
Промышленные роботы Ч. 2 учебное пособие
.pdf
При чистовой обработке рабочий подносит обрабатываемую деталь к абразивному инструменту, который стачивает острые края и шероховатости на поверхности изделия. Данная процедура занимает важное место в технологическом процессе, однако выполнять ее вручную весьма непросто.
Возможности использования роботов для окончательной обработки изделий исследовались во многих странах. Основная трудность здесь состоит в том, что роботы не обладают естественной для человека способностью контролировать качество своей работы, робот не может менять последовательность своих действий, если он не снабжен соответствующими датчиками. Поэтому одна английская фирма, специализирующаяся на изготовлении соединительных элементов водопроводных труб, осуществила проект, который позволил оснастить робот простейшей системой «машинного» зрения в виде телевизионной камеры. Предположим, робот держит латунный водопроводный кран; телекамера передает изображение крана компьютеру, который, в свою очередь, регулирует прижатие шлифовального ремня, стачивающего неровности на поверхности этой литой детали. Кроме того, компьютер управляет перемещением манипулятора робота. Таким образом, действия всех компонентов системы (телекамеры, основного манипулятора, регулирующего прижатие шлифовального ремня) взаимно скоординированы.
Очистка оборудования. Роботы используются также для очистки оборудования от загрязнений различного происхождения.
Например, инновационные технологии датской фирмы Danduct Clean позволяют проводить работы по инспекции, очистке и дезинфекции систем вентиляции с высоким качеством в короткие сроки.
С помощью специальных управляемых роботов происходит визуальный осмотр всех частей воздуховодов, что позволяет понять их реальное состояние, а также определить причины возникновения возможных проблем при эксплуатации систем вентиляции (рис. 2.21). Для удаления из воздуховодов счищаемых отложений пыли
применяются мощные фильтровентиляционные агрегаты с установленными в них фильтрами HEPA. Для очистки от жировых отложений вентиляционных систем, кухонных зонтов и другого оборудования используется технология
31
бластинга гранулами сухого льда. Процесс очистки жировых отложений сухим льдом идентичен пескоструйному процессу очистки, при котором вещества ускоряются в струе сжатого воздуха для воздействия на очищаемую поверхность. Особенность очистки сухим льдом – сублимация (испарение) гранул сухого льда при соударении с поверхностью.
Сборка. Большой объем работ на современных предприятиях приходится на сборочные операции, однако многие из них требуют особого мастерства и слишком сложны для машины. В связи с этим значительная часть сборки до сих пор выполняется вручную. Тем не менее ряд сборочных процессов уже автоматизирован; это, главным образом, относительно простые и многократно повторяющиеся операции.
На примере фирмы IBM можно проследить, как проходили эксперименты по применению роботов в сборочных процессах. Эта крупнейшая фирма по производству компьютеров не только продает роботы, предназначенные для сборки, но и использует их на собственных предприятиях во многих странах. На заводе этой компании в г. Гриноке (Шотландия) занимаются созданием «островков автоматизации» – комплексов, содержащих большое количество компьютеризированных механизмов, с помощью которых производят сборку изделий при минимальном участии человека. По оценке специалистов фирмы IBM, в результате автоматизации ежегодный объем продукции предприятия вырос в 10 раз по сравнению с 1974 годом, тогда как число работающих на нем осталось практически неизменным.
Один из таких комплексов представляет собой производственную линию, на которой изготавливаются логические блоки с силовыми каскадами. Линия включает процессоры и источники питания для дисплеев, входящих в состав микрокомпьютеров. На линии производится сборка четырех компонентов: двух частей пластмассового корпуса устройства, блока электрических цепей и пластмассовой платы со смонтированным на ней набором микросхем. Для монтажа каждого блока требуется всего два винта, которые подаются в рабочие органы роботов специальными механизмами – питателями. Роботы сами вводят винты в соответствующие отверстия изделия. Для управления всей производственной линией достаточно пяти человек. По данным фирмы IBM, для изготовления такого же количества устройств традиционными методами ручной сборки потребовалось бы вчетверо больше рабочих. В рамках предприятия между системами автоматической сборки, подобными рассмотренной, например, устанавливаются связи с помощью автоматических транспортных средств, которые перемещают изделия, находящиеся на тех или иных стадиях готовности.
На рис. 2.22 приведен пример алгоритма работы исполнительных механизмов сборочного роботизированного комплекса (РТК).
32

|
Сигнал на начало цикла |
|
|
|
|
Перенос и установка контакта |
|
|
|
|
в сборочное приспособление |
|
|
|
|
рукой 1 |
|
|
|
|
Перенос и установка контакта |
|
|
|
|
в сборочное приспособление |
|
|
|
|
рукой 1 |
|
|
|
|
Захват пластины контактной |
|
|
|
|
из механизма перемещения |
|
|
|
|
кассет рукой 2 |
|
|
|
Деталь |
Контроль |
Деталь не |
Сигнал на |
|
поставлена |
поставлена |
|||
правильности |
||||
|
|
останов |
||
|
постановки |
|
||
|
|
|
||
|
Перенос и установка пласти- |
|
|
|
|
ны контактной на два контак- |
|
|
|
|
та рукой 2 |
|
|
|
|
Захват контакта из ВБП |
|
|
|
|
рукой 1 |
|
|
|
Деталь |
Контроль |
Деталь не |
Сигнал на |
|
поставлена |
поставлена |
|||
правильности |
||||
|
|
останов |
||
|
постановки |
|
||
|
|
|
||
|
Переход манипулятора в ис- |
|
|
|
|
ходное положение |
|
|
|
|
Развальцовка |
|
|
|
Приспособление |
Сдув собранного изделия |
|
|
|
|
Приспособление |
|
||
свободно |
Контроль |
занято |
|
|
|
|
|
||
|
свободного приспо- |
|
Сигнал на |
|
|
собления |
|
останов |
|
|
|
|
||
Рис. 2.22. Алгоритм работы сборочного РТК |
|
33
Данный алгоритм показывает, что для внедрения роботов в процесс сборки большое внимание следует уделить оптимизации конструкций обслуживаемых ими изделий. К примеру, конструкция изделия должна предусматривать возможность его «послойной» сборки. Подъема и поворота деталей во время сборки следует избегать, поскольку для этих действий требуются сложные фиксаторы или захваты. Монтируемые компоненты должны быть достаточно податливыми, чтобы их можно было легко сопрягать друг с другом, причем по возможности без применения крепежных элементов (например, винтов), манипуляции которыми сложны для робота. И наконец, детали необходимо проектировать так, чтобы они без затруднений поступали по питателям к рабочим органам роботов. Детали, в частности, не должны иметь ни единого выступа, который, зацепившись, мог бы застопорить из движение к роботам. При конструировании следует уменьшить количество гибких элементов в изделии, например проводников и кабелей, заменив их жесткими компонентами (например, вместо гибкого кабеля использовать миниатюрные платы), которыми робот мог бы без труда оперировать. Следуя этим рекомендациям, можно будет осуществлять с помощью роботов сборку все большего числа промышленных изделий, и роботы-сборщики найдут широкое применение на промышленных предприятиях всего мира.
Монтаж электронных компонентов на печатных платах тоже осуществляется роботами-сборщиками. Некоторые из таких операций могут выполнять специализированные сборочные комплексы, однако, по существу, они представляют собой манипуляторы, рассчитанные на решение строго определенных задач; их нельзя запрограммировать таким образом, чтобы они выполняли какие-то другие операции или манипулировали нестандартными компонентами. Поэтому при использовании подобных установок, предназначенных для узкоспециализированного монтажа, комплекты компонентов стандартной формы загружаются в накопительные желоба многоячеечных магазинов, похожих на патронташ. Эти магазины перемещаются мимо механического захвата, который поочередно извлекает оттуда компоненты и устанавливает их в нужные места на плате.
Различные операции по обработке изделий может выполнять один РТК.
Роботизированный комплекс для обработки изделий. Компания «Но-
киа» разработала для современного производства универсальный РТК, предназначенный для обработки изделий. Робот распознает обрабатываемую деталь с помощью системы кодирования паллеты. Кроме этого, он автоматически выбирает правильную программу обработки деталей. Автоматическая смена инструмента позволяет перевести производство в безлюдный режим. РТК (рис. 2.23)
34

снабжен ограждением, выключающим питание манипулятора в случае входа в рабочую зону человека. Выпуск пыли в окружающую среду исключается отсосом непосредственно с места обработки.
Рис. 2.23. РТК для обработки изделий
В основном РТК обрабатывает детали из пластмассы, легких сплавов, стали, древесины.
РТК может быть оборудован для разных типов производства по специальному заказу. Он способен выполнять следующие операции:
–снятие облоя;
–калибровку резьб М2–М5;
–разметку и сверление отверстий малого диаметра;
–притупление острых кромок;
–сборку;
–смазку;
–пайку;
–контроль;
–испытание;
–полировку;
–нарезание резьб М2–М5;
–упаковку;
–склепку;
–сортировку.
Эксплуатация РТК осуществляется с помощью дисплея, на который выводятся сообщения о нарушениях и инструкции для продолжения работы.
35
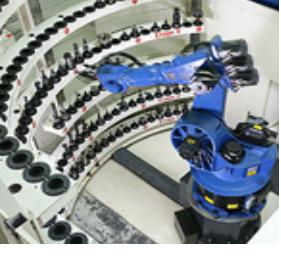
2.3. Роботы для контроля технических объектов
После того как изготовлена деталь или смонтировано несколько узлов, обычно проводится их испытание с целью выявления возможных дефектов. Тщательному контролю подвергаются линейные размеры деталей. Измерительные операции являются частью повседневных задач, решаемых на всех предприятиях мира. Роботы способны облегчить выполнение этих операций
(рис. 2.24). Для этой цели роботы оснащаются миниатюрными оптическими датчиками; как правило, это светодиоды, объединенные с полупроводниковыми светочувствительными приборами. Облучая проверяемую поверхность лучом определенной частоты, подобный датчик принимает отраженное от поверхности излучение, имеющее ту же частоту. Робот в соответст-
вии с заложенной в него программой перемещает датчик от одной точки контролируемого изделия к другой. По результатам измерения интервала времени между моментами испускания светового импульса и его приема после отражения рассчитывается форма проверяемой поверхности. Все действия выполняет компьютер данной автоматизированной системы. Эти операции позволяют избежать использования таких инструментов, как микрометры и штангенциркули.
Подобные робототехнические средства впервые применила компания «Дженерал моторс» для контроля формы и размеров автомобильных деталей. К достоинствам этой системы можно отнести отсутствие необходимости в отправке изделий на специальные пункты контроля качества: соответствующие процедуры можно осуществлять непосредственно на конвейере, не прерывая производственного процесса.
Помимо контроля готовых изделий роботы могут выполнять диагностику различного оборудования.
Вкачествепримерарассмотримработудиагностирующегоробота(Driving Robot). Этот робот предназначен для диагностики автотранспорта, т.е. для поиска и устранения неисправностей в системах управления двигателем, а также в других узлах и агрегатах современных автомобилей.
36
Как известно, нормальная работа участка диагностики возможна только при одновременном наличии измерительной аппаратуры, необходимой информации и специалиста-диагноста. При этом даже при наличии очень серьезной аппаратуры и информационной базы главным диагностическим «инструментом» является квалифицированный специалист. Поскольку найти достаточное количество таких специалистов практически невозможно, то их может заменить диагностирующий робот.
Driving Robot состоит из блоков измерительной техники, отображения, считывания данных (сканер) и центрального компьютера. Данные, полученные от измерительных приборов, передаются на центральный компьютер, где они анализируются, послечеговвидепонятногочеловекутекстаотображаютсянацветномдисплее.
Всвоих решениях Driving Robot опирается на показания датчиков, как предусмотренных конструкцией, так и входящих в комплект устройства: датчиков шумов и вибраций, устанавливаемых на корпуса узлов и агрегатов; газоанализатора и дымомера, устанавливаемых на выхлопную трубу. Эти датчики связаны с головным устройством при помощи инфракрасного порта, что помогает сократить количество проводов. Большая часть стандартных датчиков объединена при помощи общей шины, которая стандартизована для практически всех производителей современных автомобилей, в том числе и для АвтоВАЗа.
Часто возникают проблемы, связанные с двигателем и различными электронными системами, которыми современные автомобили оснащены в изоби-
лии (ABS, ESP и др.).
Впервую очередь, особенно тщательной диагностики требует система управления двигателем (СУД). Техническое состояние этой системы относится
кчислу важнейших факторов, влияющих на тяговые и скоростные показатели автомобиля в целом. Диагностирование технического состояния и ремонт СУД – это наиболее важная и значимая задача Driving Robot.
Как известно, при сгорании топливно-воздушной смеси в цилиндрах двигателя образуются различные химические вещества: СО, NO, CH и др. Анализ процентного содержания каждого из этих соединений в выхлопных газах позволяет судить о рабочих процессах, происходящих в двигателе, и выявлять причины их отклонений от нормы. При помощи газоанализатора (встроенный программно-управляемый прибор для исследования отработавших газов бензиновых двигателей) и дымомера (встроенная модульно-сконструированная измерительная система, с помощью которой можно измерять эмиссию дыма на автомобилях с дизельным двигателем) можно дополнить картину технического состояния двигателя.
37

Начало
Вкл. тестер
Проверка параметров
Параметры
соответствуют
норме
Проверка рулевого управления
Система работает нормально
Проверка систем ABS,ASR,DSC
Система работает нормально
Проверка систем ABC, DSA
Система работает нормально
Проверка датчиков
Система работает нормально
Вкл. двигатель
Двигатель работает
Вывод неисправности
Вывод
неисправности
Вывод
неисправности
Вывод неисправности
Вывод
неисправности
Выкл. двигатель
Выкл. тестер
Проверка исправности аккумулятора, цепей зажигания, проверка количества топлива и масла и т.д.
Вывод
неисправности
Рис. 2.25. Алгоритм работы диагностирующего робота
38
Еще одной важной частью блока тестирования двигателя является сканер – прибор, считывающий показания датчиков автомобиля и стандартные сообщения об ошибках, генерируемые блоком управления автомобиля (бортовым компьютером) в режиме самодиагностики. Сканер позволяет испытывать датчики
иисполнительные устройства в режиме реального времени, программировать сам блок управления, а также проверять не только СУД, но и другие системы автомобиля: ABS, климат-контроль, управление АКП и т.д. Алгоритм диагностики показан на рис. 2.25.
Данный алгоритм работает при любом состоянии систем автомобиля. С его помощью можно определить характеристики двигателя, тормозной системы, системы подвески, системы зажигания, трансмиссии и системы рулевого управления, сравнить их с нормой и вывести отчет об исправности систем
имеханизмов автомобиля на монитор. Автоматизация процесса автодиагностики значительно сокращает время на осмотр каждого автомобиля, а также повышает точность результатов.
Driving Robot используется как автономный диагностический комплекс
иприменяется как стационарно, так и мобильно, т.е. при необходимости может быть доставлен на место поломки автомобиля. Этот универсальный диагностический комплекс можно применять с целью диагностики автомобиля перед его покупкой, что даст покупателю уверенность в том, что он приобретает качественный, настроенный, диагностированный автомобиль.
2.4.Роботы для выполнения технологических операций
встроительстве и в горных работах
Строительство является крупнейшей отраслью производства. Но, несмотря на это, она наименее всего автоматизирована. Большинство видов земляных работ до сих пор производятся по технологиям прошлого века. Тем не менее современные программно-аппаратные средства, позволяющие автоматизировать строительную технику, уже существуют.
Системы управления автогрейдерами представляют собой универсальный инструмент, объединяющий возможности контроля отвала по высоте и поперечному уклону. Это обеспечивает профилирование дорожного покрытия и подготовку сложных поверхностей в автоматическом режиме. Модульность систем управления автогрейдерами позволяет подобрать оптимальный комплект и впоследствии его модернизироватьдлявыполненияопределенноговидаработ(рис. 2.26).
39

По способу задания проекта на местности системы управления подразделяются на 2D и 3D.
Использование системы 2D требует закрепления на местности проектных направлений и отметок. Для этого используются монтажные струны, фиксирующие направление работ и копирующие положение проектного профиля, или лазерные построители плоскости, создающие на объекте ров-
ные опорные поверхности, горизонтальные или с уклонами по двум направлениям.
Грейдер, оснащенный системой 3D, может свободно перемещаться по всему рабочему объекту, автоматически создавая проектную поверхность на местности с точностью 1–2 см в плане и по высоте с выдержкой проектных уклонов. При этом работа может выполняться в любое время суток. В настоящий момент компанией TOPCON предлагаются два типа систем 3D: 3D LPS и 3D GPS, использующих в качестве основных измерительных средств соответственно роботизированные электронные тахеометры GRT-2000 и приемники сигналов спутников GPS+ГЛОНАСС.
Особенности и преимущества системы 3D:
снижение доли инженерных работ;
значительное сокращение количества проходов при подготовке проектной поверхности;
точность выполнения земляных работ 0,5–2 см;
экономия топлива и моторесурса грейдера.
Полностью бесконтактные системы управления асфальтоукладчиками предназначены для выполнения асфальтирования с автоматическим контролем поперечного уклона, ровности и толщины покрытия с точностью ±1,5 мм по высоте. При подготовке ровной поверхности в качестве источника проектных отметок используются лазерные инструменты, способные формировать лазерную плоскость на большом расстоянии от машины. На рабочем органе асфальтоукладчика устанавливается датчик на специальной штанге, постоянно передающий на бортовой компьютер информацию о своем положении относительно лазерной плоскости, связанной с проектом. При обнаружении вертикального смещения датчика вместе с рабочим органом бортовой компьютер подает кор-
40