
Методическое пособие 700
.pdf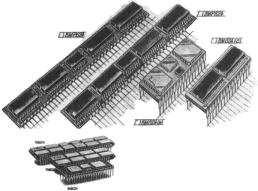
В последние годы начали интенсивно развиваться многокристальные корпуса.
Разрабатывается много видов и форм мно-
гокристальных корпусов (рис. 4.6). Основ-
ные проблемы, которые приходится ре-
шать при разработке этих корпусов, это обеспечение малых задержек сигналов и облегчение теплоотвода от кристаллов.
Этапы развития корпусов для ИС показа-
ны на рис. 4.7, 4.8.
Рис. 4.6. Примеры разнообразия многокристальных корпусов

Рис. 4.7. Многокристальный носитель на кремниевой
или тонкопленочной подложке
По мере перехода от монтажа в сквозные отверстия к монтажу на поверхность плат число выводов растет.
Носитель (рис. 4.7) позволяет обеспечить более высокую плотность размещения межсоединений, чем в случае печатных плат или тонкопленочных гибридных ИС.
Контрольные вопросы
1.Какие требования предъявляются к корпусам ИС?
2.Чем отличаются требования изготовителей корпусов и изготовителей ИС к конструкции ИС?
3.Какие существуют ограничения по пяти группам параметров к корпусам ИС?
4.Как подсчитать необходимое число выводов корпусов для разрабатываемой ИС? Приведите пример.
5.Каковы тенденции развития требований к материалам корпусов?
6.Какая существует классификация корпусов по технологии изготовления и используемым материалам?
7.Какие материалы используются для металлокерамических корпусов?
8.Охарактеризуйте металлостеклянные корпуса.
9.Какие преимущества и недостатки пластмассовых корпусов?
10.Какова конструкция корпусов чашечного типа?
5. ОБЕСПЕЧЕНИЕ НАДЕЖНОСТИ МОНТАЖА
КРИСТАЛЛОВ В КОРПУСА
Опыт показывает, что отказы ППИ обычно связаны с химическими, прочностными и электрическими видами отказов.
Прочностные отказы связаны с монтажом кристаллов в корпуса. Надежность ИС определяется в значительной степени качеством соединения кристалла с подложкой. Внутренние напряжения, возникающие в соединении, нередко приводят к ухудшению качества соединения кристалл
– подложка и повышению теплового сопротивления перехода, а зачастую к катастрофическим отказам из-за появления трещин в кристаллах, связанных с их механической прочностью, после крепления кристалла на основание корпуса. Если для
ИС малой степени интеграции вопрос о разрушении кристалла практически не стоял, то в настоящее время только у потребителей доля отказов ИС средней степени интеграции по этому виду брака составила: на входном контроле – 10,5 изделий, при производственных испытаниях – 0,65 изделий, а для ИС 3 – 5 степени интеграции на входном контроле – 267,2 изделий и при испытаниях РЭА –127,6 изделий на миллион поставленных.
5.1. Наклейка кристаллов
Основные требования, предъявляемые к клеевым соединениям: механическая прочность, высокая адгезионная способность (не менее 2 – 3 МПа) и стабильность электроизоляционных свойств в интервале рабочих температур (удельное объемное сопротивление не менее 1014 Ом·см, tg δ ≤ 10-3). Кроме того, газовыде-

ление клеевого шва в герметизированных |
|
|
h3 – толщина кристалла, клеевой компози- |
|||||||||
объемах при |
температурах эксплуатации |
|
|
ции и дна основания корпуса соответст- |
||||||||
не должно содержать агрессивных компо- |
|
|
венно; α1, α2, α3 – температурные коэффи- |
|||||||||
нентов, вступающих в реакцию с элемен- |
|
|
||||||||||
|
|
циенты линейного расширения материалов |
||||||||||
тами кристалла. |
|
|
|
|
|
|
||||||
|
|
|
|
|
|
кристалла, клеевой композиции и дна ос- |
||||||
|
В процессе наклейки кристаллов ИС |
|
|
|||||||||
|
|
|
|
|
|
|
||||||
|
|
|
нования корпуса соответственно; Т – тем- |
|||||||||
в них возникают |
внутренние |
механиче- |
|
|
||||||||
|
|
пература, |
для |
которой вычисляются на- |
||||||||
ские напряжения. |
Если |
пренебречь |
де- |
|
|
|||||||
|
|
пряжения; |
Тс |
– температура полимериза- |
||||||||
формацией изгиба, возникающей при |
|
|
||||||||||
|
|
|
|
|
|
|||||||
склейке, то оценочная формула для расче- |
|
|
ции клеевой композиции; W – величина |
|||||||||
та напряжений, возникающих в приклеи- |
|
|
усадки клеевой композиции при полиме- |
|||||||||
ваемом элементе, может быть представле- |
|
|
ризации. |
|
|
|||||||
на в виде: |
|
|
|
|
|
|
|
|
Вычисленные по формуле (5.1) на- |
|||
|
|
|
|
|
|
|
|
|
пряжения, возникающие в кристалле ИС |
|||
|
Е1 Е2 h2 |
1 |
2 Tc |
T W E3 h3 |
1 |
3 |
T |
серий 106, 134, равны: ζ = 180,8·106 Н/м2 = |
||||
|
c |
T |
|
|
||||||||
|
|
|
E1h1 |
E2 h2 |
E3 h3 |
|
|
|
180,8 МПа при применении в качестве |
|||
|
|
|
|
|
|
клея ВК-32-200 (Е2 = 2 ГПа, h2 = 100 мкм, |
||||||
, (5.1) |
|
|
|
|
|
|
|
|||||
|
|
|
|
|
|
|
α2 = 20·10-6 1/град) при посадке кристалла |
|||||
где Е1, Е2, Е3 – модули упругости материа- |
|
|
ИС (Е1 = 167 ГПа, h1 = 300 мкм; α1 = 3·10-6 |
|||||||||
|
|
1/град) в корпус 401.14-1 со стеклокерами- |
||||||||||
лов кристалла, клеевой композиции и дна |
|
|
ческим дном (Е3 = 117,6 ГПа, h3 = 600 мкм, |
|||||||||
основания корпуса соответственно; h1, h2, |
|
|
α3 = 20·10-6 1/град). |

Аналогичным образом определено напряжение на кристалле ИС при наклейке в корпус 401.14-4 (с коваровым дном) клеем ВК-32-200 (ζ = 105,9 МПа) и контактолом КВ-3 (ζ = 88,2 МПа). Рассчитанные значения напряжения составляют 46 % для ВК-32-200 и 22 % для КН-3 от предельных значений напряжений при изгибе кристал-
лов ИС серий 106,134 (ζ = 392 МПа).
5.2. Напайка кристаллов
Свойства соединяемых материалов, температурные условия формирования соединений и геометрические размеры определяют внутренние механические напряжения, которые могут приводить к разрушению изделия в местах соединений.
Рассмотрим проблему обеспечения надежного крепления кремниевого кристалла с подложкой из меда. Пусть кристалл, имеющий размеры a a h1, напаи-
вается на подложку толщиной h2. Деформацией внутри контакта можно пренебречь, поскольку h1 и h2 значительно меньше а. Силы и моменты, действующие внутри кристалла, можно рассматривать только в двух плоскостях.
На рис. 5.1 условно показаны силы и моменты, действующие внутри объема соединения, состоящего из металла и кремния. Эти силы и моменты одинаковы относительно осей Х и У вследствие того, что рассматривается элемент квадратной формы. На поверхности контакта действуют силы
dFi Fai dx ,
которые приводят к появлению момента
dM |
|
M i |
dx при i = 1,2. |
i |
|
||
|
a |
||
|
|
С учетом условий, сформулированных ранее,
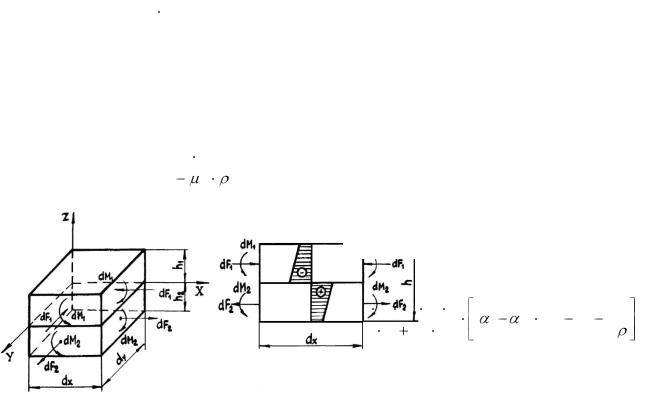
dF1 = dF2 = dF и dF/2 (h1+h2) = dM1 + dM2
.
Окончательная формула для расчета моментов, возникающих в объеме соединения кристалл – подложка, выглядит следующим образом:
Mi= |
Ei |
Ii |
, для i = |
(Ii |
i ) |
||
|
1, 2, |
(5.2) |
а)
б)
Рис. 5.1. Графическое изображение сил и моментов,
действующих внутри объема соединения
где Е – модуль упругости; I – момент инерции для прямоугольного поперечного сечения; μ – коэффициент Пуассона (μ = 0,2 – 0,5); ρ – радиус изгиба.
Усилие F можно определить из выражения:
|
|
|
|
|
|
|
F = |
||
E1 |
h1 |
E2 |
h2 |
a |
( 1 |
2 ) (Tn T ) |
h |
, |
|
E1 |
h1 |
E2 h2 |
2 |
||||||
|
|
|
|||||||
|
|
|
|
|
|
|
(5.3) |

где α1, α2 – термические коэффициенты линейного расширения кремния и подложки соответственно; Tn – температура плавления припоя; Т – рабочая температура; h
– толщина кристалла и подложки, т.е. h =
h1 + h2 .
Радиус изгиба вычисляется по формуле:
|
|
|
|
|
2 h C1 |
|
|
|
|
, |
|
|
(5.4) |
|
|
||||||
|
3 |
( 1 |
|
2 ) (Tn |
T ) |
|
|
|
|
||||||||||||
где |
|
|
|
|
|
|
|
|
|
|
|
|
|
|
|
|
|
|
|
|
|
|
h2 |
|
|
1 |
|
|
|
E |
2 |
h3 |
|
|
|
E |
h |
|
3 |
||||
С |
1 |
|
( |
|
|
|
|
|
|
2 |
|
) (1 |
|
|
1 |
1 |
) |
|
|||
|
|
|
|
|
|
|
|
|
|
|
|
|
|
|
|
|
|
||||
1 |
4 h2 |
1 |
|
(1 |
|
|
) E h3 |
|
|
E |
h |
|
4 |
||||||||
|
1 |
2 |
|
|
|
||||||||||||||||
|
|
|
|
|
|
|
|
|
1 |
1 |
|
|
|
2 |
2 |
|
|
;
Максимальное напряжение сжатия на поверхности контакта при z = 0 определяется формулой:
ζ0макс = – E1(α1 – α2)(Tn – T)C2,
|
|
|
|
|
|
|
|
|
|
|
|
|
|
|
|
|
|
|
|
|
|
|
(5.5) |
|
|
|||
где |
|
|
|
|
|
|
|
|
|
|
|
|
|
|
|
|
|
|
|
|
|
|
|
|
|
|
|
|
|
|
|
h2 |
|
|
1 |
|
|
|
|
|
E |
2 |
|
|
|
h3 |
|
|
3 h |
||||||||
|
|
|
1 |
|
( |
|
|
|
|
|
|
|
|
|
|
2 |
) |
|
|
|
1 |
|
|
|||||
|
|
|
h2 |
|
1 |
1 |
(1 |
|
2 |
) E |
|
|
h3 |
(1 |
1 |
) h |
||||||||||||
|
|
|
|
|
|
|
|
|
||||||||||||||||||||
С2 |
|
|
|
|
|
|
|
|
|
|
|
1 |
1 |
|
|
|
|
|
|
|||||||||
|
h2 |
|
|
1 |
|
|
|
|
|
E |
2 |
|
|
|
|
h3 |
|
|
E |
h |
||||||||
|
|
1 |
|
( |
|
|
|
|
|
|
|
|
|
|
|
|
2 |
) |
(1 |
1 |
|
1 |
) 3 |
|||||
|
|
|
|
|
|
|
|
|
|
|
|
|
|
|
|
|
|
|
|
|
|
|||||||
|
|
h2 |
|
1 1 |
|
|
(1 |
2 ) E1 h13 |
|
|
E2 h2 |
|||||||||||||||||
|
|
2 |
|
|
|
|
|
|
|
|
|
|
|
|
|
|
|
|
|
|
|
|
|
|
|
|
|
;
h = h1 (1 + h2/h1).
h = h1 |
+ h2. |
Напряжения, возникающие на верх- |
|
ней поверхности кристалла, определяются |
|||
|
|
как:

|
ζ1(Z1 = h1) = - E1(α1 – α2)(Tn – T)C3, |
|
териалов h1/h2 для соединения кремний- |
|||||||||||||||||||||||||
|
|
|
|
|
|
|
|
|
|
|
|
|
|
|
|
|
|
|
(5.6) |
|
медь. Минимальное значение радиуса из- |
|||||||
|
|
|
|
|
|
|
|
|
|
|
|
|
|
|
|
|
|
|
|
|
|
|
|
|
гиба получается при отношении h1/h2 = 1. |
|||
где |
|
|
|
|
|
|
|
|
|
|
|
|
|
|
|
|
|
|
|
|
|
|
|
|
|
|
|
|
|
|
|
|
h2 |
|
|
|
|
1 |
|
|
|
|
E |
2 |
|
|
h3 |
|
|
3 h |
|||||||
|
|
1 |
|
|
( |
|
|
|
|
|
|
|
|
|
|
2 |
) |
|
|
1 |
|
|
|
|||||
|
|
|
|
|
|
|
|
|
|
|
|
|
|
|
2 ) E1 h13 |
|
|
|
|
|
|
|||||||
|
|
|
|
h2 |
|
|
1 |
1 |
(1 |
|
|
(1 |
1 ) h |
|||||||||||||||
С3 |
|
2 |
|
|
|
|
|
|
|
|
|
|
|
|
|
|
|
|
|
|
|
|
|
|
|
|
||
|
|
h2 |
|
|
1 |
|
|
|
|
|
E |
2 |
|
|
h3 |
|
|
E |
h |
|||||||||
|
|
|
|
|
|
|
|
|
|
|
|
|
|
|||||||||||||||
|
1 |
|
( |
|
|
|
|
|
|
|
|
|
|
2 |
) |
(1 |
|
1 |
1 |
) |
|
|
||||||
|
|
|
|
|
|
|
|
|
|
|
|
|
|
|
|
|
|
|
|
|
|
|
||||||
|
|
|
h2 |
|
|
1 |
|
1 |
|
(1 |
2 ) E1 h13 |
|
|
E2 h2 |
||||||||||||||
|
2 |
|
|
|
|
|
|
|
|
|
|
|
|
|
|
|
|
|
|
|
|
|
|
|
|
|||
|
|
|
|
|
|
|
|
|
|
. |
|
|
|
|
|
|
|
|
|
|
|
|
|
|
|
|
|
|
Расчеты дают для кристалла из крем- |
|
|
|
|
|
|||||||||||||||||||||||
ния и подложки из меди следующие зна- |
|
|
|
|
|
|||||||||||||||||||||||
чения: ρмакс = 100 мм, ζ1 макс = –350 Н/мм2. |
|
|
|
|
|
|||||||||||||||||||||||
Поскольку допустимое значение величины |
|
|
Рис. 5.2. Зависимость коэффициента С1 от |
|||||||||||||||||||||||||
|
|
|
|
|
|
|
|
|
|
|
|
|
|
|
|
|
|
|
|
|
|
2 |
, |
|
|
|||
напряжения изгиба составляет 250 Н/мм |
|
|
отношения толщин материалов h1/h2 для |
|||||||||||||||||||||||||
в результате повышенного напряжения из- |
|
|
||||||||||||||||||||||||||
|
|
|
|
соединения кремний-медь |
||||||||||||||||||||||||
гиба возникают микротрещины, которые |
|
|
|
|
||||||||||||||||||||||||
|
|
|
|
|
||||||||||||||||||||||||
могут приводить к отказу элемента. |
|
|
|
|
|
|
|
|
|
На рис. 5.3. показана зависимость ко- |
||||||||||||||||||
На рис. 5.2. показана зависимость ко- |
|
|
|
|
||||||||||||||||||||||||
|
эффициентов С2 и С3 от соотношения тол- |
|||||||||||||||||||||||||||
эффициента С1 |
|
от отношения толщины ма- |
|
|||||||||||||||||||||||||
|
|
щин материалов h1/h2 для соединения |
||||||||||||||||||||||||||
|
|
|
|
|
|
|
|
|
|
|
|
|
|
|
|
|
|
|
|
|
|
|
|
|