
2598
.pdf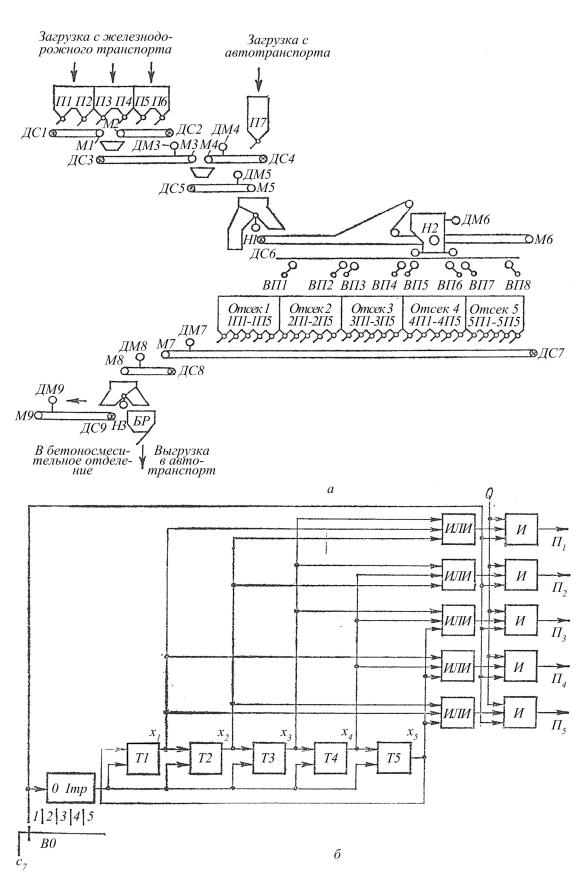
Рис. 3.19. Склад заполнителей: а– технологическая схема склада; б– структурная схема формирования командных сигналов управления питателями отсека 1
820
|
|
|
|
|
|
|
Таблица 3.6 |
||
Алгоритмы формирования командных сигналов в режимах загрузки |
|||||||||
|
|
|
|
|
|
|
|||
Наименовани |
Обозначение |
Алгоритм формирования КС в режимах загрузки |
|
||||||
исполнительны |
|
|
|
|
|
|
|
|
|
|
|
|
|
|
|
|
|
||
е механизмов |
х механизмов |
1–м |
|
2–м |
|
3–м |
|
4–м |
|
|
(рис. 3.18) |
|
|
|
|
|
|
|
|
|
П1, П2, П3 |
|
|
– |
|
g1Gc1; g2Gc1; g3Gc1; |
|
||
Питатели |
П4, П5, П6 |
|
|
– |
|
g4Gc2; g5Gc2; g6Gc2; |
|
||
|
П7 |
|
Gc4 |
|
|
– |
|
||
|
|
|
|
|
|
|
6 |
|
|
|
M1 |
|
|
– |
|
c3[G * Dis(gi)\/ m1] |
|
||
|
|
|
|
– |
|
|
i=1 |
|
|
|
M2 |
|
|
|
|
6 |
|
|
|
|
|
|
|
|
c3[G * Dis(gi)\/ m2] |
|
|||
Промежуточ |
|
|
|
– |
|
|
i=4 |
|
|
|
|
|
|
|
6 |
|
|
||
ные конвейры |
M3 |
|
|
|
|
|
|
||
|
|
|
|
c5[G * Dis(gi)\/ m3] |
|
||||
|
|
c5(g7G \/ m4) |
|
|
i=1 |
|
|||
|
M4 |
|
|
– |
|
||||
|
|
|
|
|
|
|
|
|
|
|
M5 |
|
|
(k1 \/ c6) (G \/ m5) |
|
|
|
||
|
|
|
|
|
|
|
|
|
|
Двухрукавна |
H1 |
k1c5 |
|
– |
|
|
k1c5 |
|
|
я течка |
|
|
|
|
|||||
|
|
|
|
|
|
|
|
|
|
|
|
|
|
5 |
_ |
|
|
|
|
Сбрасывающ |
|
|
|
Hв = G*Dis(kiφi); |
|
|
|
||
H2 |
– |
|
|
i=2 |
|
|
– |
|
|
ая тележка |
|
5 |
|
|
|
||||
|
|
|
|
|
|
|
|||
|
|
|
|
Hн = G*Dis(kiφi); |
|
|
|
||
|
|
|
|
|
i=2 |
|
|
|
|
Выходной |
|
|
|
G*D (1 → 0) |
|
|
|
||
M6 |
– |
|
5 |
|
|
|
– |
|
|
конвейр |
|
|
|
|
|
||||
|
|
|
Dis(kizi)\/mв |
|
|
|
|||
|
|
|
|
i=2 |
|
|
|
|
Примечания:
1. Общий алгоритм формирования КС управления исполнительным механизмом М5 получен в результате объединения частных алгоритмов k1(G\/l m5) и c6 (G\/m5).
2. Сигнал φi формируется путем выделения интервалов между левой и правой ориентациями обоих датчиков i-го отсека.
Во 2-м режиме загрузки подаваемый питателем П7 материал транспортируется промежуточными конвейерами М4, М5 и направляется шибером H1 двухрукавной течки на вход выходного конвейера М6. Сбрасывающая тележка совершает маятниковое движение в пределах заданного отсека, обеспечивая равномерное распределение поступающего материала вдоль отсека. При подаче пускового сигнала G включается исполнительный механизм тележки Н2. Когда тележка войдет в зону заданного отсека, последовательно включаются исполнительные
821
механизмы тракта: выходной М6, промежуточные М5, М4 и входной П7. После снятия сигнала G первыми отключаются исполнительные механизмы П7 и Н2, затем, по мере доработки материала, отключаются М4, М5 и М6. В этом режиме исполнительные механизмы П7 и М4 блокируются так же, как в 1-м режиме загрузки; М5 блокируется с пусковым элементом, датчиками скорости ДС6 (сигнал с6) и наличия материала ДМ5; М6 блокируется с пусковым элементом, датчиком наличия материала ДМ6 (сигнал m6), переключателем выбора отсеков и элементом контроля зоны i-го отсека (сигнал zi). При этом осуществляется селекторное управление исполнительным механизмом тележки Н2 (табл. 3.5).
В3-м режиме загрузки материал может подаваться питателями П1–П3 на промежуточный конвейер Ml или питателями П4–П6 на конвейер М2. Далее материал транспортируется промежуточными конвейерами М3, М5
ивыходным М6; сбрасывающая тележка обеспечивает равномерное распределение поступающего материала вдоль заданного отсека. При подаче пускового сигнала G исполнительные механизмы Н2, М6 и М5 включаются так же, как во 2-м режиме загрузки. Затем включаются последовательно исполнительные механизмы М3, M1 и один из входных исполнительных механизмов П1, П2 или П3. Совместно с М3 могут включаться последовательно М2 и один из входных исполнительных механизмов П4, П5 и П6. В этом режиме исполнительные механизмы П1– П6 блокируются с пусковым элементом, переключателем выбора питателей и датчиками скорости ДС1 (сигнал с1,) или ДС2 (сигнал с2); M1 и М2 блокируются с пусковым элементом, переключателем выбора питателей, датчиками скорости ДС3 (сигнал с3) и наличия материала ДМ1 (сигнал m1) или ДМ2 (сигнал m2); М3 блокируется с пусковым элементом, переключателем выбора питателей, датчиками скорости ДС5 и наличия материала ДМ3 (сигнал m3) (см. табл.3.5).
В4-м режиме загрузки в отличие от предыдущего режима, исполнительные механизмы тележки Н2 и выходного конвейера М6 не включаются, а включается исполнительный механизм H1, и шибер двухрукавной течки направляет поступающий материал в отсек 1 (см. табл. 3.6).
При выдаче материалов со склада одновременно работают три питателя выбранного отсека. Выбор отсека определяется селектирующими сигналами q1–q5 от переключателя выбора отсеков ВО, выбор питателей –
822
выходными сигналами х1–х5 кольцевого коммутатора, выполненного на триггерах Т1–Т5 по схеме сдвигового регистра (рис. 3.19, б).
|
Алгоритмы формирования команд сигналов |
Таблица 3.7 |
||
|
|
|||
|
|
|
|
|
Наименование |
Обозначение |
Алгоритм формирования КС |
||
исполнительных |
|
|
|
|
|
|
выдача в |
||
механизмов |
выдача в БСО |
|
||
механизмов (рис 3.18) |
|
автотранспорт |
||
|
|
|
||
|
1П1 – 1П5 |
q1Qc7(xi-1 \/ xi \/ xi+1) |
||
|
2П1 – 2П5 |
q2Qc7(xi-1 \/ xi \/ xi+1) |
||
Питатели |
3П1 – 3П5 |
q3Qc7(xi-1 \/ xi \/ xi+1) |
||
|
4П1 – 4П5 |
q4Qc7(xi-1 \/ xi \/ xi+1) |
||
|
5П1 – 5П5 |
q5Qc7(xi-1 \/ xi \/ xi+1) |
||
Промежуточные |
M7 |
c8 (Q \/ m7) |
||
конвейры |
M8 |
(c9 \/ p2) (Q \/ m8) |
||
Двухрукавная |
H3 |
– |
|
p2c8 |
течка |
|
|||
|
|
|
|
|
Выходной |
M9 |
p1Q \/ m9 |
|
– |
конвейр |
|
|||
|
|
|
|
Примечание. Общий алгоритм формирования КС управления исполнительным механизмом М8 получен в результате объединения частных алгоритмов с9 (Q V m8) и р2
(Q V m8).
После каждого цикла выдачи материалов при снятии сигнала датчика скорости ДС7 происходит последовательное переключение на единицу триггеров коммутатора, поэтому в новом цикле включается следующая тройка питателей. Пункт выдачи материалов со склада – бетоносмесительное отделение или автомобильный транспорт – определяется селектирующими сигналами р1 и р2 от переключателя выбора пунктов выдачи.
При выдаче материалов в бетоносмесительное отделение тройка питателей выбранного отсека подает материал на промежуточный конвейер М7. Далее материал транспортируется промежуточным конвейером М8 и направляется шибером Н3 двухрукавной течки на выходной конвейер М9. Исполнительные механизмы тракта включаются при подаче пускового сигнала Q в такой последовательности: выходной М9, промежуточные М8 и М7 и входные – тройка питателей. После снятия сигнала Q первыми отключаются исполнительные механизмы питателей, затем, по мере доработки материала, отключаются исполнительные механизмы М7, М8 и М9. В этом режиме исполнительные механизмы питателей блокируются с пусковым элементом, переключателем выбора отсеков, датчиком скорости ДС7 (сигнал с7) и кольцевым коммутатором;
823
М7 блокируется с пусковым элементом, датчиками скорости ДС8 (сигнал с8) и наличия материала ДМ7 (сигнал m7); М8 блокируется с пусковым элементом, датчиками скорости ДС9 (сигнал с9) и наличия материала ДМ8 (сигнал m8); М9 блокируется с пусковым элементом, переключателем выбора пунктов выдачи и датчиком наличия материала ДМ9 (сигнал m9) (табл. 3.7).
При выдаче материалов на автомобильный транспорт выходной конвейер М9 не включается, а включается исполнительный механизм Н3, и шибер двухрукавной течки направляет поступающий материал в расходный бункер БР. Исполнительные механизмы тракта включаются при подаче пускового сигнала Q в такой последовательности: промежуточный М8, направляющий Н3 и промежуточный М7, затем входные – тройка питателей. После снятия сигнала Q отключаются исполнительные механизмы питателей, затем, по мере доработки материала, отключаются исполнительные механизмы М7, М8 и Н3. В этом режиме исполнительный механизм М8 блокируется с пусковым элементом, переключателем выбора пунктов выдачи и датчиком наличия материала ДМ8; Н3 блокируется с переключателем выбора пунктов выдачи
идатчиком скорости ДС8 (табл. 3.6).
3.2.4.Автоматический контроль и учет материалов на складе
заполнителей
На складе заполнителей, оборудованном конвейерным транспортом, контроль принимаемых материалов – целесообразно осуществлять конвейерными весами дискретного действия, встроенными в общий тракт загрузки, а контроль отпускаемых материалов – аналогичными весами, встроенными в тракт выдачи. При этом помарочный учет материалов наиболее просто производится с помощью дифференциальных электромагнитных счетчиков импульсов (рис. 3.20, а).
В процессе загрузки емкостей склада входные конвейерные весы 1KB выдают импульсы, соответствующие определенному дискретному значению массы принятого материала. Эти импульсы поступают через селектор марки 1СМ1, управляемый переключателем марок ВМ, на вход промежуточного накопителя 1ПН1 данной марки.
Когда в промежуточный накопитель будет введено число импульсов, соответствующее дискретной единице учета материала, накопитель сбрасывается на нуль. При этом на выходе накопителя формируется
824
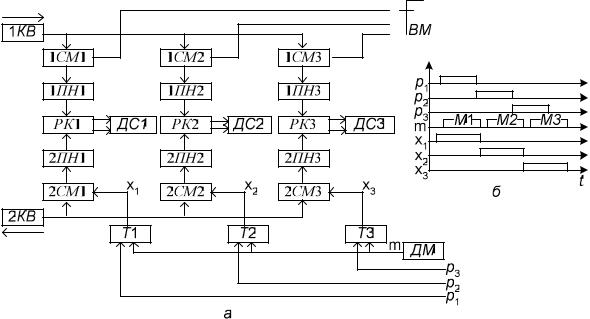
импульс, поступающий через схему разделения каналов РК1 на суммирующий вход дифференциального счетчика импульсов ДС1.
Рис. 3.20. Автоматический учет материалов на складе: а– структурная схема устройства; б– временные диаграммы формирования
При выдаче материала со склада (например, марки Ml) выходные конвейерные весы 2KB выдают импульсы, которые поступают через селектор марки 2СМ1 на вход промежуточного накопителя 2ПН1.
Выходной импульс накопителя поступает через схему разделения каналов РК1 на вычитающий вход дифференциального счетчика импульсов ДС1. Схема разделения каналов исключает возможность одновременного воздействия импульсов на суммирующий и вычитающий входы счетчика.
Выдача материалов со склада производится автоматически по сигналам запроса р1 –p3, которые всегда разделены во времени (рис.3.20,б).
Поскольку каждый сигнал запроса снимается раньше, чем заканчивается транспортирование выдаваемого материала, для управления селекторами марки 2СМ1–2СМ3 используются триггеры Т1–Т3, выделяющие интервалы времени между моментами начала сигналов запроса и окончания сигнала т датчика наличия материала ДМ на выходе тракта выдачи.
825
Промежуточные накопители позволяют уменьшить общую погрешность учета материалов, обусловленную тем, что принимаемые и отпускаемые порции материалов не всегда кратны единицам учета.
3.2.5. Автоматизация процессов сушки и нагрева материалов на складах
Основная задача автоматического управления тепловыми процессами подогрева заполнителей – проведение этих процессов в оптимальном по технологическим показателям режиме. При подогреве заполнителей необходимо автоматически регулировать их температуру в соответствии с заданным значением или в зависимости от температуры готовой бетонной смеси.
Наибольшее распространение получил двухступенчатый подогрев заполнителей, при котором устройства для подогрева вынесены за пределы бетоносмесительного отделения, в расходных бункерах которого производится только дополнительный подогрев с целью сохранения температуры заполнителей.
Подогрев заполнителей в открытых плоских, конических и трапециевидных штабелях может производиться при помощи паровых регистров и горячими газами, вдуваемыми в толщу заполнителей. В промежуточные бункера подогрева пар впускается из перфорированных или глухих регистров.
В последнее время для нагрева заполнителей в зимнее время получили применение установки с цилиндрическими вращающимися сушильными барабанами.
Автоматическое регулирование процессов подогрева и сушки заполнителей в штабелях, бункерах и сушильных барабанах может осуществляться:
1)по сигналам датчиков, контролирующих параметры теплоносителя, применяемого при нагреве;
2)по сигналам датчиков, контролирующих состояние нагреваемых заполнителей;
3)по заранее заданной программе изменения во времени режима подачи теплоносителя;
4)по комбинированному способу, сочетающему пункты 2 и 3.
К достоинствам методов, приведенных в пунктах 1 и 3, следует отнести их относительную простоту; недостатком этих методов является отсутствие информации о состоянии и параметрах нагреваемого материала.
Рассмотрим функциональную схему автоматического регулирования температуры в штабелях (рис. 3.21). Эта система регулирования
826
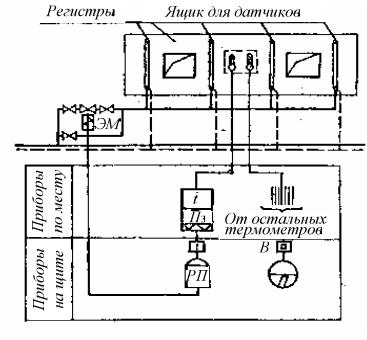
обеспечивает поддержание заданной температуры заполнителей за счет изменения количества пара, подаваемого в регистры, заложенные в штабеля. Во избежание непроизводительного расхода пара при оголенных регистрах предусмотрено устройство их отключения от паровой магистрали при снижении уровня заполнителей.
Рис. 3.21. Функциональная схема автоматического регулирования температуры заполнителей
Точность поддержания заданной температуры в штабелях невысокая, поэтому в системе осуществляется двухпозиционное регулирование температуры. Регулирующими органами служат электромагнитные клапаны ЭМ, установленные на вводе пара в регистры. Визуальный контроль температуры заполнителей в отсеках производится измерительным прибором П с переключателем В.
3.3.Автоматизация процессов дробления и сортировки
3.3.1.Основные сведения о предприятиях по переработке нерудных
строительных материалов
Предприятия по переработке нерудных строительных материалов обеспечивают потребности строительства в щебне, гравии и песке. Для этой цели существуют дробильно-сортировочные базы и заводы, гра- вийно-сортировочные заводы, заводы по обогащению песка.
827
Добыча и обогащение нерудных строительных материалов осуществляется с помощью комплекса перерабатывающих и транспортирующих машин, связанных единым технологическим процессом, представляющим собой поточно–транспортную систему
(ПТС).
Основными технологическими процессами дробильно– сортировочных предприятий являются дробление, сортировка и транспортировка.
Для дробления применяют щековые, конусные, валковые и молотковые дробилки, дезинтеграторы; для сортировки – грохоты, центрифуги; для транспортировки – тарельчатые, вибрационные и пластинчатые питатели, конвейерные линии, желоба, трубы.
Вкомплекс этих машин входят приемные, промежуточные и складские бункера и штабели. Автоматизация технологических процессов дробильно-сортировочных предприятий должна решать следующие задачи:
автоматический контроль состояния оборудования, направления грузопотоков, загрузки емкостей и наличия материалов в транспортных средствах, учет работы машин, исходного материала и готовой продукции по фракциям, а также контроль запыленности помещений и работы вентиляционных установок;
автоматическое управление пуском и остановкой в заданной последовательности технологического и транспортного оборудования, автоматическое регулирование загрузки дробильно-сортировочных агрегатов и технологических поточных линий, обеспечение оптимального режима работы технологического оборудования, автоматическое управление процессом отгрузки готовой продукции и системой обеспыливания и аспирации;
автоматическую защиту и блокировку от перегрева подшипников, перегрузки первичной дробилки, последствий поломок дробящих плит, прорыва сит на грохотах, попадания металлических предметов в дробилку, а также сигнализацию о состоянии оборудования.
Впоточно-транспортных системах должны осуществляться блокировка и защита при повреждении одного из механизмов, предпусковая сигнализация, защита и блокировка от переполнения течек и желобов складских бункеров.
Чтобы показать методику разработки и исследования автоматических систем, более подробно рассмотрены автоматизация щековой дробилки и грохота. Остальные объекты управления рассмотрены менее подробно.
828
3.3.2. Автоматическое регулирование производительности дробилок
Задача автоматического регулирования процесса дробления заключается в обеспечении оптимальной производительности дробилки за счет максимальной ее загрузки и в поддержании заданной фракционности конечного продукта. Для обеспечения оптимальной производительности дробилок их оснащают автоматическими системами регулирования, которые по степени загрузки дробилки изменяют количество материала, подаваемого питателем. Регулировать процесс дробления наиболее целесообразно на первой стадии дробления, т. е. на крупных щековых, конусных и ударных дробилках. Параметрами, характеризующими процесс дробления, являются расход и размеры материала, подаваемого в дробилку, а также фракционный состав продукции. Однако использовать эти параметры очень трудно, так как методы автоматического контроля фракционного состава материала не разработаны.
При изменении гранулометрических характеристик и твердости материала обеспечить максимальную производительность дробилки невозможно, поэтому в системах автоматического регулирования используются косвенные параметры, характеризующие процесс дробления. Такими параметрами являются: весовая загрузка питателей, сила тока электродвигателя дробилки или потребляемая им мощность, уровень материала в дробилке.
Рассмотрим методы регулирования производительности дробилки с использованием этих параметров.
Регулирование по весовой загрузке питателя заключается в поддержании заданной весовой производительности конвейера, подающего материал в дробилку. Производительность контролируется конвейерными тензометрическими или радиоизотопными весами. При изменении нагрузки датчиком подается сигнал на автоматический регулятор, исполнительный механизм которого изменяет скорость вращения питателя.
Метод регулирования с контролем по весовой загрузке питателя дает хорошие результаты только в случае постоянства гранулометрической характеристики материала. При изменении кусковатости или твердости материала обеспечить максимальную производительность дробилки невозможно. В этом случае о степени загрузки дробилки судят по силе тока двигателя. При увеличении кусковатости и твердости материала нагрузка на двигатель возрастает, в результате чего вырабатывается воздействие для уменьшения скорости ленточного питателя и подачи материала в дробилку.
При автоматическом регулировании загрузки дробилки с контролем по току двигателя на работе дробилки сказывается колебание напряжения в сети, что ограничивает применение данного метода.
829