
1223
.pdfСитовой анализ шихты следующий, %:
8,5—19 мм |
Кокс |
Агломерат |
76 |
56 |
|
6,4—8,5 мм |
19 |
39 |
6,5 мм |
5 |
5 |
При загрузке кокс крупнее агломерата. По мере прохожде
ния через печь куски кокса уменьшаются. |
Количество кокса в |
|
шихте превышает теоретическую потребность в три раза |
(что |
|
соответствует весовому отношению агломерата к коксу 43 |
19), |
|
и поэтому при прохождении шихты через |
печь электропровод |
ность ее изменяется незначительно. Некоторое увеличение элек тросопротивления в нижней части печи сопровождается неболь шим повышением температуры в этой области, чю способствует более полной отгонке цинка из шихты.
Печь обычно состоит из семи секций, опирающихся на са мостоятельные кольцевые опоры. Нижняя секция установлена на водоохлаждаемом ободе. Все части печи предохранены от ко роткого замыкания. Секции шахты печи могут быть отремонти рованы или заменены независимо от других. Стены шахты вы ложены плотным кирпичом размером 330X75 мм. В наиболее ответственных частях, например в своде над газоотводным коль цом, шахта футерована карборундовым кирпичом, а под коль цом — кирпичом из литого муллита.
Внизу печи установлен футерованный разгрузочный стол с регулируемым числом оборотов. Раймовка из печи попадает в фартук стола и отсюда специальным скребком подается в ков шевой транспортер. Перемещая стол в вертикальном направле нии, можно изменять величину щели между водоохлаждаемым ободом и столом и этим регулировать скорость выгрузки клин кера.
Вверху печи на высоте одной трети расстояния между верх ним и нижним электродами сечение печи увеличивается. Шихта, спускаясь вниз, распределяется по большей площади, создавая большую поверхность испарения. Над расширенным сечением печи расположено двухарочное кольцо со щелью внизу. Пары цинка и окись углерода при температуре 875° С поступают в это кольцо, а затем, пройдя газоход, — в конденсатор.
Для предотвращения спекания шихта в печи должна быть 8 непрерывном движении. По мере отгонки цинка точка плавле ния шихты понижается и возможность ее спекания в нижней ча сти печи возрастает. При неравномерном сходе столба шихты
иобразовании ■перемычек ток неравномерно распределяется по сечению печи, что приводит к частичному расплавлению шихты
инарушению процесса. Если такие спеки образуются, их раз^-
рушают «бомбой» — дюймовой водопроводной трубой длиной
около 300 мм, заполненной водой и заваренной с обоих торцов. «Бомбу» вводят в горячую зону, взрыв ее разрушает перемычку.
Столб шихты в печи опирается на медленно вращающуюся тарель, с которой убирают остатки дистилляции. Частицы, бед ные цинком, более легкоплавки и легче спекаются. Поэтому крупные частицы содержат меньше цинка. После охлаждения все частицы крупнее 19 мм отделяют и направляют в отвал. От сеянный мелкий остаток подвергают магнитной сепарации, при которой отделяется восстановленное железо. Магнитная часть направляется в отвал, а немагнитная, состоящая из кокса и не полностью восстановленного агломерата, разделяется дополни тельно на воздушном сепараторе. Крупный кокс (крупнее 6,4 мм)
направляют в печь, а мелочь кокса и агломерата |
(после допол |
нительного измельчения до —0,84 мм) — в шихту |
агломерации. |
Успешное осуществление процесса определяется в первую очередь правильным подбором шихты с точки зрения физиче
ских ее свойств, главным образом — постоянством |
и |
необходи |
мой величиной электрического сопротивления. |
Эти |
условия |
создаются правильным подбором расхода кокса и его крупно сти. Слишком большое количество кокса приводит к местным перегревам и снижает производительность реторты.
При описываемом способе прохождения тока по централь ному стержню температура от центра реторты к ее периферии снижается и цинк из периферийных областей отгоняется с мень шей эффективностью. Однако это необходимо для устойчивого прохождения тока и для сохранения футеровки. Даже и при этих условиях срок ее службы невелик и в печах, служащих для про изводства металла, не превышает 100 суток, а в печах, служа
щих для производства окиси цинка, 240—300 суток. |
1 т |
|
Приведенный ниже анализ потребления рабочей силы на |
||
цинка свидетельствует о большом удельном |
весе ремонтных |
|
работ. |
|
про |
Потребление рабочей силы для электротермического |
||
цесса в шахтных электропечах, чел-час!т: |
|
|
Транспорт и обжиг |
1,93 |
|
Сернокислотное производство |
0,40 |
|
Агломерация |
0,90 |
|
Выщелачивание пылей |
0,51 |
|
Дистилляция и конденсация |
4,52 |
|
На обработку окиси цинка |
МО |
|
Слесари |
3,08 |
|
Электрики |
0,54 |
|
Каменщики |
0,60 |
|
Строительные рабочие |
0,12 |
|
Подсобные рабочие |
0,44 |
|
Управленческий аппарат и прочие |
1,60 |
|
Вс е г о |
15.74 |
О характере баланса цинка в описываемом процессе можно судить по данным табл. 37.
|
Баланс цинка на заводе Джазефтаун |
Т аб л и ц а |
37 |
|||||
|
|
|
|
|
||||
Поступающее сырье |
|
|
Получаемые продукты |
|
|
|||
материал |
коли- |
% |
т |
продукт |
коли |
% |
|
т |
чество |
чество |
|
||||||
Обжиг |
|
|
|
|
|
|
|
|
Концентрат |
1955 |
55,0 |
1075 |
Огарок |
1691 |
65 |
|
1099 |
Сульфат цинка |
|
|
81 |
Пыль |
115 |
|
|
47 |
Спекание |
|
|
1156 |
|
|
|
• |
1146 |
|
|
|
|
|
|
|
||
Огарок |
1691 |
65 |
1099 |
Готовый агломерат |
1867 |
60 |
|
1120 |
Отходы мелкие |
151 |
24,5 |
37 |
Мелкий оборотный |
|
|
|
|
Отходы богатые |
52 |
15,4 |
8 |
агломерат |
4992 |
60 |
|
2635 |
Мелкий оборотный |
4992 |
60 |
2635 |
Пыль |
|
|
|
24 |
агломерат |
|
|
|
|
|
|||
Кварц |
80 |
— |
— |
|
|
|
|
|
Кокс |
270 |
— |
— |
|
|
|
|
|
Дистилляция |
|
|
3779 |
|
|
|
|
3779 |
|
|
|
|
|
|
|
|
|
Агломерат |
1867 |
60 |
1120 |
Чушковый цинк |
1000 |
100 |
|
1000 |
Оборотный агломе |
86 |
28 |
24 |
Цинковая пыль |
78 |
90 |
|
70 |
рат |
Отходы: |
687 |
11,6 |
|
80 |
|||
Оборотный кокс |
687 |
11,6 |
80 |
кокс |
|
|||
Свежий кокс |
580 |
— |
— |
агломерат |
86 |
28 |
|
24 |
Цинковая пыль |
78 |
90 |
70 |
мелкие |
151 |
24,5 |
|
37 |
|
|
|
|
богатые |
52 |
15,4 |
|
8 |
|
|
|
|
бедные |
168 |
10,7 |
|
18 |
|
|
|
|
крупные |
389 |
12,6 |
|
49* |
|
|
|
|
Прочие потери |
|
|
|
8 |
|
|
| |
1294 |
|
|
1 |
| |
1294 |
* Общие потери 75 т .
Общие технические показатели процесса работы шахтных электропечей характеризуются приведенными данными:
Расход шихты, пг/сутки Производительность Zn, т/сутки
Содержание Zn в шихте, % Прямой выход цинка, %
Расход энергии на 1 т Zn, квт-ч Содержание Zn в остатке, % Расход электродов, кг/т
Кампания печи, сутки |
• • |
Производительность цеха, |
т Zn/сутки |
Большие |
Малые |
печи |
печи |
89 |
48 |
45 |
18 |
42,8 |
41,5 |
85,3 |
77,5 |
2530 |
2890 |
14,6 |
15,3 |
2,33 До 100 363
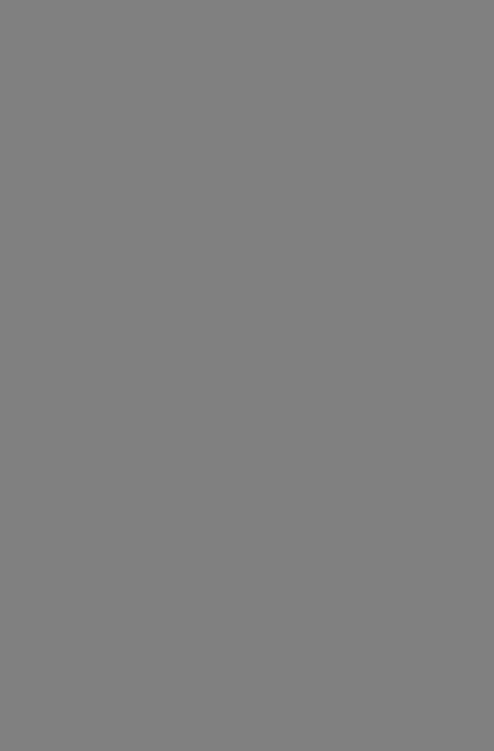
Степень конденсации цинка в жидкий металл достигает 92— 94%, что является, безусловно, хорошим показателем. Покидаю щие конденсатор газы, содержащие более 80% СО, 1,5% С02, 1,5% 0 2, 15% N2, очищаются в скруббере и вакуумным насо сом подаются на компремирующую установку и далее различ ным потребителям.
Низкая теплопроводность стенки и недостаточная циркуля ция цинка в конденсаторе лимитировали теплопередачу и огра ничивали производительность дистилляционной печи.
Печь диаметром 2400 мм потребляла 3000 ква при конденса торе с поверхностью теплообмена около 23 м2. При увеличении мощности печи на ней можно было получить 30 тцинка в сутки, но конденсатор не обеспечивал такой производительности. Это определило поиски более совершенной конструкции конденса тора.
В небольших горизонтальных ретортах количество возгоняе мого и конденсируемого цинка было невелико и проблема отво да тепла конденсации решалась весьма просто. Тепло рассеи валось с относительно большой поверхности конденсатора. Рас ход угля примерно втрое превышал теоретическую потребность, и этот огромный избыток углерода в шихте, находящейся в ре торте при температуре 1200—1300° С, обеспечивал необходимое отношение СО к С02 и удовлетворительные условия конденса ции. Периодичность процесса приводила, однако, к тому, что в первой его стадии, пока устанавливался необходимый тепловой режим конденсатора, и в последней — когда в шихте оставалось мало цинка, выход жидкого металла был меньше и среднее из влечение было ниже, чем за лучший, средний период.
С появлением вертикальных реторт непрерывного действия условия конденсации улучшились, так как в реторту поступал постоянный по величине и температуре поток паров и газов. Количество кокса в шихте лимитировалось только экономиче скими соображениями и в составе брикетов его было столько же, сколько в шихте горизонтальных реторт. Поэтому и состав парогазовой смеси был вполне удовлетворительным для после дующей конденсации. Так как производительность вертикальных реторт не превышала 8—9 т цинка в сутки, то проблема отвода тепла при конденсации решалась с помощью дополнительных карборундовых перегородок, устанавливаемых в конденсаторе (рис. 66) и служащих дополнительными поверхностями охлаж
дения.
Освоение шахтных электропечей определило ряд новых тре
бований к конденсаторам.
Производительность этих печей была много выше, чем вер тикальных реторт, и отвести в атмосферу выделяющееся при конденсации цинка тепло через стены конденсатора, выложен
ного из нетеплопроводного материала, не представлялось воз можным.
Кроме того, если для горизонтальных и вертикальных реторт можно было составлять шихту с достаточно высоким расходом кокса и при тесном его контакте с рудной частью шихты, в шахтной электропечи количество вводимого в шихту кокса ре гламентировалось не только экономическими соображениями
Рис. 66. Камерный конденсатор с перегородками:
1 — выход газов; 2 — карборундовые перегородки; 3 — летка; |
4 |
— вход |
|
газов |
и паров |
|
|
(расход угля, использование |
объема реторты), но |
и |
техниче |
скими условиями, отвечающими оптимальной электропроводно сти шихты. При этом количество кокса в шихте было меньше, чем при предшествующих процессах, и контакт его с агломера том хуже. Это, естественно, приводило к повышению содержа ния С02, и ухудшение состава газовой смеси можно было ком пенсировать только повышением ее температуры. Если темпера
тура |
газов, покидающих вертикальную реторту, |
составляет |
900° |
С, то для электрообогреваемой шахтной печи |
она равна |
1000° С. Для обеспечения этой температуры парогазовую смесь отводят из средней трети высоты шахты — из области, находя щейся в сфере обогрева током, ниже верхних электродов печи.
Таким образом, в конденсаторе необходимо отводить тепло не только от большего количества конденсируемого цинка, но и от более горячих газов. А чтобы не удлинить период охлаж дения газов и максимально исключить процесс обратного окис ления цинковых паров, необходимо производить охлаждение до статочно быстро — закалить парогазовую смесь.
Естественно, что в экстенсивно охлаждаемом камерном кон-
денсатере эти задачи выполнить невозможно. Витон и Наджарьян предложили барботажный конденсатор.
Принцип действия такого конденсатора был изложен выше. Тепло, выделяемое при конденсации цинка (555 ккал!т Zn), по глощается расплавленным цинком и выделяется через орошае мые водой стенки.
Первоначально в эксплуатации было 5 шахтных электропе
чей диаметром 1725 мм и одна диаметром |
2400 мм. |
Каждая |
||||||
малая печь имела |
конденсатор |
длиной |
6710 мм и |
большая |
||||
9450 мм. Конденсаторы |
были круглого |
сечения, диаметром в |
||||||
свету 813 мм с кожухом из рифленой стали |
толщиной |
16 мм |
||||||
и карборундовой |
футеровкой толщиной |
51 мм. |
Теплопровод |
|||||
ность стен составляла 30—40 ккал/м2-час-°С. |
|
|
|
|||||
Кожух снаружи охлаждался водой и при хороших условиях |
||||||||
в малых конденсаторах получали |
12 г, а в больших 22 т цинка |
|||||||
в сутки при температуре |
его в |
конденсаторе, |
равной |
500— |
||||
525° С. |
|
|
|
|
|
|
|
|
Попытки повысить производительность печи сопровождались повышением температуры в конденсаторах и увеличением коли чества дроссов.
Было очевидно, что низкая теплопроводность стен и недо статочная циркуляция цинка в конденсаторе лимитировали теп лопередачу и ограничивали производительность дистилляционной печи.
Шахтная печь диаметром 2400 мм потребляла 3000 ква при конденсаторе с поверхностью теплообмена около 23,2 м2. При увеличении мощности печи на ней можно было получить 30 г цинка в сутки, однако конденсатор не обеспечивал такой произ
водительности.
Изучался вопрос об удлинении конденсатора для увеличения охлаждаемой поверхности при сохранении наиболее .эффектив ного угла его наклона более 20° С. (Опыт показал, что при угле наклона 15° и менее образуются настыли и снижается теплооб мен.) Однако длинный конденсатор оказался непрочным и с пло
хим теплообменом.
Под конденсатором была установлена вторая труба — холо дильник, такого же диаметра и под таким же углом, что и ос новная (рис. 67). В первое время после пуска холодильник ра ботал весьма эффективно, однако через несколько дней он зара стал настылью и через 10 дней переставал работать. Через 15 су ток после пуска конденсатор полностью прекращал работу [327].
В дальнейшем исследовался двойной конденсатор |
с двумя |
уравнительными трубами (рис. 68). Этот конденсатор |
успешно |
работал несколько кампаний на одной из малых печей, |
однако |
оказалось невозможным удержать одинаковый газовый режим в обоих трубах, в результате чего в одной из труб образовыва-
12 М- М. Лакерник
Рис. 67. Вакуумный конденсатор с трубой-холодильником
Рис. 68. Двойной вакуум-конденсатор
Л1ись настыли и она зарастала. Ремонты конденсатора оказа лись очень сложными и заметно поднять производительность они не позволили.
В Аргентине, на заводе Комодоро Ривадавия, двойные кон денсаторы работали несколько лет и впоследствии были заме нены.
Была испытана конструкция конденсатора треугольной фор мы. При этом исходили из необходимости увеличить поверх ность наиболее нагреваемой верхней части и тем самым повы сить теплоотъем. Эта конструкция удачна и применялась до вольно широко, обеспечивая получение до 30 т цинка в сутки. Печи диаметром 2400 мм были оборудованы конденсаторами такой формы при длине 8,5 м. Столь большая длина приводила, к сожалению, к частым авариям кожуха и футеровки.
Была испытана еще одна весьма эффективная конструкция конденсаторов (рис. 69). В конденсаторе устанавливали две пе регородки, погруженные в жидкий цинк. Одна находилась вбли зи ввода газов, другая — посередине конденсатора. Эти перего родки имели два больших отверстия — в верхней части и у дни
ща. Перегородки выполняли две функции: |
обеспечивали спо~ |
|
койную поверхность расплавленного цинка |
и |
способствовали |
выравниванию температуры в конденсаторе |
за |
счет создания |
циркуляции цинка в конденсаторе вверх — вдоль свода и вниз — вдоль .его подины.
Парогазовая смесь, пробулькивающая вверх, создает «аэро лифт», вызывающий направленную вниз циркуляцию металла вдоль дна.
Отверстие в верхней перегородке было закрыто и она пре вратилась в плотину. Вдоль конденсатора расположен овальной формы открытый холодильник, имеющий стальной кожух и кар борундовую футеровку. Два патрубка диаметром 200 мм соеди няют холодильник с конденсатором. Первый патрубок соединя ет холодильник с конденсатором в точке около плотины, а вто рой — в нижнем конце, под местом входа газов в конденсатор.
Циркуляция, создаваемая «аэролифтом», обеспечивает ох лаждение металла в холодильнике, в который погружены змее вики.
Циркуляция зависит от количества паров и газов и при про изводительности около 2,5 тцинка в час составляет 0,9 тметал ла в час. Температура в конденсаторе поддерживается в преде лах 485—510° С и коэффициент конденсации достигает 97— 98% от теоретически возможного. Благодаря интенсивной цир
куляции перепад температур |
в системе |
конденсатор — холо |
|
дильник не превышает |
15° С. |
|
|
Описанная система |
охлаждения конденсаторов позволила |
||
строить их более короткими и |
прочными |
с большим углом на- |
12*
клона и с меньшими возможностями для зарастания насты лями.
По мере освоения этих конденсаторов и интенсификации ра боты холодильников мощность шахтных электропечей система-
г
Рис. 69. Вакуумный конденсатор с внешним циркуляци онным холодильником:
1 — конденсатор; 2 — |
внешний холодильник; 3 — змеевики; |
4 |
— перегородки |
тически повышалась с 3 до 4,2 тыс. ква с получением 44,5 тцин ка в сутки, до 4,8 тыс. ква с получением 50,7 т цинка в сутки, до 5,5 тыс. ква с получением 53,3 т цинка в сутки и, наконец, до
5,7 |
тыс. ква с получением 55,6 т цинка в сутки. |
|
|
Простои для ремонтов были снижены до 2% рабочего вре |
|
мени и расход энергии составил 2608,6 квт-н на 1 |
т цинка. |
|
ка, |
Последний испытанный конденсатор имел емкость 40 т цин |
|
циркуляция равнялась 15 г цинка в минуту |
и конденсиро |