
- •ВВЕДЕНИЕ
- •1. ТЕХНОЛОГИЯ РАБОТ ПО ЛИКВИДАЦИИ МЕЛКИХ ПОВРЕЖДЕНИЙ: ЗАЛИВКА ТРЕЩИН И ЗАДЕЛКА ВЫБОИН
- •1.1. Традиционные способы ремонта
- •1.3. Ремонт с применением инфракрасных разогревателей асфальтобетона
- •2.3. Технология устройства поверхностной обработки методом Чип Сил
- •2.4. Технология устройства слоя износа методами Слари Сил, Микросюрфейсинг и Кейп Сил
- •2.5. Особенности применения технологии Фиб-Сил для устройства трещино-прерывающей прослойки
- •3. УСТРОЙСТВО СЛОЕВ УСИЛЕНИЯ ДОРОЖНОЙ ОДЕЖДЫ
- •3.1. Методы измерения упругого прогиба и определение модуля упругости дорожной одежды
- •3.2. Традиционные материалы и технологии для усиления дорожных одежд
- •3.4 Устройство усилений из асфальтобетона, армированного геосинтетическими материалами
- •4. ПРИМЕНЕНИЕ МЕТОДОВ ГОРЯЧЕЙ РЕГЕНЕРАЦИИ ДЛЯ ВОССТАНОВЛЕНИЯ И УСИЛЕНИЯ ДОРОЖНЫХ ОДЕЖД С АСФАЛЬТОБЕТОННЫМ ПОКРЫТИЕМ
- •5.1. Характеристика района и определение допустимых сроков производства работ
- •5.3. Комплектование отрядов и калькуляция трудовых затрат
- •Библиографический список
- •Приложение 1
- •Приложение 2
1.3. Ремонт с применением инфракрасных разогревателей асфальтобетона
Последней из рассматриваемых технологий ямочного ремонта асфальтобетонного покрытия является заделка выбоин при помощи установок для инфракрасного нагрева асфальтобетона. Основным Спреимуществом инфракрасного ремонта является отсутствие холодного соединения или шва. Такой эффект достигается тем, что ремонтируемые участки пр мыкающие к ним площади подвергаются воз-
действ ю температуры одновременно. То есть ширина нагрева на 20поверхности-25 см превышает ш рину ремонтируемого (разрыхляемого) участка. Это устраняет любые холодные соединения или швы и создаёт
термальную связь в существующем дорожном покрытии, устраняет возможность попадан я воды мусора в швы и основание и не до-
1.Оч стбАть участок от мусора и/или воды.
2.Установить инфракрасный нагреватель асфальта над участком, предназначенным для ремонта.
3.Включить инфракрасный нагреватель от 5 до 9 мин в зависимости от типа, давности, глу ины асфальта, сезона.
4.Перемешать скребком или граблями размягченный на месте материал, устраняя дефекты,ямыДи неровности.
5.Для улучшения свойств добавляем восстанавливающий материал 1–2 кг на 1 м2.
6.Добавить необходимое количество нового асфальта для создания ровной поверхности.
7.Разровнять гладилкой. И
8.Уплотнить уложенный материал до необходимой степени. Технологической особенностью разогрева является наличие двух
всей ширине до температуры около 80 °С в нижней части разогреваемого слоя при неизменной температуре на поверхности покрытия. Режим разогрева регулируется изменением расхода газа и высоты горелок над покрытием от 10 до 20 см [9].
31
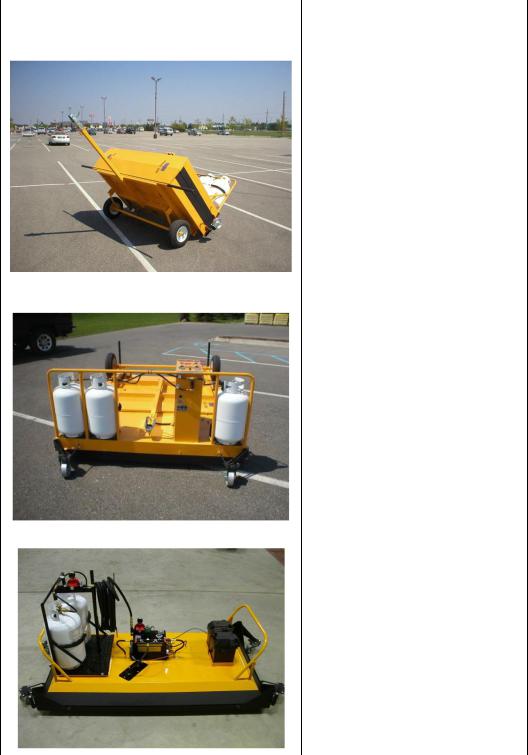
В табл. 10 приведены технические характеристики установок, применяемых для инфракрасного ремонта асфальтобетонного покрытия.
|
|
|
|
|
|
|
|
Таблица 10 |
|
|
Технические характеристики установок для инфракрасного ремонта |
||||||||
|
|
асфальтобетонных покрытий |
|
|
|
||||
|
Общий вид |
|
|
Технические характеристики |
Величина |
|
|||
|
1 |
|
|
|
2 |
|
|
3 |
|
С |
|
|
Марка |
|
|
|
КМ4-40 |
|
|
|
|
|
|
|
|
Склады- |
|
||
|
|
Тип |
|
|
|
вающийся |
|
||
|
|
|
|
|
|
прицеп |
|
||
|
|
Полная масса,кг |
|
367,4 |
|
||||
|
и |
|
Тип топлива |
|
Пропан |
|
|||
|
|
Объем баллонов пропана, л |
3 32,6 |
|
|||||
|
|
Потребление пропана, кг/ч |
11,34 |
|
|||||
|
|
Габариты |
|
|
Длина, м |
2,54 |
|
||
|
|
транспортные |
|
Ширина, м |
1,98 |
|
|||
|
|
|
|
Размеры зоны нагрева, м |
2–0,61 1,22 |
|
|||
|
|
|
|
2–0,91 1,22 |
|
||||
|
|
|
|
|
|
|
|
|
|
|
|
|
|
Марка |
|
|
|
КМ4-48 |
|
|
|
|
|
|
|
|
|
Склады- |
|
|
|
|
|
Тип |
|
|
|
вающийся |
|
|
|
|
|
|
|
|
|
прицеп |
|
|
|
|
|
Полная масса,кг |
|
367,4 |
|
||
|
|
|
|
Тип топлива |
|
Пропан |
|
||
|
бА |
|
|
||||||
|
|
Объем баллонов пропана, л |
3 32,6 |
|
|||||
|
|
|
|
Потребление пропана, кг/ч |
11,34 |
|
|||
|
|
|
|
Габариты |
|
|
лина, м |
2,54 |
|
|
|
|
|
транспортные |
|
Ширина, м |
2,27 |
|
|
|
|
|
|
|
И |
|
|||
|
|
|
|
Размеры зоны нагрева, м |
2–0,61 1,22 |
|
|||
|
|
|
Д2–1,22 1,22 |
|
|||||
|
|
|
|
Марка |
|
|
|
КМ 2-18Х |
|
|
|
|
|
Тип |
|
|
|
Склады- |
|
|
|
|
|
|
|
|
вающаяся |
|
|
|
|
|
|
|
|
|
|
|
|
|
|
|
|
Полная масса,кг |
|
194 |
|
||
|
|
|
|
Тип топлива |
|
Пропан |
|
||
|
|
|
|
Объем баллонов пропана, л |
2 32,6 |
|
|||
|
|
|
|
Потребление пропана, кг/ч |
6,4 |
|
|||
|
|
|
|
Габариты |
|
|
Длина, м |
1,98 |
|
|
|
|
|
транспортные |
|
Ширина, м |
1,06 |
|
|
|
|
|
|
Размеры зоны нагрева, м |
2–1,06 0,99 |
|
|||
|
|
|
|
|
|
|
|
|
|
32
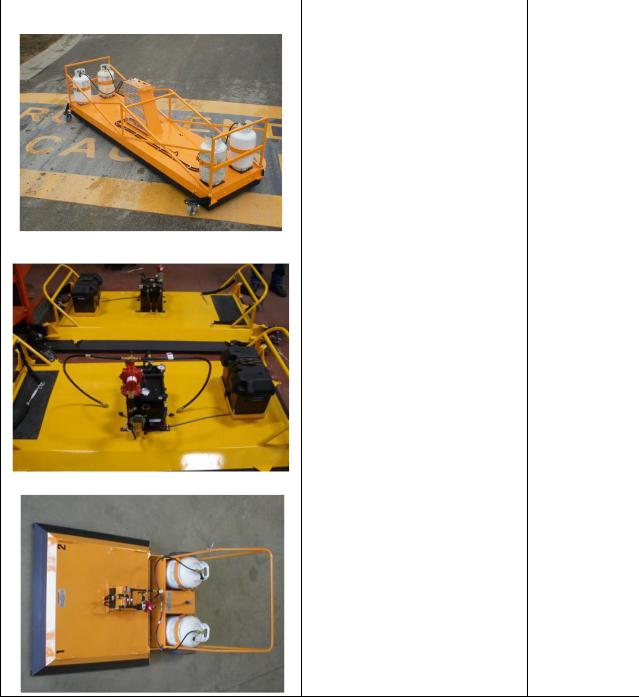
|
|
|
|
|
|
|
Окончание табл. 1.10 |
||||
|
1 |
|
|
|
2 |
|
|
|
3 |
|
|
|
|
|
Марка |
|
|
|
|
КМ 2-36 |
|
|
|
С |
|
Тип |
|
|
|
|
Склады- |
|
|
||
|
|
|
|
|
вающаяся |
|
|
||||
|
|
|
|
|
|
|
|
||||
|
Полная масса,кг |
|
|
360 |
|
|
|||||
|
Тип топлива |
|
Пропан |
|
|
||||||
|
Объем баллонов пропана, л |
|
4 32,6 |
|
|
||||||
|
Потребление пропана, кг/ч |
|
10,1 |
|
|
||||||
|
Габариты |
|
|
Длина, м |
|
3,66 |
|
|
|||
|
транспортные |
|
Ширина, м |
|
0,91 |
|
|
||||
|
Размеры зоны нагрева, м |
2–0,91 1,83 |
|
|
|||||||
|
|
|
|
|
|
|
|
|
|
||
|
и |
|
Марка |
|
|
|
|
КМ 2-16 |
|
|
|
|
|
Тип |
|
|
|
|
Склады- |
|
|
||
|
|
|
|
|
|
вающаяся |
|
|
|||
|
|
|
|
|
|
|
|
|
|||
|
|
Полная масса,кг |
|
|
125 |
|
|
||||
|
|
Тип топлива |
|
Пропан |
|
|
|||||
|
Объем |
|
баллонов пропана, л |
|
2 32,6 |
|
|
||||
|
Потребление пропана, кг/ч |
|
5,44 |
|
|
||||||
|
Габариты |
|
|
Длина, м |
|
1,47 |
|
|
|||
|
|
|
Ширина, м |
|
1,24 |
|
|
||||
|
транспортные |
|
|
|
|
||||||
|
|
Высота, м |
|
0,76 |
|
|
|||||
|
|
|
|
|
|
|
|
||||
|
|
|
|
|
|
|
|
|
|
||
|
|
|
Размеры зоны нагрева, м |
2–0,61 1,22 |
|
|
|||||
|
|
|
|
|
|
|
|
|
|
|
|
|
|
|
Марка |
|
|
|
|
LB 2-16 |
|
||
|
А |
|
|
|
|||||||
|
|
Тип |
Склады- |
|
|||||||
|
|
|
|
|
|
|
|
вающаяся |
|
|
|
|
|
|
Полная масса,кг |
|
|
124,6 |
|
|
|||
|
|
|
Тип топлива |
|
Пропан |
|
|
||||
|
|
|
Объем баллонов пропана, л |
|
2 32,6 |
|
|
||||
|
|
|
Потребление пропана, м3/ч |
|
1,91 |
|
|
||||
|
|
|
Д |
|
|
|
|
||||
|
|
|
Габариты ра- |
|
лина, м |
|
1,22 |
|
|
||
|
|
|
бочие |
|
|
|
Ширина, м |
|
1,22 |
|
|
|
|
|
Размеры зоны нагрева, м |
|
2–1,22 |
|
|
||||
|
|
|
|
|
И |
|
|
||||
|
|
|
|
|
|
Выполнив разогрев покрытия, приступают к разрыхлению асфальтобетона на всю глубину выбоины [9]. Для этого применяют грабли. Недостаток материала для заделки выбоины компенсируется добавкой новой горячей асфальтобетонной смеси, которую подают из бункера-термоса. Новую и старую разрыхленную смесь перемешивают и укладывают по всей площади карты слоем больше глубины в 1,2–1,3 раза, то есть с учетом коэффициента запаса на уплотнение [9].
33

Уплотнение смеси производят от краёв к середине карты, применяя ручные виброплиты или виброкатки [9].
Применение установок инфракрасного разогрева асфальтобетона позволяет обойтись без фрезерования материала покрытия и устройства холодных швов. Добавление нового материала обеспечивает ре-
Сгенерацию асфальтобетона. Эти достоинства технологии инфракрас-
ного ремонта позволяют выполнить работы с наилучшим качеством. В результате срок службы отремонтированного участка выше, чем
при пр менен друг х технологий.
иНа р с. 19 – 23 представлены некоторые рабочие моменты ремонта асфальтобетонного покрытия при применении инфракрасных нагревателей.
бА Д Рис. 19. Передвижение установки КМ4-40Ик месту нагрева
Рис. 20. Инфракрасный излучатель |
Рис. 21. Разогретый участок |
34

Си
РисбА. 22. Перемешивание разогретого установкой КМ4-48
Д И
Рис. 23. Разравнивание асфальтобетонной смеси при ремонте установкой КМ4-48
35
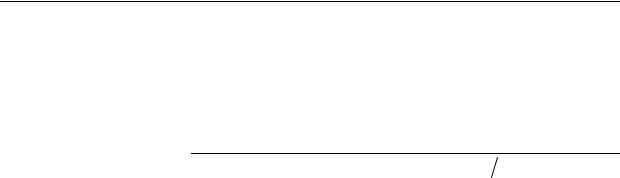
|
|
|
2. |
УСТРОЙСТВО СЛОЕВ ИЗНОСА |
|
|
|||
|
|
|
И ПОВЕРХНОСТНЫХ ОБРАБОТОК |
|
|
||||
|
|
|
2.1. Методы измерения коэффициента |
|
|
||||
|
|
|
сцепления и параметров шероховатости |
|
|
||||
С |
|
|
|
|
|
||||
|
|
Результаты исследований показали, что в России одной из основ- |
|||||||
|
ных |
ли |
сопутствующих причин |
возникновения |
дорожно- |
||||
|
транспортных про сшествий (ДТП) является скользкость покрытий. |
||||||||
|
количеством |
|
|
Таблица 11 |
|||||
|
В результате повышен я скользкости покрытий происходит увеличе- |
||||||||
|
ние кол чества ДТП |
х тяжести. |
|
|
|
||||
|
|
Вл ян |
коэфф ц ента сцепления на риск возникновения ДТП |
||||||
|
можно продемонстр ровать корреляционными зависимостями между |
||||||||
|
|
|
бА |
|
|
||||
|
|
|
ДТП |
показателем скользкости или коэффициентом |
|||||
|
сцеплен я. Так |
зав |
мости приведены в табл. 11. |
|
|
||||
|
|
Эмп р ческ е формулы для расчета относительного количества ДТП |
|||||||
|
|
на мокрых покрытиях в зависимости от коэффициента сцепления |
|||||||
|
|
Авторы |
|
|
|
Формула |
|
|
|
|
Wehner B., Schulze K.- |
|
A 45,718 Ln ì 80 3,1231 |
|
|
||||
|
H., Dames J., Lange H. |
|
|
|
|
|
|||
|
|
A 142,59 ì 80 96,099 |
|
|
|||||
|
[13] |
|
|
|
|
|
|
||
|
А – относительное количество ДТП на мокром покрытии от общего количества, |
|
|||||||
|
|
|
|
|
|
Д |
|
||
|
%; м(80) – коэффициент сцепления, измеренный при скорости движения 80 км/ч |
|
|||||||
|
и полной блокировке колеса |
|
|
|
|
||||
|
|
|
|
|
|
ì SCRIM 80 1,076 ì 80 0,006 |
|
||
|
Hiersche E.-U. [10], |
|
|
ì 80 ì SCRIM 80 0,006 1,076 |
|
||||
|
Stutze T. [12] |
|
|
|
|
|
|
|
|
|
|
|
|
A 46,572 Ln ì SCRIM 80 0,1459 |
|
||||
|
|
|
|
|
|
|
|||
|
м(SCRIM)(80)– |
|
|
|
|
И |
|
||
|
коэффициент сцепления, измеренный при скорости |
движения |
|
||||||
|
80 км/ч оборудованием SCRIM |
|
|
|
|
||||
|
Kamplade J., Schmitz H. |
|
A |
0,7975 |
|
|
|||
|
|
16,943 ì 80 |
|
|
|||||
|
[11] |
|
|
|
|
|
0,7975 |
|
|
|
|
|
|
|
|
A 18,318 ì SCRIM 80 |
|
|
Подобные исследования выполнялись в РФ. Влияние коэффициента сцепления на количество ДТП подтверждается работами А.П. Васильева [14] и М.В. Немчинова [15–17]. На рис. 24 и 25 пред-
ставлены результаты исследований Schulz V.H. [12, 17] о количестве и тяжести ДТП на мокрых покрытиях.
36
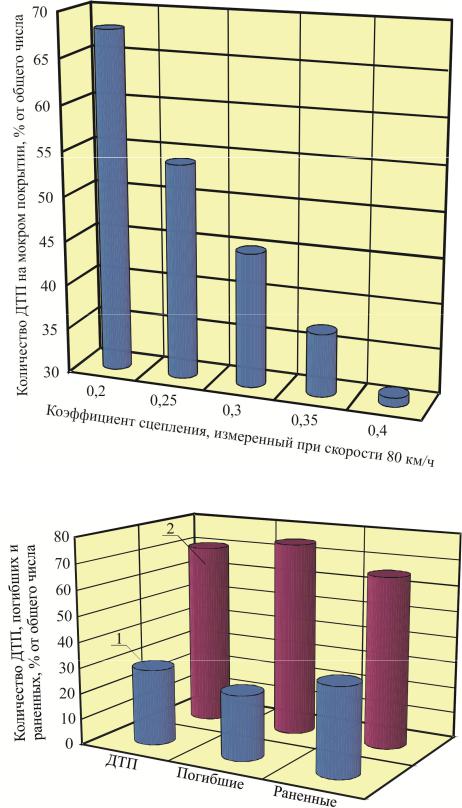
Си
РисбА. 24. Зависимость количества ДТП на мокрых покрытиях
от величины коэффициента сцепления Д И
Рис. 25. Распределение количества ДТП и их тяжести: 1 – шероховатые покрытия; 2–гладкие покрытия
37
На основании анализа данных рис. 24 можно сделать вывод о том, что мокрые шероховатые покрытия имеют более высокий коэффициент сцепления по сравнению с мокрыми гладкими покрытиями. Из анализа рис. 24 и 25 следует, что устройство шероховатых поверхностей может рассматриваться как средство уменьшения количества ДТП. Например, количество ДТП на мокрых шероховатых покрытиях на 40–50% ниже, чем на мокрых гладких покрытиях, количество погибших раненных уменьшается в 3 и 2 раза.
Результаты научных исследований легли в основу нормативных |
||
документов, так согласно указаниям ВСН 38-90 [18 п. 1.1] устройст- |
||
во шероховатой поверхности является одним из главных способов |
||
С |
|
|
повышен я коэфф ц ента сцепления. При этом требуется, чтобы |
||
шероховатость |
|
состояние дорожного покрытия проезжей части |
обеспеч вали тре ован я ГОСТ 50597-93 [2] и ОДМ [5]. Согласно |
||
этим требован ям вел чина сцепления колеса с покрытием должна |
||
быть не менее 0,3 |
змерении его шиной без рисунка протектора и |
|
при |
||
0,4 – ш ной, |
меющей рисунок протектора [5, п. 1.2.9]. Кроме того, |
|
разница коэфф ц ента сцепления по ширине проезжей части допус- |
||
кается не |
0,1, разница между коэффициентом сцепления покры- |
более тия проезжей части иАукрепленной обочины - 0,15 [5, п. 1.2.10].
Потеря шероховатости, как правило, происходит из-за полируемости каменных материалов покрытия, «выпотевания битума», обра-
зования на покрытии пленки (слояД) из материалов с низким коэффициентом сцепления [5, п. 4.1.8]. В этом случае сопротивление движению недостаточное и коэффициент сцепления ниже требуемого значения. Поэтому для повышения коэффициента сцепления необходимы мероприятия, при выполнении которых шероховатость поверхности возобновляется. Возобновление шероховатостиИможно выполнить классическим восстановительным ремонтом, устроив слой износа, обладающий требуемой шероховатостью, и шероховатую поверхностную обработку (ШПО). ШПО является одним из наиболее эффективных способов устройства шероховатых поверхностей с требуемыми параметрами [14–18].
Слои износа и поверхностные обработки обладают шероховатой поверхностью, что позволяет их применять в качестве мероприятия повышающего коэффициент сцепления.
Рассматривая правила измерения коэффициента сцепления, обратим внимание на приборы российского производства.
38
При измерении сцепных свойств дорожных покрытий выполняют сплошные или выборочные измерения в соответствии с ГОСТ 30413–96 [3]. плошные измерения выполняют при обследовании участков дорог
протяженностью более 1 |
км, выборочные |
– менее 1 км. |
|
ГО Т 33078–2014 [19, разд. 5] допускает применение портативных |
|||
С |
|
|
|
приборов для измерения коэффициента сцепления на участках авто- |
|||
мобильных дорог, где невозможно обеспечить требуемую скорость |
|||
движен я спытательной |
установки. Таким |
образом, стандарты |
|
ГО Т 30413–96 [3] |
ГОСТ 33078-2014 [19] в качестве основных из- |
||
шину |
|
||
мерен й рассматр вают сплошные измерения, которые выполняются |
|||
при помощи моб льной установки ПКРС. |
|
||
При сплошных |
змерениях сцепных свойств дорожных покрытий |
в установке ПКРС-2У должна использоваться шина без рисунка про-
специальной ш ны с гладким протектором допускается использовать
тектора либолеес р сунком глу иной не менее 1 мм. В случае отсутствия
обычную |
зношенную |
того же размера с остаточной глубиной |
канавок не |
1 мм. Измерения коэффициента сцепления произво- |
дят по левой полосе наката каждой полосы движения. При невозможности произвести измеренияАпо левой полосе наката (двухполосная дорога, крайняя левая полоса многополосной дороги) допускается производить их по правой полосе наката.
Измерения сцепных свойств производятся при постоянной скорости, которая согласно требованиямДГОСТ 30413-96 [3, п. 4.1.2 и п. 4.3.3]
составляет 60±5 км/ч, а по ГОСТ 33078-2014 [19, п. 9.1] 60±2 км/ч.
Анализ требований этих документов и формул табл. 11, в которых коэффициент сцепления измеряется при скорости 80 км/ч, свидетельствует о зависимости коэффициента сцепления от скорости движения в момент блокировки измерительногоИколеса. Такая зависимость установлена в экспериментах российских специалистов [14–17]. Поэтому для измерения коэффициента сцепления в различных странах существуют требования к скорости движения, которую следует выдерживать при измерениях. Для этой скорости движения установлены минимально требуемые значения коэффициентов сцепления.
Сцепные качества покрытия оцениваются коэффициентом продольного сцепления, измеренным на увлажненном покрытии при расчетной температуре воздуха 20 °С. Увлажнение дорожного покрытия осуществляется с помощью автономной системы искусственного увлажнения, смонтированной на автомобиле-тягаче. Не допускается производить измерения сцепных качеств дорожного покрытия во
39
время дождя, а также в течение 2–3 ч после него. При измерениях коэффициента сцепления фиксируют температуру воздуха. Полученные значения коэффициента сцепления приводят к расчетной температуре 20 ° путем их суммирования с поправками, указанными в табл. 12.
С |
|
|
|
|
|
|
|
Таблица 12 |
||||
|
|
|
|
|
|
|
|
|
||||
|
Поправки к величине коэффициента сцепления, учитывающие |
|||||||||||
|
|
температуру воздуха при измерениях |
|
|
|
|
|
|||||
|
Температура воздуха в момент из- |
0 |
5 |
10 |
15 |
20 |
25 |
30 |
35 |
40 |
|
|
|
мерений, ° |
|
|
|
|
|
|
|
|
|
|
|
|
налич |
-0,06 |
-0,04 |
-0,03 |
-0,02 |
0 |
0,01 |
0,01 |
0,02 |
0,02 |
|
|
|
Поправка к змеренному коэффи- |
|
||||||||||
|
циенту сцеплен я |
|
|
|
|
|
|
|
|
|
|
|
ледуя указан ям нструкции к ПКРС-2У перед началом работы необход мо про звести:
– в зуальный контроль состояния механических узлов, датчиков, е крепежных элементов узла ПКРС-2У;
–проверку ра очего давления в шине колеса, которое должно быть 0,17±0,01 МПа;
–проверку демпфирования подвески узла ПКРС-2У;
–присоединение электрического кабеля, трубопровода системы водополива ПКРС-2У к соответствующим разъемам, установленным на заднем борту автомо иля.
Измерение коэффициента сцепления ПКРС-2У выполняется путем проезда передвижной лаборатории по каждой полосе движения по левой полосе наката, а на участках с разделительной полосой при измерении коэффициента сцепления на крайней левой полосе движения проезд прицепа выполняется по правой полосе наката. В процессе измерений должна обеспечиваться скорость движения в диапазоне
55 – 65 км/ч.
Измерение проводят при торможении колеса узла ПКРС-2У во время движения лаборатории. При нажатии кнопки «торможение» в салоне автомобиля включается мотор-редуктор, который приводит в действие зубчатую передачу с передаточным числом i=3 и кулачок. Кулачок имеет заданный профиль и при повороте приводит в движение рычаг и тягу. При этом последовательно происходит открытие клапана полива воды, блокировка заноса узла ПКРС-2У относительно тягового автомобиля и блокировка колеса. Цикл торможения длится
3–4 с. При этом кнопка «торможение» должна удерживаться не более 1–1,5 с. Более длительного торможения следует избегать вследствиебАИ
40

того, что в этом случае происходит повторное торможение, оказывающее влияние на результат измерения.
При торможении колесо блокируется и тормозной рычаг поворачивается. При этом верхний конец тормозного рычага начинает движение в сторону дорожной лаборатории и через тормозную тягу воз-
Сдействует на шток, а тот в свою очередь на пластину. Величина перемещения пластины (прогиб) определяется с помощью датчика линейных перемещен й передается по каналам на ПЭВМ, и полученные данные могут быть представлены в табличном виде.
приведеныНа с. 26 пр ведена иллюстрация измерения коэффициента сцепления модерн з рованным прибором ПКРС-2 РДТ. На рис. 27 и 28
ллюстрац ра оты программного обеспечения, а также
Print Screen программного о еспечения при выполнении измерения. бА
Рис. 26. Полив покрытияДводой и блокировка колеса И
Рис. 27. Работа программного обеспечения при измерении
41
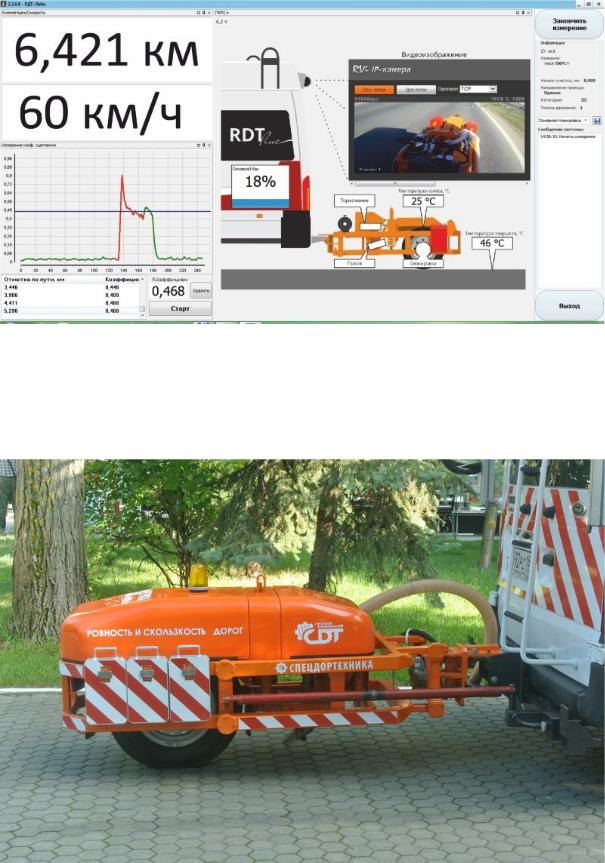
СРис. 28. Print Screen программного о еспечения при выполнении измерения
бА На р с. 29 пр ведена иллюстрация прибора ПКРС-3, при помощи
которого про зводят змерения коэффициента сцепления и продольной ровности.
Д И
Рис. 29. Прибор ПКРС-3
42
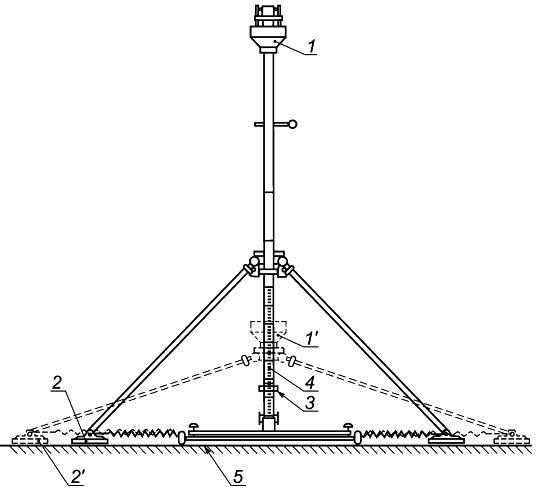
При выполнении выборочных измерений коэффициента сцепления применяют портативные переносные приборы. Наибольшее распространение из таких приборов получил портативный прибор Куз-
нецова, зарегистрированный в Госреестре под номером 10912-02 (ППК-МАДИ-ВНИИБД) и соответствует требованиям ТУ 17.1.004-87 С[4]. Принцип работы прибора основан на имитации процесса сколь-
жения заблокированного колеса автомобиля по дорожному покрытию при норм рованных условиях их взаимодействия: при нагрузке на колесо (2942+49) Н, скорости движения (60±3) км/ч на мокром дорож-
номспользованиемпокрыт с шины с гладким рисунком протекто-
ра размером 6,45x13", внутреннем давлении воздуха (0,17+0,01) МПа и полож тельных температурах окружающей среды.
хема пр бора пр ведена в стандарте [19, рис. В.1] и на рис. 30.
бА Д И
Рис. 30. Схема проведения испытаний по измерению коэффициента сцепления прибором ППК-МАДИ-ВНИИБД [19]: 1 – положение груза до проведения испытаний; 1' – положение груза после проведения испытаний; 2 – положение имитаторов до проведения испытаний; 2' – положение имитаторов после проведения испытаний; 3 – измерительное кольцо; 4–шкала прибора; 5 – увлажненное дорожное покрытие
43
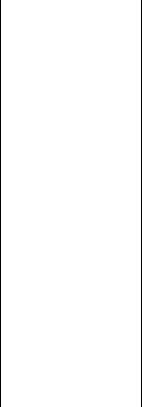
Прибор состоит из основания, на котором закрепляется в вертикальном положении направляющая штанга. В нижней части штанги
|
расположены муфта скольжения, регистрирующая шайба, измери- |
|||||
|
тельная шкала и пружинный механизм с тягами, на конце которых ус- |
|||||
|
тановлены имитаторы шин. В верхней части расположены ударный |
|||||
С |
|
|
|
|
||
|
груз, механизм сброса груза и устройство регулирования пружинного |
|||||
|
механизма. Груз при падении ударяет по подвижной муфте и раздви- |
|||||
|
гает рез новые м таторы шин, |
скользящих по дорожному покры- |
||||
|
тию. Коэфф ц ент сцепления определяется по положению на измери- |
|||||
|
характеристики |
|
рения |
|
|
|
|
тельной шкале рег стр рующей шайбы. |
|
|
|
||
|
Техн ческ е |
ППК-МАДИ-ВНИИБД приведены в |
||||
|
табл. 13. |
|
|
|
Таблица 13 |
|
|
|
|
|
|
||
|
|
Техн ческ е характеристики прибора ППК-МАДИ-ВНИИБД |
||||
|
|
Характер ст ка |
|
Единица изме- |
Величина |
|
|
|
|
|
|
|
|
|
Пределы |
змерен я коэфф циента сцепления |
– |
0,05 – 0,65 |
||
|
Предел допускаемой основной приведенной |
% |
±5 |
|
||
|
погрешности змерен я |
|
|
|||
|
|
|
|
|
||
|
Величины продольных и поперечных уклонов |
|
|
|
||
|
участков измерения не должны превышать |
% |
100 и 60 |
|
||
|
соответственно |
|
|
|
|
|
|
Масса прибора |
|
кг |
25 |
|
|
|
Масса ударного груза |
|
кг |
9±0,05 |
|
|
|
Продолжительность одного цикла измерения |
с |
20 |
|
||
|
не более |
|
|
|
||
|
бА |
|
|
|||
|
Габаритные размеры прибора в собранном |
мм |
160х730х1760 |
|
||
|
виде |
|
|
|
||
|
|
|
|
|
|
|
|
Количество воды для увлажнения покрытия |
И |
|
|||
|
под каждым имитатором, не менее |
|
л |
0,2 |
|
|
|
Д |
|
||||
|
Количество измерений на одном участке единица 5 |
|||||
|
Время приведения прибора в рабочее состоя- |
мин |
5 |
|
||
|
ние из транспортного |
|
|
|||
|
|
|
|
|
||
|
Условия эксплуатации |
|
° С |
0 – 50 |
|
Измерения сцепных свойств дорожного покрытия с помощью прибора ППК-МАДИ-ВНИИБД выполняют по левой полосе наката каждой полосы движения. Требуемое количество измерений на 1 км дороги в зависимости от однородности поверхности покрытия колеблется от 2 до 6. В соответствии с методикой измерения необходимо выполнить стандартные работы по тарировке прибора, в ходе которых необходимо:
44
1. Снять имитаторы и вместо них установить на каждую ось по два тарировочных катка.
2. Прибор устанавливают на гладком ровном покрытии и под катки на покрытие подкладывают тарировочные стальные пластины.
3. Производят окончательную установку прибора таким образом, чтобы катки касались поверхности тарировочных пластин.
4. После сбрасывания груза при тарировке прибор должен фиксировать коэфф ц ент сцепления, равный нулю. Отклонение измерительной шайбы от нулевого деления шкалы не должно превышать
3 – 5 мм.
5. При несоблюдении этого условия необходимо натянуть или |
|
С |
|
ослабить центральную пружину прибора, что достигается путем за- |
|
кручиван я стержня крепления пружины в фиксатор либо его выкру- |
|
чиван я. После |
зменения натяжения центральной пружины измере- |
ния должны |
повторены. Данная операция должна повторяться |
до тех пор, пока |
тарировке измерительная шайба не будет фикси- |
при |
|
ровать постоянно нулевое значение коэффициента сцепления или от- |
|
клоняться от него не олее чем на 7 мм. |
|
При измерении коэффициента сцепления производят следующее: |
быть 1. Прибор устанавливаютАна дорожном покрытии и с помощью
винтов-лап прибора производят его окончательную установку таким образом, чтобы нижняя поверхность резиновых имитаторов находи-
4. Дорожное покрытие должноДбыть увлажнено в зоне непосредственно перед имитаторами и в направлении их движения. Ширина ув-
лась на расстоянии (8 – 12) мм от поверхности дорожного покрытия.
2. На опорную штангу надевают груз, удерживаемый механизмом
сброса.
3. Измерительное кольцо перемещается в верхнее положение, по-
сле чего прибор готов к работе. |
И |
|
лажняемой зоны должна быть не менее 15 см, длина– не менее 50 см. 5. Нажимается кнопка сброса груза.
6. Отсчет значения измеренного коэффициента сцепления получают по положению регистрирующей шайбы на тарировочной шкале прибора.
Иллюстрация нажатия кнопки сброса груза приведена на рис. 6. После нажатия этой кнопки груз из положения, показанного на рис. 1.30 цифрой 1, падает вниз и занимает положение, показанное на рис. 1.30 цифрой 1’. При падении груз ударяет по механизму крепления имитаторов и вызывает их смещение. На рис. 30 положение ими-
45
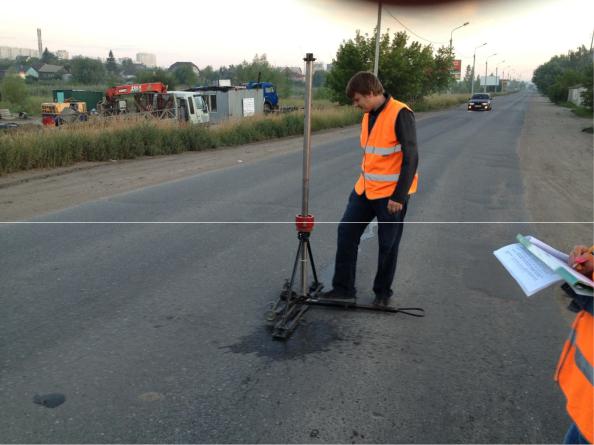
таторов до сброса груза показано цифрой 2, а их положение после удара – цифрой 2’. Перемещение механизма крепления имитаторов вызывает перемещение измерительного кольца по шкале прибора вниз. После удара имитаторы возвращаются в начальное положение, а измерительное кольцо остается в конечном положении. Конечное по-
Сложение измерительного кольца указывает величину коэффициента сцепления. Иллюстрация смещения измерительного кольца в конечное положен е показана на рис. 31, а величина коэффициента сцепления, соответствующая этому положению, приведена на рис. 7.
и бА Д
Рис. 31. Иллюстрация смещения измерительногоИкольца после воздействия падающего груза
К измеренной величине коэффициента сцепления вводят поправку на температуру, принимая ее по табл. 12.
Для измерения параметров шероховатости покрытия широко применяется метод «песчаное пятно». Этот метод регламентирован для оценки параметров шероховатости покрытий [18] и дорожных плит [21].
46
Методика измерения параметров шероховатости методом «песчаное пятно» заключается в измерении средней глубины впадин и высо-
ты выступов шероховатостей покрытия. Для выполнения измерений необходимы: штампы для распределения песка, мерная емкость, мерная линейка, щетка-сметка, природный песок в воздушно-сухом состоянии, гипс или быстротвердеющий цемент, вода [18].
СVп. огласно рекомендациям [18] объем песка должен составлять 200–250 см3. Однако при использовании для измерений готовых комплектов оборудован я требования к объему песка могут быть другие, они пр ведены в нструкциях, прилагаемых производителями к ком-
При измерении средней глубинывпадиннеобходимоследующее[18]: 1. Россыпь на поверхность покрытия определенного объем песка
плекту оборудован я. |
|
2. Равномерное распределение песка вровень с поверхностью вы- |
|
ступов шероховатости, придавая песчаному пятну форму круга (пря- |
|
моугольн ка |
квадрата). Такое распределение выполняется при |
ли |
|
помощи штампа. |
|
3. Про звести |
змерение размеров фигуры, при помощи которых |
можно определить площадь. Измерения выполняются металлической |
|
линейкой. Длябо ъективной оценки размеров песчаной фигуры можно |
|
выполнить несколько измерений, например, измерить 3 и 4 диаметра |
|
круга, а затем вычислить их среднее значение. |
4. Выполнив все измерения, находят средние размеры, например,
средний диаметр, по которому вычисляется площадь круглого пятнаSз. |
|||||||
А |
Sз, определяют- |
||||||
5. Зная объем песка Vп |
и занятую им площадь |
||||||
среднюю глубину впадин. |
|
Vп |
|
|
|
|
|
|
Hср |
. |
|
|
(1) |
||
|
|
|
|
||||
|
|
S |
з |
|
|
|
|
|
Д |
|
|||||
Для определения средней высоты выступов Rср вначале устанав- |
|||||||
ливают среднюю приведенную высоту выступов |
шероховатости |
||||||
Rcр(пр). Для этого: |
|
|
|
|
И |
||
|
|
|
|
|
1.Оконтуривают поверхность, занятую песком.
2.Удаляют песок из впадин шероховатости с помощью щетки и смазывают очищеннуюповерхностьпокрытиятехническимглицерином.
3.Изготавливают жидкое тесто из алебастра.
4.Жидкое тесто распределяют по исследуемой поверхности покрытия слоем 1,0–1,5 см. Через 5 – 7 мин слепок отделяют от покрытия и выдерживают 10 – 15 мин до затвердения.
47

5. После этого определяют объем впадин шероховатости (численно равный объему выступов шероховатости покрытия) с помощью метода "песчаного пятна" и устанавливают объем песка Vв и площадь пятна Sв.
6. реднюю приведенную выступов шероховатости Rcр(пр) опреде- |
||||
С |
|
|
|
|
ляли по формуле |
|
Vв |
|
|
|
Rср пр |
|
. |
(2) |
|
|
Sв |
|
|
редняя высота выступов шероховатости определяется по фор- |
||||
впадин |
|
|
|
|
муле |
Rср Hср Rср пр . |
(3) |
||
Последовательность операций при определении средней глубины |
||||
пр ведена на р с. 32 – 34. |
|
|||
бА |
|
|||
|
Д |
|
||
|
|
|
И |
Рис. 32. Песок, высыпанный из мерной емкости на асфальтобетонное покрытие
48
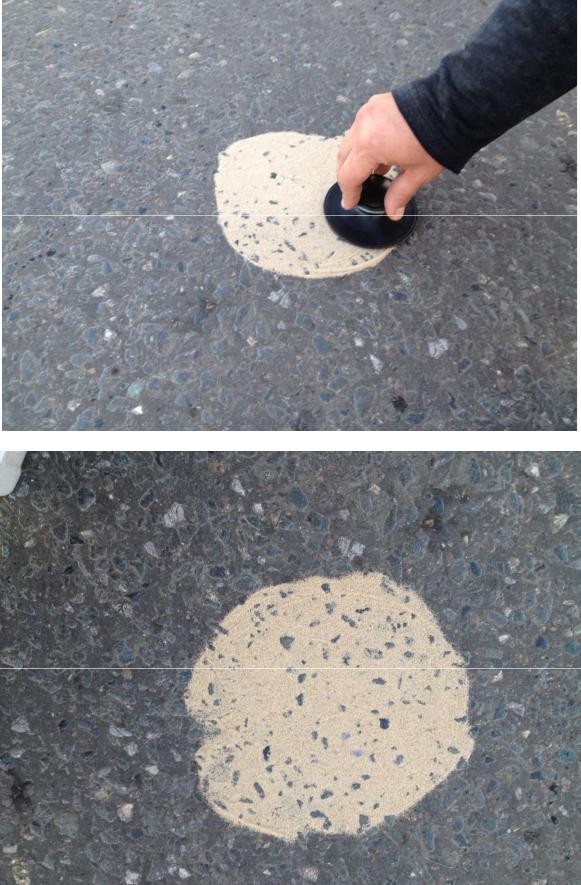
Си
бАРис. 33. Распределение песка штампом в форму круга
Д И
Рис. 34. Песчаное пятно в форме круга
49

Величины Нcр и Rcр(пр) можно получить непосредственными измерениями при помощи линеек, которые входят в комплекты оборудования. Иллюстрации измерений глубины впадин такими линейками приведены на рис. 35 и 36.
Си
бАРис. 34. Измерение параметров шероховатости
специальной линейкой Д И
Рис. 35. Измерение параметров шероховатости специальной линейкой
50
Фактические значения коэффициента сцепления и параметров шероховатости сравнивают с требуемыми значениями и принимают решение о целесообразности или нецелесообразности назначения и выполнения ремонтных мероприятий по доведению этих показателей до требуемых СП 34.13330.2012 [21] или ВСН 38-90 [18] значений.
К мероприятиям по повышению сцепных качеств и шероховатости дорожных покрытий относят различные технологии, позволяющие создать слой ли новую поверхность с требуемым коэффициентом сцепле-
ния и параметрами шероховатости. Условно такие технологии разделим |
||
на трад ц онные, оговоренные в рекомендациях [5], ВСН 38-90 [18], |
||
П 34.13330.2012 [21] современные, информация о которых приво- |
||
С |
|
|
дится в основном в справочной литературе, например, [9]. |
||
Наряду с трад ц онной технологией для устройства поверхност- |
||
ных обработок, слоев |
зноса и защитных слоев может быть примене- |
|
на одна з современных технологий, к которым относят Чип Сил,Фиб |
||
, Мак л, |
С л, Сларри Сил, Кейп Сил и другие «– Силы». |
|
Сил |
||
Некоторые технолог |
|
позволяют получить шероховатый слой. Под |
указанными терм нами понимаются следующие определения [22]: |
||
1. Поверхностная |
о ра отка (ПО) – технологический процесс |
Фоб устройства на дорожныхАпокрытиях тонких слоев с целью обеспечить
шероховатость, водонепроницаемость, износостойкость покрытий. 2. Слой износа (СИ) – верхний слой дорожного покрытия, непо-
изоляции покрытия. Д 4. Шероховатый слой (ШС) – верхний слой дорожного покрытия
средственно воспринимающий усилия от транспортных средств и препятствующий износу основных слоев дорожной одежды.
3. Защитный слой (ЗС)– верхний слой дорожного покрытия, толщиной от 0,5-1,0 мм до 10-15 мм, устраиваемый для защиты по-
крытия от проникания в него поверхностной влаги, то ест ьдля гидро- И
различной толщины, устраиваемый для создания шероховатой поверхности на тех покрытиях, у которых параметры шероховатости не обеспечивают требуемые сцепные качества.
5. Сларри Сил – это технология устройства защитных слоев покрытий с применением литых эмульсионно-минеральных смесей.
6. Микросюрфейсинг является разновидностью эмульсионноминеральной смеси типа Сларри, позволяющей производить укладку смеси более толстым слоем и в несколько слоев, более прочная, с более высокими требованиями к качеству каменного материала.
51
7. Чип Сил – это обработка поверхности, при которой происходит синхронное распределение битумной эмульсии и фракционированного каменного материала, применяется для создания шероховатой поверхности в целях поддержания в рабочем состоянии и продле-
ния долговечности существующих дорог. |
|
пС |
|
8. Кейп Сил – технология, предполагающая одновременное при- |
|
менение слоев поверхностной обработки типа Чип Сил и Сларри Сил. |
|
9. Мак |
л – является шероховатой поверхностной обработкой |
по типу Ч |
л, но сделанная с применением гелеобразоного битума |
циального |
|
Мульт грейд. |
|
10.Фог |
л – это технология нанесения битумной эмульсии спе- |
состава на существующую поверхность в виде тонкого слоя посредством его втирания жесткими щетками, устраивается на
собой |
|
покрыт е, на котором меется открытая пористость, а также выкра- |
|
шиван е матер ала. |
|
11.Скраб с л – представляет |
технологию обработки по- |
верхности по т пу Фог Сил с последующим распределением песка, устраивается на покрытие, на котором обнажен каменный материал или присутствует развитаяАсетка трещин.
12.Фиб Сил – технология устройства водонепроницаемых слоев, в котором применяется сочетание битумной эмульсии и нарезанного стекловолокна с последующим распределением щебня или устройством слоя износа.
Критериями выбора оптимального вида технологии работ в конкретных условиях строительства являются качество и стоимость работ. В общем случае качество автомобильной дороги охватывает ее
транспортно-эксплуатационные, технологические, экологические, эр- |
|
гономические, эстетические и другие свойства, включая ожидаемый |
|
срок службы [20]. |
Д |
2.2. Традиционные способы устройстваИшероховатых поверхностей
Согласно традиционной трактовке по ВСН 38-90 [18] шероховатой называют поверхность дорожного покрытия, образуемую равномерно чередующимися выступами скелетных частиц и впадинами между ними, а также собственной шероховатостью выступов и впадин либо специально созданными бороздками на поверхности покрытия.
Шероховатость подразделяется на макрошероховатость и микрошероховатость. Под термином «макрошероховатость» понимается шероховатость, создаваемая скелетными частицами, то есть зернами
52
каменного материала [18]. Под термином «макрошероховатость» понимается собственная шероховатость зерен каменного материала [18].
|
Из этих определений следует, что шероховатость поверхности |
||||
|
создается за счет макрошероховатости. Поэтому в нормативном до- |
||||
|
кументе [18] в основном используется термин «шероховатость по- |
||||
С |
|
|
|
||
|
крытия», которая характеризуется тремя основными параметрами: |
||||
|
– средней высотой выступов Rz, мм; |
|
|||
|
– средней глуб ной впадин Hcp, мм; |
определяемым |
|||
|
– коэфф ц ентом шага |
шероховатости, |
|||
|
шероховатости |
|
|
||
|
отношен ем средней глубины впадин к средней высоте выступов. |
||||
|
В табл. 14 пр ведена классификация дорожных покрытий по па- |
||||
|
раметрам |
. |
|
|
|
|
|
бА |
Таблица 14 |
||
|
Класс ф кац я ВСН 38-90 [18] дорожных покрытий по параметрам |
||||
|
|
|
шероховатости |
|
|
|
Тип шероховатых по- |
Условные |
Параметры шероховатости |
||
|
|
крыт й |
о означения |
Средняя высота |
Средняя глубина |
|
|
|
|
выступов Rz, мм |
впадин Нср, мм |
|
Гладкие |
|
Гл |
0,1< Rz 0,5 |
0,02< Нср 0,25 |
|
Мелкошероховатые |
Мшер |
0,5< Rz 3,0 |
0,25< Нср 1,5 |
|
|
Мелкошипованные |
Мшип |
– |
1,5< Нср 2,5 |
|
|
Среднешероховатые |
Сшер |
3,0< Rz 6,0 |
1,0< Нср 3,0 |
|
|
Среднешипованные |
Сшип |
– |
3,0< Нср 5,0 |
|
|
Крупношероховатые |
Кшер |
6,0< Rz 9,0 |
2,0< Нср 4,5 |
|
|
Крупношипованные |
Кшип |
– |
4,5< Нср 7,0 |
В табл. 15 приведены требования СП 34.13330.2012 [21] к глуби- |
||||
не впадин шероховатости, определяемых методом «песчаное пятно» |
||||
при помощи прибора типа КП-1319. |
И |
|||
|
ДТаблица 15 |
|||
Требования СП 34.13330.2012 [21] к глубине впадин шероховатости |
||||
Материал верхнего слоя покрытия |
|
|
Минимальная средняя глубина впадин |
|
|
|
шероховатости, мм |
|
|
|
|
|
|
|
Асфальтобетон |
|
|
1,0 |
|
Поверхностная обработка |
|
|
1,2 |
|
Цементобетон |
|
|
0,5 |
|
Из сопоставления данных табл. 14 и 15 следует, что не все типы покрытий, оговоренные в табл. 14, соответствуют требованиям табл. 15 по параметрам «средняя глубина впадин шероховатости». Отсюда следует, что требования СП 34.13330.2012 [21] ссужают область при-
53

менения шероховатых покрытий и методов их устройства, регламентируемых ВСН 38-90 [18] и представленных нами в табл. 16 и 17.
|
|
|
|
|
|
|
Таблица 16 |
|
|
|
Область применения шероховатых покрытий [18] |
||||||
|
Техническая категория дороги |
Тип шероховатого покрытия |
|
|||||
|
|
I |
|
|
|
|
Сшер или Кшер |
|
|
|
II |
|
|
Сшер, Кшер, или Мшер |
|
||
|
|
III |
|
|
Сшер, Кшер, Мшер или Кшип, Сшип |
|
||
|
|
IV V |
|
|
Кшер, Сшер, Кшип, Сшип, Мшер, Мшип |
|
||
|
Тип |
|
|
Таблица 17 |
||||
|
|
|
|
|
|
|
||
|
Класс ф кац я методов устройства шероховатых асфальтобетонных |
|||||||
С |
|
покрытий [18] |
|
|
|
|||
|
(Мшип) |
шероховатого |
|
Методы устройства шероховатых поверхностей на |
|
|||
|
асфальтобетонных |
и других черных покрытиях |
|
|||||
|
|
покрыт я |
|
|
|
|
||
|
|
1 |
|
|
|
|
2 |
|
|
|
|
|
1. Устройство верхнего слоя покрытий из асфальто- |
|
|||
|
|
|
|
етонов типов Б, Бх, Г и типа Дх с использованием в |
|
|||
|
|
|
|
смесях ще ня и дробленого песка из труднополирую- |
|
|||
|
|
|
А |
|
||||
|
Мелкошипованные |
|
щихся горных пород или щебня разной прочности |
|
||||
|
|
|
|
2. Поверхностная обработка битумным щебеночным |
|
|||
|
|
|
|
шламом с содержанием до 40% щебня размером ме- |
|
|||
|
|
|
|
нее 15 мм |
|
|
|
|
|
|
|
|
3. Устройство слоя износа из песчано- |
|
|||
|
|
|
|
|
Д |
|
||
|
|
|
|
резинобитумных смесей. |
|
|||
|
Мелкошипованные |
|
4. Втапливание черного щебня размером до 15 мм в |
|
||||
|
|
количестве 7–10 кг/м2 в поверхность слоя асфальто- |
|
|||||
|
(Мшип) |
|
|
бетона типов В, Вх или х |
|
|||
|
|
|
|
1. Устройство верхнего слоя покрытия из горячего |
|
|||
|
|
|
|
|
|
|
И |
|
|
|
|
|
асфальтобетона типа А с содержанием в смеси |
|
|||
|
|
|
|
50–65% щебня из труднополирующихся горных по- |
|
|||
|
Мелкошероховатые |
|
род размером до 15 мм |
|
|
|||
|
(Мшер) |
|
|
2. Устройство верхнего слоя покрытия из открытых |
|
|||
|
|
|
битумоминеральных смесей с содержанием в смеси |
|
||||
|
|
|
|
|
||||
|
|
|
|
55–65% щебня размером до 15 мм |
|
|||
|
|
|
|
3. Поверхностная обработка с применением битума, |
|
|||
|
|
|
|
эмульсий и мелкого щебня размером до 15 мм |
|
|||
|
Среднешипованные |
|
1 Втапливание черного щебня размером 15–20 или |
|
||||
|
|
20–25 мм в количестве 9–12 кг/м2 в поверхность |
|
|||||
|
(Сшип) |
|
|
|
||||
|
|
|
слоя асфальтобетона типов В, Вх или Дх |
|
||||
|
|
|
|
|
54

|
|
|
|
Окончание табл. 17 |
|
|
1 |
|
2 |
|
Среднешипованные |
2. Устройство верхнего слоя из открытых битумоми- |
||
|
( шип) |
|
неральных смесей с использованием щебня размером |
|
|
|
|
до 20 мм в количестве 55–65% |
|
|
|
|
3. Поверхностная обработка щебеночным битумным |
|
|
|
|
шламом с использованием щебня размером 15–20 мм |
|
|
|
|
в количестве до 40% |
|
С |
1. Поверхностная обработка с применением битума |
|||
(в том числе улучшенного различными добавками) |
||||
ли эмульсии и щебня размером 15-20 мм (в том |
||||
числе разнопрочного) |
||||
2. Поверхностная обработка битумным шламом с ис- |
||||
|
реднешероховатые |
пользованием щебня размером до 20 мм в количестве |
||
|
не менее 55% |
|||
|
( шер) |
бА |
||
|
|
3. Устройство верхнего слоя из открытых битумоми- |
||
|
|
|
неральных смесей с использованием щебня размером |
|
|
идо 20 мм в количестве 66–85% |
|||
|
|
|
4. Втапливание черного щебня размером 20–25 мм в |
|
|
|
|
количестве 9–12 кг/м2 в поверхность слоя асфальто- |
|
|
|
|
етона типов В, Bх или Дх |
|
|
Крупношипованные |
1. Устройство верхнего слоя из открытых битумоми- |
||
|
неральных смесей с использованием щебня размером |
|||
|
(Кшип) |
|
||
|
|
до 25 мм в количестве 65–85% |
||
|
|
|
||
|
|
|
|
Д |
|
|
|
1. Поверхностная обработка с применением битума |
|
|
Крупношероховатые |
(в том числе улучшенного различными добавками) и |
||
|
(Кшер) |
|
щебня размером 20–25 мм (в том числе и разно- |
|
|
|
|
прочного) |
|
Методы устройства шероховатых покрытий, оговоренные в табл. 17, будем называть традиционнымиИспособами. Каждый из этих методов имеет свою область применения, рекомендуемую ВСН 38-90. При устройстве шероховатого покрытия методом поверхностной обработки необходимо применять узкие фракции щебня, а имен-
но: 5–10, 10–15, l5–20, 20–25 мм [18, п. 3.3]. При этом выполнение поверхностной обработки на дорогах I и II категорий с использованием щебня фракций 5–10 и 10–15 мм разрешается только при условии добавления к вяжущему стабилизирующих полимеров.
Согласно классификации [18, п. 5.30] поверхностные обработки с применением битумных эмульсий и вязкого битума подразделяются на три вида:
55
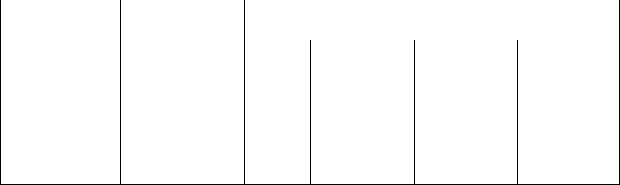
1. Одиночную поверхностную обработку, заключающуюся в том, что на очищенное от пыли и грязи покрытие производят розлив вяжущего с последующей россыпью щебня необходимых фракций и укаткой поверхности.
2. Одиночную поверхностную обработку с двукратной россыпью щебня, отличающуюся тем, что вяжущее разливают в большем количестве, а россыпь щебень выполняют в два приема. Вначале распределяют щебень фракции 15–25 мм, прикатывая его катком, а затем распределяется щебень фракции 5–10 мм, который прикатывают 4–5
разливается щин и мелкбАх повреждений, а также на цементобетонных покрытиях.
проходами катка по одному следу при скорости движения 2–3 км/ч.
3. Двойную поверхностную обработку, при которой вяжущее |
|
С |
ема, а россыпь щебня производят после каждого |
два пр |
|
розлива. Двойную поверхностную обработку применяют при обнару- |
|
жении на покрыт |
повышенного износа, большого количества тре- |
В пособ [23] наряду с применением для поверхностной обработки фракц он рованного ще ня и различных органических вяжущих регламент руются технологии эмульсионно-минеральных смесей литой консистенции на катионных эмульсиях и использование
битумных шламов.
В табл. 18 [23, п. 1.3, та л. 1] приведены рекомендации пособия [23] по выбору спосо а устройства поверхностной обработки покрытий. Данные этой таблицы дополняют рекомендуемую область применения шероховатых покрытий, представленную в табл. 16, детализируя область применения поверхностных обработок.
|
Области применения поверхностных обработок |
Таблица 18 |
||||||||
|
|
|
|
|||||||
|
Дорожно- |
|
|
|
|
И |
|
|||
Условия |
климатическая |
|
|
в зависимости от категории дороги |
||||||
движения |
зона |
|
Д |
|
|
|||||
|
I |
|
|
II |
|
III |
|
IV |
||
Опасные |
I и II |
ПО 1 |
|
ПО 2, ПО 3 |
ПО 2, ПО 3 |
ПО 3 |
|
|||
III и IV |
|
ПО 3, ПО 4 |
ПО 3, ПО 5 |
|
||||||
Затрудненные |
I и II |
ПО 6 |
|
ПО 3, ПО 7 |
ПО 2, ПО 3 |
ПО 3 |
|
|||
III и IV |
|
ПО 4, ПО 3 |
ПО 3, ПО 5 |
|
||||||
Легкие |
I и II |
ПО 9 |
|
ПО 3 |
|
ПО 10, |
ПО 10, |
|
||
III и IV |
|
ПО 3, ПО 5 |
ПО 11 |
ПО 11 |
Примечание. ПО 1 – фракционированный щебень и вяжущие с добавками полимеров; ПО 2 – фракционированный щебень, битумы, дегтебитумные вяжущие или катионные битумные эмульсии; ПО 3 – щебеночные эмульсионноминеральные смеси на катионных эмульсиях; ПО 4 – фракционированный щебень, битумы, дегтебитумные вяжущие или анионные эмульсии;
56

ПО 5 – щебеночные битумные шламы; ПО 6 – фракционированный щебень, битумы или катионные битумные эмульсии; ПО 7 – фракционированный щебень, битумы, дегтеполимерные вяжущие или катионные битумные эмульсии; ПО 8 – щебеночные и песчаные эмульсионно-минеральные смеси на катионных эмульсиях; ПО 9 – фракционированный щебень исходя из нормативного межремонтного срока службы покрытия; ПО 10 – песчаные эмульсионно-минеральные смеси на катионных эмульсиях; ПО 11 – щебеночные и песчаные битумные шламы (кроме I зоны)
огласно 38-90 [18, п. 3.5] горячие асфальтобетонные смеси можно пр менять при устройстве шероховатых поверхностей на ав-
томоб льных дорогах I-III категории. Возможность применения этого |
|
ВСН |
|
метода обуславл вается наличием прочных каменных материалов с |
|
высок м сопрот влен ем шлифующему воздействию автомобильных |
|
шин. Если так е материалы отсутствуют, то можно применить ас- |
|
фальтобетон на основе разнопрочных каменных материалов. Устрой- |
|
ство шероховатых |
методом втапливания применяется на |
покрытий |
|
бА |
дорогах I–III категор й [18, п. 3.6]. Поверхностную обработку покрытий битумными шламами применяют на дорогах III и IV [18, п. 3.8] категорий. Рекомендуется поверхностная обработка покрытий битумными шламами.
Устройство шероховатой поверхности методом одиночной поверхностной обра отки состоит в выполнении ряда технологических
операций, к которым относят:
Очистку покрытия от пыли иДгрязи выполняют механическими щетками, поливочно-моечными и подметально-уборочными машинами. В таблице 19 приведены технические характеристики механической щетки ОЩМ 1,8 и ЩФ 2.5.
– очистку покрытия от пыли и грязи;
– розлив вяжущего;
– россыпь щебня;
– прикатку поверхности катком. И
57

|
|
|
Таблица 19 |
|
|
Технические характеристики щеток механических |
|||
|
Общий вид |
Техническая |
Величина |
|
|
характеристика |
|||
|
|
|
||
С |
Марка щетки |
ОЩМ 1,8 |
||
|
Беларусь |
|||
Тип базового трактора |
80/82 и их мо- |
|||
|
|
|||
|
|
|
дификации |
|
|
и |
Ширина захвата, мм |
1800 |
|
|
Диаметр щетки, мм |
550±20 |
||
|
Эксплуатационная масса, |
230 |
||
|
кг |
|||
|
|
|||
|
|
|
||
|
|
Га аритные размеры |
2325 1905 90 |
|
|
|
7 |
||
|
|
|
||
|
|
Ра очая скорость, км/ч, не |
13 |
|
|
бА |
|||
|
|
олее |
|
|
|
|
Транспортная скорость, |
20 |
|
|
|
км/ч, не более |
||
|
|
|
||
|
|
Техническая (расчетная) |
23400 |
|
|
|
производительность, м2/ч |
||
|
|
Марка щетки |
ЩФ 2.5 |
|
|
|
Тип оборудования |
Навесная |
|
|
|
Ширина захвата, мм |
2500 |
|
|
|
О ъем бака системы оро- |
500 |
|
|
|
шения "Роса", л |
||
|
|
|
||
|
|
Д |
||
|
|
Рабочая скорость, км/ч |
1,9 – 18,4 |
|
|
|
Транспортнаяскорость,км/ч |
30 |
|
|
|
Масса, кг |
300 |
Независимо от материала, из которого изготовленыИструны щеток (нейлон, сталь), они должны быть в хорошем состоянии и достаточно жесткими, чтобы обеспечить эффективное соскабливание [24]. Рекомендации специалистов [24] сводятся к тому, что основную очистку покрытия от пыли и грязи нужно выполнять механическими щетками, а наиболее загрязненные участки, которые не удается очистить щеткой, необходимо промыть с помощью поливомоечной машины.
Мойка и уборка покрытия производятся от оси дороги к обочине. Проезжую часть с разделительной полосой начинают убирать от левой по ходу движения кромки покрытия. Первый проход машины выполняют по оси проезжей части, а остальные производят уступом, и обязательно с перекрытием на 0,25–0,5 м очищенной предыдущим
58

проходом полосы покрытия. Технические характеристики некоторых поливомоечных машин приведены в табл. 20.
|
|
|
|
|
|
|
|
|
Таблица 20 |
|||||||
|
Технические характеристики поливомоечных машин |
|||||||||||||||
|
Общий вид |
Наименование техниче- |
|
|
|
|
Величина |
|
||||||||
|
ской характеристики |
|
|
|
|
|
||||||||||
|
|
|
|
|
|
|
|
|
|
|
|
|
|
|
||
С |
Модель |
|
|
|
|
КО-713Н-40 |
|
|
|
|
||||||
|
|
|
|
|
|
|
|
|
|
|
|
|
|
|
||
Шасси |
|
|
|
|
МАЗ-457043 |
|
|
|
|
|||||||
|
|
|
|
|
|
|
|
|
|
|
|
|
|
|
||
Объем бака для воды, м3 |
|
|
|
6,15 |
|
|
|
|
|
|
|
|||||
Рабочая зо- |
щетки |
|
2,5 |
|
|
|
|
|
|
|
||||||
мойки |
|
8,5 |
|
|
|
|
|
|
|
|||||||
на, м |
|
|
|
|
|
|
|
|
|
|
|
|
|
|
||
полива |
|
20 |
|
|
|
|
|
|
|
|||||||
|
|
|
|
|
|
|
|
|
||||||||
Масса, т |
|
|
12,5 |
|
|
|
|
|
|
|
||||||
|
|
Га ариты, |
длина |
|
|
|
6450–9300 |
|
||||||||
|
|
ширина |
|
|
|
2500–3050 |
|
|||||||||
|
|
мм |
|
|
|
|
|
|
|
|
|
|
|
|
|
|
|
|
высота |
|
3200 |
|
|
|
|
|
|
|
|||||
|
|
|
|
|
|
|
|
|
|
|
||||||
|
и |
Модель |
|
|
|
|
|
КО-806-20 |
|
|
|
|
||||
|
Шасси |
|
|
|
МАЗ-5337А2 |
|
|
|
||||||||
|
|
|
|
|
|
|
|
|
|
|
|
|
|
|||
|
|
О ъем бака для воды, м3 |
|
|
9,0 |
|
|
|
|
|
|
|
||||
|
|
Ра очая зо- |
щетки |
|
2,5 |
|
|
|
|
|
|
|
||||
|
|
мойки |
|
8,5 |
|
|
|
|
|
|
|
|||||
|
|
на, м |
|
|
|
|
|
|
|
|
|
|
|
|
|
|
|
|
полива |
|
20 |
|
|
|
|
|
|
|
|||||
|
|
|
|
|
|
|
|
|
|
|
||||||
|
|
Масса, т |
|
|
18,0 |
|
|
|
|
|
|
|
||||
|
|
Га ариты, |
длина |
|
|
|
7200–9800 |
|
||||||||
|
|
ширина |
|
|
|
2500–3100 |
|
|||||||||
|
|
Д |
|
|||||||||||||
|
|
мм |
высота |
3200 |
|
|
|
|
|
|
|
|||||
|
бА |
|
|
|
|
|
|
|
|
|
||||||
|
|
Модель |
|
|
|
|
КО-823-1 |
|
|
|
||||||
|
|
Шасси |
|
|
КамАЗ-65115 |
- |
|
|
||||||||
|
|
|
|
|
|
1071 |
|
|
|
|
|
|
|
|||
|
|
Объем бака для воды, м3 |
|
|
|
|
13,0 |
|
|
|
|
|
|
|
||
|
|
|
И |
|
||||||||||||
|
|
Рабочая зо- |
щетки |
2,5 |
|
|
|
|
|
|
|
|||||
|
|
мойки |
8,5 |
|
|
|
|
|
|
|
||||||
|
|
на, м |
полива |
20 |
|
|
|
|
|
|
|
|||||
|
|
Масса, т |
|
|
20,5 |
|
|
|
|
|
|
|
||||
|
|
Габариты, |
длина |
|
|
8000–12100 |
|
|||||||||
|
|
ширина |
|
|
2950–3440 |
|
||||||||||
|
|
мм |
|
|
|
|
|
|
|
|
|
|
|
|
|
|
|
|
высота |
3200 |
|
|
|
|
|
|
|
||||||
|
|
|
|
|
|
|
|
|
|
Выполнив очистку покрытия, необходимо произвести розлив вяжущего по сухому, чистому покрытию. На практике возникают случаи, когда существующее покрытие не удается полностью очистить. На таких покрытиях пыль и грязь остается в мелких дефектах, например трещинах. В этом случае существующее покрытие необходимо
59

подгрунтовать, выполнив розлив жидкого битума или эмульсии автогудронатором. Рекомендуемые нормы расхода жидкого битума или битумной эмульсией можно принять по рекомендации [24] 0,3– 0,5 л/м2 и 0,5–0,8 л/м2 соответственно. Необходимость подгрунтовки состоит в том, чтобы связать частицы пыли для того, чтобы они не снижали сцепления каменного материала поверхностной обработки с поверхностью существующего покрытия, на котором устраивают поверхностную обработку. При применении для подгрунтовки жидких битумов предпочтен е отдают среднегустеющим или медленногустеющ м б тумам марок СГ15/25, СГ 25/40, МГ 25/40.
|
Для подгрунтовки и розлива вяжущего, который производится |
||||||
С |
|
|
|
|
|
||
|
после загустеван я подгрунтовки, применяют автогудронаторы. Тех- |
||||||
|
е характер ст ки некоторых автогудронаторов приведены в |
||||||
|
ническ |
|
|
Таблица 21 |
|||
|
|
|
|
|
|||
|
табл. 21. |
бА |
|
|
|||
|
|
Техн ческие характеристики автогудронаторов |
|||||
|
|
Общ й в д |
Наименование технической |
Величина |
|
||
|
|
характеристики |
|
||||
|
|
|
|
|
|||
|
|
1 |
|
2 |
|
3 |
|
|
|
|
Модель автогудронатора |
БЦМ-65 |
|
||
|
|
|
Емкость цистерны, 8 |
8000 |
|
||
|
|
|
Базовое шасси |
КамАЗ-53215 |
|
||
|
|
|
ДС |
|
|||
|
|
|
Полная масса, т |
18,1 |
|
||
|
|
|
Габариты |
|
лина, мм |
9200 |
|
|
|
|
|
Ширина, мм |
2500 |
|
|
|
|
|
|
|
Высота, мм |
3350 |
|
|
|
|
Характери- |
|
Ширина, м |
2,5–4,2 |
|
|
|
|
стики розлива |
|
Норма, л/м2 |
0,2–3,0 |
|
|
|
|
Модель автогудронатора |
-142Б |
|
||
|
|
|
Емкость цистерны, 8 |
7500 |
|
||
|
|
|
Базовое шасси |
КамАЗ-56100 |
|
||
|
|
|
Полная масса, т |
25,2 |
|
||
|
|
|
Габариты |
|
Длина, мм |
8355 |
|
|
|
|
|
Ширина, мм |
2550 |
|
|
|
|
|
|
|
И |
|
|
|
|
|
|
|
Высота, мм 3005 |
||
|
|
|
Характери- |
|
Ширина, м |
4,0 |
|
|
|
|
стики розлива |
|
Норма, л/м2 |
0,3–2,5 |
|
60

|
|
|
|
|
Окончание табл. 21 |
|
|
1 |
|
2 |
|
|
3 |
|
|
Модель автогудронатора |
ДМ-39Б |
|||
|
|
Емкость цистерны, 8 |
4000 |
|||
|
|
Базовое шасси |
ЗИЛ-433362 |
|||
|
|
Полная масса, т |
11,0 |
|||
|
|
Габариты |
|
|
Длина, мм |
6650 |
|
|
|
|
Ширина, мм |
2450 |
|
|
|
|
|
|
Высота, мм |
2650 |
|
|
Характери- |
|
|
Ширина, м |
4,0 |
|
|
стики розлива |
|
|
Норма, л/м2 |
0,5–5,0 |
С |
Модель автогудронатора |
АРБ-7 |
||||
Емкость цистерны, 8 |
7000 |
|||||
|
и |
Базовое шасси |
МАЗ-5337 |
|||
|
Полная масса, т |
16,0 |
||||
|
Га ариты |
|
|
Длина, мм |
8500 |
|
|
|
|
Ширина, мм |
2500 |
||
|
|
|
|
Высота, мм |
3300 |
|
|
|
Характери- |
|
|
Ширина, м |
0,2–40 |
|
|
стики розлива |
|
|
Норма, л/м2 |
0,5–3,0 |
|
бА |
|
|
|
||
|
|
|
Вяжущее разливают полосами, избегая его излишков в отдельных местах. Для равномерного розлива используют автоматы, обеспечивающие постоянство расхода вяжущего материала на единицу площа-
Д |
|
|
ди обрабатываемой поверхности. Расход вяжущего на 1 м2 |
обрабаты- |
|
ваемой поверхности в единицу времени определяют по формуле |
|
|
q Q , |
|
(4) |
B |
|
|
где Q – расход вяжущего, протекающего по главному трубопроводу, л; |
||
И |
B – ширина полосы розлива, м; V – скорость движения автогудронатора, м/мин.
Расход вяжущего Q допускается назначать согласно рекомендациям нормативных документов, например ВСН 38-90 [18, п. 5.34].
После нанесения вяжущего по нему распределяют щебень. Для распределения щебня применяют самоходные или навесные и прицепные pacпpeделители. После россыпи щебня производят укатку звеном катков. Вначале применяют средний каток, который выполняет два-три прохода по одному следу, а затем – тяжелый, который выполняет не менее двух проходов по одному следу [18]. При выборе катка необходимо руководствоваться критерием лучшего формирования поверхностной обработки. Для этого ВСН 38-90 [18] рекомендует
61
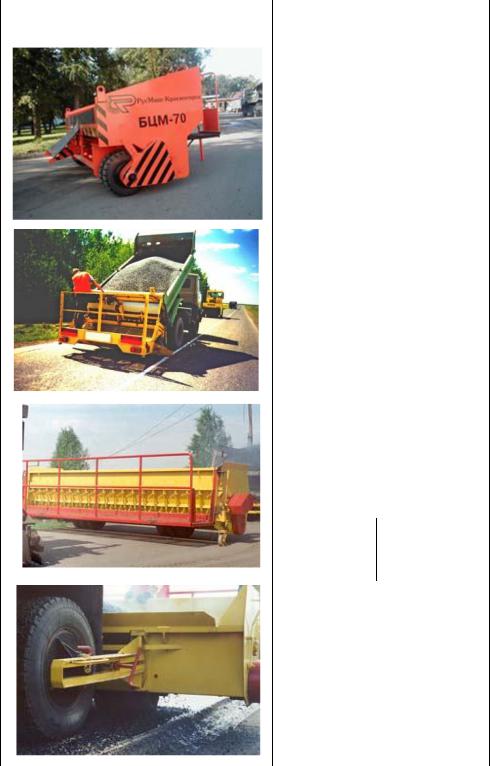
применять самоходные катки на пневматических нишах или катки с обрезиненными металлическими вальцами.
|
|
|
|
|
|
|
|
|
Таблица 22 |
|||||||
|
Технические характеристики навесных и прицепных распределителей щебня |
|||||||||||||||
|
Общий вид |
Технические |
|
|
|
|
Величина |
|
||||||||
|
характеристики |
|
|
|
|
|
||||||||||
|
|
|
|
|
|
|
|
|
|
|
|
|
|
|
||
С |
Марка |
|
|
|
|
|
|
БЦМ-70 |
|
|
|
|
|
|
||
|
|
|
|
|
|
|
|
|
|
|
|
|
|
|||
Тип |
|
|
|
|
Прицепной |
|
|
|
|
|||||||
|
|
|
|
|
|
|
|
|
|
|
|
|||||
Тягач |
|
|
|
ЗИЛ, КамАЗ |
|
|
|
|||||||||
Емкость бункера щебня, м3 |
|
1,5 |
|
|
|
|
|
|
|
|||||||
Ширина обработки, мм |
|
3000 |
|
|
|
|
|
|
|
|||||||
Масса, кг |
|
|
1500 |
|
|
|
|
|
|
|
||||||
Га ариты, |
длина |
|
3200 |
|
|
|
|
|
|
|
||||||
|
|
ширина |
|
3100 |
|
|
|
|
|
|
|
|||||
|
|
мм |
|
|
|
|
|
|
|
|
|
|
|
|
|
|
|
|
высота |
|
2000 |
|
|
|
|
|
|
|
|||||
|
|
|
|
|
|
|
|
|
|
|
||||||
|
бА |
|
|
|
|
МКДС 3.0 |
|
|
|
|
|
|||||
|
и |
Марка |
|
|
|
|
|
|
|
|
||||||
|
Тип |
|
|
|
|
|
Навесной |
|
|
|
||||||
|
Тягач |
|
|
МАЗ, КамАЗ |
|
|
||||||||||
|
|
Ширина обработки, мм |
|
|
|
|
160–3180 |
|
|
|||||||
|
|
Масса, кг |
|
|
810 |
|
|
|
|
|
|
|
||||
|
|
Га ариты, |
длина |
|
3180 |
|
|
|
|
|
|
|
||||
|
|
ширина |
|
1800 |
|
|
|
|
|
|
|
|||||
|
|
мм |
|
|
|
|
|
|
|
|
|
|
|
|
|
|
|
|
высота |
|
1500 |
|
|
|
|
|
|
|
|||||
|
|
|
|
|
|
|
|
|
|
|
||||||
|
|
Марка |
|
|
|
|
|
|
ЩР-450 |
|
|
|
||||
|
|
|
|
|
|
|
|
|
|
|
||||||
|
|
Тип |
|
|
|
|
Прицепной |
|
|
|
||||||
|
|
|
|
|
|
|
|
|||||||||
|
|
Тягач |
|
|
КрАЗ, КамАЗ |
|
|
|||||||||
|
|
|
|
|
|
|
|
|
|
|
|
|
|
|
|
|
|
|
Емкость бункера щебня, м |
3 |
1,9 |
|
|
|
|
|
|
|
|||||
|
|
|
|
|
|
|
|
|
|
|||||||
|
|
Ширина обработки, мм |
|
4500 |
|
|
|
|
|
|
|
|||||
|
|
Масса, кг |
|
|
2400 |
|
|
|
|
|
|
|
||||
|
|
|
длина |
|
5010 |
|
|
|
|
|
|
|
||||
|
|
Габариты, |
И |
|
||||||||||||
|
|
ширина |
|
3316 |
|
|
|
|
|
|
|
|||||
|
|
мм |
|
|
|
|
|
|
|
|
|
|
|
|
|
|
|
|
Двысота 1315 |
|
|||||||||||||
|
|
Марка |
|
|
|
|
|
|
ЩР-360 |
|
|
|||||
|
|
Тип |
|
|
|
|
Прицепной |
|
|
|||||||
|
|
Тягач |
|
|
КрАЗ, КамАЗ |
|
|
|||||||||
|
|
Емкость бункера щебня, м3 |
1,5 |
|
|
|
|
|
|
|
||||||
|
|
Ширина обработки, мм |
|
3600 |
|
|
|
|
|
|
|
|||||
|
|
Масса, кг |
|
|
2000 |
|
|
|
|
|
|
|
||||
|
|
Габариты, |
длина |
|
5010 |
|
|
|
|
|
|
|
||||
|
|
ширина |
|
3316 |
|
|
|
|
|
|
|
|||||
|
|
мм |
|
|
|
|
|
|
|
|
|
|
|
|
|
|
|
|
высота |
|
1315 |
|
|
|
|
|
|
|
|||||
|
|
|
|
|
|
|
|
|
|
|
62