
Методическое пособие 581
.pdf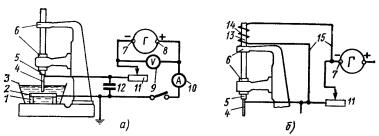
контролируя ее по амперметру 10.
Для того чтобы получить импульсные разряды, непрерывно следующие друг за другом, между электродом 4 и заготовкой 2 в электрическую схему станка включается конденсаторная батарея 12. Ее включают параллельно заготовке 2 и электроду 4. Если замкнуть выключатель электрической цепи при разведенных электродах станка, то в первый момент стрелка амперметра 10 резко отклонится и постепенно возвратится на 0. Стрелка вольтметра 9, наоборот, плавно отклонится от того значения напряжения, которое создается генератором. Это означает, что произошла зарядка конденсаторов. Теперь можно приблизить электрод к заготовке. Как только расстояние между ними станет небольшим, произойдет электрический разряд. При этом вся энергия, накопленная в конденсаторах, разрядится в промежутке между электродом и заготовкой, и чем больше заряд энергии, тем больше будет электрическая эрозия анода (заготовки).
Рис. 4.37. Станок для электроискровой прошивки отверстий (а) и соленоидный регулятор (б)
После разряда электрический ток между электродом и деталью исчезнет, так как вся энергия, накопленная в конденсаторах, израсходована, и снова начинается зарядка конденсаторной батареи. Следующий разряд произойдет, как только конденсаторы зарядятся. Этот процесс происходит непрерывно, импульсные разряды следуют один за другим до тех пор, пока не закончится обработка.
Во время обработки электрод 4 не должен касаться заготовки, иначе произойдет короткое замыкание. Между электродом 4 и заготовкой всегда должен поддерживаться небольшой, так называемый искровой промежуток. Это достигается с помощью различных устройств. Наиболее простое устройство — соленоидный регулятор (рис. 4.37, б). К верхнему концу ползуна 5 прикреплен стальной стержень-сердечник 13, который входит внутрь катушки (соленои-
131
да) 14, присоединенной к основной цепи. Присоединение сделано по разным сторонам резистора 11 так, что концы проводов 15 находятся под разными потенциалами.
Когда электрод 4 прикоснется к заготовке, электрическая цепь станка замкнется, и в ней потечет электрический ток. Тогда на концах катушки 14 создается разность потенциалов, и в ней также потечет электрический ток. Сердечник 13 намагнитится и втянется в катушку 14, т. е. поднимется, поднимая вместе с собой ползун 5 и электрод 4. Искровой промежуток 3 между электродом 4 и заготовкой 2 восстановится, и основная электрическая цепь окажется разорванной — ток в ней исчезнет. Одновременно исчезнет ток и в катушке соленоида. Сердечник 13 размагнитится, перестанет втягиваться в катушку и под действием собственной массы опустится. Вместе с ним опустятся ползун 5 и электрод 4. Между электродом и заготовкой снова произойдет электрический разряд. По мере углубления отверстия электрод будет опускаться под действием силы тяжести.
Так будет продолжаться, пока идет процесс прошивки отверстия. Соленоидный регулятор автоматически постепенно опускает электрод по мере увеличения глубины отверстия. Если электрод можно сравнить с инструментом, то соленоидный регулятор может быть уподоблен механизму подачи. Электроды, применяемые при электроискровой прошивке, делают из мягкой латуни. Электрод должен иметь профиль, подобный профилю прошиваемого отверстия. Если диаметр отверстия больше 6 мм, то электрод лучше делать пустотелым. Электроискровой прошивкой удается также изготовлять отверстия с криволинейной осью.
Универсальные электроискровые станки обычно имеют вертикальную компоновку (рис. 4.38). Автоматический регулятор подач 7 сообщает вертикальные перемещения электроду-инструменту 8. Ванну 4 с заготовкой 9, установленной на столе 3, можно перемещать в вертикальном направлении с помощью электродвигателя. Суппорт 5 при обработке отверстий с криволинейной осью поворачивается вокруг горизонтальной оси. Поперечный суппорт 6 перемещается по направляющим продольного суппорта. Продольный суппорт 5 установлен на направляющих 2 станины. Механизмы станка находятся внутри корпуса.
132
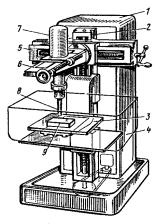
Рис. 4.38. Универсальный электроискровой станок
Электроискровый метод обработки металлов вытесняется электроимпульсной обработкой. Это объясняется тем, что электроискровая обработка имеет ряд серьезных недостатков: производительность сравнительно низка; износ электрода-инструмента относительно большой (например, износ латунных электродов составляет 25—30 % объема металла, снятого с заготовки), что значительно удорожает этот вид обработки и затрудняет получение необходимой точности. Кроме того, электроискровая обработка требует большого расхода электроэнергии. Электроимпульсный способ обработки металлов не лишен полностью недостатков электроискрового метода, однако является более производительным.
Вэлектрической схеме (рис. 4.39) электроимпульсного станка
отсутствуют конденсаторы, которые были нужны в электроискровом станке для получения импульсных разрядов.
Вэлектроимпульсном станке импульсные разряды, необходимые для электрической эрозии, создаются (генерируются) в специальном генераторе импульсов. Роль такого генератора импульсов играют преобразователь 1 и селеновый выпрямитель 2. Преобразователь изменяет (преобразует) напряжение и частоту переменного тока; его подключают к заводской сети (напряжение 380 В, частота 50 Гц). На выходных зажимах преобразователя получают ток с более низким напряжением (50 В) и повышенной частотой (490 Гц). Селеновый выпрямитель 2 пропускает ток только в одном направлении. Таким образом, в течение 1с получают 490 импульсов. При этом
133
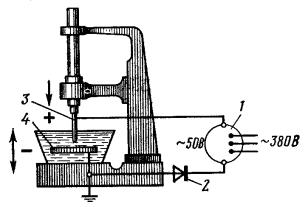
между электродом 3 и заготовкой 4 происходят электрические разряды. Заготовке сообщается колебательное движение в направлении подачи, что предохраняет электроды от короткого замыкания.
Рис. 4.39. Станок для электроимпульсной обработки
В отличие от электроискровой обработки при электроимпульсном процессе заготовка соединена с катодом электрической цепи, а инструмент — с анодом. Обработку ведут в жидкой среде (в маслах низкой вязкости: индустриальное 12, трансформаторное, а также в керосине и др.). Электроды изготовляют из меди, алюминия, чугуна, графита и т. д. Процесс электроимпульсной обработки основан на расплавлении малых объемов металла электродов в тех местах, где между ними проскакивают электрические разряды. Каждый разряд снимает очень небольшое количество металла, но так как разряды происходят очень часто, один за другим, то общий объем металла достаточно велик. По мере съема металла электрод-инструменту сообщается подача.
Электроимпульсный метод позволяет производить обработку на небольших площадях (до 180 см2) с высокой производительностью (4000 мм3/мин).
Ультразвуковые станки применяются для размерной обработки заготовок из хрупких и твердых материалов. Преимущество: возможность обработки не только токопроводящих материалов, но также полупроводников и диэлектриков. Ультразвуковой метод особенно эффективен при обработке таких материалов, как стекло, ке-
134
рамика, кварц, германий, кремний. Его также можно использовать для обработки закаленных сталей и твердых сплавов.
Метод основан на разрушении материала заготовки ударами абразивных зерен, получающих энергию от инструмента, совершающего продольные колебания с частотой 16-30 кГц и амплитудой 10-50 мкм. Для получения ультразвуковых колебаний инструмента чаще всего применяют магнитострикционные преобразователи.
Работа ультразвукового станка заключается в следующем. В зону между заготовкой и вибрирующим пуансоном (инструментом), который очень близко подходит к заготовке, но не касается ее, поступает абразивный порошок, находящийся в жидкости во взвешенном состоянии. От воздействия вибратора (преобразователя) абразивные зерна с большой силой ударяются о поверхность заготовки и с большой скоростью выбивают частицы материала (стружку). Одновременно пуансон постепенно опускается в выдолбленное таким способом пространство, и процесс продолжается.
Электрохимическая обработка материалов основана на химических процессах, протекающих в результате прохождения постоянного электрического тока через цепь, образованную электродами и находящейся между ними жидкостью (электролитом), проводящей ток. При электрохимической обработке происходит растворение и удаление с заготовки слоя металла, переходящего в неметаллическое состояние в результате образования химических соединений. Такая обработка характеризуется малой шероховатостью обработанной поверхности, высокой производительностью и большой энергоемкостью процесса. Способ используют для образования отверстий и полостей, а также для удаления заусенцев.
4.10. Станки с программным управлением
Металлорежущие станки с программным управлением представляют собой разнообразную и наиболее совершенную группу машин, в которой широко используют средства автоматики и электроники, электрические, механические, гидравлические, пневматические и другие устройства. Программное управление станками за сравнительно короткий срок бурно развивалось и стало основным направлением автоматизации металлообработки. Оно обеспечивает возможность быстрой переналадки станка, что дает возможность создавать экономически выгодные системы автоматизации для мел-
135
косерийного и единичного производства.
По виду управления станки с программным управлением делят-
ся на станки с системами циклового программного управления и станки с системами числового программного управления. В ос-
новном распространены станки с числовым программным управлением (ЧПУ).
Числовое программное управление станком — управление обработкой заготовки на станке по управляющей программе, в которой данные заданы в цифровой форме. Совокупность функционально взаимосвязанных и взаимодействующих технических и программных средств, обеспечивающих числовое программное управление станком, называют системой числового программного управления.
Числовое программное управление станками по технологическим признакам подразделяют на позиционное, контурное, адаптивное и групповое.
Позиционное управление — числовое программное управление станком, при котором перемещение его рабочих органов происходит в заданные точки, причем траектории перемещения не задаются. Такое управление применяют в основном в сверлильных и расточных станках для обработки плоских и корпусных деталей с большим числом отверстий.
Контурное управление — числовое программное управление станком, при котором перемещение его рабочих органов происходит по заданной траектории и с заданной скоростью для получения необходимого контура обработки. ЧПУ для контурной обработки позволяет осуществлять непрерывное управление скоростями рабочих движений инструмента относительно заготовки и обеспечивает их заданные положения в каждый момент времени в соответствии с профилем детали, т. е. обеспечивает автоматический обход режущего инструмента по заданному контуру детали. Для обработки плоских деталей используют системы контурной двухкоординатной, а для объемных деталей — трехкоординатной обработки.
Адаптивное управление — числовое программное управление, при котором обеспечивается автоматическое приспособление процесса обработки заготовки к изменяющимся условиям обработки по определенным критериям.
Групповое управление — числовое программное управление группой станков от ЭВМ, имеющей общую память для хранения управляющих программ, распределяемых по запросам от станков.
136
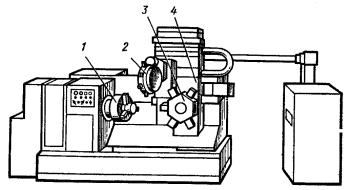
В зависимости от основных операций обработки станки с ЧПУ объединены в различные технологические группы.
Токарные станки с ЧПУ являются наиболее многочисленной группой в парке станков с ЧПУ. Их выпускают в следующих исполнениях: центровые, патронные, патронно-центровые и карусельные. В основном токарные станки имеют горизонтально расположенную ось шпинделя. Исключение составляют двухсуппортные станки и карусельные станки для обработки крупных деталей. По расположению направляющих суппорта токарные станки с ЧПУ выпускают с горизонтальным, вертикальным или наклонным расположением.
Токарные станки имеют две управляемые координаты: Z — вдоль оси шпинделя; Х — перпендикулярно этой оси. Перемещение по оси Z осуществляется кареткой станка, вдоль оси Х— поперечными салазками суппорта. На поперечных салазках установлены либо резцедержатель (при смене инструмента из магазина), либо револьверная поворотная инструментальная головка. Головка может иметь два различных положения оси поворота: совпадающее по направлению с осью 2 и перпендикулярное плоскости ХZ. Существует тенденция оснащения станков не одной, а двумя револьверными головками (рис. 4.40).
Рис. 4.40. Токарный станок с ЧПУ с двумя револьверными головками
Одна головка 2 имеет ось поворота, совпадающую по направлению с осью Z и используемую для обработки наружных поверхностей. Другая головка 3 имеет ось поворота, перпендикулярную плоскости ХZ, и инструменты, закрепленные в ней, предназначены
137
для обработки внутренних поверхностей. Располагают головки по разные стороны от оси шпинделя с некоторым сдвигом относительно друг дуга: головка 2 установлена на поперечные салазки 4 ближе переднему торцу шпинделя 1, а головка 3 удалена от него. Такое размещение способствует лучшему доступу инструментов к обрабатываемой заготовке. На станках с двумя головками в работе могут участвовать 10—16 режущих инструментов.
Расточные и сверлильные станки с ЧПУ можно разделить на две основные группы: с горизонтальным или вертикальным расположением шпинделя. На расточных станках фрезеруют плоскости и пазы, сверлят и зенкеруют отверстия, растачивают отверстия, подрезают торцы, разрезают резьбу метчиками.
На расточных станках с вертикальным расположением шпинделя целесообразно обрабатывать плоские заготовки (планки, плиты, фланцы, рычаги и др.), на горизонтально-расточных — корпусные детали. Для обработки заготовки с разных сторон на станках с вертикальным шпинделем необходимо иметь различные ее установы. Обработку с четырех боковых сторон на горизонтальнорасточном станке можно выполнять при одной установке заготовки, осуществляя поворот стола.
Сверлильные станки с ЧПУ изготовляют в двух исполнениях:
вертикально-сверлильные и радиально-сверлильные. На них можно выполнять разнообразные работы: сверление, зенкование, зенкерование, развертывание, нарезание резьб, фрезерование и т. д. Наличие крестового стола, возможность работать последовательно несколькими инструментами, а в некоторых случаях и многоинструментальными головками значительно расширяют возможности станка.
Фрезерные станки с ЧПУ компонуют по типу вертикальных и горизонтальных консольных и бесконсольных одно- и двухстоечных
станков. Горизонтально-фрезерные станки оснащают поворотным столом, управляемым по программе.
На фрезерных станках с вертикальным шпинделем преимущественно изготовляют плоскостные и коробчатой формы детали небольших габаритных размеров, а также и сложные поверхности плоских и объемных кулачков, шаблонов и других деталей. На станках с горизонтальным шпинделем обрабатывают поверхности корпусных деталей, расположенные в различных плоскостях.
В соответствии с классификацией систем управления принята следующая система обозначения моделей станков с ПУ. К основ-
138
ному обозначению модели станка добавляют один из следующих индексов: Ц—станки с цикловым управлением; Ф1—станки с цифровой индексацией положения, а также станки с цифровой индексацией и ручным вводом данных; Ф2 — станки с позиционными СЧПУ; ФЗ — станки с контурными СЧПУ; Ф4 — станки со смешанными системами ЧПУ.
Кроме того, введены индексы, отражающие конструктивные особенности станков, связанные с автоматической сменой инструмента: Р — смена инструмента поворотом револьверной головки; М - смена инструмента из магазина. Индексы Р и М записывают перед индексами Ф2 и ФЗ: например, РФ2 — станки с позиционной СЧПУ с револьверной инструментальной головкой; МФЗ — станки с контурной СЧПУ со сменой инструмента из магазина; МФ4 — станки со смешанными системами управления и магазином инструментов.
4.11. Многоцелевые станки
Многоцелевые станки (МЦ) — станки с числовым программным управлением и автоматической сменой инструмента для выполнения нескольких различных видов обработки резанием. Кроме МЦ существуют и другие станки с ЧПУ с автоматической сменой режущих инструментов, которые не называют многоцелевыми. В чем же различие между ними?
Многоцелевые станки отличаются особо высокой концентрацией обработки. На них производят черновую, получистовую и чистовую обработку сложных корпусных заготовок, содержащих десятки обрабатываемых поверхностей, выполняют самые разнообразные технологические переходы: фрезерование плоскостей, уступов, канавок, окон, колодцев; сверление, зенкерование, развертывание, растачивание гладких и ступенчатых отверстий; растачивание отверстий инструмента с тонким регулированием на размер; обработку наружных и внутренних поверхностей и др.
Для осуществления этих операций на станке необходимо иметь большой запас металлорежущих инструментов. У станков с ЧПУ и автоматической сменой инструмента запас инструментов создается обычно в револьверных головках. Среди них фрезерные и сверлильные станки, предназначенные для изготовления главным образом таких корпусных и плоских деталей, для обработки которых достаточно иметь пять—десять различных инструментов. Многоцелевые
139
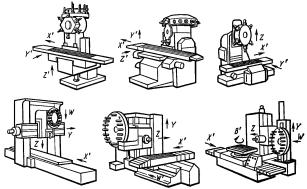
станки имеют инструментальные магазины с запасом в 15—30, а при необходимости в 50—100 и более инструментов.
Еще одна важная особенность большинства многоцелевых станков — наличие стола или делительного приспособления с периодическим или непрерывным (по программе) делением. Это обязательное условие для обработки заготовки с нескольких сторон без переустановки. Станки новых конструкций оснащают дополнительными столами и устройствами для автоматической смены заготовок. Заготовки предварительно закрепляют на приспособлении-спутнике, и вместе с ним они попадают с дополнительного стола на основной. Установку заготовки в спутник и снятие обработанной детали производят во время работы станка. Таким образом, вспомогательное время, затрачиваемое на загрузку станка, сводится к минимуму.
Многоцелевые станки имеют чаще всего контурную систему управления, позволяющую обрабатывать разнообразные криволинейные поверхности, фрезеровать отверстия и т. д. Они отличаются широким диапазоном бесступенчатого регулирования частоты вращения шпинделя (заготовки) и подач, высокими (до 8—12 м/мин) скоростями быстрых (вспомогательных) ходов, особо высокой жесткостью и надежностью.
Многоцелевые станки для обработки корпусных деталей можно разделить на две группы, характеризуемые расположением оси шпинделя относительно рабочей поверхности стола: с перпенди-
кулярным (вертикальным) расположением шпинделя к поверхности стола; с параллельным (горизонтальным) расположением шпинделя
относительно стола (рис. 4.41).
Рис. 4.41. Компоновки многоцелевых станков
140