 65—70 %
удельная производительность по агломерату |
составляет 18,0— |
|
20 т/м2 рабочей поверхности машины в сутки. |
|
|
Плавка окисленных никелевых руд в шахтных печах |
||
Цель шахтной плавки окисленных никелевых |
руд — максималь |
|
ный перевод никеля в легкоплавкий богатый |
полупродукт — |
|
штейн. Он легко отделяется от расплавленной |
породы — шлака. |
|
Шихта шахтной плавки состоит из аглрмерата |
(или брикетов), |
крупнокусковой руды, пирита (или гипса), флюса-известняка. Топ ливом служит кокс. В связи с тем что при плавке никельсодер жащих материалов (агломерата, брикетов и руд) одновременно протекают процессы восстановления и образования сульфидов, она носит название восстановительно-сульфидирующей шахтной плавки. Поведение важнейших компонентов шихты при шахтной плавке излагается ниже.
Горение кокса. Никельсодержащие материалы плавятся за
счет тепла, выделяемого при горении кокса. Кокс |
сгорает |
в воз |
||||
духе, |
подаваемом |
через |
фурмы, по |
реакции С + 0 2 = |
С02 + |
|
+ 395 |
МДж. При |
этом |
развивается |
температура |
1500—1600° С. |
По мере расходования кислорода в верхней части слоя кокса на чинается реакция С + С02 = 2СО— 172,2 МДж. Эта реакция протекает со значительным поглощением тепла, и температура печных газов быстро снижается до 1000 °С. Реакция неполного горения почти прекращается.
Общая эффективность сжигания кокса определяется соотно шением С02 и СО в газах при выходе из шихты.
Сульфидирование и образование никелевого штейна. Окислен ная никелевая руда не содержит серы, поэтому ее приходится вводить, добавляя при плавке в шихту пирит или гипс. Пирит при нагревании разлагается по реакции 2 FeS2 = 2FeS + S2. Гипс (CaS0 4 -2 H20 ) при нагревании теряет влагу и безводный сульфат
кальция |
восстанавливается |
до сульфида CaS04 + 4СО = |
= CaS + |
4С02. Образующиеся |
сульфиды железа и кальция до |
статочно полно и быстро сульфидируют силикат никеля по реак
ции |
NiO-Si02 + FeS = NiS + FeO-Si0 2; |
NiO-Si02 + CaS = |
||||
= |
NiS + |
CaO-Si02. |
|
|
|
|
|
Силикаты кальция |
(CaO-Si02) и железа |
(FeO-Si02) пере |
|||
ходят |
в |
шлак. В печи при высокой температуре NiS |
переходит |
|||
в |
более |
устойчивое |
соединение Ni3S2 по |
реакции |
6NiS == |
|
= |
2Ni3S2 + S2. Кроме |
реакций восстановления |
гипса и |
сульфиди- |
рования никеля, происходит восстановление никеля и оксидов же
леза по реакциям: |
NiO + |
СО = |
Ni + С02; |
3Fe20 3 + СО = |
||
= |
3Fe30 4 + С02; |
Fe30 4 + |
СО = |
3FeO + С02; |
FeO + СО = |
|
= |
Fe + С 02. При существующей |
в |
шахтной печи температуре |
и восстановительной атмосфере наиболее легко восстанавлива ются NiO до металлического никеля и Fe20 3 до FeO. FeO восста навливается наиболее трудно, поэтому только он частично вос станавливается до металлического железа.
Сульфиды никеля (Ni3S2) и железа (FeS) образуют основу штейна. В них растворяются восстановленные металлы никеля и железа (ферроникель), а также сульфиды меди и кобальта. Та ким образом, штейн никелевой плавки состоит в основном из Ni3S2, FeS, никеля, железа и небольшого количества Cu2S и CoS. Штейн содержит, %: 16—20 Ni; 18—22 S; 0,5—1,0 Со; 55—60 Fe
и2—4 % шлака.
Взависимости от содержания серы в штейне металлизирован
ная часть составляет 20—40 % от массы штейна. Температура плавления такого штейна 1 100 °С.
Шлакообразование. При плавке оксиды пустой породы руды, флюсов и золы кокса, взаимодействуя и сплавляясь друг с дру
гом, образуют шлак по |
реакциям |
2FeO + Si02 = 2Fe0-Si02; |
CaC03 = CaO -|- С 02; CaO |
Si02 = |
CaO*Si02. |
Сначала в шихте образуется легкоплавкий первичный шлак. Этот шлак, стекая в нижнюю часть печи, взаимодействует с твер дыми оксидами, растворяя их. Количество шлака при плавке до стигает 96—105 % от массы переработанного агломерата. Состав шлака никелевой плавки, %: 44—46 Si02; 8—12 MgO; 18—22 FeO; 4 —10 А120 3; 15—18 CaO; 1,5—2,0 Сг20 3. Температура жидкоплавкости таких шлаков 1250—1350 °С. Плотность их достигает 3,3— 3,6 г/см3.
Кроме оксидов, в шлаке в небольшом количестве находятся сульфиды железа и никеля. Содержание никеля в шлаке прак тически составляет 0,16—0,22 %.
Газы и пыль. Газы, выходя из шихты при 500—600 °С, уносят мелкие ее частицы. Количество пыли при плавке агломерата со ставляет 14—16 % и при плавке брикетов 4— 6 % от массы ни кельсодержащего сырья. Газы очищаются от пыли в пылеулав ливающей установке и имеют следующий состав, %: И —14 СО; 14—15 С 02; 0,5—1,0 0 2; 70—72 N2.
Практика шахтной плавки окисленных никелевых руд. Одним из основных условий успешной работы печи при плавке окислен ных руд является правильный состав шихты. Шихта должна быть однородна по крупности, в ней не должно быть мелочи и слиш ком крупных кусков. Количество известняка и сульфидизаторов в шихте определяют расчетом. При недостатке известняка повы шается содержание в шлаке Si02. Такие шлаки называются кис лыми, они вязкие, плохо вытекают из печи и создают большие трудности для обслуживания печи. При недостатке сульфидиза торов (гипса или пирита) в шихте образуется много ферроникеля,
Ю Заказ Ич 355 |
145 |
который |
выделяется |
из штейна, |
образуя |
настыли в горне |
печи |
и ковшах. |
количестве |
пирита |
ферроникель в |
горне |
|
При |
достаточном |
печи почти не выделяется. Пиритом можно регулировать содер жание никеля в штейне, так как избыточный FeS переходит в штейн. В противоположность этому избыток гипса мало влияет на состав штейна и избыток его разлагается, выделяя SO?. Де сульфуризация при работе на пирите составляет около 60 %, на гипсе 30%. При повышенном расходе гипса десульфуризация возрастает до 50—75 %.
Загрузка печи — одна из самых важных операций; она опре деляет успешную работу печи. Шихту в печь загружают отдель ными порциями—колошами. Масса колоши зависит от размера печи и составляет 8—10 т. Набор компонентов шихты в колошу
Рис. 51. Влияние уровня загрузки на |
распределение материалов |
при загрузке |
|
производят в установленном порядке |
по объему или по массе. |
В начале загрузки колоши по длине печи загружают кокс, затем известняк, гипс или пирит и на них загружают агломерат и руду. При загрузке, падая с загрузочных плит, крупные куски шихты ложатся дальше, а мелкий материал — ближе к той стороне, с ко торой производят загрузку. Это создает неравномерное распреде ление материала по крупности.
Компоненты шихты распределяются в печи в зависимости от уровня загрузки (рис. 51). При низком уровне кокс и кусковая часть шихты попадают к противоположной стенке кессона. Мел кая часть шихты падает ближе к центру печи. Сопротивление слоя кокса и крупного агломерата и руды меньше, и печные газы при низком уровне загрузки проходят главным образом по пери ферии. Ход печи в этом случае называется периферийным. Он характеризуется устойчивым ходом печи, большим проплавом и хорошим состоянием фурм. По мере повышения уровня загрузки кокс и кусковая часть шихты перемещаются к центру и печь пе
реходит на «центральный ход», т. е. печные газы проходят в ос новном в центре. Такой ход печи отличается малым проплавом и значительными настылями в области фурм.
Оптимальный уровень загрузки на каждом заводе, устанавли вают опытным путем в зависимости от мощности воздуходувки, крупности шихты и регламентируют технологической инструкцией. При хорошо подготовленной крупнокусковой шихте и более мощ ной воздуходувке уровень загрузки от уровня фурм устанавли вают 4—5 м.
Технические показатели шахтной плавки никелевых окислен ных руд. Шахтные печи для плавки окисленных никелевых руд имеют различные размеры, а поэтому и неодинаковую суточную производительность по проплаву никельсодержащего сырья. Для сопоставления их производительности принято определять удель ную производительность, которая равна количеству руды (агло мерата), проплавляемому на 1 м2 сечения печи в области фурм за сутки. Практически удельная производительность шахтных пе чей на отечественных заводах следующая, т/(м2?сут):
|
Воздушное |
Кислородно-воздушное |
|
дутье |
дутье (24,5 %) |
Агломерат |
35—36 |
40 |
Брикеты . . |
26—29 |
34 |
Сырая руда |
18—20 |
— |
Расход кокса. Окисленные никелевые руды требуют значитель ного расхода кокса, поэтому почти половина всех расходов на вы
плавку никеля приходится на кокс. |
причин: подготовки |
руды |
|
Расход |
кокса зависит от многих |
||
к плавке, |
химического состава сырья |
и качества кокса. |
Руды |
с высоким |
содержанием БЮг и MgO требуют большего расхода |
кокса, чем железистые руды. При плавке агломерата расход кокса меньше, чем при плавке брикетов, так как он порист, бы стрее, чем плотные брикеты, нагревается до температуры плавле ния, и шлак в агломерате почти сформирован. При большом содержании мелких классов (до —40 мм) кокса на плавку тре буется больше, так как мелкий кокс успевает сгореть преимуще ственно в верхней зоне столба шихты.
Решающее значение для экономии кокса имеет расход воз^ духа, а также обогащение дутья кислородом и подогрев дутья. Для нормальной работы необходимо подавать воздух в количе стве 45—60 м3/мин на 1 м2 сечения печи в области фурм при упругости дутья 11,0—13,0 кПа при плавке брикетов и 15,7— 18,0 кПа при плавке агломерата. Уменьшение расхода воздуха снижает проплав, так как уменьшается количество сожженного кокса в единицу времени на 1 м2 сечения печи в области фурм. Для увеличения интенсивности горения кокса и уменьшения его расхода рекомендуется дутье обогащать кислородом или подогре вать до 500—800 °С.
В настоящее время внедрено обогащение дутья кислородом до 25 % при расходе кокса 20—22 % от агломерата на «Южурал
никеле» и до 24,5 % при расходе кокса до 29 % от массы брике тов на Уфалейском никелевом комбинате.
При плавке шихты в штейн переходит 70—80 % никеля,
остальной никель распределяется |
между |
шлаком |
и |
пылью. |
|
В шлак переходит 12—16 % никеля, в пыль 6—14 %. |
|
||||
На |
1 т штейна расходуют 20 т агломерата, 4—5 т известняка, |
||||
1— 2 т |
пирита (колчедана), 5— 6 т |
кокса |
и 32 500 |
м3 |
воздуха. |
Чем меньше расходуется на 1 т штейна сырья, кокса, тем ниже себестоимость никеля.
Конвертирование никелевого штейна
Следующий за шахтной плавкой передел — это продувка никеле вого штейна в агрегатах, аналогичных конвертерам для медной плавки. Цель этой операции — полный перевод железа и по воз можности кобальта, содержащегося в штейне, в шлак и окисление части серы.
При продувке штейна в конвертере в первую очередь окисля ется (соединяется с кислородом) металлическое железо. Полу чающийся оксид железа (FeO) соединяется с загружаемым квар цем и образует силикат оксида железа, называемый фаялитом, который является основной составляющей конвертерных шлаков: 2Fe + 0 2 + Si02 = 2Fe0-Si02. После того как большая часть металлического железа окислилась, начинает окисляться серни стое железо (FeS) с образованием фаялита и сернистого газа: 2FeS + 302 + Si02 = 2Fe0-Si02 + 2S02. Параллельно с образо ванием фаялита протекает реакция образования магнетита:
3FeO -f- 1/г02 == Fe30 4 .
Продукты конвертирования. При конвертировании получаются файнштейн, конвертерный шлак, пыль и газы. Файнштейн — сплав Ni3S2, содержащий 20 % металлического никеля. Кроме никеля и
серы, он содержит небольшие |
количества железа, |
меди и ко |
|||||
бальта. Состав файнштейна, %: 76—78 Ni; 19—21 S; |
0,2 —0,3 Fe; |
||||||
0,4—2,0 |
Си; |
0,3—0,4 Со. |
Температура плавления |
файнштейна |
|||
788 °С. |
Его |
температура |
в конвертере перед |
розливом |
достигает |
||
1100 °С. |
|
|
|
конвертерного |
шлака |
являются |
|
Основными составляющими |
фаялит (60—70 %) и магнетит (18—30% ). Конвертерный шлак содержит, ,%: 24—28 Si02; 60—65 FeO; до 5 А120 3; 0,5—3,0 S. Содержание никеля в среднем достигает 0,8—2,0 %, кобальта 0,4%. Температура плавления конвертерных шлаков низкая — не превышает 1250 °С. Плотность жидкого конвертерного шлака 3,8 г/см3. Выход пыли составляет 1 —3 % от массы переработан ного штейна. Она улавливается в пылевой камере или электро фильтре и перерабатывается в конвертере. Содержание никеля в пыли достигает 25—30 %. Газы выходят из горловины конвер тера при 1000—1100°С. В период конвертирования свежей порции штейна при окислении металлического железа газы содержат азот и до 1 % (0 2 + S 02). При окислении сернистого железа содержа
ние в газе S 0 2 повышается до 12 %, но при выходе из конвертера этот газ разубоживается в 3—4 раза.
Поведение кобальта. В процессе конвертирования штейна ко бальт соединяется с кислородом труднее, чем железо, но легче, чем никель. Это объясняется тем, что кобальт имеет большее срод ство к кислороду, чем никель, но меньшее, чем железо. Поэтому кобальт при конвертировании интенсивно переходит в конвертер
ный шлак |
только |
после снижения содержания в массе железа, |
по данным |
проф. |
Н. С. Грейвера, ниже 10— 12 °/о, что позволяет |
концентрировать его в последних сливах шлака. Содержание ко бальта в конвертерных шлаках последних сливов возрастает до 1,2 %, иногда и более.
В процессе переработки штейна кобальт не полностью пере ходит в конвертерный шлак; до 15 % от всего кобальта, содер жащегося в штейне, остается в файнштейне и переходит в товар ный никель. Поскольку на уральских заводах никель не под вергают электролизу, перешедший в него кобальт теряется для кобальтового производства. Поэтому при конвертировании никеле вого штейна кобальт стремятся максимально извлечь в конвертер ный шлак, из которого его затем извлекают в кобальтовый полу продукт, пригодный для переработки в автоклавах с целью по следующего получения из него металлического кобальта.
Обеднение конвертерных шлаков. С целью увеличения извле чения кобальта и никеля конвертерные шлаки обедняют в жид ком виде. Процесс можно проводить в электропечах или конвер терах. На рис. 52 приведена технологическая схема обеднения жидких конвертерных шлаков и получения богатой кобальтом ав токлавной массы в обогреваемом конвертере. Схема внедрена на комбинате «Южуралникель». Она позволила без понижения из влечения никеля и кобальта закрыть ряд переделов, сэкономить материальные, энергетические ресурсы и снабдить сырьем гидро металлургический цех для получения солей никеля и металличе ского кобальта.
Процесс получения автоклавной массы из конвертерных шла ков состоит из следующих операций: первичного обеднения рядо вых конвертерных шлаков; вторичного обеднения оборотных конвертерных шлаков; получения автоклавной массы; обработки богатых по никелю и кобальту шлаков конвертера получения ав токлавной массы массой конвертеров обеднения.
Обеднение конвертерных шлаков производят металлизирован ным штейном (14—17 % Ni) согласно известному правилу, что бедный шлак можно получить только над бедным штейном. Ме таллическое железо штейна при перемешивании штейна со шла ком в конвертере способствует переходу части кобальта из кон вертерных шлаков в штейн по реакции СоО -|- Fe = Со + FeCX
Операции обеднения конвертерных шлаков проводят в следу ющем порядке. В обогреваемый конвертер заливают 20—30 т го
рячего штейна и один ковш конвертерного шлака |
(в соотношении |
3 1 ). Затем штейн со шлаком перемешивают |
кратковременной |
продувкой и дают отстояться в течение 5—10 мин при включен ной горелке.
Качество отстаивания определяется по ломковой пробе. От стоявшийся шлак сливают. После слива обедненного шлака зали вают следующую порцию шлака и так повторяют несколько раз.
Штейн |
|
|
|
L |
|
Конвертеры набора |
|
|
и варки файнштейна |
|
|
Файнштейн |
Конвертерный |
|
Конвертериг |
шлак |
|
Конвертер |
||
вторичного обеднения |
первичного обеднения |
|
Оборотный |
|
|
|
шлак |
|
1 Г |
|
|
Отвальный шлак |
|
|
7 |
г |
|
1 касса |
|
|
|
Г |
|
Конвертер обеднения |
|
|
шлаков от автоклавной кассы |
|
|
Шлак |
Д касса |
|
Конвертер получения |
|
|
автоклавной кассы |
I |
|
I |
|
|
Файнштейнобая Автоклавная |
Шлак |
|
касса |
касса |
I |
На переработку
Рис. 52. Краткая схема обеднения конвертерного шлака и получения авто клавной массы
Установлено, что конвертерные шлаки обедняют до отвальных (0,060 % Со и 0 ,11 % Ni) до тех пор, пока в штейне не возрастет содержание кобальта до 1,3%. Шлаки, обработанные штейном, содержащим более 1,3 % Со, направляют на вторичное обеднение
печным штейном либо |
возвращают в |
основное |
производство. |
|
В процессе обеднения |
из |
конвертерных |
шлаков, |
содержащих |
в среднем 0,4 % Со и 2,0 % |
Ni, извлекается в штейн 75—80 % Со |
|||
и до 85—90 % Ni. |
|
|
|
|