
2598
.pdf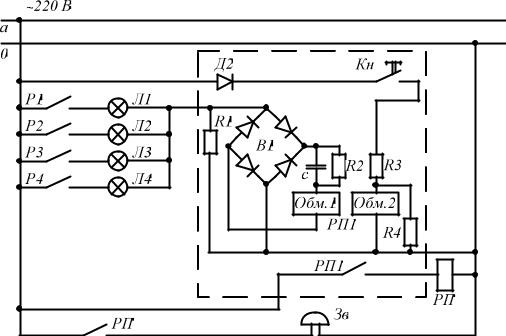
Принципиальная схема устройства реле приведена на рис. 3.35. При замыкании контактов какого–либо из реле Р1–Р4 загорается соответствующая лампочка и через входной резистор R1 устройства РИС проходит ток. В зависимости от значения R1 и тока на резисторе происходят нарастание потенциала и процесс заряда конденсатора через выпрямитель В1. Во время заряда конденсатора через обмотку поляризованного реле РП1 протекает импульс зарядного тока, вследствие чего оно срабатывает и замыкает цепь промежуточного реле РП, которое своими контактами включает звонок. При замыкании кнопки Кн цепи возврата реле РП якорь его перебрасывается в первоначальное положение.
Для определения количественных показателей работы дробильносортировочного завода необходим автоматический учет следующих показателей:
количества сырья, поступающего из карьера (осуществляется автомобильными весами, автоматически суммирующими массу груженых машин за вычетом массы тары);
количества готовой продукции по фракциям (учитывается автоматическими конвейерными весами с дистанционной регистрацией производительности).
Рис.3.35 . Принципиальная схема реле импульсной сигнализации |
Весовой контроль потоков материалов производится при помощи ленточных весов, работающих по принципу механического взвешивания,
850
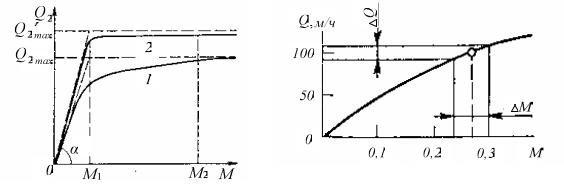
или электронных весов, действующих на основании свойств материалов поглощать радиоизотопные излучения.
Учет времени работы и простоев основного технологического оборудования осуществляется на установке «Сигнал».
3.3.7. Автоматизация конусных и валковых дробилок
Конусные дробилки являются механизмами с благоприятными условиями пуска, разгон которых легко осуществляется асинхронными двигателями с короткозамкнутыми роторами. Для пуска дробилки необходимо включить систему смазки и выбрать режим управления. В цепь пуска вводится разрешающий контакт реле контроля уровня масла.
Аварийное отключение двигателя дробилки производится при исчезновении масла на сливе и при отключении механизмов поточно– транспортных систем, следующих после дробилки. О загрузке материалом дробилки косвенно судят по току статора приводного асинхронного двигателя. Кроме того, вводят корректирующий сигнал по току нагрузки питателя. Суммарный сигнал поступает на автоматический регулятор, где он сравнивается с заданием. Регулятор, воздействуя на питатель, обеспечивает нормальный режим работы конусной дробилки.
Задача автоматического регулирования процесса дробления включает не только обеспечение полной нагрузки дробилки, но и поддержание заданной крупности материала на выходе. Автоматическое регулирование величины разгрузочной щели конусной дробилки в зависимости от необходимой крупности материала на выходе позволяет получить заданное качество дробленого материала.
Рис.3.36. Статические Рис.3.37. Статические характеристики дробилок:1– конусной; характеристики конусной дробилки КМД-
2– валковой |
1750 |
851
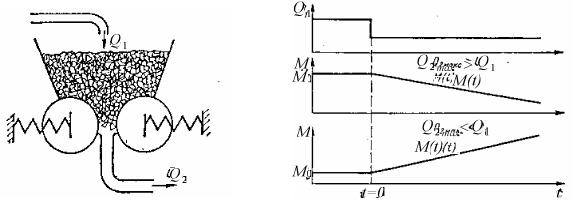
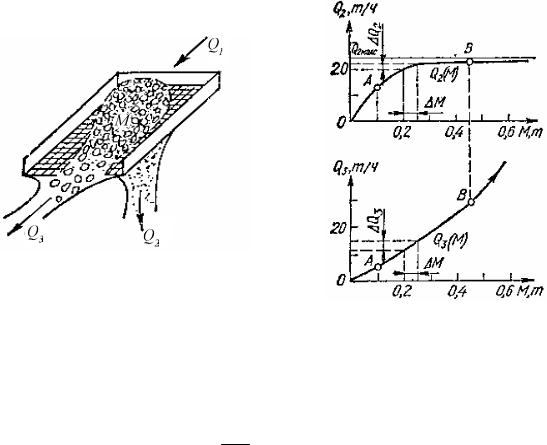
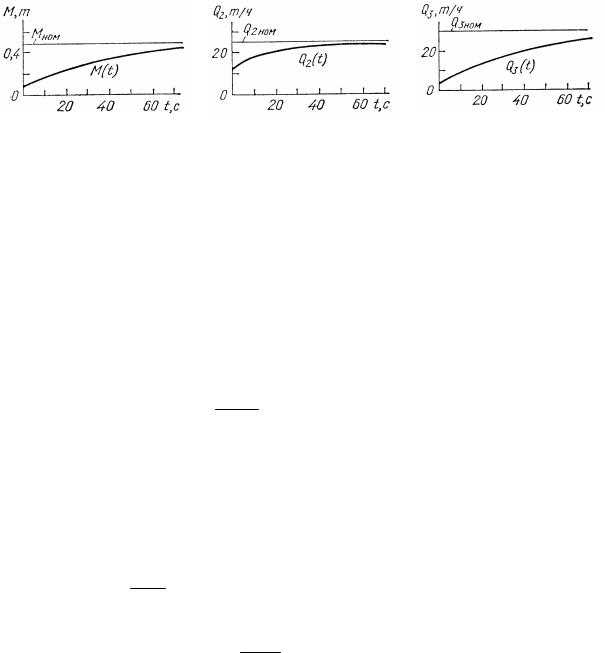
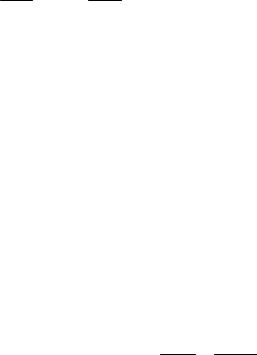
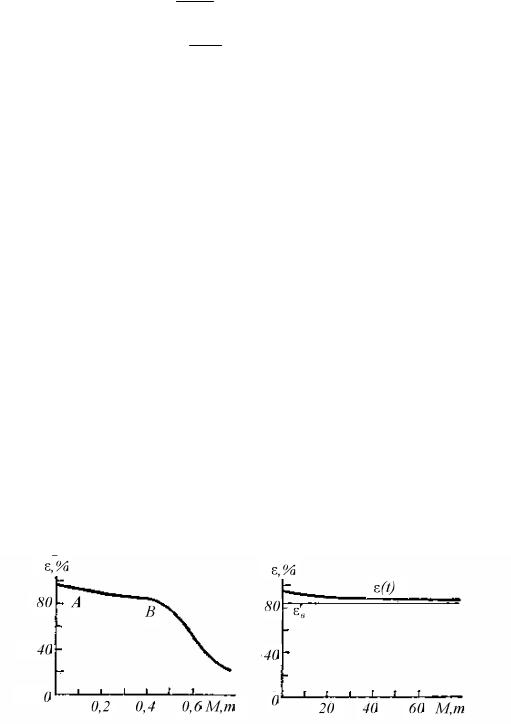
W ( p) |
Q3 |
( p) |
|
0,42 |
. |
(3.29) |
|
|
|
||||
3 |
Q1 |
( p) |
10p 1 |
|
||
|
|
В случае двухситного грохота основными уравнениями являются:
dM1 Q2 Q3 Q1; dt
dM2 Q4 Q5 Q2 . dt
Кроме того, существуют дополнительные зависимости:
Q2 f(M ); Q3 f (M );
Q4 f(M ); Q3 f (M ).
Двухситный грохот в линейном приближении характеризуется следующими передаточными функциями:
W ( p) |
M2( p) |
|
|
K2 |
|
T2 |
|
; |
(3.30) |
|||||||
|
|
|
|
|
|
|
||||||||||
|
1 |
|
Q1( p) |
|
T1 p 1 |
T2 p 1 |
|
|||||||||
|
|
|
|
|
||||||||||||
W ( p) |
Q4 |
( p) |
|
|
|
K2 |
|
|
K5 |
|
, |
|
(3.31) |
|||
|
|
|
|
|
|
|
|
|||||||||
2 |
|
Q3 |
( p) |
|
T1 p 1 |
T2 p 1 |
|
|
|
|||||||
|
|
|
|
|
|
где T1 и Т2 – постоянные времени первого и второго сит.
Таким образом, двухситочный грохот можно представить в виде двух последовательно соединенных апериодических звеньев.
В переходных процессах изменяются не только запас материала и отводимые из грохота материальные потоки, но и эффективность грохочения. На рис. 3.43 приведен примерный график зависимости извлечения ε материала в отводимый нижний поток от запаса на сите, т.е. ε=f(M). По мере увеличения запаса М извлечение ε уменьшается, асимптотически приближаясь к нулю.
Рис.3.43. Графики зависимости извлечения материала
857
