
Решение инженерных задач на высокопроизводительном вычислительном к
..pdfВместе с тем при измельчении сетки желательно избегать резких отличий геометрических размеров соседних ячеек – линейные размеры не должны отличаться более чем в 2 раза.
Граничные условия для расчета напряженно-деформиро- ванного состояния подземных трубопроводов газоперекачивающего тракта задавались на всей расчетной области: торцы магистрали были жестко закреплены; задано ограничение вертикальных перемещений по нижней части всей магистрали.
В численном расчете для сопряжения составных областей использовалась контактная постановка, так что получалась составная система, состоящая из двух или более подобластей. Подобласти соединяются между собой по линиям, называемым границами сопряжения или контакта. В общем случае каждая из подобластей имеет свои, отличные от других, физико-механи- ческие свойства материала, однако разбиение области на подобласти может производиться также из геометрических или какихлибо других соображений. В нашем случае ограничимся задачами с очевидным характером контакта, так что перед решением задачи можно заранее однозначно указать границы сопряжения и условия, которые должны быть выполнены на этих границах, – условия сопряжения. Основным типом условий сопряжения в рассматриваемых задачах является условие идеального механического контакта, состоящее в непрерывности на границе сопряжения векторов смещений и усилий. Применительно к нашим расчетным моделям контакт назначался в областях магистрали с переходом по толщине конструкции. Тип взаимодействия – идеальный контакт, моделирующий сварные соединения (bonded).
При численном моделировании напряженно-деформи- рованного состояния подземных частей трубопроводной конструкции давление грунта рассчитывалось для глубины залегания 1 м, что соответствовало приведенному давлению 10 кПа.
По результатам проведенных исследований получены поля общих перемещений (рис. 9.2) и напряжений по Мизесу
(рис. 9.3).
111

Рис. 9.2. Распределение общих перемещений, мм (часть конструкции)
Для сравнения получаемых в ANSYS результатов были проведены дополнительные расчеты в инженерном пакете ABAQUS. Сравнение результатов расчетов в системах инженерного анализа ANSYS и ABAQUS показало ихудовлетворительно совпадение.
Рис. 9.3. Распределение напряжений по Мизесу, МПа (часть конструкции)
По результатам вычислительных экспериментов были разработаны методики моделирования напряженно-деформирован- ного состояния подземных трубопроводов газоперекачивающего тракта в ANSYS и ABAQUS.
112

ГЛАВА 10. ЧИСЛЕННОЕ МОДЕЛИРОВАНИЕ ВИБРОУСТОЙЧИВОСТИ ВАЛОВ ГАЗОПЕРЕКАЧИВАЮЩИХ АГРЕГАТОВ В МАГНИТНЫХ ПОДВЕСАХ
В данной главе представлены результаты численного моделирования виброустойчивости валов газоперекачивающих агрегатов в магнитных подвесах. На основе анализа условий работы существующих конструкций были разработаны физическая и математическая модели для проведения вычислительных экспериментов. Учитывалось размещение вала в магнитном подвесе. Расчеты проводились в программных комплексах
ANSYS и ABAQUS.
Для проведения вычислительного эксперимента необходимо выбрать свойства материалов, определить геометрические характеристики конструкции и особенности ее крепления, выбрать критерии оценки, провести анализ граничных условий. Кроме того, необходимо разработать математическую модель для описания физических процессов.
Рассматривались две конструкции вала. Ниже приведена базовая конструкция вала с опорными элементами (рис. 10.1). В процессе проведения вычислительных экспериментов данная конструкция была дополнена рабочими колесами и опорными дисками (рис. 10.2, 10.3).
Рис. 10.1. Твердотельная модель базовой конструкции вала с опорными элементами
113
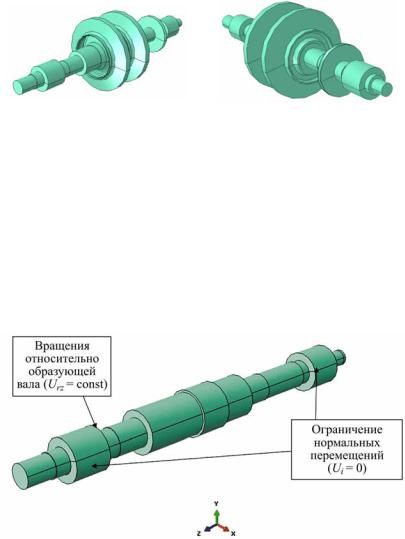
Рис. 10.2. Твердотельная модель базовой конструкции вала, дополненной лопатками
и опорными дисками (вид с переднего торца)
Рис. 10.3. Твердотельная модель базовой конструкции вала, дополненной лопатками
и опорными дисками (вид с заднего торца)
В соответствии с постановкой задачи принимались следующие граничные условия: на поверхностях опорных элементов задавались ограничения нормальных перемещений по трем осям. К торцевому элементу вала прикладывалась угловая скорость, значения которойварьировалисьотносительнообразующейвала(рис. 10.4).
Рис. 10.4. Твердотельная модель вала с граничными условиями
Вкачестве конструкционного материала, в соответствии
стехническим заданием, была выбрана конструкционная
114
сталь 45 (сталь конструкционная углеродистая качественная):
Е= 200 ГПа, ν = 0,3, ρ = 7810 кг/м3.
Сучетом особенностей условий работы валов была сформулирована следующая физическая модель:
–напряженно-деформированное состояние рассматривалось в трехмерной постановке;
–расчеты проводились в статике;
–критерием оценки работоспособности конструкции являются максимальные перемещения;
–материал конструкции упругий;
–материал конструкции изотропный;
–воздействие окружающей среды не учитывается;
–конструкция рассчитывалась с учетом воздействия силы тяжести.
На первом этапе была посчитана базовая модель вала. Далее проводились расчеты для «короткого» вала, и на третьем этапе проводились расчеты для базовой конструкции вала, дополненной рабочими колесами и опорными дисками.
В ходе математического моделирования в ANSYS исследовалось динамическое состояние роторов турбоагрегатов и их элементов при изменениях параметров их сборки.
Сложность математического описания процессов деформации роторов в составе валопроводов и развития процессов вибрации под воздействием локальных, монтажных и динамических дисбалансов приводит к выводу о целесообразности мате-
матического моделирования процесса сборки применительно к каждому отдельно взятому ротору с обязательным введением параметров внешнего воздействия.
Для обеспечения математического моделирования определены:
1)критерий оптимизации: динамические изгибы валов
иустановленных рабочих колес роторов;
115
2) целевая функция: динамические изгибы валов зависят от эксцентриситетов масс участков вала и установленных элементов, масс имитационных и уравновешивающих грузов в плоскости
коррекции и частоты вращения: ∆ R= ( f (M i , mи , mу , ω))→ min .
Экстремум: 0; 3) ограничения: эксцентриситеты участков валов не пре-
вышают 6 мкм, частота вращения валов роторов с упругой подвеской не превышает 6000 об/мин, частота вращения удлиненных гибких валов – 10000 об/мин.
Поиск оптимального решения в ходе вычислительных экспериментов заключается в определении экстремального значения изгибов ротора при условии, что все ограничения удовлетворяются. Сформулированная задача оптимизации решается в ходе поискового вычислительного эксперимента.
Использование математического моделирования позволяет управлять суммированием погрешностей роторов, искать решения, снижающие изгибы, сравнивать варианты, что обеспечивает управление технологическим процессом сборки.
Оптимизация в исследуемом случае может заключаться в рассмотрении групп возможных вариантов и выборе лучшего из них. Это обеспечивает оптимальность принимаемого решения.
Вместе с тем существует задача получения высоких результатов сборки при явном несоответствии параметров собираемых деталей. В частности, необходимо обеспечить заданный уровень уравновешенности ротора при существенном превышении эксцентриситетов масс участков (эксцентриситеты масс роторов, превышающие 1 мкм, уже находятся запределами уравновешенности).
Моделирование позволяет, используя известные параметры базовой детали и линейные параметры устанавливаемых деталей, определять их эксцентриситетно-массовые параметры.
Проведенная предварительная подготовка элементов позволит получить точностные качественные параметры ротора, намного превышающие параметры сопрягаемых деталей.
116
При проведении моделирования использовался метод конечных элементов, позволивший описать положение локальных дисбалансов и их направление по всей длине ротора. Особенностью разработанной методики математического моделирования является учет локального воздействия дисбалансов, определяемых особенностями конструкции устанавливаемых элементов и индивидуальности эксцентриситетов посадочных поверхностей. При этом моделируются прямое влияние величины и направление эксцентриситета на вектор локального дисбаланса и вектор деформации ротора [1–9 ].
Объектами моделирования были роторы компрессоров серии НЦ, разработанные и изготовленные в НПО «Искра» (г. Пермь), предназначенные для установки на компрессорных станциях газопроводов и дожимных компрессорных станциях газовых хранилищ. При этом использовались идентичные и составные цилиндрические твердотельные модели валов, роторов и их элементов.
При разработке блока исходных данных для моделирования за основу были приняты основные размеры реальных объектов и допуски на изготовление, используемые в производстве. При определении нагрузок на роторы и их элементы использовались стандартные эксплуатационные параметры, принятые для компрессоров серии НЦ.
При моделировании в состав исходных данных включены и характеристики опор с магнитными подшипниками, используемыми в компрессорах данной серии. При моделировании процессов упругих деформаций высокоскоростных роторов учитывалось также и возрастающее значение вторичных динамических дисбалансов.
Используемые расчетные программы – АNSYS, ABAQUS. В целом было проведено свыше 60 вычислительных экспериментов.
117
При этом задачи моделирования были реализованы в несколько этапов:
1.Моделирование динамического состояния ротора с упругой подвеской на высоких частотах без учета дисбалансов.
2.Моделирование динамического состояния твердотельной модели удлиненного гибкого вала в рабочем диапазоне частот.
3.Моделирование динамического состояния твердотельной модели вала с упругой подвеской в рабочем диапазоне частот.
4.Моделирование динамического состояния с учетом гравитации и без ее учета.
5.Моделирование динамического состояния с имитацией эксцентриситетов участков валов с использованием локально установленных грузов.
Для моделирования динамического состояния валов и роторов были сформированы соответствующие блоки исходных данных.
Результаты математического моделирования динамического состояния ротора (рис. 10.5) позволяют сделать следующее заключение:
– при достижении первой критической частоты вал имеет характерный изгиб, интенсивность изгибов увеличивается при увеличении эксцентриситетов участков вала и элементов ротора, влияние остаточного дисбаланса несущественно;
– при достижении второй критической частоты вал имеет характерный изгиб, интенсивность изгибов увеличивается при увеличении эксцентриситетов, влияние остаточного дисбаланса несущественно;
– во всем диапазоне эксплуатационных частот направление деформации элементов ротора определяется направлением их дисбалансов. Деформациям наиболее подвержены консольные части элементов, интенсивность изгибов увеличивается при увеличении их дисбалансов.
118

а
б
Рис. 10.5. Результаты математического моделирования деформаций ротора и его элементов под воздействием локальных дисбалансов:
а – первая; б – вторая критическая частота
Имитация дисбаланса при расчетах проводилась введением эксцентриситетов участков и точечных грузов. В табл. 10.1 приведены параметры эксцентриситетов участков, в табл. 10.2 – параметрыгрузов.
Величины эксцентриситетов были определены по результатам измерений прототипов. Массы грузов были определены расчетом исходя из эксцентриситетов и масс участков вала.
119

Таблица 1 0 . 1
Параметры эксцентриситетов участков
|
Номер |
|
Величина эксцентриси- |
|
|
|
|
Величина эксцентриси- |
|
|
|
тета участка вала ротора |
|
α |
|
тета участкаудлиненного |
|
α |
|||
|
участка |
|
с упругой подвеской, е, |
|
|
|
гибкого вала, е, |
|
||
|
вала |
|
мкм |
|
|
|
|
мкм |
|
|
|
|
|
|
|
|
|
|
|
||
|
1 |
2,85* |
270º |
|
3,65* |
|
–3,48º |
|||
|
2 |
1,31* |
13º |
|
0 |
|
0 |
|||
|
3 |
0 |
0º |
|
2,75 |
|
3,22º |
|||
|
4 |
2,12 |
36º |
|
5,55 |
|
7,74º |
|||
|
5 |
2,92 |
59º |
|
7,5 |
|
15,78º |
|||
|
6 |
2,66 |
39º |
|
5,78 |
|
23,81º |
|||
|
7 |
2,4 |
19º |
|
2,87 |
|
28,62º |
|||
|
8 |
1,2 |
9º |
|
0 |
|
0 |
|||
|
9 |
0 |
0º |
|
|
|
|
|
||
|
10 |
6,09* |
195º |
|
|
|
|
|
||
|
11 |
6,8* |
197º |
|
|
|
|
|
||
|
* Консольное положение участка |
|
Таблица 1 0 . 2 |
|||||||
|
|
|
|
|
|
|
|
|||
|
|
|
Параметры установки грузов |
|
||||||
|
|
|
|
|
|
|
|
|
|
|
|
Номер |
|
Масса груза, |
|
|
|
|
Масса груза, |
|
|
|
|
установленного |
|
α |
|
установленного |
α |
|||
|
участка |
|
|
|
||||||
|
|
на участке вала ротора |
|
|
на участке удлиненного |
|||||
|
вала |
|
с упругой подвеской, г |
|
|
|
|
гибкого вала, г |
|
|
|
|
|
|
|
|
|
|
|||
|
1 |
|
1* |
|
270º |
|
0,8* |
|
–3,48º |
|
|
2 |
|
2* |
|
13º |
|
|
0 |
|
0 |
|
3 |
|
0 |
|
0º |
|
|
0,6 |
|
3,22º |
|
4 |
|
1 |
|
36º |
|
|
4,1 |
|
7,74º |
|
5 |
|
4 |
|
59º |
|
|
7,6 |
|
15,78º |
|
6 |
|
2 |
|
39º |
|
|
3,9 |
|
23,81º |
|
7 |
|
2 |
|
19º |
|
|
0.78 |
|
28,62º |
|
8 |
|
0,6 |
|
9º |
|
|
0 |
|
0 |
|
9 |
|
0 |
|
0º |
|
|
|
|
|
|
10 |
|
6* |
|
195º |
|
|
|
|
|
|
11 |
|
1* |
|
197º |
|
|
|
|
* Консольное положение участка
120