
- •ВВЕДЕНИЕ
- •1. ТЕХНОЛОГИЯ РАБОТ ПО ЛИКВИДАЦИИ МЕЛКИХ ПОВРЕЖДЕНИЙ: ЗАЛИВКА ТРЕЩИН И ЗАДЕЛКА ВЫБОИН
- •1.1. Традиционные способы ремонта
- •1.3. Ремонт с применением инфракрасных разогревателей асфальтобетона
- •2.3. Технология устройства поверхностной обработки методом Чип Сил
- •2.4. Технология устройства слоя износа методами Слари Сил, Микросюрфейсинг и Кейп Сил
- •2.5. Особенности применения технологии Фиб-Сил для устройства трещино-прерывающей прослойки
- •3. УСТРОЙСТВО СЛОЕВ УСИЛЕНИЯ ДОРОЖНОЙ ОДЕЖДЫ
- •3.1. Методы измерения упругого прогиба и определение модуля упругости дорожной одежды
- •3.2. Традиционные материалы и технологии для усиления дорожных одежд
- •3.4 Устройство усилений из асфальтобетона, армированного геосинтетическими материалами
- •4. ПРИМЕНЕНИЕ МЕТОДОВ ГОРЯЧЕЙ РЕГЕНЕРАЦИИ ДЛЯ ВОССТАНОВЛЕНИЯ И УСИЛЕНИЯ ДОРОЖНЫХ ОДЕЖД С АСФАЛЬТОБЕТОННЫМ ПОКРЫТИЕМ
- •5.1. Характеристика района и определение допустимых сроков производства работ
- •5.3. Комплектование отрядов и калькуляция трудовых затрат
- •Библиографический список
- •Приложение 1
- •Приложение 2
3.4 Устройство усилений из асфальтобетона, армированного геосинтетическими материалами
Геосинтетические материалы применяют в дорожных конструкциях при строительстве, реконструкции и ремонте автомобильных Сдорог [96, 97]. В качестве армирующей прослойки геосинтетику применяют для армирования оснований дорожных одежд из зернистых
материалов [98, 99] асфальтобетонных слоев [100].
Арм рован е зерн стого основания георешетками или геосеткамиПрипр вод т к ус лению дорожной одежды и препятствует взаимопрон кновен ю материалов контактирующих слоев. Усиление обуславл вается совместной ра отой армирующей прослойки и материала зерн стого основания. Частицы зернистого материала бло-
–предотвращениебАпоявления усталостных трещин и колейности;
–пререраспределение горизонтальных растягивающих напряжений, в том числе температурных, которые воспринимаются армирую-
щей решеткой (сеткой) и не приводят к разрушению асфальтобетона. Применению геосинтетическихДматериалов для армирования ас-
фальтобетонных покрытий посвящено большое количество научных статей и докладов, например [101, 102, 103], Значительный вклад в развитие этого направления внесли специалисты кафедры Проектиро-
вания дорог ФГБОУ ВО СибАДИ. В результате работы научного коллектива выполнен анализ отечественных и зарубежныхИнормативных документов [104, 105]. На основе анализа разработаны методы испытаний армированного асфальтобетона на изгиб [106] и технологическую повреждаемость [107], модифицированы нормативные методы расчета асфальтобетонных покрытий, учитывающие наличие в слое армирующего материала [108, 109], и разработана методика оценки экономической эффективности [110, 111]. Большая проделанная работа позволила разработать методический документ [100], устанавливающий требования к материалам, в том числе армирующим решеткам, и регламентирующим правила проектирования и строительства. Требования этого документа [100] авторы примут за основу данного раздела.
179
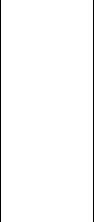
В соответствии с требованиями этого документа к геосинтетическим материалам предъявляются требования, указанные в табл. 62 [100, табл. 1].
С |
|
|
Таблица 62 |
|||
|
|
Требования к показателям свойств геосинтетических материалов |
||||
|
|
и документы, регламентирующие методику контроля [100, табл. 1] |
||||
|
|
Показатель свойств |
Значение |
Методика |
|
|
|
|
показателя |
контроля |
|
||
|
|
|
|
|
||
|
|
|
|
|
|
|
|
|
|
1. Механические свойства |
|
|
|
|
сительной |
|
DIN EN ISO 10319, |
|
||
|
Прочность при растяжен и в продольном |
|
|
|||
|
(поперечном) направлен RLR (RTR), кН/м, не |
50 |
ОДМ 218.5.006- |
|
||
|
менее |
|
|
2010 |
|
|
|
Усил в образце в направлении длины (ши- |
|
DIN EN ISO 10319, |
|
||
|
|
бА |
|
|
||
|
рины) матер ала RLR(ε) RTR(ε), отнесённое к |
25 |
ОДМ 218.5.006- |
|
||
|
ширине образца, кН/м, возникающее при отно- |
|
||||
|
|
2010 |
|
|||
|
|
деформац ε = 2%, не менее |
|
|
||
|
|
|
|
|
||
|
Длительная прочность, % от кратковремен- |
70 |
ОДМ 218.5.006- |
|
||
|
ной прочности RLR (RTR), не менее |
2010 |
|
|||
|
|
|
||||
|
Относительная прочность узловых соедине- |
|
DIN EN ISO 10321, |
|
||
|
ний геосетки RJR, % от прочности рё ер, не ме- |
5 |
ОДМ 218.5.006- |
|
||
|
нее |
|
|
|
2010 |
|
|
|
2. Стойкость к агрессивным воздействиям |
|
|||
|
Уменьшение прочности RLR (RTR) после на- |
10 |
О М 218.5-001- |
|
||
|
грева до 160 оC (теплостойкость), %, не более |
2009 |
|
|||
|
Потеря прочности (повреждаемость) мате- |
|
О М 218.5-001- |
|
||
|
риала в процессе укладки асфальтобетона, % от |
40 |
|
|||
|
2009 |
|
||||
|
исходной прочности RLR (RTR), не более |
|
|
|||
|
|
|
|
|||
|
Уменьшение исходной прочности RLR (RTR) в |
|
О М 218.5.006- |
|
||
|
25 |
2010, |
|
|||
|
|
|
|
|
||
|
агрессивных средах, %, не более |
|
И |
|
||
|
|
|
|
|
EN 14030 |
|
|
Д |
|
||||
|
Уменьшение исходной прочности RLR (RTR) |
|||||
|
после 25 циклов замораживания – оттаивания, |
10 |
О М 218.5-001- |
|
||
|
%, не более |
|
|
2009 |
|
|
|
|
|
3. Геометрические параметры |
|
|
|
|
Размер ячеек геосетки, мм, не менее: |
|
|
|
||
|
|
для мелкозернистого асфальтобетона |
25 х 25 |
ГОСТ 29104.7 |
|
|
|
|
для крупнозернистого асфальтобетона |
35 х 35 |
|
|
|
|
Ширина рулона, м |
|
От 1,5 до 4 |
ГОСТ 3811 и |
|
|
|
|
|
|
От 20 до |
||
|
Длина материала в рулоне, м |
ГОСТ 6943.17 |
|
|||
|
100 |
|
||||
|
|
|
|
|
|
180
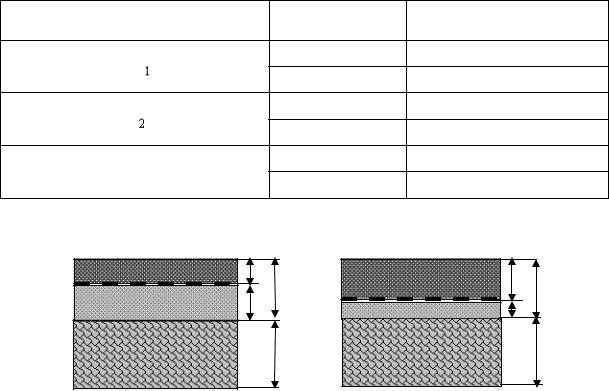
Документ [100] регламентирует правила выбора местоположения |
||||||
геосинтетического материала, армирующего асфальтобетонный слой. |
||||||
огласно этим правилам при необходимости воспринимать темпера- |
||||||
турные напряжения армируется верхняя часть слоя, а если требуется |
||||||
повышать сопротивление растягивающим напряжениям при изгибе от |
||||||
транспортной нагрузки, то следует армировать нижнюю часть. Эти |
||||||
конструктивные решения обозначены аббревиатурой ТМП (темпера- |
||||||
тура) и НГР (нагрузка). |
|
|
|
|
|
|
Для выбора конструктивного решения по армированию асфаль- |
||||||
тобетонного слоя даны таблицы и схема [100, табл. 1, рис. 3]. Эти |
||||||
данные пр ведены в табл. 63 и на рис. 81. |
|
|
||||
С |
|
|
|
|
Таблица 63 |
|
|
|
|
|
|
|
|
Выбор |
|
армирующей прослойки по глубине |
||||
Дорожно-кл мат ческая зона |
|
|
h /h0 |
Тип конструктивного |
||
|
подзона |
|
|
|
решения |
|
|
|
|
|
|
||
|
I, II |
|
|
< 1 |
|
ТМП |
|
|
|
|
|
|
|
местоположения |
|
≥ 1 |
|
НГР |
||
|
|
|
|
|
||
|
II |
|
|
< 0,9 |
|
ТМП |
|
|
|
≥ 0,9 |
|
НГР |
|
|
|
|
|
|
||
|
III |
|
|
< 0,8 |
|
ТМП |
|
|
|
≥ 0,8 |
|
НГР |
|
|
|
|
|
|
||
а) |
|
|
|
б) |
|
|
1 |
бА |
|
||||
|
h1 |
h∑ |
1 |
|
h1 h∑ |
|
2 |
|
h2 |
|
|||
3 |
|
|
2 |
|
h2 |
|
|
|
|
3 |
|
||
|
|
|
|
|
|
|
4 |
|
|
h0 |
4 |
|
h0 |
|
|
|
Д |
|||
Рис. 81. Типы принципиальных конструктивных решений: а – решение типа |
||||||
ТМП; б – решение типа НГМ; 1 –верхний слой покрытия толщиной h1; 2 – арми- |
||||||
рующая прослойка; 3 – нижний слой покрытия толщиной h2 |
из новой или реге- |
|||||
|
|
|
|
|
И |
|
нерированной смеси; 4 – существующее покрытие или несущее основание |
При применении для армирования асфальтобетонных слоев плоской георешеткой (геокомпозит) документ [100] регламентирует три различные схемы армирования: сплошную, участковую и комбинированную. При сплошном армировании полосы геосинтетического ма-
181

териала укладываются равномерно с необходимым перекрытием по- |
||||||
лос по всей длине участка производства работ. При участковом арми- |
||||||
ровании полосы материала укладываются либо над трещинами, либо |
||||||
над швами. Этот способ применим при ремонте существующих ас- |
||||||
фальтобетонных покрытий и при устройстве асфальтобетонного по- |
||||||
крытия на сборном или монолитном бетонном или железобетонном |
||||||
основании. Комбинированный способ состоит в применении сплош- |
||||||
ного арм рован я с дополнительной укладкой полос армирующего |
||||||
материала над трещ нами или швами. Схемы армирования приведе- |
||||||
ны на р с. 82 [100, р с. 2]. |
|
|
|
|
|
|
С |
2 |
|
|
2 |
|
1 |
|
|
|
|
|||
3 |
|
|
|
|
|
|
и |
|
|
|
|
2 |
|
|
в |
|
б |
|
|
|
а |
|
|
|
|
||
Рис. 82. Схемы укладки геосетки (геокомпозита): |
|
|
||||
а – сплошная; б – участковая; в – ком инированная; 1 – «старое» покрытие со |
||||||
швами; (трещинами); 2 – полосы геосетки; 3 – полотно геосетки |
|
|||||
Способ сплошного армирования рекомендуется применять в I и II |
||||||
дорожно-климатических зонах при капитальном ремонте усовершен- |
||||||
бА |
|
|
|
|||
ствованных покрытий [100]. Кроме того, для капитального ремонта и |
||||||
ремонта железобетонных и цементобетонных покрытий дорог в I ДКЗ |
||||||
рекомендован комбинированный способ армирования [100]. Комби- |
||||||
нированный способ применяют при ремонте асфальтобетонных по- |
||||||
|
|
|
Д |
|
||
крытий в случаях наличия поперечных и косых трещин, расположен- |
||||||
ных на расстоянии менее 10 м друг от друга [100]. Участковый способ |
||||||
армирования рекомендован для усиления усовершенствованных по- |
||||||
крытий с поперечными трещинами, расположенных на расстоянии |
||||||
более 10 м друг от друга [100]. Этот способ пригоден для усиления |
||||||
|
|
|
И |
|||
асфальтобетонных покрытий с центральной (осевой) и боковыми |
||||||
продольными трещинами [100]. Область применения участкового |
||||||
способа армирования ограничивается районами с мягким климатом. В |
||||||
I и II ДКЗ этот способ применять не рекомендуется потому, что после |
||||||
суровой зимы трещины на покрытии появляются рядом с полосами из |
||||||
армирующего материала [100]. |
|
|
|
|
|
182
Работы по устройству асфальтобетонных покрытий и оснований, армированных геосинтетическими материалами выполняются в соот-
ветствии с СП 78.13330.2012 [7] и ОДМ 218.5-001-2009 [100]. Соглас-
но указаниям документа [100] перед началом основных работ по устройству армированных асфальтобетонных слоев выполняют весь комплекс внеплощадочных и внутриплощадочных подготовительных работ. остав внеплощадочных работ зависит от конкретных условий, но наиболее важными являются работы [100]:
С– подбору состава асфальтобетонной смеси;
– по своевременному входному контролю всех поступающих ма-
териалов;
– отладке реж мов ра оты машин и механизмов, в том числе асфальтобетонного завода;
– устройству подъездных дорог;
– определен ю тре уемого для подвоза смеси и рулонов геосин-
|
кол чества самосвалов и грузовых автомобилей; |
тетики |
|
– определен ю тре уемого количества машин и механизмов не- |
|
обход мых для устройства армированного асфальтобетонного слоя. |
|
Основными видами внутриплощадочных работ являются [100]: |
|
– обеспечение проезда транзитного транспорта; |
|
– подготовка и настройка дозирующих устройств автогудронатора; |
|
– определение, а при нео ходимости корректировка, нормы рас- |
|
хода вяжущего, необходимой для качественного крепления геосинте- |
|
тики; |
бА |
|
|
– проверка работы машины для распределения геосинтетики; |
|
– подбор дюбелей, применяемых для крепления геосинтетическо- |
|
го материала, и проверка работы специального степлера; |
|
– пробная укладка и уплотнение асфальтобетонной смеси, в про- |
|
цессе которых подбирается составДзвена катков и проверяется отсут- |
|
ствие сдвигов геосинтетического армирующего материала от воздей- |
ствия гусениц укладчика и колес самосвалов.И В процессе основных работ выполняют:
– подготовкуоснования,накоторомустраиваетсяармированныйслой;
– розлив вяжущего;
– расстилание геосинтетических полотен с необходимым перекрытием, а также их приклеиванием к вяжущему материалу и креплением дюбелями к основанию;
– повторный розлив вяжущего материала;
– устройство слоя на геосинтетическом материале.
183
Работы по устройству армированного асфальтобетонного покрытия или основания выполняют на одной сменной захватке, длину которой вычисляют в зависимости от производительности и количества ведущих машин в отряде [100]. В качестве ведущей машины рекомендуется принимать асфальтоукладчик или асфальтобетонный за-
Свод, но допускается в качестве ведущих машин принимать катки или самосвалы [100].
Работы нач нают с подготовки основания, которое очищают от пыли грязи, а при ремонте существующего асфальтобетонного по- торамикрытия в нем заделывают дефекты. Выполнив очистку, необходимо незамедл тельно про звести розлив вяжущего. Определяющими факвыбора в да вяжущего являются погодные условия, вид геосинтет ческого матер ала, применяемого для армирования, и свойст-
ва нижележащегонеобходимостьюслоя. При устройстве армирующей прослойки между двумя свежеуложенными асфальтобетонными слоями подгрунтов-
ку выполняют в лю ом случае, даже если перерыв между устройством слоев составляет 1–2 смены [100]. Такое требование обуславли-
–необходимостьюАнадежного крепления армирующего материала
книжнему слою для предотвращения его сдвига и образования волн при движении самосвалов и воздействииБНДгусениц укладчика.
В целях обеспечения надежного приклеивания геосетки к поверхности асфальтобетонного слоя рекомендуется применять вязкие битумы марок БНД 40/60, БНД 60/90 или 90/130, а при более низких тем-
пературах рекомендуется использовать менее вязкий битум [100]. Температура битума при его распределении должнаИбыть не менее 120–150 о С [100]. Если вязкость применяемого битума велика о чем свидетель-вается:можность его применения следует проверять [100]. В случае использо-
вания разжиженного битума геосинтетику укладывают до испарения разжижителя, а асфальтобетонную смесь – после его испарения. Для подгрунтовки применяют быстрораспадающиеся битумные или полимербитумные эмульсии (классов ЭБК-1, ЭБПК-1, ЭБК-2 и др.). Их применяют при пониженной температуре воздуха, необходимости укладки
184
армирующего материала на влажное основание, а также при использовании геокомпозитов с геотекстильным материалом, не обработанным вяжущим. Преимущество применения битумных эмульсий состоит в их более равномерном распределении и возможности исправления дефектов укладки геосетки до распада эмульсии. Недостатком использования эмульсии является необходимость ожидания ее распада, что задерживает производство работ [100].
Расходу вяжущего необходимо уделить особое внимание. Недос-
таток вяжущего в отдельных местах приводит к ослаблению сцепле- |
|
ния с основан ем, а это приведет к образованию сдвигов геосетки в |
|
процессе последующей укладки асфальтобетонной смеси. Избыток |
|
С |
к прилипанию геосетки к шинам самосва- |
вяжущего может пр |
|
лов, что может пр |
к повреждению геосинтетического материа- |
ла. Рекомендуемая норма расхода битума составляет 0,9–1,2 л/м2, а |
|
вести |
|
бА |
эмульс – 1,1–1,5 л/м2. Согласно указаниям [100] повышенные расходы б тума пр н маются:
– при укладке арм рующего материала на существующее покрытие со знач тельным количеством мелких дефектов, не устранённых на предыдущем этапе ра от (мелкие трещины и т.п.);
–значительной шероховатости существующего покрытия;
–использовании геосетки или геокомпозита, не обработанных вяжущим в процессе их изготовления.
В местах торможения транспортаДи на участках с крутыми уклонами, где возможно возникновение значительных сдвигающих усилий от воздействия транспортных средств норму розлива битума и эмульсии рекомендуется снижать, но не менее чем до 0,7 л/м2 [100].
СТО-ГК «Трансстрой»-008-2007 рекомендует выполнять подгрунтовку асфальтобетонного слоя битумной эмульсиейИ, которую разливают в два приема[112].Согласнотребованиям[112,п.5.5]первыйрозливвыполняют при расходе битумной эмульсии 0,6 л/м2. Если покрытие обладает повышенной шероховатостью,то нормурозливанужно увеличить до 0,7 л/м2. О недостаточном количестве эмульсии, применяемой при подгрунтовке перед креплением геосетки, свидетельствует отсутствие характерного блеска обработанной поверхности. После первого и повторного розлива битумной эмульсии предусматривают технологический перерыв, продолжительность которого регламентирована [112, табл. 5.9] и приведена нами в табл. 64. В этой таблице содержатся все технологические операции, регламентируемые СТО-ГК «Трансстрой»-008-2007 [112] при армировании асфальтобетонныхслоевиданапродолжительностьперерывов.
185

Таблица 64
Технологические операции и продолжительность технологических перерывов по СТО-ГК «Трансстрой»-008-2007 [112, табл. 5.9]
|
Технологическая операция |
Разрыв во времени, ч |
|
|
не менее |
не более |
|
|
|
||
|
Подготовка поверхности основания |
– |
– |
С |
1 |
12 |
|
|
Заливка трещин герметизирующим материалом |
||
|
Первичный розлив битумной эмульсии |
– |
2 |
|
Укладка сетки, ее натяжен е и крепление |
2 |
6 |
|
Вторичный розл в б тумной эмульсии |
– |
2 |
|
Розлив |
1,5 |
8 |
|
Укладка вышележащего асфальтобетонного слоя |
Розл в вяжущего при подгрунтовке поверхности выполняют автогудронатором, предварительно отрегулировав и очистив его сопла.
за один ли два пр ема [100]. Ширина розлива вяжущего должна
быть на 10–15 см ольше ширины укладываемой полосы геосетки.
Количество розл вов назначают в зависимости от размеров ячейки
геосетки. Розл в вяжущего за один прием делают в том случае, если |
|
|
А |
площадь занятая ре рами сетки, составляет менее 25–30%, а открытая |
|
площадь, |
ячейками сетки, – более 70–75% [100]. В других |
прообразуемаязводят до после укладки геосинтетического материала
случаях выполняют розлив в два приема. При первом розливе на покрытие подают 70% от о щей нормы розлива битума (эмульсии), а
при втором – 30% [100]. ПослеДукладки геосетки розлив вяжущего
повторяют при тех же правилах, соблюдая норму расхода и количество розливов [100].
Доставленные на место производства работ рулоны геосинтетического материала в упаковке складируют на обочине [100]. В случае необходимости обеспечения ширины укладкиИрулоны можно разрезать [100]. Для этого рекомендуется применять нарезчик швов (раздельщик трещин) или другим средством малой механизации.
Сразу после нанесения битумной или эмульсионной подгрунтовки начинают укладывать армирующую прослойку. Укладку выполняют в продольном направлении. Уложенный на покрытие рулон ориентируют по краю подстилающего слоя и разматывают на 10 – 15 м [100]. Согласно рекомендациям СТО-ГК «Трансстрой»-008- 2007 [112, п. 5.11] край геосетки, расположенный в начале укладки, рекомендуется закрепить дюбелями. При ширине сетки 1 м рекомендуемое количество дюбелей составляет 4, а если ширина сетки больше 1 м, то дюбели располагают на расстоянии 50–60 см друг от друга.
186

При укладке геосинтетического материала следят, чтобы не было перекоса, а край геосетки совпадал с краем подстилающего слоя.
Геосетку разматывают звеном рабочих, которое в зависимости от ширины рулона может состоять из 2–4 человек (см. рис. 83, а и б) [100]. При небольшой массе рулона, в имеющееся в нем отверстие
Спродевается металлическая труба, позволяющая выполнять укладку двумя пешими рабочими, которые удерживают рулон на весу (рис. 83, в). Для увел чения производительности можно выполнять укладку геос нтет ческого материала путем параллельного раскаты-
ваниядвух трех рулонов (рис. 83, г) [100]. бА Д
Рис. 83. – Иллюстрация укладкиИгеосетки:
а – раскатка рулона, уложенного на покрытие, двумя рабочими; б – раскатка рулона, уложенного на покрытие, четырьмя рабочими; в – раскатка рулона, перемещаемого двумя рабочими на весу;
г – одновременная раскатка двух рулонов
Существуют различные специальные навесные механизмы на тракторы, автомобили и тягачи, позволяющие укладывать геосетку с
187
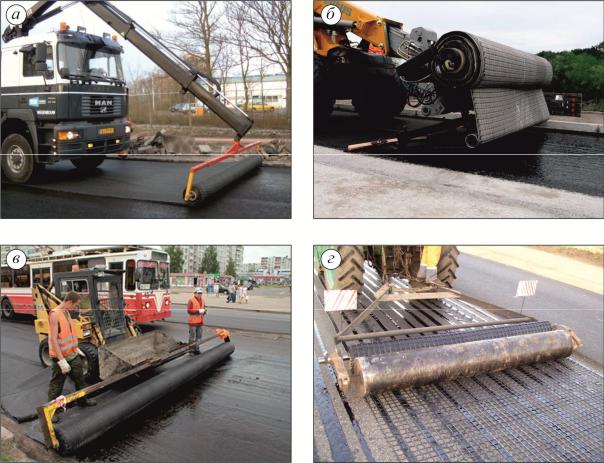
высокой производительностью. Такие механизмы представляют собой металлические рамы разнообразной конструкции, снабженные валом, который продевают сквозь отверстие в рулоне геосинтетического материала. Размеры этого вала с учетом боковых упоров, предназначенных для фиксации положения рулона, должны соответство-
Свать ширине рулона геосетки. Выполнение этого требования позволяет избежать перекосов расстилаемого полотна при его укладке. Механизмы крепятся перед машиной (рис. 84, а, б и в) или позади трактора (рис. 84, в). В первом случае дорожная машина производит укладку
основан ю, а геос нтет ка расстилается позади машины.
геосеткиперед собой, ее колеса перемещаются по геосинтетическому материалу. Во втором случае машина двигается по подгрунтованному
бА Д
Рис. 84. – Навесное оборудование для укладкиИгеосеток:
а– монтаж перед автомобилем; б – монтаж перед трактором;
в– монтаж перед мини-погрузчиком; г – монтаж позади трактора
Во избежание неплотного прилегания геосинтетического материала к основанию и непрочного сцепления с ним
188
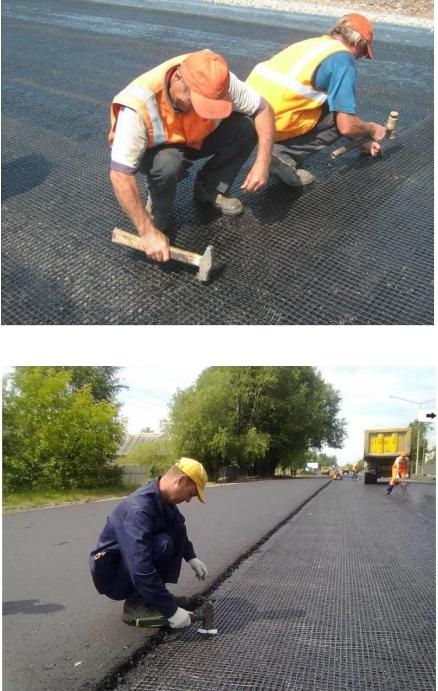
СТО-ГК «Трансстрой»-008-2007 [112, п. 5.6] рекомендует при укладке геосетки подкатывать ее ручным катком.
После раскатки рулона на 2–3 м ее натягивают вручную, проверяя отсутствие волн и складок, боковые стороны крепят к основанию забивкой дюбелей. Дюбели забивают заподлицо с поверхностью осно-
Свания. Иллюстрации крепления начального края и боковых краем геосетки приведены на рис. 85 и 86.
и
бАРис. 85. Крепление начальногоДкрая геосетки на поперечном стыке полотен
И
Рис. 86. Крепление бокового края геосетки
189
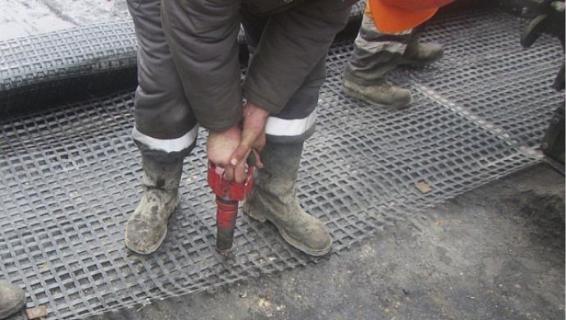
В |
соответствии с рекомендациями «Трансстрой»-008-2007 |
[112, п. 5.12] необходимо применять дюбели ДТП или ДГПШ, длина |
|
и диаметр которых составляет 40-60 мм и 3,7-4,5 мм соответственно, |
|
шайбы |
стальные диаметром не менее 36 мм и строительно- |
монтажный пистолет типа ПЦ-84 с патронами Д3 или Д4. Иллюстра- |
|
С |
|
ция крепления края геосетки при помощи строительно-монтажныого |
|
пистолета ПЦ-84 приведена на рис. 87. |
|
и |
|
|
бА |
|
Д |
|
Рис. 87 – Крепление бокового края геосетки |
|
при помощи строительно-монтажного пистолета ПЦ-84 |
Выполнив крепление геосинтетической армирующей сетки к асфальтобетонному основанию, производят второй розлив битума или битумной эмульсии [100, 112]. При этом соблюдаютИвсе правила подгрунтовки поверхностей автогудронатором.
Рекомендации [100, 112] для предохранения геосетки от возможных повреждений в процессе устройства армированной конструкции асфальтобетонного покрытия регламентируют применять с помощью ряда мероприятий. Транспортные и дорожные машины не должны производить резких ускорений и торможений, следует избегать маневров транспорта на геосетке [112, п. 5.14]. В целях защиты геосинтетики рекомендуется [112, п. 5.14]:
1. Выполнять работы с использованием укладочного комплекта с боковой загрузкой и специальными перегружателями асфальтобетонной смеси.
190
2. Выполнять укладку геосетки в направлении, противоположном направлению движения технологического потока по устройству асфальтобетонного слоя.
3. Устраивать поверхностную обработку из щебня, обработанного битумом (черный щебень), фракции 5–10 мм с прикаткой легкими катками.
4. Укладывать слой из песчаного асфальтобетона типа Г толщиной
2 см.
5. Устанавл вать временные трапы или щиты над уложенными, за-
крепленными |
втор чно обработанными битумной эмульсией по- |
|
лотнами геосетки. |
||
С |
||
Аналог чные рекомендации приведены в документе [100]. |
||
Устройство асфальто етонного слоя или слоев выполняется в соот- |
||
ветств с |
|
правилами производства работ с нефтяными ас- |
|
|
смесями или их особыми разновидностями. |
фальтобетонными |
||
3.5. Устройство усилений из асфальтобетона, армированного |
||
|
|
металлическими сетками |
|
общ |
|
|
|
А |
Для армирования асфальто етонных покрытий и оснований применяются металлические сетки. Правила проектирования слоев усиления, требования к металлическимДсеткам и технологии армирования устанавливаются в документе ОДМ 218.3.041–2014 [114].
Согласно указаниям ОДМ 218.3.041–2014 [114, п. 4.1] сетку проволочную двойного кручения, имеющую шестиугольные ячейки, необходимо изготавливать из проволоки с антикоррозийным покрытием. В качестве материала антикоррозийногоИпокрытия используется цинк (Ц) или цинк с алюминием и мишметаллом (ЦАММ) [114, п. 4.2]. Антикоррозийное покрытие из цинка должно соответствовать требованиям ГОСТ Р 50575–93 [115], а из сплава цинка с алюминием и мишметаллом – ГОСТ Р 51285–99 [116]. Антикоррозийное покрытие должно плотно прилегать к проволоке, причем адгезия должна быть не менее оговоренной в ГОСТ 11508–74 [59].
Для оценки качества адгезии антикоррозийного покрытия и стальной проволоки ОДМ 218.3.041–2014 [114, п. 4.1] рекомендуется выполнение простого теста. Суть опыта состоит в том, что оцинкованную проволоку нужно навинтить на стержень, диаметр которого должен быть в четыре раза больше диаметра проволоки. При навива-
191
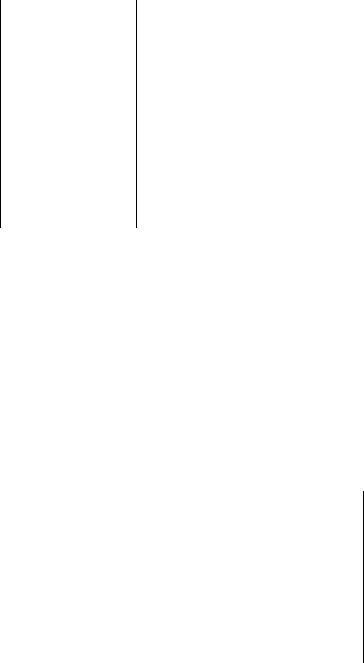
нии проволоки на стержень нужно сделать 6 витков. После навинчивания проволоку осматривают и визуально фиксируют наличие растрескиваний или отслоение чешуек покрытия, которые можно удалить пальцами.
|
Диаметр проволоки, размер ячейки сетки и диагонали ячейки |
|||||
С |
|
|
|
|
||
|
должны соответствовать требованиям [114, 116]. Эти требования при- |
|||||
|
ведены в табл. 65. |
|
|
|
Таблица 65 |
|
|
Требован я к геометрическим характеристикам ячеек сетки |
|||||
|
|
|
|
[114, табл. 4.1] |
|
|
|
ячейки |
|
Размер сечения по- |
Размер диагонали, |
||
|
Размер |
, мм |
Предельное от- |
|||
|
|
|
клонение, % |
|
перечного прута, мм |
мм |
|
60 |
|
-4…+18 |
|
2,2 |
80 |
|
|
|
2,4 |
|||
|
|
бА |
|
|||
|
|
|
|
2,7 |
|
|
|
80 |
|
-4…+16 |
2,2 |
100 |
|
|
|
|
2,4 |
|||
|
|
|
|
|
2,7 |
|
|
100 |
|
-4…+16 |
2,2 |
120 |
|
|
|
|
2,4 |
|||
|
|
|
|
|
2,7 |
|
Согласно классификации ОДМ 218.3.041–2014 [114, п. 4.5] сетку подразделяют на два типа: легкий и тяжелый. ля изготовления сетки легкого типа применяют проволоку диаметром 2,2 мм, а сетку тяжелого типа изготавливают из проволоки диаметром 2,4 или 2,7 мм. Требования к показателям технических характеристик сетки регламентированы ОДМ 218.3.041–2014 [114, табл. 4.2] и приведены в табл. 66.
|
|
|
|
|
Таблица 66 |
|
|
|
|
Д |
|||
Требования к техническим характеристикам металлических сеток, |
||||||
применяемых для армирования асфальтобетона [114, табл. 4.2] |
||||||
Тип |
Диаметр |
Размер по- |
Размер |
Нагрузка при разрыве, Кн/м |
|
|
проволоки, |
перечного |
ячейки, |
Ипродольная поперечная |
|
||
сетки |
|
|||||
|
мм |
прута, мм |
мм |
|
|
|
Легкий |
2,2 |
6,0 2,0 |
60 80 |
>32 |
>32 |
|
80 100 |
|
|||||
|
|
|
100 120 |
|
|
|
Тяжелый |
2,4…2,7 |
7,0 3,0 |
60 80 |
>40 |
>50 |
|
80 100 |
|
|||||
|
|
|
100 120 |
|
|
|
192
Армирование асфальтобетоны выполняют при усилении дорожных одежд. В этом случае выделяют три способа усиления ОДМ 218.3.041-2014 [114, п. 5.2]. Расчет усиления выполняют по критериям упругого прогиба, сопротивления усталостному разрушению от растяжения при изгибе и сдвигоустойчивости материалов конструктивных слоев и грунта земляного полотна по методикам, огово-
ренным в ОДН 218.046-01 [117] и ОДМ 218.3.041–2014 [114, разд. 7].
Технолог я арм рования асфальтобетона при усилении нежестких дорожных одежд включает в себя работы по подготовке поверхности, на которую про зводится укладка, по укладке стальной сетки и
устройству новых асфальтобетонных слоев. |
|
С |
|
огласно рекомендациям ОДМ 218.3.041–2014 [114, п. 8.5] при |
|
укладке сетки по существующему асфальтобетонному покрытию оно |
|
должно быть ч стым, не иметь дефектов в виде трещин с шириной |
|
раскрыт я |
5 мм, отдельных раковин, выбоин, шелушения и |
разрушен й о ладать ровностью, соответствующей требо- |
|
прочих |
|
ваниям СП 78.1330.2012 [7]. В случае выявления значительных де- |
|
формац й |
разрушен й существующего покрытия предусмотреть |
устранение неровностей фрезерованием и устройство выравнивающе- |
го слоя ОДМ 218.3.041-2014 [114, п. 8.6]. |
|
|
более |
|
|
Технология армировании асфальтобетонных слоёв стальными |
||
сетками включает в се я следующие операции О М 218.3.041–2014 |
||
[114, п. 10.2]: |
|
|
- очистка покрытия от загрязнений; |
|
|
|
А |
|
- ликвидация дефектов асфальтобетонного покрытия (ремонт выбо- |
||
ин, герметизация трещин и др.); |
|
|
- при необходимости фрезерование покрытия или устройство вы- |
||
равнивающего слоя; |
|
|
- доставка и укладка стальной сеткиДв проектное положение; |
||
- прикатка сетки пневматическим катком; |
|
|
- закрепление начального поперечного прута каждого рулона сетки |
||
к основанию или нижнему слою покрытия; |
И |
|
|
|
- нанесение литой эмульсионно-минеральной смеси в соответствии с рекомендациями [29];
- распределение и уплотнение асфальтобетонной смеси слоями необходимой толщины.
Организацию работ по укладке стальной сеткой и устройству слоя из асфальтобетонной смеси выполняют так, чтобы все работы
193
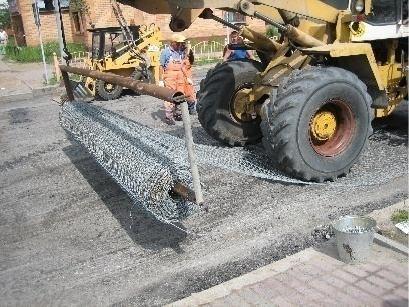
были произведены в течение одной смены ОДМ 218.3.041–2014 [114, п. 10.3].
Для очистки существующего покрытия от пыли и грязи работы выполняют с использованием механических щёток, сжатого воздуха от компрессоров, поливомоечных машин ОДМ 218.3.041–2014
С[114, п. 10.5].
Дефекты существующего покрытия, мешающие плотному контакту стальной сетки с основанием и сцеплению с асфальтобетонным слоем ус лен я, устраняют любой пригодной для этой цели техноло-
укладкигией ОДМ 218.3.041–2014 [114, п. 10.6].
Укладка стальной сетки может осуществляться средствами механизации, в качестве которых применяют механические укладчики, фронтальные погрузч ки, о орудованные специальной штангой, автомоб лем-бАсамосвалом, сна женным прицепом-разматывателем ОДМ 218.3.041–2014 [114, п. 10.8]. Один из вариантов механической
стальной сетки представлен на рис. 88.
Д
Рис. 88. – Иллюстрация укладки стальнойИсетки
Укладка стальной сетки выполняется параллельно оси дороги с недопущением образования волн и складок, внешняя сторона сетки ориентируется наверх [114, п. 10.8]. Раскатываемые из двух или более рулонов полосы сетки должны перекрывать друг друга на 6 – 16 см в продольном направлении [114, п. 10.8]. Также необходимо обеспечивать перекрытие полос в поперечном направлении, раскатываемых из
194
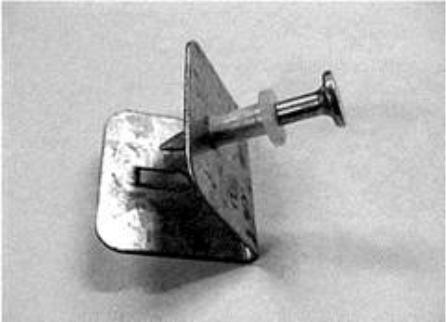
двух смежных рулонов. Величина поперечного перекрытия раскатанных лент должна составлять 12 – 30 см [114, п. 10.8].
Обеспечивая перекрытие, необходимо, чтобы не было нахлеста укрепляющих плоских прутьев одной сетки на такие же прутья второй сетки. При разматывании стальной сетки на кривых нужно выре-
Сзать соответствующий кусок сетки с внутренней стороны кривой поворота и методом наложения сформировать криволинейный участок. Для резан я сетки пр меняют ручные или электрические сетки.
После укладки сетку прикатывают к нижележащей поверхности
забиваемыепневмоколесным катком, выполняя разглаживание сетки в направлении от серед ны рулона к его краям. Полный контакт сетки с подсти-
лающей поверхностью о еспечивается при четырех проходах катка по одному следу [114, п. 10.9].
тальнуюбАсетку, плотно прилегающую к поверхности нижележащего слоя, нео ход мо закрепить, применяя специальные анкеры, подст лающую поверхность при помощи монтажного пистолета ли газового гвоздеза ивного пистолета [114, п. 10.10]. В
качестве анкеров можно применить дюбель, гвозди длиной не менее 40 мм и пластины размером 30 80 мм, нарезанные из стального оцинкованного листа. Можно использовать крепежные элементы, представленные на рис. 89.
Д И
Рис. 89. – Иллюстрация крепежного элемента [114, рис. 10.6]
195
В качестве анкеров можно применять гвоздь или арматуру с одним загнутым концом, обеспечивающим надежный контакт сетки с подстилающей поверхностью [114, п. 10.10].
По уложенной и закрепленной анкерами сетке выполняют дополнительное крепление, которое производится при помощи эмульсион- но-минеральной смеси. Эмульсионно-минеральную смесь укладывают, подбирая ширину укладки так, чтобы смесь не попадала на продольные сопряжен я полос сетки [114, п. 10.11]. Продольный нахлест полос сетки перекрывается эмульсионно-минеральной смеси при последнем проходе. Слой из эмульсионно-минеральной смеси не нуж-
дается в уплотнен |
[114, п. 10.12]. Применение эмульсионно- |
|
С |
|
|
минеральной смеси о еспечивает надежную гидроизоляцию подсти- |
||
лающих слоев дорожной одежды. Распад битумной эмульсии проис- |
||
ходит по |
стечен |
нескольких минут после ее приготовления, а для |
формирован я смеси нео ходимо время, которое составляет от |
||
1 до 3 ч. |
нео ход мости формирование смеси можно ускорить, |
|
При |
||
для этого после начала формирования смеси выжидают некоторое |
||
время пр катывают слой пневматическим катком [114, п. 10.12]. В |
||
период достижения формирования слоем из эмульсионно- |
||
минеральной смеси движение транспорта по нему не допускается. |
||
После формирования движение по слою возможно, но с ограничени- |
||
ем скорости до 30 км/ч [114, п. 10.12]. |
||
|
бА |
В случаях, когда невозможноДвыполнить крепление сетки эмуль- сионно-минеральной смесью, допускается фиксировать сетку анкерами, размещая их по всей площади сетки на расстоянии 1 м друг от друга в обоих направлениях (продольном и поперечном). При такой фиксации сетки движение по ней транспорта запрещено, а технологические машины могут передвигаться толькоИна малой скорости [114, п. 10.13]. Если крепление сетки выполнено анкерами, то дальнейшей технологической операцией является подгрунтовка, выполняемая розливом битумной эмульсии с расходом 0,7 – 1,2 кг/м2. При использовании для крепления сетки эмульсионно-минеральной смеси подгрунтовка ее поверхности не требуется [114, п. 10.13].
Укладка асфальтобетонной смеси выполняется по традиционной технологии, но при соблюдении водителями самосвалов и оператором асфальтоукладчика мер, оговоренных в ОДМ 218.3.041–2014 [114, п. 10.14], необходимых для сведения к минимуму сдвигающих усилий, возникающих в сетке.
196
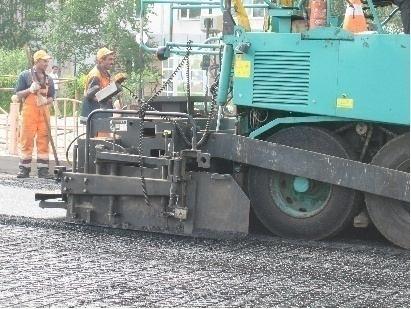
Укладка асфальтобетонной смеси и ее уплотнение звеном катков выполняются в соответствии с требованиями СП 78.13330.2012. Иллюстрация укладки смеси по сетке, закрепленной эмульсионноминеральной смесью, приведена на рис. 90.
Си
РисбА. 90. Укладка асфальто етонной смеси по стальной сетке, закрепленной слоем из эмульсионно-минеральной смеси
3.6. Устройство усиления изДасфальтогранулобетонной смеси
при помощи холодного ресайклинга
В настоящее время при реконструкции и капитальном ремонте дорожных одежд все шире применяются технологии холодного ресайклинга, а при строительстве дорожных одеждИстали внедрять технологии стабилизации грунтов вяжущими материалами.
Технология холодного ресайклинга выполняется как на заводе, так и непосредственно на дороге. В обоих случаях используется гранулят, полученный фрезерованием существующей дорожной одежды. При этом оказывается возможным фрезеровать как асфальтобетонное покрытие, так и покрытие совместно с основанием. Глубина фрезерования ограничивается только возможностями применяемого ресайклера или используемой фрезы. В качестве вяжущих материалов обычно применяют цемент, известь, жидкий битум, вспененный битум и битумную эмульсию. Таким образом, по виду вяжущего технология холодного ресайклинга практически не встречает ограничений.
197
При выполнении холодного ресайклинга по любой из технологий возможно добавление различных регенерирующих добавок нового
асфальтобетона или черного щебня. Кроме того, коррекцию зернового состава асфальтобетонного гранулята можно корректировать добавкой любых фракций щебня. Соблюдение зернового состава, точное дозирование вяжущих и качественное выполнение технологических операций позволяют выполнять устройство конструктивного слоя с высок ми параметрами прочности и деформируемости материала.
СХолодный ресайкл нг может производиться на заводе, когда материал старой дорожной одежды перевозится в центральный отвал, из которого он заб рается для о ра отки, например, смесителем прину-
дительногославливается транспортными затратами на перевозку гранулята к заводу готовой смеси на дорогу. При ресайклинге на месте транс-
действ я, ли на месте – с помощью ресайклера [118]. Первый вар ант является олее дорогим, что прежде всего обу-
работы статистический раз росАпоказателей прочности и деформируемости.
портные |
не выполняются. При приготовлении смеси на заводе |
она получается |
олее однородной, вследствие чего имеет меньший |
Несмотря на отличия в качестве смеси и различной стоимости оба варианта широко применяются в дорожном строительстве.
Сравнивая технологию холодного ресайклинга, можно выделить
2. В большинстве случаев обработкаДучастка выполняется за один проход, что существенно сокращает длину частного потока и минимизирует сроки ограничения движения.
ряд преимуществ:
1. За счет использования асфальтобетонного гранулята (АГБ) отпадает необходимость в закупке большого количества новых материалов. В результате уменьшаются расходы, связанные с добычей,
переработкой, доставкой этих материалов. |
И |
|
3. При холодном ресайклинге возможно частично исправить поперечное сечение дорожного покрытия и дефекты продольного профиля.
4. Эта технология позволяет обрабатывать верхний слой совместно с нижним, получая из них один слой, обработанный вяжущим материалом.
Метод холодного ресайклинга на стационарном или мобильном заводе состоит в приготовлении новой холодной смеси из АГБ и вяжущего (битумной эмульсии или вспененного битума). В смесь может
198

быть добавлен обновляющий агент для улучшения вязкости старого битума, а также новый заполнитель для улучшения общих эксплуатационных качеств. Полученный холодный материал используется в качестве стабилизированного слоя основания дорожной одежды.
Технология состоит в выполнении ряда операций. |
||
С |
|
|
1. |
Очистка существующего покрытия от пыли и грязи. |
|
2. |
Фрезеровка существующего покрытия и погрузка АГБ в само- |
|
свал. |
|
|
3. |
Транспорт ровка АГБ транспортируют на завод. |
|
приведены |
|
|
4. |
Пр готовлен е смеси требуемого состава на заводе. |
|
5. |
Транспорт ровка приготовленной смеси на дорогу. |
|
6. |
Устройство конструктивного слоя дорожной одежды в соот- |
|
ветств |
с трад ц онной для этой смеси технологией. |
|
|
бА |
|
На р с. 91 92 |
иллюстрации фрезерования сущест- |
|
вующего асфальто етонного покрытия с погрузкой АГБ в самосвал. |
||
Рис. 91. Фрезерование покрытия |
Д |
|
Рис. 92. Погрузка АГБ в самосвал |
||
|
фрезой Wirtgen W-130 F |
фрезой Wirtgen |
Материал существующего предварительноИочищенного от пыли и грязи асфальтобетонного покрытия фрезеруют и одновременно грузят в автомобиль-самосвал. Фрезеровку выполняют продольными проходами фрезы. Первый проход выполняют у оси проезжей части.
Приготовление смеси на стационарном или мобильном заводе имеет ряд преимуществ, связанных с возможностью тщательного контроля всех параметров и при возникновении необходимости оперативного внесения корректировок в состав смеси. Главным образом эти преимущества связаны с возможностью:
1. Смешивания доставленного на завод асфальтобетонного гранулята со щебнем, хранящемся на складе. При этом можно оператив-
199
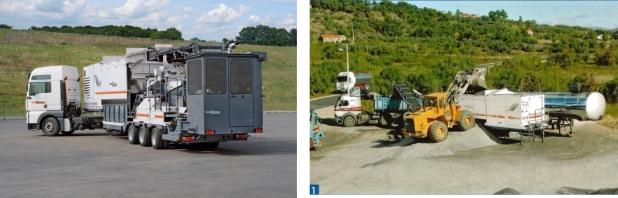
но варьировать доли разных фракций, что позволяет получать необходимый и однородный гранулометрический состав.
2. Процессом смешивания материалов в смесительной установке принудительного действия можно направленно управлять, изменяя время смешивания. Это позволяет получить смесь наибольшей одно-
Сродности.
Таким образом, качество строительства по этой разновидности ресайкл нга определяется качеством фрезерования покрытия, приготовлен я на заводе смеси требуемого состава и строительства конст-
руктивногослоя.
Рис. 93. |
Передвижная |
смесительная |
Рис. 93. Приготовление смеси на |
установка |
Wirtgen KMA |
220, приме- |
мобильном заводе с применением |
няемая для холодного |
|
установки Wirtgen KMA 220 |
|
|
|
Д |
|
ВместебАс тем необходимо отметить, что холодный ресайклинг на |
заводе менее популярен, чем метод холодной ресайклинг на дороге. Связано это с тем, что по сравнению с ресайклингом на месте этот способ менее удобен и более дорогостоящий.
Технология холодного ресайклинга на дорогеИпоявилась благодаря переоборудованию фрез. Такая модификация привела к появлению в 60-х гг. 20-го в. специальных машин, снабженных горизонтальными барабанными фрезами и камерами смешения, позволяющими выполнять инъекцию битумной эмульсии в гранулят. Дальнейшие работы по совершенствованию этих первых машин привели к появлению современных комплексных машин, предназначенных для холодного ресайклинга дорожных покрытий на большую глубину.
200
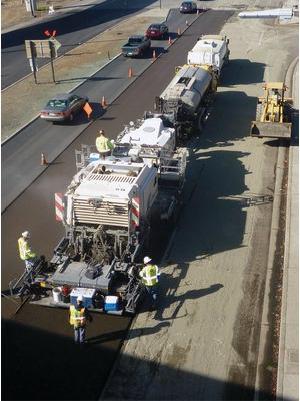
|
|
Метод холодного ресайклин- |
||
|
|
га на дороге состоит в перера- |
||
|
|
ботке и обогащении существую- |
||
С |
щих асфальтобетонных покры- |
|||
тий. Этот способ реализуется без |
||||
нагрева с добавлением вяжуще- |
||||
го. В настоящее время холодный |
||||
ресайклинг на дороге выполняют |
||||
одним из двух наиболее распро- |
||||
страненных способов: |
||||
- из машин, каждая из кото- |
||||
рых выполняет одну или две |
||||
и |
||||
элементарные задачи, составля- |
||||
ют своеобразный «поезд» ре- |
||||
сайклирующего |
оборудования, |
|||
вплоть до операций уплотнения |
||||
[119]; |
|
|||
|
|
|
||
Рис. 94. |
й в д потока при |
- применяют |
узкоспециали- |
|
зированные комплексы, выпол- |
||||
холодном ресайклинге |
Общ
Аняющие все задачи - от фрезерования до укладки перера отанного материала. Весь комплекс операций выполняется за один проход.
1.Фрезерование материала предварительноДочищенного покрытия.
2.Контроль гранулометрического состава. На различных машинах эта операция реализуется одним из двух способовИ:
–фрезы, способные выполнять фрезеровку, обеспечивая качественное измельчение материала, а зерновой состав АГБ регулируется и контролируется скоростью движения машины;
–на других машинах применяется смонтированная на трейлере дробильно-сортировочная установка в замкнутом цикле.
При необходимости в АГБ добавляется инертный материал определенной фракции.
3.Ввод добавок. Приготовленный АГБ смешивается с вяжущим (обычно битумной эмульсией, известью, портландцементом или зо- лой-уносом). Эта операция реализуется одним из двух способов:
201
– при применении ресайклеров ввод вяжущего выполняется его впрыскиванием в кожух барабана, служащего смесителем;
– при использовании других машин смеситель монтируют на трейлере.
4. Укладка смеси. Смесь из АГБ и вяжущего укладывается на от- Сфрезерованное основание с заданием определенного профиля. Как правило, укладка смеси выполняется асфальтоукладчиком. Перегрузку смеси выполняют напрямую в бункер укладчика, через валик и подборщ к смеси ли через самосвалы. На дорогах с низкой интенсивностью дв жен я укладка смеси может производиться и грейдером. Из-за большего процентного содержания в получаемой смеси фракц макс мального размера минимальный слой, рекомендуемый
для укладки – 50 мм.
5. Уплотнен е. Уложенная смесь уплотняется до заданной плотности. Обычно на данном этапе задействованы большой пневмоко-
лесный каток |
ольшой |
|
рационный двухвальцовый каток. Если |
ви |
|
||
применялась эмульс онная до авка, уплотнение обычно откладыва- |
|||
ется до тех пор, пока эмульсия не начнет распадаться. При использо- |
|||
вании портландцемента или золы-уноса уплотнение должно начаться |
|||
незамедлительно после укладки. |
|||
6. Уход. По поверхности уплотненного слоя выполняют розлив |
|||
жидкого битума или итумной эмульсии. В случае применения в ка- |
|||
бА |
|||
честве вяжущих цемента или золы эта операция позволяет создать на |
|||
поверхности пленку и предотвратить появление усадочных трещин. |
|||
После этой операции необходимо создать технологический перерыв, |
|||
при котором не допускается воздействие транспорта на слой из мате- |
|||
риала, обработанного неорганическим вяжущим. При введении в АГБ |
|||
только органических вяжущих пролив поверхности слоя битумной |
|||
эмульсии позволяет предотвратитьДрасслоение покрытия. |
|||
7. Устройство верхнего слоя. Как правило, слой из смеси, постро- |
|||
енный при помощи холодного ресайклинга, должен быть перекрыт. |
|||
Материал верхнего слоя |
назначается из условия интенсивности и со- |
става движения. При высокой интенсивностиИверхний слой или слои устраиваются из асфальтобетона. В других случаях достаточно тонкослойных покрытий или поверхностных обработок типа Сларри Сил, Фиб Сил, Кейп Сил, Чип Сил и т.п.
По глубине ресайклирования холодный ресайклинг асфальтобетонных покрытий выполняется одним из двух способов [118, 119]:
202
1. При незначительных повреждениях асфальтобетонного покрытия ресайклинг выполняется на относительно небольшую глубину, как правило, до 10 см. В этом случае выполняется устройство слоя с добавкой в качестве вяжущего битумной эмульсии [118].
2. При наличии на существующем покрытии значительных повреждений выполняют так называемый ресайклинг на полную глубину [119]. В этом случае глубина обработки составляет более 10 см, а в АГБ вводят добавки цемента, битумной эмульсии или вспененного
битума. |
|
Для прав |
льного выбора способа холодного ресайклинга необхо- |
димы предвар тельные изыскательские работы. В ходе этих работ |
|
С |
|
тся |
зучен е проектной документации и обследование су- |
производществующего покрыт я. При изучении проектной документации устанавл ваютбАконструкц ю дорожной одежды, тип и состав асфальто-
бетона существующего покрытия [118]. При полевых обследованиях выполняют в зуальную оценку состояния покрытия, фиксируя типы поврежден й (трещ ноо разование или пластическая деформация) и устанавл вают х размеры, в том числе глубину, а также причины образования [118, 120]. Отметим, что нормативные документы РФ [120], регламентируя о следование существующей дорожной, требуют обращать внимание на наличие металлических предметов (люков, решеток, коммуникаций и т.д.).
та. При этом необходимо учитыватьДто, что зернистость ресайклируемого материала отличается от его зернистости на момент укладки, а также то, что мелкие фракции зачастую связаны между собой. Это означает, что в процессе ресайклинга необходима добавка таких фракций [118].
Каждый из применяемых способов ресайклинга имеет свои особенности. Так, если для приготовления новой смеси используют только АГБ, то готовить новую смесь целесообразно с добавкой битумной
эмульсии. Это восстановливает свойства материала слоя [118]. До-
бавка вяжущего в материал старого слоя требует тщательного расче- И
При применении способа глубокого холодного ресайклинга и добавок минерального материала требуется укрепление АГБ и добавок вяжущим. В этом случае применяют технологии, позволяющие выполнять ввод как органических, так и минеральных вяжущих.
Независимо от способа на ресайклированный слой необходимо укладывать асфальтобетонное покрытие или достаточно толстый слой износа. На дорогах с малой интенсивностью движения этого можно
203
достичь поверхностной обработкой или укладкой тонкого (< 40 мм) замыкающего слоя из горячей смеси [118]. При достаточно тяжелом движении помимо слоя износа устраивают одно или двухслойное покрытие из асфальтобетона.
Холодный ресайклинг можно выполнять для восстановления свойств покрытий из необработанного материала. Под ресайклингом
Сбень, грав й, т.д.), л бо оснований из этих материалов совместно с относительно тонк м асфальтобетонным покрытием. В таких конструкциях поврежден я проявляются чаще всего в форме больших тре- в асфальтобетонных слоях, деформациях неукрепленных слоев и
необработанного материала понимают технологию, применяемую для восстановлен я покрытий либо из необработанных материалов (ще-
выбоинах [118].
творения дополнительныхобразомтре ований к ее несущей способности глу-
Добавка вяжущ х во время ресайклинга выполняется с целью улучшен я техн ческ х характеристик ресайклируемого материала,
чтобы так |
восстановить целостность материала в слое. Не- |
щин |
|
связанный матер ал |
асфальто етон могут ресайклироваться на раз- |
личную глуб ну: как правило, в пределах от 150 до 250 мм. При не-
ленных вяжущими материаламиА. Такие работы могут быть выполнены как при помощи холодного ресайклера, так и при помощи стаби-
обходимости улучшить конструкцию дорожной одежды для удовле-
бина может быть увеличена. При этом увеличивается также толщина
нового, полученного ресайклингом слоя [118]. К этому виду ресайк-
линга относят восстановление слоев из материалов и грунтов, укреп-
лизатора, измельчающего грунт и перемешивающего его с цементом |
|
или известью [118]. |
Д |
–битумную эмульсию; И
–жидкий битум;
–вспененный битум;
–цементную суспензию;
–цемент или известь в порошкообразном состоянии, которые при применении определенных ресайклеров рассыпаются перед ними по ходу движения.
В зависимости от вида вяжущего, вводимого в АГ при приготовлении АГБ-смесей, рекомендации [121] подразделяют их на типы:
204
А – без добавления вяжущего; Э – с добавлением битумной эмульсии;
В – с добавлением вспененного битума; Б - с добавлением разогретого битума;
М – с добавлением минерального вяжущего (цемента или извести); К – с добавлением комплексного вяжущего (чаще всего битумной
эмульсии и цемента).
В д вяжущего определяет скорость структурообразования (формирован я равновесной структуры) и расчетные показатели парамет-
ров прочности |
деформируемости новой смеси. |
|
Незав с мо от в да вяжущего непосредственно перед холодным |
||
С |
|
|
ресайкл нгом нео ход мо выполнить ряд подготовительных работ, |
||
включающ в се я [120, 121]: |
|
|
- перенос дв жен я на противоположную полосу движения про- |
||
езжей части л |
полное его закрытие; |
|
- уборку всех |
предметов и строительных материа- |
|
посторонних |
|
|
лов; |
|
|
- обследован е существующей дорожной одежды с целью опре- |
||
деления металлических предметов (люков, решеток, коммуникаций и |
бо т.д.); А
- осуществление всех мероприятий по уширению проезжей части,
если таковые предусмотрены проектом;
крытия дефекты и зоны неоднородностиДматериалов или толщины покрытия (визуально по наличию дефектов) Иремонтируются материалом для ямочного ремонта [120, п. 6.1].
- устройство выездов и съездов, попадающих в зону ремонтных
работ;
- установку при необходимости копирной струны справа от фрезы. Кроме того, обнаруженные при визуальной оценке состояния по-
Ресайклинг с битумной эмульсией обычно применяют для возобновления покрытия, обрабатывая ресайклируемый слой на глубину до 10 см [119]. Незначительная глубина обработки существующего покрытия учитывается при фрезеровке его материала. Эту операцию выполняют либо при помощи фрезы либо ресайклера, снабженного фрезерно-смесительным барабаном. Схема, представленная на рис. 96, иллюстрирует фрезеровку покрытия при помощи фрезы. В этом случае первый проход фрезы рекомендуется выполнять от оси дороги или полосы движения, а последующие проходы выполняются со смещением к кромке. В соответствии с этой схемой фрезеровка
205

выполняется на требуемую глубину, но не превышающую 10 см. Схема фрезеровки фрезерно-смешивающим барабаном ресайклера приведена на рис. 97. Отметим, что фрезерно-смешивающий барабан ресайклеров оборудуется кожухом, внутрь которого впрыскивается вяжущее. В большинстве случаев фрезерование существующего по-
Скрытия и смешивания асфальтового гранулята с вяжущим выполняется за один проход. Реже в случаях необходимости обеспечения требуемого гранулометр ческого состава требуется два прохода по одному следу. При первом проходе выполняют фрезеровку, а при второмисмеш ван е матер ала с вяжущим. При втором проходе выполняется дополн тельное змельчение материала.
бА
ВСША наиболее часто применяютсяДкатионные эмульсии, распадающиеся со средней скоростью, анионныеИэмульсии применяют реже [119]. Аналогичные требования содержатся в рекомендациях РФ [120, 121]. Для приготовления смесей типов Э и К используют эмульсии, отвечающие требованиям ГОСТ 18659. Так, в соответствии с [121, п. 4.4] для приготовления смесей типов Э и К используют эмульсии, отвечающие требованиям ГОСТ 18659. Причем в смесях типа Э применяют катионные эмульсии классов ЭБК-2, ЭБК-3 и анионные эмульсии классов ЭБА-2, ЭБА-3 [121].
При этом документы РФ, так же как и стандарты США, предпочтение отдают катионным эмульсиям.
Всоответствии с рекомендациями [120, п. 4.4] холодное ресайклирование с битумной эмульсией выполняется ресайклером, осущест-Рис. 96. Схема проходов при фрезеровРис. 97. Фрезеровка покрытия
206

вляющим фрезерование существующего асфальтобетонного покрытия, перемешивание в камере барабана асфальтогранулята и с эмульсией непосредственно в процессе работы.
При этом в зависимости от категории автомобильной дороги слой из АГБ, обработанного битумной эмульсией, применяется
СПри необход мости увеличения производительности ресайклера перед его пр менен ем выполняется фрезерование существующего
[120, п. 4.3]:
- для автомобильных дорог I – III категорий в слоях основания и
нижних слоях покрыт я;
- для автомоб льных дорог IV – V категорий в качестве покрытия
с последующ м устройством поверхностной обработки.
асфальтобетонного покрытия о ычной фрезой с выгрузкой получаемой смеси (асфальтогранулята) на смежную полосу. Такое фрезеро-
вышения структурнойподборпрочности нового покрытия на этапе фрезерования производится до авление и распределение щебня узких фракций на полосе перед фрезой или ресайклером [120].
вание пр ведено на с. 98. |
|
Дальнейшее |
существующего асфальтобетонного |
фрезерование |
отфрезерованного с соседней |
покрыт я на смежной полосе и |
|
полосы матер ала осуществляется ресайклером. |
|
В случае нео ходимости для улучшения зернового состава и по- |
Фрезерование существующего покрытия выполняется на задан- |
|
ную глубину, а при необходимости исправления существующего |
|
|
А |
профиля фрезерование производят от осевой линии автомобильной |
|
дороги (рис. 99). |
Д |
|
|
|
И |
Рис. 98. Предварительное фрезероваРис. 99. Сцепка автогудронатора и |
|
ние покрытия фрезой |
ресайклера (движение на фотографа) |
207
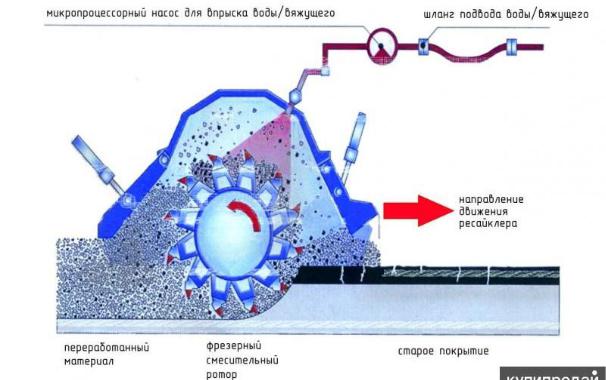
При применении ресайклера эта машина работает в жесткой сцепке с автогудронатором [120]. Ресайклер фрезерует покрытие на требуемую величину и выполняет ввод битумной эмульсии в фрезер- но-смешивающий барабан. Эмульсия подается из автогудронатора и подается под кожух фрезерно-смешивающего барабана при помощи
Снасоса, управляемого микропроцессором (рис. 100). Расход эмульсии регулируется насосом, что позволяет ее вводить в количестве, требуемом проектом.
и бА
Рис. 100. Схема работы ресайклера приДобработке АГБ битумной эмульсией: 1 – фрезеруемое покрытие; 2 – фрезерно-смешивающий барабан; 3 – переработанный материал покрытия, смешанный с эмульсией; 4 – шланг подачи эмульсии; 5 – микропроцессорный насос для впрыскаИэмульсии.
Приготовленную смесь распределяют в технологический слой и уплотняют катками, соблюдая рекомендации СП 78.13330.2012 [7] и ОДМ [120, п. 6.7], а также данные пробного уплотнения.
Полученную смесь по транспортеру загружают в кузов автомо- биля-самосвала и доставляют к асфальтоукладчику. Возможна непосредственная выгрузка в асфальтоукладчик либо в валик при использовании перегружателя (подборщика) смеси.
В соответствии с рекомендациями [120, п. 6.6] укладка смеси производится асфальтоукладчиком традиционным способом с пред-
208
варительной настройкой уплотняющих органов. Из-за большего процентного содержания в получаемой смеси фракции максимального размера минимальная толщина слоя, рекомендуемая для укладки, составляет 50 мм.
Для уплотнения предлагается применять тяжелые пневмоколесные катки и двухосные вибрационные катки со стальными вальцами.
Ска эмульс я не начнет распадаться [120, п. 6.7]. Дополнительно может производ ться повторное уплотнение катками со стальными вальцами спустя несколько дней после первоначального уплотнения. Цель повторного уплотнен я состоит в исключении небольших местных уплотнен й по траектории движения колес, возникших под воздейст-
При использовании битумных эмульсий и эмульгированных регенерирующ х агентов уплотнение обычно откладывается до тех пор, по-
виемляется верхн м слоем, то вслед за его устройством выполняется укладка верхнего слоя покрыт я в соответствии с проектом. Производство работ
10 сут для максимальнобАвозможного достижения формирования смеси под действием организованного движения транспортных средств [120, п. 6.10]. Скорость движения транспортных средств по слою, устроенному по технологии холодного ресайклинга, должна быть не
транспортной нагрузки.
Если устроенный по технологии холодного ресайклинга слой не яв-
по |
устройству |
слоя |
из |
асфальтобетона |
|
осуществляется |
традиционным |
спосо ом |
в |
соответствии |
с |
требованиями |
|
СП78.13330.2012 [7]итехнологиями,описанными внастоящемпособии. |
||||||
|
Устройство вышележащих слоев осуществляется непосредствен- |
|||||
но после устройства слоя ресайклирования либо не ранее чем через |
При устройстве на автомобильныхДдорогах IV - V категорий верхнего слоя по технологии холодного ресайклинга по нему должна быть распределена поверхностная обработка.
более 40 км/ч. |
И |
|
При необходимости исправления продольного профиля автомобильной дороги (на дорогах IV - V категорий), а также при наличии избытка битумного вяжущего или необходимости повысить несущую способность дорожной одежды следует добавлять щебень [120, п. 6.12]. Щебень доставляется на место укладки автомобилямисамосвалами и распределяется с последующим уплотнением. Толщина слоя распределенного щебня зависит от фактических параметров продольного профиля и утвержденного проекта.
209
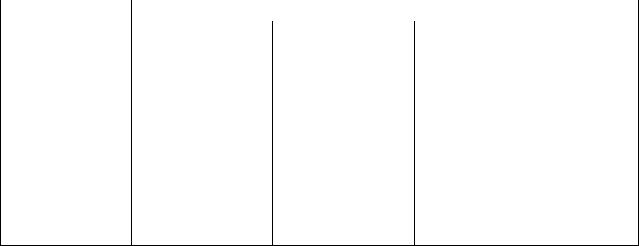
Устройство слоев усиления дорожной одежды из АГБ-смесей типа Б и В требует смешивания асфальтогрунулята с дозированными порциями битума (тип Б) и вспененного битума (тип В). Для приготовления асфальтогранулобетонных смесей типов Б и В ресайклером применяют битумы [121, п. 4.2], отвечающие требованиям соответственно ГО Т 22245 [50] и ГОСТ 11955 [51]. Марка битума принимается в зависимости от дорожно-климатической зоны и типа приготовляемой смеси. Регламентация марок битума приведена в табл. 67.
|
|
|
|
Таблица 67 |
|
Марки б тумов пр меняемых для приготовления смеси ресайклером |
|||
|
Тип, пр готав- |
|
Дорожно-климатическая зона |
|
С |
|
|
|
|
|
|
|
||
|
сме- |
I |
II и III |
IV и V |
|
си |
|||
|
|
|
|
|
|
|
БНД 200/300 |
БНД 200/300 |
БНД 130/200 |
|
Б |
СГ 130/200 |
СГ 130/200 |
СГ 700/130 и СГ 130/200 |
|
МГ 130/200 |
МГ 130/200 |
МГ 700/130 и МГ 130/200 |
|
|
ливаемой |
|
|
|
|
|
МГО 130/200 |
МГО 130/200 |
МГО 700/130 и МГО |
|
|
130/200 |
||
|
|
|
|
|
|
В |
БНД 130/200 |
БНД 90/130 |
БНД 60/90 |
|
БНД 130/200 |
БНД 90/130 |
||
|
|
|
||
|
Э и К |
БНД 90/130 |
БНД 60/90 |
БНД 60/90 |
|
БНД 130/200 |
БНД 90/130 |
БНД 90/130 |
В соответствиибАс указаниями [121, п. 4.8] для приготовления смесей всех типов,крометипа Б,в ряде случаевДтребуется добавлениеводы.
Схема работы ресайклера аналогична представленной на рис. 100 с той разницей, что под кожух фрезерно-смешивающего барабана по-
дают еще и воду.
битумы. Схема получения вспененного битума в расширительной камере приведена на рис. 101.
Особое место при холодной регенерации занимают вспененные И
Рис. 101. Схема вспенивания битума в расширительной камере
210
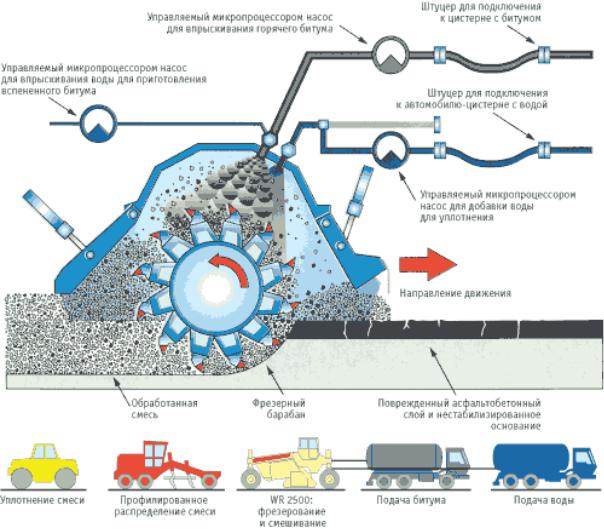
При применении ресайклеров вспененный битум готовят в расширительных камерах, расположенных перед отверстиями для выхода битума в распылительной рампе. Битум и вода подаются под напором одновременно. Современные ресайклеры приспособлены для холодного ресайклинга как с битумной эмульсией или битумом, так и со
Свспененным битумом. Например, ресайклер Wirtgen WR 2500-S снабжен 16 расширительными камерами, каждая из которых работает по принц пу, представленному на рис. 101. Схема работы этого ресайклера с пр менен ем вспененного битума приведена на рис. 102.
и бА Д
Рис. 102. Схема работы колесного ресайклера WRИ2500 при приготовлении смеси с введением вспененного битума
Вспененный битум получают добавлением к горячему битуму, имеющему температуру 150–180 °C сравнительно небольшого количества воды. В США количество добавляемой воды принимают 2 – 5% от массы битума [119]. Суть приготовления вспененного би-
211
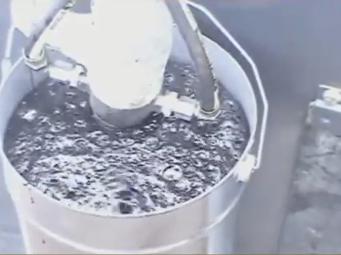
тума состоит в том, что при соприкосновении горячего битума с водой, она превращается в пар, который создает мельчайшие пузырьки, окруженные тонкой пленкой битума. Это приводит к расширению битума примерно до 15–30 раз от первоначального объема.
Для приготовления вспененного битума, обеспечивающего приемлемое качество смеси, необходимо правильно подобрать количество добавляемой воды, которое рассчитывается из объемного расширения продолж тельности сохранения пены [119]. Чем больше количество добавляемой воды, тем больше объемное расширение битума, но меньше время сохранения пены, которое характеризуют пе-
полураспада пены. |
|
|
С |
|
|
риодом |
В США обычно добав- |
|
ляют 3% воды. Это дает |
||
приемлемое объемное рас- |
||
ширение и время сохране- |
||
|
ния пены. |
|
|
На рис. 103 приведена |
|
|
иллюстрация вспенивания |
|
|
битума при добавке воды в |
|
|
количестве 3% |
от массы |
|
битума. |
|
|
Параметры |
прочности |
Рис. 103. Образование битумной пены при |
и деформируемости приго- |
|
бА |
|
|
добавлении воды в количестве 3% от массы |
тавливаемой смеси во мно- |
|
битума |
гом зависят от сил адгезии |
|
битума и минерального вяжущего. Поэтому улучшение адгезионных |
||
свойств вяжущего и АГБ приводит к увеличению прочности приго- |
||
тавливаемого материала. Под адгезиейДследует понимать сцепление |
||
между поверхностями двух разнородных контактирующих тел, то |
есть битума и минерального материала. ЭтиИсилы зависят от геометрических параметров битумных пленок на поверхности минеральной части гранулята. Образованию битумных пленок на минеральной поверхности предшествует ее смачивание битумом, величина которого определяется главным образом природой минерального материала и молекулярно - поверхностными свойствами битума – его поверхностным натяжением. Вспенивание битума облегчает смачивание минеральной поверхности и улучшает адгезию. Это обуславливается тем, что во вспененном битуме адсорбционный слой на границе раздела
212
фаз “битум – пар” насыщен асфальтенами. При контакте пленок битумной пены с минеральной поверхностью асфальтены адсорбируются на ней, при этом поверхность минерального материала сохраняет и усиливает структурные изменения вспененного битума [125, 126].
ледовательно, присутствие асфальтенов на поверхности битум- |
|
С |
|
ных пленок способствует улучшению сцепления с минеральной по- |
|
верхностью вспененного битума, при этом, рассматривая прочие рав- |
|
ные услов |
я, можно сказать, что адгезия вспененного битума будет |
выше адгез |
того же битума. Таким образом, вспенивание битума |
щихся в б туме. Вспен вание итума позволяет добиться увеличения
являетсяготовленияспособом повышения сцепления с поверхностью минерального матер ала за счет направленного использования ПАВ, содержа-
сцеплен я на несколько десятков процентов. Для обычных битумов
обычного |
|
подобное улучшен адгезионных свойств достигается только при |
|
использован |
дополн тельных дорогостоящих ПАВ, усложняющих |
технолог ю пр |
стоимость смеси. В случае же предвари- |
тельного вспен ван я итума эффект сцепления обусловлен теми |
|
ПАВ, которые входят в состав самого битума. |
|
|
А |
Практический интерес представляет оценка сил сцепления вспе- |
|
ненного и |
итума с поверхностью минерального материала. |
Как правило, величина сцепления битумных пленок с поверхностью зерен минерального материала зависит от метода ее оценки. Этот показатель оценивают различнымиДметодами, особенности которых зависят от специфики работы клеевых соединений.
В соответствии с нормативным методом испытаний [46, п. 28.1 – 28.4] качество сцепления оценивают визуально по степени сохранности пленки битумного вяжущего на зернах минерального материала после его кипячения в дистиллированной водеИ. В этом методе вода оказывает на битум отслаивающее действие. Недостатком этого метода является отсутствие возможности количественной оценки величины показателя сцепления. В связи с этим для определения величины сцепления вязкого и вспененного битума к поверхности минерального материала специалисты применяют другие способы, например метод красителей [127]. Оценка показателя сцепления методом красителей заключается в определении величины покрытой битумом поверхности материала по адсорбции красителя после отслаивания битумной пленки водой. В качестве красителя применялся метиленовый голубой, обладающий способностью избирательно адсорбироваться на поверхности зерна, не адсорбируясь на битуме [127].
213

В табл. 68 приведены результаты лабораторных исследований оценки сцепления вяжущего в вязком и вспененном состоянии к поверхности отсева дробления кварцитопесчаника и гранита (в чистом виде и с добавлением минерального порошка).
С |
|
|
|
|
|
|
Таблица 68 |
|||
|
|
Поверхность минерального материала, покрытая битумом |
||||||||
|
|
|
|
|
Вид органического вяжущего |
|
||||
|
Минеральный ма- |
|
|
|
|
Вспененный битум при добавлении |
||||
|
|
|
|
|
|
воды в количестве |
||||
|
тер ал |
Вязкий битум |
|
|
||||||
|
|
3 % от массы би- |
|
|
||||||
|
кварцитопесчан |
|
|
|
|
|||||
|
|
|
|
тума |
|
|
||||
|
|
|
|
|
|
|
|
|
|
|
|
Отсев дроблен я |
|
14,48 |
|
|
|
57,54 |
|
31,23 |
|
|
|
ка |
|
|
|
|
|
|||
|
|
|
|
|
|
|
|
|
|
|
|
Тоже + звестняк |
|
22,83 |
|
|
|
79,61 |
|
43,47 |
|
|
Тоже + пыль |
|
14,66 |
|
|
|
56,62 |
|
23,95 |
|
|
|
обычным |
|
|
|
|||||
|
Из анал за данных та л. 68 следует, что вспененный битум обла- |
|||||||||
|
дает более высок |
сцеплением с минеральным материалом по срав- |
||||||||
|
нению с |
|
вязк м итумом. Причем наибольшая сохранность |
|||||||
|
|
|
А |
|
||||||
|
пленок битума имеет место при вспенивании битума 3% воды от мас- |
|||||||||
|
сы битума. Это хорошо согласуется с данными [119, 46]. Наличие пы- |
|||||||||
|
ли несколько снижает сцепление по сравнению с чистым материалом, |
|||||||||
|
а применение минерального порошка, наоборот, увеличивает адге- |
|||||||||
|
зию. Добавление в приготавливаемую смесь воды позволяет обеспе- |
|||||||||
|
|
|
|
|
|
Д |
чить условия уплотнения смеси, а также выполнить некоторое обеспыливание гранулята [119].
Другой особенностью применения вспененного битума является то, что мелкие частицы покрываются им очень хорошо, а крупные лишь частично. При этом создается своеобразнаяИпаста, объединяющая смесь. Поэтому в США АГБ должна содержать достаточное количество мелких частиц – 4–5% мельче 0,075 мм (в данном случае фракция классифицируется по стандарту [128]).
Применение вспененного битума позволяет добиться более равномерного его распределения в смеси. В результате улучшается такой показатель, как однородность смеси. Суть этого явления состоит в быстром смачивании вспененным битумом поверхности минерального материала. Смачивание минерального материала вяжущим будет тем лучше, чем ниже его поверхностное натяжение [125], поэтому применение вспененных битумов предпочтительнее, так как при вспенивании поверхностное натяжение битума снижается.
214
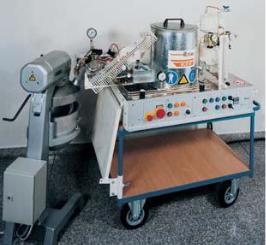
Вспененный битум при холодном ресайклинге получил широкое распространение в США, Южной Африке, Бразилии, Скандинавии и Австралии.
При последующем интенсивном уплотнении затвердевший вспененный битум демонстрирует хорошую несущую способность и эластичность, а также значительное снижение предрасположенности к образованию трещин. Для ускорения затвердевания, а также для повышен я доли заполн теля рекомендуется добавление 1–2% гидрав-
лического вяжущего ( |
звести или цемента). |
При вспен ван |
б тума не происходит никакой химической ре- |
акции, суть процесса состоит в изменении физического состояния |
|
С |
|
на коротк й промежуток времени. К обычному физическому |
состоян ю б тум возвращается в течение нескольких минут, а в больш нстве случаев меньше, чем за минуту [119].
ных лабораторныхобработанныхсмесителей приводит к тому, что прочность образцов может отличатьсяАдо 25% [129]. Многие смешивающие блендеры
Эти обстоятельства создают сложности при изготовлении образ-
цов для |
сследован я параметров прочности и деформируемости ма- |
битума |
|
териалов, |
вспененным битумом. Применение различ- |
выполняют перемешивание за 30 с, что больше времени смешивания битумной пены с минеральным материалом ресайклером.
Поэтому очень важно использовать в лаборатории установки для вспенивания битума и миксер, смешиваюшийДматериал с битумной пеной, которые позволяют имитировать полевые условия [129].
В лаборатории Wirtgen для приготовления вспененного битума применяется установка WLB 10 [130] (рис. 104). ПрименениеИэтой установки позволило специалистам компании Wirtgen определить зависимость технологических параметров вспененного битума от количества воды, добавляемой для получения битумной пены и температуры горячего битума.
На рис. 105 приведена зависимость времени полураспада вспененного битума от количества добавляемой к горячему битуму воды [131].
215
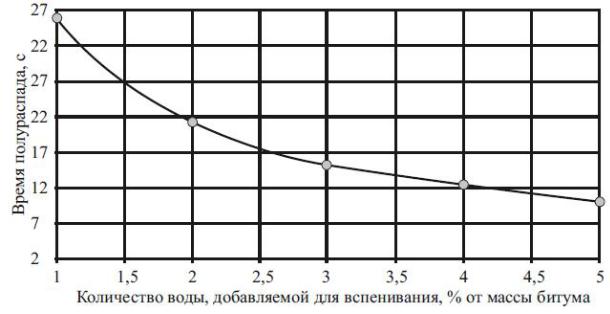
СРис. 105. Зав с мость времени полураспада битумной пены от количества доавляемой в нагретый битум воды [131]
полураспадабАуменьшается и становится меньше продолжительности перемешивания во фрезерно-смешивающем барабане. В этом случае вспененный битум возвращаетсяДв исходное состояние до завершения перемешивания. Отсюда следует вывод, что рациональное количество добавляемой воды при холодной регенерации асфальтобетонных по-
Анал з данных р с. 105 показывает, что при добавлении воды в количестве 3% от массы итума время полураспада битумной пены составляет 15 с, что соответствует времени перемешивания АГБ или грунта со вспененным итумом. При большем количестве воды время
крытий составляет 3%.
На рис. 106 приведена зависимость отношения объема вспененного битума к его начальному объему от количестваИводы, добавляемой для образования битумной пены [131]. Анализ данных рис. 106 показывает, что с увеличением количества добавляемой к нагретому битуму воды отношение объемов битумной пены и битума возрастает. Отсюда следует, что чем больше количество воды, тем лучше смачивающая способность вспененного битума. Однако увеличение количества воды, добавляемой к битуму, можно рассматривать лишь в случае уменьшения времени необходимого для качественного перемешивания битумной пены с АГБ или грунтом.
216
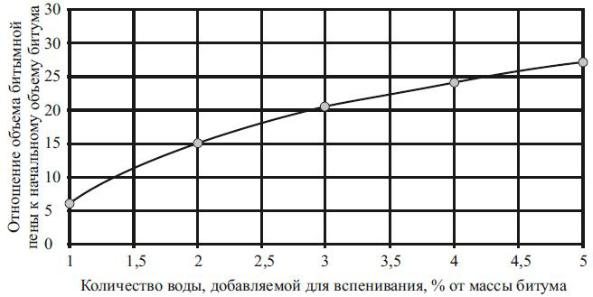
С
Рисб тума от кол чества до авляемой в нагретый битум воды [131]
. 105. Зав с мость отношения о ъема битумной пены к начальному объему
Аналог чные сследования выполнены в работах М. Кендалла с
соавторами [132] и Дж. Рамануджама [133]. Из анализа данных, полу- |
|
ченных этими специалистами, следует, что добавление воды в коли- |
|
б |
|
честве 3% приводит к расширению пены в 21 раз. Период ее полурас- |
|
пада составляет 23 с. |
[132, 133] сходятся во мнении, что наи- |
Авторы |
|
более рациональное содержание воды, добавляемой к битуму, состав- |
ляет не 3, а 2,5%. В этом случае период полураспада занимает 30 с, а объем вспененного битума увеличивается в 17 раз. К таким же выводам пришли авторы работы [134], указавшие на то, что добавку воды в количестве 2,5% от массы битума следует выполнять при его нагреве до 180 оС.
Д Анализ различных данных [131 – 134]Ипоказывает, что рацио-
нальная температура нагрева битума находится в пределах 170 – 180 оС, а количество воды, добавляемой для вспенивания, необходимо принимать 2,5 – 3%. Более детальное исследование влияния количества воды и температуры нагрева битума выполнено в работе [135]. Авторами [135] установлено, что при холодном ресайклинге качественное смешивание минерального материалы можно получит при нагреве битума до 170 оС и добавке к нему воды в количестве 2,8%. В этом случае время полураспада пены составляет 12 – 13 с, что достаточно для смешивания. Зависимость технологических параметров вспененного битума от температуры нагрева и количества добавляемой воды приведена на рис. 107.
217
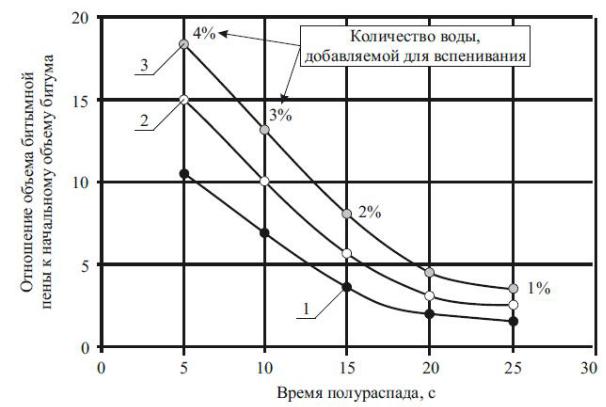
Си
Рис. 107. ЗависимостьботношенияАо ъема битумной пены к начальному объему битума и времени полураспада от количества добавляемой воды
и температуры нагрева битума
Таким образом, регулируя о ъем расхода воды и температуры нагрева битума, можно добиватьсяДизменения продолжительности периода полураспада битумной пены и добиваться качественного смешивания минерального материала с вяжущим.
К. Дженкинс выполнил исследование влияния температуры горячего битума и температуры лабораторной тары, нагревающейся от пара во время образования битумной пены, на температуру вспененного битума [136, 137]. Эти данные представлены в табл. 69.
|
|
|
|
Таблица 69 |
||
Температура вспененного битума, получаемого в лабораторных установках |
||||||
Температура |
Температура битумной пены при нагреве битума |
|
||||
о |
|
|
о |
|
|
|
тары С |
|
до температурыИ, С |
|
|||
150 |
160 |
170 |
180 |
|||
|
|
|||||
10 |
75,4 |
81,3 |
87,2 |
93,1 |
|
|
28 |
82,6 |
88,4 |
94,3 |
100,2 |
|
|
50 |
91,3 |
97,2 |
103,1 |
108,9 |
|
|
100 |
111,1 |
117,0 |
122,9 |
128,7 |
|
218
Температура битумной пены оказывает влияние на качество перемешивания, то есть на однородность смеси. Чем выше температура вспененного битума, тем меньше его вязкость, а следовательно, облегчается смещивание с грунтом или АГБ. Однородность смеси оказывает влияние на параметры прочности и деформируемости. Темпе-
Сратура лабораторной тары зависит от количества выделяемого пара и продолжительности вспенивания. Таким образом, однородность укрепленного грунта ли АГБ, обработанной вспененным битумом, и параметры прочности этих материалов зависят как от температуры
нагревамаркиб тума, так от лабораторных параметров при вспенивании
битума. ледовательно, желательным является соответствие количества вспен ваемого тума его расхода за один замес на дороге ре-
сайклером.
|
б |
Кроме того, параметры прочности и деформируемости материа- |
|
ла, обработанного вспененным итумам, зависят от: |
|
– |
тума; |
– качества б тума; |
|
– однородности смеси; |
|
|
А |
– расхода вспененного итума, который необходимо принимать в |
зависимости от зернового состава. Чем мельче размер минеральной части, тем больше суммарная удельная поверхность зерен и частиц и тем больше требуется итума для обработки материала.
По некоторым данным, применение вспененного битума позволяет уменьшить его расход по сравнению с обычными битумами на 10 – 15%. Например, если для укрепления разноразмерного среднего песка необходимо 5% жидкого битума, то ориентировочный расход
битумной пены составит 4,25 – 4,5%. |
И |
|||
Рекомендуемые компанией Wirtgen расходы вспененного битума |
||||
для АГБ-смесей приведены в таблД. 70 [118]. |
||||
|
|
|
Таблица 70 |
|
Расход вспененного битума в зависимости от размеров зерен |
||||
Доля материала, прошедшего через сито,% |
Добавка вспененного битума, % |
|
||
Зерна 4,75 мм |
Зерна 0,075 мм |
от массы сухого материала |
|
|
|
3 – 5 |
2 – 2,5 |
|
|
<50 |
5 – 7,5 |
2 |
– 3 |
|
7,5 – 10 |
2,5 |
– 3,5 |
|
|
|
|
|||
|
>10 |
3,0 |
– 4,0 |
|
|
3 – 5 |
2 |
– 3 |
|
>50 |
5 – 7,5 |
2,5 |
– 3,5 |
|
7,5 – 10 |
3,0 |
– 4,0 |
|
|
|
|
|||
|
>10 |
3,5 |
– 4,5 |
|
219
Специалисты компании Wirtgen указывают на то, что расход вспененного битума, представленный в табл. 70, справедлив при добавке в АГБ 1% цемента или извести [118]. Вследствие этого расход вспененного битума без добавки минерального вяжущего будет выше, чем представленные в табл. 70 дозировки. Поэтому расход битумной пены необходимо подбирать на основе лабораторных исследований. При этом АГБ должна иметь пригодный зерновой состав, то есть не быть сл шком крупной или слишком мелкой. Требования по грану-
лометр |
АГБ содержатся в [120, 121]. |
|
Анал з работ, |
сследовавших параметры прочности и деформи- |
|
руемости матер алов, полученных при холодном ресайклинге, пока- |
||
С |
|
|
зывает, что пр менен е вспененного битума предпочтительнее, неже- |
||
ли |
е |
тумной эмульсии. При этом все специалисты |
использован
-получениебАновых видов цемента и других неорганических вяжущих;
-совершенствование знаний о строительно-технических свойствах цементов, обработанных им Дматериалах и рабочих характеристиках соответствующих слоев [138];
-использование нового, более мощного оборудования, с большей глубиной фрезерования, способного к обеспечению лучшего качества конечного продукта [139];
-увеличение внимания к экологическимИфакторам, особенно с учетом истощения запасов качественных каменных материалов и сложностью закладки новых крупных карьеров.
В настоящее время цемент как вяжущее для холодного ресайклинга с успехом применяется в ряде стран – США [139], АвстралииФранции [144].
В Южной Африке холодный ресайклинг применяется на протяжении более чем 20 лет. В последние годы проекты по переработке ориентированы на использование малых количеств битума (около 2%) и цемента. В составе комплексного вяжущего битум применяется в виде пены (FTB) или эмульсии (ETB). Такой метод холодного ре-
220
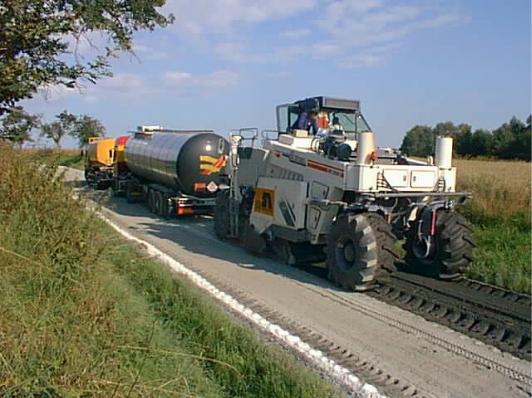
сайклинга является успешным, но при условии тщательного контроля на всех этапах производства работ [129].
При применении ресайклера WR 2500 минеральное вяжущее распределяется по поверхности, а его перемешивание с АГБ выполняется фрезерно-смешивающим барабаном при одновременном введении Свспененного битума и воды, необходимой для уплотнения. При такой технологии в состав поезда включают автомобили, транспортирующие б тум воды, ресайклер WR 2500, автогрейдер или укладчик
смеси катки, выполняющие ее уплотнение. иНа р с. 108 пр ведена иллюстрация работы ресайклера WR 2500.
бА
Рис. 108. РесайклерДWR 2500 вИсцепке
с поливомоечной машиной и автогудронатором
Другим вариантом применения комплексного вяжущего является предварительное приготовление цементной суспензии в смесителе, например WM 1000, с последующим ее введением через ресайклер в АГБ совместно со вспененным битумом (рис. 109). На рис. 110 приведена иллюстрация работы ресайклера WR 4200, выполняющего комплексное укрепление грунта органическим вяжущим и цементной суспензией, приготавливаемой смесителем WM 1000.
221
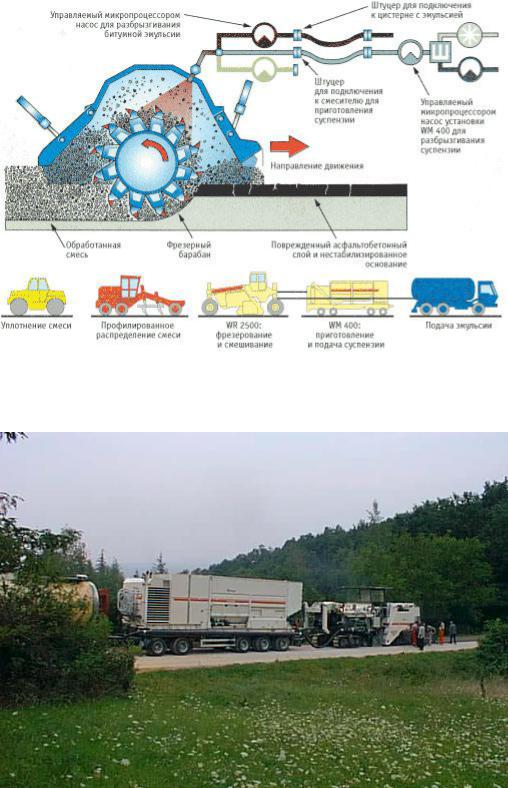
СРис. 109. Схема ра оты ресайклера при устройстве слоя из АГБ-смеси
бА с введением итумной эмульсией
и цементной суспензией
Д И
Рис. 110. Ресайклер WR 4200 в сцепке со смесителем WM 1000
Применение для укрепления грунтов цемента преследует цель повышения прочности, которая оценивается пределом прочности при сжатии (UCS) и предела прочности при растяжении (растрескивании) (ITS).
222
Эти параметры прочности материала, стабилизированного комплексным вяжущим,всоставекоторогосодержитсяцемент,существеннозависят от:
– количества цемента;
– марки цемента;
– типа материала;
Смарки цемента для обеспечения требований нормативных документов требуется разл чное количество цемента. При определении прочности степень уплотнен я играет большую роль, а внешняя температура оказывает прямое вл яние на скорость, с которой нарастает прочность. Чем выше температура, тем быстрее увеличивается прочность.
– степени уплотнения.
Как правило, зависимость прочности от содержания цемента
имеет л нейный характер. При этом в зависимости от материала и
связи. В процессе воздействия уплотняющей нагрузки эти связи час-
образовалось венного уплотнения Аважно уложить материал и закончить его укатку
При пр менен в составе вяжущего цемента и смешивании его
водой между отдельными зернами АГБ образуются кристаллические
тично разрушаются, что приводит к некоторому снижению прочности. Сн жен е прочности удет тем выше, чем больше кристалличе-
ских связей к моменту уплотнения. Поэтому для качест-
как можно в более короткий промежуток времени. Это требование особенно важно в районах с высокой температурой воздуха, то есть
склонны к трещинообразованиюД, причиной которого является возникновение напряжений, превышающих параметры прочности. Причиной возникновения этих напряжений является усадка, колебания температуры и воздействие транспортных средств.
там, где материал склонен к быстрому набору прочности [118].
При невозможности обеспечения этого требования в качестве альтернативного портландцементу вяжущего рассматривают применение извести или смеси шлака с цементом, при которых материал
набирает прочность медленнее. Материалы, обработанные цементом, И
Образование усадочных, температурных и силовых трещин можно контролировать. Для этого рассмотрим причины образования таких трещин:
–химическая реакция, которая протекает в процессе гидратации цемента при его контакте с водой и поэтому не зависит от транспортных нагрузок;
–циклическая нагрузка от транспорта.
223
Вследствие двух принципиально разных причин возникновение и последующее развитие трещины в обоих случаях различны и поэтому механизмы их торможения так же неодинаковы.
При гидратации цемента образуются пальцеобразные кристаллы силиката кальция сложной формы, связывающие между собой зерна материала [118]. В ходе этой химической реакции выделяется тепло и изменяется объем материала, что вызывает образование усадочных трещин. Эти трещ ны неизбежны, но степень растрескивания, расстояние между трещ нами и величина их раскрытия зависят от сле-
С1. одержан е цемента. Чем больше количество цемента в материале, тем больше растрескивание. Поэтому одной из задач подбора
дующ х факторов:
состава является уменьшение содержания цемента до минимума так, чтобы можно было о еспечить требования по несущей способности дорожной одежды, оцениваемой величиной общего модуля упруго-
объем в сухомстаби влажном состояниях. Особенно ярко это проявляется
. |
|
сти |
|
2. Т п |
л з руемого материала. Различные материалы при |
стабил зац |
х цементом в неодинаковой степени проявляют уса- |
дочные свойства. Кроме того, грунты существенно изменяют свой
у грунтов с числом пластичности более 10. Такие грунты стабилизируют комбинацией цемента и извести или известью. Эта мера позволяет уменьшить пластичность, а в некоторых случаях полностью
устраненить. |
А |
3.Влажность при уплотнении. Степень растрескивания зависит от количества влаги, потерянной при высыхании материала. Путем ограничения водоцементного отношения к моменту уплотнения до значения меньше 75% от полного водонасыщения можно существенно уменьшить степень растрескивания.
4.Скорость высыхания. В процессе твердения происходит высыхание материала, обработанного цементом, что сопровождается сжатием и развитием внутренних напряжений. В этом случае степень растрескивания определяется скоростью нарастания прочности по сравнению со скоростью повышения усадочных напряжений. При быстром высыхании материала эти напряжения увеличиваются быстрее набирания прочности, что сопровождается интенсивным образованием узких (волосяных) трещин. Медленное высыхание влечет за
собой менее интенсивное образование трещин, но их раскрытие в этом случае больше. Эффективной мерой борьбы с такими трещина-ДИ
224
ми является уход за слоем, в течение которого обеспечивают благоприятный режим отвердевания материала.
Раскрытие усадочных трещин по высоте слоя неодинаково. У таких трещин ширина больше в верхней части слоя.
Принципиально иными являются трещины, возникающие от воз- Сдействия транспортных средств. Такие трещины возникают тогда, когда обработанный цементом материал перенапряжен или превышена его усталостная прочность. Зарождение этих трещин происходит в растянутой, то есть н жней части слоя. Растягивающие напряжения
деленного ч сла клов нагрузки.
циалистамитем выше, чем н же модуль упругости на поверхности подстилающего слой основан я. Усталостное разрушение происходит после опре-
Особое вн ман е при выполнении холодного ресайклинга с цементом следуетбАуделять поверхности слоя. Опыт, накопленный спеЮжной Африки, показывает, что слои из материалов, обработанных сравн тельно малым количеством цемента и относительно тонк м покрыт ем ли с поверхностной обработкой, накапливают поврежден я в в де трещин, о разующихся на поверхности слоя. Трещины появляются в верхней части обработанного цементом слоя, когда напряжения превышают предел прочности при сжатии. Нормативными документами РФ такой механизм разрушения не рассматривается. Эта проблема решается увеличением предела прочности при сжатии и толщины как ресайклированногоДслоя, так и слоя износа. При этом на дорогах с такими дорожными одеждами необходимо
контролировать нагрузки на ось.
Применяемый при холодном ресайклинге цемент вызывает быстрое нарастание прочности при сжатии. Примерно 50% прочности набираются за первые 7 суток, на 28-е суткиИона достигает примерно 90% от своего максимума. Например, если окончательная величина прочности для слоя основания составляет 2 МПа, то после трех суток она будет составлять меньше 0,5 МПа, то есть дорожная одежда будет чувствительна к нагрузке со стороны транспорта. Эта проблема решается устройством технологического перерыва, в период которого по уплотненному и защищенному от высыхания слоя движения транспорта не допускают. Поврежденность материалов, обработанных цементом, усадочными трещинами, уменьшается рациональным варьированием ряда ключевых факторов.
Во-первых, необходим обоснованный экспериментально подбор состава смеси. Эта задача решается при лабораторных испытаниях,
225
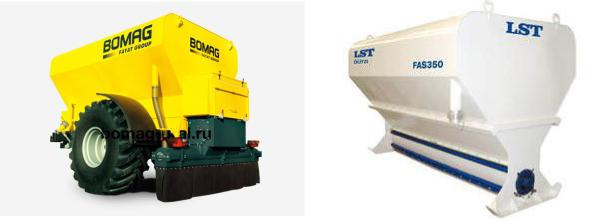
которые позволяют для различных материалов подобрать рациональное количество цемента, при котором обеспечиваются требуемые параметры прочности и минимальная поврежденность материала усадочными трещинами.
Во-вторых, при подборе составов смесей не следует применять быстротвердеющие цементы.
В-третьих, следует избегать применения цементов, у которых выход т срок годности. Цемент необходимо использовать в течение трех месяцев после даты изготовления. Соответствие марки цемента и его акт вность определяются лабораторными испытаниями.
Кроме того, на трещиностойкость оказывают влияние технологи- |
|
С |
|
факторы, к которым относят равномерность распределения |
|
цемента в смеси, качество перемешивания и уплотнения материала и |
|
уход за слоем |
пер од его формирования. |
В настоящее время распределение цемента выполняют одним из |
|
четырех |
. На олее простым и менее точным является спо- |
ческие |
|
соб ручного распределения, применяемый в развивающихся странах. |
|
При реал зац |
этого спосо а на покрытие разбивается сетка, в каж- |
дую клетку которой высыпается цемент из одного мешка. Далее руч- |
способов ными гладилками цементАраспределяется ровным слоем по поверхно-
сти покрытия. Второй способ состоит в применении распределителей цемента. В настоящее время такой способ наиболее распространен, но
Д |
|
требует применения дополнительных машин в составе поезда. В каче- |
|
стве таких машин могут быть применены прицепные и навесные рас- |
|
пределители сыпучих материалов (рис. 111 и 112). |
|
|
И |
Рис.111. Прицепной распределитель |
Рис. 112. Навесной распределитель |
BOMAG BS 10000 |
LST FAS 350 |
Прицепные и навесные устройства применяются для распределения цемента, извести или зольной пыли по поверхности покрытия с
226
целью дальнейшей переработки его материала и укрепления. Современные распределители оснащены электронной системой дозирования, позволяющей выполнить равномерное распределение материала в требуемом количестве. Проверка расхода цемента выполняется с помощью куска брезента. Все крупные распределители имеют свои предельные значения расхода, и при очень малом расходе (< 2%) нужно проверять дозирование особенно тщательно.
Оба способа меют свои недостатки, связанные тем, что сыпучие
вяжущ е матер алы легко переносятся ветром и сдуваются с поверх- |
|
ности воздушными потоками от проходящего транспорта. В этом |
|
случае нарушается доз ровка вяжущего и его содержание на поверх- |
|
С |
|
ности станов тся неравномерным. В случае дождя начинается гидра- |
|
тация цемента. Вследствие негативного влияния этих факторов рас- |
|
пределенный |
поверхности сыпучий материал необходимо неза- |
медлительно обра атывать. |
|
Трет й |
в применении ресайклеров-стабилизаторов, |
состоит |
|
снабженных встроенным распределителем сыпучего вяжущего мате- |
|
риала. Одн м з так х ресайклеров-стабилизаторов является модель |
|
WR 2500 SK, которая представляет собой удлиненную версию стан- |
способ
дартного ресайклера.АРесайклер WR 2500 SK имеет бункер вместимостью 4 м3, из которого цемент или известь через шлюзовой затвор равномерно распределяется по поверхности дороги перед самой смеси-
тельной камерой фрезерно-смесительногоДбарабана [118]. Достоинством этого способа является отсутствие пыления и независимость от погодных условий. Такая система позволяет выполнять точное дозирование вяжущих в количестве 2 – 6%, а также менее 2% [118] .
В РФ ресайклер-стабилизатор WR 2500 SK апробирован при ремонте дороги «Нагорье – Кубринск – ГраницаИМосковской области», расположенной в Переславском муниципальном районе Ярославской области. Оценивая качество работ, выполняемых при помощи этой машины, специалисты отмечают практически полное отсутствие пыли при стабилизации. Вследствие этого отметим, что применение ре- сайклеров-стабилизаторов, снабженных встроенной системой дозирования вяжущих, позволяет повысить технологичность холодного ресайклинга.
227
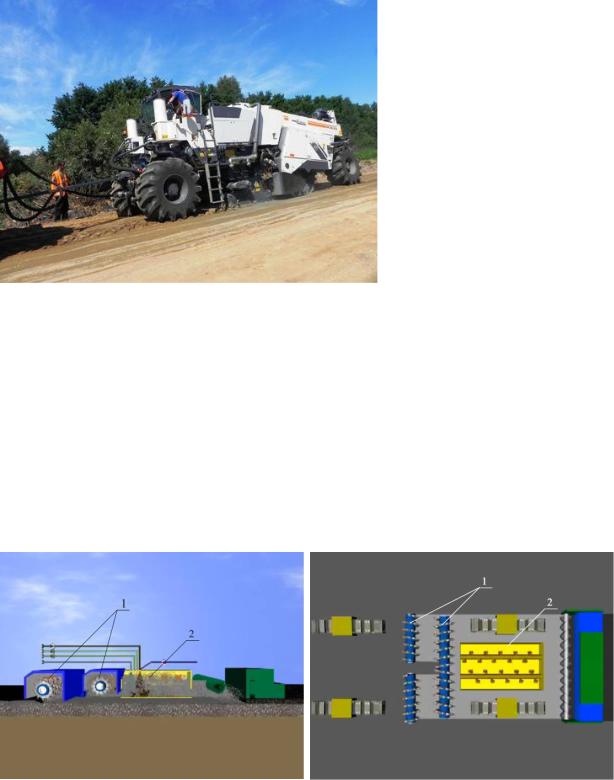
|
|
|
|
На рис. 113 пред- |
|||
|
|
|
|
ставлена операция рас- |
|||
|
|
|
|
пределения |
|
цемента |
|
С |
|
|
встроенным |
распреде- |
|||
|
|
лителем |
непосредст- |
||||
|
|
венно перед |
фрезерно- |
||||
|
|
|
|
||||
|
|
|
|
смешивающим |
бараба- |
||
|
|
|
|
ном. |
|
|
|
Рис |
|
|
Четвертый |
способ |
|||
|
|
кардинально |
отличает- |
||||
|
|
|
|
||||
|
|
|
|
ся от первых трех тем, |
|||
|
|
|
|
что в |
материал или |
||
. 113. Распределен е сухого цемента встроен- |
грунт вводится цемент- |
||||||
|
арабана |
|
но-водная суспензия, а |
||||
ным распредел телем ресайклера-стабилизатор |
|||||||
WR 2500 SK |
|
|
|
несухоевяжущее. |
|||
Цементно-водную суспензию впрыскивают в смесительную ка- |
|||||||
меру фрезерно-смеш вающего |
|
непосредственно во время |
|||||
ресайкл нга (р с. 109). Эта операция выполняется при помощи сме- |
|||||||
|
А |
|
|
|
|||
сительной установки, один из вариантов которой выпускается фир- |
|||||||
мой Wirtgen (модель WM 1000). Мобильный прицепной смеситель |
|||||||
WM 1000 применяется для получения суспензии и ее подачи по |
|||||||
шлангу в ресайклер. Как правило, эта установка работает в сцепке с |
|||||||
|
Д |
||||||
ресайклером WR-4200, на котором за фрезерно-смешивающими бара- |
|||||||
банами установлена двухвальная лопастная мешалка (рис. 114 и 115). |
|||||||
|
|
|
И |
||||
Рис. 114. Схема работы ресайклера |
Рис. |
115. |
Схема |
фрезерно- |
|||
WR-4200: 1 – фрезерно-смешивающие |
смешивающих барабанов (1) и двух- |
||||||
барабаны; 2 – двухвальная лопастная |
вальной лопастной мешалки (2) ре- |
||||||
мешалка |
|
сайклера WR-4200. |
|
|
|
228
Такая технология исключает пылеобразование на месте производства работ, повышает точность дозирования и качество смешения
измельченного материала. Смесительная установка WM-1000 оснащена бункером для цемента ёмкостью 25 м3 и баком для воды ёмкостью 11 м3. Установка WM-1000 была специально разработана для предварительного смешивания цемента с водой с получением це- ментно-водной суспензии. Вода добавляется в количестве, которое необход мо для дост жения оптимальной для уплотнения влажности грунта. Пр готовленная суспензия перекачивается в ресайклер, где вводится в рабочую камеру через специальную рампу. Водоцемент-
Сное отношен е составляет 1:1, но в большом числе случаев ресайклинга воды требуется ольше для гарантии оптимального уплотнения.
бенпривысок х расходах (> 4%) и больших глубинах ресайклинга (>
Применен е цементно-водной суспензии является самым точным способом распределен я цемента по всему материалу для ресайклинга. Он рекомендуется при лю ом расходе цемента, но особенно удо-
большое ме того, при малых Арасходах, как это зачастую имеет место при ре-
200 мм), когда уже даже крупные распределители не могут обеспе-
чить такое количество вяжущего на единицу площади. Кро-
сайклинге с органическим вяжущим, предпочтительнее лучше всего использовать распределение цементно-водной суспензии, чтобы гарантировать равномерное распределение цемента по всему материалу.
Равномерное перемешиваниеДматериалов позволяет добиваться наилучшей однородности смеси. Исследования показали, что качество смешивания материалов в больших ресайклерах сравнимо с качеством, получаемым в стационарных асфальтосмесительных установках, но при условии, что подача (скорость) машины соответствует особенностям места работы (обычно она составляет от 6 до 12Им/мин) [118].
За уплотненной поверхностью устраивают уход, к которому выдвигаются разные требования. Норматив РФ [121, п. 9.2] допускает открытие движения сразу же после уплотнения АГБ-смесей с добавлением минерального вяжущего. Стандарты Wirtgen регламентируют уход за поверхностью стабилизированного цементом слоя после его укладки в течение по меньшей мере 7 дней. При этом поверхность рекомендуется непрерывно смачивать водой из автоцистерны, оборудованной распределительной рампой достаточной ширины. В тех случаях, когда по уложенному слою необходимо открывать движение, его поверхность обрабатывают пленкообразующим материалом [118].
229
Таким образом, выполненный анализ показал, что успех применения технологий холодного ресайклинга во многом зависит от:
– Тщательности подбора состава смеси при лабораторных исследованиях.
– облюдения требований к каждой технологической операции,
Сприемки работ.
выполняемой на каждом этапе.
– Правильной организации работ не допускающей разрывов во
времени.
– Тщательности контроля качества всех поступающих |
материа- |
лов и при выполнен каждой технологической операции, |
а так же |
Поэтому весьма важно о судить требования, выдвигаемые стан-
РФ к каждой технологической операции, и правила организации работ, связанные с вы ором ведущей машины и определением
работ нове проекта, имеющегосяАу него в наличии оборудования и выбран-
темпов работ.
В соответств с рекомендациями [121, п. 8.1] при выборе техно- |
|
дартами |
учитывают цель ремонта, кате- |
логической схемы про зводства |
|
горию автомоб льной дороги, конструкцию дорожной одежды и ее |
|
состояние. Технологическую схему разрабатывает подрядчик на ос- |
ного типа АГБ-смеси.
В соответствии с выполненным анализом технологий холодного ресайклинга операция фрезерованияДможет быть отделена от остальных технологических процессов.
При такой технологии «поезд» комплектуют в соответствии с одним из трех вариантов [8, 145].
В соответствии с первым вариантом в состав специализированного потока включают:
1. Фрезу, укомплектованную транспортером, выполняющую фрезерование существующего покрытия и подачу АГБ в смеситель-
укладчик.
генерированную смесь.
2. Смеситель-укладчик, приготавливающийИи укладывающий ре-
3. Катки, выполняющие уплотнение смеси.
В этом случае фрезерной машиной выполняют фрезерование асфальтобетонных слоев на требуемую глубину. Асфальтобетонный гранулят, полученный фрезерованием, по транспортеру, которым укомплектована фреза, подают в приемный бункер смесителяукладчика. Из приемного бункера гранулят поступает в двухвальную
230
мешалку горизонтального типа, где перемешивается с органическим вяжущим. Готовую смесь укладывают и уплотняют катками. В результате изготавливают новый регенерированный слой покрытия.
В соответствии со второй технологической схемой фреза работает в сцепе со смесителем-укладчиком, который является ведущей машиной. Производительность смесителя-укладчика меньше производительности фрезы. Поэтому организация сцепки смесителя и фрезы
Скак м н мум в три раза [121, п. 8.2]. Смеситель-укладчик снабжен двумя скользящ ми уш рителями, что позволяет варьировать ширину укладки от 2,4 до 4,2 м. Вследствие этого минимальная ширина фрезерован я должна составлять 2,4 м.
влечет за собой скусственное занижение производительности фрезы,
При необход мости использования фрезы на полную мощность ее применяют раздельно со смесителем-укладчиком. При такой технологической схеме специализированный отряд комплектуют че-
тырьмя маш |
: |
||
нами |
|||
1. |
Фрезой, ра отающей независимо от смесителя укладчика. |
||
2. |
Подборщ ком, выполняющим подбор фрезерованного мате- |
||
риала и его подачу в смеситель-укладчик. |
|||
3. |
Смесителем укладчиком, который приготавливает и укладыва- |
||
ет смесь. |
|
|
|
4. |
Катками, уплотняющими приготовленную и уложенную смесь. |
||
|
|
бА |
В этом случае фреза по транспортеруДподает АГБ на смежную полосу проезжей части, укладывая асфальтовый гранулят в валик, который имеет форму призмы. Подбор ГБ выполняется подборщиком, работающим в связке со смесителем-укладчиком. Подборщик по транспортеру направляет смесь в приемный бункер смесителяукладчика. При такой организации работ производительностьИфрезы не зависит от производительности смесителя-укладчика.
При необходимости выполнения выравнивающего фрезерования фрезу ставят в одно звено с автомобилями-самосвалами, которые транспортируют АГБ к смесителю-укладчику, а избыток фрезерованной смеси перевозят на склад или другой параллельно ремонтируемый объект. При такой схеме работ производительность фрезы можно не увязывать с производительностью смесителя-укладчика. Для этого необходимо АГБ складировать на притрассовых складах. з этих складов АГБ отгружают погрузчиком в автомобили-самосвалы и направляют к смесителю-укладчику.
231
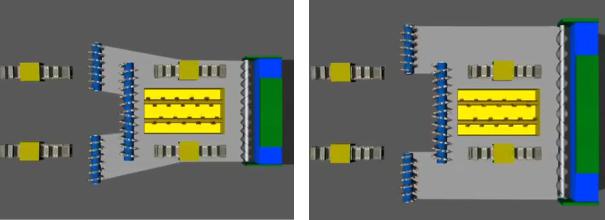
В соответствии с указаниями [121] наиболее дешевым и технологичным является второй вариант.
Технологическая схема, предусматривающая совмещение всех основных операций одной машиной, предусматривает применение гусеничного ресайклера, например WR-4200. Помимо фрезерносмешивающих барабанов и мешалки этот ресайклер снабжен распределительным шнеком и уплотнительным рабочим органом. В отличие от ресайклеров на колесном ходу гусеничные машины укомплектова-
ны распредел тельным шнеком и уплотнительным рабочим органом. |
|||
Поэтому так е ресайклеры могут распределять и уплотнять смесь. |
|||
Кроме того, WR-4200 снабжен вторым раздвижным ротором, благо- |
|||
С |
|
|
|
даря чему рабочую ш рину можно изменять от 2,8 до 4,2 м. |
|||
На р с. 116 |
117 приведена схема работы раздвижных роторов и |
||
схема работы |
макс мальной ширине регенерации покрытия. |
||
при |
|
||
бА |
|||
Рис. 116. Схема работы раздвижных |
Рис. 117. Схема работы на полную ши- |
||
роторов при уширении раздвижных |
рину после раздвижки распредели- |
||
тельного шнека и уплотнительного ра- |
|||
фрезерных барабанов |
|||
бочего органа |
|||
|
|
||
При применении гусеничных ресайклеров они являются ведущей |
|||
машиной. |
|
Д |
|
|
|
||
Перемешивание АГ с добавками осуществляется под кожухом |
|||
|
|
И |
|
фрезерного барабана, а для укладки АГБ-смеси имеется навесное |
|||
оборудование, аналогичное установленному на обычных асфальтоук- |
|||
ладчиках. |
|
|
|
В комплекте с этой машиной работает автоцистерна для транс- |
|||
портировки, хранения и подачи органического вяжущего или машина |
|||
для приготовления и подачи цементной суспензии. |
|||
Глубина фрезерования достигает 30 см. |
Ресайклер укомплектован дозаторами воды и органических вяжущих, а также специальным прижимным устройством, которое при
232
фрезеровании исключает образование в АГ крупных кусков асфальтобетона. Вибротрамбующий рабочий орган позволяет достичь высокой степени предварительного уплотнения смеси [121].
Также для холодного ресайклинга применяются колесные ре- сайклеры-стабилизаторы. Эти машины при ресайклинге асфальтобетонных покрытий уступают описанным выше, но могут применяться при укреплении грунтов. То есть, имея более широкую область применен я, ресайклеры-стабилизаторы дают несколько худшее качество
регенерац |
асфальтобетонных покрытий. |
|
||
Как |
ло, стаб лизатор |
работает по двухпроходной схеме. |
||
При первом проходе фрезеруется дорожная одежда на заданную глу- |
||||
С |
|
|
|
|
бину, автогрейдер разравнивает призмы АГ. Затем при повторном |
||||
проходе стаб л затор осуществляет перемешивание АГ с добавками |
||||
управляемыми |
|
|
||
[121]. |
|
|
|
|
Доз ровка б тума, |
эмульсии и воды осуществляется насосами, |
|||
|
кропроцессорами, цементной суспензии – насосом |
|||
суспензатора. |
|
|
|
|
Перемеш ван е |
с до авками происходит под кожухом фре- |
|||
зерного барабана [121]. Регулируемый по высоте зачистной отвал, |
||||
расположенный за фрезерным |
|
, улучшает качество пере- |
||
|
арабаном |
|
||
мешивания [121]. |
|
|
|
|
В отличие от гусеничных ресайклеров колесный стабилизатор не |
АГ и предварительного уплотнения смесиД. Смесь разравнивает автогрей-
имеет специального оборудования для распределения, выглаживания
дер. Отсюда ровность слоя и соответствие заданному поперечному профилю будет ниже, чем по предыдущим схемам [121].
К технологическим операциям нормативные документы РФ [120, 121] выдвигают определенные требования.
Для фрезерования покрытия различные зарубежные фирмы предлагают большое число фрез, отличающихся по ширине фрезерного барабана, мощности двигателя, глубине фрезерования и другим параметрам. Многие из них оснащены устройствами для сбора АГ и по-
грузки его в автомобили-самосвалы. |
И |
|
|
При выполнении выравнивающего фрезерования фреза должна |
|
быть оснащена автоматикой, которая позволяет работать по струне |
|
или с нивелировочной балкой длиной 5 – 7 м. Такая балка поставля- |
|
ется производителями по отдельному заказу. |
|
Струну натягивают на металлические штыри, установленные с шагом 10 – 20 м и на некотором расстоянии от оси или кромки по-
233
крытия. Расстояние от струны до оси или кромки зависит от конструкции следящего устройства.
Первый проход фрезы выполняют по струне, установив требуемые глубину фрезерования и уклон фрезерного барабана, а последующие – используя копир, скользящий по выровненной поверхности
Снижележащего слоя [121].
Перед выравнивающим фрезерованием целесообразно произвести выравн вающую подсыпку покрытия в местах, где это предусмотрено проектом, спользуя АГ или асфальтобетонную смесь. Вы-
нияравнивающую смесь пр катывают [121].
Направлен е вращения фрезерного барабана зависит от глубины выравн вающего фрезерования hв или глубины регенерационного
фрезерован я hp толщины пакета асфальтобетонных слоев hc [121]:
- при выравн вающем фрезеровании, когда hв< hc, и регенерационном фрезерован , когда не захватывается слой несвязного основа- (hв + hp < hc), вращение фрезерного барабана осуществляется
«сверху - вн з» по отношению к направлению движения потока;
- в случаях, когда hв ≥ hc или hв + hp ≥ hc, т.е. граница фрезеро- |
|||
|
|
АГ |
|
вания проходит между асфальто етонным и несвязным слоями или |
|||
ниже с захватомбматериала последнего, вращение фрезерного бараба- |
|||
на осуществляется «снизу - вверх». |
|
||
Зерновой состав |
зависит от ряда факторов; |
||
1. |
Конструкции фрезерного органа. |
|
|
2. |
Скорости вращения фрезерного барабана. |
||
3. |
Рабочей скорости движения фрезы. |
|
|
4. |
Глубины фрезерования. |
И |
|
5. |
Типа асфальтобетона. |
Чем тоньше задняя щель подДкожухом фрезерного барабана, тем сильнее измельчается гранулят. Это связано с тем, что чем тоньше щель, тем дольше задерживается гранулят под кожухом фрезерного барабана.
Максимальный размер АГ не может быть мельче максимального размера щебня, входящего в состав АГ. Чем выше скорость вращения фрезерного барабана, тем мельче АГ по гранулометрии. Обычно при фрезеровании толстых покрытий (более 15 см) используют первую скорость; покрытий средней толщины (8 – 15 см) – вторую скорость; тонких покрытий (менее 8 см) – третью скорость [121].
Чем прочнее покрытие, тем более низкая скорость вращения фрезерного барабана требуется для измельчения асфальтобетона [121].
234

Третий контролируемый фактор – рабочая скорость фрезы. Чем она меньше, тем мельче получается АГ [121].
Карта трудового процесса [146] для срезки асфальтобетонного по-
|
крытия |
фрезой |
Виртген W-2200 или W-4200 предусматривает |
||||||
|
7 технологических операций, указанных в табл. 71, где представлены |
||||||||
С |
|
|
|
|
|
||||
|
приемытрудапри применениифрезыВиртгенW-2200илиW-4200 [146]. |
||||||||
|
|
|
|
|
|
|
|
Таблица 71 |
|
|
|
Пр емы труда по срезке асфальтобетонного покрытия фрезой |
|||||||
|
Номер |
на менова- |
|
|
|
|
|
||
|
дений |
Характеристика приемов труда |
|
||||||
|
ние операц й |
|
|
|
|
|
|
||
|
1. Установка ограж- |
|
М1 и М2 производят расстановку временных огражде- |
|
|||||
|
|
|
|
|
|
н й и дорожных знаков согласно схеме. |
|
||
|
|
|
|
|
|
М1 и М2 производят осмотр машины, проверяют нали- |
|
||
|
2. Подготовка фрезы |
|
ч е горюче-смазочных материалов, воды в водоороси- |
|
|||||
|
к работе |
|
|
|
|
тельной установке, состояние зубьев в барабане прове- |
|
||
|
|
|
|
|
|
ряют резь овые соединения |
|
|
|
|
|
|
|
|
|
М1 и М2 прицепляют навесной щебнераспределитель к |
|
||
|
3. Россыпь |
|
пе- |
|
подъехавшему автосамосвалу, подают сигнал водителю |
|
|||
|
ред фрезой |
|
|
|
А |
|
|||
|
|
|
|
для поднятия кузова и движения машины, следуют за |
|
||||
|
|
|
|
|
|
машиной, следя за равномерной россыпью щебня |
|
||
|
|
|
щебня |
|
|||||
|
|
|
|
|
М2 - управляет машиной, следит за ее ходом. |
||||
|
|
|
|
|
|
М1 - на людает за всей работой фрезы, контролирует |
|
||
|
|
|
|
|
|
толщину срезаемого слоя, делая контрольные замеры |
|
||
|
4. Срезка асфальто- |
|
толщины сантиметром и в случае отклонений от нормы с |
|
|||||
|
бетонного покрытия |
|
помощью ручного маховика настраивает машину на тре- |
|
|||||
|
|
|
|
|
|
буемую величину; убирает со срезаемой поверхности |
|
||
|
|
|
|
|
|
посторонние предметы; по необходимости метлой сгре- |
|
||
|
|
|
|
|
|
бает разбросанный щебень в зону работы фрезы |
|
||
|
|
|
|
|
|
М2 - выключает машину. |
И |
|
|
|
|
|
|
|
|
М1 - достает необходимый инструмент, ведра с новыми |
|
||
|
|
|
|
|
|
зубьями для заменыДизношенных, открывает крышки ба- |
|
||
|
5. Замена изношен- |
|
рабанов, включает барабаны на малое вращение. |
|
|||||
|
|
М1 и М2 - при помощи металлических штырей и тяже- |
|
||||||
|
ных зубьев на новые |
|
|
||||||
|
|
|
|
|
|
лого молотка выбивают из ячеек изношенные зубья, |
|
||
|
|
|
|
|
|
вставляя на их место новые; собирают и убирают инст- |
|
||
|
|
|
|
|
|
румент на место, закрывают барабаны, предварительно |
|
||
|
|
|
|
|
|
выключив их |
|
|
|
|
6. Заправка фрезы |
|
|
М1 - выключает машину, открывает крышки емкостей. |
|
||||
|
дизельным топливом |
|
М1 подает шланг М2 и заправляют машину, следя за на- |
|
|||||
|
и водой |
|
|
|
|
полнением соответствующих емкостей |
|
||
|
7. Снятие временных |
|
М1 и М2 - снимают с прежних мест временные огражде- |
|
|||||
|
ограждений и дорож- |
|
ния и дорожные знаки и переставляют их согласно схеме |
|
|||||
|
ных знаков |
|
|
|
на новые места |
|
|
235
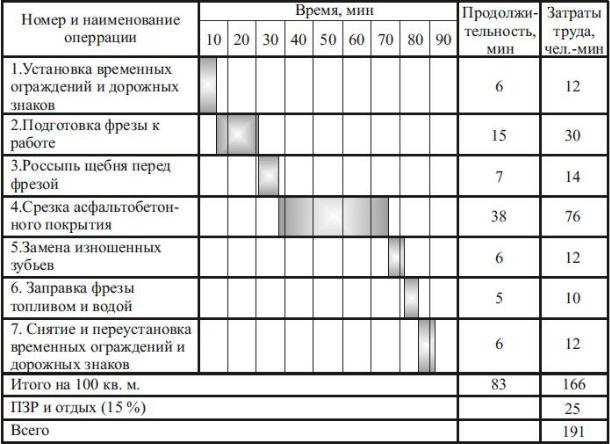
На рис. 118 представлен график трудового процесса [146].
Си
Рис. 118.бАГрафик трудового процесса фрезы W-2200 Виртген W-4200
В процессе фрезерования покрытияДзубья фрезерного барабана изнашиваются [121]. Замена зубьев является дорогостоящей операцией и фактором, снижающим производительность. На износ зубьев влияют твердость асфальтобетона, глубина фрезерования, температура покрытия и др. Наиболее благоприятнаяИтемпература для работы зубьев 10 – 30 °С [121]. В среднем через каждые 10 тыс. м2 покрытия требуется замена всех зубьев [121]. На сильный износ зубьев указывает самопроизвольное снижение рабочей скорости фрезы. Работа с изношенными зубьями может привести к повреждению держателей зуба. Зубья необходимо проверять через каждые 2 ч [121].
Во время инспектирования заменяют наиболее изношенные или разрушенные зубья. Обычно причиной разрушения является попадание зуба на захороненные в покрытие металлические предметы или крупные камни.
Зубья извлекают из держателя или вставляют в него при помощи специального съемника, входящего в состав инструмента.
236
До начала основных работ, в обязательном порядке, необходимо выполнить постройку пробного участка. Устройство пробного участка необходимо для:
1. Уточнения гранулометрического состава АГ и его корректировки в случае отличия от установленного лабораторией при подборе состава АГБ. Корректировка зернового состава АГ может быть вы-
Стики ее зменен я в течение дня. Такие данные позволяют рассчитывать необход мое кол чество воды, требуемое для увлажнения АГ до оптимальной влажности, которая необходима для приготовления и уплотнен я АГБ-смеси [120, 121]. Отметим, что в соответствии с ру-
полнена варьированием контролируемых параметров фрезерования.
2. Определен я влажности АГ после фрезерования, а также кине-
ководством [118] для АГБ-смесей понятие оптимальной влажности заменяется понят ем оптимального содержания жидкой фазы, кото-
рую составляет вода |
итумная эмульсия. |
|
3. |
качества перемешивания. |
|
Оценки |
||
4. Уточнен я опт мальной влажности АГБ-смеси для опытного |
||
состава АГ. Нео ход мость определения оптимальной влажности |
||
продиктована тем, что уплотнение образцов в лабораторных условиях |
||
отличается от укатки смеси в условиях постройки слоя. В соответст- |
||
вии с указаниями [118] методика определения оптимальной влажно- |
||
сти АГБ-смеси аналогична про ной укатке грунтов, регламентируе- |
||
мой [147], но имеет определенные отличия. При определении опти- |
||
мальной влажности Wо |
на пробном участке укладывают три секции с |
|
|
бА |
|
разным содержанием воды, а на следующий день, после испарения |
||
воды, |
определяют плотность ГБ. Кроме этого, при уплотнении вни- |
|
мательно следят за поверхностью слоя и вальцом катка, что позволяет |
||
сделать ориентировочные выводы о превышении влажности АГБ ее |
||
оптимального значения. Дело в томД, что при избыточном увлажнении |
||
перед вальцом катка образуется волна и смесь начинает налипать на |
||
него. В лаборатории определяется значение оптимальной влажности. |
Для этого под давлением 3 МПа формуют образцыИиз смесей с разным содержанием воды. Критерием является средняя плотность, которая при оптимальной влажности имеет максимальное значение.
5. Определения плотности АГБ, которая является главным параметром для оценки качества АГБ. Плотность АГБ зависит от большого числа факторов, в том числе от температуры АГБ в момент уплотнения. Чем выше температура АГБ при уплотнении, тем выше плотность АГБ. Установление реально достижимой плотности (базовой)
237

позволяет в дальнейшем осуществлять оперативный контроль качества приготовления и уплотнения АГБ-смеси.
6. Определения толщины укладываемого слоя. Чтобы получить после укатки требуемую толщину регенерированного слоя, при использовании в качестве ведущих машин смесителя-укладчика или ре- Ссайклера необходимо правильно отрегулировать высоту выходной
щели этого устройства. Такая регулировка выполняется с учетом запаса на уплотнен е, фактическая величина которого может быть ус-
тановлена только при пробном уплотнении. ниеИспользован е технологий, в которых операция фрезерования
отделена от остальных технологических процессов, позволяет совместить выравн вающее и регенерационное фрезерование. Для этого фрезерный бара ан настраивают на требуемые отметки дна корыта, которое соответствует подошве регенерируемого слоя. Получаемый излишек АГ в местах, где предусмотрено выравнивающее фрезерова-
, перемещают автогрейдером на обочину или автомобилямисамосвалами на пр трассовый склад с целью последующего исполь-
зования на участках, где не хватает Г для регенерации слоя. |
|
А |
|
После фрезерования всей ремонтируемой половины проезжей |
|
части призмыбАГ планируют автогрейдером. |
планировки по- |
Схема |
|
верхности |
АГ приведена на |
рис. 119. При выполнении |
|
планировки поверхности слоя |
|
из АГ число проходов грей- |
|
дера должно быть сведено к |
|
минимуму. Это требуется для |
|
И |
|
того, чтобы перед регенера- |
|
Дцией не уплотнять слой АГ. |
При планировке необходимо создать слой равномерной
Рис. 119. Схема планировки поверхности АГ толщины с требуемым попе-
автогрейдером |
речнымуклоном. |
|
Если пробным строительством установлена необходимость корректировки зернового состава АГ, новый минеральный материал распределяют по покрытию. Добавление нового материала следует выполнить до, а не после фрезерования. Это требование связано с тем, что проезды построечного транспорта по слою АГ вызывают слипание гранул.
238
Кроме того, при совмещении выравнивающего и регенерационного фрезерования толщина слоя АГ по ширине получается неодинаковой, что существенно осложняет и делает практически невозможным соблюдение требуемой пропорции между объемами АГ и нового
материала.
САГБ, а в случае х несоответствия требованиям [120, 121] от техноло- , предусматр вающей совмещение выравнивающего и регенера-
Такие затруднения отпадают в случае раздельного выравнивающего и регенерационного фрезерования. В этом случае распределение нового матер ала выполняют после выравнивающего фрезерования. Таким образом, соблюдение требуемой пропорции между объемами АГ новым матер алом требует тщательного контроля параметров
гииционного фрезерован я, следует отказаться. В этом случае вначале выполняют выравн вающее фрезерование. Затем на поверхность АГ подают обогащающ й материал и производят регенерационное фрезерован е, после чего поверхность слоя планируют автогрейдером.
Очередность регенерационного фрезерования откладывается и
тогда, когда |
устройство выравнивающего слоя. В этом слу- |
чае перед регенерационным фрезерованием завозят требуемое коли- |
чество АГ или асфальто етонной смеси, которые распределяют авто- |
|
требуется |
|
грейдером. Выравнивающий слой прикатывают катком. Прикатка вы- |
|
равнивающего слоя выполняется для того, чтобы пустить по нему |
|
построечный транспорт, соблюдать требования по коэффициенту уп- |
|
лотнения не нужно. |
А |
|
|
При использовании для устройства выравнивающего слоя горя- |
|
чей асфальтобетонной смеси ее состав должен быть близок к компо- |
|
нентному составу АГ. |
|
Средняя плотность пакета асфальтобетонных слоев существую- |
|
|
3 |
щей дорожной одежды составляетД2,30 – 2,40 г/см , а плотность слоя |
|
АГБ обычно находится в пределах 2,10 – 2,20 г/см3. Поэтому толщина |
регенерированного слоя из АГБ всегда больше глубины регенерационного фрезерования.
И
Соотношение между толщинами сфрезерованного слоя и слоя из АГБ, при полном использовании АГ в последнем, определяют по
формуле [121]:
h |
hа 100 Д а |
, |
(16) |
|
|||
р |
р |
|
|
|
|
239
где hр – толщина уплотненного регенерированного слоя, см; ha – глубина регенерационного фрезерования (толщина сфрезерованного слоя без учета выравни-
вающего фрезерования), |
см; Д – массовая доля добавок, |
исключая воду, % |
|||
(сверх 100% АГ) (в смесях с цементом его долю увеличивают в 1,3 раза с учетом |
|||||
воды, вступающей в реакцию); a |
и р – средние плотности пакета слоев старого |
||||
покрытия и регенерированного слоя (после высыхания), соответственно, г/см3. |
|||||
Вследствие этой особенности при расчете дорожной одежды кон- |
|||||
струкцию проектируют на толщину уплотненного регенерированного |
|||||
слоя hр, а глуб ну регенерационного фрезерования ha определяют по |
|||||
формуле |
|
|
|
|
|
С |
h |
р hр |
. |
(17) |
|
|
|||||
а |
100 Д а |
|
|||
|
|
||||
Зав с мость (17) |
меет важнейшее значение при разработке про- |
||||
ектов для определен я |
ъемов |
. |
|
|
|
Необход мо меть в виду, что плотность регенерированного слоя |
|||||
является переменной |
|
|
и может в процессе работ изменяться |
||
величиной |
|
|
|
||
в пределах ± 0,05 г/см3. Вследствие этого толщина регенерированного |
|||||
слоя может коле аться в пределах ± 0,5 см, что соответствует преде- |
|||||
лам допускаемых отклонений при контроле качества. |
|
||||
Коэффициентыработзапаса на уплотнения зависят от способа разравни- |
|||||
вания АГБ-смеси. Так если |
ГБ-смесь разравнивается без предвари- |
тельного уплотненияАви роплитой, то толщина слоя в рыхлом теле должна быть примерно на 30% большеДтолщины слоя после окончательного уплотнения. Если ГБ-смесь разравнивается с предварительным уплотнением виброплитой, то после окончательного уплотнения толщина регенерированного слоя уменьшитсяпримерно на 6%.
В АГБ-смеси типа Э содержание воды выше оптимального. По-
2.Гладковальцовым катком массой 10 –И18 т при 3 – 5 проходах по одному следу.
3.Катком на пневматических шинах массой от 16 т и выше при 4 проходах по одному следу.
Укатку выполняют от краев к оси дороги, а затем в обратной по-
следовательности с перекрытием каждого следа. Уплотнение произ- водят до прекращения осадки слоя.испаряетсяпослеэтому6
240
При уплотнении первой полосы вальцы катка должны находиться на расстоянии 15 – 20 см от кромки сопряжения. Уплотнение второй полосы следует начинать с сопряжения. При уплотнении АГБ-смесей,
содержащих цемент, продолжительность укатки не должна превы- |
|||||
ПОС |
|
|
|
|
|
шать 3 ч от их приготовления. После прохода катка на пневмошинах |
|||||
иногда требуется окончательное выравнивание поверхности авто- |
|||||
грейдером. |
|
|
|
|
|
Технолог я |
организация работ проектируется при разработке |
||||
рукции |
|
|
|
||
(проект орган |
зац и работ) и ППР (проект производства работ), |
||||
которые разрабатываются до начала работ по ремонту или реконст- |
|||||
|
. |
|
|
|
|
В проектах пр водят [121]: |
|
|
|||
1. |
работ |
|
|||
хему орган зац и движения. |
|
|
|||
2. |
Расчетную среднюю |
очую скорость ведущей машины. |
|||
3. |
Технолог ческую схему |
с распределением механизмов |
|||
по захваткам. |
|
|
|
|
|
4. |
Дл ну сменной захватки, определяемую расчетом с учетом |
||||
|
|
А |
|||
минимального темпа ра от и производительности ведущей машины. |
|||||
5. |
Количество проходов ведущей машины по ширине проезжей |
||||
части и их последовательность. |
|
|
|||
6. |
Потребность в до авляемых материалах. |
||||
7. |
Мероприятия по выравниванию дорожной одежды (если они |
||||
предусмотрены основным проектом). |
|
|
|||
8. |
Места расположения складов |
Г (если это предусмотрено тех- |
|||
нологической схемой). |
|
|
И |
||
9. |
Мероприятия по контролю качества. |
Производительность машин,Двыполняющих работы по холодному ресайклингу, могут быть определены при использовании норм времени, регламентируемых методическим документом [148].
При использовании в качестве ведущей машины смесителяукладчика или ресайклера смежные полосы укладывают впритык. В остальных случаях необходимо их перекрытие.
Минимальная ширина перекрытия смежных полос должна быть на 5 см больше толщины регенерированного слоя.
Применение машин с изменяемой шириной укладки позволяет свести к минимуму число проходов и минимизировать ширину перекрытия полос, где оно предусмотрено.
241
При использовании ведущей машины, требующей предварительного фрезерования покрытия, дневная захватка будет состоять из двух частных захваток: на первой будет работать фреза, а на второй – ведущая машина (например, смеситель-укладчик). Общая длина дневной захватки в этом случае может превысить 1 км.
Если АГБ-смесь содержит цемент, в качестве ведущей машины используют смеситель-укладчик или ресайклер (не выполняющие операц ю фрезерован я).
При необход мости выравнивания покрытия по схеме, исклю- |
|||
чающей совмещен е выравнивающего и регенерационного фрезеро- |
|||
вания, оно может осуществляться или на первой частной захватке, |
|||
С |
|
|
|
последовательно с регенерационным фрезерованием, или должно |
|||
провод ться с опережением основного потока. |
|||
спользован |
АГБ-смесей |
без добавления минерального |
|
вяжущего дв жен е по регенерированному слою может быть открыто |
|||
сразу же после окончан я уплотнения. |
|
|
|
При |
с добавлением минерального |
||
При спользован |
АГБ-смесей |
||
вяжущего дв жен е также может |
|
открыто сразу после оконча- |
|
ния уплотнения. Однако при высыхании поверхности возникает пы- |
|||
лимость. В таких случаях следует периодически слегка увлажнять по- |
|||
быть |
|
||
верхность регенерированного слоя. |
|
|
|
Для слоев, содержащих эмульсию, устройство замыкающего слоя |
|||
А |
или слоя усиления поверх регенерированногоДслоя целесообразно отложить на 2 – 3 недели, что позволяет последнему лучше сформироваться под воздействием движения транспорта.
На слоях с минеральным вяжущим под действием движения автомобилей могут появиться дефекты в виде шелушения и выбоин. Поэтому устройство замыкающего слоя или слояИусиления не следует откладывать более чем на 3 недели.
Перед устройством замыкающего слоя или слоя усиления поверхность регенерированного слоя подгрунтовывают.
Замыкающий слой или слой усиления может быть уложены при необходимости через 48 ч после регенерации нижележащего слоя.
В табл. 72 и 73 приведены технические характеристики дорожных фрез и ресайклеров, применяемых при холодной регенерации асфальтобетонных покрытий методом ресайклирования.
242
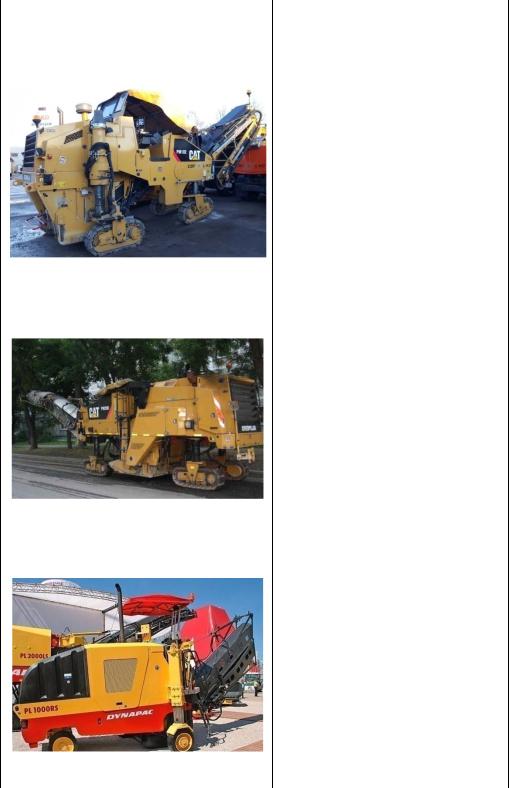
|
Технические характеристики дорожных фрез |
Таблицы 72 |
|||
|
|
|
|||
|
Общий вид |
Техническая характеристика |
Величина |
|
|
|
|
|
|
|
|
1 |
|
2 |
3 |
|
|
С |
Торговая марка |
Caterpillar |
|
||
Модель |
|
PM102 |
|
||
|
|
|
|
||
|
|
Масса, т |
|
17,1–17,6 |
|
|
|
Тип ходовой части |
Гусеничная |
|
|
|
и |
Двига- |
Модель |
Cat 3126B |
|
|
ATAAC |
|
|||
|
тель |
|
|
||
|
Мощность, кВт |
168 |
|
||
|
|
|
|||
|
|
|
|
||
|
|
Ширина фрезерования, мм |
1000 |
|
|
|
|
Глубина фрезерования, мм |
305 |
|
|
|
|
Количество резцов, единиц |
98 |
|
|
|
|
Шаг резцов, мм |
15 |
|
|
|
|
Ра очая скорость, м/мин |
0–27 |
|
|
|
|
Торговая марка |
Caterpillar |
|
|
|
|
Модель |
|
PM200 |
|
|
|
Масса, т |
|
30 |
|
|
|
Тип ходовой части |
Гусеничная |
|
|
|
|
Двига- |
Модель |
Cat C18 |
|
|
|
ACERT |
|
||
|
|
тель |
|
|
|
|
|
Мощность, кВт |
429 |
|
|
|
|
|
|
||
|
|
Ширина фрезерования, мм |
2010 |
|
|
|
|
Глубина фрезерования, мм |
320 |
|
|
|
|
Количество резцов, единиц |
178 |
|
|
|
бА |
|
|
||
|
|
Шаг резцов, мм |
15 |
|
|
|
|
Рабочая скорость, м/мин |
0–38 |
|
|
|
|
Торговая марка |
Dynapac |
|
|
|
|
Модель |
|
PL1000RS |
|
|
|
Масса, т |
И |
|
|
|
|
|
13,2 |
|
|
|
|
Д |
|
||
|
|
Тип ходовой части Колесная |
|||
|
|
|
|
Cummins |
|
|
|
Двига- |
Модель |
QSB 5.9-30- |
|
|
|
тель |
|
TAA |
|
|
|
|
Мощность, кВт |
129 |
|
|
|
Ширина фрезерования, мм |
1000 |
|
|
|
|
Глубина фрезерования, мм |
250 |
|
|
|
|
Диаметр фрезы, мм |
832 |
|
|
|
|
Рабочая скорость, м/мин |
0–30 |
|
243
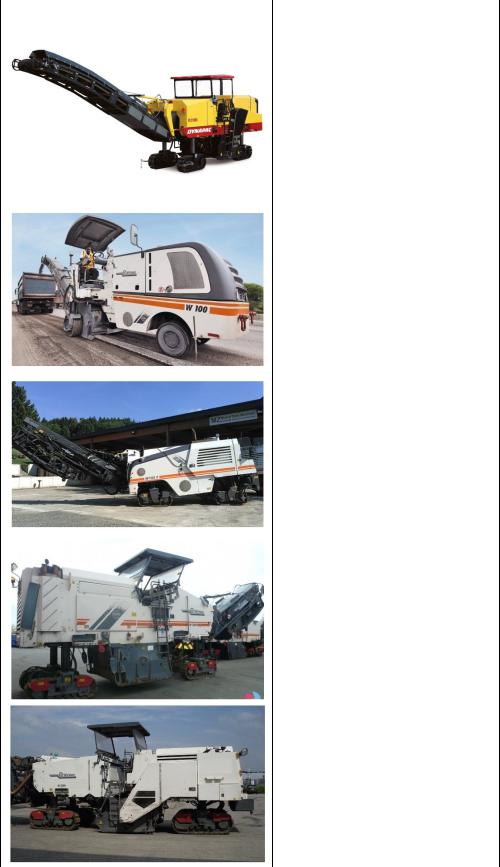
|
|
|
Окончание табл. 72 |
||
|
1 |
2 |
|
3 |
|
|
|
Торговая марка |
|
Dynapac |
|
|
|
Модель |
|
PL2100S |
|
|
|
Масса, т |
|
33,9 |
|
|
|
Тип ходовой части |
Гусеничная |
|
|
|
|
Мощность двигателя, кВт |
447 |
|
|
|
|
Ширина фрезерования, мм |
2100 |
|
|
|
|
Глубина фрезерования, мм |
320 |
|
|
|
|
Диаметр фрезы, мм |
1100 |
|
|
|
|
Рабочая скорость, м/мин |
0–40 |
|
|
С |
Торговая марка |
|
Wirtgen |
|
|
Модель |
|
W100 |
|
||
|
|
Масса, т |
|
15,0 |
|
|
|
Тип ходовой части |
Колесная |
|
|
|
Глубина |
|
155 |
|
|
|
и |
Мощность двигателя, кВт |
|
||
|
Ширина фрезерования, мм |
1000 |
|
||
|
фрезерования, мм |
300 |
|
||
|
|
Ра очая скорость, м/мин |
0–30 |
|
|
|
|
Торговая марка |
|
Wirtgen |
|
|
|
Модель |
|
W100F |
|
|
|
Масса, т |
|
20,8 |
|
|
|
Тип ходовой части |
Гусеничная |
|
|
|
|
Мощность двигателя, кВт |
227 |
|
|
|
|
Ширина фрезерования, мм |
1000 |
|
|
|
|
Д |
320 |
|
|
|
|
Глубина фрезерования, мм |
|
||
|
А |
|
|
||
|
|
Рабочая скорость, м/мин |
0–32 |
||
|
|
Торговая марка |
|
Wirtgen |
|
|
|
Модель |
|
W2000 |
|
|
|
Масса, т |
|
32,2 |
|
|
|
|
И |
|
|
|
|
Тип ходовой части |
Гусеничная |
|
|
|
|
Мощность двигателя, кВт |
421 |
|
|
|
|
Ширина фрезерования, мм |
2000 |
|
|
|
|
Глубина фрезерования, мм |
320 |
|
|
|
|
Рабочая скорость, м/мин |
0-84 |
|
|
|
|
Торговая марка |
|
Wirtgen |
|
|
|
Модель |
|
W2200 |
|
|
|
Масса, т |
|
46,77 |
|
|
|
Тип ходовой части |
Гусеничная |
|
|
|
|
Мощность двигателя, кВт |
671 |
|
|
|
|
Ширина фрезерования, мм |
2200 |
|
|
|
|
Глубина фрезерования, мм |
350 |
|
|
|
|
Рабочая скорость, м/мин |
0-84 |
|
244
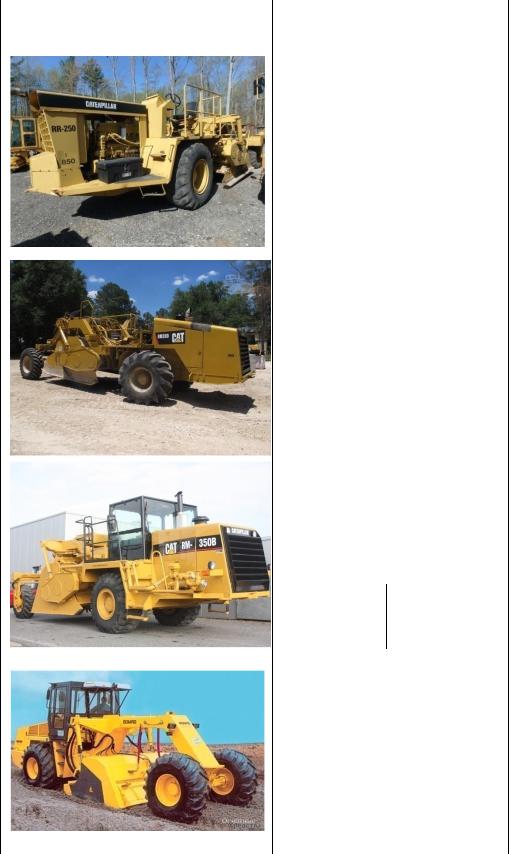
|
|
|
|
|
|
|
Таблицы 73 |
|
|
Технические характеристики ресайклеров-стабилизаторов |
|||||||
|
Общий вид |
|
Техническая характеристика |
Величина |
|
|||
|
|
|
|
|
|
|
|
|
1 |
|
|
2 |
|
3 |
|
||
С |
|
Торговая марка |
|
Caterpillar |
|
|||
|
Модель |
|
|
|
RR-250 |
|
||
|
|
|
|
|
|
|
||
|
|
|
Тип ходовой части |
Колесная |
|
|||
|
|
|
Мощность, кВт |
|
321 |
|
||
|
и |
Ширина обработки, мм |
2 438 |
|
||||
|
Глубина обработки, мм |
381 |
|
|||||
|
Габариты, |
длина |
9 525 |
|
||||
|
|
|
|
|||||
|
|
|
ширина |
3 454 |
|
|||
|
|
|
мм |
|
|
|
|
|
|
|
|
высота |
3 000 |
|
|||
|
|
|
|
|
||||
|
|
|
Ра очая скорость, м/мин |
27,6 |
|
|||
|
|
|
Торговая марка |
|
Caterpillar |
|
||
|
ГлубинаГа ариты, |
|
ширина |
3000 |
|
|||
|
|
|
Модель |
|
|
|
RM-300 |
|
|
|
|
Тип ходовой части |
Колесная |
|
|||
|
|
|
Мощность, кВт |
|
261 |
|
||
|
|
|
Ширина обработки, мм |
2438 |
|
|||
|
|
А |
457 |
|
||||
|
|
|
обработки, мм |
|
||||
|
|
|
|
|
длина |
10000 |
|
|
|
|
|
мм |
|
высота |
3500 |
|
|
|
|
|
Ра очая скорость, м/мин |
15,5 |
|
|||
|
|
|
Торговая марка |
|
Caterpillar |
|
||
|
|
|
Модель |
|
|
|
RM-350B |
|
|
|
|
Тип ходовой части |
Колесная |
|
|||
|
|
|
Мощность, кВт |
|
373 |
|
||
|
|
|
Ширина обработки, мм |
2438 |
|
|||
|
|
|
Глубина обработки, мм |
457 |
|
|||
|
|
|
|
|
|
И |
|
|
|
|
|
Габариты, |
|
длина |
10320 |
|
|
|
|
|
Дширина 2980 |
|
||||
|
|
|
мм |
|
высота |
3590 |
|
|
|
|
|
Торговая марка |
|
Bomag |
|
||
|
|
|
Модель |
|
|
|
МРН 121 |
|
|
|
|
Тип ходовой части |
Колесная |
|
|||
|
|
|
Мощность, кВт |
|
263 |
|
||
|
|
|
Ширина обработки, мм |
2100 |
|
|||
|
|
|
Глубина обработки, мм |
430 |
|
|||
|
|
|
Габариты, |
|
длина |
9050 |
|
|
|
|
|
|
ширина |
2500 |
|
||
|
|
|
мм |
|
|
|||
|
|
|
|
высота |
2600 |
|
||
|
|
|
|
|
|
|||
|
|
|
Рабочая скорость, м/мин |
100 |
|
245

|
|
|
|
Окончание табл.73 |
||
|
1 |
|
2 |
3 |
||
|
|
Торговая марка |
Bomag |
|||
С |
Модель |
|
|
МРН 122-2 |
||
Тип ходовой части |
Колесная |
|||||
Мощность, кВт |
360 |
|||||
Ширина обработки, мм |
2330 |
|||||
Глубина обработки, мм |
500 |
|||||
Габариты, |
длина |
9050 |
||||
ширина |
2810 |
|||||
мм |
|
|
|
|||
высота |
3420 |
|||||
|
||||||
Рабочая скорость, м/мин |
43,2 |
|||||
|
и |
Торговая марка |
Bitelli |
|||
|
Модель |
|
|
ST 200 |
||
|
Тип ходовой части |
Колесная |
||||
|
Мощность, кВт |
265 |
||||
|
Ширина обработки, мм |
2000 |
||||
|
обработки, мм |
350 |
||||
|
|
Га ариты, |
|
длина |
8 900 |
|
|
|
|
ширина |
2 500 |
||
|
|
мм |
|
|||
|
|
|
высота |
2 600 |
||
|
|
|
|
|||
|
|
Ра очая скорость, м/мин |
50 |
|||
|
Глубина |
|
|
|
||
|
|
Торговая марка |
Wirtgen |
|||
|
|
Модель |
|
|
WR 2500 |
|
|
|
Тип ходовой части |
Колесная |
|||
|
|
Мощность, кВт |
448 |
|||
|
А |
|
||||
|
|
Ширина обработки, мм |
2438 |
|||
|
|
Глубина обработки, мм, до |
500 |
|||
|
|
Габариты, |
|
длина |
8 200 |
|
|
|
|
ширина |
3 200 |
||
|
|
мм |
|
|||
|
|
|
высота |
3 200 |
||
|
|
|
|
|||
|
|
Д |
|
|||
|
|
Рабочая скорость, м/мин, до |
200 |
Безусловно, что качественный холодныйИресайклинг возможен при соблюдении всех правил контроля.
Контроль качества АГБ-смеси начинают с входного контроля. При приготовлении АГБ смешением на дороге контролируют параметры вяжущих материалов и щебня, если его добавка предусмотрена проектом. Если АГБ готовят на заводе, то контролируют зерновой состав АГ. При этом партией АГ считается материал, сфрезерованный с 10 тыс. м2 проезжей части. В случае существенного расхождения по-
246
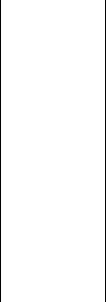
казателей АГ, поступившего в виде партии и использованного при подборе состава смеси, необходима корректировка его состава.
При операционном контроле проверяют:
- точность дозирования компонентов с учетом влажности АГ и технологический режим приготовления АГБ-смеси (ежедневно); - марку цемента (не реже одного раза в три месяца); - однородность эмульсии (не реже двух раз в месяц);
- влажность АГ, если смесь готовят не на дороге, при ее изменении из-за прошедшего ранее дождя.
испаренмесь отвозят в ла ораторию в емкости или пакете, исключающих е бАвлаги, прессуют три образца. Образцы извлекают из
При пр емочном контроле на выходе из смесителя отбирают пробу АГБ-смеси массой 3 кг. Отбор пробы производят ежедневно, но
С |
2 |
не менее одной про ы на 200 т или 1000 м слоя толщиной 10 см. |
пресс-формы при помощи выталкивателя и измеряют их размеры.При операц онном контроле качества проверяют соответствие требованиям утвержденного рецепта дозирования вяжущего материала, щебня
(при услов |
его пр менения). Точность дозирования определяют |
||||||
оперативно на пульте управления ресайклера по показаниям расходо- |
|||||||
меров. Результаты контроля входят в состав исполнительной доку- |
|||||||
ментации. |
|
|
|
|
|
|
|
Рекомендованные значения основных геометрических парамет- |
|||||||
ров и характеристик уложенного слоя по технологии холодного ре- |
|||||||
сайклинга приведены в табл. 74. |
|
|
Таблица 74 |
||||
|
|
|
|
|
|
||
Основные геометрические параметры и характеристики уложенного слоя |
|||||||
|
|
по технологии холодного ресайклинга |
|
|
|||
Параметры, подле- |
|
|
|
Способ |
Регистрация |
|
|
|
Показатели качества |
результатов |
|
||||
жащие контролю |
|
|
|
||||
|
|
Дконтроля |
|
||||
|
|
|
|
|
|
контроля |
|
1 |
|
|
2 |
|
3 |
4 |
|
Однородность по- |
|
|
|
|
|
|
|
верхности уложен- |
|
Однородная |
|
Визуальный |
Журнал произ- |
|
|
ного слоя после уп- |
|
|
|
|
водства работ |
|
|
лотнения |
|
|
|
|
И |
|
|
|
|
|
Не более 10% результатов |
|
|
|
|
|
|
|
определений могут иметь |
|
|
|
|
|
|
|
отклонения от проектных |
Рейка |
|
|
|
Поперечный уклон |
|
значений в пределах от - |
То же |
|
|||
|
|
|
|||||
|
|
|
0,015 (-0,010)% до 0,030 |
|
|
|
|
|
|
|
(0,015)%, остальные - до ± |
|
|
|
|
|
|
|
0,010 (0,005)% |
|
|
|
|
247

Окончание табл.74
|
|
1 |
|
|
|
2 |
|
|
3 |
4 |
|
|
|
|
Не |
более |
10% результатов |
|
|
|
|||
|
|
|
определений |
могут |
иметь |
Нивелир |
|
|
|||
|
Высотные отметки |
отклонения |
от проектных |
Журнал ниве- |
|
||||||
|
значений |
в |
пределах |
до |
|
лирования |
|
||||
С |
|
|
|||||||||
±100 (20) мм, остальные - |
|
|
|
||||||||
|
|
|
|
|
|
||||||
|
|
|
до ±50 (10) мм |
|
|
|
|
|
|||
|
|
|
Не |
более |
5% результатов |
3- |
|
|
|||
|
|
|
определений |
могут |
иметь |
метровая |
Ведомость |
|
|||
|
Ровность |
|
значения просветов |
в |
пре- |
дорожная |
контрольных |
|
|||
|
Толщина |
|
|
|
рейка |
измерений |
|
||||
|
|
|
делах до 10 (6) мм. осталь- |
|
|||||||
|
|
|
ные - до 5 (3) мм |
|
|
|
|
|
|||
|
|
|
Не |
олее |
10% результатов |
|
|
|
|||
|
|
|
определений |
могут |
иметь |
Мерная |
|
|
|||
|
|
|
отклонения |
от проектных |
линейка |
То же |
|
||||
|
|
|
значений в пределах от -15 |
|
|
||||||
|
|
|
|
|
|
||||||
|
|
|
до 20 см, остальные - до |
|
|
|
|||||
|
|
|
±10 см |
|
|
|
|
|
|
|
|
|
|
|
Не |
олее |
10% результатов |
|
|
|
|||
|
|
|
определений |
могут |
иметь |
Рулетка |
|
|
|||
|
|
|
отклонения |
от проектных |
|
|
|||||
|
Ширина |
бзначений в пределах от -15 |
|
-«- |
|
||||||
|
|
|
до 20 см, остальные - до |
|
|
|
|||||
|
|
|
±10 см |
|
|
|
|
|
|
|
|
|
|
|
|
|
|
ВНИИБД |
|
||||
|
Коэффициент сцеп- |
|
|
|
|
|
|
ППК |
|
|
|
|
ления колеса авто- |
МА |
Ведомость |
|
|||||||
|
мобиля с покрытием |
|
Не ниже 0,3 |
|
|
|
контрольных |
|
|||
|
(для верхних слоев) |
|
|
|
|
|
|
|
измерений |
|
|
|
|
|
|
|
|
|
|
|
|
||
|
|
|
|
|
|
|
|
|
И |
В первую очередь в лаборатории проверяют содержание воды в смеси и среднюю плотность АГБ (по ГОСТ 12801-98 [46] с учетом п. 7.16 [121]). При этом необходимо учитывать, что в смесях с цементом около 30 % воды от его массы вступает в реакцию с цементом и потому определенное испытанием количество воды в смеси будет меньше введенного.
При определении средней плотности АГБ образцы высушивают до постоянного веса на воздухе или в сушильном шкафу с принудительной вентиляцией при температуре не выше 40 °С. Образцы, высушенные в сушильном шкафу, следует охладить до комнатной температуры. Затем образцы из смесей погружают на 30 мин в сосуд с водой, имеющей температуру (20±2) °С. Уровень воды в сосуде дол-
248
жен быть выше поверхности образцов не менее чем на 20 мм, после чего образцы взвешивают в воде, следя за тем, чтобы на образцах не
было пузырьков воздуха. Образцы из укрепленных грунтов перед |
|||||||
взвешиванием в воде погружают в парафин при температуре |
|||||||
(60±5) ° . После взвешивания в воде образцы обтирают мягкой |
|||||||
С |
|
|
|
|
|
|
|
тканью и вторично взвешивают на воздухе. |
|
||||||
реднюю плотность образца из смеси m, г/см3, вычисляют по |
|||||||
формуле |
|
|
|
g в |
|
|
|
|
|
т |
|
|
, |
(18) |
|
|
|
|
|||||
|
|
|
g g |
|
|||
вычисляют0 |
g в |
1 |
|
|
|||
|
|
|
2 |
|
|
где g - масса образца, взвешенного на воздухе, г; в - плотность воды, равная 1 г/см3; g1 - масса образца, взвешенного в воде, г; g2 - масса образца, выдержанно-
го в течен е 30 м н в воде |
вторично взвешенного на воздухе, г. |
|
||||||||
|
|
образца |
|
|
|
|||||
|
|
реднюю плотность о разца из укрепленного грунта m0, г/см3, |
||||||||
|
|
по формуле |
|
|
|
|
|
|
||
|
|
|
т |
g3 g4 g3 |
g п |
, |
(19) |
|||
где g3 - масса |
, покрытого парафином и вторично взвешенного на возду- |
|||||||||
хе, |
г; g4 - масса |
о разца, |
покрытого парафином |
и взвешенного |
в воде, г; |
|||||
|
|
|
|
|
3 |
. |
|
|
|
|
|
п - плотность парафина, равная 0,93 г/см |
|
|
|
|
|||||
|
|
За результат определения средней плотности принимают округ- |
||||||||
|
|
|
|
|
Д |
|||||
ленное до второго десятичного знака среднеарифметическое значение |
||||||||||
результатов определенияАсредней плотности трех образцов. Если рас- |
||||||||||
хождение между наибольшим и наименьшим результатами парал- |
||||||||||
лельных определений превышает 0,03 г/см3 то проводят повторные |
||||||||||
испытания и вычисляют среднеарифметическое из шести значений. |
||||||||||
|
|
|
2 |
|
|
|
|
И |
||
|
|
Затем определяют предел прочности при сжатии при 20 °С образ- |
||||||||
цов АГБ (по п. 7.27 с учетом их возраста по п. 3.1 [121]). |
|
|||||||||
|
|
Предел прочности АГБ при сжатии при 20 °С (R 20), 50 °C (R 50) и |
||||||||
в |
|
водонасыщенном |
состоянии |
|
(Rв) |
|
определяют |
согласно |
ГОСТ 12801-98 [46].
Кроме указанных испытаний в процессе приемочного контроля на каждые 40 тыс. м регенерированного слоя осуществляют периодический контроль:
1.гранулометрического состава АГБ-смеси (по п. 7.19 [121]);
2.предела прочности при сжатии при 50 °С образцов АГБ (по п. 7.27 с учетом их возраста по п. 3.1 [121], табл. 3);
249
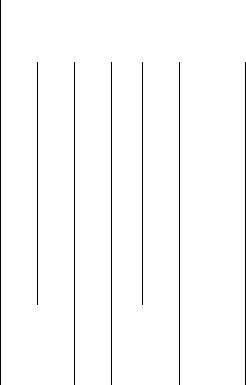
3. водонасыщения образцов АГБ (по п. 7.26 [121]); коэффициента водостойкости образцов АГБ (по ГОСТ 12801-98 [46]).
Показатели физико-механических свойств АГБ, в зависимости от категории автомобильной дороги и типа смеси, должны соответство-
|
вать значениям, указанным в табл. 75. |
|
|
|
|
|
|
|
|
|
||||||||||
С |
|
|
|
|
|
|
|
|
|
|
|
|
|
Таблица 75 |
||||||
|
|
|
|
|
|
|
|
|
|
|
|
|
|
|
|
|
||||
|
|
|
Показатели физико-механических свойств АГБ |
|
|
|
||||||||||||||
|
|
|
|
|
|
Нормы для категории автомобильной дороги |
|
|
||||||||||||
|
Показатель |
|
|
I - II |
|
|
|
III |
|
|
|
|
IV |
|
|
|
||||
|
|
|
|
|
|
|
|
для смесей типа |
|
|
|
|
|
|||||||
|
прочности |
М, |
|
|
|
|
М, |
|
|
|
|
М, |
|
|
|
|
||||
|
|
|
|
|
Э |
|
В |
Э |
В |
Б |
Э |
|
В |
Б |
А |
|
||||
|
|
|
|
|
|
К |
|
|
|
|
К |
|
|
|
|
К |
|
|
|
|
|
1. Предел |
|
|
|
|
|
|
|
|
|
|
|
|
|
|
|
|
|
|
|
|
при сжат |
|
, не менее, |
|
|
|
|
|
|
|
|
|
|
|
|
|
|
|
|
|
|
|
|
бА |
|
|
|
|
|
|
|
|
|||||||||
|
МПа, при температуре |
|
|
|
|
|
|
|
|
|
|
|
|
|
|
|
|
|
||
|
20 °С в возрасте: |
|
|
|
|
|
|
|
|
|
|
|
|
|
|
|
|
|
||
|
а) 1 суток |
|
- |
- |
|
1,4 |
- |
- |
1,4 |
1,2 |
- |
|
- |
1,4 |
1,2 |
0,7 |
|
|||
|
б) 7 суток |
|
1,4 |
2,0 |
|
- |
1,4 |
2,0 |
- |
- |
1,4 |
2,0 |
- |
- |
- |
|
||||
|
2. То же, при 50 °С в |
|
|
|
|
|
|
|
|
|
|
|
|
|
|
|
|
|
||
|
возрасте: |
|
|
|
|
|
|
|
|
|
|
|
|
|
|
|
|
|
|
|
|
а) 1 суток |
|
- |
- |
|
0,7 |
- |
- |
0,6 |
0,5 |
- |
|
- |
0,6 |
0,5 |
0,4 |
|
|||
|
б) 7 суток |
|
0,7 |
0,8 |
|
- |
0,6 |
0,7 |
- |
- |
0,5 |
0,7 |
- |
- |
- |
|
||||
|
3. Коэффициент водо- |
0,7 |
|
0,7 |
0,6 |
0,6 |
|
0,6 |
0,6 |
0,6 |
|
|||||||||
|
стойкости, не менее |
|
|
|
||||||||||||||||
|
|
|
|
|
|
|
|
|
|
|
|
|
|
|
|
|
|
|||
|
4. Водонасыщение по |
10 |
|
10 |
Д |
14 |
16 |
|
||||||||||||
|
объему, %, не более |
|
12 |
12 |
|
14 |
|
|||||||||||||
|
|
|
|
|
|
|
|
|
|
|
|
|
|
|
|
|
|
|||
|
Гранулометрический состав |
|
ГБ-смеси должен соответствовать |
|||||||||||||||||
|
требованиям, установленным в ГОСТ 9128–2009 [45] для пористых и |
|||||||||||||||||||
|
высокопористых щебеночных смесей, за исключением частиц мельче |
|||||||||||||||||||
|
|
|
|
|
|
|
|
|
|
|
|
|
И |
|||||||
|
0,071 мм, содержание которых не нормируется. |
|
|
|
|
|
|
|
||||||||||||
|
Для дорог I – II категорий применяют щебеночные смеси, а для |
|||||||||||||||||||
|
дорог |
III – IV |
категорий допускается |
применение песчаных |
АГБ-смесей. Если в АГ, используемом для приготовления щебеночных смесей, содержание щебня меньше 35%, при приготовлении АГБ-смеси необходимо добавление недостающей фракции щебня.
Содержание в АГ гранул крупнее 50 мм не должно превышать 5% по массе.
Гранулометрический состав АГ определяют согласно ГОСТ 12801–98 [46]. Отличие заключается в том, что из пробы массой 500 г битум не удаляют, рассев производят всухую.
250
Водонасыщение определяют на образцах цилиндрической формы или на образцах-вырубках (кернах). Для смесей испытание проводят на образцах, использованных для определения средней плотности.
Образцы из смесей, взвешенные на воздухе и в воде, помещают в сосуд с водой с температурой (20±2) °С. Уровень воды над образцами должен быть не менее 3 см.
осуд с образцами устанавливают в вакуумную установку, где создают поддерж вают давление не более 2000 Па (15 мм рт. ст.) в течение 1 ч при спытании образцов из смесей с вязкими органическими вяжущ ми; 30 м н – при испытании образцов из смесей с жид-
кими |
эмульг рованными вяжущими. Затем давление доводят до ат- |
|
С |
||
мосферного |
образцы выдерживают в том же сосуде с водой с тем- |
|
пературой (20±2) °С в течение 30 мин. После этого образцы извлека- |
||
ют |
сосуда, взвеш вают в воде, обтирают мягкой тканью и взвеши- |
|
вают на воздухе. |
||
Образцы |
з укрепленных грунтов, предназначенных для приме- |
|
из |
||
нения в районах со среднемесячной температурой самого холодного |
||
месяца м нус 20 °С ниже (I - III дорожно-климатические зоны) по- |
||
сле взвешивания на воздухе и в воде, подвергают полному водонасы- |
||
щению, а для укрепленных грунтов, предназначенных для примене- |
ния в районахбАсо среднемесячной температурой самого холодного месяца выше – 10 °С – капиллярному водонасыщению.
Полное водонасыщение образцов высотой и диаметром 50 мм проводят в течение 2 сут, а образцов больших размеров – в течение 3 сут, при этом во всех случаях в первые сутки образцы погружают в
воду на 1/3 высоты, а в последующие – полностью. ля предотвраще-
щение проводят в ванне с гидравлическимДзатвором.
ния высыхания образцов, погруженных в воду на 1/3 высоты, насы- И
Капиллярное водонасыщение проводят через слой воды, постоянно поддерживаемый с помощью уровнемера в устройстве для капиллярного водонасыщения.
В сосуд на металлическую подставку укладывают металлическую
сетку или устанавливают емкость с сетчатым дном, которое закрывают фильтровальной бумагой. На фильтровальную бумагу насыпают слой мелкого песка одной фракции толщиной 15 см и через сутки после его насыщения ставят образцы, которые насыщают в течение 3 сут. Для предотвращения высыхания сосуд с образцами помещают в ванну с гидравлическим затвором.
251
После этого образцы извлекают из сосуда или устройства для капиллярного водонасыщения, взвешивают в воде, а затем вытирают мягкой тканью или фильтровальной бумагой и взвешивают на воздухе.
Водонасыщение образца W, %, вычисляют по формуле для смесей
|
W |
|
g5 |
g |
100 |
|
|
|
|
g2 |
|
|
|||
|
|
|
g1 |
(20) |
|||
для укрепленных грунтов |
|
|
|
|
|
|
|
|
|
|
|
|
|
|
|
С |
W |
g5 |
g |
100 |
|
||
g |
|
|
|||||
|
|
g1 |
(21) |
||||
|
|
|
|
|
|
||
|
|
|
|
|
|
|
|
определения |
|
|
|
|
|
|
|
где g - масса образца, взвешенного на воздухе, г; g1 - масса образца, взвешенного в воде, г; g2 - масса о разца, выдержанного в течение 30 мин в воде и взвешенного на воздухе, г; g5 - масса насыщенного водой образца, взвешенного на воздухе, г.
бА |
|
За результат |
водонасыщения принимают округлен- |
ное до первого десят чного знака среднеарифметическое значение трех определен й.
Водостойкость Кв вычисляют с точностью до второго десятичного знака по формуле
Rв20 |
, |
(22) |
Кв R |
||
20 |
|
|
где и Rв20 – предел прочности при сжатии при температуре (20±2) °С водонасы- |
||
Д |
|
щенных в вакууме образцов, МПа; R20 – предел прочности при сжатии при температуре (20±2) °С образцов до водонасыщения, МПа.
После подбора состава изготавливают соответствующую смесь для проверки остальных физико-механических свойств АГБ. На замес
требуется 4 кг АГ. |
И |
Прессуют шесть образцов и через сутки или 7 сут (в зависимости от типа АГБ-смеси) определяют их среднюю плотность. После этого делят образцы на две группы по три образца так, чтобы средние арифметические результаты определения плотности в каждой из групп были максимально близки.
Для трех образцов одной из групп определяют водонасыщение, а также показатели Rв и Кв. Это делается сразу после определения средней плотности. При вычислении водонасыщения используют значения массы образцов, взвешенных на воздухе, полученные при определении их средней плотности.
Перед определением показателя R50 образцы из второй серии высушивают (после определения средней плотности) до постоянного веса.
252
Если показатель W или Kв не отвечают требованиям, следует или откорректировать гранулометрический состав АГБ-смеси, или увеличить содержание вяжущего в смесях типа Б, В и Э, или перейти на смеси типов К или М, для которых, как правило, не возникает про-
блем с этими показателями.
СЕсли в результате приемочного контроля выявлено несоответствие показателей ф з ко-механических свойств АГБ и показателей, полученных при под оре, то проверяют свойства всех исходных материалов, состав смеси, технологический процесс ее приготовления и производят коррект ровку составов.
Если показатель R 50 не отвечает требованиям, что иногда имеет место для смесей типов Б, В, и Э, следует перейти на смеси типов К или М, для которых всегда может быть обеспечено требуемое значе-
ние этого показателя путем увеличения содержания цемента.
При устройстве конструктивного слоя из АГБ-смеси при опера-
контроле проверяют: |
|
ционном |
|
– Толщ ну рыхлого слоя - металлическим щупом с делениями с |
|
учетом коэфф ц ента уплотнения смеси (см. п. 8.23 [21]). Толщина |
|
регенерированного слоя из ГБ всегда больше, |
чем глубина регене- |
рационного фрезерования. Это связано с разницей в плотностях |
|
АГБ и исходного пакета асфальтобетонных |
слоев: обычно – |
2,10 – 2,20 г/см3 у первого и 2,30 – 2,40 г/см3 – у второго. |
– Качество продольных и поперечных сопряжений и ровность |
|
слоя в зоне сопряжения в перпендикулярном к нему направлении; |
|
бА |
|
– Плотность слоя – радиоизотопным прибором; |
|
– Поперечные уклоны – рейкой с уровнем. |
|
При приемочном контроле проверяют: |
|
– Высотные отметки по оси проезжей части. |
|
- Толщину уплотненного слояД– по кернам. |
|
- Среднюю плотность слоя. |
И |
- Ширину слоя. |
|
- Поперечные уклоны. |
При приемке работ предварительная оценка ровности поверхности в продольном направлении проводится либо на основе графической записи, полученной с помощью приборов типа ПКРС или других приборов, показания которых приведены к показаниям ПКРС, либо путем проезда на автомашине по всему сдаваемому участку по каждой полосе движении. На основе такой оценки выбираются захватки для детального измерения ровности и поперечных уклонов.
253
Детальный контроль ровности поверхности основания или покрытия на выбранных захватках следует вести путем измерения просветов под трехметровой рейкой, определения показаний стрелочного прибора или передвижной рейки.
Измерение просветов под трехметровой рейкой с помощью клина (промерника) следует производить в пяти контрольных точках, рас-
СНа каждой захватке следует произвести:
положенных на расстоянии 0,5 м от концов рейки и друг от друга.
Детальные змерения ровности следует производить на расстоянии 0,5 – 1,0 м от каждой кромки покрытия или края полосы движе-
ния.
– 100 – 130 змерений просветов (25 – 30 приложений рейки) или непрерывную граф ческую запись неровностей;
– 80 – 100 змерений поперечных уклонов рейкой с уровнем (25–30 змерен й для захваток длиной 100 – 150 м);
– определен |
|
абсолютных или относительных от- |
вертикальных |
|
|
меток путем н вел рования с шагом 5 м. |
||
Ш р ну слоя |
поперечные уклоны измеряют не менее чем в |
|
20 местах на сдаваемом участке. |
|
|
бА |
||
|
Д |
|
|
|
И |
254