
Якубенко Технологические процессы производства тепловой 2013
.pdfОтработанный пар из цилиндров низкого давления направляется в конденсаторы К. Из каждого ЦНД пар поступает в свой конденсатор с охлаждающей поверхностью 33160 м2. Расход охлаждающей воды в каждый конденсатор составляет 169800 м3/ч.
Регенеративная система турбоустановки состоит из четырех ступеней ПНД (П-1 – П-4) поверхностного типа, двух деаэраторов Д и двух групп по два ПВД (П-6, П-7 А и Б). Давление пара в деаэраторах при номинальной нагрузке составляет 0,6 МПа. Для повышения экономичности конденсат греющего пара из ПНД-1 и ПНД-3 закачивается дренажными насосами СН ПНД-1 и СН ПНД- 3 в конденсатный тракт.
Питательная вода в ПВД подается двумя турбопитательными насосами БН-1+ПН-1, БН-2+ПН-2, мощностью около 11 МВт каждый. Приводные турбины ТП-1, ТП-2 питаются перегретым паром, отбираемым за СПП, и имеют собственные конденсаторы К.
Цилиндр высокого давления турбины К-1000-60/1500-2 выполнен двухпоточным, симметричным (рис. 5.7). Каждый из потоков включает семь ступеней направляющих и рабочих лопаток.
Ротор высокого давления двухопорный, жесткий, сварнокованый, состоящий из четырех частей. Материал ротора – хромомолибденовая сталь.
На хвостовиках ротора выполнены шейки опорных подшипников диаметром 560 мм, проточки концевых лабиринтовых уплотнений и маслоотбойников. На концевом участке ротора со стороны ЦНД (вторая подшипниковая опора) заодно с валом выполнен гребень упорного подшипника диаметром 950 мм и фланец муфты соединения роторов. Там же расположен гребень датчика осевого сдвига валопровода. Хвостовик стороны регулятора (передний стул, первая подшипниковая опора) выполнен с гребнем для датчика относительного расширения ротора ЦВД. Там же к ротору со стороны регулятора крепится хвостовик с автоматом безопасности и деталями импульсного масляного насоса.
Рабочие лопатки в ступенях ЦВД установлены на дисках с помощью грибовидных хвостовиков. На первых четырех ступенях рабочая часть лопаток постоянного профиля, на остальных – переменного. Рабочие лопатки первой ступени имеют цельно фрезерованную бандажную полку с замыканием на круг с помощью связей типа «ласточкин хвост».
211
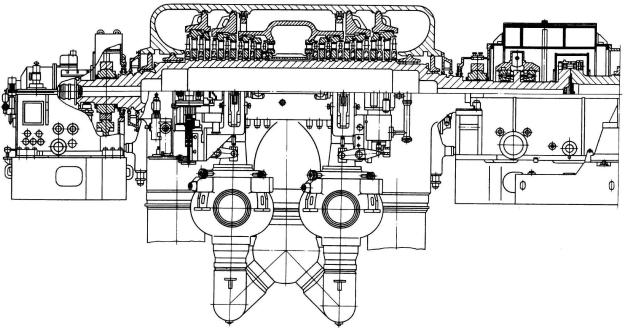
212
Рис. 5.7. Цилиндр высокого давления турбины К-1000-60/1500-2
Рабочие лопатки остальных ступеней имеют накладные приклепанные ленточные бандажи (см. рис. 5.5.). На бандажах всех ступеней проточены с внешней стороны пояски для размещения над ними уплотнительных гребней диафрагм.
Масса облопаченного ротора ЦВД 49280 кг, максимальный диаметр 2220 мм, длина 11035 мм.
Корпус ЦВД выполнен двойным. Внутренний и внешний корпусы выполнены из стали 15Х1М1ФЛ и состоят из двух половин, сболченных между собой по горизонтальному разъему. Внутренний корпус включает в себя по три ступени в каждом потоке. Две пары диафрагм последующих ступеней (в каждом потоке) установлены в обоймы, помещенные в расточках внешнего корпуса. Диафрагмы сварной конструкции, выполненные из нержавеющей стали, соединяются по разъему, а некоторые из них – попарно в осевом направлении. Камеры между внешним и внутренним корпусами используется для отбора пара. Из камеры между обоймами пар отбирается для питания второго ПВД. В нижней половине внешнего корпуса, кроме патрубков отборов пара на регенерацию, выполнены патрубки подвода пара к ЦВД. Наружный корпус ЦВД опирается на приливы подшипников с помощью лап, отлитых заодно с фланцами нижней части корпуса.
Для уменьшения протечек пара и устранения подсосов воздуха
вместах выхода концов ротора из корпуса установлены ступенчатые лабиринтовые уплотнения. Со стороны регулятора и со стороны генератора имеется по две обоймы и по одному корпусу уплотнений, в кольцевых расточках которых установлено по десять уплотнительных колец, которые образуют по три камеры подвода и отсоса уплотняющего пара.
Проточная часть цилиндров низкого давления турбины К-1000- 60/1500-2 состоит из двух симметричных потоков по семь ступеней
вкаждом (рис. 5.8).
Каждый цилиндр низкого давления включает в себя внешний корпус в сборе с выхлопными патрубками, обойму (внутренний корпус), ротор и направляющий аппарат с диафрагмами.
Корпус ЦНД выполнен двухстенным, поскольку давление на входе в цилиндр достаточно высокое – 1,12 МПа. Внутренний корпус содержит по четыре ступени в каждом потоке. Диафрагмы остальных ступеней установлены в наружном корпусе.
213
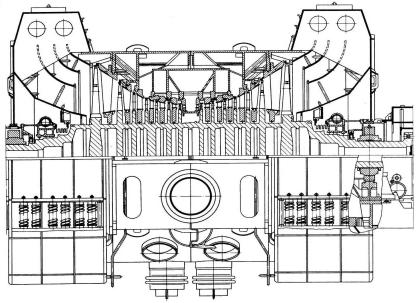
Рис. 5.8. Цилиндр низкого давления турбины К-1000-60/1500-2
Подвод пара в ЦНД – боковой выполнен в нижней половине цилиндра двумя трубопроводами диаметром 1200 мм.
За первой, второй, четвертой и шестой ступенями ЦНД организованы отборы пара на регенерацию и теплофикацию, с которыми отводится значительная часть влаги. Кроме того, диафрагмы двух последних ступеней выполнены с внутриканальной сепарацией влаги.
В местах прохода через внешний корпус ЦНД трубопроводов подвода пара и отборов установлены линзовые компенсаторы, допускающие свободу относительных перемещений внешнего и внутреннего корпусов.
Пар в конденсаторы поступает из ЦНД через переходные патрубки, оборудованные также системой линзовых компенсаторов, благодаря которым корпуса ЦНД имеют возможность независимо от конденсаторов расширяться или сужаться, не воспринимая массы конденсаторов и воды.
Конденсаторы турбины присоединяются к выходным патрубкам соответствующих ЦНД жестко, с помощью сварки; при этом
214
конденсаторы устанавливаются на пружинах, допускающих тепловые расширения каждого переходного патрубка и конденсатора. Для ЦНД турбины К-1000-60/1500-2 только масса воды, заполняющей водяные камеры и трубки конденсатора, составляет почти 600 тонн. Поэтому принята раздельная схема опирания корпуса ЦНД и конденсатора: ЦНД опирается на верхнюю, а конденсатор – на нижнюю фундаментные плиты.
Большие габариты ЦНД (осевой размер 11,38 м, поперечный – 14,86 м) приводят к появлению больших сил, действующих на корпус от атмосферного давления. При этом оказываются многотонные весовые нагрузки на фундамент из-за большой массы сборочных единиц и деталей и нагрузок от перепада давлений.
С целью решения этих проблем в проекте турбины К-1000- 60/1500-2 создана специальная система опирания всех ЦНД на фундамент. Опирание и фиксация ЦНД осуществляются на специальные пружинные опоры выхлопных патрубках.
Каждый ЦНД в сборе опирается на верхнее строение фундамента восемью лапами выхлопных патрубков. Четыре лапы («торцевые лапы») – основные несущие, расположены на торцевых стенках; другие четыре лапы («боковые лапы» или «боковые балконы») – разгрузочные, расположены на боковых стенках выхлопных патрубков. Торцевые лапы крепятся к торцевым стенкам нижних частей выходных патрубков в зоне горизонтального разъема. С их помощью ЦНД опирается на фундаментные рамы, установленные на стенах верхнего строения фундамента турбины. Между торцевыми лапами и рамами имеются разгрузочные устройства пружинного типа, воспринимающие часть вертикальной нагрузки, приложенной к корпусу, и уменьшающие тем самым силы трения на поверхностях опирания. Боковые балконы служат для дополнительного опирания ЦНД через блоки специальных пружин на продольные балки верхнего строения фундамента турбины. Пружины боковых балконов и разгрузочные устройства торцевых лап воспринимают до 85 % массы ЦНД в сборе, и поэтому на опоры торцевых лап действует небольшая часть массовой нагрузки и вертикальная сила от атмосферного давления.
Корпуса подшипников ЦНД выполнены выносными. Они устанавливаются на фундаментные рамы, залитые в поперечные ригели. К корпусам подшипников жестко прикреплены камеры конце-
215
вых уплотнений ЦНД, а герметичность соединений этих камер с торцевыми стенками выходных патрубков обеспечивается установкой сильфонов, не препятствующих взаимному перемещению корпусов подшипников и ЦНД. Таким образом, нагрузка почти в 200 тонн от массы ротора ЦНД воздействует только через корпуса подшипников на поперечные ригели верхнего строения фундамента и не передается на внешний корпус ЦНД.
Роторы ЦНД двухпоточные, двухопорные, жесткие, сварные, изготовленные каждый из четырнадцати кованых заготовок. Концевые части роторов имеют шейки диаметром 800 мм под опорные вкладыши, а также проточки концевых лабиринтовых уплотнений и маслоотбойников. Фланцы полумуфт роторов откованы заодно с хвостовиками.
На рабочих лопатках первых трех ступеней проточная часть выполнена с постоянным профилем, рабочие лопатки с четвертой по седьмую ступень имеют проточую часть переменного профиля. Рабочие лопатки пяти первых ступеней ЦНД имеют в корневой заделке на роторе грибовидные хвостовики, а у двух последних рядов в корневой заделке – елочные хвостовики с торцевой заводкой по дуге окружности.
Все рабочие лопатки ЦНД снабжены бандажами. Лопатки с первой по третью ступень имеют цельнофрезерованные бандажи с демпферными вставками типа «ласточкин хвост». Лопатки четвертой и пятой ступеней имеют накладные (приклепываемые) ленточные бандажи. Лопатки шестой ступени выполнены с цельнофрезерованной бандажной полкой. Лопатки седьмой ступени имеют приклепываемые бандажные полки типа «наездник».
Два последних ряда рабочих лопаток дополнительно имеют по одной демпферной трубчатой бандажной связи. Входные кромки рабочих лопаток шестой и седьмой ступеней закалены токами высокой частоты для уменьшения эрозионного воздействия капель влаги.
В дисках второй, третьей и четвертой ступеней выполнено по пятнадцать пароразгрузочных отверстий диаметром 80 мм.
Масса облопаченного ротора ЦНД составляет 180000 кг. Длина каждого ротора низкого давления составляет 12493 мм.
Несколько большие массу и габариты имеет ротор ЦНД-3 с учетом промежуточного вала и установленного на нем колеса ва-
216
лоповоротного устройства. Масса облопаченного ротора ЦНД-3 в сборе с промежуточным валом и колесом валоповоротного устройства составляет 193000 кг, длина ЦНД-3 в сборе с промежуточным валом – 13593 мм.
Максимальный диаметр роторов ЦНД – 5622 мм. Длина рабочей лопатки последней ступени составляет 1450 мм. По железной дороге ротор транспортируется без лопаток двух последних ступеней. Облопачивание этих двух последних ступеней производится на монтаже.
Пар, поступающий в ЦНД, разделяется на два потока направляющим аппаратом. В каждом потоке ЦНД расположено по семь диафрагм. Диафрагмы ЦНД – сварной конструкции. Тела и обода диафрагм выполнены из углеродистой стали, сопловые (направляющие) лопатки и бандажные ленты – из нержавеющей стали. Все диафрагмы сбалчиваются и разбалчиваются по горизонтальному разъему.
На первых пяти ступенях ЦНД установлены рабочие лопатки с профилем постоянного сечения с удлиненной входной кромкой (чисто активные лопатки). На шестой и седьмой ступенях рабочие лопатки выполнены закрученными с переменной хордой по длине (активно-реактивные лопатки). На этих же ступенях направляющие лопатки выполнены полыми. Через эти полости организована внутриканальная сепарация влаги. На диафрагмах (направляющих лопатках) шестой ступени, со стороны выхода пара, установлены козырьки, прикрепленные к ободьям с зазором. Через этот зазор отводится влага, отсепарированная направляющим аппаратом.
Во всех диафрагмах в пазах центральной расточки установлены уплотнительные кольца лабиринтовых уплотнений из двадцати сегментов каждое.
Обойма ЦНД – сварная, состоит из двух половин, сболченных между собой по горизонтальному разъему. Она выполнена из проката углеродистой стали, фланец горизонтального разъема – литой. Четырьмя лапами, расположенными у горизонтального разъема, обойма опирается на внутренние опорные площадки внешнего корпуса. В обойме сделана кольцевая полость, в которую подводится пар по двум патрубкам, и кольцевые полости отборов за первой и второй ступенями. Из полостей отборов пар через патрубки в нижней половине обоймы направляется в систему регенерации.
217
На продольных фланцах горизонтального разъема выполнены прорези для уменьшения термических напряжений.
Внешний корпус ЦНД выполнен сварным из проката углеродистой стали и состоит из четырех частей, сболченных между собой по горизонтальному и вертикальному разъемам. Вертикальный разъем выполнен для обеспечения возможности провоза корпуса по железной дороге. К торцевым фланцам корпуса присоединяются выхлопные патрубки.
С помощью приварных патрубков в нижней половине внешнего корпуса ЦНД выполнены отборы за четвертой и шестой ступенями и организован вывод отборов из внутреннего корпуса цилиндров.
Выхлопной патрубок ЦНД выполняет следующие функции: организует и направляет поток пара после последней ступени в переходной патрубок конденсатора, воспринимает и передает на фундамент усилия от вакуумной нагрузки и массы ЦНД.
На турбине К-1000-60/1500-2 ведется постоянный контроль большого количества разнообразных параметров, для чего установлены следующие контрольно-измерительные приборы:
•датчики теплового расширения для определения абсолютного расширения корпусов ЦВД, ЦНД-1, ЦНД-2, ЦНД-3;
•датчики угловой скорости для контроля частоты вращения ротора;
•датчики относительного расширения роторов ЦВД и ЦНД-3;
•датчики контроля вибрации роторов;
•датчики контроля вибрации подшипников;
•датчик сигнализации вращения ротора на валоповоротном устройстве;
•датчики осевого сдвига валопровода;
•датчики контроля прогиба роторов;
•термоэлектрические преобразователи для замера температуры металла: корпусов ЦВД и ЦНД, фланцев ЦВД, трубопроводов пара, стопорно-регулирующих клапанов, выхлопных патрубков ЦНД;
•термоэлектрические преобразователи для замера температуры масла на напорном и сливных маслопроводах упорного и всех опорных подшипников;
•термоэлектрические преобразователи для замера температуры баббита вкладышей всех опорных подшипников и всех сегментных секторов подушек упорного подшипника.
218

5.4. Система промежуточного перегрева пара на турбине К-1000-60/1500-2
С развитием АЭС с водоохлаждаемыми реакторами, в парогенераторах которых вырабатывается насыщенный пар, приобрел особое значение вопрос о влиянии влажности пара на характеристики паротурбинных установок [6, 7, 14, 17 – 19]. Для турбин на насыщенном паре большая часть ступеней работает на влажном паре. Влага может присутствовать в потоке пара в виде тумана, капель или пленок, движущихся по поверхностям подвижных и неподвижных элементов проточной части и срывающихся в виде струй и капель.
Термодинамическим параметром такого двухфазного потока является степень сухости пара
х = 1 – у,
где у – степень влажности.
В свою очередь, в [19] вводится понятие массовой степени влажности ум:
ум = mж/(mж + mп),
где mж и mп – массы соответственно жидкости и пара в рассматриваемом объеме.
Различают также объемную степень влажности:
уо = Vж/(Vж + Vп),
где Vж и Vп – объемные доли фаз.
Влажность пара снижает внутренний относительный КПД цилиндра турбины и вызывает эрозионный износ проточной части.
Влияние влажности на КПД обусловлено неизбежными затратами энергии на разгон и отбрасывание капель влаги, на трение потока пара о капли и о пленки влаги, а также увеличением концевых потерь и тормозящим воздействием ударов капель, срывающихся пленок и т.д.
Внутренний относительный КПД цилиндра турбины при работе на влажном паре определяется по формуле
ηвл =ηпл xcp ,
0 0 100
где ηпл0 – внутренний относительный КПД турбины на перегретом паре; хср – средняя сухость пара в %.
219
Из этого следует, что с увеличением влажности на 1 % происходит снижение ηо на 1 %.
Влияние влажности пара на долговременную надежность турбоагрегата обусловлено интенсификацией процессов коррозии и эрозии. В процессе расширения насыщенного пара в турбине его влажность непрерывно увеличивается и достигает значений, недопустимых по условиям эрозионного износа [19] проточной части ЦНД. В потоке пара образуются капли влаги разных размеров, обладающих различными траекториями и скоростями. На входной кромке профиля лопаток повреждения возникают в виде мелких вмятин и постепенно к середине профиля переходят в нерегулярные шероховатости, оспины, зазубрины с рваными кромками. Процесс эрозии все более развивается по мере увеличения неравномерности геометрических характеристик поверхности. То есть начавшийся процесс эрозии лавинообразно стимулирует его дальнейшее развитие.
Полное устранение или частичное снижение нежелательных последствий влияния влаги в проточной части турбоагрегата возможно активными и пассивными методами.
Среди пассивных методов (не изменяющих содержание влаги в проточной части) наиболее распространено упрочнение поверхностей лопаток, подверженных эрозии, с применением различных способов: местная закалка кромок, хромирование, электроискровая обработка и др.
Совершенно обязательно упрочнение поверхностного слоя лопаток для последних ступеней всех цилиндров турбины.
К числу активных методов защиты от эрозии относятся:
•отсос влаги из проточной части вместе с отборами пара на регенеративный подогрев;
•внутриканальная сепарация – отсоса влаги с поверхностей направляющих лопаток;
•сбор влаги, отбрасываемой центробежными силами в щелях
иканалах;
•использование выносных сепараторов;
•применение промежуточного перегрева.
Эффективность промежуточной сепарации и перегрева пара, как и других способов снижения влажности пара в проточной части, определяется, прежде всего, повышением надежности (умень-
220