
Промышленные роботы Ч. 2 учебное пособие
.pdfний Wi(s). Кроме того, при реализации закона управления синтезируется и используется дополнительный сигнал UРТ(t), соответствующий рабочей точке Р (РТ). Этот сигнал помогает улучшить качество управления, обеспечивая более быструю адаптацию к изменениям параметров установки, и увеличивает гибкость системы управления. Исходя из всего вышесказанного, общий закон управления определяется выражением:
U(t)=UПК(t)+UОС(t)+UРТ(t). (4.106)
Синтез регулятора прямого канала управления. Линеаризованную мо-
дель (4.84) динамики манипулятора можно представить моделью в частотной
области (через передаточную функцию) |
|
(s) (C Bs As2 ) 1T (s), |
(4.107) |
где (s) – приращение углов поворота в шарнирах. |
|
Учитывая вышеизложенное, в качестве передаточной функции Q(s) размерностью n n регулятора прямого канала управления выбирается инверсия линеаризованной модели (4.107):
|
2 |
) |
1 1 |
C Bs As |
2 |
. |
(4.108) |
Q(s) (C Bs As |
|
|
|
Уравнение (4.108) дает простое выражение инверсии линеаризованной модели (4.84) манипулятора, что обеспечивает возможность практической реализации Q(s). Необходимо отметить, что инверсия Q(s) многомерного объекта регулирования W(s) в общем случае представляет собой сложную динамическую систему. Тогда закон управления, реализуемый регулятором прямого канала управления, задается выражением:
|
|
2 |
r (s) |
(4.109) |
TПК(s) Q(s) r (s) C Bs As |
|
|||
или |
|
|
|
|
|
|
|
|
(4.110) |
TПК(t) C r (t) B r (t) A r (t), |
|
где r (t) r (t) (t) – требуемый n-мерный вектор-столбец приращений уг-
лов поворота в шарнирах.
Реализация закона управления (4.110) с использованием регулятора прямого канала управления, представляющего собой инверсию робота, осуществляется непосредственной подачей в прямой канал управления требуемых сигналов положения r , скорости r и ускорения r и умножением их на матрицы С,
В и А соответственно.
Синтез регулятора обратной связи. Для повышения устойчивости замк-
нутой системы управления манипулятором и улучшения качества переходных процессов используется регулятор цепи обратной связи K(s):
151

K(s)=Kp+Kvs, |
(4.111) |
где Kp и Kv – матрицы (размерностью п п) коэффициентов обратной связи по положению и скорости, которые необходимо определить. Закон управления, реализуемый регулятором цепи обратной связи, имеет вид:
|
|
(4.112) |
TОС(s) K(s) r (s) (s) K p Kvs e(s) |
||
или |
|
|
TОС(t) K pe(t) Kve(t), |
|
(4.113) |
где e(t) r (s) (s) – n-мерный вектор приращений ошибки отслеживания по положению.
Фактически уравнение (4.113) представляет собой закон управления канала обратной связи по состоянию для линеаризованной модели (4.84) робота, поскольку оно содержит сигналы обратной связи как по (t), так и по (t).
Учитывая результаты вышеприведенного анализа, построим систему управления движением в кинематических парах в приращениях, скомбинировав регулятор цепи обратной связи K(s) и регулятор прямого канала управления Q(s), как показано на блок-схеме (рис. 4.35).
Рис. 4.35. Система управления движением манипулятора в приращениях
С учетом рис. 4.35 закон движения в приращениях задается следующим образом:
– в частотной области
|
2 |
|
|
(4.114) |
T (s) TПК(s) TОС(s) C Bs As |
|
r (s) K p Kv s e(s), |
||
– во временной области |
|
|
|
|
|
|
(t) Kpe(t) Kve(t). |
(4.115) |
|
T (t) C r (t) B r (t) A r |
Когда закон движения в приращениях применяется к нелинейной модели манипулятора, полный закон управления задается выражением:
152
|
|
(t) (ti ) T (t) (ti ) C r (t) B r (t) A r (t) Kpe(t) Kve(t). (4.116) |
Полный закон управления представляет собой сумму двух компонент. Первой из них является значение вектора моментов (ti ) в кинематических парах, приложенного в номинальной рабочей точке Р. Вторая компонента обусловлена регуляторами K(s) и Q(s), обеспечивающими управление движением в приращениях. Пусть далее n-мерный полный заданный вектор описывается выражением r (t) r (ti ) r (t), a n-мерный полный вектор углов поворота в шарнирах (t) (ti ) (t). Подстановка этих выражений в уравнение (4.116) дает полный закон управления, определенный через суммарные переменные:
* |
|
|
(4.117) |
(t) |
(t i ) C r (t) B r (t) A r (t) Kpe(t) Kve(t), |
||
где * (t i ) – n-мерный суммарный вектор ошибки отслеживания, |
|
||
* |
|
|
(4.118) |
(t i ) (ti ) C r (ti ) B r (ti ) A r (ti ). |
Видно, что кроме двух членов, соответствующих регуляторам цепи обратной связи и прямого канала управления, в полном законе управления (4.117) присутствует третий член, отражающий влияние положения рабочей точки Р.
Синтез алгоритмов управления промышленным роботом на основе диффеоморфного преобразования координат и нелинейной обратной связи по состоянию – диффеометрического регулятора. Вначале стабилизируется новая линейная и разомкнутая по выходу динамическая система. Затем для обеспечения устойчивости стабилизированной системы к неопределенностям в значениях параметров робота и задания добавляется контур оптимальной коррекции ошибок для каждой линейной подсистемы с разомкнутым выходом. Структурная схема системы управления с оптимальной коррекцией ошибок представлена на рис. 4.36.
Стабилизация осуществляется путем использования контура линейной обратной связи F в системе и желаемого установления полюсов замкнутой системы. Поскольку F является постоянной блочно-диагональной матрицей, вся система, называемая L&D-блоком, останется линейной с разомкнутым выходом (см. рис. 4.36). Для новогоконтураобратнойсвязи вводятся линейные регуляторы:
|
|
|
vi |
vi |
Fi zi , |
|
|
|
|
|
|
|
(4.119) |
||
где Fi = [fi1 fi2]. Тогда система (4.102) принимает вид: |
|
|
|
|
|
|
|||||||||
0 |
1 |
0 |
|
|
|
|
0 |
1 |
|
0 |
|
|
(4.120) |
||
|
|
|
|
||||||||||||
zi |
zi |
|
(vi Fi zi ) |
fi1 |
fi2 |
zi |
vi . |
||||||||
0 |
0 |
1 |
|
|
|
|
|
|
1 |
|
|
153

Рис. 4.36. Система управления манипуляционным роботом с диффеометрическим регулятором
Полюсы каждой подсистемы определяются выражением:
|
S |
|
|
|
|
1 2 , |
|
|
|
|
|
|
|
(4.121) |
||||||
|
1,2 |
|
|
n |
n |
|
|
|
|
|
|
|
|
|
|
|
|
|
||
где – коэффициент затухания; – собственная частота; 2 |
f |
i1 |
,2 2 |
f |
i2 |
. |
||||||||||||||
|
|
|
|
n |
|
|
|
|
|
|
|
|
|
n |
|
n |
|
|
||
|
Желаемый входной сигнал для каждой подсистемы можно получить из |
|||||||||||||||||||
уравнений: |
|
|
|
|
|
|
|
|
|
|
|
|
|
|
|
|
|
|
|
|
|
zd |
|
|
0 |
|
|
1 |
zd |
|
0 |
|
|
|
|
|
|
||||
|
|
2di 1 |
|
|
|
|
|
|
|
|
2di 1 |
|
|
Vid , |
|
|
(4.122) |
|||
|
z |
2i |
|
fi1 |
fi2 |
z |
2i 1 |
|
1 |
|
|
|
|
|
|
|
||||
|
|
|
|
|
|
|
|
|
|
|
|
|
|
|
|
|
|
|
||
|
yid 1 |
0 |
|
d |
|
, |
i 1,2,3, |
|
|
|
|
|
|
(4.123) |
||||||
|
z2i 1 |
|
|
|
|
|
|
|
||||||||||||
|
|
|
|
|
zd |
|
|
|
|
|
|
|
|
|
|
|
|
|
|
|
|
|
|
|
|
|
2i 1 |
|
|
|
|
|
|
|
|
|
|
|
|
|
|
где |
yd – желаемая траектория. |
|
|
|
|
|
|
|
|
|
|
|
|
|
|
|
|
|
|
|
|
i |
|
|
|
|
|
|
|
|
|
|
|
|
|
|
|
|
|
|
|
|
Оптимизация ошибок. Для синтеза оптимальной системы управления не- |
|||||||||||||||||||
обходимо рассмотреть ошибки |
|
|
|
|
|
|
|
|
|
|
|
|
|
|
|
|
|
|
||
|
|
|
e |
|
y |
|
yd |
|
|
|
|
|
|
|
(4.124) |
|||||
|
|
ei |
i1 |
|
|
|
i |
i |
|
|
|
|
|
|
|
|
||||
|
|
|
ei2 |
y |
i |
yd |
|
|
|
|
|
|
|
|
|
|
||||
|
|
|
|
|
|
|
|
i |
|
|
|
|
|
|
|
|
|
|
|
Из уравнений (4.120)–(4.124) можно получить следующее:
d
(vi vi
т.е.
или
ei 0fi1
154
) ( yi yid ) fi2 ( yi yid ) f
vi ei 2 fi2ei2 fi1ei1
1 |
|
0 |
|
|
|
|
d |
|
|
e |
(v |
|
) Ae |
||||||
|
|
|
vi |
||||||
i |
|
i |
|
|
|
i i |
|||
fi2 |
|
1 |
|
|
|
|
|
|
|
i1 ( yi yid ),
Bi vi .
(4.125)
(4.126)

В систему управления вводится контур оптимальной коррекции ошибок, обеспечивающий минимизацию целевой функции:
|
|
t |
|
||||
J ( |
|
) |
|
R |
|
dt ei (t)TQei (t)dt ei (t)T Sei (t), |
(4.127) |
vi |
vi |
vi |
|||||
0 |
|
|
|
|
|
где R – положительно-определенная матрица; Q и S – положительнополуопределенные матрицы; t – время окончания процесса.
В соответствии с линейной теорией оптимального управления оптимальная коррекция определяется выражением:
|
|
|
0 |
R 1bT P(t)e (t), |
(4.128) |
|
|
|
|||||
|
vi |
|||||
|
|
|
|
i |
i |
|
где |
bT – транспонированная i-я (i = 1, 2, 3) матрица частных передаточных от- |
|||||
|
i |
|
|
|
||
ношений. |
|
|
|
P |
P |
|
является положительно-определенной матрицей |
Матрица P(t) P11 |
P12 |
|
|
21 |
22 |
|
|
решения уравнения Риккати:
P(t) P(t)Ai AiT P(t) P(t)bi R 1biT Р(t) Q.
Если рассматривать установившееся решение при t , то P(t) 0
и уравнение Риккати принимает форму алгебраического уравнения:
PAi AiT P Pbi R 1biT Р Q 0.
Отсюда (4.128) принимает вид:
|
|
0 |
R 1bT Pe (t), |
(4.129) |
|
||||
vi |
||||
|
|
|
i i |
|
или
v0 R 1 P ( y yd ) P ( y yd ) ,
i 12 i i 22 i i
где
P Rf |
i1 |
R f 2 |
Q R 1 |
, |
12 |
i2 |
11 |
|
|
P22 2Rfi2 4 fi22 2 fi22 |
fi22 Q11 Q11 R 1 . |
4.7.5. Экспериментальная проверка работоспособности синтезированных алгоритмов управления на ПЭВМ
С целью экспериментальной проверки работоспособности синтезированных алгоритмов управления было проведено моделирование на ПЭВМ IBM PC. Для этого разработана программа в среде MATLAB. Проведение линеаризации прогрессивным методом, основанным на применении теории групп Ли, вруч-
155
ную практически невозможно. Объектом моделирования являются регулятор, построенный с использованием классической теории многомерных систем (многомерный регулятор), и регулятор, синтезированный на основе указанного новейшего метода управления. Моделирование проведено в двух режимах: при от- сутствии(1-йрежим) иприналичии(2-йрежим) параметрическихвозмущений.
Сравнительная оценка экспериментальных результатов моделирования уравнений динамики робота минимальной конфигурации с синтезированными многомерным и диффеометрическим регуляторами показывает существенное преимущество алгоритмов управления, основанных на новейшем методе. Так, при значительном изменении массы нагрузки для новейшего метода ошибка отслеживания траектории не превысила 0,1 мм, в то время как ошибка многомерного регулятора превысила 4 мм. При наличии в системе модельных ошибок (отклонение параметров модели объекта на 50 %) многомерный регулятор теряет устойчивость, а диффеометрический регулятор сохраняет устойчивость и требуемую точность позиционирования (0,1 мм).
4.7.6. Разработка алгоритмов управления на основе робастных систем
Следующим этапом разработки системы является создание системы робастного управления, которая базируется на современных формализованных подходах к математическому моделированию, исследованию и проектированию систем. Адаптивная САУ реагирует в процессе функционирования на изменение свойств ОУ и внешних воздействий и приспосабливается к новым условиям на основе изменения структуры устройств и параметров управления ими, чтобы показатель качества достигал экстремального значения.
Главной задачей синтеза робастных систем управления является поиск закона управления, который сохранял бы выходные переменные системы и сигналы ошибки в заданных допустимых пределах, несмотря на наличие неопределенностей в контуре управления. Неопределенности могут принимать любые формы, однако наиболее существенными являются шумы, нелинейности и неточности в передаточной функции объекта управления. Поэтому в дальнейшем необходимо разработать робастной регулятор, обеспечивающий работу системы в условиях заданной неопределенности.
156
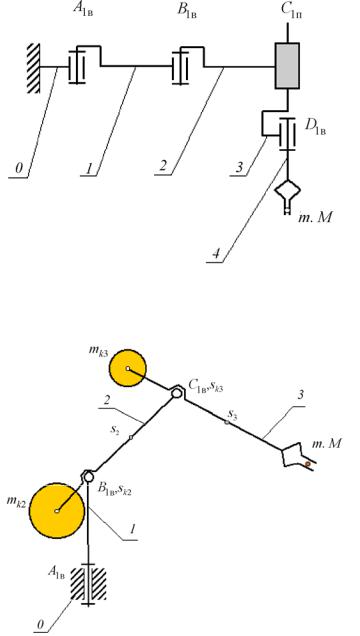
5.УРАВНОВЕШИВАНИЕ МАНИПУЛЯТОРОВ
Вбольшинстве кинематических схем манипуляторов приводы воспринимают статические нагрузки от веса звеньев. Это требует значительного увеличения мощностей двигателей приводов и моментов тормозных устройств. Дляборьбы с этим используюттриметода:
1. Применение кинематических |
|
||
схем манипуляторов, в которых вес |
|
||
звеньев воспринимается подшипни- |
|
||
ками кинематических пар. На мощ- |
|
||
ность приводов и тормозных уст- |
|
||
ройств при таком решении вес ока- |
|
||
зывает влияние только через силы |
|
||
трения в парах. В качестве примера |
|
||
можно |
привести |
кинематическую |
|
схему робота SCARA (рис. 5.1). Не- |
|
||
достатком этого |
метода являются |
Рис. 5.1. Кинематическая схема робота SCARA: |
|
большие |
осевые |
нагрузки в под- |
|
шипниках. |
|
0, 1, 2, 3, 4 – звенья манипулятора |
|
|
|
2.Уравновешивание звеньев манипулятора с помощью корректировки их массы. При этом центр
масс si звена с помощью корректирующих масс mki смещается в центр кинематической пары ski (рис. 5.2). Недостатком этого метода является значительное увеличение массы манипулятора имоментов инерции его звеньев.
3.Уравновешивание веса звеньев манипулятора с помощью упругих разгружающих устройств –
пружинных |
разгружателей или |
Рис. 5.2. Уравновешивание звеньев |
|
уравновешивателей. Эти устройства |
|||
манипулятора корректировкой их массы: |
|||
не позволяют |
обеспечить полную |
0, 1, 2, 3 – звенья манипулятора |
разгрузку приводов от действия веса на всем относительном перемещении звеньев. Поэтому конструкция этих уст-
ройств включает кулачковые или рычажные механизмы, которые согласуют упругую характеристику пружины с характеристикой уравновешиваемого веса звеньев.
157

|
На рис. 5.3 показана такая |
||||
|
схема |
уравновешивания |
звеньев. |
||
|
Здесь обозначены: S21 – перемеще- |
||||
|
ние звена 2 относительно звена 1; |
||||
|
S32 – перемещение звена 3 относи- |
||||
|
тельно звена 2; 10 – угол поворота |
||||
|
звена |
1 относительно |
стойки. |
||
|
В промышленном |
роботе, |
имею- |
||
Рис. 5.3. Уравновешивание звеньев |
щем такую схему, |
привод верти- |
|||
кального перемещения руки снаб- |
|||||
манипулятора пружинными разгружателями: |
|||||
0, 1, 2, 3 – звенья манипулятора |
жен механизмом для силовой раз- |
грузки, состоящим из пружины и кулачкового механизма с профилем, выполненным по спирали Архимеда.
158

6. ОПРЕДЕЛЕНИЕ ТОЧНОСТИ СРАБАТЫВАНИЯ МАНИПУЛЯТОРА
Точность манипуляторов определяется погрешностями позиционирования характеристической точки схвата (точки М) и погрешностями угловой ориентации схвата. Погрешности позиционирования определяются технологическими отклонениями размеров звеньев манипулятора, зазорами в кинематических па-
рах манипулятора и |
механизмов |
|
||
приводов, деформациями (упругими |
|
|||
и температурными) звеньев, а также |
|
|||
погрешностями системы |
управле- |
|
||
ния и датчиков обратной связи. В |
|
|||
результате |
погрешностей |
точка М |
|
|
описывает |
в пространстве |
некото- |
|
|
рый эллипсоид, который называется |
|
|||
эллипсоидом отклонений (рис. 6.1). |
|
|||
В паспортных данных манипу- |
Рис. 6.1. Эллипсоид отклонений выходного |
|||
ляторов указывается |
максимально |
звена манипулятора: 0, 1, 2, 3 – звенья |
допустимое отклонение центра схвата манипулятора (точки М) от его номинального расположения на множестве возможных конфигураций механизма.
Информацию о точности срабатывания манипулятора получают с помощью сенсорной системы робота. Сенсорные системы разных роботов различаются по своему устройству (число установленных датчиков и дискретность пространственного их расположения, схема размещения элементарных датчиков в сенсоре, место сенсора в робототехнической системе). Организация сенсорной системы влияет на алгоритмы обработки информации, получаемой от датчиков, и, следовательно, на время вычисления параметров, необходимых для полного определения исходной программы движений, а также на погрешность позиционирования робота.
6.1. Сенсорные устройства роботов
Под сенсорными устройствами робота будем понимать чувствительные устройства, предназначенные для получения оперативной информации о состоянии внешней среды в адаптивных системах управления роботами. В отдельных системах робота имеются различные чувствительные устройства, не-
159
обходимые для функционирования этих систем, например датчики обратной связи в приводах, во вторичных источниках питания и т. п. Однако эти чувствительные устройства, ориентированные на внутренние параметры отдельных составных частей робота, не специфичны для него в целом и поэтому не отнесены нами к сенсорным устройствам роботов, как таковым. Сенсорные устройства (датчики) различаются по измеряемым параметрам, по принципам действия, по структуре построения, по характеру изменения выходного сигнала, по принципам считывания сигналов.
По виду выявляемых свойств внешней среды сенсорные устройства роботов делятся на три группы:
1)устройства, служащие для определения геометрических параметров объектов;
2)устройства, выявляющие другие физические свойства объектов;
3)устройства, определяющие химические свойства объектов.
Характерными представителями сенсорных устройств первой группы являются измерители координат (информационные линейки, сканирующие локаторы, координаторы и т. п.). Вторая группа сенсорных устройств (для определения физических свойств объектов) наиболее велика и разнообразна. Здесь в первую очередь следует выделить измерители усилий, плотности, упругости, температуры, оптической прозрачности. В третью группу входят измерительные устройства для установления химического состава и химических свойств среды.
Информация от сенсорных устройств используется в системе управления робота для обнаружения и распознавания объектов внешней среды, а также для управления движением робота и его манипуляторов. В соответствии с этим сенсорные устройства можно разделить по назначению на три группы: устройства, предназначенные для определения свойств среды, выявления объектов в рабочей зоне и датчики обеспечения перемещений исполнительных органов робота.
К первой и второй группам относят чувствительные устройства, предназначенные для выявления различных физико-химических свойств объектов среды, включая, в частности, датчики параметров рельефа в рабочей зоне, специальных признаков для обнаружения и распознавания определенных объектов.
В третью группу входят всевозможные датчики положения и ориентации объектов в рабочей зоне относительно робота, датчики усилий, возникающих при взаимодействии робота с внешней средой, датчики прикосновения, проскальзывания и т. д.
160