
Промышленные роботы Ч. 2 учебное пособие
.pdfМеханизм, показанный на рис. 4.1, состоит из трех подвижных звеньев и трех кинематических пар: двух трехподвижных сферических А3сф и С3сф и одной одноподвижной вращательной В1в.
Для каждой кинематической пары манипулятора указываются: имя или обозначение КП (заглавная буква латинского алфавита A,B,C и т.д.); звенья, которые образуют пару (0/1,1/2 и т.п.); относительное движение звеньев в паре (для одноподвижных пар вращательное, поступательное и винтовое); подвижность КП (для низших пар от 1 до 3, для высших пар от 4 до 5); ось ориентации КП относительно осей базовой или локальной систем координат.
Рабочее пространство манипулятора – часть пространства, соответ-
ствующая множеству возможных положений его звеньев.
Зона обслуживания манипулятора – часть пространства, соответствующая множеству возможных положений центра схвата манипулятора. Зона обслуживания является важной характеристикой манипулятора. Она определяется структурой и системой координат руки манипулятора, а также конструктивными ограничениями, наложенными на относительные перемещения звеньев в КП.
Подвижность манипулятора W – число независимых обобщенных координат, однозначно определяющее положение схвата в пространстве.
Она вычисляется по формуле Малышева:
5 |
|
W 6n (6 i) pi |
(4.1) |
i 1
или для незамкнутых кинематических цепей по формуле
W 5 |
i p i , |
(4.2) |
i 1 |
|
|
где n – число подвижных звеньев, рi – число одноподвижных пар. Маневренность манипулятора М – подвижность манипулятора при за-
фиксированном (неподвижном) схвате:
M W 6. |
(4.3) |
Угол сервиса – телесный угол, на который может повернуться последнее звено манипулятора (звено, на котором закреплен схват) при фиксации центра схвата в заданной точке зоны обслуживания. Он дает возможность изменять ориентацию схвата. Угол сервиса
ψ f |
C |
/ l2 |
, |
(4.4) |
|
СМ |
|
|
где fC – площадь сферической поверхности, описываемая точкой С звена 3, lCM – длина звена 3.
91

Относительная величина k = / (4 ) называется коэффициентом сервиса. Для манипулятора, изображенного на рис. 4.2,
– подвижность
W = 6 3 – (3 2 – 5 1) = 18 – 11 = 7;
– маневренность
M = 7 – 6 = 1;
– формула строения
W = [ 10 + 10 + 10 ] + 21 + [ 32 + 32 + 32 ].
Рис. 4.2. Структурная цепь манипулятора
Структура кинематической цепи манипулятора должна обеспечивать требуемое перемещение объекта в пространстве с заданной ориентацией. Для этого необходимо, чтобы схват манипулятора имел возможность выполнять движения минимум по шести координатам: трем линейным и трем угловым. Рассмотрим для примера шестиподвижный манипулятор с вращательными кинематическими парами (рис. 4.3). На объекте манипулирования имеется точка М, которая совпадает с центром схвата. Положение объекта в неподвижной (базовой) системе координат x0y0z0 определяется радиусом-вектором точки М и ориентацией единичного вектора A с началом в этой точке. Положение точки
впространстве задается в одной из трех систем координат:
–прямоугольной декартовой с координатами xM, yM, zM;
–цилиндрической с координатами rsM, M, zM;
–сферической с координатами rM, M, θM.
92

Ориентация объекта в пространстве задается углами , и , которые вектор ориентации A образует с осями базовой системы координат.
Рис. 4.3. Схема шестиподвижного манипулятора
При структурном синтезе механизма манипулятора необходимо учитывать следующее:
1.Кинематические пары манипуляторов снабжаются приводами, включающими двигатели и тормозные устройства, поэтому в схемах манипуляторов обычно используются одноподвижные кинематические пары – вращательные или поступательные.
2.Необходимо обеспечить не только заданную подвижность схвата манипулятора, но и такую ориентацию осей кинематических пар, которая обеспечивала бы необходимую форму зоны обслуживания, а также простоту и удобство программирования движений манипулятора.
3.При выборе ориентации кинематических пар необходимо учитывать расположение приводов (на основании или на подвижных звеньях), а также способ уравновешивания веса звеньев.
При выполнении первого условия кинематические пары с несколькими степенями подвижности заменяют эквивалентными кинематическими соединениями. Пример такого соединения для сферической пары показан на рис. 4.4.
Перемещение схвата в пространстве можно обеспечить, если ориентировать оси первых трех кинематических пар по осям одной из систем координат.
93
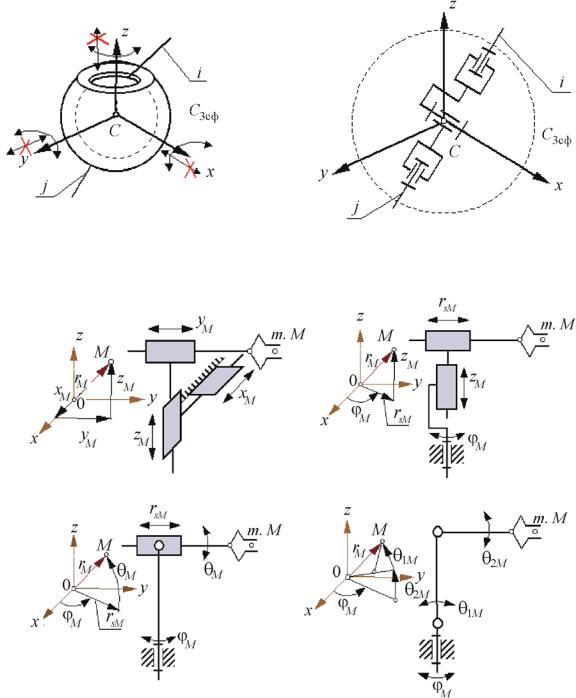
При этом выбор системы координат определяет тип руки манипулятора и вид его зоны обслуживания. По ГОСТ 25685–83 определены виды систем координат для руки манипулятора (рис. 4.5). Здесь даны примеры структурных схем механизмов, соответствующих системам координат. Структурные схемы механизмов кисти, применяемых в манипуляторах, показаны на рис. 4.6. Присоединяя к выходному звену руки тот или иной механизм кисти, можно получить большинство известных структурных схем манипуляторов, которые применяются в реальных промышленных роботах.
а |
б |
Рис. 4.4. Сферическая кинематическая пара (а) и эквивалентное ей кинематическое соединение (б)
а |
б |
в |
г |
Рис. 4.5. Системы координат руки манипулятора: а – прямоугольная (декартова); б – цилиндрическая; в – сферическая; г – угловая (ангулярная)
94

Рис. 4.6. Структурные схемы кисти манипулятора
Структура манипулятора определяется и местом размещения приводов. Если приводы размещаются непосредственно в кинематических парах, то
кмассам подвижных звеньев манипулятора добавляются массы приводов. Суммарная нагрузка на приводы и их мощность увеличиваются, а отношение массы манипулятора к полезной нагрузке (максимальной массе объекта манипулирования) уменьшается. Поэтому при проектировании роботов приводы звеньев руки, как наиболее мощные и обладающие большей массой, стремятся разместить ближе к основанию робота. Для передачи движения от привода
кзвену используются дополнительные кинематические цепи.
Рассмотрим, например, схему руки манипулятора ПР фирмы ASEA (рис. 4.7). Ктрехзвенномумеханизму сангулярнойсистемойкоординатдобавлены:
–для привода звена 2 – простейший кулисныймеханизм, образованныйзвеньями
4, 5 и2;
–для привода звена 3 – цепь, состоящая из кулисного механизма (звенья 6, 7
и8) ишарнирного четырехзвенника (звенья8, 9, 2 и3).
Таким образом, в рычажном механизме можно выделить кинематическую цепь руки (звенья 1, 2 и 3) и кинематиче-
ские цепи приводов. |
|
Манипуляторы, у которых приводы |
Рис. 4.7 Кинематическая цепь |
размещены на основании, имеют более |
руки манипулятора ПР фирмы ASEA |
сложные механизмы. Однако увеличение числа звеньев и кинематических пар компенсируется уменьшением масс и моментов инерции, подвижных звеньев
95

манипулятора. Кроме того, замкнутые кинематические цепи повышают точность и жесткость механизма. По сравнению с рассмотренными манипуляторами в целом лучшими энергетическими и динамическими характеристиками, а также более высокой точностью обладают манипуляторы с комбинированным размещением приводов (часть приводов на осно-
вании, часть на подвижных звеньях).
В кинематических схемах этих манипуляторов веса звеньев вызывают дополнительную нагрузку на приводы. Фирма SKILAM разработала робот SANCIO (рис. 4.8), в котором веса приводов и звеньев воспринимаются кинематическими парами и влияют на момент двигателей только через силы трения. Такая структурная схема механизма потребовала увеличения размеров кинематиче-
ских пар, однако в целом был получен существенный выигрыш по энергетическим и динамическим показателям.
Данные примеры не охватывают всех возможных ситуаций рационального выбора структуры манипуляторов. Они только демонстрируют наиболее известные из удачных структурных схем.
Важная особенность манипуляторов – изменение структуры механизма в процессе работы. В соответствии с циклограммой или программой работы робота в некоторых кинематических парах включаются тормозные устройства. При этом два звена механизма жестко соединяются с друг другом, образуя одно звено. Из структурной схемы механизма исключается одна кинематическая пара и одно звено, число подвижностей схвата механизма уменьшается (обычно на единицу). Изменяется структура механизма и в тех случаях, когда в процессе выполнения рабочих операций (например, при сборке или сварке) схват с объектом манипулирования соприкасается с окружающими предметами, образуя с ними кинематические пары. Кинематическая цепь механизма замыкается, а число подвижностей уменьшается. В этом случае в цепи могут возникать избыточные связи. Эти структурные особенности манипуляторов необходимо учитывать при программировании работы промышленного робота.
Быстродействие ПР определяют максимальной скоростью V линейных перемещений центра схвата манипулятора. Различают ПР с малым (V < 0,5 м/с), средним (0,5 < V < 1,0 м/с) и высоким (V > 1,0 м/с) быстродействием. Совре-
96

менные ПР имеют в основном среднее быстродействие, и только около 20 % – высокое. Схема программы расчета быстродействия робота приведена в прил. 1 (рис. П. 1.3).
Точность манипулятора ПР характеризуется абсолютной линейной погрешностью r позиционирования центра схвата. Промышленные роботы делятся на группы с малой ( r < 1 мм), средней (0,1 мм < r < 1 мм) и высокой ( r < 0,1 мм) точностью позиционирования.
На рис. 4.9 показана типовая конструкция манипулятора с ручным управлением для выполнения погрузоразгрузочных операций. В большинстве случаев такие манипуляторы имеют угловую систему координат, т. е. шарнирную кинематику. В этих сбалансированных манипуляторах осуществляется автоматическое уравновешивание (балансировка) груза аналогично тому, как это часто делается и в манипуляторах роботов. Благодаря этому оператор с помощью рукоятки, укрепленной у захватного устройства манипулятора, без затраты
усилий может перемещать взятый груз |
Рис. 4.9. Электромеханический сбаланси- |
в рабочей зоне манипулятора. |
рованный манипулятор ШБМ-50 |
Рассмотрим устройство сбалансированных манипуляторов на примере отечественного шарнирно-балансирного манипулятора модели ШБМ-150 грузоподъемностью 150 кг (см. рис. 4.9). На колонке 1 поворотного устройства 2 расположена приводная головка 3 с электроприводом поворота в вертикальной плоскости звена 4. Звено 4 включает пантограф, который обеспечивает сохранение вертикального положения звена 5 при поворотах звена 4. На конце звена 5 установлены поворотная головка 6 с рукояткой управления 7, зажим 8 и закрепленное в нем сменное захватное устройство 9.
Сама рычажная система манипулятора сбалансирована с использованием пружинного устройства, расположенного в приводной головке 3. Оператор
97
управляет манипулятором с помощью рукоятки 7. При ее повороте вверх привод перемещает захватное устройство вверх, а при повороте вниз – соответственно вниз. Скорость перемещения при этом пропорциональна углу поворота рукоятки. При нейтральном положении рукоятки груз останавливается и удерживается в этом положении. В горизонтальной плоскости манипулятор перемещается за счет мускульной силы оператора. Однако усилие здесь требуется небольшое – только на преодоление сил трения и инерции. Сбалансированные манипуляторы проще и дешевле роботов, их легче внедрить в производство. Хотя они не высвобождают рабочих подобно роботам, но позволяют ликвидировать тяжелый ручной труд. Применение сбалансированных манипуляторов оправданно там, где по каким-то причинам невозможно или пока затруднительно использовать роботы.
Грузоподъемность выпускаемых сбалансированных манипуляторов – до 2500 кг. Наиболее тяжелые (грузоподъемностью свыше 250 кг) имеют гидравлический привод. При грузоподъемности 100–250 кг используют электропривод, при меньшей грузоподъемности (до 150 кг) сбалансированные манипуляторы снабжают обычно пневматическими приводами.
Одним из перспективных направлений развития сбалансированных манипуляторов является применение автоматизированного управления на базе микропроцессорной техники в виде супервизорного управления.
Исполнительное устройство – это устройство, выполняющее все двигательные функции манипуляционного механизма.
Рабочий орган – составная часть исполнительного устройства для выполнения технологических операций или вспомогательных переходов.
Рабочие органы манипуляторов служат для непосредственного взаимодействия с объектами внешней среды и делятся на захватные устройства и специальный инструмент. Рабочие органы могут быть снабжены средствами очувствления (сенсорными устройствами).
Захватное устройство предназначено для того, чтобы взять объект, удерживать его в процессе манипулирования и отпустить по окончании этого процесса. Существуют следующие основные типы захватных устройств: механические устройства (схваты), пневматические и электромагнитные. Кроме того, в связи большим разнообразием объектов манипулирования разработано большое количество различных комбинаций этих типов захватных устройств
98

имножество специальных захватных устройств с различными оригинальными принципами действия (например, клейкие захватные устройства, накалывающие, использующие аэродинамическую подъемную силу и т. п.).
Схваты – это аналог кисти руки человека. Самые простые двухпальцевые схваты напоминают обычные плоскогубцы, снабженные вводом. На рис. 4.10 показана конструкция подобного схвата с пневмоприводом. В зависимости от объектов манипулирования применяют схваты с тремя, четырьмя и значительно реже с большим числом пальцев. В сложном схвате с тремя пальцами каждый из них имеет три подвижных звена и может поворачиваться также относительно продольной оси. В связи с простотой совершаемых схватами движений (зажим – разжим) в них широко используются нерегулируемые пневматические
иэлектрические приводы, значительно реже гидравлические. На рис. 4.11 показано устройство пневматического схвата с пятью гибкими надувными пальцами. За счет разной жесткости пальцев по сечению при подаче в них сжатого воздуха они изгибаются, захватывая находящиеся в их зоне предметы.
Рис. 4.10. Двухпальцевый схват: 1, 2 – пальцы |
Рис. 4.11. Пневматический схват с пятью |
(губки); 3, 4 – рычажная передача, 5 – шток |
гибкими надувными пальцами: а – внеш- |
пневматического двигателя (пневмоцилинд- |
ний вид; б – разрезы пальца: 1 – тонкостен- |
ра); 6 – возвратная пружина |
ная часть; 2 – гофры; 3 – толстостенная |
|
часть; 4 – подводвоздуха; 5 – деформации |
|
оси пальца при подаче сжатого воздуха |
Схваты очувствляют с помощью контактных датчиков, тактильных датчиков, датчиков проскальзывания, усилия (по одной или нескольким осям) и дистанционных датчиков (ультразвуковых, оптических и др.), выявляющих предметы снаружи, вблизи схвата и между его пальцами.
В наиболее распространенном типе вакуумного захватного устройства
использованы широко известные вакуумные присоски, которые удерживают
99
объекты за счет разрежения воздуха при его отсосе из полости между присоской и захватываемым объектом. Для захватывания объектов сложной формы применяют вакуумные захватные устройства с несколькими присосками.
Магнитные захватные устройства также давно известны в технике
ишироко используются для взятия ферромагнитных объектов. В роботах нашли применение в основном захватные устройства с электромагнитами, но имеются устройства и с постоянными магнитами. Для освобождения захваченного предмета их обычно снабжают специальными механическими выталкивателями.
Захватные устройства часто присоединяют к последнему звену манипулятора через промежуточные податливые конструктивные элементы. С их помощью осуществляется компенсация возможных неточностей позиционирования
иустраняются возникающие при этом механические перенапряжения в звеньях манипулятора в случаях манипулирования объектами, на перемещение которых наложены механические ограничения (механическая сборка и разборка, установка заготовок в зажимы и гнезда технологического оборудования и снятие их, перемещение предмета по направляющим и т.п.).
Рабочий инструмент. В тех случаях, когда объектом манипулирования является рабочий инструмент, с помощью которого робот выполняет соответствующие технологические операции (нанесение покрытий, сварку, завинчивание болтов или гаек, зачистку поверхностей и т. д.), этот инструмент, как правило, не берется захватным устройством, а непосредственно крепится к манипулятору вместо него. Часто при этом к инструменту необходимо обеспечить подвод энергии или какого-либо рабочего тела: для окрасочного робота – краски и воздуха к пульверизатору, для сварочного робота – сварочного тока к сварочным клещам при точечной сварке или проволочного электрода, газа и охлаждающей воды при дуговой сварке и т. д. Для этого требуется разработка специальной конструкции всего манипулятора.
4.2.Задачи механики кинематической цепи манипулятора
К основным задачам механики манипуляторов можно отнести:
–разработку методов анализа и синтеза исполнительных механизмов (включая механизмы приводов);
–программирование движения манипулятора;
–расчет управляющих усилий и реакций в КП;
100