
1223
.pdfталла, что позволило ему избежать трудности конденсации. Спо соб, однако, оказался экономически неприемлемым.
Все перечисленные конструкции были ориентированы на пе реработку окисленных цинковых материалов.
Броун и Остерле [250] в это же время пытались провести процесс с сульфидным цинком по реакции
2ZnS + 2СаО + 7С = 2Zn + 2СаС2 + CS2 + 2СО;
2ZnS -f CaO + 4С = 2Zn + СаС2 + CS2 + СО.
Возгонка цинка протекала достаточно полно, однако в при сутствии серы получалось много пусьеры, карбид кальция был сильно загрязнен примесями и не мог быть использован. Про цесс был нерентабелен.
В1907 г. в Лионе было организовано промышленное произ водство окиси цинка, основанное на восстановлении цинка же лезом. Однако из-за примесей железа окись имела желтый от тенок.
Впоследующем перерабатывали сульфидные руды в смеси
сокисью кальция и углеродом:
ZnS + СаО + С - СО + CaS + Zn.
Получаемая окись была хорошего качества. В 1914 г. этим способом было получено и некоторое количество металлическо го цинка. В 1917 г. в Моренне была построена установка, на которой в 4 печах с коксовыми фильтрами мощностью по 370 кет перерабатывалось 16 тцинковой руды в сутки.
Мак-Джонсон в 1903 г. сконструировал печь в виде камеры, в торцы которой закладывались графитовые блоки, служившие для подвода тока. Между блоками засыпали кокс, используе мый как тело сопротивления. На кокс насыпали смесь обожжен
ной руды и кокса, |
при нагревании которой восстанавливался |
и возгонялся цинк. |
Печь была периодического действия, перед |
каждой операцией ее приходилось полностью вычищать и, есте ственно, она не нашла применения.
Джонсон сконструировал конденсатор в виде скруббера, оро шаемого цинком, движущимся в противотоке с парами. Этот ра циональный принцип был успешно реализован пятьдесят лет спустя. Джонсон установил полезность предварительного перед плавкой восстановления железа шихты, вытесняющего цинк из его окисленных и сульфидных соединений.
В дальнейшем Джонсон сконструировал печь непрерывного действия с электродами, погруженными в шлак, который отде лялся от свинца и штейна. Газы очищали от пыли в коксовом фильтре, обогреваемом током.
Здесь же происходила регенерация двуокиси углерода в окись. Однако сколько-нибудь успешных результатов на этой печи получено не было и в 1914 г. в Хартфорде (США, Коннек тикут) была построена печь без коксового фильтра. При плавке огарка, содержавшего 37% Zn, в сутки получали 250 кг Zn, при выходе его 78% и удельном расходе энергии 1645 квт-ч/т шихты.
Продолжая поиски Казаретти и Бертани, Джонсон приме нительно к смешанным рудам пытался осуществить двуступен чатый процесс с отгонкой цинка в многоподовой муфельной печи, установленной над электропечью, и последующей плавкой клин кера. Осуществить эту идею ему не удалось.
Имберт, Томсон и Фитцджеральд {252] предложили осуще ствить осадительную плавку при взаимодействии свинцово-цин ковых шихт с медью по реакциям
ZnS + 2Cu Z Cu2S + Zn
и
PbS + 2Cu^Cu2S + Pb-
Образующийся при этом штейн должен был подвергаться бессемерованию и регенерируемая медь возвращалась в про цесс.
Эти опыты ввиду явной нецелесообразности были прекра щены, и в качестве осадителя испытывали железо. Реакционной средой служили расплавы СаО — FeO и FeO — FeS.
Фултон впервые предложил использовать для электротер мии неплавящиеся брикеты [253, 254]. Смесь обожженной руды, коксовой мелочи и каменноугольной смолы в отношении 100: : 60 20 после коксования при 450—500° С нагревали в электро печи для отгона цинка.
Такой способ позволял экономить энергию, затрачиваемую на плавление, и исключить коррозию стен расплавом. Обесцинкованные брикеты плавили в шахтной печи для извлечения свинца, меди и драгоценных металлов. В 1916 г. в Ист-Сан-Луи была построена установка для суточной переработки около 2,5 т концентрата.
Брикеты диаметром 235 мм и высотой 530 мм укладывались по три штуки в реторту и служили телом сопротивления. Три реторты присоединяли к одному конденсатору, что обеспечива ло равномерный поток паров в нем и постоянную температуру. При среднем расходе энергии около 2200 квт-ч/г руды извле чение цинка в возгоны превышало 90%. Опыты дали положи тельные результаты и были прекращены в 1918 г. по ряду при чин нетехнического характера.
Натузиус [255] предложил конструкцию шахтной печи, верх няя часть которой служит для подогрева шихты, а в нижнюю.
футерованную доломитом или другим электропроводным в на гретом виде материалом, введены электроды.
Конструкция эта не была испытана автором, но отдельные ее элементы использованы в настоящее время.
Лаваль [257] был первым, кому удалось осуществить про мышленный электротермический процесс в металлургии цинка. Первая сконструированная им печь была дуговой. Тепло дуги излучалось на поверхность откоса шихты и жидкий шлак стекал на под.
Позднее Лаваль разработал конструкцию печи, ставшую прототипом современных печей. В этой печи расплавлялась вся шихта и электроды погружались в расплав. При плавке пресле довалась цель восстановления и отгонки цинка с одновремен ным выделением меди в штейн.
В 1898 г. была построена первая печь и в 1903 г. ее начали эксплуатировать. Несколько позднее были построены установки в Сорпсборге (Норвегия) и в Троллхеттане (Швеция). На заво де в Сорпсборге перерабатывался цинковый лом. В Троллхет тане перерабатывали цинковые руды, содержащие медь и сви нец. На этом заводе в 1909 г. работало несколько опытных пе чей мощностью 260 кет с одним подовым и одним верхним по груженным электродом. Построенные позднее печи мощностью 370 кет имели два погруженных электрода, из которых один был неподвижен, а другой двигался для регулирования мощ ности.
В конденсаторах получали смесь жидкого цинка и пусьеры. которые в горячем состоянии интенсивно перемешивали в котле. При этом часть пусьеры превращали в цинк, а часть окислялась и улетучивалась в виде окиси цинка. Оставшуюся пусьеру воз вращали в процесс. В дальнейшем пусьеру перерабатывали в
короткобарабанной печи диаметром 2,5 м |
и длиной 1,5 м. |
В жидкий цинк переходило до 65% металла. |
При ликвации |
получали свинец, содержащий 2—3% Zn, и гартцинк с 90% Zn, 5% Fe и 5% Pb. Полученный при этом цинк отвечал марке «Прайм Вестерн». Для получения более чистого цинка была построена дуговая редистилляционная одноступенчатая печь размером 3x2,5 м с глубиной ванны около 1 м. Цинковые пары, содержащие 99,8% Zn, конденсировались на охлаждаемых воз духом трубах и металл выпускался через летку. Таким способом очищали весь цинк, полученный во вращающихся печах.
В 1913 г. заводы в Троллхеттане и Сорпсборге произвели
17 тыс. т цинка.
В описанном виде процес применялся до 1925 г., после чего он был усовершенствован. Была установлена круглая агломе рационная машина. Агломерат не пылил и плавился постепенно, что улучшило условия работы конденсатора. Вместо нескольких
8 М. М. Лакерннк
маленьких печей была |
сооружена печь мощностью 4500 ква |
с тремя погруженными |
в шлак регулируемыми электродами. |
Печь была тщательно закрыта. Шлак и штейн выпускали* через общий шпур. Шлак содержал 45—55% кремнезема, 25—30% окиси кальция, магния и бария, 10—15% закиси железа и оки си марганца и 5—15% глинозема. При этом шлак содержал ме~ нее 1% Zn и образовывался ферросилиций.
Рис. 51. Усовершенствованная печь Лаваля
Конденсатор был рассчитан на осаждение цинка в виде пыли. Он был разделен на 3 камеры высотой 7,5 ж, шириной 2,5 м и длиной 0,5 м каждая. Камеры были стальные со шнеком для разгрузки пыли и принудительным охлаждением водой. Печь ра ботала под небольшим давлением и имела вспомогательное защитное устройство для подачи азота и двуокиси углерода для предотвращения взрывов при подсосах воздуха (рис. 51).
Несмотря на перечисленные усовершенствования, расход энергии был высок, производительность не превышала 7 трафи нированного цинка в сутки и в период кризиса в 30-х годах за вод был закрыт.
Он был пущен во время второй мировой войны, чтобы обес печить потребности Швеции в цинке. Перерабатывались концен траты, содержавшие 52% Zn, 32%S, 8% Fe и 2,5% Pb, разные материалы, оставшиеся от прошлой кампании печи, а также вторичное сырье.
После окончания войны производство было прекращено, так как процесс был нерентабелен. Причин нерентабельности было много: низкая производительность завода, ограниченная отсут-
ствием агрегатов для предварительного обжига концентратов; большие тепловые потери печи, на которой при внешней поверх
ности 115 м2 |
терялось 460 |
кет |
при потребляемой |
мощности |
2000 /сет, что |
соответствует |
23%. |
При увеличении |
мощности |
вдвое во столько же раз уменьшились бы потери. Получаемые в печи газы с высокой теплотворной способностью не использо вались для подогрева шихты, что могло заметно уменьшить рас ход энергии; конденсатор примитивной конструкции не позво лял получать цинк в жидком виде и количество оборотных ма териалов было велико.
Анализ истории развития электротермии цинка показывает, что на протяжении полувека предпринимались попытки осуще ствить этот процесс. Эти попытки не увенчались успехом, но они не прошли даром и ряд рациональных идей, предложенных ра нее, но не нашедших в то время правильного инженерного ре шения, воплощен в практику в настоящее время.
Токопроводящая шихта братьев Коулс, брикеты Фултона, кольцевой канал для цинковых паров Натузиуса, печь Лаваля с погруженными в шлак электродами и конденсатор с орошени ем цинком Мак-Джонсона в новом инженерном решении на но вой технической основе нашли свое место в современной элек тротермии цинка — процессе, в котором по-новому решена про блема получения этого металла.
Глава IV
ЭЛЕКТРОПЛАВКА МЕДНЫХ КОНЦЕНТРАТОВ
Главным источником производства меди являются сульфид ные .руды, в которых преобладающими медьсодержащими мине ралами являются халькопирит, борнит, ковеллин, халькозин и др.
Основная доля мирового производства меди основывается на месторождениях медистых песчаников и медно-порфировых руд. Колчеданные руды занимают третье место.
В настоящее время прямая переработка кусковых руд в шахтных печах — пиритная и полупиритная плавка, потеряли былое значение. На некоторых предприятиях, располагающих прочной кусковой пиритной рудой, свободной от цинка, с высо ким содержанием серы, применяют медно-серную плавку — процесс, позволяющий одновременно с выплавкой штейна поду чать элементарную серу. Такой процесс осуществляется, напри мер, в Медногорске (СССР), Тамсхавене (Норвегия), Эргани Маден (Турция), Рио Тинто (Испания), Сан Доминго (Порту галия). Но этот способ также имеет подчиненное значение в производстве меди.
После освоения в первой четверти нынешнего века процесса флотационного обогащения руд плавка флотационных концент ратов в отражательных печах стала основным способом произ водства меди.
В зависимости от состава руды, крупности содержащихся в ней минералов, степени прорастания рудных минералов между собой и с пустой породой концентраты имеют различный состав (табл. 20).
Чтобы из концентрата, содержащего 20% или менее меди, получить штейн с содержанием 35—40% Си, часть серы должна быть удалена из него предварительным обжигом и в огарке должно остаться столько серы, сколько ее необходимо для По лучения штейна желаемого состава. При обжиге FeS превраща ется в Fe20 3 или Рез04, которые в последующем необходимо пре вратить в FeO для образования фаялитового шлака.
Обжиг обычно производят в многоподовых печах, хотя в
Т а б л и ц а 20
Состав медных концентратов
Исходная руда |
Содержание в концентрате. % |
|
||
|
|
|
|
|
Си |
Zn |
S |
Fe |
Si02 |
Медистые колчеданы |
8—20 |
1—2 |
35 -43 |
32—37 |
3 - 5 |
Медно-цинковая |
8—15 |
2—4 |
30—35 |
25—30 |
3—5 |
Вкрапленники |
20—25 |
— |
30 |
25—27 |
5—10 |
Порфировая |
28—35 |
— |
15—20 |
16—20 |
20—29 |
настоящее время для этой цели начинают применять и процесс в кипящем слое.
Огарок выходит из обжиговой печи -при температуре 500— 600° С и в горячем виде загружается в отражательную печь. При добавке флюсов, жидкого конвертерного шлака и внутрен них оборотных материалов завода в процессе плавки образуется штейн необходимого состава.
Такой процесс проводится в две стадии и требует примене ния обжиговой аппаратуры и связанных с ней устройств для пылеулавливания.
Концентраты, содержащие 25—30% Си, можно плавить с получением штейна, содержащего до 45% Си без предваритель ного обжига.
Плавка обожженного концентрата имеет следующие преиму щества:
1. Меньший расход топлива, не превышающий 150 кг/т ших ты, а при использовании подогретого дутья — 120 кг/т шихты (соответственно 0,8—.1,1 X Ю6 ккал/т шихты или после вычета тепла пара, полученного в котлах-утилизаторах, около 0,6 X X Ю6 ккал/т).
2.Больший удельный проплав, достигающий 3—5 т/м2 пло щади печи в сутки (на отечественных заводах 6—8 т/м2).
3.Возможность изменять в широких пределах содержание
меди в штейне.
4. Малое содержание серы в газах отражательной печи и возможность использования серы, переходящей в обжиговые газы.
5.Спокойный ход печи.
Кнедостаткам процесса следует отнести наличие двух ра
бочих процессов (обжига и плавки), большой объем аппара туры для пылеулавливания и увеличенные отложения магнети
та на поду отражательной печи.
Плавка необожженного концентрата имеет следующие пре имущества: один рабочий процесс (отсутствует обжиг) и соот-
ветственио более простая аппаратурная схема и уменьшенное ферритообразование.
Кчислу недостатков процесса следует отнести:
1.Больший расход топлива, достигающий 200—240 кг/i
шихты, что отвечает 1,5—1,8 X Ю6 ккал/т шихты или, за выче том тепла пара из котлов-утилизаторов, около 0,8 X Ю6 ккал/т.
2.Меньший удельный проплав, составляющий 3—4 т/м2 площади печи в сутки.
3.Содержание меди в штейне не регулируется и практиче ски примерно в 1,25—1,3 раза больше содержания меди в кон
центрате.
4.Печные газы содержат много серы [2—4% (объемн.)], использование и обезвреживание которой более сложно, чем га зов обжиговых печей.
5.Неспокойный ход печи при загрузке сырой шихты.
6.Увеличение объема конвертерного передела.
Главнейшие реакции, протекающие при отражательной
плавке огарка, следующие: |
|
2FeS + 6Fe20 3 + 7Si02 = |
7 (2FeO • Si02) + 2S02; |
FeS + Cu20 = Cu2S + FeO; |
|
FeS ~F 10Fe2O3 = |
7Fe30 4 -f- S02; |
FeS -f- 3Fe30 4 = |
lOFeO S02; |
2FeO • Si02 + CaO • Si02 + другие силикаты = шлак; n Cu2S + m FeS -f- другие сульфиды = штейн.
Химизм электроплавки аналогичен химизму отражательной плавки.
1.ПЛАВКА ЖЕЛЕЗИСТЫХ МЕДНЫХ КОНЦЕНТРАТОВ
Внастоящее время наиболее крупное «предприятие, перера батывающее медные концентраты электротермическим мето дом,— завод Роншер в Швеции.
Завод расположен на севере страны вблизи города Шелефтео на полуострове в Ботническом заливе.
Медное производство завода .включает обжиг и сушку кон центратов, электроплавку их на штейн, бессемерование штейна, огневое и электролитическое рафинирование меди и электро плавку катодной меди на вайербарсы. Общая схема завода при ведена на рис. 52.
До 1946 г. на заводе применяли отражательную плавку. Данные о заводе опубликованы Гернеридом [258], кроме то
го, автор ознакомился с работой завода, посетив его в 1956 г.
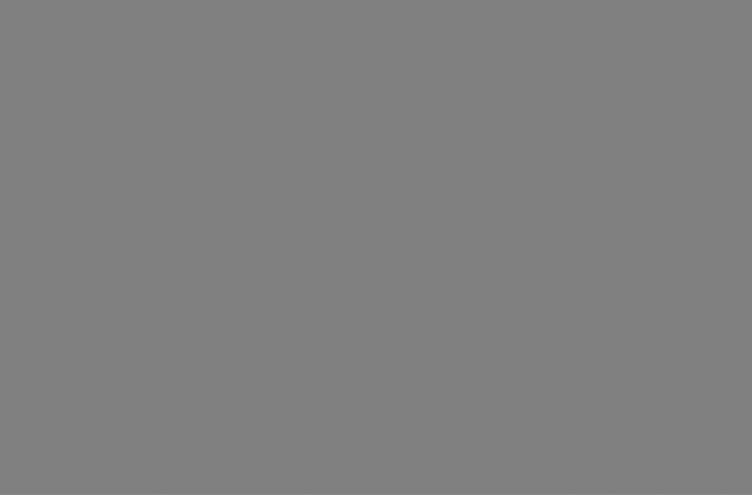
[259], сведения о нем сообщены также К. М. Симаковым [260], побывавшим на заводе в 1958 г.
Концентрат доставляется в Роншер в специальных бункерахвагонах с донной разгрузкой. Для оттаивания концентратов, иногда смерзающихся в зимнее время, служит тепляк, отапли ваемый горячим воздухом с принудительной циркуляцией.
Концентрат |
разгружают в бункеры, откуда |
транспортером |
|||
и элеватором |
подают |
в |
шихтарник. В шихтовом |
отделении |
|
имеются линии подвесных |
параболической формы |
бункеров |
|||
емкостью 4500 |
т'каждый. Концентраты и флюсы |
закладывают |
|||
слоями с последующим |
выпуском усредненной шихты на тран |
||||
спортеры, расположенные под каждой линией бункеров. |
Обжиг производят в четырех двенадцатиподовых печах диа метром 6 мЛотапливаемых мазутом.
Концентраты сортируют по содержанию мышьяка.
|
Си |
As |
S |
Медный концентрат А |
25—27 |
0,5—2 |
30 |
Медный концентрат Б |
25—27 |
2—6 |
30 |
Мышьяковый концентрат |
1 |
10—12 |
20—25 |
Концентраты группы А только сушат до содержания 2—3% |
|||
влаги. Концентраты группы Б обжигают в |
многоподовой печи |
||
В отдельной печи обжигают |
мышьяковый |
концентрат в смеси |
|
с пылью, полученной п.ри обжиге медного |
концентрата с воз |
гонкой мышьяка в виде трехокиси. Производительность обжиго вых печей 150—200 г/сутки.
В огарке от обжига медного концентрата остается 14% S и 0,36% As. После обжига мышьякового 'концентрата в огарке
остается 13,9% S и 1,37% As. Газы |
направляются |
на |
серно |
|||
кислотное производство, |
а пыль |
электрофильтров— на |
произ |
|||
водство металлического и белого |
мышьяка и других мышьяко |
|||||
вых продуктов. |
пыль |
содержит, |
%: 0,4 Си, 0,01 |
Ni, |
0,1 Pb, |
|
Мышьяковая |
||||||
0,07 Bi, 0,4 Sb, 0,18 Si, 81—90 As20 3. |
|
|
||||
Обожженный |
медный концентрат выпускают из печи в бун |
кер емкостью 5 г. К бункеру троллейный погрузчик с вилочным захватом подвозит контейнер емкостью 4,5 т. При установке контейнера под бункером крышка контейнера специальным уст ройством открывается и телескопическая горловина бункера погружается в контейнер. Перед этим останавливают вал печи. Содержимое бункера пересыпается в контейнер. Таким обра зом, бункер одновременно является дозатором. После заполне ния контейнера все действия повторяются в обратном порядке. Вся операция хорошо механизирована и не сопровождается выделением газа и пыли. Один из трех подъемников поднимает на колошниковую площадку контейнеры с огарком и подсушен