
Оборудование машиностроительных производств. учебное пособие. Пачевский В.М., Яценко С.Н
.pdf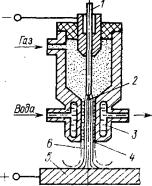
3.8. Плазменная сварка
Плазма значительно ионизированный и нагретый до 6000 - 30000°С газ, смесь нейтральных молекул, электронов и ионов с высокой электропроводностью. Под действием магнитных полей плазма образует поток, которым производится сварка, резка, напыление, термическая обработка металла, стекла, керамики и др. Плазма получается нагревом плазмообразующего газа в дуговом разряде или нагревом в индукторе. Мощность плазмотронов может достигать тысячи киловатт, что превышает потребности. При плазменной дуговой сварке (рис. 3.5) дуга 2 горит между неплавящимся электродом 1 горелки и изделием 5. Канал 4 сопла 3 охлаждается водой. Плазменная струя 6 образуется за счет подаваемого в горелку газа: аргона или его смеси с водородом или гелием, азота, воздуха. При сварке плазменной струёй дуга горит между вольфрамовым электродом и соплом горелки.
Рис. 3.5. Плазменная горелка
Сварка плазменной дугой применяется для коррозионностойкой стали, титана, никелевых сплавов, молибдена, вольфрама и других материалов и по проплавляющему действию стоит между аргонодуговой и электронно-лучевой сваркой. Возможность стабилизировать проплавление (поскольку этот процесс менее чувствителен к изменению длины дуги, чем аргонодуговая сварка) позволяет применять плазменную дугу для сварки тонких листов. Плазменная дуга может обеспечить сварку встык без разделки и присадочного материала листов толщиной до 9,5 мм, а иногда и
51
больше, требует меньше присадочного материала, обладает высокой производительностью. Для сварки материалов толщиной 0,025-0,8 мм применяют микроплазменную дугу (сила тока 0,1 -10 А).
Для плазменной сварки применяются те же автоматы, что и для дуговой с заменой горелки, для микроплазменной - аппараты серий МПИ и МПУ. Для ручной плазменной и аргонодуговой сварки выпускается установка УПС-301.
3.9. Электронно-лучевая сварка
При электронно-лучевой сварке (ЭЛС) металл плавится за счет превращения кинетической энергии электронов, бомбардирующих место сварки, в тепловую. Электроны излучаются накаливаемым катодом и ускоряются электрическим полем. По линии сварки луч устанавливается с помощью магнитной отклоняющей системы. Устройства для получения электронного сварочного луча называются электронными пушками. Среди пушек Пл-104 ... Пл-108 имеются модели, устанавливаемые внутри, вне вакуумной камеры и в специальном отсеке. Например, пушка У752, устанавливаемая снаружи, применяется для однопроходной сварки больших толщин. Имеется много других моделей.
Для свободного движения электронов, уменьшения числа их столкновений с молекулами газов, обеспечения чистоты наплавленного металла, устранения его окисления, азотирования, уменьшения количества растворенных в нем газов процесс ведется в камерах с вакуумом (0,13 10-3) - (0,13 10-9) Па. Плотность энергии в электронном луче на два порядка выше, чем в дуге, что позволяет получать узкую и глубокую зону проплавления с металлом околошовной зоны, не претерпевшим значительных изменений. Шов по ударной вязкости может соответствовать основному металлу, а после термической обработки превосходит его. Вязкость околошовной зоны равна вязкости основного металла. ЭЛС в вакууме обеспечивает лучшие физико-механические характеристики металла сварного соединения по сравнению с аргонодуговой сваркой. Благодаря малому количеству теплоты, введенному в зону сварки, деформации изделий по сравнению дуговой сваркой невелики. Луч позволяет производить сварку в узких щелях, недоступных другим методам.
Вакуумные камеры установок ЭЛС позволяют помещать в них изделия достаточно больших размеров. Так, у установки У350 длина
52
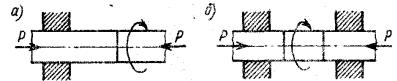
изделия может достигать 4 м. Скорость сварки на установке У350 и других установка серий У и УЛ находится в пределах 10 - 100 м/ч. Имеются также установки серии ЭЛУ.
Для перемещения изделия вдоль луча в процессе сварки в вакуумных камерах устанавливаются координатные столы, вращатели, манипуляторы, а для повышения производительности устанавливаются магазины, позволяющие переходить к сварке последующего изделия без извлечения из камеры предыдущего, что сопряжено с необходимостью иногда длительной откачки воздуха из камеры.
3.10. Сварка трением
При сварке трением (рис. 3.6, а) теплота для нагрева стыков получается за счет быстрого вращения одной из свариваемых деталей, прижимаемой к другой. В процессе трения пластичный металл стыка вместе с разрушенными оксидными пленками и инородными включениями выдавливается в радиальном направлении, образуя кольцевой грат. После нагрева до необходимой температуры (1100 – 1300 °С - для черных металлов) производится прекращение вращения и сильное сжатие. Если свариваемые детали массивны, то они не вращаются, а прижимаются к вращающейся промежуточной не массивной детали (рис. 3.6, б), которую можно быстро остановить. Для сварки трением применяются машины серий МСТ и СТ.
Рис. 3.6. Сварка трением
Преимущества сварки трением объясняются локализованным в поверхностных слоях тепловыделением. Этот способ отличается высокой производительностью, экономичностью (расход энергии в 5 - 10 раз меньше, чем при электрической стыковой сварке), хорошим качеством сварного соединения (металл стыка и прилегающих зон свободен от дефектов, мелкозернист, обладает прочностью и пластичностью не меньшими, чем основной металл), стабильностью
53
качества соединения, независимостью качества от чистоты поверхности, гигиеничностью процесса (отсутствие ультрафиолетового излучения, газовых выделений и брызг металла) Процесс позволяет сваривать разнородные металлы и легок для автоматизации и механизации.
К недостаткам способа относятся: его неуниверсальность (одна из деталей должна быть телом вращения, другая должна иметь плоскость, по которой и происходит сварка); громоздкость оборудования, делающая его немобильным; искривление волокон металла, делающее стык потенциальным очагом усталостного разрушения или коррозии в агрессивных средах.
3.11. Диффузионная сварка
Диффузионная сварка заключается в возникновении связей на атомарном уровне в результате сближения свариваемых поверхностей за счет локальной пластической деформации при повышенной температуре, обеспечивающей взаимную диффузию соединяемых материалов. Для защиты от окисления и азотирования сварка ведется в вакуумной камере. Преимущества этого метода сварки: высокое качество соединения, возможность соединять разнородные материалы и детали сложной конфигурации, экономия энергии, гигиеничность, легкость механизации и автоматизации. Процесс позволяет сваривать металлические сплавы, керамику, графит, стекло, сапфир и другие материалы в однородном или разнородном сочетаниях.
Установки для диффузионной сварки серий СДВУ, СЖМ, УДС содержат рабочую вакуумную камеру; механический, гидравлический или пневматический механизм сварочного давления; индукционный, электронно-лучевой или радиационный источник нагрева; вакуумную систему; систему управления и контроля.
3.12. Холодная сварка
Холодная сварка производится без нагрева, сдавливанием соединяемых частей встык и внахлестку. Возникающая пластическая деформация вызывает растекание материала в месте соединения. Это приводит к сглаживанию неровностей, выносу оксидных пленок из зоны контакта и образованию активных центров схватывания. Схемы холодной сварки аналогичны схемам контактной электриче-
54
ской. Холодная сварка позволяет сваривать однородные и разнородные материалы, обладающие высокой пластичностью. Применяется для стыковой сварки алюминиевых и медных проводов, шовной сварки тонкостенных труб и оболочек, получения многослойного проката из лент. Листовые детали могут соединяться точечной холодной сваркой.
Для стыковой холодной сварки проводов применяются клещи КС-6, машины и полуавтоматы серии МСХС; для точечной сварки – серии МТХС; для шовной – серии МХС.
55
4. МЕТАЛЛОРЕЖУЩЕЕ ОБОРУДОВАНИЕ
4.1.Общие сведения о металлорежущих станках
Впроцессе изготовления изделий в современном машиностроительном производстве обработка резанием играет особую роль. Именно такая обработка позволяет придать заготовкам деталей машин и приборов, полученных литьем, прокаткой, ковкой, штамповкой требуемую форму, точные размеры и заданное качество поверхности. Серьезные недостатки, присущие обработке резанием: сравнительно низкая производительность и образование значительного количества отходов (в среднем 20 % материала превращается в стружку).
Вподавляющем большинстве случаев процесс обработки резанием осуществляют на металлорежущих станках с помощью различных режущих инструментов. Металлорежущие станки являются основным видом технологического оборудования машиностроительных предприятий, количественно намного опережая все его остальные виды.
Металлорежущим станком называется технологическая машина, предназначенная для размерной обработки металлических и неметаллических заготовок с целью получения деталей заданной формы и размеров с требуемой точностью и заданным качеством поверхности. Как правило, на станках осуществляется обработка резанием, при которой с поверхности заготовки в виде стружки удаляется припуск, снимаемый с помощью различных режущих инструментов – лезвийных или абразивных. Кроме того, к станкам относят также технологическое оборудование, в котором для размерной обработки используется пластическое деформирование поверхности заготовок, электрофизические и электрохимические методы, сфокусированный электронный или лазерный луч и т.д.
4.1.1.Классификация металлорежущих станков
Взависимости от характера выполняемых работ (токарных, фрезерных, шлифовальных и др.) станки делятся на 9 групп. Каждая из групп делится на типы, характеризующие назначение станка, его компоновку, степень автоматизации (таблица).
56
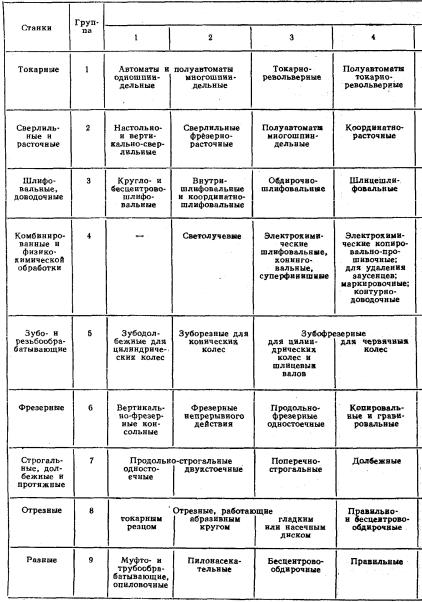
Классификация металлорежущих станков
57
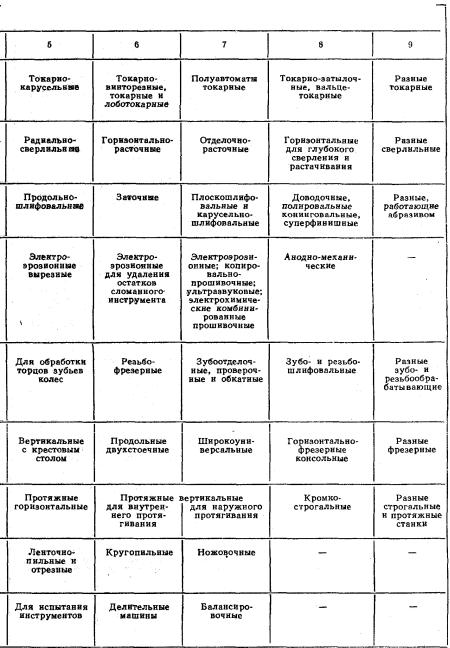
Продолжение таблицы
58
Для большинства типов станков стандартами установлены основные параметры, характеризующие размеры обрабатываемых деталей или геометрические размеры станка. Например, для токарных, круглошлифовальных и зубообрабатывающих станков основным параметром является наибольший диаметр обрабатываемой детали; для сверлильных и внутришлифовальных станков - наибольший диаметр обрабатываемого отверстия; для фрезерных и плоскошлифовальных станков – размеры рабочей поверхности стола и т.д.
Однотипные станки экономически целесообразно создавать по размерным рядам. В размерный ряд входят станки подобные по кинематической схеме, конструкции и внешнему виду, но имеющие разные параметры-размеры. Каждый станок может обрабатывать детали в определенном диапазоне размеров.
Типоразмер станка характеризуется его классификационным типом и максимальным значением основного параметра. Конкретное конструктивное исполнение станка данного типоразмера, предназначенного для заданных условий обработки, называется моделью станка. Таким образом, одному типоразмеру может соответствовать несколько различных моделей.
Станки классифицируются по степени универсальности, сте-
пени автоматизации, степени точности и по массе.
Классификация станков по степени универсальности предусматривает подразделение их по технологическим признакам: универсальные – выполняют разнообразные операции при обработке деталей различных по форме и размерам в единичном и мелкосерийном производстве. Для них характерна частая смена обрабатываемых деталей и частая переналадка. Специализированные предназначены для обработки однотипных деталей сравнительно узкой номенклатуры, сходных по конфигурации, но имеющих различные размеры. Имеют высокую степень автоматизации, используются в крупносерийном и массовом производстве при больших партиях деталей и редкой переналадке. Специальные станки используются для обработки заготовок одного типоразмера в условиях массового производства.
По степени автоматизации различают простые (неавтоматизированные) станки, полуавтоматы и автоматы. На простых станках механизированы только рабочие движения, сообщаемые режущему инструменту и обрабатываемой заготовке. Все остальные движения (установка заготовки, подвод инструмента, изменение режима реза-
59
ния и др.) выполняются рабочим вручную. Применяют в единичном, мелкосерийном и серийном производствах. В полуавтоматах автоматизированы все движения, составляющие цикл обработки, кроме установки заготовки и снятия детали. Автоматами называются станки, на которых весь цикл обработки, включая установку заготовки и снятие детали, осуществляется автоматически. Рабочий лишь периодически загружает в станок партии заготовок и контролирует размеры и качество поверхности обрабатываемых деталей. Станки автоматы и полуавтоматы могут иметь механическое или гидравлическое управление, они требуют трудоемкой переналадки, применяются только в условиях крупносерийного или массового производства. Станки с ЧПУ (числовым программным управлением) легки в переналадке, могут применяться в производстве любой серийности.
По степени точности станки делят на пять классов: нормальной Н, повышенной П, высокой В, особо высокой А точности и особо точные С (мастер-станки). Большинство универсальных станков относится к классу Н. Станки классов В, А и С работают в специальных термоконстантных помещениях, в которых поддерживаются постоянные температура и влажность.
По массе станки делят на легкие (до 1 тонны), средние (до 10 тонн) и тяжелые (свыше 10 тонн). В свою очередь тяжелые станки делятся на крупные (до 30 тонн), собственно тяжелые (до 100 тонн) и особо тяжелые или уникальные (свыше 100 т).
Обозначение станков состоит из трех-четырех цифр, первая из которых указывает группу, вторая – тип, третья и четвертая – один из главных размеров. Буква после первой или второй цифры указывает на модернизацию (конструктивное улучшение) базовой модели станка, причем станок тем более модернизирован, чем дальше эта буква от начала алфавита. Буква или буквы в конце индекса обозначают модификацию (видоизменение) базовой модели станка. Например, для указания класса точности станка после цифр индекса вводится соответствующая буква (кроме класса Н). В моделях станков с ЧПУ в конце индекса вводят букву Ф с цифрой, означающей принятую систему управления: Ф1 – с цифровой индикацией и предварительным набором координат, Ф2 – с позиционной системой управления, Ф3 – с контурной системой управления, Ф4 – с универсальной системой для позиционной и контурной обработки.
Примеры. Модель 16К20ПФ3 расшифровывается следующим
60