
- •ВВЕДЕНИЕ
- •1. ТЕХНОЛОГИЯ РАБОТ ПО ЛИКВИДАЦИИ МЕЛКИХ ПОВРЕЖДЕНИЙ: ЗАЛИВКА ТРЕЩИН И ЗАДЕЛКА ВЫБОИН
- •1.1. Традиционные способы ремонта
- •1.3. Ремонт с применением инфракрасных разогревателей асфальтобетона
- •2.3. Технология устройства поверхностной обработки методом Чип Сил
- •2.4. Технология устройства слоя износа методами Слари Сил, Микросюрфейсинг и Кейп Сил
- •2.5. Особенности применения технологии Фиб-Сил для устройства трещино-прерывающей прослойки
- •3. УСТРОЙСТВО СЛОЕВ УСИЛЕНИЯ ДОРОЖНОЙ ОДЕЖДЫ
- •3.1. Методы измерения упругого прогиба и определение модуля упругости дорожной одежды
- •3.2. Традиционные материалы и технологии для усиления дорожных одежд
- •3.4 Устройство усилений из асфальтобетона, армированного геосинтетическими материалами
- •4. ПРИМЕНЕНИЕ МЕТОДОВ ГОРЯЧЕЙ РЕГЕНЕРАЦИИ ДЛЯ ВОССТАНОВЛЕНИЯ И УСИЛЕНИЯ ДОРОЖНЫХ ОДЕЖД С АСФАЛЬТОБЕТОННЫМ ПОКРЫТИЕМ
- •5.1. Характеристика района и определение допустимых сроков производства работ
- •5.3. Комплектование отрядов и калькуляция трудовых затрат
- •Библиографический список
- •Приложение 1
- •Приложение 2
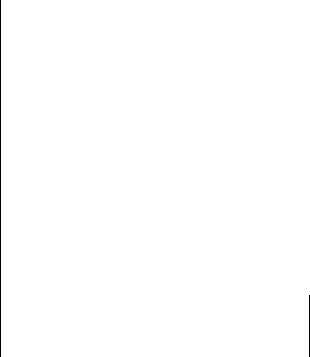
3.2. Традиционные материалы и технологии для усиления дорожных одежд
Традиционными материалами, применяемыми для устройства усиления дорожных одежд, являются материалы, используемые при усилении дорожных одежд по нормативной методике [31, разд. 5]. Такие материалы и наименьшая толщина конструктивных слоев приведены в [31, п. 5.1.3] и даны в табл. 44.
Таблица 44
Трад ц онные материалы и минимальная толщина слоев
|
|
Матер ал слоев усиления |
Толщина слоев |
|
|||
|
|
усиления, см |
|
||||
С |
|
|
|
|
|||
|
|
|
|
|
крупнозернистый |
6–7 |
|
|
Асфальтобетон: |
|
|
мелкозернистый |
3–5 |
|
|
|
|
|
песчаный |
3–4 |
|
||
|
|
|
|
|
|
||
|
|
|
|
|
холодный |
3 |
|
|
Щебеночные |
грав йные |
, обработанные органиче- |
5 |
|
||
|
материалы |
|
|
||||
|
ским вяжущ м в установке и смешением на дороге |
|
|
||||
|
Щебень, |
|
органическим вяжущим способом про- |
8 |
|
||
|
питки |
|
|
|
|
|
|
|
|
|
|
|
|
|
|
|
обработанный |
|
|
||||
|
Щебеночные и гравийные материалы, обработанные цементом |
8 |
|
||||
|
на твердом основании |
|
|
|
|
|
|
|
Грунты, обработанные органическим вяжущим способом сме- |
6 |
|
||||
|
шения на дороге |
|
|
|
|
||
|
|
|
|
|
|
||
|
Минеральные |
материалы, |
не обрабо- |
щебеночном слое |
8 |
|
|
|
гравийном слое |
10 |
|
||||
|
танные вяжущим, на: |
А |
|
|
|||
|
|
|
15 |
|
|||
|
|
|
|
|
песчаном слое |
|
|
|
Примечание. Большие из значений толщин асфальтобетонных покрытий даны |
||||||
|
для дорог I–II категорий, а меньшие – для дорог III–IV категорий. |
||||||
|
Технологии, применяемые для устройства слоев усиления из ма- |
||||||
|
|
|
|
Д |
|||
|
териалов, представленных в табл. 44, и все технологические требова- |
||||||
|
ния приведены в СП 78.13330.2012 [7] и различной нормативной, |
||||||
|
справочной и учебной литературе. |
|
|
|
|||
|
Традиционные технологии строительства слоев усиления из асфаль- |
||||||
|
тобетонных смесей, требования к ним и материалам, используемым при |
||||||
|
|
|
|
|
И |
их приготовлении, правила подбора состава смесей, технологический регламент, методы входного, операционного и приемочного контроля
описаны в пособии, руководствах и рекомендациях [35, 36, 37, 38, 39, 40, 41], учебной литературе [42, 43, 44]. Все технические требования и методы определения показателей физических и механических свойств приведены в ГОСТ 9128–2013 [45] и ГОСТ 12801–98 [46].
117
В соответствии с требованиями ГОСТ 9128–2013, классификация асфальтобетонных смесей и асфальтобетонов выполняется по следующим признакам:
1. Вид минеральной составляющей, применяемой для изготовле-
ния асфальтобетонной смеси. В зависимости от вида минерального заполнителя асфальтобетонные смеси и асфальтобетоны классифицируют на щебеночные, гравийные и песчаные ГОСТ 9128–2013 [45, п. 4.1.1].
ГОСТхолодные по 9128–2013 [45, п. 4.1.2]:
2. Вязкость, спользуемого битума и температура при укладке. В зависимости от эт х показателей смеси подразделяют на горячие и
зованиемпользован ем ж дк х нефтяных дорожных битумов и укладываемые с температурой не менее 5 °С.
– горяч ми смесями являются смеси, приготовляемые с испольвязк х ж дких нефтяных дорожных битумов и уклады-
больш наибольшего размераАминеральных зерен, применяемых при приго-
ваемые с температурой не менее 110 °С;
– холодными смесями называют смеси, приготовляемые с ис-
3. На й размер минеральных зерен. В зависимости от
товлении асфальто етонной смеси, смеси и асфальтобетон подразде-
ляют по ГОСТ 9128–2013 [45, п. 4.1.3]:
– крупнозернистые, у которых наибольший размер минеральных зерен ограничен 40 мм;
– мелкозернистые – 20 мм;
– песчаные – 10 мм.
4.Остаточная пористость. В зависимости от этого показателя асфальтобетоны подразделяют по ГОСТ 9128–2013 [45, п. 4.1.4]:
– высокоплотные с остаточной пористостью от 1 до 2,5 %;
– плотные с остаточной пористостью свыше 2,5 до 5%;
– пористые с остаточной пористостью свыше 5 до 10%;
– высокопористые с остаточной пористостью свыше 10%.
5.В зависимости от содержания в них щебня или гравия щебеночные и гравийные горячие смеси, а так же плотные асфальтобетоны подразделяют на типы ГОСТ 9128–2013 [45, п. 4.1.5]. Тип А характеризуется содержанием щебня или гравия более 50% до 60%. Тип Б характеризуется содержанием щебня или гравия более св. 40% до 50%. Тип В характеризуется содержанием щебня или гравия более 30
до 40%. В высокоплотных горячих смесях и асфальтобетонах должно содержаться щебня более 50 до 70%.ДИ
118
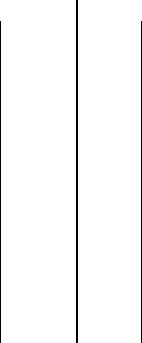
Холодные смеси и асфальтобетоны в зависимости от содержания щебня или гравия подразделяют на два типа Бх и Вх. Песчаные горя-
чие и холодные асфальтобетонные смеси и асфальтобетоны классифицируют в зависимости от вида применяемого в них песка. Горячие и холодные смеси и асфальтобетоны, в составе которых использован песок из отсевов дробления, подразделяют на типы Г и Гх. Если в составе таких асфальтобетонов применяют природный песок, то их классиф ц руют на т пы Д и Дх.
С6.Все асфальтобетоны подразделяют на марки, которые обеспепоказателями физико-механических свойств. Классифика-
Высокопор стые асфальтобетонные смеси подразделяют на вы-
чиваютсябетонов установлены количественные требования, характеризующие качество [45, разд. 5]. Все эти показатели определяются по ГОСТ 12801–98.
сокопор стые щебеночные и высокопористые песчаные.
ция устанавл вается ГОСТ 9128–2013 [45, п. 4.1.6, табл. 1].
К основным показателям и характеристикам смесей и асфальто-
Согласно рекомендациям ГОСТ 9128–2013 [45, прил. А и прил. К] для асфальто етонов, при устройстве верхних слоев покрытий дорог определена о ласть применения. Такие рекомендации приведены в табл. 45 и 46.
|
|
|
|
|
|
|
|
|
|
|
Таблица 45 |
||
Область применения асфальтобетонов при устройстве верхних слоев |
|||||||||||||
|
покрытий автомобильных дорог и городских улиц |
|
|
|
|||||||||
|
бА |
|
|
|
|
|
|||||||
Дорож- |
|
|
|
|
Категория автомобильной дороги |
|
|
|
|||||
но- |
Вид ас- |
|
I, II |
|
|
III |
|
|
IV |
|
|
||
клима- |
фальто- |
Марка |
|
Марка |
Марка |
|
Марка |
|
Марка |
Марка |
|
||
тическая |
бетона |
смеси |
|
битума |
смеси |
|
битума |
|
смеси |
битума |
|
||
зона |
|
|
|
|
|
|
|
|
|
|
|
|
|
1 |
2 |
3 |
|
|
4 |
5 |
|
6 |
|
7 |
|
8 |
|
|
|
|
|
|
|
Д |
|
|
|
||||
|
|
|
|
|
|
|
|
БНД |
|
|
БНД |
|
|
|
|
|
|
|
|
|
90/130 |
|
|
90/130 |
|
||
|
|
|
|
|
|
|
|
БНД |
|
|
БНД |
|
|
|
|
|
|
|
БНД |
|
130/200 |
|
|
130/200 |
|
||
|
Плотный |
|
|
90/130 |
|
|
БНД |
|
|
БНД |
|
||
|
и высо- |
|
|
|
БНД |
|
|
И |
|
||||
|
коплот- |
I |
|
130/200 |
II |
|
СГ |
|
III |
|
СГ |
|
|
|
|
|
|
|
|
|
|
|
|||||
|
ный |
|
|
|
БНД |
|
130/200 |
|
|
130/200 |
|
||
|
|
|
|
200/300 |
|
|
МГ |
|
|
|
МГ |
|
|
|
|
|
|
|
|
|
130/200 |
|
|
130/200 |
|
||
|
|
|
|
|
|
|
|
МГО |
|
|
МГО |
|
|
|
|
|
|
|
|
|
130/200 |
|
|
130/200 |
|
119
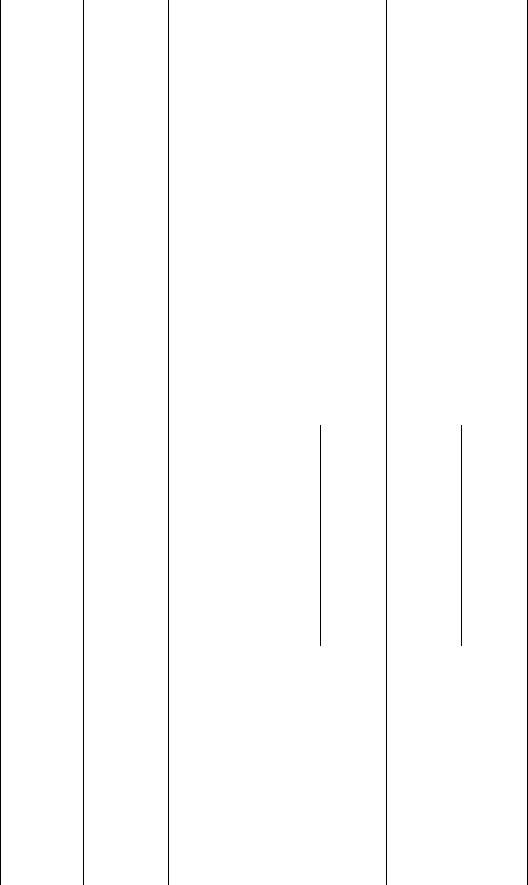
Продолжение табл. 45
|
1 |
2 |
3 |
|
4 |
5 |
6 |
7 |
8 |
|
|
|
|
|
|
|
|
|
|
БНД |
|
С |
|
|
|
|
|
|
60/90 |
|
||
|
|
|
|
БНД |
|
БНД |
|
|||
|
|
|
|
60/90 |
|
90/130 |
|
|||
|
|
|
|
БНД |
|
БНД |
|
|||
|
|
|
|
|
|
|
|
|
||
|
|
|
|
|
|
|
90/130 |
|
130/200 |
|
|
|
|
|
БНД |
|
БНД |
|
БНД |
|
|
|
|
|
|
40/60 |
|
130/200 |
|
200/300 |
|
|
|
|
Плотный |
|
БНД |
|
БНД |
|
БН 60/90 |
|
|
|
и |
60/90 |
|
200/300 |
|
БН 90/130 |
|
|||
|
|
высо- |
I |
II |
III |
|
||||
|
|
коплот- |
|
БНД |
|
БН |
|
БН |
|
|
|
|
ный |
|
90/130 |
|
60/90 |
|
130/200 |
|
|
|
|
|
|
|
БН |
|
БН |
|
БН |
|
|
|
|
|
90/130 |
|
90/130 |
|
200/300 |
|
|
|
|
|
|
|
|
|
БН |
|
СГ |
|
|
II, III |
|
|
|
|
|
130/200 |
|
130/200 |
|
|
|
|
|
|
|
|
БН |
|
МГ |
|
|
|
|
|
|
|
|
200/300 |
|
130/200 |
|
|
|
|
|
|
|
|
|
|
МГО |
|
|
|
|
|
|
|
|
|
|
130/200 |
|
|
|
|
|
|
|
|
|
|
СГ 70/130 |
|
|
|
|
|
|
|
|
|
|
СГ |
|
|
|
|
|
|
|
|
|
|
130/200 |
|
|
|
|
|
|
|
|
СГ |
|
МГ |
|
|
|
Из хо- |
|
|
|
|
|
70/130 |
|
|
|
|
|
|
|
|
70/130 |
|
|
||
|
|
бА |
II |
МГ |
|
|||||
|
|
лодных |
Не рекомендуется |
I |
СГ |
|
||||
|
|
смесей |
|
|
|
|
|
130/200 |
|
|
|
|
|
|
|
|
130/200 |
|
|
||
|
|
|
|
|
|
|
|
МГО |
|
|
|
|
|
|
|
Д |
|
||||
|
|
|
|
|
70/130 |
|
||||
|
|
|
|
|
МГО |
|
||||
|
|
|
|
|
130/200 |
|
||||
|
|
|
|
|
|
|
БНД |
|
|
|
|
|
|
|
|
|
|
40/60 |
|
БНД |
|
|
|
|
|
БНД |
|
БНД |
|
|
||
|
|
|
|
|
|
40/60 |
|
|||
|
|
|
|
40/60 |
|
60/90 |
|
|
||
|
|
|
|
|
|
БНД |
|
|||
|
|
|
|
БНД |
|
БНД |
|
|
||
|
|
|
|
|
И60/90 |
|
||||
|
|
|
|
60/90 |
|
90/130 |
|
|||
|
IV, V |
Плотный |
I |
II |
III |
БНД |
|
|||
|
БНД |
БН |
|
|||||||
|
|
|
|
|
|
90/130 |
|
|||
|
|
|
|
90/130 |
|
40/60 |
|
|
||
|
|
|
|
|
|
БН 40/60 |
|
|||
|
|
|
|
БН 40/60 |
|
БН |
|
|
||
|
|
|
|
|
|
БН 60/90 |
|
|||
|
|
|
|
БН 60/90 |
|
60/90 |
|
|
||
|
|
|
|
|
|
БН 90/130 |
|
|||
|
|
|
|
|
|
|
БН |
|
|
|
|
|
|
|
|
|
|
|
|
|
|
|
|
|
|
|
|
|
90/130 |
|
|
|
120
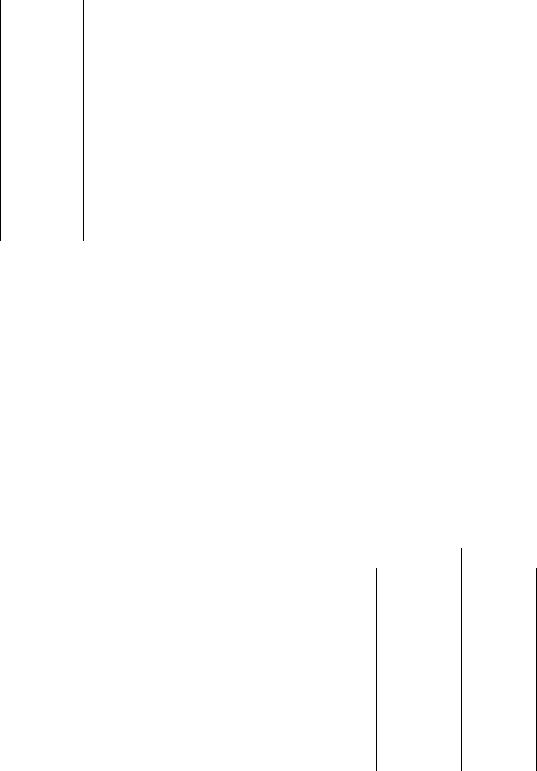
Окончание табл. 45
|
1 |
2 |
3 |
|
4 |
5 |
6 |
7 |
8 |
|
|
|
|
|
|
|
|
|
СГ 70/130 |
|
|
|
|
|
|
|
|
|
СГ |
|
|
|
|
|
|
|
|
|
130/200 |
|
|
|
|
|
|
|
СГ |
|
МГ |
|
|
Из хо- |
|
|
|
|
|
70/130 |
|
|
|
|
|
|
|
70/130 |
|
||
|
IV, V |
лодных |
Не рекомендуется |
I |
II |
МГ |
|||
|
СГ |
||||||||
|
|
смесей |
|
|
|
|
|
130/200 |
|
|
|
|
|
|
|
130/200 |
|
||
С |
|
|
|
|
|
МГО |
|||
|
|
|
|
|
|
||||
|
|
|
|
|
|
70/130 |
|||
|
|
|
|
|
|
МГО |
|||
|
|
|
|
|
|
130/200 |
|||
|
|
|
|
|
|
|
|
|
|
|
Примечан |
|
|
|
|
|
|||
|
|
я: |
|
|
|
|
|
|
|
|
1. Для городск х скоростных и магистральных улиц и дорог следует приме- |
||||||||
|
нять асфальтобетоны |
з смесей видов и марок, рекомендуемых для дорог кате- |
|||||||
|
горий I II; для дорог промышленно-складских районов – рекомендуемые для |
дорог категор III; для остальных улиц и дорог – рекомендуемые для дорог категории IV.
2. Битумы марок БН рекомендуется применять в мягких климатических условиях, характеризуемых средними температурами самого холодного месяца года выше минус – 10 °С.
3. Битум марки БН 40/60 должен соответствовать технической документации, утвержденной в установленном порядке.
Таблица 46
Область применения полимерасфальтобетонов при устройстве слоев
|
|
покрытий автомобильных дорог и городских улиц |
|
|
|
||||||
|
бА |
|
|
|
|
||||||
Дорожно- |
|
|
|
Категория автомобильной дороги |
|
||||||
|
Вид полимерас- |
|
|
I, II |
|
III |
|
||||
климатическая |
|
|
|
|
|||||||
фальтобетона |
|
Марка |
|
Марка |
Марка |
|
Марка |
|
|||
зона |
|
|
|
|
|
|
|||||
|
|
|
|
смеси |
|
битума |
смеси |
|
битума |
|
|
|
|
|
|
|
|
|
|
||||
|
|
|
Плотный и высо- |
|
|
|
ПБВ 130 |
|
|
ПБВ 130 |
|
I |
|
|
|
Д |
ПБВ 200 |
|
|||||
|
|
|
|
|
|||||||
|
|
коплотный |
|
I |
|
ПБВ 200 |
II |
|
|
||
|
|
|
|
|
|
ПБВ 300 |
|
|
ПБВ 300 |
|
|
|
|
|
|
|
|
|
|
|
|
||
|
|
|
Плотный и высо- |
|
|
|
ПБВ 60 |
|
|
ПБВ 60 |
|
II, III |
|
|
|
I |
|
ПБВ 90 |
II |
|
ПБВ 90 |
|
|
|
|
коплотный |
|
|
|
|
|||||
|
|
|
|
|
|
ПБВ 130 |
|
|
ПБВ 130 |
|
|
|
|
|
|
|
|
|
|
|
|
||
|
|
|
|
|
|
|
ПБВ 40 |
|
|
ПБВ 40 |
|
IV, V |
|
|
Плотный |
|
I |
|
И |
|
|||
|
|
|
|
|
|
|
ПБВ 60 |
|
|
ПБВ 60 |
|
Примечание. Для городских скоростных и магистральных улиц и дорог следует применять полимерасфальтобетоны из смесей видов и марок, рекомендуемых для дорог категорий I и II; а для дорог промышленно-складских районов – рекомендуемые для дорог категории III.
121
К материалам, применяемым для изготовления асфальтобетона, предъявляются определенные требования, оговоренные в соответст-
вующих государственных стандартах на технические условия. При |
||
поступлении материалов их показатели определяют в лаборатории по |
||
методикам, регламентируемым государственными стандартами на |
||
С |
||
методы испытаний. |
||
Требования к физико-механическим свойствам щебня приведены |
||
в ГО |
Т 8267–93 [26], а методы испытаний и обработки их результа- |
|
тов при определен показателей регламентированы ГОСТ 8269.0–97 |
||
определение |
||
[47]. |
Песок |
спытывают в соответствии с требованиями |
ГО |
Т 8735–88 [48], определяя все необходимые показатели, которые |
|||
сопоставляются с тре ованиями 8735–88 [49]. Показатели свойств |
||||
вязких |
ж дк х тумов регламентируются ГОСТ 22245–90 [50] и |
|||
ГО |
Т 11955–82 [51] соответственно. Определение показателей вы- |
|||
полняют согласно тре ованиям ГОСТ [52–60], каждый из которых |
||||
регламент рует |
|
одного из показателей. |
||
|
При поступлен |
материалов на завод в рамках входного кон- |
||
троля |
х тест руют |
при соответствии показателей требованиям |
||
стандартов на технические условия принимают в работу. Асфальто- |
||||
бетонный завод выпускает смесь, из которой отбирают пробы и |
||||
формуют образцы. Про ы и о разцы испытывают согласно требова- |
||||
ниям ГОСТ 12801–98 [46] и устанавливают соответствие показателей |
||||
требованиям ГОСТ 9128–2013 [45]. |
||||
|
В настоящее время разработаны технологии строительства ас- |
|||
|
|
бА |
||
фальтобетонных покрытий и оснований для различных условий. Тра- |
||||
диционная технология, позволяющая выполнить работы с наилучшим |
||||
качеством, применяется при температурах воздуха не ниже 5 оС вес- |
||||
ной и 10 оС осенью [7, п. 12.3.1]. При этом поверхность слоя, на кото- |
||||
рый производится укладка асфальтобетоннойДсмеси, должна быть су- |
||||
хой и чистой. Это требование должно выполняться в целях обеспече- |
||||
ния сцепления укладываемого слоя с нижним слоем. |
||||
|
Объемы работ по устройству асфальтобетонных покрытий и ос- |
|||
нований в РФ большие, |
что обуславливает актуальность работ, на- |
|||
|
|
|
|
И |
правленных на разработку мероприятий, позволяющих выполнять ра- |
||||
боты при более низких температурах. Поэтому нормативные и мето- |
||||
дические документы РФ содержат ряд требований, которые необхо- |
||||
димо соблюдать при выполнении работ по асфальтированию при низ- |
||||
ких |
положительных |
и |
отрицательных температурах воздуха. |
СП 78.11330–2012 [7] и пособие [36, п. 5.5] допускает выполнение ра-
122
бот с использованием горячих смесей при температурах воздуха, изменяющихся в интервале от 5 до 0 оС. При таких температурах необходимо выполнить ряд требований, позволяющих обеспечить достаточно медленную интенсивность охлаждения горячей асфальтобетонной смеси, что позволяет обеспечить требуемые температуры для ук-
Сладки смеси и уплотнения уложенного слоя. Во-первых, толщина ук-
ладываемого слоя должна быть не менее 4 см. Во-вторых, в смеси должны быть введены ПАВ, с активированными минеральными по-
рошками ли спец альными добавками. В-третьих, при устройстве низкихверхнего слоя асфальтобетонного покрытия необходимо обеспечить
температуру н жнего слоя не ниже 20 оС. Если такую температуру обеспеч ть невозможно, то выполняют строительство только нижнего слоя покрыт я, который должен быть из плотного мелкозернистого асфальтобетонабА[7].
Огран чен я накладываются СП 78.11330–2012 [7] на интервал температур воздуха, при которых допускаются работы по асфальт рован ю, а в ды и типы асфальтобетонных смесей и асфальтобетонов, пр меняемых при строительстве при пониженных температурах воздуха, могут ыть расширены за счет соблюдения требований различных специальных рекомендаций и указаний. В рекомендациях [37] изложены тре ования, позволяющие производить работы по устройству верхних слоев покрытий при пониженных температурах воздуха из крупнозернистых асфальтобетонныхДсмесей. Целью этих мероприятий является обеспечение продолжительности технологического процесса, не превышающего максимальное допустимое время, которое зависит от начальной температуры смеси на месте укладки [37, п. 4.2]. Соблюдение этих требований позволяет устраивать верхние слои покрытий не только из мелкозернистойИсмеси, регламенти-
руемой [7], но и из крупнозернистой.
Указания [8] содержат ряд требований, позволяющих расширить диапазон пониженных температур воздуха, при которых согласно требованиям [7] могут выполняться работы по асфальтированию. Соблюдение этих требований позволяет производить устройство слоев асфальтобетонных покрытий даже при отрицательных температурах воздуха, но не ниже – 10 оС.
Технологию работ по устройству асфальтобетонных покрытий при пониженных температурах следует отнести к работам в особых условиях, ограничения на которые вытекают из теплофизических рас-
123
четов. Работы в особых условиях рассматриваются в отдельной учебной, справочной и нормативной литературе.
В настоящем пособии авторы ограничатся кратким изложением технологии производства работ при температуре воздуха, только в
диапазоне от 5 оС весной и 10 оС осенью.
Спри помощи автогудронаторов.
Для обеспечения сцепления укладываемого слоя с нижним слоем необходимо выполнить очистку поверхности от пыли и грязи и подгрунтовку б тумом ли эмульсией. Очистка поверхности слоя, на которую будет выполняться укладка смеси, производится поливомоечными маш нами. Сухая очищенная поверхность подгрунтовывается
Доставку смеси выполняют автомобилями самосвалами, а ее укладку про зводят асфальтоукладчиком с последующим уплотнением катками. Асфальтоукладчик представляет собой дорожностроительную маш ну с плавающим рабочим органом, выполняю-
щую укладку, проф л |
, отделку и предварительное уплотне- |
|
рование |
|
|
ние (до определенной степени) асфальтобетонной смеси. Главным ра- |
||
бочим органом асфальтоукладчика является выглаживающая плита, |
||
которая производит формирование поперечного профиля, выравнива- |
||
ние и предварительное уплотнение уложенного слоя. Выглаживаю- |
||
щие плиты классифицируют по типу конструкции, по способам по- |
||
догрева и уплотнения. |
|
|
бА |
|
|
По типу конструкции выделяют жесткие и раздвижные выглажи- |
||
вающие плиты. Жестко выглаживающая плита является монолитной и |
||
имеет постоянную ширину, но ширину укладки можно увеличить пу- |
||
тем установки на базовую секцию навесных уширителей. |
крепле- |
ния навесных уширителей применяютДлявертикальные и горизонтальные специальные расчалы, которые жестко крепятИуширители с обеих сторон выглаживающей плиты. Раздвижная выглаживающая плита имеет изменяемую ширину. Изменение ширины выполняется при помощи гидравлически выдвигаемых уширителей. Поэтому у таких плит можно непосредственно с пульта управления оперативно изменять ширину укладки, увеличивая или уменьшая ее. Раздвижные выглаживающие плиты эффективно используются при укладке слоев с изменяющейся шириной.
По способу подогрева выделяют выглаживающие плиты с электрическим и газовым подогревом. Подогрев выглаживающей плиты является необходимым условием технологического процесса, он позволяет предотвратить налипание асфальтобетонной смеси на выгла-
124
живающие листы. Налипание смеси приводит к дефектам поверхности слоя в виде неравномерной структуры, например, образование полос, выпадение мелких частиц и т.п. Отметим, что П 78.13330–2012 [7, п. 12.3.13] регламентирует вырубку и после-
дующее переустройство участков с дефектами поверхности, к которым относят раковины, участки с избыточным или недостаточным содержанием битума и пр. Под прочим можно понимать любой дефект поверхности слоя, который можно фиксировать визуально. Поэтому прогрев выглаж вающей плиты важен, он позволяет избежать многих дефектов.
СПо способу уплотнения выделяют статическую и вибрационную выглаж вающ е пл ты, а также выглаживающие плиты с трамбующим
плитыплита уплотняет смесь за счет воздействия собственного веса. Такие целесообразны при ра оте с хорошо уплотняющимися смесями и
брусом прессующей планкой. Таким образом, по способу предвари-
тельного уплотнен я меется 4 типа выглаживающих плит. Статическая
при скорости дв жен я укладчика не более 5 м/мин. Вибрационные вы-
глаживающ пл ты уплотняют смесь за счет вибрации, которая проис-
рен в смеси. С увеличениемАтолщины укладываемого слоя влияние час-
ходит из-за вращения де алансного вала. Плавно изменяя частоту вра-
щения |
вала, изменяют вибрационное воздействие. Вибра- |
|
дебалансного |
ция способствует олее равномерному и замкнутому распределению зе- |
иперемещается вверх и вниз, какДправило, на величину 1,5 – 7 мм. За счет этого трамбующий брус направляет смесьИпод выглаживающую плиту, обеспечивая равномерную подачу смеси и ее предварительное уплотнение. Трамбующий брус устанавливается как на статические, так
ивибрационные выглаживающие плиты. Прессующая планка размещается после выглаживающих элементов плиты, она совершает вертикальные колебательные движения, которые позволяют достичь наиболее высокой степени уплотнения на этапе укладки смеси. меются сведения, что в некоторых случаях применение прессующей планки позволяет достичь требуемого коэффициента уплотнения и обойтись без применения катков.
125
Таким образом, применение трамбующего бруса или прессующей планки позволяет получить после укладки слой с наибольшей степенью предварительного уплотнения, что снизит энергоемкость процесса уплотнения катками. Целесообразность применения уплотняющих рабочих органов наглядно показана в рекомендациях [37, п. 4.4], в которых указано, что при распределении смеси с включенными уплотняющими рабочими органами коэффициент уплотнения достигает значен й от 0,86 до 0,96, а без включения этих органов значение ко-
эффиц ента уплотнен я варьируется в диапазоне 0,78–0,82. Авторы |
|
считают необход мым обратить внимание на требуемую величину |
|
коэфф ц ентов уплотнения рекомендуемые значения коэффициен- |
|
С |
. Согласно требованиям СП 78.13330–2012 |
тов запаса на |
[7,уплотнениеп. 12.5.3] коэфф ц енты уплотнения конструктивных слоев должны быть небАменее 0,99 при устройстве слоя из высокоплотного или
плотного асфальто етона типа А и Б, 0,98 – из плотного асфальтобетона т па В, Г Д, а также из пористого и высокопористого асфальтобетона, 0,96 – з холодных асфальтобетонных смесей. Требования, выдвигаемые к коэфф циентам запаса на уплотнение [7, п. 12.3.6], регламентируют, что толщина слоя из горячей асфальтобетонной смеси, уложенной асфальтоукладчиком, должна быть на 10 – 15% больше проектной толщины слоя. Таким образом, при укладке смеси укладчиком величина коэффициента запаса на уплотнение составляет
1,10 – 1,15. Для примера разделимДтребуемое значение коэффициента уплотнения 0,99 на коэффициент запаса на уплотнение 1,15, тогда получим 0,99/1,15=0,86. Сравнивая полученное значение с величинами, представленными в рекомендациях [37, п. 4.4], несложно убедиться, что они соответствуют значениям, которые характеризуют коэффициенты уплотнения после укладки смеси с включеннымиИуплотняющими рабочими органами. Поэтому требования СП 78.13330–2012 [7, п. 12.3.6] в части толщины слоя после укладки смеси справедливы при применении выглаживающей плиты с включенным трамбующим брусом или работающей прессующей планкой. Если требуемую величину коэффициента уплотнения 0,99 поделить на коэффициенты уплотнения, получаемые после укладки без применения рабочих уплотняющих органов, 078 и 0,82, то получим 0,99/0,82=1,21 и 0,99/0,78=1,27. Эти значения сопоставимы с коэффициентами запаса на уплотнение, принимаемыми при укладке смеси автогрейдером или распределением вручную, которые принимают в диапазоне 1,25–1,3 (см. СП 78.13330–2012 [7, п. 12.3.6]). Сделанное замечание крайне
126
важно потому, что ошибка в расчете толщины слоя после укладки при качественном уплотнении может привести к отклонениям толщины
конструктивного слоя, превышающим допустимые СП 78.13330–2012 [7] значения. Такое несоответствие устраняется переустройством всего дефектного участка.
Скоторыми он должен не только следить, но и управлять ими [61]. Автоматиз рованные с стемы управления (САУ) работают совместно с механ ческ ми средствами копирования базовой поверхности: лыжей или коп рной струной [61, с. 20].
Для управления выглаживающей плитой разработаны автомати-
зированные системы. Такие системы снижают нагрузку на оператора асфальтоукладч ка. выполняющего большое количество операций, за
зернистыхсмесей следует выполнять звеном средних и тяжелых кат-
огласно указан ям посо ия [36, п. 5.7] применяются асфальто-
трамбующегобрусаи ви рационной выглаживающей плиты эффекта
укладч ки, оборудованных ви рационной плитой и трамбующим
брусом уплотнен е уложенных горячих мелкозернистых и крупно-
ков. При спользован таких укладчиков уплотнение этих смесей не требует пр менен я легкого катка. Необходимость выполнения этого требования обуславливается тем, что легкие катки при применении
уплотнения не дают,Аа время на свою работу требуют. В течение этого времени температура смеси в уложенном слое уменьшается, а это
значит, что уплотнение среднимиДи тяжелыми катками потребует большего числа проходов по одному следу и будет более энергоемким. Легкие катки, работающие с асфальтоукладчиками, снабженными такими рабочими органами предварительного уплотнения, необходимы только при укладке песчаных смесей.
Укладку асфальтобетонных смесей выполняютИпо одной из трех схем. При использовании широкозахватных укладчиков укладку следует вести на всю ширину. Современные укладчики снабжены механизмами излома плиты, что позволяет укладывать двухскатный поперечный профиль слоя, причем как положительного, так и отрицательного. Укладчики снабжаются либо механическим ручным трещоточным механизмом излома плиты, либо гидравлическим приводом излома. Гидравлический привод излома позволяет автоматически изменять величину поперечного излома плиты в зависимости от пройденного расстояния. Ручной механизм излома плиты такой возможности не дает, но его оказывается достаточно в большинстве случаев, и он довольно прост в обращении.
127
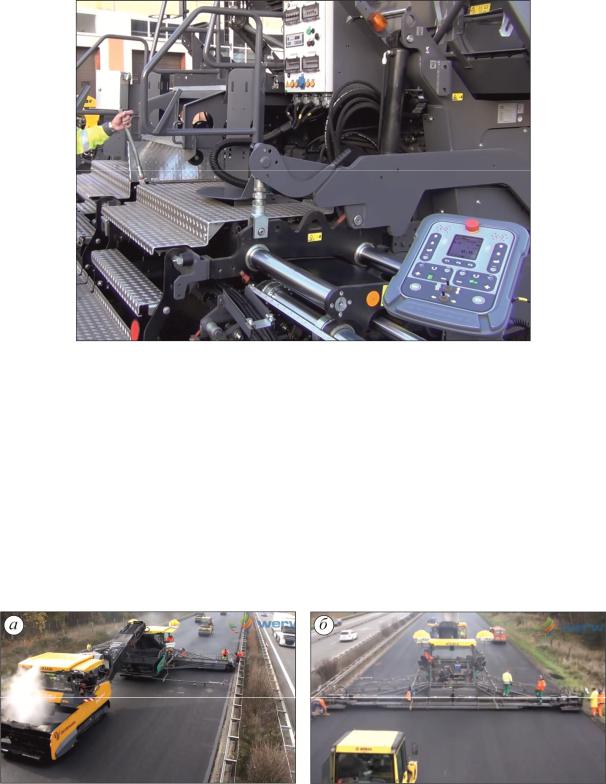
Иллюстрация управления изломом плиты при помощи ручного трещоточногомеханизма приведена на рис.66.
Си
бАРис. 66. Управление поперечным изломом плиты при помощи ручного трещоточного механизма
Эта схема считается наи олее эффективной, но при ремонте, капитальном ремонте или реконструкции может применяться при перекрытии движения по участку работД. Обычно ремонтные работы выполняют с перекрытием только одной полосы движения или перекрытием нескольких полос движения, но в одном направлении. Поэтому широкозахватные укладчики наиболее эффективны при ремонте мно-
гополосных проезжих частей. Иллюстрация такой укладки приведена на рис. 67.
И
Рис. 67. Укладка асфальтобетонной смеси широкозахватным укладчиком при капитальном ремонте проезжей части дороги I технической категории: а – направление укладки на фотографа; б – направление укладки от фотографа
128
Второй по эффективности схемой укладки асфальтобетонной смеси является укладка сопряженными полосами двумя или несколькими укладчиками [36, п. 5.8].
При невысоких темпах строительства или при ремонте с перекрытием движения по одной полосе проезжей части укладку ведут сопряженными полосами одним укладчиком [36, п. 5.9]. В этом случае необходимо обеспечивать хорошее, качественное сопряжение смежных полос. Поэтому длину укладываемой полосы ограничивают в завис мости от температуры воздуха [36, табл. 12]. Такие ограниче-
пр ведены в табл. 47.
|
|
|
|
|
Таблица 47 |
СДл на укладываемой полосы асфальтобетонной смеси |
|||||
|
Температура воздуха, °С |
Длина укладываемой полосы на участках, м |
|||
|
защищенных от ветра |
не защищенных от ветра |
|||
|
|
||||
|
5 – 10 |
30 |
– 60 |
|
25 – 30 |
|
10 – 15 |
60 – 100 |
|
30 – 50 |
|
|
15 – 25 |
100 |
– 150 |
|
50 – 80 |
|
ния |
|
|
|
|
|
Выше 25 |
150 |
– 200 |
|
80 – 100 |
|
Пр мечан е. К защ |
щенным от ветра участкам |
относят застроенные и лес- |
||
|
ные участки, а также участки в глу оких выемках. |
|
|
||
|
В пособии [36, п. 5.12] выдвигаются требования к минимальной |
||||
|
бА |
|
допустимой температуре горячей асфальтобетонной смеси при ее укладке. Минимальная допустимая температура смеси зависит от тол-
|
|
|
|
Д |
|
|
|||||||
щины слоя и температуры воздуха. Требования к минимальной тем- |
|||||||||||||
пературе смеси приведены в табл. 48. |
|
|
|
|
Таблица 48 |
||||||||
|
|
Минимальная допустимая температура |
|
|
|
|
|
||||||
|
горячей асфальтобетонной смеси при укладке |
|
|
|
|
||||||||
|
Скорость |
Минимальная температура смеси в асфальтоукладчике, |
|
||||||||||
Толщина |
|
|
|
|
|
|
И |
|
|||||
слоя, см |
ветра, |
|
°С, при температуре воздуха, °С |
|
|
|
|
||||||
|
м/с |
30 |
20 |
|
|
15 |
10 |
|
5 |
|
|
0 |
|
До 5 |
До 6 |
115 |
125 |
|
130 |
135 |
|
140 |
|
|
145 |
|
|
|
6–13 |
120 |
135 |
|
140 |
145 |
|
150 |
|
|
155 |
|
|
5–10 |
До 6 |
105 |
115 |
|
120 |
125 |
|
130 |
|
|
135 |
|
|
6–13 |
110 |
120 |
|
115 |
130 |
|
135 |
|
|
140 |
|
||
|
|
|
|
|
|
Необходимость соблюдения температурного режима укладки смеси обуславливается тем, чтобы температура смеси в период ее уплотнения катками соответствовала требуемой величине, которая характеризует возможность уплотнения до требуемой величины коэффициента уплотнения. Интенсивность остывания смеси зависит от температуры воздуха, скорости ветра и толщины слоя. Чем меньше
129
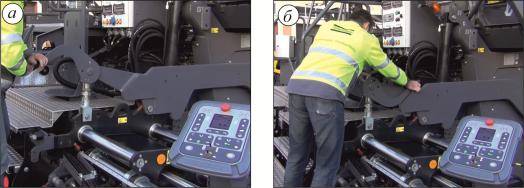
толщина слоя, тем интенсивнее остывает смесь. Поэтому минимальная температура смеси при укладке тонких слоев выше, чем при укладке более толстых слоев. Чем ниже температура окружающей среды и выше скорость ветра, тем интенсивнее остывает смесь. Эти обстоятельства учитываются в табл. 48 тем, что минимальная темпера-
Стура смеси возрастает при понижении температуры воздуха и увеличении скорости ветра.
Толщ на слоя, укладываемого асфальтоукладчиком, регулирует-
ся углом атаки выглаж вающей плиты, который изменяется путем ус- глаживающейтановки рычага определенное положение. На рис. 68 приведены ил-
люстрац установки максимального и минимального угла атаки выпл ты.
РисбА. 68. Регулировка угла атаки выглаживающей плиты:
а – установка рычага в положениеД«максимальный угол атаки»; б – установка рычага в положение «минимальный угол атаки»
Когда угол атаки выглаживающей толщины минимальный, то укладываемый слой имеет минимальную толщину, и, наоборот, если угол атаки максимальный, то слой укладываетсяИмаксимальной толщины. Большинство современных укладчиков способны укладывать слои максимальной толщиной 30–35 см. Некоторые модели, например Vogele Super 3000-2, укладывает слои толщиной до 50 см на всю ширину дороги, работая с производительностью до 1600 т/ч.
Современные укладчики снабжены информационными пультами управления оператора асфальтоукладчика и дорожного мастера. Пульт оператора расположен в кабине, а пульт мастера монтируется в задней части укладчика и позволяет мастеру, не теряя визуального контроля над процессом укладки и количеством материала перед выглаживающей плитой, вносить изменения в рабочие настройки шнека, транспортера, автоматической системы управления. На рис. 69 приве-
130

дена иллюстрация пульта управления мастера, которым снабжен ук-
ладчик Atlas Copco (Dynapac).
Си бА Д
аи б – управление механическими тумблерамиИуширения плиты
иконтроля за цилиндрами толщины слоя; в, г и д – кнопочные блоки настройки параметров транспортера, винтового шнека и автоматической системы нивелирования; е – информационный дисплей
131
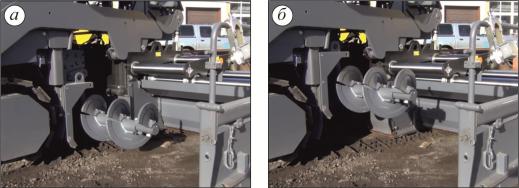
Геометрические характеристики слоя (ширина, толщина, поперечный уклон) являются параметрами, подлежащими строительному контролю. Если их отклонения от данных проекта или нормативных документов превышают допуски, оговоренные в СП 78.13330 [7, разд. 12 и прил. А, табл. А1], то дефектные участки переустраива-
Сются. Поэтому возможность изменения мастером параметров укладки асфальтобетонной смеси непосредственно с пульта управления способствует повышен ю качества устройства слоев из асфальтобетона.
Кроме того, возможность оперативного управления винтовым нияшнеком тоже пр вод т к повышению качества укладки. Шнек расположен перед выглаж вающей плитой и предназначен для перемещеасфальтобетонной смеси из зоны выгрузки транспортного транспортера в зону боковых щитков, которые ограничивают ширину слоя. РавномерностьбАраспределения смеси шнеком по ширине влияет на количество матер ала перед выглаживающей плитой (призма волоче- ). Равномерность распределения смеси в призме волочения сильно влияет на качество уложенной поверхности. Винтовой шнек может управляться автомат з ровано или вручную. Автоматизированное управление шнеком о еспечивается ультразвуковыми датчиками. На современных укладчиках ручное управление имеет важную особенность, оно позволяет выполнить реверсивное вращение шнека, то есть переместить материал в направлении от боковых щитков к середине. Шнек может перемещаться по высотеД(рис. 70), что обеспечивается
гидравлической регулировкой рамы шнека по высоте.
Рис. 70. Иллюстрация перемещения винтовогоИшнека по высоте: а и б – положения шнека в нижней и верхней точках траектории вертикального перемещения
Основные работы по устройству асфальтобетонного слоя включают: доставку асфальтобетонной смеси, ее перегрузку в приемный бункер асфальтоукладчика, укладку смеси и предварительное уплот-
132

нение асфальтоукладчиком, окончательное уплотнение звеном катков. Наиболее распространенной схемой устройства конструктивного слоя дорожной одежды является технология работ, показанная на рис. 71 [62].
С |
|
катки |
|
бА |
|
Рис. 71. Трад ц онная технология устройства конструктивного слоя из горячей |
|
асфальтобетонной смеси специализированным отрядом, включающим самосва- |
|
лы, асфальтоукладч |
[62, рис. 6, С. 5] |
Укладка выполняется на подгрунтованную поверхность, которая осуществляется за 1–6 ч до начала укладки по сухой и очищенной от грязи и пыли поверхности. При усилении существующей дорожной одежды все дефекты существующего покрытия (трещины, выбоины и неровности) должны ыть заделаны и фрезерованы.
Норма расхода вяжущего, применяемого для подгрунтовки, регламентируется СП 78.13330.2012 [7, п. 12.3.2], а требуемая температура нагрева указана в [7, табл. 9]. Следуя этим требованиям, температуру нагрева органического вяжущего принимают по табл. 49, а
норму расхода – по табл. 50. |
|
И |
||
|
|
|
Таблица 49 |
|
Температура нагреваДорганического вяжущего |
|
|||
Показатель консистенции вяжущего |
|
|
Температура нагрева, оС |
|
|
40–60 |
|
140–150 |
|
Глубина проникания иглы при |
61–90 |
|
135–145 |
|
91–130 |
|
130–140 |
|
|
25 °С, 0,1 мм |
|
|
||
131–200 |
|
120–130 |
|
|
|
|
|
||
|
201–300 |
|
110–120 |
|
Условная вязкость по вискозиметру |
131–200 |
|
90–110 |
|
с отверстием 5 мм при 60 °С, с |
70–130 |
|
80–90 |
|
Из анализа данных табл. 49 следует, что чем больше вязкость битума, тем выше требуемая температура его нагрева.
133
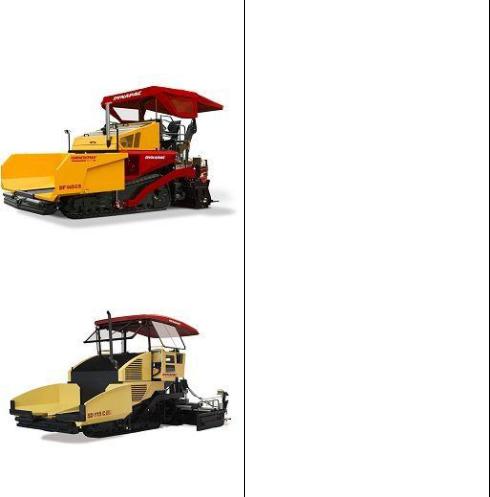
Таблица 50
Нормы расхода органических вяжущих, применяемых для подгрунтовки поверхности перед устройством асфальтобетонного слоя
Вид органического вяжущего |
Грунтуемая поверхность |
Расход, л/ м2 |
|
Битум |
Нижний слой асфальтобетон- |
0,2–0,3 |
|
ного покрытия |
|||
|
|
||
Битумная эмульсия 60% |
Основание дорожной одежды |
0,5–0,8 |
|
Битум |
Нижний слой асфальтобетон- |
0,3–0,4 |
|
ного покрытия |
|||
|
|
||
Битумная эмульс я 60% |
Основание дорожной одежды |
0,6–0,9 |
|
асфальтоукладчиков |
|
|
|
|
||
|
В табл. 51 пр ведены технические характеристики некоторых со- |
||||||
Свременных |
. |
|
|
Таблица 51 |
|||
|
Техн ческ |
е характеристики асфальтоукладчиков |
|||||
|
Общ й в д |
|
Техническая характеристика |
Величина |
|
||
|
1 |
|
|
2 |
3 |
|
|
|
|
|
Производитель |
|
DYNAPAC |
|
|
|
|
|
Модель |
|
|
DF145CS |
|
|
|
|
Масса, кг |
|
|
20300 |
|
|
|
|
Мощность, кВт |
172 |
|
||
|
|
|
Ходовая часть |
|
|
гусеничная |
|
|
|
|
Ширина |
|
стандартная |
2550 |
|
|
|
|
|
минимальная |
2000 |
|
|
|
|
|
укладки, мм |
|
|
||
|
|
|
|
максимальная |
13500 |
|
|
|
|
|
|
|
|
||
|
|
|
Толщина слоя при укладке, мм |
до 350 |
|
||
|
бА |
|
|
||||
|
|
Рабочая скорость м/мин |
до 23 |
||||
|
|
|
Транспортная скорость, км/ч |
5 |
|
||
|
|
|
Производитель |
|
DYNAPAC |
|
|
|
|
|
Модель |
|
|
SD115C |
|
|
|
|
Масса, кг |
|
И |
|
|
|
|
|
|
|
19200 |
|
|
|
|
|
Д |
|
|||
|
|
|
Мощность, кВт 120 |
||||
|
|
|
Ходовая часть |
|
|
гусеничная |
|
|
|
|
Ширина |
|
стандартная |
2550 |
|
|
|
|
укладки, мм |
|
минимальная |
2000 |
|
|
|
|
|
максимальная |
8200 |
|
|
|
|
|
|
|
|
||
|
|
|
Толщина слоя при укладке, мм |
До 300 |
|
||
|
|
|
Рабочая скорость м/мин |
До 25 |
|
||
|
|
|
Транспортная скорость, км/ч |
4,5 |
|
134

|
|
|
|
Продолжение табл. 51 |
||
|
1 |
|
2 |
|
3 |
|
|
|
Производитель |
|
DYNAPAC |
|
|
С |
Модель |
|
|
SD135C |
|
|
Масса, кг |
|
|
20000 |
|
||
Мощность, кВт |
|
140 |
|
|||
Ходовая часть |
|
Гусеничная |
|
|||
Ширина |
стандартная |
2550 |
|
|||
укладки, |
минимальная |
2000 |
|
|||
мм |
максимальная |
10000 |
|
|||
Толщина слоя при укладке, мм |
До 300 |
|
||||
Рабочая скорость м/мин |
До 25 |
|
||||
Транспортная скорость, км/ч |
4,5 |
|
||||
|
и |
Производитель |
|
DYNAPAC |
|
|
|
Модель |
|
|
DF145P |
|
|
|
Масса, кг |
|
|
18300 |
|
|
|
Мощность, кВт |
|
153 |
|
||
|
Ходовая часть |
|
Колесная |
|
||
|
|
Ширина |
стандартная |
2550 |
|
|
|
|
укладки, |
минимальная |
2000 |
|
|
|
|
мм |
максимальная |
8800 |
|
|
|
|
Толщина слоя при укладке, мм |
До 300 |
|
||
|
|
Ра очая скорость, м/мин |
До 23 |
|
||
|
|
Транспортная скорость, км/ч |
5 |
|
||
|
|
|
|
|
ОАО «Брян- |
|
|
|
До |
|
|||
|
|
Производитель |
|
ский арсенал» |
|
|
|
бА |
|
|
|||
|
|
Модель |
Асф-К-3-02 |
|||
|
|
Масса, кг |
|
|
16500 |
|
|
|
Мощность, кВт |
|
155 |
|
|
|
|
Ходовая часть |
|
Колесная |
|
|
|
|
|
|
И |
|
|
|
|
Ширина укладки, мм |
2500–4500 |
|
||
|
|
Толщина слоя при укладке, мм |
250 |
|
||
|
|
Рабочая скорость м/мин |
До 20 |
|
||
|
|
Транспортная скорость, км/ч |
16 |
|
||
|
|
Производитель |
|
ОАО «Брян- |
|
|
|
|
|
ский арсенал» |
|
||
|
|
|
|
|
|
|
|
|
Модель |
|
|
Асф-К-2-04 |
|
|
|
Масса, кг |
|
|
14500 |
|
|
|
Мощность, кВт |
|
77,2 |
|
|
|
|
Ходовая часть |
|
Колесная |
|
|
|
|
Ширина укладки, мм |
2500–4700 |
|
||
|
|
Толщина слоя при укладке, мм |
До 250 |
|
||
|
|
Рабочая скорость м/мин |
До 25 |
|
||
|
|
Транспортная скорость, км/ч |
18 |
|
135
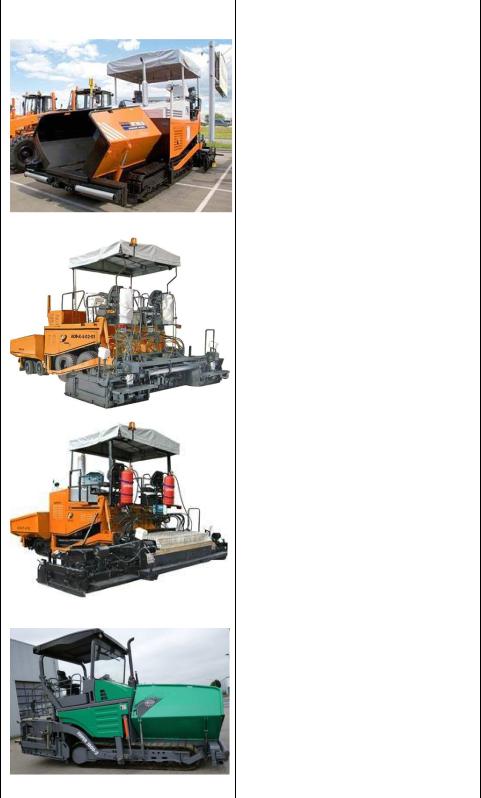
|
|
Продолжение табл. 51 |
||
|
1 |
2 |
3 |
|
|
|
Производитель |
ОАО «Брян- |
|
|
|
ский арсенал» |
|
|
|
|
|
|
|
|
|
Модель |
Асф-Г-3-08 |
|
|
|
Масса, кг |
16400 |
|
|
|
Мощность, кВт |
114 |
|
|
|
Ходовая часть |
Гусеничная |
|
|
и |
Ширина укладки, мм |
2500–4500 |
|
|
Толщина слоя при укладке, мм |
До 300 |
|
|
|
Рабочая скорость м/мин |
До 14 |
|
|
С |
|
|||
Транспортная скорость, км/ч |
3,3 |
|
||
|
|
Производитель |
ПО «Ирмаш» |
|
|
|
Модель |
Асф-К-4-02-01 |
|
|
|
Масса, кг |
19800 |
|
|
бА |
96,5 |
|
|
|
|
Мощность, кВт |
|
|
|
|
Ходовая часть |
Колесная |
|
|
|
Ширина укладки, мм |
2500–4500 |
|
|
|
Толщина слоя при укладке, мм |
До 300 |
|
|
|
Ра очая скорость м/мин |
До 20 |
|
|
|
Транспортная скорость, км/ч |
16 |
|
|
|
Производитель |
ПО «Ирмаш» |
|
|
|
Модель |
Асф-Г-4-03 |
|
|
|
Масса, кг |
22000 |
|
|
|
Мощность, кВт |
154 |
|
|
|
Ходовая часть |
Гусеничная |
|
|
|
Ширина укладки, мм |
2500–9000 |
|
|
|
Толщина слоя при укладке, мм |
300 |
|
|
|
Рабочая скорость м/мин |
До 24 |
|
|
|
Транспортная скорость, км/ч |
3,1 |
|
|
|
Производитель |
Vоgele |
|
|
|
До |
|
|
|
|
Модель SUPER 1800-2 |
||
|
|
Масса, кг |
20000 |
|
|
|
Мощность, кВт |
129,6 |
|
|
|
Ходовая часть |
Гусеничная |
|
|
|
Ширина укладки, мм |
2550–9000 |
|
|
|
И |
|
|
|
|
Толщина слоя при укладке, мм До 300 |
||
|
|
Рабочая скорость м/мин |
До 24 |
|
|
|
Транспортная скорость, км/ч |
4,5 |
|
136
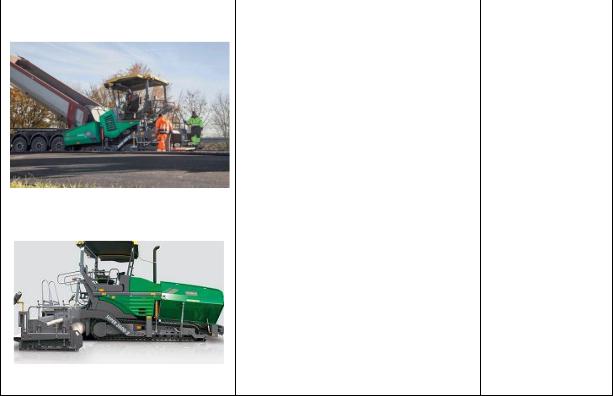
|
|
Окончание табл. 51 |
|
|
1 |
2 |
3 |
|
|
Производитель |
Vоgele |
|
|
Модель |
SUPER 1800-3 |
|
|
Масса, кг |
24900 |
|
|
Мощность, кВт |
116 |
|
|
Ходовая часть |
Гусеничная |
|
|
Ширина укладки, мм |
2550–10000 |
|
|
Толщина слоя при укладке, мм |
До 300 |
|
|
Рабочая скорость, м/мин |
До 24 |
|
|
Транспортная скорость, км/ч |
4,5 |
С |
Производитель |
Vоgele |
|
Модель |
SUPER 3000-2 |
||
|
и |
|
|
|
Масса, кг |
22150 |
|
|
Мощность, кВт |
300 |
|
|
Ходовая часть |
Гусеничная |
|
|
Ширина укладки, мм |
3000–16000 |
|
|
Толщина слоя при укладке, мм |
До 500 |
|
|
|
||
|
|
Ра очая скорость, м/мин |
До 24 |
|
|
Транспортная скорость, км/ч |
4,5 |
выполняетсябАукладка.
Выбор укладчика о уславливается тремя обстоятельствами, к которым относят нео ходимую ширину укладки, требования к мобильности передвижения, а при ремонте состояние основания, на которое
Гусеничные укладчики эффективны при устройстве слоев большой ширины, они могут выполнять постройку двухскатного профиля на всю ширину. Участки ремонта покрытия могут выбираться выбо-
рочно, что требует мобильностиДперемещения от одного участка укладки к другому, расположенному от первогоИна некотором расстоянии. Это требует мобильного перемещения укладчика. В таких случаях наиболее целесообразно применять колесный укладчик. При восстановительном ремонте существующее покрытие фрезеруют на определенную глубину, что позволяет частично устранить дефекты и неровности. В ряде случаев фрезерование предусматривают не на всем протяжении ремонтируемого участка, а лишь на его отдельных частях. Суммарная протяженность таких участков может составлять 10–70% от длины ремонтируемого участка. В таких случаях на участках с неотфрезерованной поверхностью могут сохраняться неровности, которые копируются колесным укладчиком, что может привести к неудовлетворительной ровности отремонтированного покрытия. В
137
таких случаях предпочтение отдают гусеничному укладчику. Следовательно, для применения колесных укладчиков необходимы два обязательных условия: небольшая ширина укладки и качественно подготовленная поверхность, по которой выполняется устройство слоя. Мобильность перемещения колесного укладчика важна при выборочном ремонте покрытия, в этом случае она является определяющим фактором. В иных условиях целесообразно применение гусеничных укладч ков.
Обсуждая вопрос выбора способа подогрева выглаживающей |
|||
плиты, отмет м, что стоимость укладчика с газовым обогревом |
|||
меньше, чем с электр ческим. Газовый обогрев работает независимо |
|||
С |
|
|
|
от |
, что повышает ресурс двигателя. Газовый обогрев в экс- |
||
плуатац |
дешевле, но тре ует второго вида топлива. Газовые балло- |
||
ны необход мо вовремя подвозить на объект и монтировать на уклад- |
|||
чике, а после про зводства ра от их демонтируют. Электрический |
|||
обогрев |
|
|
и не требует второго вида топлива. |
двигателя |
|
||
Электр |
ческ й огрев значительно безопаснее газового. Укладчики |
||
с электр ческ м подогревом комплектуют более мощным двигате- |
|||
лем, от которого |
генератор, питающий электрический обог- |
||
рев. Электрообогрев |
отает с полной мощностью только перед на- |
||
|
работает |
||
чалом работ, а при выполнении укладки мощность уменьшается. На- |
|||
гревательные элементы распределены по поверхности плиты и могут |
|||
|
|
А |
уплотнение смеси. Д Существуют выглаживающие плиты высокого уплотнения, кото-
включаться независимо. Нагревательными элементами снабжены трамбующий брус и прессующая планка, их нагрев предотвращает налипание смеси на уплотняющие органы. В настоящее время элек-
трический обогрев вытесняет газовый. Электрообогрев более удобен
в работе и позволяет более качественно выполнять предварительное И
рые укомплектованы вторым трамбующим брусом или одной-двумя прессующими планками. Такие плиты позволяют укладывать слой с более высоким коэффициентом уплотнения до 0,95–0,98. Безусловно,
что при уплотнении катками это преимущество позволяет уменьшить как количество катков, так и число проходов по одному следу. Поэтому анализ возможностей асфальтоукладчика в части предварительного уплотнения смеси необходим при проектировании технологии уплотнения, связанной с выбором типа катков, определением их весовых параметров и ориентировочным назначении числа проходов. Только в этом случае в проекте производства работ можно обоснован-
138
но подобрать звено катков. Проверка и уточнение параметров уплотнения принятым звеном катков осуществляется выполнением пробной укатки, которая позволяет определить требуемое число проходов по одному следу в конкретных условиях (температура уплотняемой смеси, толщина укладываемого слоя, температура воздуха, скорость ветра и т.п.).
Доставка смеси организовывается бесперебойно, что требует ряда технолог ческ х расчетов. В первую очередь оценивают расстоя-
ние, на которое может быть доставлена смесь [63]. Условием такого |
||
расчета является обеспечение требуемой температуры укладки и тем- |
||
пературы последующего уплотнения. Самосвалы, оборудованные |
||
С |
|
|
системой подогрева кузова (или) термоизоляцией кузова, обеспечи- |
||
вают менее нтенс вное остывание смеси. Интенсивность остывания |
||
смеси можно уменьш ть, |
укрыв ее в кузове тентом. Кроме того, на- |
|
личие укрывного материала препятствует образованию корки, кото- |
||
рая появляется на |
|
смеси при остывании или способству- |
поверхности |
|
|
ет существенному уменьшению толщины этой корки. В настоящее |
||
время выпускают спец альные самосвалы для перевозки горячей ас- |
||
фальтобетонной смеси. Такие машины оборудованы термостойким |
||
кузовом ковшового типа с двойными боковыми стенками и много- |
||
слойным днищем, имеют систему газового обогрева выхлопными га- |
||
зами. Для снятия потерь сверху эти машины снабжены алюминиевым |
||
бА |
Загрузка асфальтобетонной Дсмеси в бункер укладчика выполняется постепенно в процессе работы укладчика. При работе укладчик, двигаясь вперед, укладывает смесь и толкает самосвал, который отгружает смесь в расходный бункер по мере продвижения укладчика. Доставив асфальтобетонную смесь на объект, водитель подает само-
механическим тентом. Таким образом, специальные самосвалы снабжены комплексом мероприятий по предотвращению потерь тепла. Отсюда следует, что для доставки горячей смеси на разные расстояния можно применять различные самосвалы, снабженные разными
системами сохранения тепла. |
И |
|
свал под разгрузку задним ходом. Выполняя этот маневр, необходимо остановить самосвал на близком расстоянии от укладчика. Укладчик, вырабатывая остатки смеси от предыдущей загрузки, приближается к самосвалу и упирается в самосвал подкатными отбойными роликами [64, разд. 5.2]. Такая схема стыковки самосвала и укладчика обусловлена тем, что при ударе самосвала, двигающегося задним ходом, об отбойные ролики на поверхности свежеуложенного слоя возникает
139
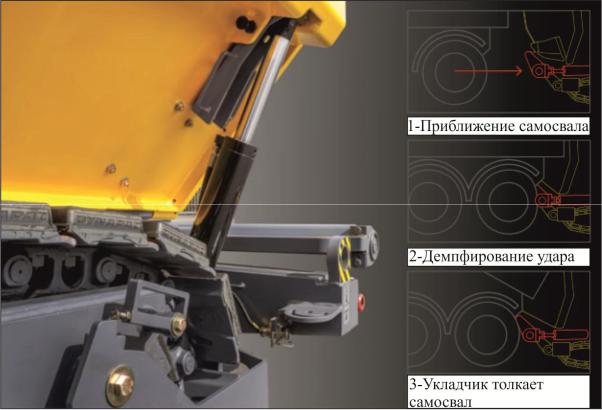
отпечаток выглаживающей плиты. Такой отпечаток является дефектом, требующим устранения. У современных укладчиков рама отбойных роликов снабжается двумя гидравлическими цилиндрами, выполняющими роль демпферов и гасящих энергию удара [65, с.2]. Такая конструкция позволяет избежать дефекта свежеуложенной по-
Сверхности при случайном ударе самосвала об отбойные ролики. Такими роликами оснащены гусеничные асфальтоукладчики серии SD, выпускаемыми компан ей DYNAPAC. Схема гашения энергии удара системой отбойных роликов с механизмом гидравлического демпфи-
рования«Safe Impact» приведена на рис. 72 [65, с. 4]. бА Д
Рис. 72. Схема гашения энергии удара системойИ«Safe Impact»
Система «Safe Impact» позволяет регулировать вылет от роликов до колес самосвала и использовать автомобили различных типов.
Водитель медленно поднимает кузов, и смесь перемещается к заднему борту. После этого задний борт открывают. Такая последовательность помогает производить разгрузку смеси непрерывным потоком и уменьшать ее сегрегацию, которая создает дефекты в покрытии
[64, разд. 5.2].
140
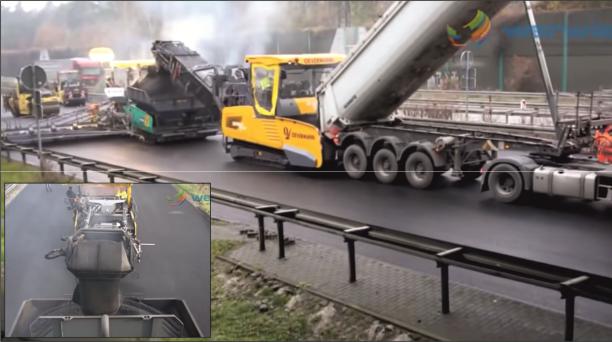
Технология загрузки расходного бункера укладчика непосредственно из самосвала постепенно вытесняется пришедшей из-за рубежа новой технологией, согласно которой для перегрузки смеси применяют специальный перегружатель. Иллюстрация этого технологическо-
го процесса приведена на рис. 73. Си
Рис. 73. ПрименениебАперегружателя асфальтобетонной смеси при ее приемке из самосвала и погрузке в расходный бункер укладчика
В настоящее время вДРФ действуют рекомендации ОДМ 218.5.002–2009 [66] по применению перегружателей асфальтобетонной смеси в технологическом процессе устройства покрытий. Согласно указаниям [66, разд. 4] применениеИперегружателя асфальтобетонной смеси дает преимущества в качестве укладываемого слоя и технологичности процесса. Главным преимуществом, способствующим повышению качества, является устранение фракционной и температурной сегрегации [66]. Положительными технологическими являются непрерывная подача смеси в расходный бункер, отсутствие контакта самосвала и укладчика, увеличение скорости разгрузки и укладки, возможность применять асфальтоукладчик в местах, где из-за ограничений по высоте невозможна разгрузка самосвалов (в тоннелях, под мостами, линиями электропередач и т.д.).
Сигнал для начала перегрузки подает оператор перегружателя, а водитель самосвала подает его задним ходом до касания колесами упорных валиков перегружателя [66]. При устройстве асфальтобетон-
141
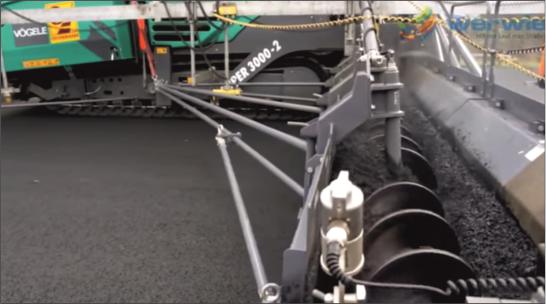
ных слоев с применением перегружателя смеси возможны различные схемы работы машин. Самосвал может разгружаться в неподвижный перегружатель, а может перемещаться вместе с ним. Первую схему разгрузки самосвала применяют, когда бункер асфальтоукладчика заполнен смесью. Вторую схему используют, когда перегружатель по-
Сдает смесь в асфальтоукладчик. В случаях применения двух перегружателей один стоит под загрузкой, а второй перегружает смесь в укладч к.
Выгруженная в отвальный бункер перегружателя смесь при помощиив браторов подается на сходящийся трехшаговый шнек, который перемеш вает смесь и перемещает ее по конвейеру в промежуточный бункер. В н жней части промежуточного бункера установлено два трехшаговых шнека, которые подают смесь на задний конвейер, устраняябАфракц онную температурную сегрегацию. Из заднего конвейера смесь непрерывно поступает в приемный бункер укладчика
[66, разд. 5].
Укладывая асфальто етонную смесь, укладчик должен перемещаться с постоянной скоростью, не превышающей 2,5 – 3,0 м/мин, но в случаях доставки смеси после длительного перерыва большим количеством самосвалов допускается на непродолжительное время увеличить скорость укладчика до 5 м/мин [36, п. 5.16]. Из приемного бункера асфальтоукладчика смеси по транспортеру подаются в зону шнеков. В процессе укладки визуальноДконтролируют равномерность распределения винтовыми шнеками смеси по ширине (рис. 74).
И
Рис. 74. Равномерность распределения смеси по ширине правым шнеком
142
Асфальтоукладчик работает непрерывно, его остановка производится в том случае, когда уровень смеси в бункере опускается до
уровня шиберных заслонок [64]. При ожидании самосвала в течение небольшого периода времени нельзя расходовать смесь настолько, что будет виден пластинчатый питатель. Такое же требование регламентирует пособие [36, п. 5.14]. Смесь вырабатывают полностью только в конце смены и при остановке работ на длительный период. В
СУкладка горяч х смесей производится с включенным трамбующим брусом, холодные смеси укладывают при выключенном трамбующем брусе [36, п. 5.17].
этом случае во збежание поломки асфальтоукладчика расходуют
всю смесь, находящуюся в бункере, шнековой камере и под плитой.
органаостановкиза 10 м до . Если в процессе работ по укладке смеси
При необход мости совершить остановку укладчика оператор должен пр нять меры для предотвращения возникновения на поверхности слоя уступа. Для этого оператор выключает привод рабочего
происход тбпереполнение шнековой камеры, то необходимо произвести регул ровку лопаток датчиков уровня.
После прохода асфальтоукладчикаАповерхность слоя осматривают на предмет наличия трещин, раковин, разрывов и т.п. дефектов. Наличие таких дефектов недопустимо, а одной из причин их возникновения может ыть неточная регулировка рабочих органов по высо-
чины их возникновения и способыДустранения представлены в технических рекомендациях ТР 103-07 [67] и приведены нами в табличной форме ниже по тексту.
те, недостаточная температурой прогрева выглаживающей плиты, неравномерное заполнение смесью шнековой камеры [36, п. 5.18]. Обнаруженные дефекты исправляют вручную до начала уплотнения
слоя катками. Перечень дефектов, возникающих при устройстве ас-
фальтобетонного слоя при укладке и уплотнении смеси, а также при- И
При укладке смеси сопряженными полосами особое внимание уделяют устройству продольных и поперечных сопряжений уклады-
ваемых полос. Длина укладываемой полосы ограничена требованиями табл. 47. Согласно ТР 103-07 [67, п. 5.2.3, табл. 4] при укладке сопряженных полос двумя укладчиками длины укладываемых участков могут быть увеличены.
В процессе устройства сопряжений необходимо соблюдать требования по температуре смеси в ранее уложенной полосе. Если температура смеси в смежной полосе ниже требуемой, то ее края разо-
143

гревают. Для разогрева применяют один из двух способов. Согласно требованиям [36, п. 5.19] края ранее уложенной полосы можно разогреть путем укладки на полосу горячей смеси шириной 10–20 см. Под воздействием температуры кромка ранее уложенной полосы разогревается. Выполнив разогрев полосы, смесь сдвигают на смежную не-
Суплотненную полосу. При этом у сопряжения полос толщина неуплотненной полосы не должна быть меньше толщины ранее уложенной, уплотненной полосы. Вторым способом разогрева кромки является пр менен е нфракрасных разогревателей асфальтобетона, вы-
разогревателя могут перемещаться пешим оператором, а могут монна укладч ке и перемещаться вместе с ним. Иллюстрация
тироватьсяполненных в в де линейки. Их применение регламентируется [36, п. 5.19] рекомендациями [67, п. 5.5.4]. Инфракрасные линейки-
такого оборудованбАя приведена на рис. 75.
а– перемещаемая пешим операторомД; б – перемещаемая асфальтоукладчиком
Спомощью линейки-разогревателя нагревИасфальтобетонного слоя толщиной 3 – 4 см до температуры 80 – 100 °С осуществляется в течение 2 – 3 мин. Линейку-разогреватель перемещают со скоростью,
устраиваемая полоса соприкасается с разогретым краем ранее уложенной полосы, который подвергается уплотнению одновременно с новой [67].
Разогретый край ранее уложенной полосы позволяет обеспечить температуру, требуемую для уплотнения. В этом случае можно выполнить качественное уплотнение продольного сопряжения. Такое
144
уплотнение исключает одну из возможных причин образования продольной технологической трещины в процессе эксплуатации покрытия. По мнению специалистов, причиной возникновения технологической трещины являются недостаточная плотность и избыточная пористость асфальтобетона в зоне швов сопряжения [68]. Д.В. Барковский [68, с. 2], цитируя исследования специалистов США [69, 70], указывает, что в зоне швов сопряжения коэффициент уплотнения асфальтобетона практ чески всегда ниже, чем в основном покрытии. Причем м н мальная плотность асфальтобетона имеет место непо-
средственно в шве |
на неограниченной кромке. В работе [68] приве- |
дены разл чные конструкции продольного стыка смежных полос и |
|
С |
|
технолог его устройства, применяемые в РФ и США для повыше- |
|
его качества |
предотвращения возникновения технологической |
трещины. К так м конструкциям и технологиям относят: обрезку |
|
ния |
|
бА |
кромки отрезным д ском, подогрев кромки инфракрасным разогревателем, конструкц ю формовочный клин (Мичиганский клин), уплотнение кромки краевым уплотнителем, стыковочные ленты, а также технолог уплотнен я стыка. Технологии уплотнения стыка подразделяют на три спосо а: уплотнение с перекрытием смежной полосы, уплотнение с горячей стороны с отступом от стыка и уплотнение с холодной стороны с отступом от стыка.
Нами показано, что применение линеек разогревателей и технологий уплотнения продольного сопряженияДполучило распространение в РФ, требования к этим технологическим процессом приведены в пособии [36] и ТР 103–07 [67]. Требования к технологии уплотнения сопряжения регламентированы СП 78.13330–2012 [7, п. 12.3.8]. Согласно этим требованиям вальцы катка в процессе уплотнения первой смежной полосы катка не должны приближатьсяИболее чем на 10 см к кромке сопряжения [7]. Уплотнение второй полосы начинают по продольному сопряжению [7]. После уплотнения сопряжение полос должно быть ровным и плотным. Сравнивая технологию, регламентируемую СП 78.13330–2012 [7, п. 12.3.8], с технологиями, применяемыми в США и рекомендуемыми NCAT (Национальный центр технологий асфальтобетона США) отметим, что она соответствует способу уплотнения с перекрытием смежной полосы. Согласно этой технологии первый проход катка выполняется по второй (свежеуложенной полосе), но с перекрытием сопряжения на величины 15 см.
Другой рекомендуемой технологией уплотнения продольного сопряжения является технология уплотнения с горячей стороны с от-
145

ступом от сопряжения. В этом случае первый проход делается по горячей полосе с отступом от сопряжения на 15 см. Эта технология эф-
фективна при уплотнении слоев, толщина которых превышает 10 см. |
|
В остальных случаях рекомендуется уплотнение с перекрытием по- |
|
лос. Иллюстрация этих технологий приведена на рис. 76. |
|
С |
|
уплотнения |
|
бА |
|
Р с. 76. Спосо ы |
продольного стыка [68, рис 25 и 26]: |
а – с перекрыт ем смежной полосы; – с горячей стороны с отступом от края
Технология уплотнения с холодной стороны признана неэффективной, и она не рекомендуется для практического использования.
Уплотнение края полосы при помощи краевого уплотнителя также нашло применение в РФ. В этом случае каток оборудуют коническим стальным вальцом диаметромДу основания 75 мм, который крепят через систему гидрорегулировки на стойке ведущего вальца на расстоянии 15 см от него.
Способ устройства продольного сопряжения полос с обрезкой кромки отрезным диском состоит в обрезке неуплотненной кромки на величину 38–50 мм [68]. Обрезку выполняютИпри помощи диска, установленного на катке или автогрейдере. Недостатком технологии является большое количество асфальтового лома. Компенсация этого недостатка выполняется тем, что обрезанный асфальтобетонный лом вывозят на базу для последующего применения с реализаций технологий, позволяющих восстанавливать свойства материала и использовать повторно. В РФ данная технология нашла применение, причем на практике отрезным диском устраивают перпендикулярные поперечные сопряжения. В этом случае каток с отрезным диском ставят перпендикулярно оси проезжей части и срезают лишний асфальтобетон. Клиновой поперечный скат убирают в несколько проходов катка с отрезным диском. Тогда первый проход выполняют и на дальнем
146
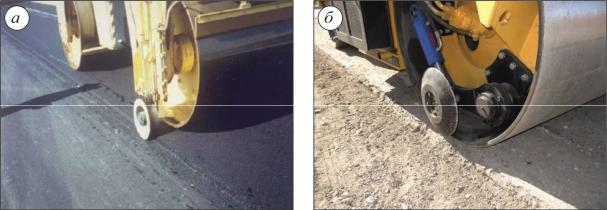
расстоянии от будущего поперечного стыка, а каждый последующий проход – с приближением к устраиваемому поперечному стыку.
Иллюстрации уплотнителя и обрезчика кромки приведены на рис. 77.
С |
|
кромки |
|
Рис. 77. Пр спосо лен я для устройства продольного сопряжения полос |
|
покрыт я: а – уплотнитель кромки; б – обрезчик кромки |
|
В работе [68] соо щается, что битумно-каучуковые стыковочные |
|
США |
|
ленты нашли широкое применение в |
, странах Западной Европы |
и ближнегобзару ежья. Технология применения ленты проста, она раскладывается вдоль кромки, после чего выполняют стандартные операции по укладке смеси и ее уплотнению во второй смежной полосе.
нии до толщины ранее устроеннойДполосы.
При любом способе устройства сопряжения вертикальный край ранее уложенного асфальтобетона смазывается битумной эмульсией
еще до начала укладки новой полосы. При устройстве новой полосы смесь распределяется слоем с учетом его уменьшения при уплотне-
При окончании укладки смеси слой ее клинообразно утончается. В результате формируется клин, по которому идет движение транспорта до возобновления работ по укладке. При возобновлении этих работ клинообразная часть слоя обрубается вертикально по рейке или шнуру в направлении, перпендикулярном оси дороги.
И
Толщина покрытия в местах обрубки должна быть не менее проектной. Для образования качественного поперечного стыка в месте обрубки слоя вертикальная грань ранее уложенного слоя смазывается битумной эмульсией и на это место устанавливается плита асфальтоукладчика. Необходимо, чтобы перед началом укладки плита была
147
прогрета обогревающими устройствами или горячей асфальтобетонной смесью.
Другим способом устройства поперечного шва является укладка в поперечном направлении деревянного бруса толщиной, равной толщине уплотненного слоя асфальтобетона. Для смягчения толчков от движущегося транспорта перед брусом укладывается клинообразный упор из асфальтобетонной смеси.
Устройство поперечных и продольных стыков является начальным этапом укладки новой горячей полосы. Этим операциям предшествует уплотнен е смеси после укладки. Уплотнение смеси выполня-
ют, |
соблюдая |
определенные |
правила, |
регламентируемые |
С |
|
|
|
|
П 78.13330.2012 [7], посо ием [36], рекомендациями [37, 38, 39, 40, |
||||
41, 64, 67, 71]. Нео |
следования этим правилам пояснена в |
ходимость учебной л бАтературе [42, 43, 63, 72].
Асфальтобетонные смеси уплотняют сразу же после укладки. Уплотнен е горяч х смесей начинают при максимально возможных температурах, при которых от действия уплотнителя не образуется сдвиговых деформац й [36, п. 5.22]. Соблюдение этого требования позволяет выполнять уплотнение с наиболее эффективным использованием времени, в течение которого смесь остывает до предельной температуры. На о еспечение такого рационального уплотнения направлены требования СП 78.13330.2012, согласно которым необхо-
торможение и реверсирование [7,Дп. 12.3.9].
димо обеспечить минимальные расстояния между асфальтоукладчиком и дорожными катками [7, п. 12.3.9]. Во избежание образования дефектов на свежеуложенной поверхности катки должны двигаться
непрерывно, не останавливаясь на неуплотненной поверхности
[7, п. 12.3.9]. При движении катков необходимо исключить резкое И
Регламентируемая пособием [36] температура уплотнения горячих асфальтобетонных смесей при содержании в них щебня 40% и более составляет 120 – 160 °С, а при содержании щебня менее 40% и песчаных смесей их уплотнение начинают при температуре 20-30 °С
ниже [36, п. 5.23]. Применение в составе горячих смесей добавок ПАВ и активированного минерального порошка позволяет уменьшить температуру начала уплотнения на 10–20 °С [36, п. 5.23]. При уплотнении холодных смесей их температура должна быть не ниже 5 °С [36, п. 5.23].
В рекомендациях [64, табл. 5.5] приведены начальные и конечные (критические) температуры уплотнения горячих плотных асфальтобе-
148
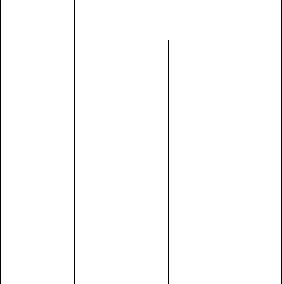
тонов, а также указан рациональный температурный режим для всех этапов уплотнения. Эти рекомендации приведены в табл. 52.
|
|
|
|
|
|
Таблица 52 |
|
|
Рекомендуемые температуры и режим уплотнения |
||||
|
|
|
горячих плотных асфальтобетонов |
|
||
|
|
Рекомендуемая темпера- |
Рациональный температурный режим |
|||
|
Тип |
тура уплотнения, °С |
уплотнения слоя на различных этапах, °С |
|||
|
смеси |
начальная |
критическая |
предвари- |
промежу- |
заключи- |
|
|
тельный |
точный |
тельный |
||
|
|
|
|
|||
|
А |
140–160 |
75–80 |
От 140–145 |
От 120–125 |
От 95–100 |
|
до 120–125 |
до 95–100 |
до 75–80 |
|||
|
|
|
|
|||
|
Б |
120–140 |
70–75 |
От 125–130 |
От 105–110 |
От 85–90 |
|
до 105–110 |
до 85–90 |
до 70–75 |
|||
С |
|
|||||
|
В |
110–130 |
60–65 |
От 115–120 |
От 100–105 |
От 80–85 |
|
до 100–105 |
до 80–85 |
до 60–65 |
|||
|
|
|
|
|||
|
|
|
бА |
От 105–110 |
От 85–90 |
|
|
Г |
120–140 |
70–75 |
От 125–130 |
||
|
и |
до 105–110 |
до 80–90 |
до 70–75 |
||
|
|
|
60–65 |
От 105–110 |
От 85–90 |
От 70–75 |
|
Д |
100–120 |
до 85–90 |
до 70–75 |
до 60–65 |
При температуре смеси выше начальной катки «тонут», образуя волны и трещины, а при температуре ниже критической уплотнение перестает быть эффективным [64].
В зависимости от гранулометрического состава и видов материалов асфальтобетонные смеси по способностиДк уплотнению и подразделяют на жесткие и мягкие [72]. За рубежом по способности к уплотнению выделяют три типа смесей: жесткие, нормальные и пластичные (мягкие) [62]. В состав мягких смесей входит природный песок, а в ряде случаев природный окатанный каменный материал, они содержат небольшое количество минеральногоИпорошка и битум низкой вязкости [72]. Такие смеси наиболее пластичны и требуют осторожного уплотнения, чтобы избежать сдвига и образования трещин на поверхности [72]. Жесткие смеси, наоборот, в своем составе содержат дробленый песок, большое количество крупного щебня и минерального порошка, смешанного с вязким битумом [72]. Жесткие смеси оказывают значительное сопротивление уплотнению и требуют больших энергозатрат, чтобы достичь установленной степени уплотнения.
Для уплотнения асфальтобетонной смеси применяют вибрационные катки, статические катки гладковальцовые и на пневматических шинах, а также комбинированные. Выбор катков и режим их работы
149
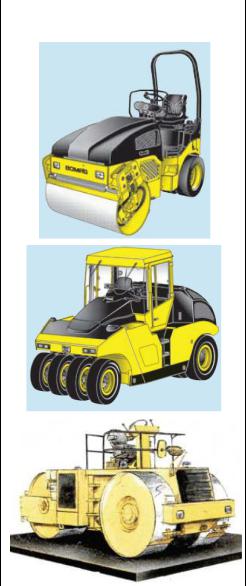
при уплотнении определяет степень уплотнения асфальтобетонной смеси, которая должна соответствовать требованиям [7]. Указанные нами катки применяются в нормальных условиях, когда уплотняется достаточная площадь. В стесненных условиях в дополнение к тяжелому оборудованию рекомендуется использовать виброплиты и мини-катки, к которым можно отнести катки с ручным режимом управления [72].
В табл. 53 пр ведены средства механизации, применяемые для уплотнен я асфальтобетонных смесей в нормальных и стесненных условиях.
Средства механ |
|
|
|
Таблица 53 |
|||||
зации уплотнения асфальтобетонных смесей [62, 72] |
|||||||||
|
Уплотн |
|
В д уплотнителя |
Общая характеристика |
|
||||
|
1 |
|
2 |
|
|
3 |
|
|
|
|
тели |
Легкие тандемные |
|
катки с |
|
||||
|
рамой на шарнирном соеди- |
|
|||||||
|
Легк е |
|
|
нении выпускаются |
|
массой |
|
||
|
|
|
от 1,3 до 4.2 т, рабочей ши- |
|
|||||
|
тандемные |
|
|
||||||
|
|
риной от 80 до 138 см. Оба |
|
||||||
|
катки |
|
|
|
|||||
|
|
|
вальца катка оснащены гид- |
|
|||||
|
|
|
|
|
|||||
|
|
|
|
ростатическим приводом и |
|
||||
|
|
|
|
вибросистемой |
|
|
|
||
|
|
|
|
|
|
||||
|
|
бА |
Пневмоколесные катки име- |
||||||
|
|
ют управляемую качающую- |
|
||||||
|
|
ся переднюю ось и непод- |
|
||||||
|
|
|
|
|
|||||
|
Пневмоколес- |
|
вижный задний мост. За счет |
|
|||||
|
|
применения |
балласта мас- |
|
|||||
|
ные катки |
|
|
||||||
|
|
са катка может быть |
|
увели- |
|
||||
|
|
|
|
|
|
||||
|
|
|
|
чена до 24–27 т. Уплотнение |
|
||||
|
|
|
Д |
|
|
||||
|
|
|
|
происходит за счет собст- |
|
||||
|
|
|
|
венного веса катка |
|
|
|
||
|
|
|
|
Трехвальцовые катки |
|
имеют |
|
||
|
Современные |
|
три больших ведущих вальца |
|
|||||
|
|
и |
совмещенное |
рулевое |
|
||||
|
статические |
|
|
||||||
|
|
И |
|
||||||
|
трехвальцовые |
|
управление. |
Масса |
|
катков |
|
||
|
|
8–15 |
т. Балластировкой во- |
|
|||||
|
катки |
|
|
|
|||||
|
|
|
дой можно изменять уплот- |
|
|||||
|
|
|
|
|
|||||
|
|
|
|
няющее воздействие |
|
|
|
||
|
|
|
|
|
|
|
|
|
|
150
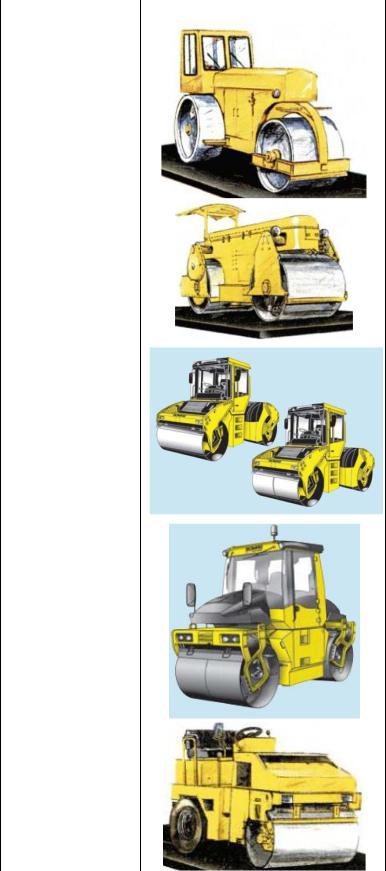
Продолжение табл. 53
|
1 |
|
2 |
|
|
|
3 |
|
|
|
|
|
|
|
|
В отличие |
от |
современных |
|
||
|
|
|
|
|
моделей такие катки имеют |
|
||||
|
Обычные стати- |
|
|
два больших ведущих вальца |
|
|||||
|
ческие трех- |
|
|
и рулевой |
валец меньшего |
|
||||
|
вальцовые катки |
|
|
размера. |
Вид |
уплотнения |
|
|||
|
|
|
|
|
статический за счет собст- |
|
||||
|
|
|
|
|
венного веса катка |
|
|
|||
|
|
|
|
|
|
|||||
|
катки |
|
Масса катка 7–14т при рабо- |
|
||||||
С |
|
Статические катки-тандемы |
|
|||||||
|
имеют один ведущий валец и |
|
||||||||
|
тат ческ |
е |
|
жесткую раму. Масса катков |
|
|||||
|
|
6-12 т. Балластировкой водой |
|
|||||||
|
тандемы |
|
|
|||||||
|
|
можно изменять уплотняю- |
|
|||||||
|
|
|
|
|
|
|||||
|
|
|
|
|
щее воздействие. |
|
|
|||
|
|
|
|
|
|
|
||||
|
|
|
|
|
чей ширине 1,50, 2,00 и |
|
||||
|
Тандемные кат- |
|
2,13 м. Вибрация передается |
|
||||||
|
|
либо |
на оба |
вальца, либо |
|
|||||
|
ки с шарнирно- |
|
|
|||||||
|
|
только на передний или зад- |
|
|||||||
|
сочлененной |
|
|
|||||||
|
рамой |
бА |
ний. |
Они |
всегда |
следуют |
|
|||
|
один за другим, даже при |
|
||||||||
|
|
|
||||||||
|
|
выполнении поворотов (вле- |
|
|||||||
|
|
во/вправо) |
|
|
|
|
||||
|
|
|
|
Тандемные катки с управ- |
|
|||||
|
|
|
|
|
ляемыми |
вальцами |
имеют |
|
||
|
|
|
|
|
массу от 7 до 10 т, рабочую |
|
||||
|
Тандемные кат- |
|
ширину 1,50 и 1,68 м. Такие |
|
||||||
|
|
катки оснащены гидростати- |
|
|||||||
|
ки с управляе- |
Дческим приводом вальцов и |
|
|||||||
|
мыми вальцами |
|
вибросистемы. Вибрация пе- |
|
||||||
|
|
|
|
|
редается либо на оба вальца, |
|
||||
|
|
|
|
|
либо только на передний или |
|
||||
|
|
|
|
|
задний |
|
|
|
|
|
|
|
|
|
|
И |
|
||||
|
|
|
|
|
Комбинированные катки |
|||||
|
|
|
|
|
имеют один вибрационный |
|
||||
|
Комбинирован- |
|
валец и заднюю ось с тремя |
|
||||||
|
|
или четырьмя пневматиче- |
|
|||||||
|
ные катки |
|
|
|||||||
|
|
скими шинами. Масса катков |
|
|||||||
|
|
|
|
|
|
|||||
|
|
|
|
|
4–15 т. |
|
|
|
|
|
|
|
|
|
|
|
|
|
|
|
|
151
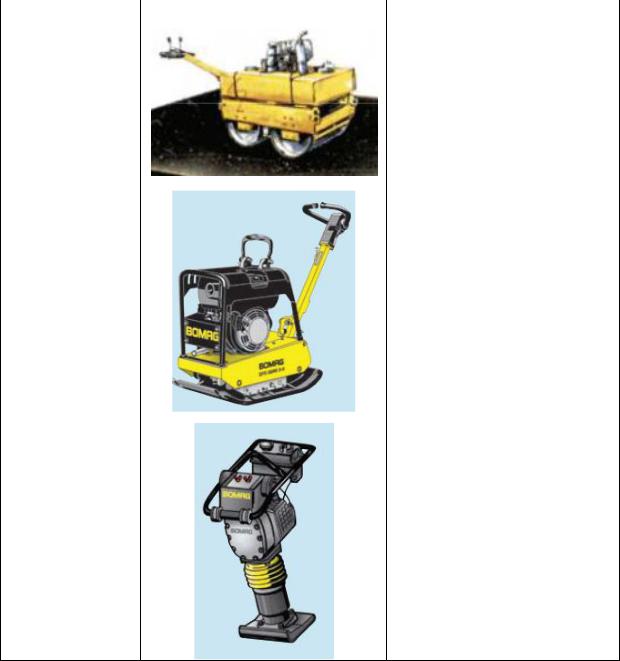
|
|
|
Окончание табл. 53 |
|
1 |
2 |
3 |
|
|
|
Ручные катки имеют два |
|
|
|
вибрационных вальца на же- |
|
|
|
сткой раме. Для удобства |
|
Двухвальцовые |
|
оператора предусмотрена |
|
ручные катки |
|
виброизолированная руко- |
|
|
|
ять. Масса катков 400– |
|
|
|
1000 кг. Рабочая ширина – |
|
|
|
от 60 до 75 см. |
С |
|
Масса виброплиты 50–150кг, |
|
|
а рабочая ширина – от 45 до |
||
|
60 см. Они оснащаются бен- |
||
|
зиновыми или дизельными |
||
|
|
|
|
|
|
|
двигателями. Вибратор на- |
|
ты |
|
правленного действия при- |
|
|
водится в действие через |
|
|
Вибропл |
||
|
клиновой ремень и центро- |
||
|
бежную муфту. Управление |
||
|
|
|
|
|
|
|
движением происходит за |
|
|
|
счет регулировки направле- |
|
|
|
ния действия вибратора |
|
|
|
Вибротрамбовки применяют |
|
|
|
в ограниченных пространст- |
|
|
|
вах на территориях, приле- |
|
|
|
гающих к стенам, заборам, |
|
|
|
коммуникационным элемен- |
|
бАтам (например, люки) и т.д. |
||
|
Трамбовки |
|
Масса не превышает |
|
|
|
|
|
|
|
60–80 кг. Кривошипный |
|
|
|
привод передает быстрые |
|
|
|
вертикальные возвратно- |
|
|
|
поступательные движения к |
|
|
|
Д |
|
|
|
башмаку трамбовки |
Статическое уплотнение происходит вследствиеИвоздействия нагрузки от веса катка. Такой вид уплотнения производят статические гладковальцовые катки (трехвальцовые и тандемные) и катки на пневматических шинах [62]. Гладковальцовые катки уплотняют смесь, передавая на укатываемый слой линейную нагрузку. Пневмоколесные катки выполняют уплотнение за счет нагрузки от колес и давления воздуха в них. Статические катки, по сравнению с вибрационными, дают довольно незначительное уплотнение. Поэтому статические гладковальцовые и пневматические катки рекомендуется при-
152
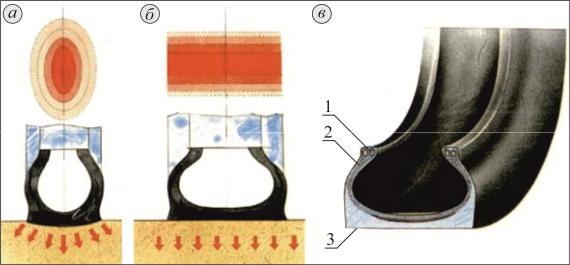
менять только после предварительного уплотнения асфальтобетонной смеси укладчиком [62].
Катки на пневматических шинах могут иметь обычные или широкопрофильные шины [72]. Авторы в работе [72] сообщают, что обычные шины более многофункциональны, их применяют для уп- Слотнения грунтов и асфальтобетонных смесей, а давление воздуха в
них можно регулировать от 0,3 до 0,9 МПа. Широкопрофильные шины пр меняют при строго фиксированном давлении воздуха 0,4 МПа. Широкопроф льные шины целесообразно применять при оконча- ристельной укатке, они деальны для затирания и отделки поверхности. Иллюстрац я эт х двух типов пневматических шин приведена на
. 78 [72].
бА Рис. 78. Типы шин, применяемыеДна пневматических катках [72]:
а – обычная шина; б – широкопрофильная шина; в – конструкция шины; 1 – армированная кромка; 2 – каркас; контактная поверхность
При уплотнении обычными шинами частицыИматериала перемещаются вниз и в стороны (рис. 78, а). При уплотнении широкопрофильной шиной горизонтальные смещения частиц имеют существенно меньшую величину.
В процессе укатки материал уплотняется и изменяется контактная площадь. С каждым проходом вертикальное смещение поверхности слоя (осадка) уменьшается [72]. На практике измерить контактное давление по подошве шины невозможно хотя бы потому, что этот процесс займет время, которое необходимо для уплотнения горячей смеси при рациональных температурах (см. табл. 52). Поэтому оператор пневматического катка давление воздуха в шинах оценивает визу-
153
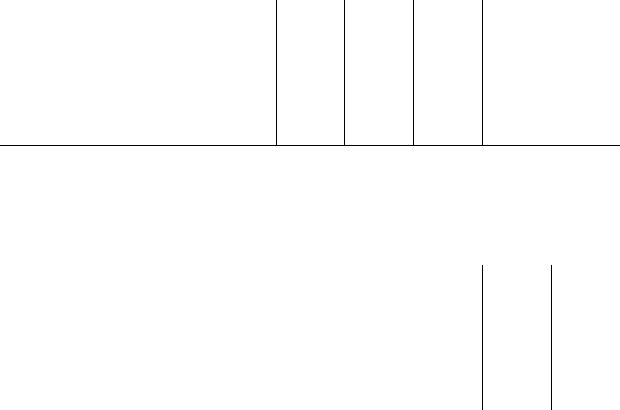
ально. Например, если оператор видит, что шины тонут в материале, он может использовать систему регулировки давления воздуха в шине, обычно известную под названием "Воздух наружу" или "Воздух навыпуск", для уменьшения давления в шинах [72]. Уменьшение давления воздуха в шине приводит к увеличению площади контактной поверхности, а значит, к уменьшению контактных давлений, определяемых отношение нагрузки от колеса к площади отпечатка шины. И наоборот, увел чен е давления воздуха приводит к повышению давления по подошве [72]. Централизованная система регулировки воздушного давлен я позволяет его поддерживать постоянным на каж-
|
дом пер оде укатки [72]. |
|
|
|
|
|
|
|
|||||
С |
|
|
|
|
|
|
|
|
|
||||
|
Для определен я контактной площади шины и контактного дав- |
||||||||||||
|
удобно |
спользовать специальные таблицы и графики. |
Такие |
||||||||||
|
таблицы граф ки содержатся в работе [72]. Данные работы [72] |
||||||||||||
|
приведены в |
. 54 |
55. |
|
|
|
|
|
|
|
|||
|
ления |
|
шине, МПа |
Таблица 54 |
|||||||||
|
|
табл |
|
|
|
|
|||||||
|
|
Зав с мость контактной площади отпечатка от нагрузки |
|
||||||||||
|
на колесо давления воздуха в шине пневматического катка |
||||||||||||
|
Нагрузка на колеса |
|
Контактная площадь, см2, при давлении воздуха в |
||||||||||
|
|
|
|
|
|
|
|
|
|
||||
|
|
|
|
|
|
|
|
|
|
|
|
|
|
|
Масса, кг |
|
|
Вес, Н |
0,25 |
0,33 |
0,49 |
0,63 |
0,74 |
|
|
0,85 |
|
|
1220 |
|
|
11968 |
|
361 |
322 |
246 |
219 |
212 |
|
|
199 |
|
1360 |
|
|
13342 |
|
438 |
387 |
309 |
270 |
251 |
|
|
238 |
|
1810 |
|
|
17756 |
|
548 |
503 |
406 |
341 |
309 |
|
|
283 |
|
2270 |
|
|
22269 |
|
670 |
586 |
483 |
406 |
374 |
|
|
348 |
|
|
|
|
|
|
А |
|
|
|
|
|
||
|
2730 |
|
|
26781 |
|
761 |
664 |
554 |
470 |
438 |
|
|
406 |
|
3000 |
|
|
29430 |
|
– |
715 |
593 |
541 |
477 |
|
|
438 |
|
|
|
|
|
|
|
Д |
|
|
|
|||
|
|
|
|
|
|
|
|
|
Таблица 55
Зависимость контактного давления от нагрузки на колесо и давления воздуха в шине пневматического катка
Нагрузка на колеса |
Контактное давление, МПа, при давлении воздуха в |
|
||||||
|
|
шине, МПа |
|
|
|
|||
|
|
|
|
|
|
|
||
Масса, кг |
Вес, Н |
0,25 |
0,33 |
0,49 |
0,63 |
0,74 |
0,85 |
|
1220 |
11968 |
0,30 |
0,33 |
0,40 |
0,48 |
0,50 |
0,52 |
|
|
|
|
|
|
И |
|
||
1360 |
13342 |
0,31 |
0,35 |
0,43 |
0,50 0,54 0,56 |
|||
1810 |
17756 |
0,33 |
0,36 |
0,44 |
0,52 |
0,58 |
0,63 |
|
2270 |
22269 |
0,33 |
0,38 |
0,47 |
0,55 |
0,60 |
0,65 |
|
2730 |
26781 |
0,35 |
0,40 |
0,49 |
0,57 |
0,61 |
0,66 |
|
3000 |
29430 |
– |
0,42 |
0,50 |
0,55 |
0,63 |
0,67 |
|
154
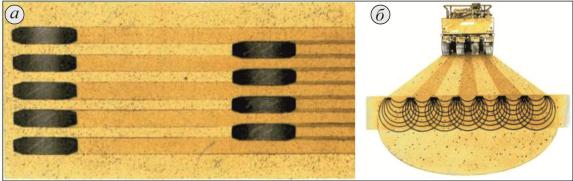
Пневматические шины, установленные на разных вальцах, перекрывают проходы друг друга. При нормальном давлении такое перекрытие должно составлять 30–50 мм [72]. Важно получить равномерное контактное давление по всей уплотняющей площади. Это позволяет обеспечить отсутствие следа на поверхности, что особо важно
Спри уплотнении асфальтобетонных слоев [72]. Нагрузка от каждого колеса формирует в уплотняемом материале луковицу напряжений. Так как проходы перекрываются, то по принципу суперпозиции силы, напряжен я от каждой нагрузки можно суммировать. В этом случае вицперекрыт е луков ц напряжений приводит к одной большой луковице [72]. На р с. 79 показаны перекрытия следов прохода катка и луко-
напряжен й.
Рис. 79.бАСхемы уплотнения катком на пневматических катках [72]:
а – перекрытие проходов колесами на разных вальцах; б – перекрытие луковиц вертикальных напряженийДот колес на разных вальцах
Статические гладковальцовые катки бывают двухвальцовые и трехвальцовые (см. табл. 53). Традиционные трехвальцовые катки имеют два ведущих вальца и один поворотный, меньшего диаметра, а также жесткую раму. Современные катки имеетИтри ведущих вальца одинакового диаметра [62, 72]. Величина уплотняющего усилия гладковальцового катка зависит от линейной нагрузки. Линейная нагрузка трехвальцовых катков массой 10–15 т составляет 50–80 кгс/см или 49,1–78,5 кН/м. При уплотнении асфальтобетонных смесей нагрузка должна превышать указанные нижние пределы [72]. Особенностью конструкции традиционных трехвальцовых катков является то, что нагрузка от переднего вальца на 30% меньше, чем от задних вальцов. Поэтому для однородного уплотнения смеси задние вальцы должны проходить всю поверхность [72]. На практике такое требование выдержать сложно. У современных катков с одинаковыми по диаметру вальцами и шарнирным управлением нагрузка более менее одинако-
155
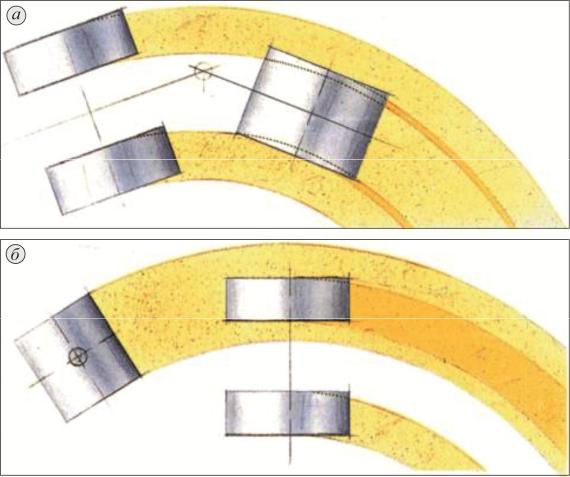
вая [72]. Поэтому современные трехвальцовые катки обеспечивают равномерное уплотнение поверхности в пределах прохода. За два параллельных прохода каток с учетом перекрытия следа покрывает полосу шириной 3,7, а рабочая ширина составляет 2 м. Линейная нагрузка статического тандемного катка с двумя вальцами меньше, чем у трехвальцового катка. Диаметр вальца тандемного катка составляет 1,2–1,5 м, а рабочая ширина – 1,1–1,4 м. Нагрузка на передний валец составляет 40%, а на задний 60% [72]. В качестве балласта наиболее
удобно |
спользовать воду, а другие типы пригруза (металлические |
|
чушки, лом, бетонные блоки) неудобны, их трудно заменить [72]. Со- |
||
временные катки оборудованы шарнирным сочленением, что позво- |
||
С |
перекрытие проходов катка на поворотах |
|
ляет обеспеч вать |
||
( . 80, а). Трад ц онные трехвальцовые катки сочленены жесткой |
||
рамой |
вынуждены на поворотах пропускать целые полосы неуплот- |
|
ненного матер ала (р |
с. 80, ). |
|
рис |
||
|
бА |
|
|
|
Д |
|
|
И |
Рис. 80. Схемы перекрытия проходов вальцов на повороте [72]:
а– перекрытие проходов вальцов современного катка с шарнирным сочленением;
б– перекрытие проходов вальцов традиционного катка с жесткой рамой
156
Авторы работы [72] сообщают, что диаметр вальца влияет на величину угла въезда на уплотняемый материал и сопротивление качению. Причем чем больше диаметр вальца, тем меньше угл въезда и сопротивление качению. Отсюда следует рекомендация, которую нужно соблюдать при уплотнении асфальтобетонных смесей. Суть рекомендации состоит в том, что при применении катков с линейной нагрузкой более 50 кгс/см валец должен иметь диаметр 1500 мм и более [72]. Не менее важным фактором для уплотнения является дуга
контакта, ее дл на определяет площадь контакта вальца и уплотняе- |
|
мого матер ала. Особую важность длина дуги контакта приобретает |
|
при уплотнен мягк х смесей, склонных к выдавливанию из-под |
|
С |
|
вальца. Малая площадь контакта приводит к высоким давлениям, вы- |
|
зывающ м сдв г асфальто етонной смеси и образование трещин. По- |
|
этому |
уплотнен пластичных асфальтобетонных смесей наибо- |
при лее целесообразнобАпр менять катки с большими диаметрами вальцов.
Авторы пособ я [72] п шут: «…, чем больше диаметр вальца и контактная площадь, тем лучше каток подходит для работы на подвижных смесях».
Режимы уплотнения определяют на основании пробной укладки и уплотнения асфальто етонной смеси укаткой, а ориентировочные значения параметров уплотнения приведены в нормативной и справочной литературе.
Виброуплотнение является наиболееДэффективным методом уплотнения асфальтобетонных смесей. По данным работы [62], жесткие асфальтобетонные смеси нельзя уплотнить до требуемой степени без применения вибрационных катков. Поэтому вибрационные катки получили широкое применение в практике строительства асфальтобетонных покрытий. Вибрационным каткам, поИсравнению с катками статического действия, требуется меньшее число проходов по одному следу, что экономит время и повышает производительность укатки. Вибрация уменьшает трение внутри материала, а динамическая нагрузка и вес катка уплотняют материал. Отсюда следует, что основными показателями уплотняющей способности вибрационных катков являются масса и характеристика вибрации, к которым относят частоту и амплитуду [62].
При уплотнении слоев большой толщины целесообразно применять тяжелые тандемные вибрационные катки, которые способны работать с различной частотой и амплитудой. Скорость вибрационных катков при уплотнении составляет 3 – 6 км/ч. Для качественного уп-
157
лотнения необходимо установить требуемое число проходов. Отметим, что слишком большое число проходов может привести к разрыхлению материала. То есть ошибка в определении числа проходов даст диаметрально противоположный результат вместо ожидаемого качественного уплотнения [62].
СВ брац онные характеристики частоты и являются параметрами колебательного процесса. Частота определяется отношением числа колебан й (ударов вальца о поверхность) к единице времени. Измеря-
Линейная нагрузка от вальца вибрационного катка обуславливается массой вальцового модуля, которая определяется массой вальцо-
вого агрегата частью массы рамы. Статическая линейная нагрузка
вычисляется отношен ем массы к ширине вальца.
ется в герцах (Гц =1/с, под единицей понимают одно колебание). Ампредставляет со ой максимальное смещение вальца от сред-
него положен я [72] о ычно измеряется в миллиметрах.
Для макс мального уплотняющего эффекта частота вибрирова- |
|
плитуда |
|
ния должна |
в пределах 25 – 40 Гц, что соответствует 1500 – |
2400 колебан й/м нуту [72]. Если частоту вибрации изменять в этом |
|
диапазоне, то на величину усилия и уплотняющую способность осо- |
|
бого влияния не |
удет. Для повышения эффективности уплотнения в |
быть |
|
диапазоне рекомендуемых частот необходимо изменять амплитуду, |
|
она на таких частотах существенно влияет на степень уплотнения. |
|
|
А |
Для уплотнения крупнообломочных материалов и глинистых грунтов |
|
используют большие амплитуды, варьирующиеся в пределах 1,5 – |
|
2,0 мм. Для уплотнения слоев из асфальтобетонных смесей применя- |
ют амплитуды 0,4 – 0,8 мм, а рабочая частота находится в диапазоне
33 – 50 Гц [72]. |
И |
Амплитуда важна при уплотнении разных смесей пластичных и |
|
жестких, а также асфальтобетонныхДслоев малой и большой толщины. |
|
На мягких смесях и тонких слоях работают с малыми амплитудами |
|
[72]. В этом случае именно малые амплитуды и рекомендуемый диа- |
|
пазон частот дают наилучший результат, не вызывая разрушения сла- |
бых агрегатных смесей. Жесткие смеси и слои большой толщины требуют использования высоких амплитуд. Поэтому возможность изменения амплитуды при уплотнении асфальтобетонных слоев является преимуществом вибрационных катков, имеющих такую опцию. Возможность изменения амплитуды является преимуществом при уплотнении толстых слоев оснований из зернистых материалов. Уплотнение таких слоев начинают при больших амплитудах, но в процессе
158
уплотнения и увеличения плотности валец, как правило, начинает отскакивать от уплотняемой поверхности [72]. Увеличение числа проходов при той же амплитуде эффекта уплотнения не дает. В этом случае эффективно уменьшить амплитуду и продолжать уплотнение.
Поэтому возможность использовать два значения амплитуды позволяет изменять уплотняющее усилие. На асфальтобетоне два значения амплитуды могут быть использованы, чтобы приспособить каток к разным потребностям уплотнения, обусловленным типом и состоя-
нием смесей |
зменен ями толщин укладки [72]. |
|
овременные катки снабжаются системой автоматического кон- |
||
троля в брац |
, которая выключает вибрацию на скоростях ниже ус- |
|
С |
|
|
тановленного предела. Когда каток остановлен или меняет направле- |
||
дв жен я |
в рац я прекращена. Расстояние |
между ударами |
вальца об уплотняемую поверхность называют ударным пространст- |
||
вом, его вел ч на зав сит от скорости катка. На уплотняемых ас- |
||
фальтобетонных слоях малое ударное пространство |
предотвращает |
|
ние |
|
|
образован е неровностей [72]. Ра очая скорость вибрационного катка |
||
при уплотнен |
асфальто етонной смеси должна быть в пределах от |
|
3 до 6 км/час [72]. Наличие у катка двух вибрационных вальцов по- |
||
вышает его производительность (примерно на 50%) по сравнению с |
||
катком, имеющим один ви рационный и один статический валец. Это |
||
объясняется тем, что тандемному катку с двумя вибрирующими валь- |
||
цами требуется меньше проходов для уплотнения смеси до требуемой |
||
плотности. |
|
|
бА |
|
|
При выборе катка для уплотнения асфальтобетонной смеси учи- |
||
тывают ширину вальца. Известно, что ширина вальца определяет ве- |
||
личину укатываемой площади. Отсюда следует, что чем шире валец, |
||
тем больше укатываемая им площадь, а значит, и выше производи- |
||
тельность. К сожалению, при уплотненииДасфальтобетонных слоев |
||
этот тезис не работает. Дело в том, что уплотняя асфальтобетонную |
||
полосу, разложенную укладчиком, нужно исходить из того, что эту |
полосу необходимо перекрывать за минимальноеИчисло параллельных полос (укатанных полос) [72]. Авторы пособия [72] приводят такой пример. Пусть ширина укладки составляет 3,5–3,9 м. Каток с шириной вальца 1450 мм перекроет разложенную укладчиком полосу с необходимым перекрытием полос уплотнения тремя параллельными проходами. Катку с шириной вальца 1600 мм для перекрытия такой полосы тоже потребуется три прохода по ширине, но ширина перекрытия полос уплотнения будет существенно больше требуемого пе-
159
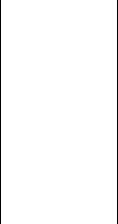
рекрытия. Поэтому в этом случае целесообразно принять каток с шириной вальца 1450 мм, а от применения катка с вальцом шириной 1600 мм в данном случае лучше отказаться.
Рассмотрев достоинства и недостатки катков различного типа, приведем сведения из рекомендаций и нормативных документов об уплотняющей способности катков и рациональной комплектации
Сотметим, что они подразделяются по массе: на легкие – 5–6 т; средние – до 8 т тяжелые – более 10 т [64]. Для каждого типа катков, выполняющего уплотнен е асфальтобетонной смеси на определенной стадии установлены рекомендуемые контактные давления [64, табл. 5.6]. Ста-
звеньев.
Рассматр вая область применения катков статического действия,
уплотнен я отделены значениями коэффициентов уплотнения, которых необход мо дост чь в конце каждой стадии. Данные рекоменда-
ций [64, табл. 5.6] пр ведены та л. 56. |
|
|
|
||
дии |
|
|
Таблица 56 |
||
Рекомендуемые контактные давления для различных этапов |
|||||
уплотнения |
|
смеси [64] |
|
|
|
|
Границы эта- |
|
Значения контактных дав- |
|
|
Тип катка |
Коэффициент |
лений катков, МПа, для ти- |
|
||
|
пов уплотне- |
|
|
|
|
(этап уплотнения) |
асфальтобетонной |
пов смесей |
|
||
ния |
уплотнения |
|
|||
|
|
А |
В |
|
|
|
|
|
|
||
Легкий |
Начало |
0,70 |
0,50–0,55 |
0,40–0,45 |
|
(предварительный) |
Конец |
0,85 |
1,20–1,25 |
1,17–1,30 |
|
Средний |
Начало |
0,85 |
1,20–1,25 |
1,17–1,30 |
|
А |
|
||||
(промежуточный) |
Конец |
0,92 |
1,65–1,80 |
1,50–1,70 |
|
Тяжелый |
Начало |
0,92 |
1,65–1,80 |
1,50–1,70 |
|
(заключительный) |
Конец |
1,0 |
2,80–3,10 |
2,60–2,90 |
|
|
|
Д |
|
|
|
Из анализа данных табл. 56 следует, что при укладке асфальтобе- |
|||||
|
|
|
И |
тонных смесей современными укладчиками предварительное уплотнение обеспечивается рабочими органами укладчика. Поэтому в современных условиях производства работ по асфальтированию применение легких катков нецелесообразно. При применении современных укладчиков коэффициенты уплотнения смеси после укладки зачастую превышают начальные значения, характерные для промежуточного этапа. Этот факт необходимо учитывать на практике, устанавливая рациональный режим работы средних и тяжелых катков.
Проходы катков выполняются в направлении от краев к оси дороги, а затем от оси к краям, перекрывая каждый след на 20–30 см.
160
При уплотнении первой полосы, уложенной по схеме укладки сопряженными полосами, ее край на расстоянии 10 см от кромки уплотня-
ют при уплотнении второй полосы, выполняя первые проходы по сопряжению [36, п. 5.26], то есть применяется схема уплотнения с перекрытием смежной полосы. Вальцы катков в процессе уплотнения смачиваются водой или смесью воды с керосином. Это позволяет избежать налипания асфальтобетонной смеси на вальцы [36, п. 5.28].
С1,5–5 км/ч, пр чем на промежуточном этапе уплотнения – 3–5 км/ч и на заключ тельном – 2–3 км/ч [64]. В процессе работы катков необходимо обеспеч вать с нхронность их работы с асфальтоукладчиком. инхрон зац ю укладчика с катками выполняют изменением скорости укатки ли ч сла проходов катка по одному следу в рекомендуемом д апазоне [64]. При этом число проходов катка по одному следу
Катки стат ческого действия должны двигаться со скоростью
не должно быть меньше тре уемого количества, которое зависит от |
||
смеси, ее температуры и толщины укладываемого слоя. Чтобы |
||
типа |
необхо- |
|
уточн ть |
ч сло проходов катка по одному следу, |
|
димо про звести про ную укатку слоя [64]. |
|
|
Катки на пневматических шинах обычно используют на проме- |
||
жуточном этапе уплотнения асфальтобетонного слоя [64]. |
Уплот- |
|
|
требуемое |
|
няющее воздействиеАкатка на слой зависит от нагрузки на колесо, давления в шине и ее жесткости (см. рис. 78 и 79).
Применение вибрационныхДкатков позволяет использовать для уплотнения смеси один из трех режимов: статического действия (вибраторы отключены), комплексного действия (один валец оказывает на материал статическое воздействие, а второй – вибрационное) и вибрационного воздействия режиме. Рекомендуемый документом [64] диапазон частот и амплитуд составляет 25–58ИГц и 0,2–0,8 мм, что согласуется с представленными нами далее диапазонами частот 33 – 50 Гц и амплитуд 0,4–0,8 мм, указанной в пособии [72]. Поэтому несмотря на небольшие различия специалисты практически единодушны во мнении о рациональном режиме работы вибрационного катка.
Для катков различных типов установлены диапазоны варьирования рекомендуемого числа проходов по одному следу. Эти данные могут приниматься в качестве ориентировочных значений и уточняться выполнением пробного уплотнения.
При обеспечении качества выполнения работ по устройству конструктивных слоев дорожной одежды имеется контроль качества. Со-
161
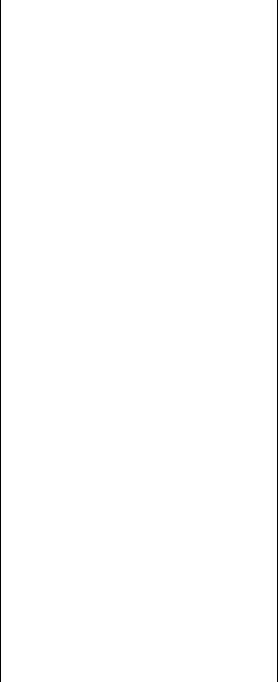
став, режим и объем контроля индивидуален для материалов и регламентирован СП 78.13330.2012 [7]. Подробно рассматривать требова-
|
ния к контролируемым параметрам и правила их определения в посо- |
||||||
|
бии не будем, ограничимся сведениями о дефектах, которые возника- |
||||||
|
ют на укладываемой и уплотняемой поверхности асфальтобетонного |
||||||
С |
|
|
|
|
|||
|
слоя. Эта информация приведена в табл. 57. |
|
Таблица 57 |
||||
|
Пр ч ны возн кновения и способы устранения дефектов поверхности |
||||||
|
укладываемой |
уплотняемой поверхности асфальтобетонного слоя |
|||||
|
|
|
|
[67, п. 8.2] |
|
|
|
|
Наименованчего выглаживающая плита то |
ройств укладчика и |
|
||||
|
|
|
де- |
Причины возникновения |
Способы устране- |
|
|
|
фекта |
|
|
ния |
|
||
|
|
1 |
|
2 |
|
3 |
|
|
|
|
|
Связаны, как правило, с неравно- |
|
|
|
|
|
|
|
мерной подачей смеси к шнековым |
Проверить работу |
|
|
|
|
|
|
п тателям укладчика, в результате |
|
||
|
|
|
|
питающих уст- |
|
||
|
|
|
|
|
|
|
|
|
Коротк е |
|
30–90 см, |
поднимается, то опускается вслед- |
выглаживающей |
|
|
|
|
чаще |
ств е изменения давления смеси |
плиты, а также ста- |
|
||
|
волны |
|
45–60 см |
на плиту. Другими причинами мо- |
|
||
|
шагом |
|
|
гут ыть износ шарниров плиты, |
бильность состава |
|
|
|
|
|
смеси и ее темпера- |
|
|||
|
|
|
|
неправильная установка угла атаки |
|
||
|
|
|
|
туры |
|
||
|
|
|
|
плиты, неста ильность смеси по |
|
||
|
|
|
|
|
|
||
|
|
|
|
составу (при укатке). |
|
|
|
|
|
|
|
Могут быть вызваны неправиль- |
Регулировка часто- |
|
|
|
|
|
7–10 см |
Д |
|
||
|
|
|
ным режимом работы виброкатка |
ты и амплитуды |
|
||
|
|
|
бА |
|
|
||
|
|
|
Появляются из-за колебаний со- |
|
|
||
|
|
|
|
става и температуры смесей в при- |
|
|
|
|
|
|
|
бывающих автосамосвалах или |
Проконтролировать |
|
|
|
|
|
|
резких изменений направления |
работу механизмов |
|
|
|
|
|
|
|
И |
|
|
|
Длинные волны |
движения катков. Кроме того, |
на укладке и каче- |
|
|||
|
|
|
|
длинные волны могут отражать |
ство (однородность |
|
|
|
|
|
|
неровности нижнего слоя основа- |
и температуру) под- |
|
|
|
|
|
|
ния. Расслоение смеси при достав- |
возимой смеси |
|
|
|
|
|
|
ке также может быть причиной по- |
|
|
|
|
|
|
|
явления длинных волн |
|
|
|
|
|
|
|
Как правило, вызваны неудовле- |
Проверить и отрегу- |
|
|
|
|
|
|
творительным состоянием или не- |
лировать работу пли- |
|
|
|
|
|
|
правильной работой укладчика (в |
ты, контролировать |
|
|
|
Разрывы по центру |
первую очередь, его выглаживаю- |
температуру смеси и |
|
|||
|
полосы укладки |
щей плиты), пониженной темпера- |
плиты. Одиночные |
|
|||
|
|
|
|
турой укладываемой смеси, появ- |
разрывы устраняют- |
|
|
|
|
|
|
лением в составе смеси негабарит- |
ся вручную добавле- |
|
|
|
|
|
|
ного щебня |
|
нием горячей смеси. |
|
162
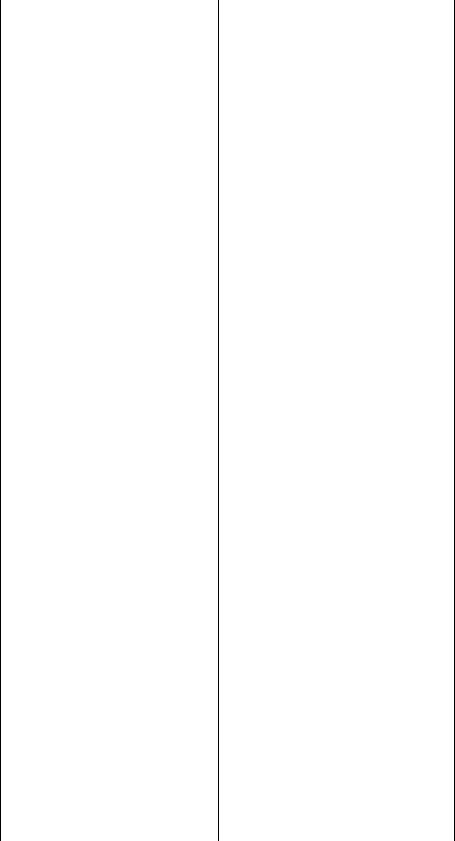
|
|
|
|
Продолжение табл.57 |
||
|
1 |
|
2 |
|
3 |
|
|
|
|
Вызывается главным образом |
|
Контроль и регули- |
|
|
|
|
расслоением смеси при при- |
|
|
|
|
|
|
|
ровка работы орга- |
|
|
|
Неоднородная текстура |
|
готовлении и доставке, низ- |
|
нов асфальтоуклад- |
|
|
поверхности покры- |
|
кой температурой смеси, ко- |
|
чика и (или) устра- |
|
|
тия (особенно при работе с |
|
лебаниями состава смеси и |
|
нение причин рас- |
|
|
щебен стыми смесями) |
|
неправильной регулировкой |
|
|
|
|
|
|
слаивания смеси на |
|
||
|
|
|
подачи смеси под выглажи- |
|
|
|
|
|
|
|
АБЗ |
|
|
|
|
|
вающую плиту |
|
|
|
|
|
|
|
|
|
|
С |
|
Возникают при остановках |
|
Регулировать или |
|
|
|
укладчика перед разгрузкой |
|
|
|||
|
|
отремонтировать |
|
|||
|
|
|
очередного самосвала, не- |
|
плиту укладчика, |
|
|
|
|
правильном взаимодействии |
|
|
|
|
леды от выглаж вающей |
|
|
добиться взаимо- |
|
|
|
|
укладчика и самосвала (рез- |
|
|
||
|
пл ты |
|
|
действия при раз- |
|
|
|
и |
|
ких торможениях) или при |
|
грузке автосамосва- |
|
|
|
ра оте укладчика с уширите- |
|
|
||
|
|
|
лов, сократить оста- |
|
||
|
|
лями |
|
|
||
|
|
|
|
новки укладчика |
|
|
|
|
|
|
|
|
|
|
|
|
|
|
|
|
|
|
|
О ычно проявляется после 2- |
|
С учетом основной |
|
|
|
|
|
причины следует, в |
|
|
|
|
|
3 проходов катка (особенно |
|
первую очередь, |
|
|
|
|
гладковальцового) в начале |
|
|
|
|
|
|
|
проверить и откор- |
|
|
|
|
|
укатки. Трещины могут по- |
|
|
|
|
|
|
|
ректировать или |
|
|
|
|
|
являться и в промежуточный |
|
|
|
|
|
|
|
|
|
|
|
|
|
Д |
|
||
|
|
|
период укатки при повышен- |
|
изменить состав |
|
|
|
|
|
смеси (некоторые |
|
|
|
|
|
ной температуре смеси и |
|
|
|
|
бАсмеси растрескива- |
|
||||
|
|
|
пластичных (малощебени- |
|
ются даже при тем- |
|
|
Растрескивание (появление |
стых) смесях. Редко трещины |
|
пературе 65°С), от- |
|
|
|
коротких поперечных |
возникают при значительной |
|
корректировать ре- |
|
|
|
трещин). |
разности температур уклады- |
|
|
||
|
|
жим уплотнения (в |
|
|||
|
|
|
И |
|
||
|
|
|
ваемой смеси и нижнего |
|
первую очередь |
|
|
|
|
слоя.Причинами растрески- |
|
температурный) |
|
|
|
|
вания могут быть состав сме- |
|
или изменить со- |
|
|
|
|
си, неправильно выбранные |
|
став звена дорож- |
|
|
|
|
режимы уплотнения катком |
|
ных катков, напри- |
|
|
|
|
(повышенная скорость катка, |
|
|
|
|
|
|
|
мер, использовать в |
|
|
|
|
|
резкие развороты или оста- |
|
начале укатки толь- |
|
|
|
|
новки катка на покрытии) |
|
|
|
|
|
|
|
ко пневмокаток |
|
|
|
|
|
|
|
|
|
|
|
|
Неправильная регулировка |
|
Корректировка ра- |
|
|
Неравномерная толщина |
выглаживающей плиты или |
|
боты выглаживаю- |
|
|
|
слоя |
повышенной скоростью дви- |
|
щей плиты уклад- |
|
|
|
|
|
жения укладчика |
|
чика |
|
163
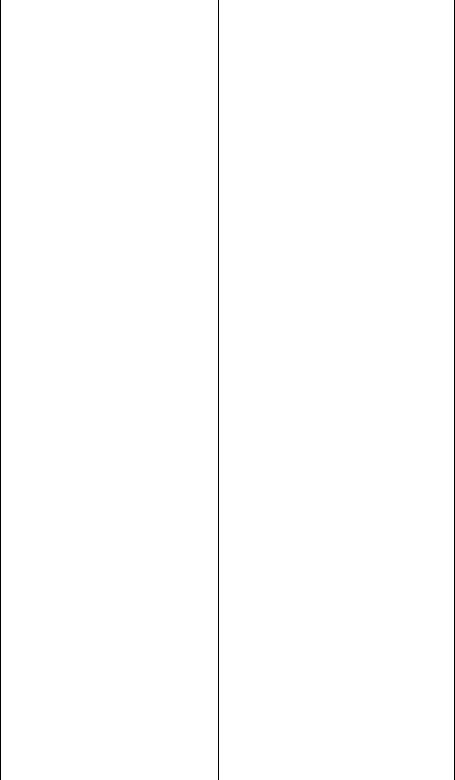
|
|
Продолжение табл. 57 |
||
|
1 |
2 |
3 |
|
|
|
Могут быть вызваны либо |
Дефект, в случае |
|
|
|
двух последних |
|
|
|
|
недостаточным уплотнением |
|
|
|
|
причин, может |
|
|
|
|
нижнего слоя или сцеплени- |
|
|
|
Продольные трещины |
быть устранен |
|
|
|
ем с ним, либо сдвигом от |
|
||
|
вдоль полотна |
только частично, |
|
|
|
тяжелого катка при разворо- |
|
||
|
|
пока смеси нахо- |
|
|
|
|
тах, либо уплотнением слиш- |
|
|
|
|
дятся в горячем со- |
|
|
|
|
ком горячей смеси |
стоянии |
|
|
|
|
|
|
С |
Обычно появляются в началь- |
Добиться в первую |
|
|
ный период эксплуатации по- |
очередь минималь- |
|
||
крытия в виде двух жирных |
ного содержания |
|
||
|
|
полос по колее движения. Они |
влаги в укладывае- |
|
|
|
могут вызывать резкое повы- |
|
|
|
|
мой смеси, сниже- |
|
|
|
|
шение скользкости покрытия |
ния содержания би- |
|
|
|
осо енно в мокрую погоду. |
|
|
|
Выступан е б ту- |
тума или изменения |
|
|
|
Причины связаны главным |
|
||
|
маи(жирные пятна) на по- |
состава смеси. Как |
|
|
|
о разом с повышенным со- |
|
||
|
верхности покрыт я |
крайняя мера может |
|
|
|
держанием битума в составе |
|
||
|
|
быть рекомендова- |
|
|
|
|
асфальто етонной смеси, рас- |
|
|
|
|
на присыпка жир- |
|
|
|
|
слоением смеси, присутствием |
ных пятен сухим |
|
|
|
воды в смеси, повышенным |
|
|
|
|
мелким песком или |
|
|
|
|
содержанием битума при об- |
|
|
|
|
минеральным по- |
|
|
|
|
ра отке (подгрунтовке) ниж- |
рошком |
|
|
|
Д |
|
|
|
|
него слоя |
|
|
|
|
Обычно остаются в процессе |
|
|
|
бАначального или основного |
Соответственно |
|
|
|
|
уплотнения и удаляются на |
проверить и при |
|
|
|
этапе окончательного уплот- |
необходимости от- |
|
|
|
нения. Однако при непра- |
корректировать со- |
|
|
|
И |
|
|
|
|
вильном режиме уплотнения |
став и температуру |
|
|
Следы от катков |
они могут остаться на гото- |
смеси, увеличить |
|
|
на покрытии |
вом покрытии. Причинами |
число проходов |
|
|
|
дефекта могут быть высокая |
катков, применить |
|
|
|
температура или повышенная |
более тяжелый ка- |
|
|
|
пластичность состава смеси, |
ток или пневмока- |
|
|
|
недостаточное число прохо- |
ток при оконча- |
|
|
|
дов или остывание смеси до |
тельной укатке |
|
|
|
окончания укатки |
|
|
164

Окончание табл. 57
|
1 |
|
|
|
2 |
|
3 |
|
|
|
|
|
|
|
|
Следует |
четко |
со- |
|
|
|
|
|
|
|
блюдать |
правила |
|
|
|
|
|
|
|
|
работ, |
целесооб- |
|
|
|
Некачественные швы со- |
|
|
|
разно рекомендо- |
|
|||
С |
|
Имеют причиной несоблю- |
вать разогрев хо- |
|
|||||
|
пряжения полос (разность |
|
|
||||||
|
уровней или расслоение |
|
дение |
вышеприведенных |
лодных спаек газо- |
|
|||
|
смеси в шве) |
|
правил их выполнения. |
выми |
горелками |
|
|||
|
|
|
|
|
|
или линейками де- |
|
||
|
рекомендациям |
|
|
фектных |
мест |
с |
|
||
|
|
|
подкаткой катком. |
|
|||||
|
|
|
|
|
|
|
|||
|
3.3. Устройство ус |
ления из особых видов асфальтобетона |
|
|
|||||
|
бА |
|
|
|
|
||||
|
огласно |
|
|
[64, разд. 8] к особым видам асфальто- |
|||||
|
бетона относят пол мерасфальто етон, дисперсно-армированный ас- |
||||||||
|
фальтобетон |
ще еночно-мастичный асфальтобетон. В пособии [36, |
|||||||
|
разд. 6] пр ведено еще |
|
ольшее количество особых разновидностей |
||||||
|
асфальтобетона. К ним относят асфальтобетоны с добавками дробле- |
||||||||
|
ной резины, серы, стеклянного |
оя, порошковых отходов промыш- |
|||||||
|
ленности, а также асфальто етоны на основе природных битумосо- |
||||||||
|
держащих пород (киров) и многощебенистый асфальтобетон. |
|
|
||||||
|
В составе полимерасфальтобетона содержится битум с добавкой |
||||||||
|
|
|
|
|
Д |
|
|
||
|
полимера. Битум, улучшенный добавкой полимера, называют поли- |
||||||||
|
мерно-битумным вяжущим (ПБВ) [36, 64]. Известны различные клас- |
||||||||
|
сы полимеров: эластомеры, пластмассы, смолы и термоэластопласты. |
||||||||
|
Каждый класс полимеров обладает своими достоинствами, но для |
||||||||
|
приготовления |
ПБВ целесообразно применять термоэластопласты |
|||||||
|
|
|
|
|
И |
||||
|
[36, п. 6.2]. Термоэластопластами (термопластичные эластомеры) на- |
||||||||
|
зывают полимеры синтетического происхождения в невулканизиро- |
||||||||
|
ванном состоянии, которые сочетают свойства пластмасс и эластоме- |
||||||||
|
ров. Термопластичные эластомеры имеют высокую прочность, |
ха- |
рактерную для пластмасс, и эластичность, присущую эластомерам. В пособии [36] сообщается, что температура хрупкости термоэластопластов достигает – 80 °С и ниже. При температуре около 80 °С термоэластопласты растворяются в нефтепродуктах. Лучшими для приготовления ПБВ являются дивинилстирольные (ДСТ) и изопренстирольные (ИСТ) термоэластопласты [36].
165
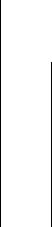
Требования к полимерно-битумным вяжущим приведены в стандартах [45, 73] и документах [64, 74, 75], а также учебной литературе [76]. Приготовление асфальтобетонных смесей с полимернобитумным вяжущим имеет температурные особенности перемешивания этого вяжущего с минеральными материалами [36, п. 6.8]. Технологические особенности хранения и транспортирования ПБВ изложены в стандарте [73, разд. 7].
Пол мерасфальтобетон отличается более высокой деформативностью при отр цательных температурах и повышенной упругостью
|
при полож тельных. Например, модуль упругости при |
– 20 °С – |
||||||||||
|
в 3–6 раз меньше, а при 40 °С – в 1,5–3 раза больше, чем у асфальто- |
|||||||||||
С |
туме марок БНД [36, |
п. 6.9]. В связи с такими |
||||||||||
|
бетона на вязком |
|||||||||||
|
пол мерасфальто етоны рекомендуется применять в рай- |
|||||||||||
|
онах евера |
С |
ри. В та л. 58 приведены данные рекомендаций |
|||||||||
|
[64], которые |
ллюстр руют сравнение показателей асфальтобетонов |
||||||||||
|
на ПБВ вязком |
туме покрытий дорог г. Омска. |
|
|
|
|
|
|||||
|
свойствами |
|
|
|
Таблица 58 |
|||||||
|
|
|
|
|
|
|
|
|
||||
|
Сравнен е показателей полимерасфальтобетона (ПАБ) |
|
|
|||||||||
|
|
и асфальто етона ( Б) [64, табл. 8.2] |
|
|
|
|
|
|||||
|
б |
|
Значение показателя |
|
||||||||
|
|
по окончании |
через год |
|
||||||||
|
|
Показатель |
|
|
|
|||||||
|
|
|
|
строительства |
эксплуатации |
|
||||||
|
|
|
|
|
|
|
|
|||||
|
|
|
|
|
|
|
|
АБ |
ПАБ |
|
АБ |
|
|
Плотность, г/см3 |
|
|
|
|
|
2,43 |
2,40 |
2,42 |
|
2,37 |
|
|
Водонасыщение, % по объему |
|
|
2,5 |
1,5 |
2,4 |
|
2,7 |
|
|||
|
|
|
ПАБ |
|
|
|
|
|
|
|||
|
Набухание, % |
|
|
|
|
|
0 |
0 |
0,1 |
|
0,2 |
|
|
Предел прочности при |
|
|
при 20 °С |
|
3,3 |
3,4 |
3,9 |
|
4,6 |
|
|
|
сжатии, МПа |
|
|
|
при 50 °С |
|
1,3 |
1,3 |
1,4 |
|
1,5 |
|
|
Водостойкость |
|
|
|
|
|
0,98 |
0,95 |
0,90 |
|
0,85 |
|
|
Показатель трещиностойкости R/E 104(см. § 1.4) |
|
1,41 |
0,9 |
1,4 |
|
0,6 |
|
||||
|
|
|
|
|
Д |
|
|
|
|
|||
|
|
|
|
|
|
И |
Асфальтобетон с дробленой резиной, применяемый в верхних слоях дорожной одежды, позволяет снизить динамические нагрузки, передаваемые на нижележащие слои, что повышает долговечность конструкции [36, п. 6.10]. Кроме того, применение асфальтобетонов с дробленой резиной приводит к повышению фрикционных свойств покрытия, что в ряде случаев уменьшает расход высокопрочного трудношлифуемого щебня [36, п. 6.10]. Таким образом, применение дробленой резины в составе асфальтобетонных смесей является экономически оправданным. Для асфальтобетонов применяют резину марки РДС, которая предварительно дробится до размера 1 мм и
166
меньше. Причем наибольшая прочность и плотность асфальтобетона обеспечивается при содержании в дробленой резине зерен мельче
0,63 мм не менее 60% массы [36, п. 6.11].
Для приготовления дробленой резины могут быть использованы изношенные шины. История применения дробленой резины из изношенных шин в составе асфальтобетонных смесей и технологии дроб-
Свводится л бо в м неральный заполнитель (1–2% от массы минеральной части), л бо в б тумное вяжущее (5–7% от массы битума), которое перемеш вается с минеральными материалами. В первом случае ее зерновой состав уч тывается в общем зерновом составе минераль-
ления рассмотрены в монографии [77, гл. 10].
При пр готовлен асфальтобетонной смеси дробленая резина
ных составляющ х, а во втором – не учитывается.
Пр готовлен е асфальто етонных смесей с дробленой резиной
технолог ческ е осо енности, описанные в [36, пп. 6.13 – |
|
6.15]. В настоящее время совершенствованию технологий приготов- |
|
имеет |
резиновой крошкой посвящено |
ления асфальто етонных смесей |
|
большое кол чество ра от [78, 79, 80, 81, 82], в том числе и разработ- |
|
ке новых разновидностей |
[83]. Специалисты считают, |
что введение резины в итум или гудрон является одним из наиболее |
|
асфальтобетона |
|
эффективных спосо ов их модификации [80, 81]. Основным техноло- |
|
гическим требованием при создании резинобитумного вяжущего яв- |
|
ляется растворение резины в битуме или гудроне [80, 81]. |
реше- |
ния этой задачи необходимо правильно выбрать технологический ре- |
|
А |
|
жим растворения резины, который обуславливается зерновым соста- |
|
вом резиновой крошки, типом каучука, входящим в ее состав, соста- |
|
вом битума, видом пластификатора, температурой и временем сме- |
|
шивания [81]. В результате термомеханической термообработки би- |
|
тума и резины происходит набуханиеДлярезины в масляных фракциях |
|
битума, ослабление межмолекулярных связей в резине и девулкани- |
|
зация резины [80, с. 21]. В результате девулканизации резины возни- |
|
кает каучуковое вещество, которое структурирует битум [80, с. 22]. |
|
Результатом взаимодействия битума и резины является образова- |
|
И |
|
ние трехфазной системы, состоящей из битума, резины и смеси рези- |
|
новых частиц и битума, которые представляют собой набухшие час- |
|
тицы резины, покрытые гелем [80, с. 22]. |
|
Регламентируемые пособием [36] способы ввода дробленой рези- |
ны в состав смеси имеют свои недостатки. При сухом способе введения резиновой крошки ее набухание происходит постепенно, что мо-
167
жет привести к разуплотнению и разрушению асфальтобетона в покрытии [80, с. 26]. Отсюда следует, что продолжительность процесса набухания необходимо учитывать в технологическом процессе устройства слоя покрытия. При мокром способе введения резиновой крошки отмечают снижение адгезии битума и уменьшение водостойкости и параметров сопротивления сдвигу [80, с. 26]. Для нейтрализации этих недостатков при мокром способе необходим ввод добавок и применен е спец ального оборудования [80, с. 27]. Это приводит к снижен ю эконом ческой эффективности.
Сасфальтобетона с рез новой крошкой, необходимо тонкое измельчерез ны. Это тре ование нужно соблюдать при любом способе введен я рез ны в состав смеси. Требуемое измельчение резины достигается пр менен ем различных технологий и оборудования
Для дост жен я требуемого качества покрытия, построенного из
битум уплотняемости готовыеАасфальто етонные смеси целесообразно вы-
[80, табл. 1.2].
Улучшен е удо оукладываемости и уплотняемости асфальтобе- |
|
ние |
мягчителя, например сланце- |
тонных смесей тре ует до авки в |
|
вого, в кол честве 4–7% массы |
итума [36, п. 6.15]. Для улучшения |
держивать в накопительных ункерах в течение 1–2 ч [36, п. 6.15]. Технология строительства покрытий из асфальтобетонных сме-
сей приведена в указаниях [84]. Технология строительства таких по-
нять укладчики с активными уплотняющимиДляорганами. В этом случае обеспечивается максимальное предварительное уплотнение смеси. Наиболее предпочтителен способ укладки на всю ширину, но допускается укладка сопряженными полосами. При укладке сопряженными полосами длина укладываемой полосы должна быть не более 100 м на
крытий должна соответствовать требованиям СП 78.13330.2012, но с учетом специфичности смеси. При укладке смесей с дробленой резиной или каучуками (порошковым и низкомолекулярным) должна находиться в пределах 140-160 °С, а температура смесей с добавкой по-
листирола – 160–180 °С [84, п. 5.2]. |
укладки необходимо приме- |
|
И |
защищенных от ветра участках и не более 50 м на открытых участках. При температуре воздуха ниже 15 °С длину полосы следует уменьшить в 2 раза [84, п. 5.3]. Особое внимание следует уделять уплотнению асфальтобетонных смесей с дробленой резиной или полистиролом. Температура смеси с резиновой добавкой должна быть на 10 °С ниже температуры смесей на обычных нефтяных битумах [84, п. 5.4]. Смеси с добавкой полистирола начинают уплотнять сразу же после
168
укладки, а заканчивают к моменту остывания смеси до температуры не ниже 100 °С. При укатке асфальтобетонных смесей с полистиролом при температуре ниже 100 °С в покрытии образуются технологические трещины [84, п. 5.4]. Асфальтобетонные смеси с порошковым или низкомолекулярным каучуком, а также смеси с добавкой полипропилена уплотняют так же, как и обычные смеси на нефтяных би-
тумах [84, п. 5.5].
Звено катков назначают в зависимости от начального коэффициента
уплотнен я, |
который достигается за счет предварительного уплотнения |
||
рабочими органами асфальтоукладчика. Для правильного и рациональ- |
|||
ного комплектован я звена катками определяют начальную величину |
|||
С |
|
|
|
коэфф ц ента уплотнен я после укладчика. Методика определения на- |
|||
чального коэфф ц ента состоит в том, что перед укладчиком на поверх- |
|||
ность слоя, на который |
удет производиться укладка смеси, устанавли- |
||
вают |
ческую пластину с размерами 200 150 1,5 мм [84, п. 5.6]. |
||
К пласт не крепят |
|
проволоку, второй конец которой за- |
|
металлическую |
|
||
крепляют на |
не. После прохода укладчика пластина со смесью ак- |
||
куратно звлекается. После остывания образца он снимается с пластины |
обоч и транспортируется вАла ораторию для определения коэффициента уп-
лотнения. Коэффициент уплотнения определяется расчетным путем по данным испытаний на среднюю плотность асфальтобетона и его максимальную стандартную плотность. Испытания выполняют в соответствии
с ГОСТ12801–84. |
Д |
|
|
При уплотнении смесей с начальным коэффициентом уплотнения |
более 0,9 звено катков комплектуют гладковальцовым катком массой 10–13 т, который выполняет 4–6 проходов, либо вибрационным катком массой 6–8 т, выполняющим 2–4 прохода при выключенном вибраторе, и 3–4 прохода с включенным вибраторомИ. Окончательное уплотнение производят гладковальцовым катком массой 11–18 т при 10–12 проходах. Если начальный коэффициент уплотнения ниже 0,9, то в звено вводят гладковальцовый каток массой 6–8 т, который начинает уплотнение уложенной полосы смеси, выполняя 2–4 прохода [84, п. 5.7]. Смеси с добавкой полистирола уплотняют гладковальцовым катком массой 11–18 т или катком на пневматических шинах
[84, п. 5.8].
Вальцы катков обильно смачивают водой или мыльным раствором. Особую важность это требование приобретает при первых проходах.
169
Для приготовления асфальтобетонных смесей применяют порошковые отходы промышленности, к которым относят: пыль уноса це-
ментных заводов, золу-унос ТЭС, ферропыль, флотохвосты, шламы и пр. [36, п. 6.16]. Добавка порошковых отходов производится с целью экономии минерального порошка. Порошковые отходы испытывают Спо ГО Т Р 52129-2003 [85], устанавливая соответствие их физико-
механических характеристик требованиям этого стандарта, и определяют область пр менения. Отходы отличаются разнообразием по хи-
в верхн х слоях покрытий на дорогах IV категории в любой дорожно-
мическому зерновому составу, они используются для замены мине- климатрального порошка в смесях III марки, которые могут быть применены
ческой зоне [45, прил. А].
Порошковые отходы подразделяют на грубодисперсные (с со-
держан емгрубодчаст ц мельче 0,071 мм в количестве 30–60%) и тонко-
дисперсные (с содержанием частиц мельче 0,071 мм в количестве
60–95%). К сперсным порошковым отходам относят (флото-
хвосты, золошлаковые смеси, отсевы дробления слабых известняков), а к тонкод сперсным – (ферропыль, шламы, пыль уноса цементных заводов, циклонная Апыль). Применение тонкодисперсных отходов может приводить к некоторому увеличению расхода битума за счет большой удельной поверхности. Некоторые отходы, например асбестовые, потребляют итум в повышенном количестве, что также при-
игрубодисперсными отходами промышленностиДприведены в пособии [36, пп. 6.17 – 6.21]. Укладка и уплотнение таких смесей выпол-
няется в соответствии с правилами СП 78.13330.2012.И Природные битумосодержащие породы (киры) применяют в ас-
фальтобетонах для полной или частичной замены нефтяных битумов. Киры представляют собой рыхлые породы, преимущественно мелкие
ипылеватые пески, пропитанные природными битумами различной вязкости [36, п. 6.24]. Крупные месторождения киров находятся за пределами РФ в Казахстане и Азербайджане. Поэтому применение таких асфальтобетонных смесей для строительства покрытий на дорогах России экономически нецелесообразно. Правила приготовления асфальтобетонных смесей и подбора их состава рассмотрены в пособии [36, пп. 6.23 – 6.28]. Правила укладки и уплотнения таких асфаль-
170
тобетонных смесей не отличаются от технологии устройства покрытий из асфальтобетонов на нефтяных битумах.
ера применяется в составе асфальтобетонных смесей для уменьшения температуры нагрева минеральных материалов и битума, снижения расхода битума, увеличения производительности уплотнителей, улучшения эксплуатационных свойств и повышения долговечности асфальтобетонных покрытий [36, п. 6.30]. Применяемые технические серы (комовая, жидкая, молотая) должны соответствовать тре-
бованиям |
127.1–93 [86]. При проектировании состава асфаль- |
||||
тобетона оп раются на принцип постоянства объема вяжущего. Этот |
|||||
принц п заключается в том, что объем серно-битумного вяжущего |
|||||
ГОСТ |
тума и серы) должен быть равен объему биту- |
||||
(суммарный объем |
|||||
в асфальтобетоне |
ез до авки серы. |
|
|
||
Подбор выполняют согласно указаниям пособия [36], которое |
|||||
регламент |
рует под ор зернового состава, определение содержания |
||||
|
с последующ м определением дозировки серы. Между биту- |
||||
битума |
битумов |
марок |
|||
мом |
серой рекомендуются соотношения: для |
||||
БНД 40/60, БНД 60/90, БН 60/90, БН 90/130 |
– 70:30, |
марки |
|||
БНД 90/130 – 60:40. Изменять вышеуказанные соотношения можно |
|||||
лишь |
в сторону уменьшения содержания серы. |
В монографии |
|||
В.Д. Галдиной [87, 88] приводятся данные о прочности и величине |
|||||
модуля упругости асфальто етонов на серобитумном вяжущем. В за- |
|||||
|
|
бА |
|
|
[87, табл. 1.5]. Модуль упругостиДасфальтобетонов на серобитумных вяжущих выше модуля упругости асфальтобетонов на нефтяных би-
висимости от содержания серы в серобитумном вяжущем прочность асфальтобетона различна. При сравнительно малом содержании серы прочность асфальтобетона меньше прочности асфальтобетонов без
добавки серы, но при увеличении содержания серы прочность увели-
чивается и превосходит прочность асфальтобетонов без добавки серы И
тумах [87, табл. 1.6].
При приготовлении смеси серу вводят либо в битум, либо в виде самостоятельного компонента непосредственно в смеситель
[36, п. 6.35].
Работы по устройству покрытия производят согласно требованиям СП 78.13330.2012, но соблюдая некоторые правила, оговоренные в [36, п. 6.36]. Первое из этих правил касается температуры смесей при укладке в слой. В том случае, если содержание серы до 2% массы смеси, то температура укладки должна быть не ниже 110 °С. При содержании серы свыше 2% – не ниже 120 °С. Уплотнение смеси начи-
171
нают сразу после укладки. Для уплотнения асфальтобетона с добавкой серы число проходов катка можно уменьшить по сравнению с рекомендуемым СП 78.13330.2012. Например, для уплотнении смесей с содержанием серы до 2% число проходов катков всех видов может быть уменьшено на 15–20%, а при содержании серы больше 2% – на 25–30% (по сравнению с уплотнением асфальтобетонных смесей на нефтяных битумах без добавки серы) [36, п. 6.36].
Многощебен стые асфальтобетоны повышенной плотности содержат в своем составе 55 – 70% щебня [36, п. 6.37]. В таких асфаль-
тобетонах содержан |
щебня может быть выше, чем в горячем плот- |
ном асфальтобетоне т па А, в составе которого содержится до 60% |
|
С |
многощебенистых асфальтобетонных сме- |
щебня. Для пр |
сей пр меняют ще ень с наи ольшим размером зерен до 20 мм
готовления
способствует жду песком и минеральнымАпорошком. Этот подбор производят так,
[36, п. 6.38]. На ольшая плотность достигается за счет применения
песков с модулем крупности 1,5 – 2 и активированных минеральных порошков [36, . 6.38]. Применение активированного минерального
порошка |
уменьшению содержания битума [36, п. 6.38]. |
Подбор состава смеси начинают с определения соотношения ме- |
чтобы пористость их смеси песка и минерального порошка была минимальна. Затем под ирают количество битума так, чтобы показатели физико-механических свойств о разцов, уплотненных комбиниро-
меняют для устройства покрытийДтолщиной 3,5–5,0 см назначаемой по расчету, а при использовании в составе смеси щебня фракции 5–10 мм – для устройства защитных слоев минимальной толщины
ванным способом, соответствовали требованиям [36, табл. 14]. При таком подборе, несмотря на повышенное содержание минерального порошка, количество битума в составе многощебенистой асфальтобетонной смеси не превышает пределы, оговоренные ГОСТ 9128–2013.
1,5–2,0 мм [36, п. 6.41].
Многощебенистый асфальтобетон повышенной плотности при- И
Строительство слоев из многощебенистого асфальтобетона по-
вышенной плотности имеет особенности. Первая особенность связана с необходимостью обеспечения максимальной плотности, которая необходима для повышения шероховатости. Поэтому укладку многощебенистых смесей необходимо выполнять современными моделями асфальтоукладчиков, обеспечивая температуру смеси в бункере укладчика не ниже 140 °С.
172
Продольные и поперечные сопряжения верхнего слоя покрытия подвержены разрушающему воздействию воды. Кроме того, при уст-
ройстве сопряжений покрытия нельзя допускать местного накопления щебня, так как это приведет к образованию выбоин и неровностей [36, п. 6.42]. Поэтому укладку многощебенистых смесей ведут либо на всю ширину, либо несколькими укладчиками, расстояние между которыми не должно превышать 30 м. Не разрешается распределять по поверхности слоя щебень, оставшийся при ручной заделке продольных сопряжен й. Сопряжения должны быть особенно тщательно уплотнены. Контроль качества устройства сопряжений выполняют
Свизуально, при х правильном устройстве они незаметны. Уплотнение слоя выполняют гладковальцовыми катками массой 8–18 т и са-
гладковальцовымимоходными катками на пневматических шинах массой 16 т. Рекомендации [89, бАп. 5.6] заключается в том, что в качестве рационального
режима уплотнен я многоще енистой смеси надо начинать укатку катками массой 10 – 13 т, а заканчивать пневмо-
катками массой 16 т.
Стеклянный ой является промышленным или бытовым отходом, зерна которого по прочности и зерновому составу сопоставимы с аналогичными характеристиками минерального материала. Поэтому применение стеклянного оя в составе асфальтобетонных смесей позволяет экономить минеральный материал. Согласно указаниям [36, п. 6.43] применение стеклянногоДбоя позволяет экономить не только минеральный материал, но и уменьшить расход битума, получив покрытие с высокими рефлектирующими свойствами. В составе асфальтобетонных смесей применяют бутылочный, оконный, закаленный и любой другой стеклянный бой, ограничивая наибольший размер зерна 15 мм. Стеклянный бой испытываютИна дробимость, принимая 15% потери массы в качестве предельного значения [36, п. 6.43]. Стеклобой используют для приготовления смесей для плотного горячего асфальтобетона типа Б и Г. При добавлении в смесь до 10% стеклянного боя качество смеси не снижается, но при большей дозировке стеклобоя существенно снижаются прочность при 50 оС, водостойкость и морозостойкость. Поэтому для повышения показателей указанных свойств рекомендуется вводить в битум добавки, например 2% извести, а также 15% нефтеполимерной смолы или 2–3% катионных ПАВ, вводимых в битум [36, п. 6.44]. При приготовлении асфальтобетонных смесей, содержащих стеклянный бой, температура нагрева минеральных материалов и стеклянного боя может
173
быть на 10–20 оС ниже, по сравнению с регламентируемой СП 78.13330.2012. На такое же значение может быть снижена температура готовой смеси.
Укладывать асфальтобетонную смесь, содержащую стеклянный бой, следует при температуре не ниже 110 оС. Уплотнение уложенного слоя, начинают легкими катками (за 3–5 проходов по одному следу), а затем средним или тяжелым катком (за 10–12 проходов) [36, п. 6.46].
В услов ях роста автомобилизации происходит увеличение на- |
|||
грузки от транспортных средств и числа их приложений. Это обстоя- |
|||
тельство требует пр менения в дорожных покрытиях и основаниях |
|||
С |
|
|
|
особых разнов дностей асфальтобетона. Такими разновидностями |
|||
являются |
д сперсно-армированные, |
полимерно-дисперсно- |
|
|
ще еночно-мастичные асфальтобетоны. В настоящее |
||
время так |
асфальто етоны широко применяют при строительстве |
||
покрыт й |
верхн х слоев оснований нежестких дорожных одежд на |
||
армированные |
|
|
|
федеральных автомо льных дорогах [90]. Дисперсное армирование |
|||
асфальтобетонных смесей применяют в качестве мероприятия, повы- |
|||
шающего трещиностойкость асфальтобетона [91]. Конструкции до- |
|||
рожных одежд с покрытиями и основаниями из |
дисперсно- |
армированныхбА, полимерно-дисперсно-армированных и щебеночномастичных асфальто етонов включают в альбомы типовых конструк-
ций [92]. Д
Дисперсно-армированный асфальтобетон представляет собой уложенную в слой и уплотненную дисперсно-армированную асфальтобетонную смесь, которую приготавливают введением дисперсной арматуры в традиционную асфальтобетонную смесь [64, разд. 8.2]. Дисперсно-армированные асфальтобетонныеИсмеси рекомендуется применять на дорогах высоких технических категорий, как правило, I и II, а также на городских магистральных улицах с повышенной грузонапряженностью [64]. Покрытия из дисперсно-армированного асфальтобетона эффективны на участках торможения автомобилей, что свидетельствует о более высоком сопротивлении сдвигу и меньшей ползучести по сравнению с асфальтобетонами на нефтяных битумах. Кроме того, дисперсное армирование приводит к повышению трещиностойкости, особенно в тех случаях, когда армирование выполняют фиброй [91, разд. 5].
Классическое армирование асфальтобетонной смеси выполняется одним из двух способов. Первый способ состоит во введении в ас-
174
фальтобетонную смесь армирующих волокон длиной до 20 мм. Этот способ называется дискретным способом армирования [64]. Второй
способ заключается во введении в смесь через фильеры расплава волокнообразующего полимера. Этот способ армирования называют континуальным способом армирования [64].
Сдеструкц при температуре нагрева 110–120 °С. Поэтому рекомендации [64] запрещают применять для изготовления дисперсной арматуры пол уретановые поливинилхлоридные соединения.
Дисперсную арматуру изготавливают из химических искусственных и синтетических или минеральных волокон. Для изготовления армирующ х волокон непригодны материалы, которые подвергаются
В качестве д сперсной арматуры успешно применяют фибру из ПАН-волокна [91]. Фибру вводят в смесь одним из четырех способов, который вы ирают в зависимости от вида исполь-
зуемой ф бры.
Первый способ предполагает вдувание предварительно вспушен- |
|
специального |
|
ной ф бры в «сухой» замес, то есть до введения вяжущего. Этот спо- |
|
соб предназначен для введения фибры длиной 18±1,6 мм [91, п. 5.2.4]. |
|
Второй способ тоже состоит во вдувании вспушенной фибры, но |
|
в «мокрый» замес. Этот |
применяют для фибры, длина нарезки |
способ |
|
которой составляет также 18±1,6 мм [91, п. 5.2.4]. |
|
Третий способ заключается во введении фибры через бункер по- |
|
А |
|
дачи минеральных материалов. Этот способ применяют для введения |
|
фибры длиной 6±0,5 мм. Фибру с большей длиной нарезки этим спо- |
|
собом вводить нельзя, так как возникает опасность образования комь- |
ев и сгустков фибры в асфальтобетонной смеси. Время перемешива- |
|
ния замеса следует увеличить на 10–40 с. Необходимость увеличения |
|
|
И |
времени перемешивания продиктована необходимостью равного рас- |
|
пределения фибры для приготовленияДоднородной асфальтобетонной |
|
смеси [91, п. 5.2.4]. |
|
При реализации четвертого способа фибру вводят через систему |
|
подачи минерального порошка. Длина фибры должна составлять те |
же 6±0,5 мм, а содержание минерального порошка должно быть больше 5%. Этот способ нельзя применять в тех случаях, когда минеральный порошок объединяют с пылью уноса [91, п. 5.2.4].
При введении дисперсной арматуры волокна должны быть сухими. Применение влажных волокон недопустимо [64]. Во избежание комкования волокон максимальная длина их нарезки ограничивается 20 мм. Особенности подбора состава дисперсно-армированного ас-
175
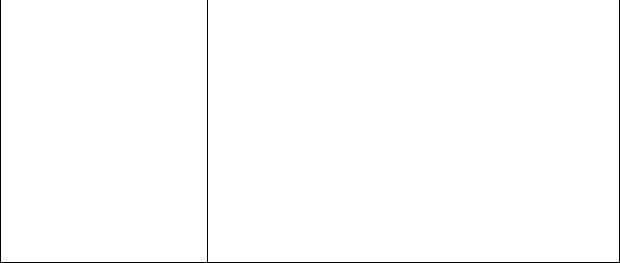
фальтобетона и технология его приготовления приведены в рекомендациях [64]. Эти же рекомендации регламентируют технологию постройки покрытий и оснований из дисперсно-армированных асфальтобетонных смесей.
Технологической особенностью строительства слоев оснований и покрытий дорожных одежд из дисперсно-армированных асфальтобетонных смесей является необходимость строго соблюдать температу-
|
ру смеси при укладке |
уплотнении [64]. Ориентировочные интерва- |
|||||
|
лы изменен я температуры при ее выгрузке в бункер укладчика при- |
||||||
|
ведены в табл. 59. |
Эти |
температуры |
даны в рекомендациях |
|||
|
[64, табл. 4]. |
|
|
|
|
|
|
С |
|
|
|
|
Таблица 59 |
||
|
|
|
|
|
|
|
|
|
Ор ент ровочные |
нтервалы изменения температуры асфальтобетонной |
|||||
|
|
перед ее выгрузкой в приемный бункер асфальтоукладчика |
|||||
|
|
|
|
Температура смеси, °С |
|||
|
Марка |
тума |
высокоплотной, плотной |
плотной типов В, Г и Д, |
|||
|
пористой и высокопорис- |
||||||
|
|
|
|
||||
|
смеси |
и Б, пористой и |
|
|
|||
|
|
|
типов |
той, высокопористой |
|||
|
|
|
высокопористой |
|
|||
|
|
|
|
|
песчаной |
||
|
|
|
|
|
|
|
|
|
БНД 40/60, |
БНД 60/90, |
|
|
|
|
|
|
БНД90/130, БН 60/90, БН |
|
120–160 |
|
|
100–130 |
|
90/130 |
б |
|
|
|
|||
|
|
|
|
|
|
||
|
БНД 130/200, БНД200/ |
|
|
|
|
|
|
|
300, БН 130/200, БН 200/ |
|
100–140 |
|
|
80–110 |
|
300 |
|
|
|
|
|
|
|
|
СГ 130/200, МГ 130/200, |
|
|
|
|
|
|
|
|
А |
|
||||
|
МГО 130/200 |
|
|
70–100 |
|
В рекомендациях [64] подчеркиваетсяД, что наличие в составе асфальтобетонной смеси дисперсной арматуры исключает отклонение в температурном режиме при укладке и уплотнении, так как оно влечет
за собой снижение коэффициента ее уплотнения. Полимерно-дисперсно-армированный асфальтобетон (ПДА)
представляет |
собой |
уплотненную |
полимерно-дисперсно- |
||
армированную асфальтобетонную смесь с резиновым термоэласто- |
|||||
пластом (ПДА смесь). ПДА смесь является |
И |
||||
рационально подобран- |
|||||
ной смесью минеральных материалов (щебня и песка с минеральным |
|||||
порошком или |
без |
него) |
с |
полимерно-дисперсной армирующей |
|
(структурирующей) |
добавкой |
– резинового термоэластопласта |
(РТЭП) и битумом, взятых в определенных соотношениях и перемешанных в нагретом состоянии [93, разд. 3].
176
Горячие полимерно-дисперсно-армированные асфальтобетонные смеси и полимерно-дисперсно-армированные асфальтобетоны в зависимости от вида минеральной составляющей подразделяются на щебеночные, песчаные и щебеночно-мастичные [93, п. 4.1]. ПДА смеси и ПДА асфальтобетоны подразделяют на мелкозернистые с размером зерен каменного материала до 20 мм и песчаные с размером зерен до 5 мм [93, п. 4.2]. Щебеночно-мастичные асфальтобетонные смеси и асфальтобетоны подразделяют по крупности используемого для их
приготовлен я щебня на ЩМА-20, ЩМА-15 и ЩМА-10 (соответст- |
|||||||
венно на больш й размер зерен 20, 15 и 10 мм) [94, разд. 4]. Щебе- |
|||||||
ночные ПДА смеси классифицируют на типы А и Б. Такое подразде- |
|||||||
С |
|
|
|
|
|
||
ление выполняют в зависимости от содержания щебня, которое для |
|||||||
типа А составляет |
олее 50 до 60%, а для типа Б – более 40 до 50%. |
||||||
Песчаная |
ПДА смесь |
меет только один тип, а именно тип Г, |
кото- |
||||
рый готовят на песках |
з отсевов дробления, а также на их смесях с |
||||||
|
|
песком |
|
содержании последнего не более 30% по мас- |
|||
природным |
|
|
|
||||
се [93, п. 4.4]. |
|
|
|
|
|
||
|
Требован я к зерновому составу и показателям физико- |
||||||
механических характеристик приведены в рекомендациях |
[93, |
||||||
табл. 1 – 6]би стандарте [94, та л. 1 – 4]. |
|
изло- |
|||||
|
Приготовление |
|
и ЩМА смесей имеет особенности, |
||||
женные в рекомендациях [93]. Строительство покрытий из таких сме- |
|||||||
сей |
должно выполняться |
в соответствии с |
требованиями |
||||
СП 78.13330.2012, но с учетом особенностей смесей. Верхний слой |
|||||||
|
|
|
ПДА |
|
|
||
покрытия из ПДА смесей устраивают в сухую погоду при температу- |
|||||||
ре окружающего воздуха не ниже + 5 °С, осенью – не ниже + 10°С |
|||||||
[93, п. 8.2]. Укладка ПДА смеси выполняется асфальтоукладчиком. |
|||||||
Предпочтительной укладкой является укладка на всю ширину. Для |
|||||||
укладки применяют укладчики |
Дс пассивной или вибрационной вы- |
||||||
глаживающей плитой и трамбующим брусом. При укладке ПДА сме- |
|||||||
сей типов А и Б, а также ЩМА смеси скорость укладчика должна на- |
|||||||
ходиться в пределах 2–3 м/мин [93, п. 8.4], а при укладке ПДА смеси |
|||||||
типа Г скорость укладки может быть увеличена до 4–5 м/мин [93, |
|||||||
п. |
8.4]. |
Частота |
оборотов |
И |
|||
валов трамбующего |
бруса |
1000– |
1400 об/мин; вала вибратора плиты 2500–3000 об/мин. При укладке и уплотнении ПДА и ЩМА смесей необходимо соблюдать температурный режим, оговоренный в рекомендациях [93, табл. 8 и табл. 9]. Эти температуры приведены в табл. 60 и 61.
177

|
|
|
|
|
Температура укладки ПДА смесей |
|
Таблица 60 |
|||||
|
|
|
|
|
|
|
||||||
|
Марка битума |
|
БНД 60/90 |
|
БНД 90/130 |
БНД 130/200 |
|
БНД 200/300 |
||||
|
Температура |
|
150–160 |
|
145–155 |
140–150 |
|
140–150 |
||||
|
ПДА смеси |
|
|
|
||||||||
|
|
|
|
|
|
|
|
|
|
|
||
|
|
|
|
|
|
|
|
|
|
|
|
Таблица 61 |
|
|
|
|
Температура уплотнения ПДА и ЩМА смесей |
||||||||
|
|
|
|
|
|
|
Температура смеси в начале уплотнения, °С |
|||||
|
Марка б тума |
|
плотного асфальтобетона |
плотного асфальтобетона |
||||||||
|
|
типов А, Б и ЩМА высо- |
||||||||||
|
смеси |
|
типа Г |
|||||||||
С |
|
|
коплотного |
|
|
|||||||
|
|
|
|
|
|
|||||||
|
БНД 60/90 |
|
|
145–155 |
|
|
125–140 |
|||||
|
БНД 90/130 |
|
|
|
140–150 |
|
|
|||||
|
|
|
|
|
|
|
|
|||||
|
ПДА |
более |
|
|
|
|
||||||
|
|
|
|
допускается укладывать сопряженными полосами, |
||||||||
|
длина которых должна ыть не олее 100 м на защищенных от ветра |
|||||||||||
|
участках не |
|
50 м на открытых участках [93, п. 8.7]. ПДА сме- |
си предвар тельно уплотняют легким гладковальцевым катком, выполняя 2–4 прохода по одному следу. Первый проход выполняют с выключенной ви рацией, а остальные – с включенной вибрацией. Затем уплотнение продолжают ком инированным или гладковальцевым катком массой 16–18 т с включенной вибрацией, выполняя 4–8 про-
ходов [93, п. 8.8]. Уплотнение |
смесей начинают выполнять |
|
Д |
легким гладковальцевым катком с приводом на оба вальца, осуществ- |
|
ляя 2–4 прохода по одномуЩМАследу. Окончательное уплотнение произ- |
водят катком массой 8–10 т при 4–6 проходах по одному следу [93, п. 8.9]. Указанное количество проходов катка ориентировочное, точное число проходов определяют пробным уплотнением.
Качество уплотнения ЩМА смеси оцениваютИпо показателям остаточной пористости или водонасыщения образцов, которые отбирают не раньше чем через сутки после устройства слоя покрытия [94, п. 9.2]. Качество уплотнения ПДА смеси оценивают величиной коэффициента уплотнения, который должен быть не ниже 0,99 (для высокоплотных и плотных ПДА асфальтобетонов из смесей типов А и Б) и 0,98 (для плотного ПДА асфальтобетона из смесей типа Г) [93, п. 8.9].
Более подробная технология устройства покрытий из ЩМА смесей приведена в специализированных учебных пособиях, например
[95, подразд. 4.3]
178