
1223
.pdf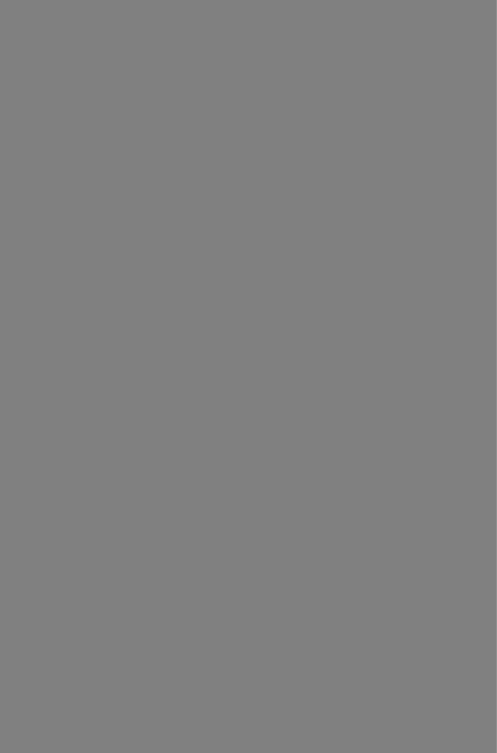
шамот. Печь без ремонта работала 6 лет, в 1952 г. была отре монтирована и переделана в период остановки из-за отсутствия энергии. Износа кладки не обнаружено.
С каждой продольной стороны печи имеется 5 бункеров, за крываемых круглыми чугунными крышками. При загрузке машинист электрокары снимает крышку, опускает течку кон тейнера в горловину бункера, выдвигает шибер и разгружает содержимое контейнера в бункер. Температура загружаемого
Рис. 54. Ванна электропечи мощностью 12 000 ква для плавки медных концентратов:
1 — шихта; 2 — шлак; 3 — штейн; 4 — магнетитовая настыль
в печь огарка 650—750° С и соотношение между обожженным и подсушенным концентратами равно 1 1. Над люком бункеров печи имеется вентиляция, включаемая машинистом в период вьтпрузки огарка.
Бункеры снабжены семнадцатью чугунными течками кругло го сечения. Течки имеют внутренние дисковые клапаны для руч ного регулирования количества подаваемого в печь концентрата. Пять течек расположены вблизи электродов, а двенадцать — дальше от них. При этом достигается равномерная загрузка и необходимый слой шихты на любом участке (рис. 54). Это очень важно, так как дает возможность влиять на проплав, содержа ние меди в шлаках и на состав штейна, поскольку концентрат расплавляется главным образом благодаря погружению его в перегретый шлак.
Энергия подается 6 самоспекающимися электродами диа метром 1,2 м от 6 трансформаторов по 2000 ква каждый, разби тыми на 3 группы. Группы соединены параллельно и питают по 2 электрода. Ток подводится к электродам посредством восьми шин сечением 325 X Ю мм, объединенных в пакет. К концам
шин присоединено 48 гибких кабелей, оканчивающихся толсто стенными медными трубами, охлаждаемыми «водой и прикреп ленными к электрододержателям.
Сила тока регулируется вручную или автоматически с пуль та по принципу поддержания постоянного сопротивления меж ду электродами и штейном в результате вертикального пере мещения электрода. Принятая система регулирования позволяет концентрировать тепловыделение в различных уровнях слоя шлака и сохранять защитный слой магнетита на подине под электродом' Если толщина слоя растет, электроды опускают, если уменьшается — подымают. Для контроля за оптимальной толщиной магнетита в подине печи на глубине 250 мм «под проекцией электродов «вмонтированы термопары. Температура в этой точке поддерживается на уровне 180—200° С.
Электродные щеки-зажимы ранее охлаждались холодной водой. При этом в электроде между зажимом и спеченной частью (ниже свода) образовывались пустоты, грозившие обры вом электрода. После подачи воды с температурой 50—60° С образование пустот прекратилось. Кроме того, при этом улуч шился контакт между кожухом и зажимом, что позволило ослабить затяжку зажимов и уменьшить связанную с этим де формацию электродов. Это способствовало улучшению уплотне ния между электродом и сальником свода печи. Одновременно электрические потери в этом контакте снизились с 1,5 до 0,3%.
Для выпуска шлака в торце печи имеются три летки, армиро ванные медными 'кессонами, и три медных желоба, охлаждае
мых водой, два из них |
попеременно |
работают на грануляцию, |
|||||
а третий — аварийный служит |
для |
выпуска шлака в мульды. |
|||||
Летки расположены на высоте 1,0, 1,12 и 1,25 |
от пода. Жело |
||||||
ба укрыты |
чугунными |
плитами и вентилируются. |
Шлак вы |
||||
пускается |
непрерывно |
и после грануляции гидротранспортом |
|||||
при отношении ж : т = |
10:1 сбрасывается в море. |
Производи |
|||||
тельность насоса 8000 л/мин. |
Шлак |
ежечасно |
анализируется |
||||
на медь и кремнезем и обычно |
содержит 0,32—0,36% Си и 39— |
||||||
41% |
Si02. |
|
|
|
обращенном в конвертер |
||
На противоположном торце печи, |
ное отделение, расположенное перпендикулярно плавильному, имеются три штейновых шпура. Один из них, расположенный ниже остальных,— аварийный, остальные два работают пооче редно, в течение двух недель каждый.
Штейн выпускается в ковши по мере потребности конвертер ного отделения. Шпуры открывают, прожигая кислородом, а закрывают с помощью «пушки». Обычно штейн содержит 36— 40% Си.
В своде печи имеются отверстия для отвода газов в коллек тор грушевидного сечения, находящийся в стороне от печи, >выше
свода. Дно коллектора футеровано износостойкими базальтовыми плитами и пыль из него непрерывно возвращается в -печь скребковым транспортером.
Для снижения содержания меди в шлаке на 0,1—0,2% в зо ну, близкую к выпуску шлака, загружают бедный медью колче дан, а богатые медью -продукты загружают в переднюю часть печи. При 35%-ном содержании меди в штейне в случае раз дельной загрузки шлак содержит 0,3% Си, при обычной загрузке содержание меди в шлаке подымается до 0,4%.
В 1952 г. в части печи, |
из которой производится выпуск |
|||||||||||
шлака, был сооружен |
водоохлаждаемый порог, в период рабо |
|||||||||||
ты которого шлак содержал не более 0,2% |
Си. Так как охлаж |
|||||||||||
дающие трубы были сделаны |
из |
обычного |
железа, порог про |
|||||||||
стоял всего 6 месяцев, после |
чего |
потребовался ремонт печи, |
||||||||||
при котором порог не был восстановлен. |
|
|
|
|
||||||||
Печь |
обычно |
работает при |
разрежении 5—6 мм вод. ет., |
|||||||||
и объем газов достигает 30 тыс. м3/час при |
температуре 300° С. |
|||||||||||
Рабочая |
мощность |
10000 кет, производительность 600 т шихты |
||||||||||
в сутки |
(4,3 т/м2 пода). |
|
|
|
|
|
|
|
|
|||
Технические показатели плавки. |
|
|
|
|
|
|||||||
Проплавлено, |
тыс. /и: |
|
|
|
|
|
|
|
103676 |
|
||
огарка при 700° С |
|
|
|
|
|
|
|
|
||||
сухих концентратов |
|
|
|
|
|
|
101409 |
|
||||
холодных оборотов |
. |
|
. . . |
|
|
|
14393 |
|
||||
Содержание в шихте меди, % |
|
|
|
|
15,3 |
|
||||||
Получено штейна при температуре |
И 12° С, тыс. m |
|
|
98177,0 |
|
|||||||
Получено шлака при температуре |
1209° С, |
тыс. m |
|
|
185620,0 |
|
||||||
Расход электроэнергии, квт-ч/ш шихты |
. |
|
|
394 |
|
|||||||
Израсходовано рабочей силы на 1 |
т шихты, чел-час. |
|
0,276 |
|||||||||
Состав штейна и шлака |
приведен в табл. 21. |
|
|
|||||||||
|
|
|
Состав штейна и шлака |
|
Т а б л и ц а |
21 |
||||||
|
|
|
|
|
|
|
||||||
|
|
|
|
|
|
Содержание. % |
|
|
|
|
||
Продукт |
Си |
Fe |
N1 |
S |
Zn |
Pb |
As |
Si02 FeO |
CaO-f- |
Au |
A*r |
|
|
+ MgO |
Al?Oe e/m |
г/т |
|||||||||
Штейн |
35,6 |
30,2 0,4 |
24,6 |
5,4 |
2,7 |
0,3 |
38,1 37,8 |
5,2 |
30,5 |
339 |
||
Шлак |
0,38 |
0,03 |
0,8 |
4,1 |
0,5 |
|
8,1 |
|
В Болгарской Народной Республике на заводе в Пирдоне медный концентрат после обжига в кипящем слое подвергается плавке в электропечи. Электропечь имеет длину 8 м, ширину 3,8 м й высоту 4 м при площади ванны 30 м2. Кладка подины и стен — из магнезита, свода — из шамота и жаростойкого бето на. По длинным сторонам печи имеется 10 загрузочных от верстий.
Питание печи током производится от трансформатора мощ ностью 3500 ква при напряжении от 90 до 178 в через три само
стоятельных |
самоспекающихся электрода |
диаметром |
700 мм. |
Суточный |
проплав составляет 184 г, |
что соответствует |
|
6 т/м2 в сутки при удельном расходе энергии 393 квт-ч/т. |
|||
Шихту загружают в печь при температуре 450—500° С. Шлак |
|||
содержит 40—42% ЗЮг, 42% FeO и 7% СаО + MgO. |
Штейн |
содержит 36% Си. Глубина шлакового слоя 1,8—2 ж, штейново-
го слоя 0,6 м. Десульфуризация |
три плавке составляет 20% |
|
и |
газы, содержащие 2,5—3% сернистого ангидрида, совместно |
|
с |
богатым газом от конвертеров |
направляют на производство |
серной кислоты. В связи е загрузкой |
мелкого, пылящего огарка |
|||
из печи для обжига в кипящем |
слое |
при |
тлавке происходит |
|
большой .вынос пыли, достигающий 3% от веса загрузки. |
||||
Для переработки |
медных |
концентратов |
рудника Килямба |
|
в Уганде (Северная |
Родезия) |
установлена |
электропечь мощ |
ностью 5000 кет. Печь трехэлектродная, длиной 13,5 ж, шириной 5,34 ж, производительностью 9000 т меди в год [261].
Установка печи позволила успешно перерабатывать конвер терные шлаки с разрушением содержащихся в них ферритов и заметно уменьшить выход газов, сократив объем пылеулавли вающей аппаратуры, и получать серную кислоту три минималь ных затратах.
Об исследованиях в лабораторном масштабе плавки медных концентратов Алтая сообщает И. И. Кершанский [262]. Концен траты перед плавкой окатывали в чашевом грануляторе до зерен размерами 10—15 мм. В состав перерабатываемой шихты помимо концентратов входили кварцевый песок, клинкер от вельцевания кеков и до 40% по весу оборотных конвертерных шлаков (табл. 22). О выходе продуктов плавки и распределении между ними металлов можно судить по данным табл. 23.
При добавке в шихту 20% по .весу клинкера, содержавшего 25% С, что определило содержание в шихте 2,7% С, плавка про текала без осложнений. При этом в штейне и шлаке оставалось не более 35% цинка из шихты, основная его часть переходила в возгоны. Штейн при этом получался беднее медью и богаче железом. Дальнейшее увеличение количества клинкера в шихте приводило к образованию настылей в печи и нарушало ход
плавки.
При плавке концентратов, обожженных предварительно до содержания 13% S, в составе шихты, составленной из 100 ч. ога.рка, 16 ч. конвертерного шлака, 16 ч. клинкера и 27 ч. квар цевой руды (на штейн с 40% Си И шлак е 40% ЭЮг), был по лучен штейн с содержанием 40% Си, 5% РЬ и 5% Zn при 23% Fe. Цинка в штейн перешло 20% (30% перешло в шлак и 50% — в возгоны), меди 96% и свинца 70%.
Т а б л и ц а 22
Компоненты
Состав шихты медной |
электроплавки |
|
|
|||
Содержа компоние нентов.% |
Си РЬ Zn |
Fe |
S |
sio2 |
CaO |
A I2O3 MgO |
|
|
Примерное содержание, % |
|
Рудная шихта |
|
45,7 |
23 |
1,6 |
8,9 |
23,8 |
32,5 |
5,4 |
0,1 |
0,4 |
2,4 |
|
Беловский концентрат |
6,4 |
23 |
5,1 |
12,6 |
21,9 |
31,4 |
1,6 |
— |
0,7 |
0,9 |
||
Березовский |
концент |
19,7 |
20 |
1,9 |
Н ,7 |
22 |
31 |
5,9 |
0,6 |
0,2 |
1,7 |
|
рат |
|
кон- |
20,5 |
20 |
11,3 13,5 |
17,5 |
28,8 |
3,1 |
0,8 |
0,6 |
1,5 |
|
Золотушинский |
||||||||||||
ттаиФПпФ |
|
|
|
|
|
|
|
|
|
|
|
|
центрат |
|
|
|
|
|
|
|
|
|
|
|
1,4 |
Зыряновский |
концент |
7,7 |
12 |
3,6 |
2,8 |
32,1 |
33 |
5,2 |
0,5 |
0,8 |
||
рат |
|
кон |
|
— |
0,4 |
0,2 |
1,2 |
|
84,6 |
— |
— |
— |
Лениногорский |
— |
— |
||||||||||
центрат |
|
|
|
|
|
|
|
|
|
|
|
0,6 |
Кварцевый песок |
— |
3 |
М |
4,2 |
23,8 |
8,2 |
17 |
1 |
— |
|||
Клинкер |
|
|
|
|
|
|
|
|
|
|
|
|
Оборотный |
20—78 |
4 |
3,2 |
9,8 |
42,3 |
2,8 |
18,7 |
1,1 |
_ |
0,2 |
||
конвертер |
|
|
|
|
|
|
|
|
|
|
||
ный шлак |
|
|
|
|
|
|
|
|
|
|
||
|
|
|
|
|
|
|
|
|
|
Т а б л и ц а |
23 |
|
Выход продуктов и распределение между ними металлов |
|
|
||||||||||
|
|
при плавке алтайских медных концентратов, |
% |
|
|
Выход Продукты % от веса
шихты
Штейн |
70 |
Шлак |
22,1 |
Пыль |
1,2 |
Медь |
Свинец |
|
Цинк |
Железо |
|||
содержа ние |
распреде ление |
содержа ние |
распреде ление |
содержа ние |
распреде ление |
содержа ние |
распреде ление |
22 |
99 |
4 |
82 |
10 |
76 |
32 |
85 |
0,27 |
1 |
0,55 |
3 |
6 |
13 |
19 |
15 |
— |
— |
15 |
15 |
42 |
11 |
— |
— |
Шлак содержал 0,73% Си и 5% Zn и не мог считаться от вальным. Расход флюсов составил 26%. Полученные результа ты не позволяют усмотреть существенных преимуществ плавки обожженной шихты.
Степень десульфуризации при плавке необожженной шихты близка к 25%, она увеличивалась с добавкой конвертерного шлака и уменьшалась с ростом в шихте количества клинкера. Степень десульфуризации при плавке обожженной шихты со ставляет 13%.
Максимальное извлечение золота и серебра в штейн получе но при плавке необожженной шихты, в особенности в присутст-
вии содержащегося в клинкере восстановителя. При этом поте ри в шлаке составили: золота 0,9%, серебра 0,5%. В пыль перешло не 'более 0,03% каждого из этих металлов. При плавке огарка потери золота и серебра в шлаке достигли 6% и в пыли
0,6- 0,7% .
Проведенные опыты показали возможность и целесообраз ность электроплавки необожженных медных концентратов, со держащих 20% и более меди в смеси с конвертерным шлаком и клинкером. При этом получаются отвальные шлаки и в штейн извлекается около 99% Си, 82% РЬ и 76% Zn. Извлечение меди при плавке обожженной шихты несколько ниже и шлак значи тельно богаче.
Плавка гранул успешно протекала |
при содержании в них |
|||
до 9% влаги. |
Десульфуризация |
при |
плавке необожженных |
|
концентратов |
составляла до 25% |
и преимущественно |
происхо |
|
дила за счет термического разложения |
халькопирита. |
Добавка |
углерода снижала десульфуризацию и способствовала уменьше нию потерь металлов со шлаками.
При |
бессемеровании штейна и переработке |
конвертерных |
||||||
шлаков |
медь весьма |
полно |
извлекается в |
черновой |
металл, |
|||
свинец — в (пыли конвертерного передела |
и |
цинк — в пыли |
||||||
электропечи. |
что |
плавка |
сульфидных |
железистых |
||||
Выше указывалось, |
||||||||
медных |
концентратов |
производится |
главным |
образом |
в отра |
жательных печах. Преимущества электроплавки перед этим процессом не столь велики, чтобы они определили необходи мость немедленного отказа от старой технологии и переоборудования заводов на электроплавку.
Видимо, в первую очередь при строительстве новых заводов будут выбирать наивыгоднейший процесс и с учетом конкрет ных условий принимать ту или иную технологию.
В этой связи особый интерес представляют условия плавки медных концентратов, полученных из руд с кремнистой вмещаю
щей породой, концентратов |
тугоплавких, содержащих |
много |
||||
кремнезема. |
|
таких |
концентратов излагается |
ниже.2 |
||
Опыт электроплавки |
||||||
2. ПЛАВКА КРЕМНИСТОГО МЕДНОГО КОНЦЕНТРАТА |
|
|||||
Плавке |
подвергали |
концентрат, |
содержащий |
28—38% Си, |
||
2—4% РЬ, |
1—4% Zn, |
6—8% Fe, |
12—18% S, |
20—34% |
SiO?, |
4% Alg03 и около 2,5% суммы окислов кальция и магния. Лабораторные исследования проводил К. В. Сушков [263
266], полупромышленные испытания в печи 150 ква — автор с сотрудниками [267], описываемые исследования проводил И. И. Кершанский в полупромышленном масштабе.
Высушенный концентрат транспортировали к расходному бункеру. Газы из сушильного 'барабана очищали от-пыли в мокром циклоне и кек направляли на сушку. Конвертерный шлак и известняк после взвешивания дробили в щековой и вал ковой дробилках и загружали в бункеры.
Порцию сухого концентрата загружали из бункера в кюбель, в который в необходимом количестве добавляли конвертерный шлак и известняк. Кюбель с шихтой мостовым краном подавали к одному из 6 бункеров электропечи, расположенных по длин ным ее -сторонам. Шихту загружали в печь через свод плунжер ными питателями непрерывного действия, установленными под каждым бункером.
Печь прямоугольная, размером 2,55 X 1,3 ж (F = 3,3 ж2),
трехфазная, мощностью 500 ква. |
уровне -расплава динасовым, |
Стальной кожух футерован на |
|
выше расплава — магнезитовым |
кирпичом. Толщина кладки |
460 жж, пространство между кладкой и кожухом заполнено ди атомовым кирпичом, шамотной набивкой и аобокартонохм. Арочный овод выложен шамотным кирпичом толщиной 300 жж. В своде имеется шесть отверстий диаметром 200 жж для за грузки шихты и три отверстия диаметром 300 жж для электро
дов. Кроме того, имеются |
два малых отверстия диаметром |
60 жж для замера глубины ванны и температуры в печи. |
|
Для выпуска штейна в боковой стене печи предусмотрены |
|
два шпуровых отверстия |
диаметром 30 жж, расположенных на |
высоте 80 и 120 жж от подины. Шпур для выпуска шлака распо ложен в торцевой стене на высоте -550 жж от подины.
Кожух орошается водой, а штейновые шпуры защищены во доохлаждаемыми медными кессонами. Газы по кессонированному газоходу поступают таким же способом в охлаждаемую камеру, в которой дожигается окись углерода и осаждается грубая пыль. Пыль из камеры удаляется проложенными по ее дну шнеками. Из камеры газы направляются в рукавный фильтр
и после очистки выбрасываются в атмосферу. |
|
|
||
Печь питается |
электроэнергией от трехфазного трансформа |
|||
тора типа ЭПТЦН-5600/6, |
имеющего 49 ступеней |
напряжения. |
||
Напряжение -при холостом ходе 6000/120 У з — 30 |
в. |
|||
Электроды графитированные диаметром 250 жж с распадом |
||||
750 жж. Перемещаются они |
с помощью электролебедок, а про |
|||
ход их через свод |
герметизирован гидравлическим |
уплотни |
||
тельным устройством. |
|
|
|
|
Характеристика исходных продуктов |
|
|||
Концентрат содержал |
около 50% классов |
мельче 0,1 мм |
и 45% классов от 0,1 до 0,2. На все классы крупнее 0,2 мм при ходилось только 5% концентрата.
Через сито минус 10 мм (проходило 30% конвертерного шлака, 62% известняка и весь «кексик.
Медь, -свинец и цинк представлены в концентрате в виде сульфидов. Конвертерный шлак содержал, %: 3—13 Си, 4—10 РЬ, 3—8 Zn, 27—35 Fe, 0,3—4 S, 22—34 Si02, 1 A120 3 и от
2 до 3,5 суммы |
окислов |
кальция и |
магния. В конвертерном |
|
шлаке |
первого |
периода |
содержатся |
магнетит, цинковистый |
фаялит |
и силикатное стекло. Шлак |
включает капли штейна |
и меди, на долю которой приходится 2/3 общего содержания ме ди в шлаке. Свинец входит в -состав силикатного стекла. Кон вертерные шлаки второго периода богаты медью, находящейся в окисленном состоянии и в виде металла. Анализ фазового -со
става шлаков |
подтвердил |
необходимость |
применения |
при |
||||
плавке кокса для восстановления свинца, меди и магнетита. |
|
|||||||
|
Сушка концентрата |
|
|
|
|
|||
Поступающие |
на завод |
концентраты содержали |
10—15% |
|||||
влаги и высушивались в 'барабане |
до содержания |
ее 2—4%. |
||||||
При этих условиях пылеобразование |
было |
незначительным и |
||||||
подача шихты в печь -не вызывала затруднений. |
на |
уровне |
||||||
Температуру |
в топке барабана |
поддерживали |
||||||
280—340° С. Производительность |
барабана |
составляла 4 т!час |
||||||
при расходе мазута 25—30 кг на 1 тконцентрата. При этом |
без |
возвратные потери с выхлопными газами в среднем составляли 3,5 кг/час пыли, а пыль, уловленная в -сухом и мокром циклонах, содержала 36—38% Си, 3—7% РЬ, 2—4% Zn, 5—9% Ре, 16— 20% S, 18—22% Si02 и 2—3% С и по составу мало отличалась от концентрата.
Плавка концентратов с известняком и конвертерным шлаком
Плавку проводили при линейном напряжении на электродах 290 в, силе тока 1300 а, глубине ванны около 1000 м и заглубле нии электродов около 475 мм. В шихту вводили 20% конвертер ных шлаков, 12% известняка и 0,5% коксика.
Продукты плавки выпускали перегретыми — шлак при 1320—1380° С, штейн при 1100—1150° С. Расход электроэнергии составил 560 квт-ч и электродов 2,2—2,75 кг на 1 тшихты. Удельная производительность печи по шихте составила 6,6 т/м2 в сутки (5,0 т/м2— по концентрату). При этом удельная мощ ность равнялась 150 ква/м2. Простои составили около 1,5% календарного времени. Баланс металлов приведен в табл. 24.
Выход штейна составил 65% |
и шлака 55%, а пыли из камеры |
|
и рукавного фильтра 4,5% |
от |
веса концентрата. Штейн содер |
жал 50% Си, 6% РЬ и 5% |
Zn и в него было извлечено около |
9 М. М. Лакерник
95% Си, 84% РЬ и 65% Zn. Пыль, помимо металлов, содержала
до 15% Si02, 2% СаО и |
2% А120 3. В пыль перешло 4% |
Си, |
8,5% РЬ и 10% Zn. |
выход пыли связан с малым подсво |
|
Сравнительно высокий |
||
довым пространством в печи и плавкой мелкого материала. |
|
|
|
Т а б л и ц а |
24 |
Выход продуктов плавки и распределение межДу ними компонентов, %
Продукт плавки
Выход про дуктов. % |
Медь |
|
содержа ние |
распреде- , ление |
Свинец |
Цинк |
Железо |
Сера |
||||
|
|
|
|
|
|
|
| |
содержа ние |
распределе!гие |
содержа ние |
распреде ление |
содержа ние |
распреде ление |
содержа ние |
распреде ление |
Загружено |
|
|
|
|
|
|
|
|
|
|
|
|
|
|
Концентрат |
|
100 |
33,24 96,3 |
3,52 69,8 |
3,83 71,2 |
7,2 |
|
50,8 16,38 97,8 |
||||||
Конвертерный шлак |
20,5 |
6,20 |
3,7 |
7,41 30,2 |
7,55 28,8 33,2 |
|
47,9 |
1,78 |
2,2 |
|||||
Известняк |
|
11,8 |
— |
— |
— |
— |
— |
— |
1,56 |
1,3 |
— |
— |
||
Кокс |
|
0,5 |
|
|
|
|
|
|
|
|
|
|
|
|
Получено |
|
|
|
|
|
|
|
|
|
|
|
|
|
|
Штейн |
|
65,1 |
50,21 94,74 6,46 84 |
5,2 |
65,0 13,37 61,4 23,89 95,2 |
|||||||||
Шлак |
|
55,5 |
0,35 |
0,56 0,50 |
5,5 |
2,17 22,8 |
9,28 36,3 |
— |
— |
|||||
Пыль камерная |
2,5 |
33,26 |
2,9 |
9,06 |
5,5 |
9,17 |
5,8 |
7,92 |
1,5 17,01 |
2,7 |
||||
Пыль фильтров |
|
2,0 |
30,4 |
1,8 |
9,88 |
5,0 14,28 |
6,4 |
5,81 |
0,8 17,6 |
2,1 |
||||
Шлак содержал от 0,2 до 0,5% Си, от 0,3 до 0,8% РЬ и от 1,3 |
||||||||||||||
до 3,2% Zn. Кроме того, шлак содержал 10% Ре, |
до 14% СаО, |
|||||||||||||
53—59% |
Si02, 6% |
А120 3 и |
1,6% MgO. |
Потери |
металлов |
со |
||||||||
шлаком |
весьма |
малы и |
не |
превышают |
0,6% Си, |
5,4% |
РЬ |
|||||||
и 22% Zn. |
|
|
|
|
при |
условиях |
слабовосстанови |
|||||||
Степень десульфуризации |
||||||||||||||
тельной атмосферы в печи крайне мала и близка к 2%. |
|
|
||||||||||||
|
Распределение благородных металлов, редких |
|
|
|||||||||||
|
|
|
и рассеянных элементов |
|
|
|
|
|
||||||
Анализ сырья и продуктов плавки показал, что в штейн |
из |
|||||||||||||
влекается 95% Ag, в пыль |
его переходит около 5% и в шлак |
|||||||||||||
0,5% при содержании в нем 3,6 г/г Ag. |
|
Re и 0,03% |
Cd рас |
|||||||||||
При содержании |
в концентрате |
0,002% |
||||||||||||
пределение этих |
металлов по продуктам |
плавки |
характери |
|||||||||||
зуется данными, приведенными в табл. 25. |
|
|
|
|
|
|
||||||||
Основная часть |
рения и кадмия переходит в штейн, около |
|||||||||||||
30% этих металлов |
переходит в пыль и ничтожное количество |