
2598
.pdfТогда получим |
|
|
|
|
|
T |
|
d |
A μ1 – μ2 |
|
|
|
|
|
|
||
|
0 dt |
|
|||
или |
|
|
|
|
|
T |
d |
κ1μ1 – k2μ2, |
(3.66) |
||
|
|||||
|
dt |
|
где Т – постоянная времени объекта; κ1 и k2 – коэффициенты передачи объекта; μ1 и μ1 – относительные перемещения регулирующих органов (прихода и отбора).
Из выражения (3.66) видно, что автоклав представляет собой одноемкостный объект с положительным самовыравниванием. Характер переходного процесса экспоненциальный.
3.8.7.Автоматизация термовлажностной обработки изделий
сконтролем прочности
Внастоящее время более 90% продукции заводов сборного железобетона подвергается термовлажностной обработке с целью интенсификации твердения бетона. Наиболее распространенным методом прогрева является пропаривание конструкции при нормальном давлении и температуре паровоздушной среды до 100 ° С. Считается, что выполнение заданной программы регулирования температуры во времени вполне обеспечивает требуемую прочность бетона. Однако температура изделий вследствие экзотермии бетона не равна температуре паровоздушной среды. Тепловые удары на бетон ухудшают его структуру, поэтому фактическая прочность бетона в момент окончания прогрева остается неизвестной. Для улучшения качества изделий и экономических показателей необходимо использовать непрерывную информацию о фактической температуре и прочности твердеющего бетона. Это позволит управлять процессом твердения бетона и своевременно корректировать режим в реально сложившихся условиях.
Имеется ряд предложений по применению физических методов контроля прочности прогреваемого бетона с целью коррекции продолжительности тепловой обработки. Рекомендуются методы определения прочности, основанные на электропроводности, динамической упругости, ультразвуковой проницаемости, контрактации бетона, контроле градусовчасов и температурно-временного эквивалента. Многие из этих методов отличаются сложностью и дают значительные погрешности.
Остановимся на наиболее перспективном методе температурно-вре- менного эквивалента. В основу аналитического определения прочности
950
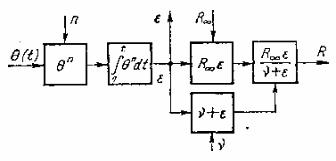
бетона, твердеющего при переменной температуре, положено понятие температурно–временного эквивалента прочности ε (θ, t), т.е. функционала температуры θ(t) и продолжительности твердения t, связанного с прочностью бетона однозначной зависимостью R (ε).
Значение температурно-временного эквивалента имеет вид
t |
|
ε = Ф[θ (t)] dt, |
(3.67) |
0 |
|
где Ф [θ (t)] –экспериментально установленная функция температур вида
Ф [θ (t)] = (θ0 + θ)n, |
(3.68) |
θ0 – температура бетона, при которой он не твердеет; п = 1,2 ÷ 2 – опытная постоянная, которая зависит от минералогического состава цемента.
Зависимость прочности бетона от температурно-временного эквивалента выражена гиперболой вида
R R |
ε |
, |
(3.69) |
|
|||
|
ν ε |
|
где R –потенциальный предел прочности; –постоянная, характеризующая состав и структуру бетона.
На основании формул (3.67) – (3.69) составлен алгоритм функциони рования счетно-решающего устройства, структурная схема которого показана на рис. 3.98 и отражает последовательность математических операций для получения значений прочности бетона. Контроль твердения осуществляется автоматическим
регулятором тепловой обработки |
Рис. 3.98. Алгоритмическая структура |
бетона (АРТОБ-1), объединяю- |
счетно-решающего устройства |
|
щим счетно-решающее и программно-регулирующее устройства. Структурная схема прибора АРТОБ-1 приведена на рис. 3.99.
Изделие 1 с установленным в бетон датчиком температуры 2 помещается в пропарочную камеру 3. Заданный режим изменения температуры бетона выполняется программным устройством 12, которое управляет исполнительным механизмом 10, регулирующим подачу теплоносителя через командное устройство 11. Датчик температуры включен в одно из плеч равновесного моста 4.
Электронный усилитель 5 усиливает сигнал разбаланса моста и управляет реверсивным двигателем 6, перемещающим записывающее
951
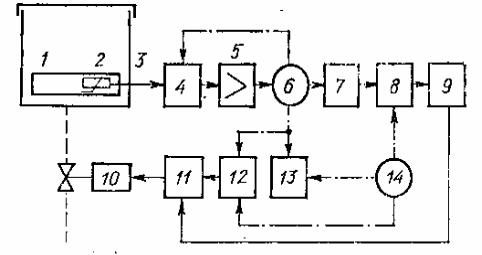
устройство 13, которое вычерчивает график температуры изделия на ленте, движущейся с помощью синхронного двигателя 14. Реверсивный двигатель управляет работой степенного устройства 7, выполняющего функцию ε (θ). Сигнал от степенного устройства поступает на интегратор 8, который интегрирует функцию ε (θ) во времени, т. е. накапливает значение температурно-временного эквивалента ε. Кроме того, сигнал степенного устройства передается в индикаторно-сравнивающее устройство 9, которое поворачивает барабан с укрепленной на нем шкалой. Цена деления шкалы зависит от температурно-временного эквивалента и определяется по формуле (3.67). Когда бетон изделия достигнет прочности, заданной в индикаторно-сравнивающем устройстве, подается сигнал на командное устройство 11, отключающее исполнительный механизм 10.
Рис. 3.99. Структурная схема прибора АРТОБ -1
Продолжительность работы устройства не ограничена. С внедрением автоматического устройства расход пара на кубический метр изделий по сравнению с ручным управлением сократился на 14,5%, уменьшилась продолжительность прогрева балок на 10–18 ч, увеличилась производительность отдельных линий на 25%.
3.8.8. Многоканальное регулирование температуры в пропарочных камерах, кассетах, автоклавах
Наиболее распространенные системы автоматизации технологических процессов предусматривают использование индивидуальных устройств для регулирования отдельных параметров. Это приводит к большим
952
затратам на приобретение, монтаж, эксплуатацию регуляторов и вызывает значительные расходы на сооружение щитов и помещений для их размещения. Кроме того, на предприятии необходимо иметь большой резервный парк регуляторов. Одним из действенных способов снижения затрат на аппаратуру автоматики, сокращения габаритов щитов, площадей щитовых помещений, а также повышения надежности работы аппаратуры является использование многоканальных регуляторов.
Многоканальными регуляторами принято называть устройства, предназначенные для автоматического регулирования многих параметров, измеряемых отдельными датчиками путем воздействия на отдельные регулирующие органы. В этих регуляторах предусматривается многократное использование наиболее сложных и дорогих функциональных узлов. К числу таких устройств могут относиться усилители, формирователи, корректирующие устройства. Важным достоинством многоканального регулирования является увеличение вероятности безотказной работы регулируемых объектов.
Для связи объектов регулирования с общим автоматическим регулятором может быть использован временной способ разделения каналов, предусматривающий поочередную связь. Интервалы времени, через которые осуществляется присоединение объекта управления к регулятору, называется циклом обегания регулятора T0. Практическое распространение получили многоканальные регуляторы с постоянным циклом обегания. Для этих регуляторов при регулировании п параметров время каждой связи индивидуальных устройств с общей частью регулятора в пределах цикла обегания равно
tсв = T0/n.
Вследствие временного разделения каналов многоканальные регуляторы относятся к устройствам дискретного действия, в которых регулируемые параметры подвергаются квантованию по времени. На рис.3.100 изображена обобщенная функциональная схема многоканального регулятора. В регуляторе установлены:
датчики Дi, осуществляющие измерение регулируемых параметров;
задатчики Здi, с помощью которых производится установка заданных регулируемых параметров;
исполнительные механизмы ИМi, воздействующие на регулирующие органы РОi;
элементы динамической настройки автоматического регулятора АР, определяющие параметры закона регулирования по каждому каналу;
контакты Рi, подключающие поочередно Дi, Здi, ИМi к общей части регулятора АР;
953
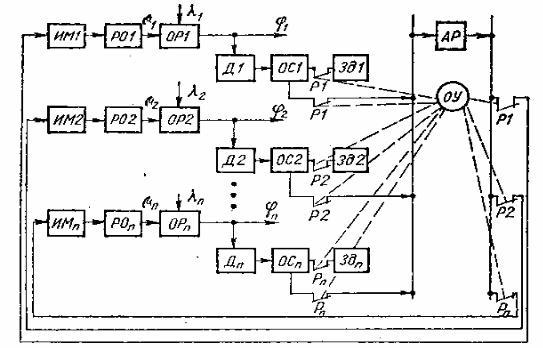
сравнивающее устройство ОСi, в котором происходит алгебраическое суммирование сигналов датчиков и задатчиков и формирование сигналов ошибки;
усилитель сигнала ошибки и формирующее устройство, расположенные в АР, вырабатывают сигналы управления исполнительными механизмами;
обегающее программное устройство ОУ, которое осуществляет управление всеми переключающими устройствами. Блок управления часто включает в себя генератор импульсов (ГИ), с помощью которого задается темп работы многоканального регулятора.
Рис. 3.100. Функциональная схема многоканального регулятора
В настоящее время нашей промышленностью выпускаются современные многоканальные регуляторы. В системе КТС ЛИУС выпускается комплекс КМ-1201-1 на 16 каналов управления, в системе АСКР-ЭЦ - регуляторы А-761-05 на 16 каналов, А-305-13 и А-306-14 на 8 каналов управления, в системе «Центр» – регуляторы БРП-10 на 10 каналов и БППИ-20 на 20 каналов управления.
Для контроля и регулирования большого числа различных технологических параметров могут быть использованы машины многоканального централизованного контроля и регулирования. В этих системах осуществляется простейшее позиционное регулирование технологических параметров.
954
На предприятиях строительной индустрии пропарочные камеры, кассеты и автоклавы обладают большой тепловой инерционностью, поэтому нет надобности вести непрерывный контроль и управление. В этом случае можно использовать одно автоматическое устройство для контроля и управления тепловыми процессами многих объектов. Были разработаны программные многоканальные электрические автоматические регуляторы МРТЭ-10, БМРТЭ, «Памир» и пневматические установки «Пуск-ЗС» и «Пуск-ЗП».
Пневматическая установка централизованного контроля, регулирования и дистанционного управления «Пуск-ЗП» (рис 3.101) предназначена для программного автоматического регулирования процесса тер– мовлажностной обработки железобетонных изделий в группе пропарочных камер, кассет, автоклавов и пр.
Установка состоит из десяти независимых каналов контроля и регулирования и создана на базе элементов универсальной системы промышленной пневмоавтоматики УСЭППА. Установка «Пуск-ЗП» включает в себя станцию централизованного контроля и управления (СЦКУ), десять преобразователей температуры в давление (датчиков), десять исполнительных механизмов подачи пара, десять исполнительных механизмов эжекторов и пневмолиний. Исполнительные механизмы представляют собой нормально закрытые клапаны с мембранными приводами.
Станция централизованного контроля и управления состоит из функциональных модулей:
комбинированного модуля М198м, предназначенного для обнаружения отклонений параметров от заданных, отработки ПИ-закона регулирования, формирования управляющих сигналов и коммутации их к исполнительным механизмам подачи пара. В этот блок входит регулятор типа ПРЗ, 21;
модуля включения эжекторов М200;
модуля включения вентиляторов М141, предназначенного для включения двух групп вентиляторов по сигналам, полученным из модуля М200;
модуля ручных задатчиков, предназначенного для создания опорного давления на элементах задатчиков.
Кроме того, установка имеет управляющее устройство УУ-1, электронный коммутатор ЭК-1, панель сигнализации ПС. Для контроля прочности изделий используется ультразвуковой прибор типа УКБ-1.
Рассмотрим работу установки в автоматическом режиме.
955
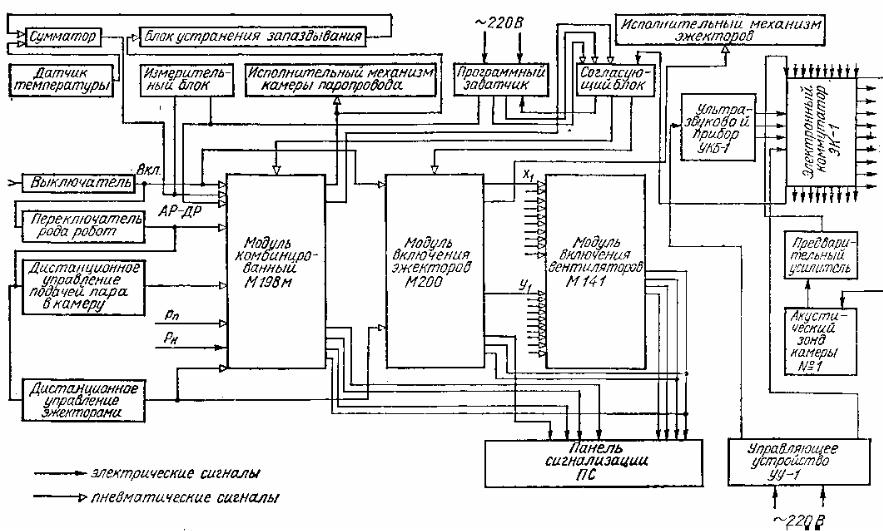
956
Рис. 3.101. Схема автоматического управления процессом термовлажностной обработки изделий с использованием аппаратуры «Пуск-ЗП»
При включении установки тумблером «Автоматический режим» (АР), находящимся на панели управления, комбинированный модуль М198м, сравнивая сигнал датчика температуры и задатчика, реализует ПИ-закон регулирования и подает управляющие команды на исполнительный механизм паропроводов. Одновременно сигнализируются отклонения допустимых значений температур. При отклонении температуры за пределы нижнего допустимого значения автоматически останавливается двигатель программного задатчика. Установка имеет коммутаторы и регистрирующий прибор, записывающий температуру и задание по каждому каналу. По окончании цикла прогрева выдается сигнал на модуль М200, который формирует управляющий сигнал на исполнительные механизмы эжекторов, открывая вентиляционные камеры. Аналогичные воздействия поступают от аппаратуры УКБ-1 при достижении изделием заданной прочности.
Одновременно высвечивается сигнал «Эжектор включен». Через заданный промежуток времени включаются магнитный пускатель вентилятора и сигнализация «Вентилятор включен». После окончания процесса термовлажностной обработки и охлаждения камеры и изделия включается сигнал «Цикл окончен», снимается сигнал «Эжектор включен» и останавливается программный задатчик.
Перевод любого канала в режим дистанционного управления осуществляется тумблером ДР. При этом остальные каналы работают в автоматическом режиме.
3.8.9. Расчет устойчивости многоканальных систем автоматического регулирования
Исследование многоканальных систем автоматического регулирования осуществляется путем рассмотрения процесса в одном контуре регулирования. Приведем методику исследования такой системы на примере регулирования температуры в пропарочной камере. Импульсная система автоматического регулирования температуры в пропарочной камере описывается следующей системой уравнений:
уравнение объекта регулирования
T0φ΄ + φ = k (μ – λ); |
(3.70) |
уравнение датчика температуры
δη + φ = 0; |
(3.71) |
уравнение жесткой обратной связи
957
σ = η – μ; |
(3.72) |
уравнение исполнительного механизма широтно-импульсной системы регулирования [5]
μ (n +1) – μ (n) = kиσ (n), |
(3.73) |
где δ – коэффициент неравномерности регулирования; η – относительное перемещение чувствительного органа; σ – относительное значение входного сигнала исполнительного механизма; п – порядковый номер периода; k – коэффициент усиления.
Вэтой системе уравнение (3.70) является дифференциальным, уравнения (3.71) и (3.72) – алгебраическими, а уравнение (3.73) – разностным. Для исследования процесса необходимо совместное их решение, а это вызывает необходимость превратить все уравнения в разностные. Для преобразования дифференциального уравнения в разностное необходимо проинтегрировать его в пределах периода и подставить переменные: в начале периода ( t = 0) – значение φ (п), в конце периода (t = ∞) – значение φ (п + 1).
Вуравнении объекта регулирования для простоты преобразования положим λ = const. Кроме того, будем считать, что μ , меняется скачком в начале периода. Длительность включения сервомотора по сравнению с
периодом регулирования мала. На основании этого можно считать, что μ = μ (п) = const. Тогда уравнение объекта регулирования можно рассматривать как дифференциальное уравнение с постоянной правой частью. Проинтегрируем это уравнение в пределах промежутка времени n- го периода. Полное решение этого уравнения будет
φ = φ1+ φ2, |
(3.74) |
где φ1 и φ2 – общее и частное решения.
Найдем общее решение
T0φ1΄ + φ1 = 0.
Напишем характеристическое уравнение
T0 z + 1 = 0,
тогда корень уравнения
z = – 1/ T0,
общее решение уравнения
φ1 = ce−t/T0,
где с – постоянная интегрирования.
958

Найдем частное решение линейного уравнения (3.70): так как правая часть уравнения постоянна, то решение его
φ2 = В.
Подставив это решение в уравнение (3.74), получим тождество
B= kμ (n) – kλ, так как Т0 dB = 0. dt
Полное решение уравнения объекта регулирования
φ = φ1+ φ2 = ce−t/T0 + kμ (n) – kλ. |
(3.75) |
Постоянную интегрирования с находим по начальным условиям:
в начальный момент n-го периода (t = 0) φ= φ(п), тогда по уравнению (3.75)
φ = φ (п) = kμ (n) – kλ+с, |
(3.76) |
откуда |
|
c = φ (п) – kμ (n) + kλ. |
(3.77) |
Подставив в уравнение (3.75) вместо с его выражение (3.77), получим |
|
φ (п) = kμ (n) – kλ + [φ (п) – kμ (n) + kλ] e−t/T0. |
(3.78) |
Чтобы найти φ (п + 1), необходимо в уравнение (3.78) подставить t = T, тогда получим
φ (п+1) = kμ (n) – kλ + φ (п) e−T /T0 – k [μ (n) – λ] e−T /T0. |
(3.79) |
Для получения разностного уравнения необходимо из φ (п + 1) вычесть φ (п), тогда получим
φ (п+1) – φ (п) e−T /T0 = kμ (n) (1– e−T /T0 ) – kλ (1– e−T /T0 ). |
(3.80) |
Значительно проще превращается в разностное алгебраическое уравнение, так как его переменные связаны между собой в любой момент времени и в том числе в момент t ~ п.
Напишем все уравнения системы автоматического регулирования в разностной форме:
φ (п+1) – φ (п) e−T /T0 = kμ (n) (1– e−T /T0 ) – kλ (1– e−T /T0 ); (3.81)
959