
Методическое пособие 581
.pdfОсобое место в группе станков для абразивной обработки занимают доводочные станки, предназначенные для выполнения отделочных операций, при которых достигается наивысшая точность и минимальная шероховатость поверхности. Обработка на этих станках осуществляется с помощью мелкозернистых абразивных брусков (хонингование, суперфиниш) или с помощью свободного абразива – порошка в жидкой среде или пасты (полирование, притирка).
К конструкции шлифовальных и доводочных станков предъявляют повышенные требования в отношении жесткости, виброустойчивости, износостойкости и температурных деформаций.
Станки шлифовально-доводочной группы применяют при любых масштабах производства (в условиях крупносерийного и массового производств предпочтение отдают специализированному оборудованию).
Круглошлифовальные станки. На круглошлифовальных стан-
ках обрабатывают наружные цилиндрические, конические, торцовые и фасонные поверхности. Шлифование осуществляется с продольной, поперечной, а иногда и наклонной (на торцекруглошлифовальных станках) подачей периферией, торцом или фасонной поверхностью круга.
Наружное круглое шлифование с продольной подачей (рис. 4.31, а) осуществляют при вращении в одну сторону шлифовального круга vk и обрабатываемой детали vд (круговая подача). Кроме того, деталь совершает возвратно-поступательное движение продольной подачи sпрод, шлифовальный круг в конце каждого одинарного или двойного хода получает периодическое перемещение поперечной подачи sпоп на глубину резания t. По этой схеме обрабатывают относительно длинные детали. При глубинном круглом шлифовании жестких валов круг устанавливают на глубину припуска t и ведут обработку с односторонней продольной подачей sпрод, поперечная подача здесь отсутствует. Врезное шлифование с непрерывной поперечной подачей круга sпоп при отсутствии продольной подачи применяют в тех случаях, когда длина обрабатываемой поверхности меньше ширины круга, а также при шлифовании фасонных поверхностей профильным кругом.
На рис. 4.32 показан круглошлифовальный станок. Обрабатываемая деталь устанавливается в центрах передней 3 и задней 5 бабок, расположенных на столе станка. Привод передней бабки (бабки изделия) сообщает детали вращательное движение круговой подачи
121
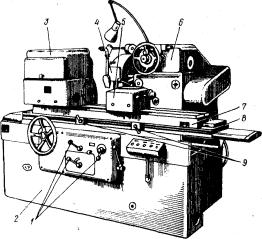
со скоростью 20 - 30 м/мин. Стол получает возвратнопоступательное движение продольной подачи по направляющим станины 2 с помощью штока гидропривода, расположенного внутри станины. Круглошлифовальные станки делятся на простые и универсальные.
Рис. 4.32. Круглошлифовальный станок
Внутришлифовальные станки применяют для обработки ци-
линдрических, конических, фасонных отверстий и торцов. Их делят на патронные и планетарные. Первые наиболее распространены и применяются для шлифования отверстий в деталях средних и малых размеров, вторые – для шлифования отверстий в крупных деталях.
Движения в станках патронного внутреннего шлифования аналогичны движениям при наружном круглом шлифовании (рис. 4.31, б).
В процессе планетарного внутреннего шлифования деталь остается неподвижной, а все необходимые движения сообщаются шлифовальномукругу(рис. 4.31, в).
Бесцентрово-шлифовальные станки широко применяются для высокопроизводительной обработки деталей типа тел вращения, которые не подлежат закреплению в центрах или в патроне. Применяются в крупносерийном и массовом производстве в связи со сложностью наладки. Схема бесцентрового сквозного шлифования напроход приведена на рис. 4.31, г.
122
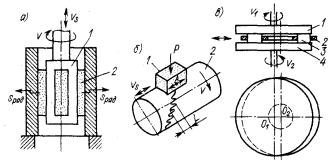
Плоскошлифовальные станки предназначены для обработки плоских поверхностей. Различают станки с горизонтальным шпинделем, работающие периферией круга (рис.4.31, д), и станки с вертикальным шпинделем, работающие торцом круга (рис.4.31, е). Максимальные размеры деталей, обрабатываемых на плоскошлифовальных станках, определяются размерами их стола.
Доводочные станки применяют для получения минимальной шероховатости поверхности и наивысшей точности размеров и формы детали. К отделочным методам обработки относятся хонингова-
ние, суперфиниш, притирка и полирование.
Хонингование (рис. 4.33, а) применяется в основном для обработки отверстий диаметром от 3 до 1500 мм и длиной до 20 м в деталях типа гидроцилиндров, орудийных стволов и т.п.
Хон (хонинговальная головка) 1, оснащенный 3 - 12 мелкозернистыми абразивными брусками 2, совершает одновременно вращательное и возвратно-поступательное движения в обрабатываемом отверстии неподвижной детали 3. Абразивные бруски установлены в пазах цилиндрической поверхности хона и в конце каждого двойного хода специальным гидравлическим или механическим устройством раздвигаются на несколько микрометров, осуществляя движение радиальной подачи sрад. Со шпинделем станка хон соединяется шарнирно, поэтому бруски хона самоустанавливаются по отверстию, и точность хонингования практически не зависит от точности станка.
Рис. 4.33. Схемы работы на доводочных станках
Благодаря жесткой конструкции хона и принудительной радиальной подаче брусков хонингование исправляет небольшие погрешности формы предварительно развернутого или расшлифованного отверстия (овальность, конусность и пр.), но не исправляет по-
123
ложения оси. Окружная скорость движения хона v = 0,25 1,0 м/с, а скорость движения вдоль оси v = 0,1 - 0,3 м/с. Соотношение между v и vs, подбирается таким образом, чтобы зерна брусков перемещались по неповторяющимся пересекающимся винтовым траекториям (принцип неповторяющегося следа), что позволяет получить поверхность с высокими эксплуатационными свойствами. При хонинговании применяют обильное охлаждение керосином или эмульсией. Припуск на хонингование не превышает 0,2 мм. Хонингованием достигают 7-го квалитета точности с параметром шероховатости Rа = 0,32 0,08 мкм, отклонением от цилиндричности в пределах 3 - 5 мкм.
Хонинговальные станки могут быть одношпиндельными и многошпиндельными, с вертикальным, горизонтальным или наклонным расположением шпинделей. Возвратно-поступательное движение шпинделя осуществляется от гидравлического привода.
Суперфиниш (рис.4.33, б) представляет собой особый вид тонкой абразивной обработки предварительно отшлифованных поверхностей (чаще всего наружных цилиндрических) специальными головками, оснащенными одним-четырьмя мелкозернистыми брусками. Бруски закрепляются в головке не жестко, как при хонинговании, а упруго, и при обработке самоустанавливаются по поверхности детали. Особенностью суперфиниша является быстрое колебательное движение А бруска 1 вдоль оси детали 2 в сочетании с вращением детали и ее возвратно-поступательным движением вдоль оси. Подпружиненный брусок снимает шероховатость, но не устраняет погрешности формы. Для суперфиниша применяются одно- и многошпиндельные станки, обычно специализированные на обработку конкретной детали.
Притирка (рис. 4.33, в) – тонкая отделка поверхностей предварительно отшлифованных деталей мелкозернистым абразивным порошком, смешанным со смазочным материалом и нанесенным на поверхность инструмента (притира). Притирка осуществляется с помощью двух чугунных притиров-дисков 1 и 4, между которыми помещается сепаратор 2 с обрабатываемыми деталями 3.
Полирование – обработка деталей при помощи особо мелкозернистой (полировальной) пасты, нанесенной на эластичный полировальный круг, изготовляемый из войлока, кожи или парусины. Полирование доводит поверхность детали до зеркального блеска, но не изменяет размеров и формы детали.
124
4.7.Резьбообрабатывающие станки
Всовременном машиностроении применяют много методов обработки резьбы с использованием различных станков и инструментов. Нарезание резьбы возможно осуществить на станках токарной группы, сверлильных и расточных.
Для более производительной обработки резьбы применяют специализированное оборудование. В условиях общего машиностроения для обработки резьбы применяют резьбофрезерные и резьбошлифовальные станки.
Резьбофрезерные станки бывают двух типов:
- станки, работающие дисковыми резьбовыми фрезами; - станки, работающие гребенчатыми фрезами.
Станки, работающие дисковыми фрезами, по своей компо-
новке и кинематике аналогичны токарно-винторезным станкам с тем отличием, что вместо резьбового резца на суппорте установлена фрезерная головка с закрепленной на ее шпинделе дисковой резьбовой фрезой. Заготовку устанавливают в центрах, а ось вращения фрезы 1 (рис. 4.34, а) поворотом фрезерной головки в вертикальной
плоскости устанавливают к оси вращения заготовки 2 под углом , равным углу подъема винтовой линии нарезаемой резьбы. Это необходимо для получения неискаженного профиля резьбы. Фрезе сообщают главное вращательное движение со скоростью резания vф и продольную подачу sпр вдоль оси заготовки, которая вращается с круговой подачей sкр (в некоторых моделях станков движение продольной подачи сообщается не фрезе, а заготовке). Движения sпр и sкр должны быть строго согласованы между собой: продольная подача за время одного оборота заготовки должна быть равна величине шага нарезаемой резьбы. Такое согласование обеспечивается подбором сменных шестерен гитары, устанавливаемых при настройке станка. В начале процесса обработки фрезе сообщают поперечное движение для установки ее на глубину профиля резьбы.
Станки, работающие гребенчатыми фрезами, применяют для нарезания как наружных, так и внутренних резьб (рис. 4.34, б). Гребенчатую фрезу 1, вращающуюся со скоростью резания vф, подводят к заготовке 2, вращающейся со скоростью круговой подачи sкр, и осуществляют врезание на глубину профиля резьбы с радиальной подачей sп при одновременной продольной подаче sпр, равной шагу нарезаемой резьбы. После нарезания фрезу быстро отводят и воз-
125
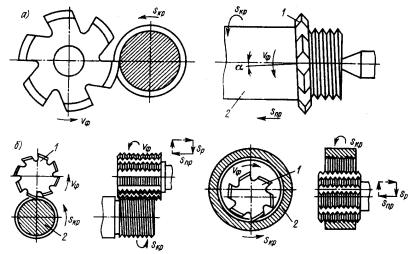
вращают в исходное положение (в некоторых моделях станков движения врезания, продольной подачи и отвода совершаются заготовкой).
Гребенчатая фреза представляет собой как бы набор дисковых фрез, поэтому витки по всей длине резьбы обрабатываются одновременно, в результате процесс фрезерования значительно ускоряется. Минимальная длина гребенчатой фрезы должна быть на 2-3 шага больше длины фрезеруемой резьбы.
Рис. 4.34. Схемы фрезерования резьбы
Резьбошлифовальные станки применяют для чистовой обра-
ботки точных резьб, предварительно нарезанных на других станках. Схемы резьбошлифования аналогичны схемам резьбофрезерования, только вместо резьбовых фрез используются профильные шлифовальные круги.
4.8. Зубообрабатывающие станки
Предназначены для обработки зубьев зубчатых колес. По технологическому назначению делятся на зуборезные и зубоотделоч-
ные.
Нарезание зубьев заключается в обработке впадин между ними
126
(рабочих боковых поверхностей и дна) по всей ширине зубчатого колеса. В зависимости от способа образования зубьев колеса различают два метода зубонарезания: метод копирования и метод обката (огибания).
Зуборезные станки, работающие по методу копирования.
При обработке по методу копирования режущая часть фасонного зуборезного инструмента (фрезы, резцы, протяжки) имеет профиль, точно соответствующий профилю нарезаемых впадин. В процессе зубонарезания инструмент, перемещаясь вдоль оси заготовки, переносит (копирует) свой профиль по всей длине зуба. Обычно работа по методу копирования позволяет одновременно нарезать одним инструментом только одну впадину колеса. Для обработки следующей впадины требуется поворот заготовки на один зуб, т.е. на 1/z часть окружности, осуществляемый с помощью делительного устройства станка.
Нарезание по методу копирования цилиндрических прямозубых и косозубых колес, а также прямозубых конических колес производят чаще всего дисковыми модульными фрезами на гори- зонтально-фрезерном станке (рис. 4.35, а и б).
Обработка зубьев дисковыми и пальцевыми модульными фрезами на консольно-фрезерных станках является неточной и малопроизводительной. Погрешность профиля инструмента полностью переносится на обрабатываемую заготовку. Неточность делительной головки вносит дополнительные погрешности. Низкая производительность обусловливается прерывистым характером обработки, а также большой величиной врезания. В силу указанных недостатков этот метод применяется в единичном и мелкосерийном производствах, а также при ремонтных работах. Единственным, но существенным преимуществом этого метода является то, что для его осуществления не требуется специального оборудования и оснастки.
В условиях крупносерийного и массового производства метод копирования применяют для предварительной обработки, используя специальные станки, работающие по полуавтоматическому циклу,
например, зубофрезерные полуавтоматы, зубодолбежные полуавтоматы, специализированые протяжные станки.
Весьма производительными являются зубодолбежные полуавтоматы для обработки цилиндрических зубчатых колес небольших размеров. Обработка колеса ведется одновременно долблением всех впадин между зубьями специальными многорезцовыми головками.
127
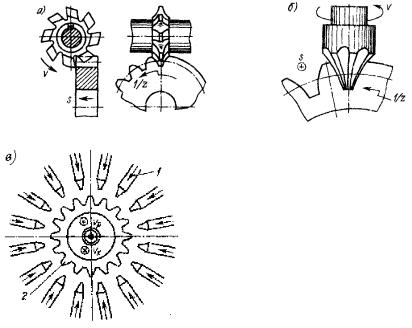
Схема многорезцового долбления представлена на рис. 4.35, в. Резцы 1, имеющие профиль впадины нарезаемого колеса, расположены в головке радиально по отношению к заготовке 2. Во время работы заготовке сообщают главное возвратно-поступательное движение со скоростями vр – рабочего хода и vх – холостого хода в вертикальном направлении, а резцам – одновременное прерывистое движение радиальной подачи. За несколько двойных ходов резцы врезаются на полную глубину впадины и нарезание зубьев заканчивается. Недостаток метода – необходимость иметь головку, соответствующую параметрам каждого обрабатываемого колеса.
Рис. 4.35. Схемы зубонарезания по методу копирования
Зубонарезание по методу обката заключается в механическом воспроизведении беззазорного зубчатого, реечного или червячного зацепления. Режущий инструмент имеет форму зубчатого колеса, зубчатой рейки или червяка, т.е. такой детали, которая могла бы ра-
128
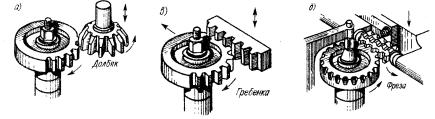
ботать в паре с нарезаемым колесом. В процессе обработки инструменту и заготовке сообщают согласованные движения, воспроизводящие соответствующее зацепление (движение обката). Одновременно режущий инструмент совершает рабочее движение резания.
По сравнению с методом копирования метод обката обеспечивает более высокую производительность и точность обработки благодаря непрерывности процесса, а также тому, что при обкате одновременно нарезается несколько впадин, и каждая из них профилируется целым рядом зубьев режущего инструмента.
При зубонарезании по методу обката профили режущих кромок инструмента, перемещаясь, занимают относительно профилей зубьев нарезаемого колеса ряд последовательных положений, срезая при этом материал заготовки в тех местах, где должны быть впадины между зубьями. Эвольвентные профили обрабатываемых зубьев возникают при этом как огибающие ряды последовательных положений режущих кромок (или ряда последовательных срезов материала заготовки). Поэтому такой метод профилирования зубьев называют еще методом огибания.
а б в Рис. 4.36. Схемы нарезания цилиндрических колес по методу обката
При зубонарезании по методу обката одним инструментом можно нарезать колеса данного модуля с любым числом зубьев. На рис. 4.36 приведены схемы зубонарезания: зубодолбление дисковым зуборезным долбяком (а), зубодолбление зуборезной гребенкой (б), зубофрезерование червячной фрезой (в).
По методу обката работают специализированные зубодолбежные, зубофрезерные и зубострогальные станки. Все они являются полуавтоматами и применяются в условиях серийного и массового производств.
129
Зубоотделочные станки. Отделочная обработка нарезанных зубчатых колес производится для достижения большей точности размеров и меньшей шероховатости поверхности зубьев с целью повышения плавности и бесшумности работы зубчатых передач и их долговечности. К числу зубоотделочных операций относятся шевингование и обкатка, зубошлифование, притирка и зубохонингование. Эти операции выполняют на специализированных зубоотделочных станках.
4.9. Станки для электрофизических и электрохимических методов обработки
Этими методами обрабатываются заготовки из материалов с низкой обрабатываемостью резанием (твердые и жаропрочные сплавы, титановые, вольфрамовые и др.), а также детали с размерами и формами поверхностей, обработка которых обычными механическими методами затруднительна (детали с малыми криволинейными отверстиями, узкими прорезями, с углублениями сложной формы).
Работа электроэрозионных станков основана на использовании явления электрической эрозии – направленного разрушения токопроводящих материалов в результате теплового воздействия импульсных электрических разрядов между инструментом и заготовкой. Основными разновидностями электроэрозионного метода являются электроискровая и электроимпульсная обработка.
При обработке на электроискровом станке для прошивки отверстий (рис. 4.37, а) заготовку 2 погружают в бак с жидкостью и соединяют с положительным полюсом, выполняющим функции анода. Электрод (инструмент) 4, являющийся катодом, соединяют с отрицательным полюсом и укрепляют на ползуне 5, имеющем вертикальное перемещение по направляющим 6. Заготовка 2, стол 1, на котором ее закрепляют, корпус бака и станина станка электрически соединены между собой и заземлены, так что их электрический потенциал всегда равен нулю. Это необходимо для безопасности работы на станке.
Если, опустив ползун 5, прикоснуться электродом 4 к заготовке 2, то в электрической цепи пойдет электрический ток от отрицательной клеммы 7 генератора Г к положительной клемме 8. В электрическую цепь включен резистор 11. Это катушка из длинной тонкой проволоки. Изменяя сопротивление, можно регулировать силу тока,
130