
Промышленные роботы Ч. 2 учебное пособие
.pdfректирующий сигнал в систему гидропривода для возвращения рабочего органа в проектное положение. В других случаях используются акустические датчики, работающие по принципу дальномера. С их помощью выполняется точное копирование проектного профиля, закрепленного на местности с помощью монтажных струн. С помощью датчика наклона выполняется контроль поперечного уклона подготавливаемого покрытия. Бортовой компьютер исполняет роль блока управления и настройки системы, аккумулирует информацию, получаемую со всех датчиков, выполняет мгновенный анализ соответствия текущего полотна проекту и вносит необходимую корректировку в положение рабочего органа машины.
В состав системы управления входят: блок управления, лазерный датчик, ультразвуковой датчик, датчик наклона, акустическая система сглаживания. Блок управления принимает сигналы от датчиков (ультразвуковых, лазерных и наклона) для анализа и корректировки положения виброплиты асфальтоукладчика, посылает сигналы в гидроклапаны, контролирующие главные цилиндры каждой стороны машины. Таким образом, с помощью блока управления можно регулировать толщину покрытия в процессе работы.
Лазерный датчик, закрепляемый с одной стороны (с двух сторон) машины на раме выброплиты, используется для контроля положения рабочего органа по высоте относительно плоскости, задаваемой лазерным построителем. Он имеет светоиндикаторы для визуального оповещения оператора при смещении отвала относительно лазерной плоскости. Погрешность определения лазерной плоскости ±1 мм. Датчик оснащен системой сервопривода для быстрого поиска зоны действия лазера.
Ультразвуковой датчик контролирует смещения рабочего органа по высоте относительно монтажных струн, бордюрных камней и прочих поверхностей, определяет смещения по высоте с точностью ±1 мм, имеет встроенную систему визуального оповещения и систему температурной компенсации измерений.
Датчик наклона оснащен двумя разъемами для подключения одновременно к двум блокам управления. Встроенный термодатчик позволяет учитывать изменения температуры воздуха в процессе работ и вносить поправки в значения поперечного уклона. Он закрепляется непосредственно на раме рабочего органа и определяет его поперечный наклон. Диапазон измерений ±20 %, дискретность отсчетов 0,025 %. Имеет пыле- и водозащищенную конструкцию.
41

Акустическая система сглаживания (система контроля высоты) объединяет несколько ультразвуковых датчиков для вычисления осредненной опорной отметки относительно струны или другой поверхности. В отличие от механической лыжи, перетаскиваемой по земле, акустическая система сглаживания – полностью бесконтактная система. Она используется для более сглаженного асфальтирования.
Системы управления бульдозерами. Системы управления, разработан-
ные для бульдозеров, позволяют выполнять предварительные земляные работы
вавтоматическом режиме с контролем поперечного уклона и высоты отвала
сточностью ± 2 см. Системы 2D управления бульдозерами (рис. 2.27), состоящие из лазерного датчика, блока управления и гидроклапанов, наиболее эффективны при подготовке ровных поверхностей. А комплект простейшей индикаторной системы с ручным управлением отвала состоит всего из одного лазерного датчика, что уже дает значитель-
Рис. 2.27. Машиныдляземляных работ ное увеличение эффективности и повышение качества земляных работ.
Для реализации больших и сложных проектов идеально подходит система 3D GPS. Во время работы координаты отвала постоянно сравниваются с загруженными в бортовой компьютер проектными данными. Управление отвалом полностью берет на себя автоматика. Информация о работе системы и о положении бульдозера на объекте выдается на дисплей, размещенный в кабине машиниста.
Системы управления экскаваторами.
Новейшая индикаторная система управления экскаватором 3Dxi обеспечивает оператора экскаватора всей необходимой информацией о положении ковша и самой машины при выполнении любых земляных работ (рис. 2.28). В отличие от лазерных систем
Рис. 2.28. Экскаватор с системой
управления экскаваторами, 3Dxi позволяет
управления 3Dxi оператору видеть положение своей машины на рабочем объекте с точной координатной
привязкой к характерным линиям и направлениям проекта. В процессе работы оператор также может видеть положение зубьев ковша по отношению к окончательной проектной поверхности, что является особенно полезным при экска-
42
вации с большой глубины, при полном отсутствии видимости ковша и при опасности повреждения коммуникаций.
С помощью постоянного контроля, связанного с цифровым проектом, оператор экскаватора значительно снизит расходы, необходимые для выполнения геодезических измерений на объекте. Разбивка может быть сведена до минимума, так как фазы повторного выноса в натуру и полевого контроля в течение всего срока работ на проекте полностью исключаются. Оператор всегда точно знает, где находится окончательная проектная поверхность, поэтому нет необходимости ждать геодезиста для выноса или контроля. Информация о сравнении данных цифрового проекта с действительным положением машины постоянно отображается на экране бортового компьютера.
Разработанные системы 3Dxi управления экскаваторами не только снижают непосредственные расходы, но и гарантируют высокое качество результатов работы.
43
3. ПРИНЦИПИАЛЬНОЕ УСТРОЙСТВО ПРОМЫШЛЕННОГО РОБОТА
3.1. Общие сведения об устройстве ПР
На сегодняшний день основным типом манипуляционных устройств для роботов являются механические манипуляторы. Они представляют собой разомкнутую кинематическую цепь, составленную из кинематических пар, имеющих одну (реже две) степень подвижности с поступательным или угловым перемещением рабочего органа, расположенного на конце манипулятора, и приводов, чаще всего раздельных для каждой степени подвижности.
Степени подвижности манипулятора делятся на переносные и ориентирующие. Переносные степени подвижности служат для перемещения объекта манипулирования в пределах рабочей зоны манипулятора, а ориентирующие – для его ориентации в пространстве.
Теоретически минимально необходимое число переносных степеней подвижности для перемещения объекта манипулирования в любую точку совершенно свободной рабочей зоны равно трем. Однако для расширения манипуляционных возможностей и обеспечения требуемых значений кинематических и динамических параметров манипулятора (реализации более сложных траекторий движения, например, для обхода препятствий, повышения быстродействия и т. п.) манипуляторы обычно снабжают несколькими избыточными переносными степенями подвижности, хотя это, разумеется, существенно усложняет и повышает стоимость робота.
Максимально необходимое число ориентирующих степеней подвижности равно трем. Обычно они реализуются кинематическими парами с угловым перемещением, обеспечивающими поворот рабочего органа манипулятора относительно его продольной и двух других взаимно перпендикулярных осей.
Приводы манипулятора, которые могут быть электромеханическими, гидравлическими и пневматическими, обычно размещают непосредственно в звеньях манипулятора или выносят на его основание с передачей движения на соответствующее звено через различного типа передаточные механизмы.
Место размещения приводов в значительной степени определяет конструкцию манипулятора. Размещение приводов непосредственно в звеньях манипулятора существенно упрощает кинематические связи, что также способствует повышению точности. Недостатком такой компоновки является увеличение массы подвижной части манипулятора. Последнее ведет к снижению его грузо-
44
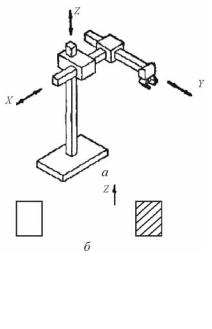
подъемности и динамических параметров. В связи с этим обычно, оптимизируя конструкцию манипуляторов, прибегают к комбинации двух вариантов размещения приводов для разных степеней подвижности.
Для увеличения мощности приводов широко используют различные устройства уравновешивания.
На рис. 3.1–3.3 показаны конструкции манипуляторов с тремя переносными степенями подвижности в различных системах координат и их рабочие зоны.
Манипуляторы, работающие в прямоугольной системе координат (рис. 3.1), имеют рабочую зону в виде параллелепипеда. Здесь осуществляются только поступательные перемещения, поэтому такая система координат наиболее удобна для выполнения прямолинейных движений. Кроме того, она максимально упрощает программирование робота, так как оно обычно выполняется именно
впрямоугольной системе координат, и, следовательно, в этом случае не требуется пересчета программ из одной системы координат в другую.
Манипулятор, работающий в сферической системе координат (рис. 3.2), может осуществлять как поступательные, так и угловые перемещения. Он может быть использован для контурной и позиционной системы обслуживания.
Приведенный на рис. 3.3 манипулятор с угловой (ангулярной) системой координат производит только угловые перемещения, т.е. все его звенья представляют собой шарниры. B связи с этим часто такие манипуляторы называют еще шарнирными и антропоморфными. Роботы с такого типа манипуляторами благодаря возможности последних складываться, практически не выступая за габарит основания робота, обладают наибольшей компактностью, хотя и наиболее сложны в управлении. Все представленные манипуляторы имеют всего по три переносных степени подвижности. Однако поскольку манипуляторы реальных роботов в большинстве случаев содержат большее количество звеньев и, следовательно, обладают избыточностью по числу степеней подвижности,
вних чаще всего реализуются различные комбинации рассмотренных выше основных типов систем координат при разных соотношениях степеней подвижности с поступательным и угловым перемещениями.
45

Рис. 3.2. Манипулятор со сферической |
Рис. 3.3. Манипулятор с угловой системой |
системой координат (a) и его рабочая |
координат (a) и его рабочая |
зона (б) |
зона (б) |
Наряду с дальнейшим совершенствованием механических манипуляторов, заимствованных в робототехнике от конструкций копирующих и других типов манипуляторов с неавтоматическим управлением, ведутся работы по созданию принципиально новых типовманипуляционных устройств. К ним относятся, в частности, устройства для манипулирования предметами с помощью управляемого электромагнитного поля. В настоящее время подобные устройства получили практическое применение как для перемещения, так и для ориентации произвольно расположенных предметов. Имеются устройства для сварки электронным лучом, программно-управляемым по двум координатам, для сварки, резки и раскроя различных материалов лазерным лучом. Подобные устройства могут заменять также в специальных роботах последние звенья с их рабочим органом.
3.2. Конструкции узлов и агрегатов ПР
ПР состоит из манипулятора (силового исполнителя) и программатора (системы управления), т.е. является автоматическим манипулятором с программным управлением.
Для выполнения сложных производственных функций ПР должен иметь: рабочие органы (руки); управляющую систему и ЭВМ; комплекс датчиков рабочих органов робота и состояния рабочей среды; комплекс средств общения человека с роботом, необходимых для ввода команд, контроля функционирова-
46
ния. Устройство управления робота управляет его манипуляционными устройствами и устройством передвижения, образуя в совокупности с ними как объектами управления систему автоматического управления роботом. Кроме того, часто устройство управления роботов используют для управления различными другими объектами (технологическим оборудованием, транспортными устройствами и т.п.), которые работают совместно с роботом, образуя с ним единый технологический комплекс.
По способу управления различают следующие системы управления роботами и соответствующие устройства управления:
–программные, в которых управление осуществляется по заранее составленнойиостающейсянеизменнойвпроцессереализацииуправляющейпрограмме;
–адаптивные, в которых управление реализуется в функции от информации о текущем состоянии и изменениях внешней среды и самого робота, получаемой в процессе управления от сенсорных устройств;
–интеллектуальные, в которых адаптивные свойства развиты до уровня, соответствующего интеллектуальной деятельности человека.
При этом в зависимости от типа реализуемого по отдельным степеням подвижности движения различаются устройства:
–контурного управления, когда управляемое движение осуществляется по непрерывной траектории;
–позиционного управления, когда управляемое движение производится шагами (по конечному числу точек позиционирования);
–циклового управления, когда число таких точек по каждой степени подвижности сводится к начальной и конечной, которая при этом определяется механическим упором или концевым выключателем.
Устройства управления могут быть индивидуальными, входящими в со-
став одного робота, или групповыми, управляющими несколькими роботами. Конструктивно индивидуальные устройства управления выполняют либо отдельно от механической части робота, либо, что значительно реже, в общем с ней корпусе.
Большинство роботов имеет электронные устройства управления, выполненные на микроэлектронной элементной базе с примением микропроцессоров и микро- и мини-ЭВМ.
Однако существуют и неэлектрические устройства управления роботов, чаще всего реализуемые по принципам пневмоники и предназначенные, как правило, для использования в особых взрыво- и пожароопасных условиях.
47

Манипулятор промышленного робота по своему функциональному назначению должен обеспечивать движение выходного звена и закрепленного в нем объекта манипулирования в пространстве по заданной траектории и с заданной ориентацией. Для полного выполнения этого требования основной рычажный механизм манипулятора должен иметь не менее шести степеней подвижности, причем движение механизма в каждой из них должно быть управляемым. Промышленный робот с шестью степенями подвижности сложен как в изготовлении, так и в эксплуатации. Поэтому в реальных конструкциях промышленных роботов часто используются механизмы с числом степеней подвижности менее шести. Наиболее простые манипуляторы имеют три (реже две) степени подвижности. Такие манипуляторы значительно дешевле в изготовлении и эксплуатации, но требуют особой организации рабочей среды. Эти требования связаны с заданной ориентацией объектов манипулирования относительно механизма робота. Поэтому оборудование должно располагаться относительно такого робота с требуемой ориентацией.
Рассмотрим для примера структурную и функциональную схемы промышленного робота с трехподвижным манипулятором. Основной механизм руки манипулятора состоит из неподвижного звена 0 и трех подвижных звеньев 1, 2
и 3 (рис. 3.4).
а |
б |
Рис. 3.4. Промышленный трехподвижный манипулятор: а – функциональная схема; б – структурная схема
48

Механизм этого манипулятора соответствует цилиндрической системе координат. В этой системе звено 1 может вращаться относительно звена 0 (относительное угловое перемещение 10), звено 2 перемещается по вертикали относительно звена 1 (относительное линейное перемещение S21) и звено 3 перемещается в горизонтальной плоскости относительно звена 2 (относительное линейное перемещение S32). На конце звена 3 укреплено захватное устройство, или схват, предназначенное для захвата и удержания объекта манипулирования при работе манипулятора. Звенья основного рычажного механизма манипулятора образуют между собой три одноподвижные кинематические пары (одну вращательную А и две поступательные В и С) и могут обеспечить перемещение объекта в пространстве без управления его ориентацией. Для выполнения каждого из трех относительных движений манипулятор должен быть оснащен приводами, которые состоят из двигателей с редуктором и системы датчиков Д обратной связи. Так как движение объекта осуществляется по заданному закону движения, то в системе должны быть устройства, сохраняющие и задающие программу движения, которые назовем программоносителями (дискеты, диски CD, магнитные ленты и др.). Преобразование заданной программы движения в сигналы управления двигателями осуществляется системой управления. Эта система включает ЭВМ с соответствующим программным обеспечением, цифроаналоговые преобразователи и усилители. Система управления в соответствии с заданной программой формирует и выдает на исполнительные устройства приводов (двигатели) управляющие воздействия ui. При необходимости она корректирует эти воздействия по сигналам xi, которые поступают в нее с датчиков обратной связи. Функциональная схема промышленного робота приведена на рис. 3.5.
Рис. 3.5. Функциональная схема промышленного робота
49

В зависимости от условий эксплуатации ПР к узлам и агрегатам предъявляются различные требования: высокая надежность функционирования, обеспечение заданной точности обработки программы, минимальная масса и инерционность, минимальный мертвый ход, обеспечение возможности работы в конкретных тяжелых условиях среды.
Некоторые конструкции узлов ПР, работающих в разных системах координат, показаны на рис. 3.6, 3.7, 3.8. Рука манипулятора промышленного робота (см. рис. 3.6) передвигается в сферической системе координат и несет кисть с захватом. Рука может перемещаться в радиальном направлении R в направляющих башни. Последняя может поворачиваться в горизонтальной и вертикальной плоскостях, обеспечивая повороты руки. Три степени свободы руки позволяют доставить деталь в любую точку рабочей зоны. Механизм кисти обеспечивает захвату дополнительно две степени свободы – поворот в вертикальной плоскости и поворот вокруг своей продольной оси, необходимые для ориентации детали. Захват имеет дополнительное движение для зажима детали.
Рис. 3.6. ПР со сферической системой координат
Система ЧПУ роботом позиционная. Все движения, кроме захвата, осуществляются по программе от гидроцилиндров и происходят в следящем режиме. Привод захвата работает от пневмоцилиндра. Блок памяти выполнен на магнитном барабане.
Предусмотрена возможность подачи команд в системы управления обслуживаемого технологического оборудования и получения сигналов об исполнении командрабочимиорганамиэтогооборудованиядлявыполнениярабочегоциклаПР.
Программирование производится методом обучения. При этом рука манипулятора с пульта ручного управления проводится последовательно через заданные точки рабочей траектории захвата. При остановке в каждой заданной
50