
2598
.pdf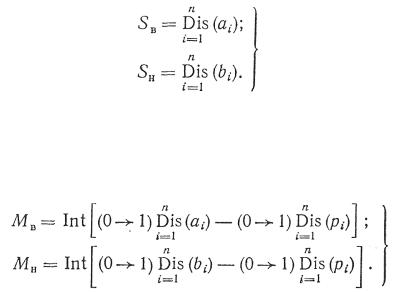
позициями (соседними пунктами).
В качестве адресоносителя применяется смонтированная на тележке адресная плата АП с выступающими пластинами. Установка необходимого адреса на плате может производиться различными способами (копирами,
кулачковым механизмом, электромагнитами и пр.).
Если направление перемещения тележки задается импульсами аi -
вперед или bi - назад от кнопок, расположенных в каждой адресной позиции, то стартовые сигналы имеют вид
(3.3)
Следовательно, алгоритмы формирования командных сигналов вклю-
чения двигателя тележки вперед Мв и назад Мн следующие:
(3.4)
Контроль перемещения грузоносителей можно производить в функ-
ции времени или в функции пути.
При контроле в функции времени система адресования не имеет об-
ратной связи с транспортной сетью, и накопление адресной информации происходит в результате отсчета временных интервалов. В этом случае точность определения адреса зависит от колебаний скорости движения грузоносителей. Поэтому такие системы адресования можно применять только при стабилизированной скорости грузоносителя.
При контроле в функции пути дискретной единицей адресной инфор-
мации является электрический сигнал от датчика, определяющего перемещение грузоносителя на определенный отрезок пути (шаг транспортирова-
ния). В этом случае контрольное устройство отображает положение грузоносителя на линии транспортирования и фиксирует момент прохождения адресных позиций. Наиболее просто такие устройства реализуются с помощью сдвиговых регистров или счетчиков импульсов.
810
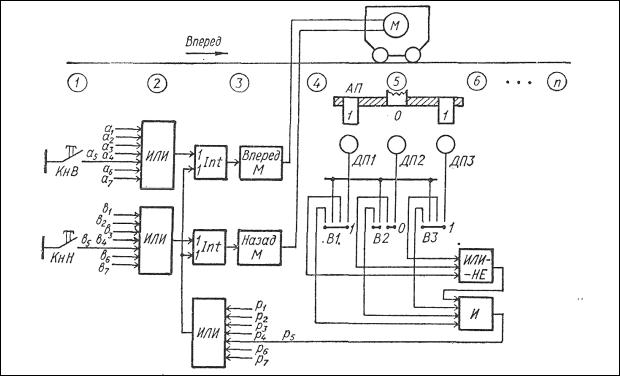
Рис. 3.17. Структурная схема управления тележкой с использованием адресоносителя
Рассмотрим систему адресования (рис. 3.18), в которой перемещение самоходной тележки контролируется реверсивным двоичным счетчиком - триггеры Т1-ТЗ.
В адресных позициях установлены путевые датчики ДП1-ДП7, определяющие положение тележки при появлении сигналов от датчиков.
3.2. Автоматизация складов материалов и изделий
3.2.1. Характеристика складов как объектов автоматизации
На заводах железобетонных конструкций склады в основном используются для хранения цемента, заполнителей бетона и железобетонных изделий. В зависимости от рода материалов, подлежащих хранению, склады имеют характерные особенности и могут быть классифицированы по ряду признаков. Склады цемента подразделяются на закромные, бункерные и силосные, оборудованные механическим (элеваторы, шнеки) и пневматическим транспортом (винтовые и камерные пневмонасосы, эрлифты, аэрожелоба). На предприятиях стройиндустрии наибольшее распространение получили бункерные и силосные склады цемента как более совершенные.
Бункерные склады цемента имеют ряд отсеков, заканчивающихся внизу коническими бункерами, из которых цемент гравитационно
811
(самотеком) поступает в винтовые конвейеры, элеваторы или винтовые пневматические насосы для дальнейшего транспортирования на бетонный завод или транспортные средства. Загрузка бункерного склада может осуществляться различными средствами: механическими разгрузочными лопатами и через приемные бункера винтовыми конвейерами или пневматическим транспортом.
В силосных складах для хранения цемента используют металлические или железобетонные силосы (банки). В типовых прирельсовых складах цемент из железнодорожных вагонов поступает в приемные бункера, откуда транспортируется в силосы. Выдача цемента из силосов производится с помощью донных разгружателей (на бетонный завод) или блоковых разгружателей (на автотранспорт). Вертикальный транспорт цемента осуществляется ленточными элеваторами или эрлифтом, горизонтальный транспорт - винтовыми конвейерами, пневмовинтовыми насосами и аэрожелобами.
Автоматизация складов цемента заключается в автоматическом контроле уровня цемента в емкостях хранения, загрузке емкостей, выдаче требуемой марки цемента по сигналам запроса из бетоносмесительного отделения и перекачке цемента из одной емкости в другую при длительном хранении на складе.
Склады заполнителей бетона можно подразделять следующим обра-
зом.
По виду внешнего транспорта различают склады прирельсовые с поступлением материалов в железнодорожном подвижном составе, с доставкой материалов автомобильным или водным транспортом.
По способам механизации выгрузки материалов из внешних транс-
портных средств различают склады с гравитационной разгрузкой, с разгрузкой сталкиванием, черпанием и гидромеханизированным способом.
По методам загрузки могут быть склады с приемными устройствами и системой машин для штабелирования материалов или без приемных устройств - с непосредственной подачей материалов из транспортных средств в емкости хранения, а также склады, оборудованные машинами, совмещающими операции выгрузки и штабелирования материалов.
По методам разгрузки склады разделяются на разгружаемые методом гравитации и специальными машинами - грейферными кранами, самоходными разгрузчиками, экскаваторами или другими машинами.
По способу хранения склады могут быть открытыми, закрытыми или частично закрытыми.
По типу емкостей хранения различают склады штабельные, бункерные, полубункерные, штабельно-полубункерные и силосные.
Автоматизация складов заполнителей заключается в автоматической выгрузке прибывающего в железнодорожных вагонах материала, загрузке
812
емкостей, выдаче материала требуемой фракции по сигналам запроса из бетоносмесительного отделения, сушке и нагреве выдаваемого со склада материала. В условиях предприятий стройиндустрии необходимо обеспечить оперативный учет количества принимаемых и отпускаемых материалов для получения сведений об истинной величине запаса цемента и заполнителей на складах. На складах железобетонных изделий погрузочно-разгрузочные работы механизированы и осуществляются в основном с помощью мостовых и козловых кранов. В зоне действия крана вдоль подъездных путей и сквозных проездов располагаются складские площадки со штабельным или кассетным хранением изделий, уложенных на деревянных подкладках с применением прокладок. Автоматизация складов железобетонных изделий может быть осуществлена на основе программно–дистанционного управления механизмами кранов. В этом случае предусматривается автоматическое адресование крана по заданным координатам склада и дистанционное управление механизмами подъема. Все команды должны передаваться по радиоканалам, поскольку такелажник управляет краном из различных пунктов склада.
3.2.2. Автоматическое управление оборудованием склада цемента
Склад цемента, оборудованный пневмотранспортом (рис. 3.18, а), состоит из шести банок Б1–Б6 с датчиками верхнего (В1–В6) и нижнего (Hl–1–H6–1) уровней. Склад может работать в трех режимах: загрузки, перекачки и выдачи цемента в бетоносмесительное отделение (БСО). При выдаче цемента работают донные разгружатели М6–1 – М6–2 определенной банки, вентилятор нижнего аэрожелоба четной (М8) или нечетной (М7) группы. При этом через соответствующий шибер М10 или М9 материал поступает в промежуточный бункер БП1, состояние которого контролируется датчиками верхнего (У1) и нижнего (У2) уровней. С помощью пневмовинтового насоса, включающего в себя шнек M11 и вентиль М12, цемент подается в бетоносмесительное отделение. При перекачке цемент поступает в один из промежуточных бункеров БП2 или БП3, а затем эрлифтом (исполнительные механизмы М13–М14 или М15– М16) подается на вход верхнего аэрожелоба. Один из шиберов Ml–М5 верхнего аэрожелоба направляет цемент в соответствующую банку. При загрузке цемент поступает в промежуточный бункер БП2 или БП3, а затем подается в одну из банок так же, как в режиме перекачки. Режим работы задается пусковыми сигналами выдачи Q, загрузки G и перекачки Р.
При выдаче цемента выбор разгружаемых банок определяется селектирующими сигналами b1 – b2 от переключателя выдачи. При этом объединяются сигналы выбора четных (bj) и нечетных (bi) банок с целью
813
формирования сигналов принадлежности выбранной банки к четной (Вч) или нечетной (Bн) группе:
Вч = b2 \/ b4 \/ b6 ; |
(3.5) |
Вн = b1 \/ b3 \/ b5 . |
(3.6) |
При подаче пускового сигнала Q включаются исполнительные ме– ханизмы тракта выдачи цемента в такой последовательности: вентиль Ml2 подачи сжатого воздуха в камеру пневмовинтового насоса, двигатель M11шнека насоса, вентилятор М7 или М8 нижнего аэрожелоба, шибер нечетных (М9) или четных (М10) банок и донные разгружатели выбранной банки, работающие поочередно. Отключение исполнительных механизмов происходит после снятия сигнала Q. Вначале отключаются донные разгружатели, затем с задержкой во времени на доработку цемента отключаются вентилятор нижнего аэрожелоба и соответствующий шибер. Двигатель шнека МП и вентиль М12 также отключаются с задержкой во времени на доработку после опорожнения промежуточного бункера БП1.
В режиме выдачи цемента (табл. 3.3) входные исполнительные механизмы – донные разгружатели – блокируются с пусковым элементом,
переключателем выдачи, элементом циклической работы и элементами контроля состояния вентилятора М7 (разгружатели нечетных банок) или вентилятора М8 (разгружатели четных банок).
Промежуточные исполнительные механизмы М7 и М8 блокируются с переключателем выдачи и следующими элементами: пусковым, контроля состояния бункера БШ и разгружателей нечетных или четных банок. При этом для доработки цемента нижними аэрожелобами после снятия пускового сигнала Q необходимо осуществлять задержку на окончание сигналов, характеризующих состояние донных разгружателей.
Направляющие исполнительные механизмы М9 и М10 блокируются с реле контроля давления воздуха РД1 и элементами контроля состояния вентиляторов нижних аэрожелобов.
Промежуточный исполнительный механизм МП блокируется с пусковым элементом, реле контроля давления воздуха РД1 и датчиком нижнего уровня У2 бункера БШ. При этом для доработки цемента пневмовинтовым насосом после снятия пускового сигнала Q необходимо осуществлять задержку на окончание сигнала датчика У2.
814
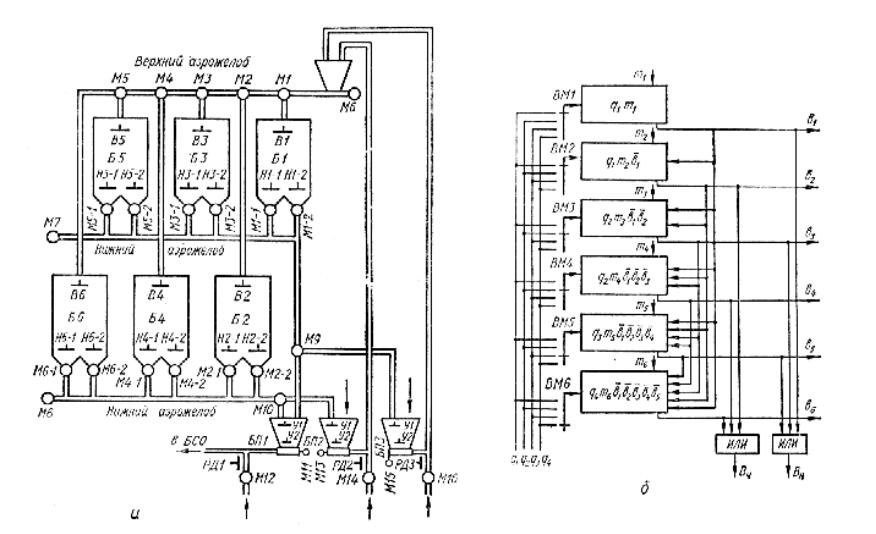
815
Рис. 3.18. Склад цемента: а– технологическая схема склада; б– структурная схема устройства выбора банок
Таблица 3.3
Алгоритмы формирования командных сигналов в режиме выдачи цемента
Наименование |
Обозначение |
|
|
исполнительных |
Алгоритм формирования КС |
||
механизмов |
|||
механизмов (рис 3.18) |
|
||
|
|
||
Разгружатели нечетных |
Mi–1, Mi–2 |
_ |
|
банок |
(i = 1,3,5) |
BiQv7x; BiQv7x |
|
|
|
|
|
Разгружатели четных |
Mj–1, Mj–2 |
_ |
|
банок |
(i = 2,4,6) |
BjQv8x; BjQv8x |
|
|
|
5 |
|
Вентиляторы нижних |
M7 |
φ1v11[BнQ\/D(1→0)Dis(vi1\/vi2)] |
|
|
i=1 |
||
аэрожелобов |
|
6 |
|
|
M8 |
φ1v11[BчQ\/D(1→0)Dis(vj1\/vj2)] |
|
|
|
j=2 |
|
Шибер нечетных банок |
M9 |
d1v7 |
|
Шибер четных банок |
M10 |
d1v8 |
|
|
|
|
|
Шнек пневмовинтового |
M11 |
d1 [Q \/ D (1→0)y21] |
|
насоса |
|||
|
|
||
Вентиль подачи |
M12 |
Q \/ D (1→0)y21 |
|
сжатого воздуха |
|||
|
|
Примечание. d1 – сигнал реле контроля давления воздуха РД1; φ1–сигнал, соответствующий интервалу времени между моментами заполнения БП1 до датчика верхнего уровня У1 и опорожнения до датчика нижнего уровня У2; vk – сигнал, характеризующий состояние (включен – выключен) k-го исполнительного механизма; х
– селектирующий сигнал, определяющий очередность работы донных разгружателей; y21 – сигнал датчика нижнего уровня У2 бункера БП1.
Таблица 3.4
Алгоритмы формирования командных сигналов в режиме загрузки цемента
Наименование |
Обозначение |
|
|
исполнительных |
Алгоритм формирования КС |
||
механизмов |
|||
механизмов (рис 3.18) |
|
||
|
|
||
Шибера верхнего |
M1–M5 |
k1v6; k2v6; k3v6; k4v6; k5v6; |
|
аэрожелоба |
|||
|
|
||
Вентилятор верхнего |
M6 |
G \/ D (1→0) (d2 \/ d3) |
|
аэрожелоба |
|||
|
|
||
Шнеки эрлифтов |
M13 |
d2 [G \/ D (1→0)y22] |
|
M15 |
d3 [G \/ D (1→0)y23] |
||
|
|||
Вентили подачи сжатого |
M14 |
vв [g2G \/ D (1→0)y22] |
|
воздуха |
M16 |
vв [g3G \/ D (1→0)y23] |
Примечание. d2 и d3 – сигналы реле контроля давления воздуха РД2 и РДЗ соответственно; y22 и y23 – сигналы датчиков нижнего уровня У2 бункеров БП2 и БПЗ соответственно.
816
Выходной исполнительный механизм M12 блокируется с пусковым элементом и датчиком нижнего уровня У2 бункера БП1. Поскольку вентиль подачи сжатого воздуха отключается одновременно с двигателем шнека МП, то в этом случае также необходимо осуществлять задержку на окончание сигнала датчика У2.
При загрузке цемента выбор загружаемых банок определяется селектирующими сигналами k1 – k5 от переключателя загрузки. В этом случае включается требуемый шибер верхнего аэрожелоба. Если все шибера Ml–М5 отключены, то цемент направляется в банку Б6. Выбор эрлифта определяется селектирующими сигналами g2 и g3 от переключателя эрлифтов.
При подаче пускового сигнала G включаются исполнительные механизмы тракта загрузки цемента в такой последовательности: вентилятор М6 верхнего аэрожелоба, один из шиберов Ml–М5 верхнего аэрожелоба, вентиль Ml4 или Ml6 подачи сжатого воздуха в камеру эрлифта, двигатель М13 или М15 шнека эрлифта. Отключение исполнительных механизмов происходит после снятия сигнала G. После опорожнения промежуточного бункера БП2 или БП3 отключаются вентиль и шнек эрлифта с задержкой во времени на доработку цемента. Затем отключаются вентилятор М6 и шибер верхнего аэрожелоба.
В режиме загрузки цемента (табл. 3.3) промежуточные исполнительные механизмы М14 и Ml6 блокируются с пусковым элементом, если марки цемента нескольких банок находятся в одинаковых положениях, то выбирается банка с наименьшим порядковым номером. Это обеспечивается сигналами запрещающей блокировки, которая осуществляется в направлении от банок с меньшими порядковыми номерами к банкам с большими порядковыми номерами.
Выбор разгружаемой банки возможен только при наличии в ней цемента, что контролируется парой датчиков Нi1, Нi2 нижнего уровня. Поэтому при формировании сигналов выбора i-й банки необходимо учитывать значение сигнала наличия материала
mi= hi1 \/ hi2,
где hi1 и hi2 – сигналы датчиков нижнего уровня Нi1 и Нi2 соответственно. Таким образом, алгоритм формирования сигнала bi выбора i-й банки
можно записать в виде
i–1 _
bi = qkmiCon (bn).
n=1
817
Сигналы принадлежности выбранной банки к четной Bч или нечетной Вн группе формируются в соответствии с алгоритмами.
Продолжительность выдачи цемента в бетоносмесительное отделение зависит от длительности сигналов запроса q1 – q4. При рассмотренном способе формирования сигналов выбора разгружаемой банки и ее групповой принадлежности длительность сигналов bi, bj, Вн и Вч соответствует длительности сигналов запроса. Следовательно, алгоритмы формирования командных сигналов (см. табл. 3.5) включения донных разгружателей и вентиляторов нижних аэрожелобов можно упростить путем исключения пускового сигнала Q. В данном случае этот сигнал формируется в результате объединения сигналов запроса.
4
Q = Dis(qk).
k=1
Датчики верхнего уровня В1–В6 цемента в банках (рис. 3.18, а) используются оператором склада для контроля процессов загрузки и перекачки.
Таблица 3.5
Общие алгоритмы формирования командных сигналов в режимах выдачи, загрузки и перекачки цемента
Наименование |
Обозначение |
Алгоритм формирования КС |
||
механизмов |
исполнительных |
|
|
|
|
механизмов (рис 3.18) |
|
|
|
Разгружатели |
Mi–1, Mi–2 |
|
_ |
|
нечетных банок |
(i = 1,3,5) |
xbiv7 (Q \/P); xbiv7 (Q \/P) |
||
Разгружатели |
Mj–1, Mj–2 |
|
_ |
|
xbjv8 (Q \/P); xbjv8 (Q \/P) |
||||
четных банок |
(i = 2,4,6) |
|||
|
|
|||
|
|
|
|
|
|
|
_ |
_ |
|
|
M7 |
(φ1v11 \/φ3v15)[Bн(Q \/P) \/ |
||
|
|
5 |
||
Вентиляторы |
|
|
D(1→0)Dis(vi1\/vi2)] |
|
|
|
i=1 |
||
нижних |
|
|
||
|
_ |
_ |
||
аэрожелобов |
|
|||
M8 |
(φ1v11 \/φ2v13)[Bч(Q \/P) \/ |
|||
|
|
6 |
||
|
|
|
D(1→0)Dis(vj1\/vj2)] |
|
|
|
|
j=2 |
|
Вентилятор |
|
|
|
|
верхнего |
M6 |
G \/ D (1→0) (d2 \/ d3) |
||
аэрожелоба |
|
|
|
|
Шнек эрлифтов |
M13 |
|
d2 [G \/ D (1→0)y22] |
|
M15 |
|
d3 [G \/ D (1→0)y23] |
||
|
|
|||
Вентиль подачи |
M11 |
|
vв [g2G \/ D (1→0)y22] |
|
сжатого воздуха |
M16 |
|
vв [g3G \/ D (1→0)y23] |
818
3.2.3.Автоматическое управление оборудованием склада заполнителей
Рассмотрим, как осуществляется автоматическое управление оборудованием склада заполнителей закрытого типа с надштабельным конвейером (рис. 3.19, а). Склад состоит из пяти отсеков, в которые поступает материал по двум трактам: с автомобильного и с железнодорожного транспорта. Материал из отсеков склада также выгружается по двум трактам: в бетоносмесительное отделение и в автомобильный транспорт. При автоматическом управлении оборудованием склада заполнителей должна обеспечиваться определенная очередность включения и отключения исполнительных механизмов конвейерного транспорта.
Вработе склада предусматриваются следующие четыре режима загрузки:
1)материал поступает в отсек 1 с автомобильного транспорта;
2)материал поступает в отсеки 2–5 с автомобильного транспорта;
3)материал поступает в отсеки 2–5 с железнодорожного транспорта;
4)материал поступает в отсек 1 с железнодорожного транспорта.
Вкаждом режиме загрузки работающие питатели П1–П7 определяются селектирующими сигналами gl–g2 от переключателя выбора питателей, а загружаемые материалами отсеки склада – сигналами k1– k5 от переключателя выбора отсеков. Состояние каждого конвейера контролируется датчиками скорости ДС и датчиками наличия материала ДМ. Положение сбрасывающей тележки Н2 контролируется путевыми выключателями ВП1–ВП8 с механическим запоминанием срабатывания.
В1-м режиме загрузки питатель П7 подает материал на промежуточный конвейер М4. Затем через перегрузочное устройство материал поступает на промежуточный конвейер M5 и направляется шибером H1 двухрукавной течки в отсек 1. При подаче пускового сигнала G исполнительные механизмы тракта включаются последовательно: промежуточный М5, направляющий H1, промежуточный М4 и входной П7. После снятия сигнала G первым отключается входной исполнительный механизм П7, затем, по мере доработки материала, отключаются промежуточные М4, М5 и направляющий H1. В этом режиме исполнительный механизм П7 блокируется с пусковым элементом и датчиком скорости ДС4 (сигнал с4); М4 блокируется с пусковым элементом, переключателем выбора питателей, датчиками скорости ДС5 (сигнал с5) и наличия материала ДМ4 (сигнал m4); M5 блокируется с пусковым элементом, переключателем выбора отсеков и датчиком наличия материала ДМ5 (сигнал m5); H1 блокируется с переключателем выбора отсеков и датчиком скорости ДС5 (табл. 3.6).
819