
Методическое пособие 581
.pdf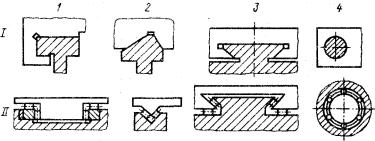
Наиболее ответственной частью станины являются направляющие. Обычно станина имеет пару направляющих, с которой сопрягается пара направляющих, принадлежащих подвижному исполнительному механизму (суппорту, столу, ползуну). На рис. 4.4 приведены примеры направляющих скольжения (I) и качения (II). Направляющие станины заштрихованы. Они могут быть охватываемыми и охватывающими. Охватываемые направляющие скольжения (I, 1- 4) имеют выпуклый профиль. Они просты в изготовлении, на них не задерживается стружка, но они плохо удерживают смазку, поэтому такие направляющие применяют при малых скоростях перемещения (например, при подаче суппорта токарного или стола фрезерного станка).
Рис. 4.4. Формы направляющих
Охватывающие направляющие скольжения с вогнутым профилем хорошо удерживают смазку, но требуют надежной защиты от попадания стружки и загрязнений. Их целесообразно применять при высоких скоростях перемещения в шлифовальных, продольнострогальных и других станках.
По профилю направляющие делятся на прямоугольные 1, призматические (V-образные) 2, типа «ласточкин хвост» 3 и круглые 4. Суппорт токарного станка перемещается по комбинированным направляющим, одна из которых выполнена плоской, а другая призматической, чем обеспечивается правильное расположение резца относительно продольной оси заготовки. Регулирование зазоров в направляющих осуществляется с помощью клиньев, планок и т. п.
В средних и легких станках с ЧПУ, в координатно-расточных, шлифовальных, копировальных и других станках все большее распространение находят направляющие качения (II). Они обеспечива-
71
ют малую силу сопротивления движению, отсутствие скачков при малых скоростях движения, высокую точность установочных перемещений и долговечность. В зависимости от тел качения направляющие качения могут быть шариковыми или роликовыми.
Для защиты направляющих от механических повреждений и от попадания на рабочую поверхность стружки, СОЖ и других загрязнений применяют защитные устройства, выполненные в виде стальных лент, продольных или телескопических щитков, гармоникообразных мехов (гофр) и т. п.
В ряде случаев для повышения износостойкости направляющих их выполняют накладными: изготовляют из стали, закаливают и крепят винтами, приклеивают или приваривают к станине.
Столы, планшайбы и суппорты. Подвижные корпусные узлы предназначены либо для закрепления и рабочего перемещения обрабатываемой заготовки (столы фрезерных, строгальных, расточных, шлифовальных станков, планшайбы карусельных и зубо-фрезерных станков), либо для установки и рабочего перемещения режущего инструмента (суппорты токарных, строгальных и зубо-фрезерных станков, ползуны поперечно-строгальных, долбежных и зубошлифовальных станков). Все эти узлы имеют прямолинейные или круговые направляющие, соответствующие направляющим неподвижных базовых деталей - станин, стоек или поперечин и выполненные в виде пар трения или качения. Как и станины, подвижные узлы должны обладать высокой жесткостью.
Столы и планшайбы станков имеют коробчатую форму. С целью повышения жесткости тело стола усиливают, как правило, продольными, поперечными или радиальными ребрами. Узел стола может быть простым (собственно стол, перемещающийся по направляющим станины) или состоять из нескольких корпусных деталей (салазок, поворотной части, собственно стола), перемещающихся относительно друг друга и образующих общий сложный узел.
Для закрепления заготовок или станочных приспособлений (например, машинных тисков) столы и планшайбы имеют плоскости с Т-образными пазами стандартного размера, в которые заводятся головки специальных болтов. Эти пазы могут быть направлены вдоль стола (рис. 4.5, а), по радиусу (рис. 4.5, б) или по окружности планшайбы, во взаимно перпендикулярных направлениях (рис. 4.5, в). Нередко по контуру плоскости стола предусматривается канавка, служащая для сбора стружки и СОЖ (рис. 4.5, г).
72
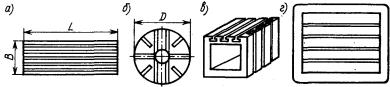
Рис. 4.5. Расположение пазов на столах и планшайбах
Суппорты станков различаются разнообразием конструкций. При необходимости обеспечить перемещение инструмента в разных направлениях (продольное, поперечное, под углом) суппорт состоит из одних-трех салазок (кареток) и имеет поворотную часть.
Механизмы второй группы обеспечивают прямой и обратный ход ведомого звена (цикл) за один оборот ведущего звена. К ним относятся кривошипно-шатунные, кривошипно-кулисные и кулачковые механизмы.
Шпиндельный узел – важнейшая часть станка с вращательным главным движением. Он включает в себя собственно стальной вал, часто пустотелый, с опорами и установленные на нем детали привода вращения и патрон или оправку для крепления обрабатываемой заготовки или режущего инструмента. От шпиндельного узла в большой степени зависит точность обработки, производительность и надежность всего станка. Поэтому к нему предъявляется ряд требований: высокая точность вращения (малые биения конца шпинделя); высокая жесткость и виброустойчивость на всех режимах резания; минимальные тепловыделения вследствие нагрева подшипников и минимальные температурные деформации, влияющие на точность обработки и на работоспособность опор; долговечность; быстрое, точное и надежное закрепление заготовки или инструмента.
Шпиндель вращается на опорах качения или скольжения. В настоящее время более 95 % станков изготовляют со шпиндельными узлами на шариковых или роликовых подшипниках качения, имеющих меньшую стоимость и большую простоту в эксплуатации. Для привода шпинделей часто используются зубчатые передачи, простые, компактные и передающие большие крутящие моменты, однако из-за погрешностей шага, нарушающих плавность вращения шпинделя, их обычно не применяют в прецизионных станках и при высоких частотах вращения. При применении ременной передачи существенно по-
73
вышается плавность вращения и уменьшаются динамические нагрузки, но размеры конструкции увеличиваются.
Для изготовления шпинделей применяют конструкционные стали 45, 50, 40Х с поверхностной закалкой.
К прочим составляющим станков относятся механизмы прямолинейного движения, механизмы периодического движения, реверсивные механизмы, предохранительные и блокировочные устройства, системы управления станками, системы смазывания и охлаждения.
Механизмы прямолинейного движения. Преобразование вращательного движения в прямолинейное поступательное осуществляется в металлорежущих станках с помощью механизмов, которые можно разделить на две группы. Механизмы первой группы, к которым относятся реечные передачи и передачи винт-гайка, преобразуют равномерное вращательное движение ведущего звена в равномерное поступательное движение ведомого звена. Для изменения направления поступательного движения (реверсирования) нужно изменить направление вращательного движения. Механизмы второй группы обеспечивают прямой и обратный ход ведомого звена за один оборот ведущего звена. К ним относятся кривошипно-шатунные, кри- вошипно-кулисные и кулачковые механизмы.
Реечные передачи по своей конструкции делятся на зубчатореечные и червячно-реечные. Зубчато-реечные передачи обеспечивают значительные перемещения ведомого звена на один оборот ведущего звена и имеют высокий КПД. Они широко применяются в приводах подач токарных, сверлильных, расточных и других станков, а также в приводе главного движения продольно-строгальных станков (рис. 4.7, а). При вращении реечной шестерни zр стол 1 про- дольно-строгального станка получает поступательное движение от прикрепленной к нему зубчатой рейки 2.
В зацепление с зубчатой рейкой 2 стола 1 продольно-фрезер- ного или продольно-строгального станка может входить не зубчатое колесо, а червяк 3 (рис. 4.7, б). Червячно-реечная передача обладает большей жесткостью и плавностью в работе, чем зубчато-реечная, так как в зацеплении с червяком одновременно находятся несколько зубьев рейки. Применение такой передачи дает возможность уменьшить число передаточных механизмов в кинематической цепи главного движения, а расположение червяка под углом к рейке позволяетвынестиприводзапределыстола,чтоупрощаеткомпоновкустанка.
74
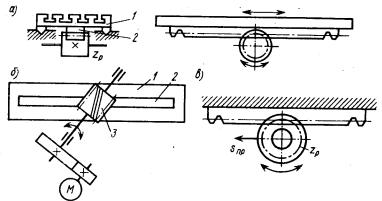
В токарных станках для перемещения суппорта по направляющим станины используется зубчато-реечная передача, в которой рейка неподвижно закреплена на станине станка, а реечная шестерня находится в фартуке суппорта и перемещается вместе с ним, перекатываясь по рейке (рис. 4.7, в).
Рис. 4.7. Реечные передачи
Вприводах подачи и вспомогательных движений столов, суппортов и других исполнительных органов станков широкое применение находит передача винт - гайка, обладающая самоторможением, высокой точностью и плавностью движения ведомого звена при больших и малых перемещениях. Наиболее часто применяется передача винт - гайка скольжения, простая по конструкции и технологичная в изготовлении. Она имеет, как правило, резьбу трапецеидального профиля с углом 30°, что допускает применение разъемной гайки (гайка ходового винта).
Вприводах подач точных станков шлифовальных, копиро- вально-фрезерных, координатно-расточных и особенно в станках с ЧПУ применяется передача винт - гайка качения, преимуществом которой являются отсутствие зазора в резьбе, низкие потери на трение и почти полная независимость силы трения от скорости. Передача состоит из винта 1 (рис. 4.8), гайки 2, комплекта шариков 3 и канала 4 возврата шариков. Соединение начального и последнего винтов гайки каналом обеспечивает непрерывную циркуляцию шариков.
75
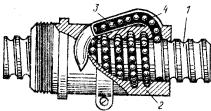
Рис. 4.8. Шариковая пара винт-гайка
Вприводах возвратно-поступательного главного движения быстроходных станков с небольшим ходом инструмента применяют
механизмы кривошипно-шатунные (зубодолбежные станки) и кри-
вошипно-кулисные (поперечно-строгальные и долбежные станки). В этих станках частота двойных ходов инструмента равна частоте вращения кривошипа. В отличие от кривошипно-шатунного механизма, у которого скорости рабочего и холостого ходов одинаковы,
вкривошипно-кулисных механизмах холостой ход совершается с большей скоростью, чем рабочий, благодаря чему сокращается время, затрачиваемое на осуществление холостых ходов.
Впоперечно-строгальных станках применяют кривошипнокулисные механизмы с качающейся кулисой (рис. 4.9, а). Качающаяся кулиса приводится в движение кулисным камнем, сидящим на пальце кривошипного зубчатого колеса zк, вращающегося в одном направлении. При этом верхний камень перемещает ползун с резцом горизонтально и одновременно перемещается вертикально по пазу ползуна, преобразуя качательное движение кулисы в возвратнопоступательное движение ползуна. Рабочий ход ползуна осуществляется при движении пальца от В к А, а холостой - при движении пальца от А к В. Таким образом, рабочему ходу соответствует поворот кривошипного колеса на угол α, а холостому ходу - поворот на угол β. При равномерном вращении кривошипного колеса время холостого хода меньше времени рабочего хода, т. е. холостой ход осуществляется быстрее. Изменение скорости ползуна при рабочем ходе vp и холостом vx вдоль пути L показано на графике.
На рис. 4.9, б схематически изображен кривошипно-кулис-ный механизм с вращающейся кулисой, применяемый в долбежных станках. Здесь кривошип, равномерно вращающийся с постоянной
окружной скоростью п, сообщает неравномерное вращение с пере-
76
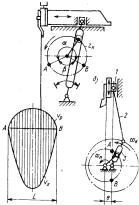
менной скоростью к кулисе-кривошипу 3, ось вращения которой отстоит от оси ведущего кривошипа на величину е. Движение пальца кривошипа от А к В соответствует рабочему ходу, от В к А - холостому ходу. Вращение кулисы 3 с помощью шатуна 2 преобразуется в возвратно-поступательное движение ползуна 1 с резцом.
В приводах подач и вспомогательных движений станковавтоматов и полуавтоматов широко применяют кулачковые механизмы. Они служат для осуществления возвратно-поступательных или (реже) качательных движений ведомого звена (толкателя, ползуна, коромысла), многократно повторяющихся при непрерывном вращении ведущего звена (кулачка) с постоянной угловой скоростью.
Рис. 4.9. Кривошипнокулисные механизмы
Конструктивно кулачковые передачи могут выполняться с дисковыми (плоскими) кулачками (рис. 4.10, а, б) или цилиндрическими (барабанными) кулачками (рис. 4.10, в, г). Кулачки могут быть связаны с подвижным рабочим органом станка непосредственно (а, в) или через промежуточную передачу, например в виде коромысла (б,
г).
Главная особенность кулачкового механизма заключается в том, что характер движения ведомого звена может быть установлен соответствующим профилированием кулачка. Так, в передаче, показанной на рис. 4.10, а ролик 3, установленный на толкателе 2, неподвижен, находясь в контакте с цилиндрическим участком профиля дискового кулачка 4. С началом подъема профиля вращающегося
77
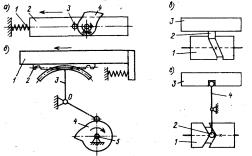
кулачка толкатель перемещается влево, причем скорость его движения зависит от угла подъема профиля. Рабочий участок профиля, осуществляющий равномерное движение толкателя (движение подачи) очерчивается по архимедовой спирали. При падении профиля толкатель отводится в исходное положение. Пружина 1 обеспечивает постоянный контакт ролика с кулачком и осуществляет обратный ход толкателя. Во втором случае (б) кулачок 4, сидящий на распределительном валу 5 автомата, находится в контакте с роликом коромысла 3, имеющим в верхней части зубчатый сектор, сопряженный с рейкой 2, закрепленной на суппорте 1. При повороте коромысла с сектором вокруг точки 0 суппорт перемещается в направлении, показанном стрелкой.
Механизмы с цилиндрическим кулачком (рис. 4.10, в, г) подобны передаче винт - гайка, однако винтовая поверхность кулачка 1 имеет переменный шаг, а вместо гайки используется ролик 2, что позволяет сообщать ползуну 3 поступательное перемещение с переменной скоростью.
Рис. 4.10. Кулачковые механизмы
Кулачковый механизм позволяет осуществить автоматический цикл движений суппорта, состоящий из быстрого подвода суппорта, медленной рабочей подачи, выдержки и быстрого отвода суппорта в исходное положение.
Механизмы периодического движения. Для преобразования вращательного движения в периодическое (прерывистое) в станках применяют храповые и мальтийские механизмы. Храповые механизмы осуществляют периодические движения в течение коротких промежутков времени и служат для осуществления прерывистой
78
подачи на строгальных, долбежных и шлифовальных станках. Мальтийские механизмы применяют для осуществления периодических движений через сравнительно длительные промежутки времени и используют в автоматах и полуавтоматах для периодического поворота на постоянный угол револьверных головок, шпиндельных блоков и поворотных столов.
Храповой механизм показан на рис. 4.11, а. Подпружиненная собачка 2 смонтирована на коромысле 7, свободно сидящем на ходовом винте подачи. На этом же винте на шпонке закреплено храповое колесо 3. Коромысло собачки получает качательное движение от кривошипно-шатунного механизма, состоящего из шатуна 6 и кривошипного диска 5, при вращении которого коромысло 7 вместе с собачкой 2 получает качательное движение. При движении влево собачка попадает во впадину между зубьями храпового колеса и поворачивает его на некоторый угол; при движении вправо собачка за счет наличия скоса отжимает пружину и проскальзывает по зубьям храпового колеса - в результате передачи движения не происходит. Величину подачи, определяемую углом периодического поворота ходового винта, регулируют либо перемещением пальца по радиальному пазу кривошипа диска 5 на требуемое расстояние, от чего зависит размах качаний коромысла 7, либо соответствующей установкой щитка 4, прикрывающего часть зубьев храповика. При этом часть пути собачка скользит по щитку, а при прохождении остального пути захватывает требуемое число зубьев. Для изменения направления подачи (вращения храповика) нужно за кнопку 1 вытянуть собачку кверху и повернуть на 180 °.
Мальтийский механизм состоит из поводка 3 с фиксирующим сегментом 4 и цевкой 2, а также мальтийского креста 1, имеющего радиальные пазы и фиксирующие гнезда, по форме соответствующие фиксирующему сегменту (рис. 4.11, б). При вращении поводка цевка входит в продольный паз креста, поворачивает его на угол 2 (в нашем случае 90 °) и выходит из паза. Поводок при этом повернется на угол 2 . После выхода цевки фиксирующий сегмент поводка заходит в сегментное гнездо креста и фиксирует его в определенном положении до тех пор, пока цевка не войдет в следующий паз. Для безударной работы механизма угол у входа цевки в паз должен быть равен 90 °. Число пазов мальтийского креста составляет обычно 4 или 6, а крест за один оборот кривошипа поворачивается соответственно на 90 или на 60 °.
79
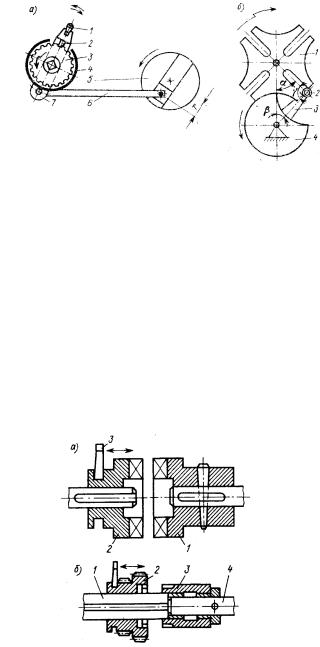
Рис. 4.11. Механизмы прерывистого движения
Муфты. Муфты служат для соединения валов и передачи вращения от одного вала к другому. Наряду с постоянными муфтами, не разъединяемыми в процессе работы станка, широкое применение находят сцепные муфты, играющие важную роль в управлении станками. Сцепные муфты применяют для периодического соединения и разъединения валов механизмов станка. Конструктивно сцепные муфты выполняются кулачковыми, зубчатыми или фрикционными.
На рис. 4.12, а показана кулачковая муфта, состоящая из двух полумуфт - неподвижной 1 и подвижной 2 с торцовыми кулачками (зубцами), сидящих на соединяемых валах на шпонках. Для включения муфты подвижную полумуфту 2 вилкой 3 перемещают вдоль вала, вводя кулачки полумуфт в зацепление друг с другом.
Рис. 4.12. Сцепные муфты
80