
Методическое пособие 581
.pdf1.3. Литье в оболочковые формы
При оболочковом литье формовочная смесь состоит из кварцевого песка и термореактивной смолы. При насыпке смеси на нагретую металлическую полумодель, смола плавится в слое смеси, примыкающей к модели, связывая песчинки в полутвердую оболочку (скорлупу) толщиной 6-15 мм. Затем оболочковая полуформа высушивается в печи, склеивается со второй полуформой, заформовывается в ящики с дробью или песком и заливается сплавом. Отливка имеет чистые поверхности без включений, раковин и трещин. Сокращается в 7-8 раз расход формовочной смеси, повышается производительность труда. Литье в оболочковые формы применяется преимущественно для отливок, формы для которых имеют одну плоскость разъема и минимальное число стержней. Этот способ применяется обычно при крупносерийном и массовом производстве отливок. Процесс легко автоматизируется. Масса получаемых отливок обычно равна 10-15 кг. Но стоимость литья в оболочковые формы в 2 раза выше стоимости литья в песчаные формы.
Применяется машина 51713 для изготовления оболочковых полуформ гравитационным способом в серийном и массовом производстве точных отливок из черных металлов и цветных сплавов. Для работы в паре с машиной 51713 выпускается машина для склеивания оболочковых полуформ 51813. На основе названных машин для мелкосерийного производства создается робототехнический комплекс, который освобождает от ручной работы в зоне высоких температур с загазованной атмосферой, сокращает численность работающих, повышает производительность труда, решает экологические вопросы.
1.4. Литье по выплавляемым и выжигаемым моделям
Этот способ обеспечивает получение весьма точных исходных заготовок, обработка резанием которых максимально сокращается. Способ длителен, трудоемок и долог, но эффективен при изготовлении деталей сложной формы и малой массы из цветных и черных сплавов. Например, зубчатых колес, шлицевых валиков, а также различного режущего инструмента. Находит применение в массовом и серийном производстве.
21
Легкоплавкий или растворимый материал (например, смесь парафина и стеарина) запрессовывается в разогретом состоянии в точно изготовленную прессформу. Как только модель затвердеет, ее извлекают из прессформы, погружают в жидкую огнеупорную массу и обсыпают чистым кварцевым песком. После просушки процесс повторяют до тех пор, пока толщина стенки огнеупорной формы не достигнет 1,5-3 мм. Модель из формы удаляется выплавлением или растворением, и поэтому форма не нуждается в разъемах. Заготовки, полученные литьем по выплавляемым моделям, имеют повышенную прочность. В качестве оборудования используются пресс-формы из металла, пластмасс, гипса и др. Используются автоматы карусельного типа для изготовления модельных звеньев 61201 (рис.1.11,а) производительностью 400 запрессовок в час. Основой автомата является поворотный стол 1, на котором радиально расположены десять пневматических механизмов 2 запирания пресс-форм. На первой позиции пресс-форма запирается, к литнику поджимается шприц 4 и запрессовывает модельный состав. Затем шприц отходит, и стол поворачивается на 36 °. На следующих шести позициях модель охлаждается в закрытой пресс-форме. На восьмой позиции пресс-форма открывается, модель 7 толкателями выталкивается в водяной конвейер 8, который течением выносит ее, предотвращая падение на нее следующей модели. Здесь модель окончательно охлаждается. На девятой позиции литниковые отверстия прочищаются иглой 6 и на полость пресс-формы смазочная жидкость наносится распылением через форсунки 5. На десятой позиции пресс-форма закрывается.
После изготовления модели объединяют в модельные блоки с литниковой системой. В условиях крупносерийного и массового производства звенья моделей вслед за моделью чаши нанизывают на стояк-каркас (рис. 1.11, б), который облегчает манипулирование блоком при изготовлении линейных форм на установках и автоматизированных линиях.
Для производства выжигаемых пенополистирольных моделей объемом 25 - 625 см3 в крупносерийном и массовом производстве применяется автомат 69213 производительностью 100 - 280 запрессовок в час.
22
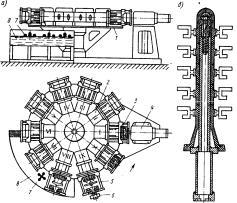
Рис. 1.11. Карусельный автомат для получения выплавляемых моделей и стояк для их сборки
1.5. Литье под давлением
Литье под давлением применяют, в основном, при изготовлении сложных тонкостенных отливок с глубокими полостями, получение которых в металлических формах обычным способом невозможно, так как жидкий металл, соприкасаясь с формой, очень быстро охлаждается и теряет свою жидкотекучесть, в результате чего плохо заполняются наиболее глубокие и узкие полости. Металл может заполнить все полости такой формы только под большим давлением (200-250 МПа), которое и создается прессующим поршнем машин для литья под давлением. Литейная форма в этом случае должна выдерживать высокие давления. Поэтому все элементы литейной формы, называемой пресс-формой, в том числе стержни, изготовляются из металлов. Высокие давления в пресс-форме стремятся раскрыть ее, поэтому механизм закрытия пресс-форм машины должен обеспечивать надежное удержание пресс-формы в замкнутом состоянии. Вследствие действия больших давлений и усилий все манипуляции с пресс-формой (открытие, закрытие, выталкивание отливки, вставкаи вытяжка стержней и др.)выполняютсятолькомашиной.
Литьем под давлением можно получать самые сложные тонкостенные (до 1 мм) отливки, с самыми мелкими (диаметром до 1 мм) длинными отверстиями, с готовой резьбой, надписями, рельефом, накаткой, с самой чистой поверхностью, с самой высокой точностью
23
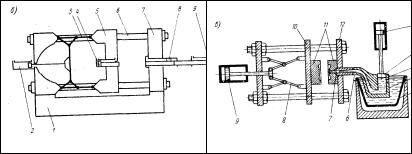
размеров (до 9-го квалитета), с самыми малыми припусками на обработку резанием (0,3 - 0,5 мм). Этот способ литья обладает самой высокой производительностью, соперничая с листовой штамповкой (самый высокопроизводительный процесс машиностроительного производства). Отливки отличаются также коррозионной стойкостью и герметичностью. К недостаткам этого способа относятся газовая пористость и усадочные раковины в отливках. Наличие в отливках пор со сжатыми в них газами делают нежелательной их термическую обработку.
Литьем под давлением изготовляют отливки массой от нескольких граммов до 30 кг и более: блоки цилиндров автомобильных двигателей, корпуса электродвигателей, корпуса гидротрансформаторов, картеры блока двигателей автомобилей, корпуса фотоаппаратов, карбюраторов, мясорубок, водопроводной арматуры, приборов, готовален, замков, швейных машин, застежек «молния» и др.
Рис. 1.12. Оборудование для литья под давлением
Пресс-формы очень сложны, трудоемки и дороги. Поэтому литье под давлением применяется в основном в массовом и крупносерийном производстве отливок преимущественно из цветных (цинковых, алюминиевых, медных, магниевых) сплавов, которые при заливке имеют температуру гораздо меньшую, чем у черных. Стойкость пресс-форм (в тысячах запрессовок) может достигать для цинковых сплавов 300 - 500, для магниевых 80 - 100, для алюминиевых 30 - 50 и для медных 5 - 20.
Наиболее широко применяются машины с холодной горизон-
тальной камерой прессования 711А06 ... 71119, позволяющие по-
лучать отливки массой до 50 кг (при литье алюминиевых сплавов), с
24
числом холостых циклов в час от 300 до 21. На станине 1 таких машин (рис. 1.12, а) по направляющим 6 под действием самотормозящей рычажной системы 3, приводимой гидравлическим цилиндром 2, перемещается подвижная плита 5 с гидровыталкивателем 4. На этой плите устанавливается подвижная часть пресс-формы. Неподвижная часть пресс-формы устанавливается на неподвижную плиту 7 с камерой прессования 8, куда заливается порция сплава, загоняемая в пресс-форму пресс-поршнем цилиндра 9.
Имеются машины с вертикальной холодной камерой прессо-
вания, например 71217, отличающиеся меньшими габаритными размерами, но имеющие более длительный цикл и меньшую производительность. Во многих случаях имеющиеся на заводах вертикальные машины заменяются горизонтальными.
Машины с горячей камерой прессования 4 (рис. 1.12, б) отли-
чаются высокой производительностью. Эта камера находится в тигле с расплавленным металлом 5. Части пресс-формы 11 в момент прессования сжаты гидроцилиндром 9 через рычажный механизм запирания 8 между подвижной 10 и неподвижной 12 плитами. При движении прессового поршня 2 вниз под действием гидроцилиндра 1 сплав движется по металлопроводу 6, мундштуку 7 и заполняет пресс-форму. После затвердевания отливки поршень идет вверх, и остатки сплава сливаются в камеру прессования, а сплав из тигля через открывшееся отверстие 3 наполняет камеру. Подвижная плита отводится влево механизмом запирания машины, отливка выталкивается из пресс-формы. Затем пресс-форма обдувается, смазывается, смыкается и цикл повторяется. Машина-автомат для литья под давлением с горячей камерой прессования 713А05 предназначена для получения отливок из цветных сплавов (цинковых, оловянных, свинцовых) в серийном и массовом производстве.
1.6. Литье в металлические формы
Отливки, залитые в металлические формы, имеют большую точность размеров и низкую шероховатость поверхности, чем при литье в песчаные формы. Такие отливки требуют меньшего припуска на механическую обработку. Структура металла получается более мелкозернистой, повышается его прочность. Устраняется необходимость в формовочном и смесеприготовительном хозяйстве, улучшаются технико-экономические показатели производства и санитарногигиенические условия труда. К недостаткам способа относятся: большая стоимость изготовления формы; повышенная теплопровод-
25
ность формы, приводящая к пониженной заполняемости форм металлом вследствие быстрой потери жидкотекучести. В целях получения качественной отливки и удлинения срока службы кокиль в процессе работы поддерживают в нагретом состоянии.
Металлические формы – кокили – являются многоразовыми литейными формами, заполняемыми свободной заливкой. При литье средних по величине отливок чугунные кокили выдерживают 0,1 – 0,3 тысячи заливок стали, 1 – 3 тыс. заливок чугуна, 1 – 8 тыс. заливок медных сплавов, десятки тысяч заливок алюминиевых, магниевых, цинковых сплавов. Кокили бывают вытряхные, створчатые, с параллельным разъемом, с несколькими разъемами.
Вытряхные кокили применяются в мелкосерийном и серийном производстве для отливок простой формы. Створчатые кокили состоят из двух полуформ. Они применяются для отливок, форма которых позволяет раскрывать кокиль поворотом полуформы относительно оси.
Самые сложные отливки из черных и цветных сплавов в серийном и массовом производстве позволяют получать кокильные машины. При массовом производстве изделий заготовки получают на автоматических многопозиционных установках. Автоматически выполняются подготовка металлической формы и ее заливка, выбивка, транспортировка к очистным агрегатам и очистка заготовок.
1.7. Центробежное литье
Способ обеспечивает высокое качество исходных заготовок, представляющих собой тела вращения – гильзы, кольца, втулки, трубы, зубчатые колеса. Центробежное литье получают на центробежных машинах в металлической форме, вращающейся относительно горизонтальной или вертикальной оси. Заливаемый металл центробежными силами отбрасывается на периферию формы, что позволяет получать полые отливки без применения стержней. Заготовки имеют высокую плотность по наружной поверхности и более точный ее профиль, но внутренняя поверхность имеет меньшую плотность и более грубая. Преимущества: повышается качество заготовок, уменьшается расход жидкого металла, снижаются трудоемкость и себестоимость последующей обработки резанием. Исполь-
зуются машины литейные центробежные ЛН102А и ЛН104Б,
ЦЛ288, ЦЛ269.
26
2. ОБОРУДОВАНИЕ ДЛЯ ОБРАБОТКИ МЕТАЛЛОВ ДАВЛЕНИЕМ
2.1.Общие вопросы кузнечно-штамповочного производства
Воснове кузнечно-штамповочного производства лежит способность материалов деформироваться, т.е. изменять свою форму без разрушения под действием внешних сил. Кузнечноштамповочное производство позволяет получать фасонные заготовки, отличающиеся лучшими механическими характеристиками материала (особенно пластичности и вязкости) по сравнению с литыми заготовками, что обеспечивает повышенную надежность деталей.
Втаких заготовках отсутствуют поры и раковины, возможные в литье, но недопустимые в ответственных деталях, от стабильной работы которых зависят жизнь и здоровье людей. В самолете до 80-90 % деталей, а в автомобиле до 85 % деталей – штампованные. Однако подобные заготовки проще по форме и дороже по цене.
Внастоящее время из всех видов кузнечных машин, используемых в стране, около 60 % приходится на кривошипные кузнечноштамповочные машины. Это объясняется их простотой в обслуживании, возможностью организовывать процессы штамповки в автоматическом режиме, длительным сохранением стабильности регулировки и высокими точностными характеристиками штампуемых изделий. Кроме того, современные кривошипные кузнечнопрессовые машины наиболее полно отвечают требованиям эргономики и оказывают минимальное воздействие на окружающую среду.
К методам получения заготовок обработкой давлением отно-
сятся ковка, штамповка, прессование.
2.2.Резка и нагрев заготовок
Кподготовительным операциям обработки металлов давлени-
ем относятся резка заготовок и нагрев металла.
Резка проката и слитков самая распространенная операция металлообработки. Кривошипные ножницы выполняют резку заготовок сдвигом одной части заготовки относительно другой. Имеются кривошипные ножницы для резки сортового проката (круглого, квадратного, профильного), листового проката и комбинированные. Сортовые ножницы выпускаются с номинальным усилием до 40 МН
27
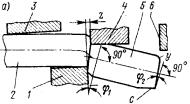
(модель НА1546), они могут резать круглые штанги диаметром до 320 мм (при в = 500 МПа), квадрат со стороной до 300 мм, полосу 450 х 200 мм и совершают 12 ходов в минуту. Мелкие сортовые ножницы могут совершать до 50 ходов в минуту.
Сущность такого способа резки прутков (рис. 2.1, а) состоит в том, что в верхнем положении ножа 4 и прижима 3 пруток 2 подается до упора 6, после чего прижим опускается и прижимает пруток к неподвижному ножу 1, затем подгонной нож отрезает заготовку 5. Длина заготовки меняется регулированием упора.
Резка на кривошипных ножницах высоко производительна и происходит без отходов, вызванных самим процессом резки.
Недостатком является искажение формы заготовки, косина (неперпендикулярность торцов образующей заготовки), смятие с и утяжины у. Не всегда удовлетворительна и точность резки. Для уменьшения искажений формы заготовки выпускаются ножницы
(Н1834 и Н1838) для резки с дифференциальным зажимом, при ко-
торой пруток и заготовка зажимаются силой Q, пропорциональной усилию резки Р. Резку с предварительным подогревом применяют для предотвращения дефектов (трещин), снижения усилия и повышения точности отрезаемых заготовок.
Рис. 2.1 Схема резки заготовок
Разрезка в штампах на прессах позволяет добиться более высокой (чем на ножницах) точности размеров и формы. Применяется также холодная ломка на прессах проката, на который предварительно нанесены канавки – концентраторы напряжений. Точность ломки невысока.
28
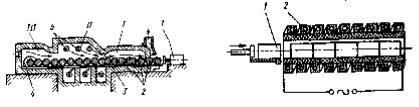
Отрезка заготовок со снятием стружки на отрезных станках отличается высокой точностью и практически отсутствующим искажением сечения заготовки в зоне реза, однако имеет меньшую производительность и сопровождается отходом металла в стружку.
Применяется также газокислородная резка сортового и листового проката.
Для резки листа применяются ножницы кривошипные листовые, которые могут быть гидравлическими, высечными, двухдисковыми и многодисковыми.
Нагрев металла перед обработкой давлением предназначен для уменьшения в 10-15 раз сопротивления металла деформированию и повышения его пластичности. Нагревательные устройства кузнечных и штамповочных цехов делятся на пламенные, электрические и комбинированные. Пламенные печи работают на природном газе или мазуте, такой нагрев универсален и дешев. По характеру распределения температуры в рабочем пространстве печи делятся на камерные (температура одинакова во всех точках рабочего пространства) и методические (температура растет от места загрузки заготовок к месту их выгрузки).
Методические печи могут иметь две, три, четыре зоны с различной температурой. В методических печах (рис. 2.2, а) заготовки 2 перемещаются толкателем 1 (транспортером, шагающими балками и др.) по подкладкам 3 от места загрузки к окну для выдачи нагретых заготовок 4, навстречу потоку продуктов сгорания топлива от горелок 5 (для газа) или форсунок (для мазута). В зоне I печи производится предварительный подогрев, в зоне II - нагрев до окончательной температуры, в зоне III температура в разных точках заготовки выравнивается.
а б Рис. 2.2. Схемы нагревательных устройств
29
Электронагрев более дорог, но позволяет достичь более высокой производительности труда, провести полную автоматизацию, улучшить условия труда. Основные виды оборудования для элек-
тронагрева: электропечи сопротивления, индукционные нагрева-
тели, установки электроконтактного нагрева.
При индукционном нагреве (рис.2.2, б) заготовки 1 продвигаются толкателем через спираль из медной трубки (индуктор) 2, по которой для охлаждения циркулирует вода и пропускается переменный электрический ток. Заготовки нагреваются за счет индуцированных в них токов.
2.3. Ковка
Ковка – способ обработки металлов давлением, при котором инструмент оказывает на заготовку многократное прерывистое действие, в результате чего она, деформируясь, постепенно приобретает заданную форму и размеры. Ковкой получают изделия массой до 200 тонн из слитков или проката. Различают ковку в штампах и без применения штампов, так называемую свободную.
При свободной ковке (ручной или машинной) металл не ограничен совсем или ограничен с одной стороны. Свободная ковка на молотах и прессах позволяет получать заготовки простой формы массой от нескольких килограммов до сотен тонн из углеродистых и легированных сталей и специальных сплавов в единичном и мелкосерийном производстве. В качестве оборудования для ковки исполь-
зуются пневматические ковочные молоты, паровоздушные ко-
вочные молоты, гидравлические ковочные прессы. Пневматические ковочные молоты (рис. 2.3) приводятся в
действие электродвигателем 13, соединенным муфтой 12 с редуктором 11, уменьшающим скорость вращения и увеличивающим вращающий момент на кривошипе 15, приводящем в движение шатун 14 и поршень 5 компрессорного цилиндра 9. При перемещении поршня 8 поочередно в верхней и нижней полостях компрессорного цилиндра 9 воздух сжимается до 0,2 - 0,3 МПа и при открывании с помощью педали золотников (кранов) 6 или 7 подается в рабочий цилиндр 5, поршень которого 4 на конце массивного штока несет верхний боек 3. В результате падающие части 3 и 4 перемещаются вниз вверх и наносят удары по заготовке, лежащей на нижнем бойке 2, закрепленном на массивном шаботе 1. Масса шабота ковочных
30