
2598
.pdf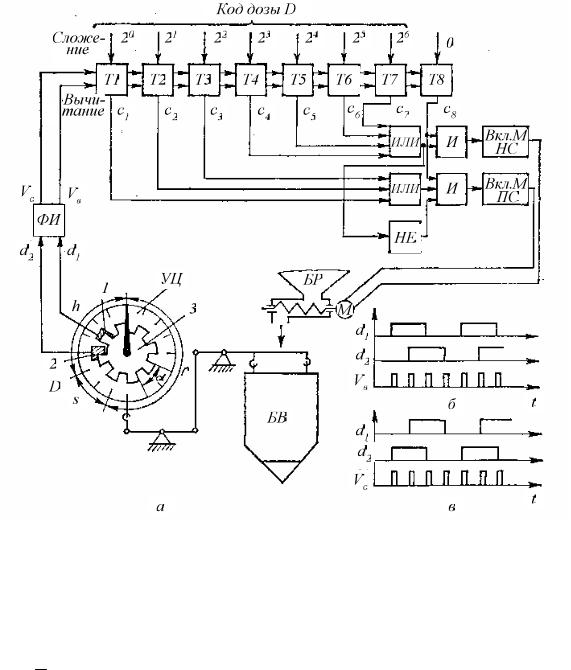
Рис. 3.53. Цифровая автоматическая система управления дозатором:
а – структурная схема управления; б – формирование импульсов при прямом ходе стрелки; в – формирование импульсов при обратном ходе стрелки
На основании указанных временных диаграмм можно записать алгоритмы формирования импульсов унитарного кода:
Vâ d2 Im p 0 1 d1 d2 Im p 1 0 d1 d1 Im p 0 1 d2
|
d |
1 Im p 1 0 d2; |
|
(3.35) |
||
|
|
|
|
|
|
|
Vc |
d |
1 Im p 0 1 d2 d1 Im p 1 0 d2 d2 Im p 0 1 d1 |
|
|||
|
|
|
|
|
|
|
d2 Im p 1 0 d1. |
|
|||||
|
|
Импульсы унитарного кода поступают на вычитающий и суммирующий входы реверсивного двоичного счетчика. Старшие разряды счетчика Т4–Т7 соответствуют зоне r номинального режима загрузки, младшие разряды Т1–Т3 соответствуют зоне s режима досыпки,
870

дополнительный разряд знака Т8 – зоне h перегрузки весового бункера. В начале каждого цикла дозирования в триггеры основных разрядов вводится в двоичном коде число, соответствующее требуемой дозе материала, а триггер дополнительного разряда устанавливается на нуль.
Алгоритмы формирования командных сигналов номинального режима М1 и режима пониженной скорости M2 можно записать так:
M1 c8 c4 c5 c6 c7 ; |
|
|
|
|
|
|||||||||||
|
|
|
|
(3.36) |
||||||||||||
|
|
|
|
|
|
|
|
|
|
|
|
|
|
|
|
|
M |
2 |
|
c |
8 |
c |
4 |
c |
5 |
c c |
c c |
2 |
c |
3 |
. |
|
|
|
|
|
|
|
6 |
7 |
1 |
|
|
|
Когда стрелка циферблатного указателя пройдет зону r, все триггеры старших разрядов переключатся на нуль, а триггеры младших разрядов – на единицу. При этом снимается командный сигнал М1 и появляется М2, в результате чего двигатель М питателя включается на пониженную скорость.
Когда стрелка пройдет зону s, все триггеры счетчика переключаются на нуль и двигатель М отключается. Если вследствие динамической перегрузки стрелка окажется в зоне h, то переключается на единицу триггер дополнительного разряда и прекращается управляющее воздействие на двигатель М.
3.4.4. Динамические и статические характеристики дозаторов непрерывного действия
Весовой дозатор непрерывного действия (питатель, грузоприемное устройство) – объект регулирования – и регулятор производительности (датчик весового расхода, регулирующий блок, исполнительный механизм) представляют собой автоматическую систему регулирования, предназначенную для поддержания постоянства весового расхода Q потока дозируемых сыпучих материалов и жидкостей. Возмущающими воздействиями здесь являются колебания объемной массы материала во времени, изменение задания и нестабильность источников питания (давления воздуха, напряжения, тока). Несоответствие между заданной и выходной производительностью дозатора устраняется управляющим воздействием на регулирующий орган объекта – питатель.
При дозировании сыпучих материалов используют питатели принудительного действия, из которых на предприятиях стройиндустрии применяют ленточные питатели с регулированием сечения материала на ленте или скорости ленты, шнековые питатели с регулированием скорости двигателя и вибрационные лотковые питатели с регулированием амплитуды колебаний лотка. Статические и динамические характеристики указанных питателей приведены в табл. 3.8.
871
Таблица 3.8
Статические и динамические характеристики питателей
Тип питателя |
Статическая характеристика |
|
Динамическая |
|||||||||||||||||
|
|
|
|
|
|
|
|
|
|
|
|
|
характеристика |
|||||||
Ленточный питатель |
Q |
2 |
|
vf a |
2 |
b |
2 |
, |
|
|
|
|
L |
|
||||||
с регулированием |
|
|
|
|
|
Q QВХ |
t |
|
|
, |
||||||||||
3 |
|
|
|
|||||||||||||||||
|
|
|
|
|||||||||||||||||
сечения (парабола со |
|
|
|
|
|
|
|
|
|
|
|
|
|
|
v |
|
||||
где – объемная масса, кг/м3; |
где L – рабочая длина |
|||||||||||||||||||
срезанным сверху |
||||||||||||||||||||
сектором) |
v – скорость ленты, м/с; |
ленты питателя, м |
|
|||||||||||||||||
|
f – коэффициент трения; |
|
|
|
|
|
|
|
||||||||||||
|
a – ширина нижнего слоя, м; |
|
|
|
|
|
|
|
||||||||||||
|
b – ширина верхнего слоя, м |
|
|
|
|
|
|
|
||||||||||||
Ленточный питатель |
Q |
2 |
f a2 |
b2 v |
Q kv |
|
|
|
|
|
||||||||||
с регулированием по |
|
|
|
|
|
|
|
|||||||||||||
|
|
|
|
|
|
|
|
|
||||||||||||
скорости |
|
|
3 |
|
|
|
|
|
|
|
|
|
|
|
|
|
|
|
||
|
|
|
|
|
|
|
|
|
|
|
|
|
|
|
|
|
|
|
||
Шнековый питатель |
Q |
D |
2 |
s n, |
|
|
Q kn 1 e |
t / T |
, |
|||||||||||
|
|
|
|
|
|
|
||||||||||||||
|
|
|
|
|
где Т – постоянная времени |
|||||||||||||||
|
|
|
|
|
|
4 |
|
|
|
|
|
|
||||||||
|
где D – диаметр шнека, м; |
электропривода, с |
|
|||||||||||||||||
|
s – шаг шнека, м; |
|
|
|
|
|
|
|
|
|
||||||||||
|
n – частота вращения, 1/с; |
|
|
|
|
|
|
|
||||||||||||
|
– коэффициент заполнения |
|
|
|
|
|
|
|
||||||||||||
|
материала |
|
|
|
|
|
|
|
|
|
|
|
||||||||
Вибрационный |
Q F mcos , |
|
|
|
|
|
L |
|
||||||||||||
лотковый питатель |
где F – площадь выходного |
Q Q |
ВХ |
t |
|
|
, |
|||||||||||||
|
||||||||||||||||||||
|
|
|
|
v |
|
|||||||||||||||
|
отверстия питателя, м2; |
где L – рабочая длина |
||||||||||||||||||
|
ω – угловая частота колебаний, |
|||||||||||||||||||
|
лотка, м; |
|
|
|
|
|
||||||||||||||
|
рад/с; |
|
|
|
|
|
|
|
v – скорость перемещения |
|||||||||||
|
m – амплитуда колебаний лотка, |
|||||||||||||||||||
|
м; |
|
|
|
|
|
|
|
|
|
|
материала, м/с |
|
|
|
|||||
|
|
|
|
|
|
|
|
|
|
|
|
|
|
|
|
|
|
|||
|
– угол между тяговым |
|
|
|
|
|
|
|
||||||||||||
|
усилием вибратора и |
|
|
|
|
|
|
|
||||||||||||
|
направлением движения лотка, |
|
|
|
|
|
|
|
||||||||||||
|
град |
|
|
|
|
|
|
|
|
|
|
|
|
|
|
|
|
|
В дозаторах непрерывного действия, предназначенных для дозирования сыпучих материалов, грузоприемными устройствами являются ленточные конвейеры с встроенной весовой роликоопорой. В этом случае погрешность автоматического дозирования определяется непостоянством скорости конвейера vк, длины его загрузки Lк и мгновенного значения нагрузки Рк материала на ленте конвейера.
Ленточный конвейер служит для передачи нагрузки материала на силоизмерительный элемент и, следовательно, может рассматриваться в системе автоматического регулирования дозатора как преобразователь, входная величина которого – производительность питателя QП, а выходная
– нагрузка материала Рк. Тогда динамические свойства грузоприемного
872

устройства отображаются на структурной схеме системы с помощью двух звеньев – W1(p) и W2(р).
Передаточная функция первого звена отображает поступление материала на движущийся с постоянной скоростью конвейер:
W1( p) 1 . p
Передаточная функция второго звена отображает ссыпание материала с конвейера, в результате чего уменьшается нагрузка материала:
W2( p) 1 e p к , p
где τк – время перемещения материала от входа до выхода конвейера. Поскольку входная величина для обоих звеньев – производительность
питателя QП, а нагрузка материала Рк (выходная величина грузоприемного устройства) определяется алгебраической суммой выходных сигналов звеньев, то результирующая передаточная функция записывается по правилу параллельного соединения:
W( p) |
1 |
1 e p к . |
(3.37) |
|
|||
|
p |
|
3.4.5. Автоматическое управление дозаторами непрерывного действия
Для автоматического управления дозаторами непрерывного действия могут использоваться регуляторы различных типов: позиционные (Пз), пропорциональные, или статические (П), пропорционально-интегральные, или изодромные (ПИ), и пропорционально-интегральные с воздействием по производной (ПИД). Выбор типа регулятора производится в зависимости от динамических характеристик дозатора (как объекта регулирования) и требований, предъявляемых к системе.
При оптимальных настройках системы регулирования весовые дозаторы непрерывного действия обеспечивают дозирование массы материалов с интегральной погрешностью, выраженной в процентах максимальной производительности дозатора (0,5–2%) за время 3–6 мин. Внутри этого интервала времени мгновенные отклонения производительности дозатора могут отличаться и зависят от возмущающего воздействия.
Рассмотрим типовые системы автоматического регулирования производительности дозаторов непрерывного действия.
Весовой дозатор непрерывного действия для песка и щебня (рис. 3.54) состоит из конвейера 1, подающего материал в смеситель; конвейера 2 дозатора, связанного с коромыслом 4 весов; электромагнитного
873
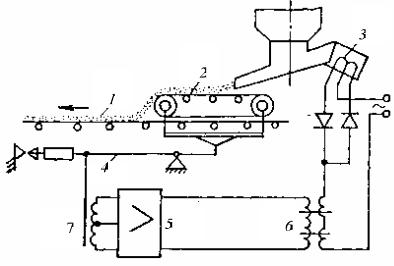
вибратора 3; фазочувствительного электронного усилителя 5, усиливающего сигнал от индуктивного датчика 7, сердечник которого соединен с коромыслом весов, и дросселя насыщения 6, подключенного к источнику питания последовательно с управляющей обмоткой электромагнитного вибратора.
При изменении положения коромысла весов соответственно изменяется ток подмагничивания дросселя насыщения, что в свою очередь приводит к изменению тока управления электромагнитного вибратора и, следовательно, производительности питателя дозатора.
Аналогично построена схема управления дозатором цемента со шнековым питателем (рис. 3.55). В этой схеме дроссель насыщения 7 подключен к источнику питания переменного тока последовательно с якорем электродвигателя 4 привода шнека. Кроме того, в цепь якоря электродвигателя включен выпрямитель, обеспечивающий питание якоря постоянным током. При изменении положения коромысла весов 5 соответственно изменяется число оборотов шнека 3 и скорость выдачи материала из бункера на конвейер 2 дозатора.
Рис. 3.54. Схема автоматического управления дозатором с вибропитателем
Дозатор, предназначенный для непрерывной подачи жидких компонентов технологических смесей (рис. 3.56), имеет весовой бак 9 со сливной трубой 4, насосом 10 и приводом 8.
Весовая система состоит из грузоприемного 5 и передаточного 1 рычагов, воспринимающих усилие от весового бака и передающих его на циферблатный пружинный указатель 2.
874
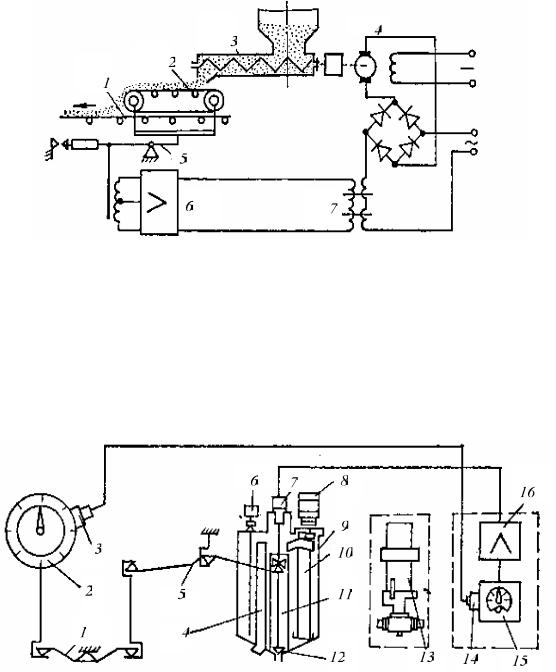
Электромагнитный вентиль 13 обеспечивает циклическую заливку бака 9 по сигналам уровнемера 6. Работа дозатора происходит следующим образом. По шкале задатчика 15 назначается необходимая производительность.
Рис. 3.55. Схема автоматического управления дозатором со шнековым питателем
Сельсин-датчик 14, жестко связанный с выходным валом задатчика 15, вращается с частотой, пропорциональной заданной производительности, а сельсин-датчик 3, связанный с осью стрелки циферблатного указателя 2, вращается с частотой, пропорциональной частоте вращения стрелки и, следовательно, истинному массовому расходу жидкости в единицу времени.
Рис.3.56. Автоматический дозатор для непрерывного дозирования жидких компонентов
При синхронной работе сельсинов их угловое рассогласование равно нулю. В этом случае истинный массовый расход компонента соответствует заданному. При отклонении истинной производительности от заданной произойдет угловое рассогласование сельсинов, в результате чего в их цепи возникает ток. Усиленный электронным усилителем 16 ток сельсинов
875
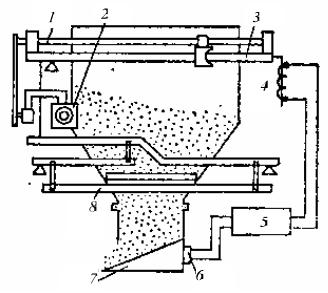
приведет во вращение реверсивный электродвигатель 7 привода в сторону, корректирующую значение истинной производительности, увеличивая или уменьшая проходное сечение 12 клапана 11.
По такому же принципу работает бункерный дозатор (рис. 3.57) для дозирования сыпучих материалов с электронным пропорциональным регулятором 5 и установкой 2 для возврата стрелки на нуль.
Рис. 3.57. Автоматический бункерный дозатор непрерывного действия
Производительность дозатора устанавливается заданием скорости привода ходового винта 1 с передвижной гирей. Величина отклонения рычажной системы 8 и коромысла 3 весов, пропорциональная изменению массы в бункере, определяется положением датчика в дифференциальном трансформаторе 4. Пропорционально положению датчика возникает электрический сигнал, который передается на электронный регулятор 5, регулирующий амплитуду и производительность вибродвигателя 6 лоткового питателя 7 в зависимости от величины отклонения коромысла 3 весов.
При многокомпонентном дозировании несколько дозаторов непрерывного действия с автономным регулированием объединяются в систему, которая может функционировать следующим образом.
Вариант 1. Несвязанное дозирование нескольких компонентов с производительностью, поддерживаемой в заданном постоянном соотношении (рис. 3.58, а), осуществляется от общего для всех дозаторов канала. Сигнал от программного задатчика, определяющий значение производительности всех компонентов, подается для операций умножения на постоянный коэффициент 0,2 Km 2 на аналого-множительные
876
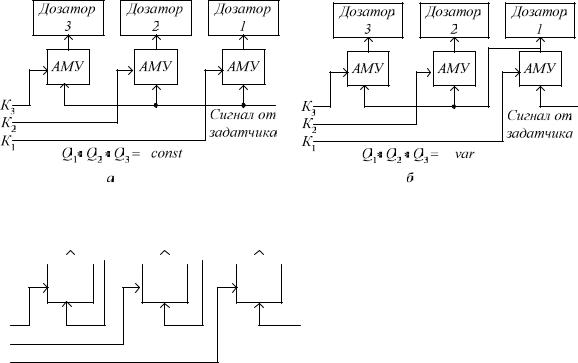
устройства АМУ, число которых равно числу дозаторов; значения соотношения можно менять изменением коэффициентов К1 – К3.
Вариант 2. Функциональное дозирование нескольких компонентов с коррекцией соотношения и параллельным соединением дозаторов (рис. 3.58, б). В этом случае дозатор 1 основного компонента принимается за ведущий. На него поступает сигнал задания через функциональный блок АМУ или программный задатчик. Этот же сигнал является входным для функциональных блоков ведомых дозаторов 2 и 3, на которые поступают сигналы, корректирующие производительность каждого дозатора.
Дозатор |
|
Дозатор |
|
Дозатор |
||||||||||
3 |
|
|
|
2 |
|
|
1 |
|
||||||
|
|
|
|
|
|
|
|
|
|
|
|
|
|
|
|
|
|
|
|
|
|
|
|
|
|
|
|
|
|
|
АМУ |
АМУ |
АМУ |
|
К3 |
|
|
|
Сигнал от |
К2 |
|
|
|
задатчика |
К1 |
|
|
|
|
Q1*Q2 *Q3 |
= |
var |
|
|
|
|
|||
|
в |
|
|
|
Рис. 3.58. Структурные схемы автоматических систем многокомпонентного дозирования: а– несвязанное дозирование компонентов; б– дозирование компонентов с коррекцией соотношения при параллельном соединении дозаторов; в– дозирование компонентов с коррекцией соотношения при последова-
тельном соединении дозаторов
Вариант 3. Функциональное дозирование нескольких компонентов с коррекцией соотношения и последовательным соединением дозаторов (рис. 3.58, в). В установке трехкомпонентного дозирования с коррекцией соотношения в качестве ведомых принимаются дозаторы 2 и 3, включенные последовательно с ведущим дозатором 1 основного материала.
3.4.6. Автоматический контроль расхода материалов при дозировании
Автоматический контроль расхода материалов в дозаторах дискретного действия с циферблатными указателями массы можно осуществить путем суммирования нарастающим итогом угла поворота
877
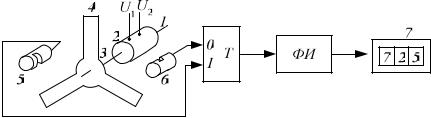
стрелки при загрузке или разгрузке весового бункера в каждом цикле дозирования. При этом угол поворота стрелки передается на измерительное устройство непосредственно (прямой контроль) либо после преобразования в числоимпульсный код (косвенный контроль).
Рассмотрим устройство прямого контроля расхода материала при дозировании (рис. 3.59). Дифференциальная электромагнитная муфта 2 фрикционного типа может находиться в двух состояниях: в одном состоянии выходной вал 3 муфты сцепляется с осью 1 стрелки весоизмерительной головки дозатора, в другом – фиксируется, т. е. происходит запоминание достигнутого положения.
На валу 3 муфты установлен экранный флажок 4, выполненный в виде трех металлических лепестков, расположенных под углом 120° . При повороте вала 3 лепестки входят в щели бесконтактных путевых датчиков
5 и 6.
Рис. 3.59. Схема автоматического устройства прямого контроля расхода материала
Электрические сигналы от датчиков поступают на соответствующие входы триггера Т, связанного с формирователем импульсов ФИ, который переключает электромагнитный счетчик импульсов 7.
Устройство работает следующим образом. При загрузке материала в бункер дозатора на обмотку электромагнитной муфты подается управляющее напряжение U1, фиксирующее выходной вал. При включении выпускного затвора для разгрузки подается напряжение U2 и происходит переключение муфты в другое состояние, при котором ось стрелки дозатора сцепляется с выходным валом муфты. Поэтому экранный флажок при разгрузке поворачивается вместе со стрелкой дозатора. После закрытия выпускного затвора электромагнитная муфта снова переключается, обеспечивая запоминание положения флажка. При следующем цикле разгрузки экранный флажок будет поворачиваться в том же направлении, следовательно, общий угол поворота флажка соответствует сумме порций выгружаемого материала.
При входе одного из лепестков экранного флажка в щель датчика 5 триггер переключается на единицу, затем при входе другого лепестка в щель датчика 6 – сбрасывается на нуль. При этом формируется импульс,
878
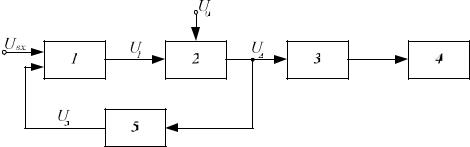
переключающий электромагнитный счетчик на один шаг. Таким образом, угол 120° соответствует весовой единице учета материала.
В данном устройстве благодаря использованию двух датчиков и триггера исключаются ложные срабатывания электромагнитного счетчика при колебаниях стрелки весоизмерительной головки.
Поэтому выходное напряжение измерительного моста пропорционально произведению скорости движения ленты конвейера на мгновенную массу груза на ленте, т. е. мгновенной производительности конвейера:
UВЫХ kvKq.
3.4.7. Автоматический контроль расхода материалов на конвейерных лентах
Автоматический контроль расхода материала в дозаторах непрерывного действия состоит из интегрирований производительности дозатора в течение определенного времени. При этом производительность дозатора моделируется в виде аналогового напряжения постоянного тока.
Интегрирование аналогового напряжения во времени с представлением результата в цифровом виде можно осуществить путем преобразования входного напряжения в пропорциональную частоту (частотно-импульсное преобразование) и суммирования числа импульсов.
Рис. 3.60. Схема автоматического устройства контроля расхода материала в дозаторе непрерывного действия
В устройстве автоматического учета материалов в дозаторе непрерывного действия (рис. 3.60) напряжение Uвх пропорционально производительности дозатора, поступает на вход интегрирующего узла 1. На выходе интегрирующего узла появляется линейно нарастающее напряжение U1. Когда это напряжение достигает значения U0, на выходе сравнивающего узла 2 формируется импульс U2, поступающий через делитель частоты 3 на электромеханический счетчик импульсов 4. Одновременно импульс U2 воздействует на узел обратной связи 5, формирующий импульс U5 со стабильным значением вольт-секундной
879