
1223
.pdfВ настоящее время годовая производительность завода со ставляет 37 тыс. тсвинца и основная технологическая схема та кова: агломерация свинцовых концентратов с предварительной сушкой и окатыванием шихты; плавка агломерата в электропе чи; продувка расплавленного свинца .в горизонтальных конвер терах; рафинирование чернового свинца, в том числе обезмеживание в котлах; обессеребрение цинком и вакуумное обесцинкование свинца с последующей щелочной доводкой; переработка конвертерных шлаков во вращающейся короткобарабанной пе чи с получением медно-натриевого штейна и чернового свинца; очистка отходящих газов (конвертерных и от короткобарабан ной печи) в скоростных пылеуловителях (рис. 55).
Агломерация
Как известно, агломерация концентрата, содержащего 80% свинца, представляет большие трудности, связанные с вытапли ванием металлического свинца, и нигде не применяется. Поэто му на заводе Роншер применяют схему подготовки и спекания шихты, существенно отличающуюся от других известных схем.
Поступающие на завод концентраты после оттаивания по дают на разгрузочную станцию, откуда (через промежуточный склад) направляют в бункеры шихтовочного отделения или, в случае необходимости, на сушку.
Концентрат сушат в трубчатой печи, отапливаемой мазутом* с автоматическим регулированием температуры путем измене ния расхода мазута и воздуха.
Концентрат, высушенный с 5—12 до 1—2% содержания влаги, транспортируют для хранения в пять бетонных бункеров общей емкостью 12,5 тыс. т. Отсюда грейферным краном его передают в четыре промежуточных бункера, питающих ковше вой транспортер, передающий концентрат на доизмельчение в молотковые дробилки, из которых он лотковым питателем вы дается на сборный транспортер.
Способ приготовления шихты для агломерации существенно отличается от известных нам до настоящего времени. Шихта агломерации состоит из концентрата, оборотного агломерата, пыли агломерационного и плавильного цехов, а также известня ка, предварительно измельченного в стержневых мельницах.
Шихту 'подготавливают последовательным окатыванием. Компоненты шихты подаются из соответствующих бункеров ве совыми питателями с автоматическим регулированием на лен точные транспортеры, которые передают их на окатывание. Окатывание (грануляцию) производят последовательно четырь мя грануляторами (двумя барабанными и двумя чашевыми). Производительность грануляторов составляет, т/час: 23 агломе
рационного оборота, 1,5 пыли, 3 известняка, 23 концентрата; всего 50,5 т/нас (обычно расход пыли составляет 10, а концент рата и возврата по 20 т/час).
В первый цилиндрический барабанный гранулятор подается весь оборотный агломерат, пыль и известянк. Оборотный агло мерат представляет собой хорошо отгрохоченный, кусковой спе ченный материал с размерами частиц —12 +5 мм. Влажность шихты колеблется в пределах 5—8%, и так как она заметно влияет на процесс грануляции, регулированию влажности уде ляется большое внимание. Увлажняется каждый компонент от дельно. Питание и разгрузка всех грануляторов производятся непрерывно.
Первые гранулы ленточным транспортером подаются во вто рой конический барабанный гранулятор, в который непрерывно загружается половина концентрата (11,5 т). Барабан, так же как и первый, делает 10 оборотов в минуту. Если влажность по ступающего со склада концентрата 2—3%, то дополнительно его не увлажняют.
Гранулы второго гранулятора транспортируют в третий — чашевый гранулятор, куда также непрерывно подается вторая половина концентрата (11,5 т) и накатывается второй его слой. Наконец, эти гранулы поступают в четвертый чашевый грануля тор для окончательного, более прочного окатывания гранул и питания паллет агломерационной машины. Обычно гранулы име ют правильную шарообразную форму с прочно накатанным сло ем концентрата толщиной 1,5—2,5 мм.
Чашевые грануляторы диаметром 4 м имеют одинаковую конструкцию. Скорость вращения колеблется от 10 до 12 об/мин; угол наклона чаши можно менять по потребности, но обычно он поддерживается в пределах 45—50°.
Своеобразный метод окатывания шихты, примененный швед скими металлургами, позволяет вести агломерацию при невысо кой температуре без местных перегревов, добиваясь обжига и спекания частиц в интервале температуры 850—900° С. Извест но, что при температуре ниже 800° С окисление сульфида свин ца кислородом протекает крайне медленно, а при температуре выше 900° С сульфид интенсивно взаимодействует с окислами свинца, образуя металлический свинец, вызывающий прежде временное сплавление шихты, заливание колосников паллет и вакуум-камер агломерационной машины со всеми вредными по следствиями, исключающими возможность получать агломерат удовлетворительного качества.
Получая очень пористую (из гранул диаметром 16—20 мм) шихту, на заводе Роншер обеспечивают регулирование темпера туры при обжиге и агломерации, что позволяет вести процесс •с образованием небольшого количества металлического свинца.
Большая пористость гранул препятствует сливанию получаю щегося свинца в большие массы, а мелкие капли поглощаются
гранулами.
Главное свойство гранул—пористость не только ядра, но и окатанной оболочки. Эта пористость появляется в результате испарения влаги и некоторого набухания оболочки, что обеспе чивает впитывание образующегося в зоне высокой температуры металлического свинца и его окиси или других легкоплавких компонентов шихты.
Однородность и хорошая газопроницаемость шихты обеспе чивают возможность большой вертикальной скорости обжига и спекания на ленточной агломерационной машине.
Готовые гранулы загружают на тележки машины, на слой постели, состоящей из наиболее крупных частиц агломерата.
На заводе имеется одна агломерационная машина площадью 27 м2, шириной 1,5 м -с 10 камерами всасывания. В голове ма шины установлено два питателя — один для постели, другой для гранул. Питатели барабанные, без маятников.
Агломерат, содержащий около 70% РЬ, 5—6% S (в том чис ле около 3% сульфидной), сбрасывают с паллеты в виде равно мерно спеченного остывшего до темного цвета пирога и дробят в валковой дробилке. Дробленый материал наклонным тщатель но закрытым ковшевым транспортером подается на верхнюю от метку цеха и подвергается классификации на двухдечном виб рационном грохоте для разделения на три класса. Самый круп ный класс ( + 12 —20 мм) поступает на агломерационную ма шину в качестве постели, средний класс ( + 5 —12 мм) направ ляется на шихтовку в качестве оборота, (мелкий класс передает ся в плавильный цех. Газы очищаются от пыли в рукавном фильтре с рукавами из синтетических тканей.
В агломерационном цехе на отметке верхней ветви паллет агломерационной машины установлен пульт управления, из ко торого хорошо виден весь цех. Наряду с обычными контрольно измерительными приборами, характеризующими работу маши ны (температура и расход газов, разрежение и др.), там имеет ся общая схема агломерационного цеха, позволяющая с по мощью световой сигнализации судить о состоянии того или иного агрегата, а также пускать в ход или останавливать отдельные агрегаты. На пульте установлен также телевизор, позволяющий наблюдать за качеством окатывания шихты.
Цех работает одну смену в сутки и обслуживается четырьмя рабочими.
Электроплавка
Шихта состоит из агломерата (85%), молотого известняка (3—5%), конвертерного шлака свинцового производства и гру
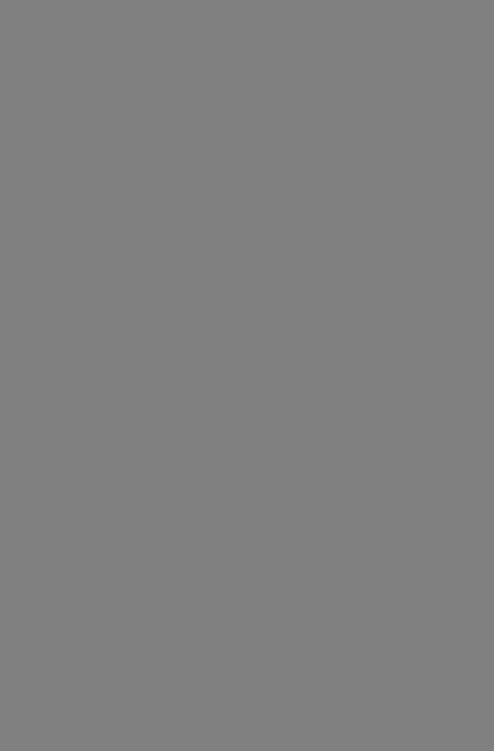
на рис. 57. Для снижения потерь свинца -со шлаком шихту перед выпуском шлака не загружают.
Возникающее около электродов интенсивное движение ших ты, погруженной в перегретый примерно до 1400°С шлак, обес печивает хороший контакт и форсированное плавление.
Печь работает на шлаке состава, %: 24 Si02, 30—35 СаО, 16—17 FeO, 13—15 ZnO, 4—5 MgO, 2—3 А120 3, 3—4 Pb. Темпе ратура шлака 1300—1400° С. Шлак выпускают через торец печи и отвозят в жидком состоянии в отвал. За каждый выпуск по* лучают 15—20 т шлака, что составляет 50% по отношению к чистому свинцу. Шлаковая летка обслуживается вручную. По тери свинца со шлаком 1,5%. У торца лечи сделан железобетон ный зумпф на случай аварийного .выпуска расплава.
Черновой свинец содержит, %: 90 РЬ, 2,5—3 S, 3—4 Си. Его выпускают через шпур в одной из боковых стен и сливают в конвертер. Образовавшийся в печи штейн полностью растворяет ся -в черновом свинце и вместе с ним выпускается в ковши. Уро вень свинца в печи 275—300 мм.
Проплав печи на 1 м2составляет в среднем около 5 г, расход электродов 9 кг, электроэнергии 487 квт-ч/т шихты.
Печь работает при разрежении 5—6 мм вод. ст. Выход пыли составляет около 12% от веса шихты.
Печь прямоугольной формы размером 13X4, 5 X 3,2 м при площади ванны около 58 м2. Мощность ее около 4000 ква, что соответствует 70 кет на 1 м2 года. Печь снабжена четырьмя самоспекающимися электродами диаметром 1 м, соединенными по схеме Скотта с двумя трансформаторами. Вторичное напря жение трансформаторов может -быть выбрано из 17 ступеней между 100—200 или 200—400 в. Электроды погружены в шлак, служащий телом сопротивления. Футеровка печи магнезитовая, стены и подина закрыты кожухом из листовой стали толщиной 25 мм, шпуры защищены водоохлаждаемыми медными плитами. Кожух до уровня верхней отметки ванны орошается водой. Ра диус подины 4 м при ширине печи 4,5 м. Под печи краями упи рается в пояс из пятовых магнезитовых блоков; на этот же пояс опираются стенки печи. Конструкция и крепление подины пре дупреждают ее всплывание в свинцовой ванне.
Кожухи самоспекающихся электродов из стали толщиной 1,2 мм сварены сплошным плотным швом, благодаря чему при заливке электродов расплавленной электродной массой и при наращивании поверхность электрода над сводовым кольцом по лучается ровной и чистой, без натеков и прогаров. Потери в контакте между электродом и щеками не превышают 0,3% под водимой мощности.
Уплотнение сводовых колец, имеющих зазор 100 мм вокруг электрода, представляет легкую стальную конструкцию, лежа
щую непосредственно на своде печи (рис. 58) с набивкой из ас бестового шнура.
Перепуск электродов производится не более чем на 250 мм.
/1
1 Асбестовый шнур
Рис. 58. Уплотнение сводовых колец на печах завода Роншер
Черновой свинец для удаления содержащихся в нем серы, мышьяка, сурьмы-продувают воздухом в горизонтальных конвер терах с магнезитовой футеровкой, работающих при температуре 900—1000° С не более 2—3 час. в сутки, в течение которых про дувается все количество получаемого свинца. Конвертер диамет
ром 1,8 Mt длиной 4 м |
(внутренние размеры), |
емкостью около |
40 т чернового свинца |
снабжен 18 фурмами, обеспечивающими |
|
подачу 100 м3 ^воздуха |
в минуту. Установлено |
два конвертера, |
в которых перерабатывают также различные продукты рафини ровочного передела.
10*
Конвертерные шлаки после повышения в них вследствие цир куляции концентрации меди до 25% поступают в небольшую вращающуюся на роликах короткобарабанную печь, отапливае мую мазутом и работающую при температуре 1200° С. Вместе <со шлаками в эту печь иногда загружают также медистые шлике ры, снятые при рафинировании в котле продутого в конвертере свинца. При добавке 'кокса и 7% кальцинированной соды вос станавливают свинец и получают медно-натриевый штейн, со держащий 40% Си и направляемый в. конвертер медеплавильно го завода.
Продутый свинец, содержащий не более 0,1% .меди, после ох лаждения до 500° С ковшами доставляется на рафинирование. Время (продувки 1 т свинца 0,9 мин.
Извлечение свинца при электроплавке 96%. Общее извлече ние свинца с учетом переработки полупродуктов достигает 98,2%.
Обезмеженный свинец подвергают дальнейшим обычным ста диям рафинирования [288].
Тепло отходящих из электропечи газов утилизируется в кот лах площадью 360 м2, дающих около 3 тшара в час. Запылен ные газы 'после котла при температуре 350° С проходят пылевую камеру, где оседает 25—40% возгонов. После охлаждения в по верхностном холодильнике до 100° С газы направляют в элект рофильтр, где улавливают основную массу пыли. С появлением скоростных пылеуловителей они были установлены после элек трофильтра для выделения из газов остатков пыли.
Общий к. п. д. газоочистки 99,0—99,5%. Газы после трубы Вентури проходят циклоны, в которых отделяется шлам, под вергаемый отстаиванию и фильтрации на барабанном -вакуум- фильтре.
2. ВОССТАНОВИТЕЛЬНАЯ ПЛАВКА В ЭЛЕКТРОПЕЧИ
Возможность (Применения реакционного процесса в электро печи (к богатым свинцовым концентратам подтверждена описан ной выше промышленной практикой завода Роншер.
В настоящее время в результате успехов флотационного обо гащения значительно увеличивается количество богатых свинцо вых концентратов, содержащих менее 80, но не более 60% свин ца, для которых реакционная плавка нерациональна.
Представляет большой интерес оценить возможность приме нения к таким концентратам восстановительной электроплавки
всравнении с шахтной плавкой.
В1948 г. автор исследовал процесс восстановительной плав ки свинцовых концентратов, содержащих примеси меди и цинка.
При этом 85% свинца было извлечено в металл, в возгоны пе-
решло 85% цинка, в штейн было извлечено 90% меди. Система
тические исследования в этом направлении |
были |
проведены |
|||||
в период 1952—1960 |
гг. |
А. П. |
Сычевым и др. [289—293] во |
||||
ВНИИцветмете и на Лениногорском заводе. |
площадью 1,2 м2 |
||||||
Построенная |
для |
исследований |
печь |
||||
(1,75 X 0,7 X 1,5) |
питалась |
током |
от трансформатора |
с нижней |
|||
ступенью напряжения |
ПО в. Подина |
печи была выложена из |
угольных блоков, стены (на высоту ПО мм) — из хромомагнези тового кирпича, свод и верхняя часть стен — из шамотного кир пича. В своде печи по продольной ее оси имелось четыре отвер стия для загрузки шихты и отвода газов, а также для ввода электродов. Печь работала при давлении 0,5—1,0 мм вод. ст.
Были исследованы некоторыефакторы, влияющие на ход плавки.
Выбор напряжения
Исследование проводилось с агломератом, приготовляемым для шахтной плавки, и поэтому получаемый шлак содержал 38% закиси железа, около 22—23% кремнезема, до 15% окиси цинка и не более 15% окиси кальция.
Из приведенной выше характеристики шлаков видно, что расплав отличается большой электропроводностью и плавка его при высоком напряжении сопровождается сильным перегревом верхней части. Это ведет к повышенному улетучиванию свинца и снижению прямого выхода его в металл.
Для более высокого выхода свинца в металл необходимо стремиться к равномерному распределению подводимой мощности в приэлектродной зоне и к исключению местных перегревов шла ка. Такие условия получаются при заглублении электродов, рав ном примерно половине высоты шлаковой ванны.
При опытах на печи описанной конструкции не удалось заглубить электроды более чем на 80—100 мм при общей высо те шлаковой ванны 500—600 мм. При этом перегревались верх ние слои расплава, температура отходящих газов повышалась до 1150° С и в возгоны переходило до 20% свинца.
Трансформатор был заменен на другой — со ступенями на пряжения 57—76 в. Опыты показали, что наилучшим оказалось напряжение 57 в. При этом погружение электродов составило 300—320 мм, вся ванна равномерно прогревалась, температура отходящих газов не превышала 600—700° С и в возгоны перехо дило не более 5% свинца.
В условиях выбранного оптимального напряжения было ис следовано влияние количества серы в агломерате и восстанови теля в шихте на показатели плавки.
Влияние расхода восстановителя
Вводимый в шихту углерод расходуется на восстановление окислов свинца, цинка и железа и расход его определяется главным образом содержанием этих компонентов в агломерате.
Для агломерата, содержащего 18% железа, 12% цинка и 36% свинца, при условии восстановления-половины окиси цинка
и получении штейна, содержащего 30% железа, |
теоретический |
|||||||||
расход углерода равен 3,5, что соответствует 4% кокса. |
на вы |
|||||||||
В табл. 30 показано влияние расхода |
восстановителя |
|||||||||
|
|
|
|
ход свинца в металл из агло- |
||||||
|
|
Т а б л и ц а 30 |
мерата, содержавшего 3 и 4% |
|||||||
Выход свинца в металл |
серы. |
|
|
|
|
|
||||
|
Выход свинца. % при |
содержа- |
что |
с |
увеличением |
расхода |
||||
Расход |
содержании серы |
|||||||||
кокса |
|
|
Нвештейнеа |
восстановителя |
возрастает |
вы- |
||||
% |
3% |
4% |
% |
ход свинца в металл. |
|
|
||||
|
|
|
|
|
повышение содержания се- |
|||||
4 |
80,0 |
74,0 |
42.1 |
<ры |
в агломерате, |
сопровож- |
||||
5 |
85,0 |
82.7 |
33.2 |
дающееся увеличением |
содер- |
|||||
6 |
88,2 |
85.7 |
22*7 |
жания в нем сульфида свин- |
||||||
7 |
90,5 |
88,9 |
12.2 |
ца, |
вызывает |
необходимость |
||||
вителя |
|
|
|
увеличивать расход |
восстано- |
|||||
для образования большего |
количества |
металлического |
||||||||
железа, способного разрушить сульфид свинца. |
|
|
|
|
||||||
Увеличение расхода восстановителя сопровождается сниже |
||||||||||
нием потерь свинца в шлаке и увеличением степени |
возгонки |
|||||||||
цинка |
(табл. 31). |
|
|
|
|
|
|
|
|
|
|
|
|
|
|
|
|
Т а б л и ц а |
31 |
||
|
Влияние расхода восстановителя на потери свинца в шлаке |
|
|
|||||||
Содержание |
|
Расход восстановителя. % |
|
|
|
|
||||
|
|
|
|
|
|
|
|
|
||
серы в |
4 |
5 |
|
|
6 |
|
7 |
|
|
|
агломерате |
|
|
|
|
|
|
|
|
|
|
% |
потери |
| возгон |
потери возгон |
потери |
В О З Г О Н |
потери |
В О З Г О Н |
|||
|
||||||||||
3 |
8,7 |
— |
3,8 |
23,2 |
2,8 |
30,7 |
2,3 |
44,0 |
||
4 |
— |
10,2 |
9,6 |
4,8 |
18,7 |
2,3 |
42,3 |
Влияние содержания серы в агломерате
Серу оставляют в агломерате для перевода меди в штейн. Чем больше содержание серы, тем полнее извлечение меди в штейн и тем меньше ее переходит в черновой свинец. О харак тере этого влияния можно судить по данным, приведенным в та'бл. 32.