
Якубенко Технологические процессы производства тепловой 2013
.pdfТеоретически возможно создание системы регулирования давления первого контура посредством компенсации температурных изменений объема теплоносителя соответствующими подпиткой или продувкой первого контура. Однако жесткие требования, предъявляемые к этой системе регулирования (при изменении средней температуры теплоносителя на 1 °С компенсирующее изменение объема имеет величину порядка 80 л) при реальных переходных режимах работы делают применение такой системы экономически неэффективной и автоколебательной.
По указанным выше причинам на РУ с реакторами типа ВВЭР применяется самостоятельная система компенсации давления (объема) с демпфирующим «элементом» в виде паровой упругой подушки.
Система компенсации объема является составной частью реакторной установки (рис. 4.11.) и предназначена для создания и поддержания давления в первом контуре в стационарных режимах, ограничения отклонений давления в переходных и аварийных режимах.
Параметры системы компенсации давления выбраны такими, чтобы не допускать кипения теплоносителя первого контура, за исключением незначительного местного кипения в активной зоне. Пределы изменения давления составляют при этом 18,0–12,0 МПа.
По критериям безопасности система компенсации давления относится к группе устройств нормальной эксплуатации. В соответствии с классификацией по категориям сейсмостойкости система относится к первой категории.
При проектировании с точки зрения работоспособности системы компенсации объема приняты следующие определяющие режимы:
•с максимальным положительным объемным возмущением –
режим сброса нагрузки энергоблоком со скоростью 200 % Nном за секунду с номинального значения до уровня собственных нужд;
•с максимальным отрицательным объемным возмущением – режим ложного срабатывания аварийной защиты реактора и режим разрыва паропровода второго контура.
При расчете этих режимов учитывались отказы в работе отдельного оборудования реакторной установки.
131
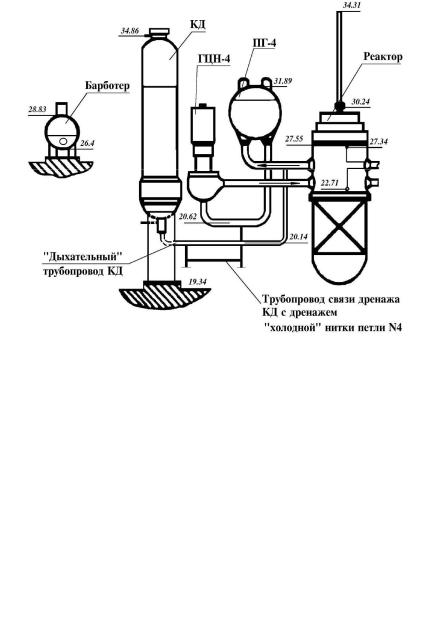
Рис. 4.11. Схема связи системы компенсации объема с ГЦТ
Соотношение водяного и парового объемов КД выбрано из условия, что ни в одном из проектных режимов, за исключением режимов аварийного разуплотнения первого и второго контуров, не должно происходить заброса пара в первый контур из КД и оголения электронагревателей КД.
Система компенсации объема (рис. 4.11) состоит из следующих элементов:
•компенсатора давления;
•”дыхательного” трубопровода, соединяющего нижнюю часть КД с горячей ниткой четвертой петли ГЦК;
•трубопровода впрыска с арматурой, соединяющего паровое пространство КД с холодной ниткой первой петли ГЦК;
•трубопровода сброса парогазовой смеси с предохранительной и контрольной арматурой, соединяющего паровое пространство компенсатора давления с барботером;
•импульсных предохранительных устройств;
132
•барботера;
•системы КИП и А.
Компенсатор давления одновременно является элементом системы обеспечения давления и компенсации объема в первом контуре. Отсюда пошло его двоякое название – в документации он называется как компенсатором давления, так и компенсатором объема.
Компенсатор давления обеспечен тремя линиями впрыска воды из «холодной» нитки первой петли от напора ГЦН, служащей для уменьшения давления первого контура при наличии паровой подушки. Трубопроводы впрысков состоят из труб 219×20, 159×17, 133×14, 18×2,5, регулирующей и запорной арматуры. В случае необходимости повышения давления в первом контуре компенсатор давления обеспечен тремя ступенями электронагревателей.
Водяной объем КД по соединительному «дыхательному» трубопроводу Ду350 сообщается с теплоносителем «горячей» нитки четвертой петли ГЦТ. Во время работы РУ дыхательный трубопровод всегда находится в разогретом состоянии за счет замкнутой циркуляции теплоносителя по следующей схеме: дыхательный трубопровод КД → дренаж КД → дренаж четвертой петли ГЦТ → на всас ГЦН-4 → дыхательный трубопровод КД.
Давление в КД создается паровой подушкой, образующейся в верхней части компенсатора при кипении воды. Кипение достигается за счет тепла электронагревателей, размещенных под уровнем воды в нижней части КД.
При изменении средней температуры теплоносителя первого контура в переходных режимах, связанных с нарушением в работе оборудования и при изменении нагрузки, часть теплоносителя перетекает из компенсатора в контур или из контура в компенсатор по соединительному трубопроводу Ду350. При этом ограничение отклонений давления от номинального значения достигается за счет сжатия или расширения паровой подушки в компенсаторе.
Водяной объем также участвует в процессе компенсации давления: при расширении пара вода в КД испаряется, увеличивая объем паровой подушки и способствуя тем самым поддержанию давления, а при сжатии паровой фазы происходит ее конденсация на поверхности воды, что ограничивает рост давления.
При большом росте давления и поочередном отключении четырех групп электронагревателей через дренчерные сопла, располо-
133
женные в верхней части КД, по линии впрысков подается теплоноситель из «холодной» нитки первой петли ГЦТ для конденсации пара в паровой подушке. В зависимости от переходного процесса подача «холодного» теплоносителя замедляет или совсем прекращает рост давления в первом контуре.
При аварийном росте давления и невозможности остановить его впрыскиванием «холодного» теплоносителя включаются в работу по определенному алгоритму импульсно-предохранительные устройства, сбрасывающие излишки пара из парового объема КД в барботер. Для сброса давления парогазовой смеси из КД в режиме его разогрева (расхолаживания) и при продувке его парового объема предусмотрен трубопровод, соединяющий паровое пространство компенсатора давления с трубопроводом сброса пара за импульснопредохранительными устройствами.
Компенсатор давления (рис. 4.12) представляет собой вертикальный цилиндрический сосуд с эллиптическими днищами, в нижней части которого расположены28 съемных блоков электронагревателей общей мощностью 2520 кВт. Мощность блоков ТЭH выбрана из условияобеспечения проектной скоростиpазогpеваКД пpипуске РУ.
Основные технические характеристики КД приведены в табл. 4.2. Материал обечаек и днищ – низколегированная сталь марки 10ГН2МФА. Внутренняя поверхность КД плакирована нержавеющей сталью.
На верхнем днище КД встроены люк-лаз и штуцеры для подсоединения трубопроводов. Крышка люка-лаза уплотняется двумя прокладками: одной никелевой прямоугольного сечения и одной асбографитовой, и затягивается при помощи шпилек М64. Из полости, образованной этими прокладками, выведен штуцер для подсоединения к трубопроводу линии контроля плотности.
К нижнему днищу КД приварен патрубок с переходом к трубе 426×40 мм, соединяющей компенсатор давления с «горячей» ниткой 4 петли ГЦТ.
Зона электронагревателей выполнена в виде цилиндрической обечайки с двумя рядами отверстий под блоки электронагревателей. Каждый блок ТЭН выполнен из девяти U-образных трубчатых нагревателей (наружный диаметр 13,6 мм), при помощи нержавеющих втулок закрепленных и вваренных в крышку блока.
134
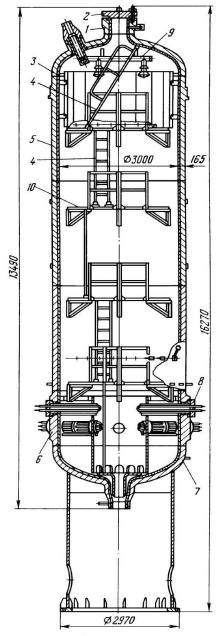
Таблица 4.2
Основные технические характеристики компенсатора давления
Наименование |
Ве- |
параметра |
личи |
Номинальное давление, |
16на |
МПа |
|
Давление гидравлических |
25 |
испытаний на прочность, |
|
МПа |
|
Температура номиналь- |
346 |
ная, °С |
|
Объем полный, м3 |
79 |
Объем воды при номи- |
55 |
нальном режиме, м3 |
|
Объем пара при номи- |
24 |
нальном режиме, м3 |
|
Количество блоков элек- |
28 |
тронагревателей, щт. |
|
Мощность блока ТЭН, |
90 |
кВт |
|
Общая мощность всех |
2520 |
блоков ТЭН, кВт |
|
Высота корпуса КД без |
13235 |
опор, мм |
|
Рис. 4.12. Компенсатор давления: 1 – горловина; 2 – крышка; 3, 7 – днища; 4 –лестница;
5 – обечайки корпуса;
6 – обечайка блоков ТЭН;
8 – блоки ТЭН; 9 – коллектор;
10 – площадка
Каждый блок электронагре-
135
вателей имеет мощность 90 кВт. Для удобства управления и регулирования давления в первом контуре все блоки ТЭН разбиты на четыре группы. Работа четырех групп ТЭН КД компенсирует утечку из паровой части КД до 5 т пара в час.
Электронагреватель представляет собой трубку диаметром 13 мм, выполненную из сплава 08Х18Н10Т, внутри которой помещена спираль из нихромовой проволоки. Пространство между стенками трубы и спиралью заполнено прессованным кристаллическим порошком плавленой окиси магния (периклаз), который хорошо проводит тепло и обладает высоким сопротивлением.
К внутрикорпусным устройствам КД относятся разбрызгивающее устройство, защитный экран, тепловой экран в патрубке нижнего днища, опорная обечайка электронагревателей, лестницы и площадки. Все внутрикорпусные устройства КД выполняются из нержавеющей стали.
Разбрызгивающее устройство предназначено для распыления воды по паровому объему для обеспечения конденсации пара при впрыске и выполнено в виде раздающего коллектора. Коллектор имеет четыре разбрызгивающих насадки и с помощью хомутов крепится к швеллерам, которые приварены к верхнему днищу. Разбрызгивающие насадки крепятся на резьбе к патрубкам раздающего коллектора.
Защитный экран служит для защиты от попадания «холодной» воды от разбрызгивающего устройства на корпус. Он выполнен из съемных листов, свободно висящих на кронштейнах. Опорная обечайка блоков ТЭН предназначена для фиксации их в рабочем (горизонтальном) положении и предохранения от резких поперечных потоков среды при положительных и отрицательных возмущениях по объему первого контура, а также для организации контура естественной циркуляции при работе ТЭН. В верхней части обечайки расположено 28 отверстий с обоймами для установки блоков ТЭН, в нижнем торце обечайки сделаны вырезы для обеспечения дренажа и организации естественной циркуляции.
Опорная обечайка ТЭН в верхней части крепится при помощи болтов к кронштейнам, приваренным к корпусу КД, в нижней части приварена к наплавке на нижнем днище. Крепление обеспечивает температурные перемещение обечайки. КД устанавливается на неподвижную опору. Для восприятия сейсмических нагрузок КД
136
закрепляется в верхней части упорным кольцом, заделанным в бетонное перекрытие. Конструкция этого крепления не препятствует термическому расширению сосуда вверх и по радиусу, удерживает в вертикальном положении и не позволяет смещаться в горизонтальной плоскости при толчках. Снаружи весь КД покрыт теплоизоляцией, состоящей из отдельных съемных блоков. Блоки теплоизоляции состоят из металлического каркаса, матрацев из базальтового волокна толщиной 60 мм в оболочке из кремнеземистой ткани и защитного алюминиевого покрытия.
Импульсно-предохранительные устройства предназначены для сброса пара из КД при превышении давления в первом контуре выше заданного при отказе впрыска или недостаточной его эффективности. Импульсно-предохранительное устройство состоит из главного предохранительного клапана, импульсных клапанов, электротехнических устройств и трубопроводов связи.
Главный предохранительный клапан срабатывает после открытия любого из двух импульсных клапанов. Пар от ГПК КД по сбросному трубопроводу поступает в парораспределяющие коллекторы с соплами под слой воды, которой заполнен барботер.
Барботер (рис. 4.13.) представляет собой горизонтальный цилиндрический сосуд, состоящий из обечайки корпуса и двух эллиптических днищ, заполненный «чистым» конденсатом. Внутри барботера размещены два раздающих коллектора, к которым по трубопроводу Ду 250 подводится пар от ПК КД. По всей длине каждого коллектора предусмотрены сопла, которые способствуют эффективной конденсации пара в объеме холодной воды.
Основные технические характеристики барботера приведены в табл. 4.3.
|
Таблица 4.3 |
|
Основные технические характеристики барботера |
||
|
|
|
Наименование параметра |
Величина |
|
Геометрический объем барботера, м3 |
30 |
|
Объем воды в барботере, м3 |
20 |
|
Давление разрыва мембран, МПа |
0,7÷0,87 |
|
Уровень воды, мм |
1700 |
|
Поверхность охлаждения водяного змеевика, м2 |
35 |
|
137
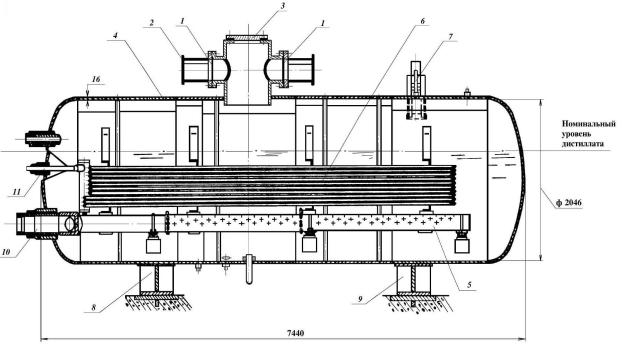
138
Рис. 4.13. Барботер:
1 – резинометаллическая мембрана; 2 – защитный колпак; 3 – люк-лаз; 4 – корпус; 5 – паровой коллектор; 6 – поверхность охлаждения; 7 – уравнительный сосуд; 8 – неподвижная опора; 9 – подвижная опора;, 10 – патрубок
сброса от ГПК КД; 11 – патрубок подачи воды промежуточного контура на охлаждение
Для охлаждения воды внутри барботера установлен теплообменник, состоящий из входного и выходного коллекторов и пучка теплообменных труб, по которым подается вода промежуточного контура. Парораздающие коллекторы и трубы теплообменника на опорах имеют свободные температурные перемещения.
В верхней части барботера расположен люк диаметром 450 мм, на котором установлены две разрывные резинометаллические мембраны, служащие в качестве предохранительных устройств. Для исключения образования взрывоопасной газовой смеси внутри полости барботера производится непрерывная продувка его верхнего газового объема азотом с расходом 1– 2 м3 в час.
Барботер устанавливается на одну неподвижную и одну подвижную опоры, что не препятствует его термическому расширению, и обеспечивает прием пара из КД без разрыва предохранительной мембраны в режимах нормальной эксплуатации и в режимах с нарушениями нормальных условий эксплуатации РУ по сценариям проектных аварий.
Суммарная пропускная способность разрывных предохранительных мембран барботера обеспечивает расход пара, получаемый при открытии всех ИПУ КД.
Система охлаждения барботера обеспечивает его охлаждение до нормальной рабочей температуры стационарного состояния в течение двух часов после окончания переходного процесса.
4.4. Ядерный реактор ВВЭР-1000 на АЭС с реакторной установкой проекта В-320
Реакторная установка В-320 с реактором ВВЭР-1000 (рис. 4.14, 4.15) является составной частью энергоблока АЭС и совместно с турбинной и генераторной установками используется для производства электроэнергии в базовом режиме.
Назначение реакторной установки – выработка сухого насыщенного пара для турбинной установки, где тепловая энергия пара преобразуется в механическую энергию вращения валопровода, а затем в генераторной установке – в электрическую энергию.
Реакторная установка В-320 оснащена модернизированным серийным ядерным реактором ВВЭР-1000 корпусного типа с водой под давлением.
139
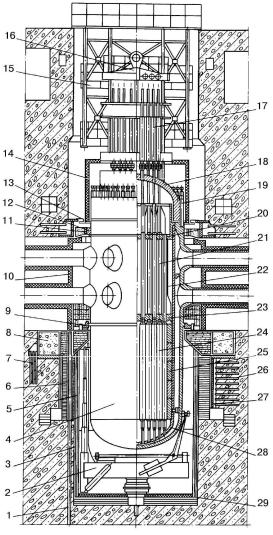
Рис. 4.14. Реактор ВВЭР-1000 в проектном положении:
1 – канал ионизационной камеры; 2 – машина для осмотра корпуса реактора; 3 – нижняя секция теплоизоляции; 4 – корпус реактора;
5 – верхняя секция теплоизоляции; 6 – металлоконструкция
радиационной тепловой защиты; 7 – анкерные связи опорной фермы;
8– опорная ферма;
9– опорное кольцо корпуса реактора;
10– теплоизоляция зоны патрубков;
11– шпонка упорного кольца;
12– упорное кольцо;
13– сильфон;
14– теплоизоляция ВБ;
15– каркас;
16– траверса;
17– привод СУЗ;
18– крышка ВБ;
19– шпилька УГР;
20– верхняя плита БЗТ;
21– защитная труба БЗТ;
22– БЗТ;
23– нижняя плита БЗТ;
24– ТВС;
25– выгородка;
26 – анкерная связь обечайки бокса;
27– обечайка бокса;
28– ШВК;
29– теплоизоляция нижней части
140