
1044
.pdfсиловыми граничными условиями
Z (H+0= T , |
(6.55) |
В приведенных выражениях использованы обозначения: N - число пролетов; t - расстояние в плоскости поперечного сечения от частицы материала до плоскости, проходящей через центр тяжести сечения перпендикулярно плоскости изгиба и плоскости поперечного сечения; Т - усилие натяжения проволоки; и(,\ е т - смещение и деформация линии центров
тяжести i-го пролета; к(,) - кривизна линии центров тяжести i-го пролета,
Таким образом, для определения изогнутой линии центров тяжести необходимо решить совместную систему уравнений (6.50) - (6.55), при этом дифференциальное уравнение изгиба (6.51) с помощью метода конечных разностей заменяется системой алгебраических уравнений относительно значений функций прогибов во всех внутренних точках j-1,j, j+1, j+2 по длине пролета:
= (z(i)cosa(i)- Y (i)sina(i))Au(i)+ AeTjE lltdF, j = 2,M i-2; i = l,N,
F
где Mj - число узловых точек в i-м пролете.
Аппроксимация граничного условия (6.53) имеет вид
u0) _ u(0 |
1 |
( |
UMi U Mi-l _ |
|
i = l,N -l. |
ДСw |
l-tg y (,) |
|
|
|
Для определения напряженно-деформированного состояния частиц материала проволоки используется совместный эйлерово-лагранжев подход. Согласно принятым гипотезам движение материальных частиц происходит по траекториям, совпадающим с линиями тока. Зная положение конкретной частицы t, зависимость кривизны к(£) и деформации Бт(0 проволоки от продольной координаты согласно равенству (6.49) можно подсчитать деформацию £, а значит, с использованием равенства (6.48) и напряжение <т этой частицы, прослеживая ее движение вдоль траектории. Это позволяет
исследовать историю нагружения всех материальных частиц, определить величины с*9 Ея(е*).
Связанность двух указанных задач заключается в том, что для решения задачи изгиба требуется знание Ех(ер) по всему объему проволоки, а для исследования напряженно-деформированного состояния необходимо знать изменение кривизны к(£) проволоки по длине. Для решения связанной задачи используется итерационная процедура. На первой итерации предполагается, что материал проволоки идеально упругий, Ех полагается равным модулю упругости Е. Решением системы уравнений (6.50)-(6.55) определяются реакции связей Yj, Zi, Mj на концах пролетов, прогибы и кривизны линии центров тяжести по длине пролетов. Сечение проволоки представляется совокупностью конечного числа элементарных ячеек, в пределах каждой ячейки напряженно - деформированное состояние материала предполагается однородным. Перемещаясь вместе с каждой такой ячейкой вдоль ее траектории, прослеживаем историю деформирования, определяем Е х(е*) и уточняем e-KQ
согласно выражению (6.52). Далее, зная величину хордового модуля в каждой точке проволоки, можно подсчитать коэффициенты в дифференциальном уравнении изгиба (6.51). Затем вновь решить систему уравнений (6.50) - (6.55), определить реакции связей, кривизну проволоки и так далее до тех пор, пока
для двух последовательных итераций п и п+1 выполняется условие |
|
п^ 1 р”(0-Р"*'(С ]|>8. |
(656) |
где 5 - |
заданная величина погрешности; О - объем, занимаемый проволокой; |
p(Q - |
вектор состояния материала в какой-либо точке проволоки, |
Р(0= {о, е, tcfeX u(0}-
Для оценки сходимости итерационной процедуры проведен вычислительный эксперимент. За основу взята задача о правке на трехроликовой правильной машине бруса прямоугольного поперечного сечения из идеально упругопластического материала, аналитическое решение которой известно [21]. При выполнении расчетов принято, что высота бруса 0,05 м, ширина 0,03 м, предел текучести 200 МПа, модуль упругости 200 ГПа, длина роликовой машины 1 м, смещение центрального ролика -0,01 м, начальная кривизна бруса отсутствует.
Сходимость решения исследовалась на последовательности разностных сеток, состоящих из 5, 10, 15, ..., 40 узлов на каждом пролете, а также последовательности сеток из 8, 16, 32, 64, 128, 256 и 512 конечных элементов, аппроксимирующих область, занятую поперечным сечением профиля.
На рис. 6.20 приведены результаты вычислительного эксперимента. Видно, что усилие на центральной опоре практически во всех случаях близко к точному значению (14550 Н), наибольшая погрешность не превышает 7 %. Наибольшая
кривизна бруса (0,133 и '\ достигается на центральной опоре) более
чувствительна к числу узлов конечно-разностной сетки, нежели по отношению к числу конечных элементов в плоскости поперечного сечения, что, повидимому, связано с малой точностью аппроксимации вторых производных функции прогибов при малом числе узлов.
Число конечных элементов определяет точность подсчета коэффициентов дифференциального уравнения (6.51) упругопластического изгиба. Как показывают расчеты, влияние аппроксимации поперечного сечения конечными элементами сказывается лишь до определенного их числа. В рассматриваемом примере с брусом оказалось достаточно лишь 32 треугольных элементов; дальнейшее увеличение их числа практически не влияет на получаемые результаты. Следует отметить, что сходимость итерационной процедуры разработанного алгоритма имеет немонотонный характер (рис. 6.21).
Изложенный подход позволяет исследовать процесс знакопеременного изгиба профиля любого сечения независимо от вида упрочнения материала, дает возможность проследить историю деформирования материальных частиц от начала до конца процесса. Напряженно-деформированное состояние всех точек сечения проволоки в момент окончания знакопеременного изгиба и снятия растягивающего усилия представляет собой не что иное, как остаточные напряжение и деформацию в готовой проволоке. Решение задачи в такой постановке дает информацию об изгибающих моментах и усилиях на роликах, остаточной кривизне и о вытяжке проволоки.
Для оценки эффективности использования в промышленных условиях предложенной методики решения задачи о знакопеременном изгибе с растяжением проведено численное исследование [23] некоторых вариантов процесса рихтовки арматурной проволоки диаметром 5 мм из стали 80. Деформационное упрочнение материала аппроксимировалось согласно экспериментальным данным ВНИИметиза формулой
CTS = Gs + 720е°5, МПа, |
(6.57) |
причем
о, = 8 7 4 МПа ( 3 5 0 ° С); а ° = 1 1 0 0 МПа ( 3 0 0 ° С); C j = 1 5 0 0 МПа ( 2 4 ° С).
При проведении расчетов полагалось (рис. 6.18): расстояния между центрами роликов по 0,075 м; центры 2, 4, б, 7, 9 и 11 роликов неподвижны, смещения центров 3, 5, 8 и 10 роликов в Каждом варианте одинаковы и равны -1 , -3, -5 мм; натяжения 11000 и 13200 Н.
Сравнение результатов численного и экспериментального исследований процесса проводилось по значениям давления проволоки на ролики (табл. 6.4) и по величине вытяжки проволоки после рихтовки (рис. 6.22). Различие представленных результатов в обоих случаях не превышало 10 %.
Численное реш ение |
|
|
|
|
|
|
|
|
|
|
|
||||
Точное реш ение |
|
|
|
|
|
|
|
|
|
|
|
||||
1.4 |
|
|
‘t |
U |
<П И |
г |
и |
1.4 |
|
|
|
|
|
|
|
|
|
в |
д |
|
|
|
|
|
|
|
|||||
1.0 |
|
о |
( |
|
|
о . |
|
о |
1.0 |
8 —(\ |
R |
4 1 |
R 1} |
в |
|
|
|
|
|
|
|
|
|
|
|
|
* |
0 |
^ |
|
|
|
|
|
|
|
|
|
|
|
|
□ |
|
|
|
|
|
0.6 |
|
|
|
|
|
|
|
|
0.6 |
|
|
|
|
|
|
0.2 |
4 |
8 |
16 |
32 |
64 |
128 256 |
512 |
0.2 |
|
|
|
|
|
|
|
|
|
|
|
|
|
|
|
||||||||
|
|
|
|
|
1& |
|
|
|
|
|
|
|
|
|
|
1.4 |
|
|
|
|
|
|
|
|
1.4 |
|
|
|
|
|
|
1.0 |
|
О |
i1 |
п |
^ |
й |
1? |
0 |
1.0 |
|
4--- 0- |
|
|
|
|
|
---5 |
1 |
|
1 |
|
|
|
|
|
||||||
0.6 |
|
□ |
|
|
|
|
|
|
0.6 |
|
|
|
|
|
|
|
|
|
|
|
|
|
|
|
|
|
|
|
|
||
0.2 |
4 |
8 |
16 |
32 |
64 |
128 256 |
512 |
0.2 |
8 |
16 |
32 |
64 |
128 2S6 |
512 |
|
|
4 |
||||||||||||||
|
|
|
|
|
в |
|
|
|
|
|
|
|
г |
|
|
Рис. 6.20. Сходимость численного решения задачи об изгибе бруса
взависимости от числа узлов по длине пролетов и числа конечных элементов
всечении; о - усилие на опоре; Д - наибольшая кривизна; □ - остаточная кривизна бруса; а - 5 узлов, б - 10 узлов, в - 15 узлов, г - 20 узлов
Рис. 6.21. Сходимость последовательности значений изгибающего момента на центральной опоре при выполнении итерационной процедуры
Анализ полученного решения подтверждает принятую гипотезу о точечном контакте проволоки и роликов, поскольку огибание последних происходит по дуге менее 3°. Хорошее качественное и количественное совпадение расчетных данных с экспериментальными дает возможность говорить о справедливости сделанных предположений, об эффективности применения рассмотренного подхода к исследованию процесса стационарного знакопеременного изгиба с натяжением.
Таблица 6.4 Расчетное и замеренное (в скобках) давление проволоки на ролики, Н
Смещения |
|
|
|
Номера роликов |
|
10 |
|
||||
2 |
3 |
4 |
5 |
6 |
7 |
8 |
9 |
11 |
|||
роликов, мм |
|||||||||||
- 3 |
980 |
1990 |
2250 |
2330 |
1150 |
975 |
1900 |
2250 |
2350 |
1300 |
|
|
|
(2200) |
|
(2500) |
|
|
(2100) |
|
(2600) |
1680 |
|
- 5 |
1680 |
2990 |
3150 |
3260 |
1620 |
1500 |
2840 |
3120 |
3210 |
||
|
|
(3150) |
|
(3400) |
|
|
(3150) |
|
(3400) |
|
Отличительной особенностью предложенного алгоритма является принципиальная возможность учета истории нагружения каждой частицы материала при ее движении по линиям тока. Это, в свою очередь, позволяет объяснить механизм образования вытяжки проволоки при знакопеременном изгибе с натяжением, который рассмотрим на результатах расчетов одного из вариантов (смещение -3 мм, натяжение 11000 Н, а\ = 1500 МПа).
Рис. 6.22. Расчетные (-о-) и замеренные (Д) значения вытяжки проволоки
взависимости от заглубления роликов
ипределатекучести при натяжении 13200 кН;
1 - а°5 = 874 |
МПа, 2 - а* = 1100 МПа, |
3 - |
а* = 1500 МПа |
Проследим историю нагружения четырех диаметрально противоположных частиц А, В, С и D (рис. 6.23). Для простоты примем, что до растяжения остаточные напряжения отсутствуют. Тогда перед входом на участок знакопеременного изгиба в проволоке есть только постоянное по сечению напряжение растяжения (в данном варианте 560 МПа), к которому в
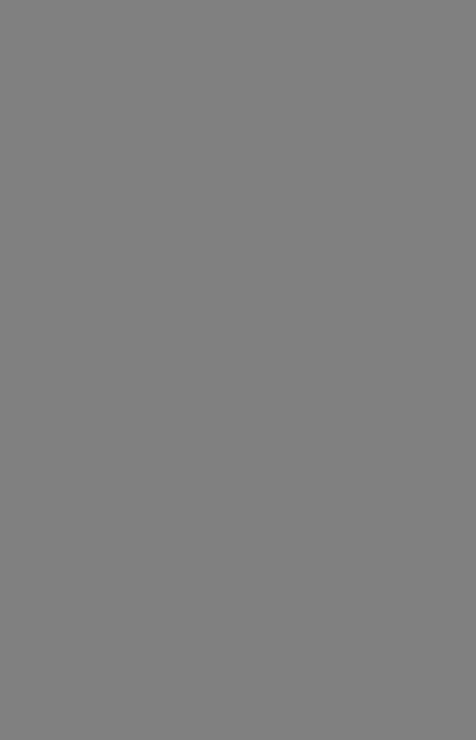
наиболее растянутых и растяжению наиболее сжатых волокон, обусловливает наличие сжимающих и растягивающих напряжений соответствующих зонах.
а |
б |
Рис. 6.23. История нагружения точек (отмечены на схеме) сечения проволоки в процессе знакопеременного изгиба
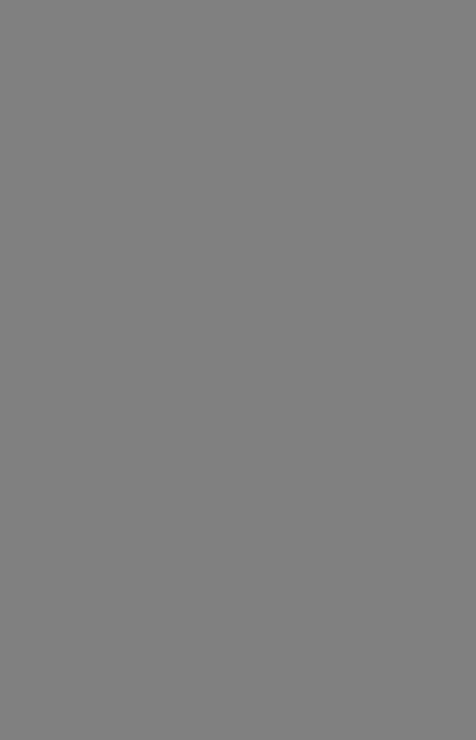
Моделирование поведения тяжелой полосы металла в процесе свободного петлеобразования
Важнейшей тенденцией развития широкополосных станов горячей прокатки является повышение массы используемых заготовок, позволяющее увеличить производительность и улучшить качество горячекатаных полос. Сопутствующая этому необходимость удлинения промежуточного рольганга приводит к увеличению производственных площадей стана и тепловых потерь при транспортировке этих полос по рольгангу. Соответственно возрастают капитальные затраты на строительство или реконструкцию станов, ухудшается температурный режим процесса прокатки.
Решить указанные проблемы позволяет петлеобразование раскатов на выходе из черновой группы стана. В отличие от широко применяемого за рубежом способа прокатки со смоткой раскатов в рулоны на промежуточных перемоточных устройствах новый способ обеспечивает значительно более высокую производительность стана.
Из возможных вариантов реализации процесса петлеобразования относительно толстых широких полос наиболее экономичным, предпочтительным для внедрения при реконструкциях действующих станов и представляющим большой научный интерес является вариант [24, 25] свободного петлеобразования (рис. 6.25), когда петля раската формируется исключительно за счет разности скоростей в последней черновой клети / и в специальных тянуще-тормозных роликах 2.
Вначале скорости этих роликов синхронизированы и движущийся раскат имеет плоскую форму. При подходе переднего конца раската к летучим ножницам перед чистовой группой ролики затормаживаются и между ними и клетью начинает формироваться и накапливаться петля. После выхода заднего конца раската из клети происходит выборка петли роликами.
Процесс свободного петлеобразования относительно толстой и широкой движущейся полосы теоретически не изучен, вместе с тем для проектирования петлеобразующего оборудования, прогнозирования характера протекания процесса и обеспечения его стабильности необходима математическая модель, которая позволяла бы определять геометрические, кинематические и энергосиловые параметры процесса на стадиях образования и выборки петли.
С точки зрения механики твердого деформируемого тела исследование процесса петлеобразования требует решения нестационарной динамической задачи упругопластичности при наличии как геометрической (связь деформаций и перемещений, “большие” перемещения и повороты материальных частиц), так и физической (учет упругопластических свойств материала) нелинейностей.
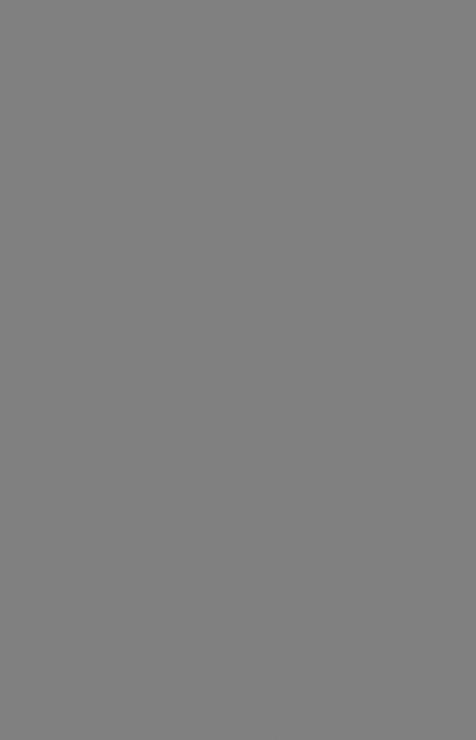