
1236
.pdfПриготовление расплавов бронз других марок во многом сходно с приготовлением алюминиевых бронз. Технологические
особенности плавки и литья подробно излагаются в стандартах предприятия.
Бронзы в основном как сплавы горячеломкие, со значитель ными температурными и концентрационными интервалами за твердевания отливают в «глухие» кристаллизаторы, не имеющие непосредственного выхода воды на слиток. Затвердевание слитка происходит за счет потерь тепла в водоохлаждаемом кристалли заторе и на воздухе.
Вторичное охлаждение происходит в кольцевом спрейере, рас положенном на расстоянии 400—800 мм от нижнего фланца кри сталлизатора. Вторичное охлаждение не влияет на процесс за твердевания, а лишь понижает температуру полностью затвердев шего слитка.
Для плавки медно-никелевых сплавов используют индукцион ные канальные печи с кислой футеровкой, которые обычно приме няют для плавки латуней и других медных сплавов (см. гл. III).
Медно-никелевые сплавы склонны к науглероживанию. По этому древесный уголь в качестве защитного покрова применяют только при плавлении сплавов с 15—20 % никеля. Сплавы с боль шим содержанием никеля плавят под слоем флюсов из смесей, содержащих, кроме древесного угля, силикаты и фтористые соли. Медно-никелевые сплавы в большей степени, чем другие медные сплавы, склонны к поглощению водорода и кислорода.
Для плавки нейзильбера в качестве шихты используют катод ную медь, катодный никель, электролитический цинк и отходы собственного производства. Перед разливкой сплав обрабатывают технологическими добавками: марганцем (0,1 %) шли кремнием
и магнием (по 0,05% каждого). Для сокращения потерь металла
вшлаке в конце плавки в состав защитного покрова вводят кри олит (50—100 г на 100 кг шихты). Слитки нейзильбера отливают
полунепрерывным способом.
Плавку мельхиора ведут под слоем прокаленного древесного угля. Шихтовые материалы загружают в печь в следующей после довательности: никель, отходы и затем медь. Расплав обрабаты вают марганцем, кремнием и магнием. Технологические параметры литья слитков даны в табл. И.
Получаемые слитки, помимо высокого качества, должны иметь ровную и чистую, свободную от литейных дефектов поверхность, так как качество полуфабрикатов определяется не только качест вом литого металла, но и состоянием поверхности заготовок. Год ные слитки подвергают механической обработке непосредственно
влитейных цехах.
Укруглых слитков отрезают литниковую и донную части.
Слитки разрезают на мерные заготовки, поверхность их, как пра вило, не обрабатывают. Обнаруженные единичные дефекты, не соответствующие заводским стандартам, устраняют маятниковыми шарошками, причем допускается только пологое снятие слоев ме-
Т а б л и ц а 11. Технологические параметры литья слитков меди и ее сплавов непрерывным методом
Марка сплава |
Диаметр или |
Высота |
Скорость |
Температура |
сечение |
кристаллиза |
литья, м/ч |
литья, °С |
|
|
слитка, мм |
тора, мм |
|
|
М1р |
150 |
270—505 |
12—14 |
1180—1220 |
Л 90 |
150 |
305 |
15—17 |
1170—1190 |
ЛбЗ |
300 |
270 |
6—8 |
1060—1110 |
ЛС59—1 |
200 |
305 |
11—12 |
1100—1140 |
БрА5 |
200 |
200 |
3,5 |
1130-1150 |
БрАЖМц 10-3-1,5 |
200 |
195 ~ |
4,0—4,5 |
1180—1200 |
БрБ2 |
100 |
100—260 |
7,0—8,5 |
1080—1120 |
МНЗО |
125 |
250 |
6 ,0 -7 ,0 |
1330-1360 |
МНЦ15—20 |
130X300 |
150 |
10—12 |
1330—1250 |
талла, не допускается резких углов и переходов, иначе дефекты могут появиться на поверхности полуфабрикатов.
У прямоугольных слитков отрезают, литниковую и донную части. Слитки разрезают на мерные заготовки. Поверхность прямо угольных слитков фрезеруют на станках с жестко установленными или плавающими фрезами.
Основной задачей при производстве слитков меди и медных сплавов является получение хорошего качества при максимальном выходе годного и минимальных затратах на производство.
Под хорошим качеством понимается свободный от литейных и неметаллических дефектов слиток, имеющий требуемый хими ческий состав и обеспечивающий необходимый уровень свойств полуфабрикатов. Качество слитков зависит от многих факторов, что объясняется сложностью литейных процессов. Кроме того, влияние этих факторов часто совместное. Поэтому различные дефекты слитков нередко являются следствием одной и той же причины.
Взависимости от характера и причин дефекты, возникающие
вслитках меди и медных сплавов, отливаемых полунепрерывным или непрерывным способом, можно условно разделить на четыре группы: 1) несоответствие по химическому составу; 2) несоответ ствие размеров; 3) поверхностные дефекты; 4) внутренние де фекты.
КОНТРОЛЬНЫЕ ВОПРОСЫ
1.Для каких целей применяют медь в народном хозяйстве?
2.Какие элементы содержат медные концентраты?
3.Какие способы получения меди Вы знаете?
4.Что такое штейн и шлак? Назовите их важнейшие свойства.
5.Зачем обжигают медные концентраты?
6.Как записываются главные реакции переделов обжига, плавки и кон центрирования?
7.Как рафинируется медь?
8.Какие металлы (примеси) выделяют на переделе рафинирования?
9.Какие меры надо принимать по охране природы от вредных выделений медеплавильного завода?
10. Какие меры предосторожности следует применять на основных переде лах производства меди?
11. Особенности производства слитков меди и сплавов.
Глава |
ОЧИСТКА ГАЗОВ |
VII |
МЕТАЛЛУРГИЧЕСКИХ ПРОЦЕССОВ |
|
ОТ ПЫЛИ |
Отходящие газы технологических процессов производства цветных металлов уносят много мелких частиц шихты и возгонов, содер жащих ценные металлы. Количество образующейся пыли, опре деляемой в процентах от массы переработанной руды (концент рата или шихты), зависит от вида металлургического агрегата, крупности шихты, а также от содержания в шихте металлов и соединений, легко переходящих в газы. Наибольший унос пыли с газами наблюдается при обжиге в печи КС и вельцевании отхо дов цинкового производства, наименьший — в электропечах рудной плавки. Так, при вельцевании и шлаковозгонке извлекаемые ме таллы, цинк, свинец, кадмий и индий уносятся с газами в виде пыли и ее недостаточное улавливание приводит к большим эко номическим потерям. Но и при других невозгоночных процессах, например при переработке свинцового концентрата, в пыль пере ходит до 7—8 % всего свинца, находящегося в производстве. Поэтому пыль необходимо уловить и переработать, чтобы увели чить извлечение свинца в товарный металл и повысить рентабель ность производства.
Ниже приведены данные о выносе пыли при металлургических процессах получения цветных металлов, % ’
Обжиг в печи КС . Агломерация .
Шахтная плавка: медных руд ...............
свинцового агломерата
Окисление никелевых руд: агломерата .
брикетов ....................................................
Отражательная плавка сырого и обожжен ного концентрата . .
Плавка в электропечи . Конвертирование . Шлаковозгонка
30-45
о Г о
3—й
4—6
14—16
3—6
0,5—1,5
0,5—1,5
2—2,5
25—30
Большие колебания в величине уноса пыли с газами определя ются крупностью шихты и интенсивностью и характером процесса^. При плавке в шахтных печах хорошо подготовленной кусковой шихты унос пыли газами не превышает 3—4 % и потери металлов с пылью невелики. При плавке шихты, содержащей повышенное количество мелочи, унос пыли увеличивается.
Интенсификация процессов шахтной плавки путем увеличения расхода воздуха и применения низкой сыпи связана с большим уносом пыли, улавливание которой для извлечения из нее цветных металлов приобретает большое значение.
Наряду с экономической важностью улавливания пыли на ме таллургических заводах очищать газы необходимо для создания нормальных санитарных условий работы и предотвращения ущерба, причиняемого пылью и газами живой природе и людям.
Выброс пыли, образующейся при производстве свинца, цинка, сурьмы и других металлов, в атмосферу сверх допустимых кон центраций компонентов (свинца, мышьяка, цинка и др.) вредно влияет на здоровье работающих и проживающих в районах, окру жающих завод. Пыль, содержащая Si02, при вдыхании ее в боль ших дозах приводит к тяжелому легочному заболеванию — си ликозу.
В Советском Союзе предельно допустимые концентрации (ПДК) вредных веществ в атмосфере населенных пунктов и про изводственных помещений (рабочей зоне) весьма ограниченны. Это является ярким подтверждением заботы КПСС и Советского правительства о здоровье населения нашей страны и защите при роды. Так, среднесуточная концентрация в атмосфере свинца и его соединений (в пересчете на свинец) должна быть не более 0,0007 мг/м3, S02 0,05 мг/м3, мышьяка 0,003 мг/м3, пыли, содержа щей более 70% свободного Si02 (кварц), 1,0 мг/м3. Превышение этих значений предельно допустимых концентраций не допуска ется.
Предельно допустимые концентрации в воздухе некоторых га зов паров и пылей следует учитывать при разработке технологи ческих процессов очистки газов и при контроле за санитарными условиями. Поэтому способы очистки газов определяются не только ценностью извлекаемой пыли и серы, но и необходимостью улучшения санитарного состояния воздушного бассейна вокруг предприятия.
Пыли, содержащиеся в технологических газах, можно разде лить на две основные группы: механическая (грубая пыль) и возгоны (тонкая пыль). Грубая пыль (механически увлекаемая газами печей)— частицы шихты с размерами от нескольких микрометров до нескольких десятков микрометров. Тонкая пыль обычно состоит из частиц возгонов, образующихся в процессе испарения и конденсации металлов и их соединений (например, мышьяка, цинка и др.), с размером частиц порядка от десяти до одного микрометра.
Для удаления пыли из газов металлургических печей в цвет ной металлургии применяют пылеуловители различных конструк ций в зависимости от величины частиц, физической природы, хи мического состава пыли из-за многообразия свойств очищаемых газов (температуры, химического состава, влажности).
Ниже кратко описана применяемая в цветной металлургии га зоочистительная аппаратура.
Этот вид пылеуловителей в цветной металлургии применяют огра
ниченно из-за их |
низкой |
эффективности: частицы |
пыли менее |
5 мкм даже при |
больших |
размерах пылевых камер |
не улавли |
ваются. Пылеосадительные камеры громоздки и занимают много места: при небольшой высоте большие длина и ширина. Скорость газа в камере невелика — не более 0,5—2,0 м/с. Крупные частицы пыли, находящиеся в газе, проходящем вдоль камеры, вследствие резкого уменьшения скорости движения газов под действием силы тяжести выпадают из газовой струи, оседают на дно камеры-бун кера, из которой пыль периодически выпускают. Степень улавли вания при очистке газов, содержащих крупную механическую пыль и.возгоны, составляет не более 40 %.
В свинцовой промышленности, где газы содержат много тон кой пыли, осадительные камеры не нашли применения. Грубая пыль на таких заводах оседает в газоходах. Поэтому в последних устраивают люки и бункера, через которые осевшую пыль перио дически выпускают и возвращают в производство.
§ 2. Циклоны и батарейные циклоны
Циклоны — распространенный тип пылеуловителя. В цветной ме таллургии циклонные пылеуловители применяют преимущественно для предварительной очистки газов от крупной пыли (0,5 мкм
ибольше), возгоны в циклонах улавлива ются всего на 30—40 %. Схема устройства
идействие циклона показаны на рис. 38. Принцип работы циклона состоит в том,
что газы поступают в него по касательной к корпусу циклона и приобретают враща тельное движение по окружности между
внутренней |
цилиндрической |
поверхностью |
циклона и |
центральной выходной трубой. |
|
Пыль |
под действием |
центробежной |
силы отбрасывается к стенке циклона, отделяется от газа и опускается в бун кер к выпускному отверстию. Газ выходит через выхлопную трубу циклона, увлекая с собой мелкие частицы пыли. Коэффици-
Рис. 38. |
Схема устройства |
и действия |
циклона: |
|
/ — корпус; 2 — Корпус конуса; |
3 — входной |
патрубок; 4 — |
||
крышка; |
5 —*труСа; 6 — пылеотводящее отверстие; |
сплошные |
||
линии — |
внутренний вихрь, штриховые линии — |
внешний |
||
вихрь |
|
|
|
|
ент улавливания пыли в циклоне достигает 90—92 %. Коэффициент полезного действия определяется отношением количества улов ленной пыли к общему его количеству в газе, поступающем на очистку.
Диаметр циклона обычно равен 0,8—2,5 м при высоте 3—4 Ъл. Практически доказано, что при уменьшении диаметра циклона коэффициент улавливания пыли возрастает. Циклоны малого диа метра (40—260 мм) стали объединять в батареи, способные про пускать необходимое количество газов. Аппараты, состоящие йз 16, 32, 40 и более малых циклонов, называют батарейными цик
лонами.
В малых циклонах, называемых элементами батарейных цик лонов, выделение пыли достигается не подводом к ним газов По
Рис. 39. Циклонный |
элемент: |
|
Рис. 40. Схема устройства батарейного |
|||
1 — выхлопная труба циклонного элемента; |
циклона: |
|
||||
2 — направляющий |
аппарат-розетка; |
3 — |
1 — бункер; 2 — корпус; |
3 — циклонный эле |
||
корпус элемента |
|
|
|
мент; 4 — камера для |
установки элементов; |
|
|
|
|
|
5 — розетка; 6 — газораспределительная каме |
||
|
|
|
|
ра; 7 — выхлопная труба; 8 — камера чистого |
||
|
|
|
|
газа; 9, |
10 — выход газа |
|
касательной, |
а |
созданием |
в |
каждом |
элементе |
направляющего |
устройства в виде небольшой розетки или винта (рис. 39). Благо даря винту или розетке газовому потоку придается вращательное движение.
Циклонный элемент (рис. 39) состоит из корпуса, направляю щего аппарата розетки и выхлопной трубы для удаления очищен ного газа.
Схема батарейного циклона приведена на рис. 40. Неочищен ный газ по входному патрубку вводят в общую распределительную камеру. В ней газы распределяются по циклонным элементам, проходя через направляющие аппараты розетки, приобретают вра щательное движение, опускаются вниз и теряют большую часть своей пыли. Пыль собирается в бункере, а очищенные газы под нимаются вверх через выхлопные трубы, поступают в камеру,
откуда по патрубку их отсасывают эксгаустером из аппарата и выбрасывают через дымовую трубу в атмосферу. Коэффициент полезного действия таких аппаратов 92—96 %.
Обслуживание батарейных циклонов весьма просто и сводится тс поддержанию их герметичности, а также систематической раз грузке пыли. Батарейные циклоны устанавливают для очистки тазов от пыли шихты агломерационных машин и шахтных печей.
§ 3. Электрофильтры
Электрофильтром называется пылеуловитель, в котором запылен ный газ подвергается действию электрического поля высокого напряжения, образуемого между двумя электродами. Цо форме осадительных электродов электрофильтры делятся на трубчатые
и пластинчатые, а по |
движению газов — на горизонтальные |
(только пластинчатые) |
и вертикальные (пластинчатые и трубча |
тые) . По состоянию уловленной пыли электрофильтры делятся на
Рис. 41. Схема электрофильтра с преобразователем тока:
/ — распределительный щит; 2 — выпрямитель; |
3 — трансформатор; |
4 — корони- |
рующий электрод; 5 — осадительный электрод; |
6 — выгрузка пыли; |
7 — земля |
сухие, когда пыль улавливается в сухом виде, и мокрые, когда влажные из-за конденсации паров воды газы и пыль улавлива ются в мокром виде (в виде пульпы).
Схема электрофильтра с преобразователем тока дана на рис. 41. Трубчатые электрофильтры состоят из отдельных секций труб диаметром 200—360 мм. Каждая труба (осадительный элек трод) заземлена, т. е. соединена металлическим проводником с зем лей. В центре трубы расположен электрод, к которому подводят постоянный электрический ток напряжением 50—90 кВ от отри цательного полюса выпрямителя тока. Пылегазовую смесь про пускают через трубу снизу вверх. Попадая в электрическое поле, частицы заряжаются, при этом вокруг центрального электрода
наблюдается голубое кольцевое свечение, называемое короной. Отсюда и название электрода: коронирующий. Отрицательно за ряженные частицы пыли притягиваются к осадительному элек троду, остаются на внутренних стенках трубы или падают вниз (сухие электрофильтры) в сборники пыли.
Трубы периодически встряхивают, и пыль падает в располо женный под ними бункер. Коронирующие электроды также пери одически встряхивают для очистки их от пыли. В отличие от су хих электрофильтров пыль, осевшую на осадительных и коронирующих электродах, в мокрых электрофильтрах удаляют не встряхиванием, а промывкой.
Постоянный ток получают выпрямлением переменного тока. Ток высокого напряжения получают при помощи повышающего трансформатора, который имеет две обмотки, первичную и вто ричную. К первичной обмотке подводится ток низкого (400— 500 В) напряжения; она имеет малое число витков из толстой медной проволоки. Вторичная обмотка имеет большое число вит ков из тонкой медной проволоки. К ней 'подводится ток низкого
напряжения первичной обмотки, превращаясь в ток |
высокого |
(до |
90 000 В) напряжения. Напряжение во вторичной |
обмотке |
тем |
больше, чем больше число витков медной проволоки. Так |
как |
мощность при этом остается постоянной, то сила тока во вторич ной обмотке уменьшается во столько раз, во сколько раз увели чивается напряжение тока. Обычно сила тока во вторичной об
мотке, подводимая к коронирующим электродам, |
равна 0,18— |
||||||
0,22 |
А при напряжении |
90 000 В. |
Тогда |
мощность |
трансформа |
||
тора |
W = |
(90 000 X 0,22) |
1000 = |
19,8 кВ-А. |
|
||
Ниже |
приведена характеристика трубчатого электрофильтра: |
||||||
|
|
Температура газов, °С: |
|
400—450 |
|||
|
|
при входе вэлектрофильтр . . |
|||||
|
|
при выходе |
изэлектрофильтра . . . . |
200—250 |
|||
|
|
Скорость газа в камере электрофильтра, |
|
||||
|
|
м/с. |
|
|
|
0,5—1,0 |
|
|
|
Размеры осадительных электродов (труб), |
|
||||
|
|
мм: |
|
|
|
200—300 |
|
|
|
диаметр |
|
|
|
||
|
|
длина |
|
|
|
3000—4000 |
|
Принцип действия |
и условия |
работы |
пластинчатого электро |
фильтра не отличаются от трубчатого, но вместо труб в нем па раллельно расположены пластины, между которыми висят на расстоянии 100—150 мм коронирующие электроды.
Электрофильтры требуют тщательного наблюдения и ухода за ними. При неправильном регулировании температуры, электриче ского режима, влажности или скорости очищаемого газа коэффи циент полезного действия резко падает. Электрофильтры приме няют для очистки газов при обжиге файнштейна, концентратов, а также после конвертеров и шахтных печей. Электрофильтры расходуют меньше энергии, чем рукавные, но плохо улавливают пыль, содержащую большое количество оксидов металлов.
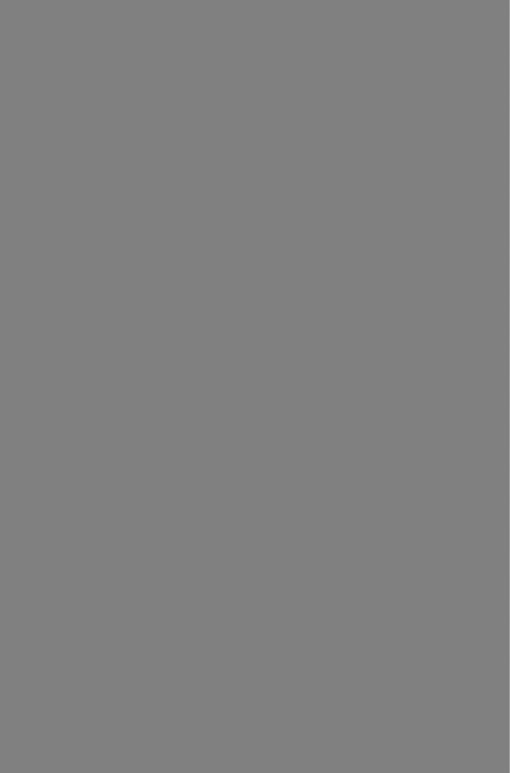
креплены к рамам подвеса, закрепленным на стержне, связанном с встряхивающим механизмом. Механизм встряхивания действует автоматически и поочередно встряхивает рукава во всех каМеРахДля более интенсивной работы рукавного фильтра его периоди чески продувают воздухом в направлении, обратном движению газов.
Газы, подаваемые вентилятором или засасываемые дымососом, проходят через поры ткани, пыль осаждается на внутренней по верхности ткани и ее порах, очищенные газы выбрасываются из фильтров в атмосферу через дымовую трубу.
Рис. 43. Схема поверхностного охладителя (кулера) |
газов: |
|
/ — труба кулера; |
2 — бункер для пыли; 3 — дроссельный |
клапан |
для прямого хода |
газов (помимо охладительных труб) |
|
Рукавные фильтры в цветной металлургии изготовляют из чисто шерстяной ткани; ткани, состоящей из 30 % капрона и 70 % шерсти; синтетических волокон (нитрон, лавсан, капрон), а также из стеклянного волокна. Температура газов для шерстяных рука вов должна быть не более 90 °С, лавсановых 130 °С, из стеклян ного волокна 240 °С. Поэтому газы из металлургических печей, температура которых обычно колеблется в пределах 400—800 °С, перед поступлением в рукавные фильтры следует охлаждать.
Охлаждают газы в трубчатых змееобразных металлических поверхностных охладителях (рис. 43), представляющих собой си стему стальных труб диаметром 300—4Q0 мм. Газ, проходя по тру бам, отдает тепло в атмосферу через их стенки, имеющие большую поверхность. Пыль осаждается в бункера.