
- •ВВЕДЕНИЕ
- •1. РОЛЬ, НАЗНАЧЕНИЕ И ОСОБЕННОСТИ ПРОИЗВОДСТВЕННЫХ ПРЕДПРИЯТИЙ ДОРОЖНОГО ХОЗЯЙСТВА
- •1.1. Общие сведения о производственных предприятиях дорожного хозяйства
- •1.3. Организация контроля качества продукции производственных предприятий дорожного хозяйства
- •2. КАРЬЕРЫ НЕРУДНЫХ СТРОИТЕЛЬНЫХ МАТЕРИАЛОВ
- •2.1. Классификация карьеров
- •2.2. Изыскания месторождений полезных ископаемых
- •2.3. Разработка горных пород
- •2.4. Выемка и погрузка горной породы
- •3.1. Классификация асфальтобетонных заводов
- •3.2. Технологические процессы на АБЗ
- •3.6. Транспорт производственных предприятий
- •4. ЦЕМЕНТОБЕТОННЫЕ ЗАВОДЫ
- •4.1. Назначение и классификация цементобетонных заводов
- •4.2. Приготовление цементобетонной смеси
- •4.4. Проектирование генеральных планов ЦБЗ
- •5. СКЛАДСКОЕ ХОЗЯЙСТВО ПРОИЗВОДСТВЕННЫХ ПРЕДПРИЯТИЙ
- •5.1. Организация материально-технического снабжения производственных предприятий дорожно-строительными материалами
- •5.3. Назначение складов и их классификация
- •5.4. Организация складских работ и технико-экономические показатели работы склада
- •5.6. Основные требования к складской переработке каменных материалов
- •5.7. Транспортирование каменных материалов и погрузочно-разгрузочные работы на складах
- •5.10. Транспортирование порошкообразных материалов и погрузочно-разгрузочные работы на складах
- •5.12. Основные требования к складской переработке органических вяжущих
- •5.14. Технологические схемы и компоновка складов органических вяжущих
- •5.15. Примеры технологических расчетов
- •6.1. Классификация заводов и полигонов
- •6.2. Технология изготовления изделий и конструкций
- •6.3. Способы производства железобетонных изделий
- •7. БИТУМНЫЕ И ЭМУЛЬСИОННЫЕ БАЗЫ
- •7.1. Назначение и размещение битумных баз
- •7.2. Технологические процессы подготовки органических вяжущих
- •7.4. Основные технологические операции при получении эмульсии
- •7.6. Охрана труда при приготовлении битумных эмульсий
- •8. ТРЕБОВАНИЯ БЕЗОПАСНОСТИ НА ПРОИЗВОДСТВЕННЫХ БАЗАХ И ЗАВОДАХ
- •8.1. Общие требования
- •8.2. Охрана труда
- •8.3. Требования безопасности на битумных и эмульсионных базах
- •8.5. Техника безопасности при эксплуатации ЦБЗ
- •8.6. Охрана труда на полигонах и заводах
- •Библиографический список
- •Приложение 1
- •Приложение 2
- •Приложение 3
- •Приложение 4
- •Приложение 5
- •Приложение 6
- •Приложение 7
- •Приложение 8
- •Приложение 9
- •Приложение 10
- •Приложение 11
- •Приложение 13
3.6. Транспорт производственных предприятий
Основными видами транспорта на производственном предприятии являются железнодорожный и автомобильный, редко – водный.
Длина разгрузочного фронта для железнодорожного пути определя-
ется [6]: |
|
L = n · l + l1 · (n – 1), |
(3.1) |
где l – дл на вагона; l1 – расстояние между вагонами; n – число вагонов, |
|
n = Nед · T/Tн, |
(3.2) |
здесь T – время, затрач ваемое на разгрузку одного вагона; |
Nед – общее |
Счисло транспортных ед ниц в наземном составе; Tн – договорное время, |
|
отведенное железной дорогой в соответствии с Уставом железных дорог. |
|
Грузоподъемность крытых вагонов и платформ – 50–60 т. Длина ва- |
|
гона – 15 м, хопры – 12,4 м, думкары – 12,8 м. Согласно Уставу железных |
дороги дорог, массабАгруза в одной подаче должна составлять 500 т.
Автомоб льные на предприятии проектируют исходя из объема грузооборота. О ычно проектируют кольцевую магистраль с вспомогательными дорогами.
Производственное предприятие с размером площадки более 5 га должно иметь не менее двух выездов. Ширину выездов принимают не менее 4,5–4,9 м. При тупиковых дорогах должны быть предусмотрены петлевые объезды или площадки 12х12 м для разворота автомобилей. Расстоя-
ние от края проезжей части дорогиДдо зданий и сооружений принимают от
0,5 до 12 м. Ко всем зданиям должны быть обеспечены подъезды для пожарных автомобилей. Дороги должны иметь капитальное покрытие, только на заводах кратковременного действия разрешается применять покрытие щебеночное, или гравийное, или из укрепленных материалов. Внутри-
заводской транспорт выбирают в зависимости отИхарактера перемещаемых грузов. Рекомендуется использовать трубопроводный, пневматический,
гидравлический и конвейерный транспорт.
На территории завода должен быть обеспечен водоотвод за счет устройства поверхностных лотков, дренажа или ливневой канализации. Кроме этого, должны быть проложены все инженерные сети – фекальная канализация, теплопровод, газопровод, котельные сети. Выбор способа прокладки инженерных сетей (поземный, надземный или подземный) производится на основании технико-экономических расчетов.
При прокладке инженерных сетей к ним предъявляют следующие требования:
- прокладку сетей следует вести вдоль проездов, параллельно линии застройки;
62

- прокладку вести в местах, удобных для последующего ремонта се-
тей;
- прокладка наземных или подземных сетей не должна стеснять движение транспорта и работников предприятия, не должна лишать освещения.
СПри вертикальной планировке территории предприятия уклоны поверхности площадки следует принимать не менее 3‰ и не более 50‰ для глинистых грунтов, не более 30‰ для песчаных и не более 10‰ для легкоразмываемых грунтов.
изготовлен3.7. Обеспечен е предприятий электроэнергией, водой, паром
и сжатым воздухом
водственного предпр ят я, вида выпускаемой продукции, технологии её я, кол чества ра очих, времени года, суток и местных усло-
вий.
Потребность в воде и электроэнергии зависит от мощности произ- бА
Расчет потре ности в электроэнергии. Потребление электроэнер-
гии для стац онарных предприятий производится от постоянных сетей действующих систем. Передвижные предприятия используют передвижные электростанции. Электроэнергия необходима для питания силовых двигателей, освещения ра очих мест и т.д. Все потребители электроэнер-
гии делятся на три категории:
влечь опасность для жизни людей, брак продукции (карьеры, котельные и т.д.);
II категория – строительные машины и механизмы. Возможны простои механизмов, транспорта, рабочих и т.д. (цех помола, компрессорные
станции и т.д.);
I категория – потребители, нарушениеДпитания которых может по-
III категория – щебеночные заводы, гравийно-сортировочные заводы, склады, наружное освещение и т.д.
Для обеспечения надежного энергоснабжения необходимо иметь два
независимых источника питания, т.е. две трансформаторные подстанции.
Потребную мощность Р трансформаторной подстанции определяют
И
по формуле [6] |
|
|
|
|
|
|
|
|
|
|
|
|
|
|
|
|
P 1,1 |
P k |
cos |
P k |
2 |
cos |
|
P |
k |
3 |
|
|
P |
k |
4 |
, (3.3) |
|
c |
1 |
|
t |
|
ов |
|
|
он |
|
|
где 1,1 – коэффициент, учитывающий потери мощности в сети; Рс – силовая мощность силовых установок; Pt – потребная мощность на технологические нужды; Рoв – потребная мощность для внутреннего освещения, определяется по нормам освещения на 1 м2 площади помещения; Pон – по-
63
требная мощность для наружного освещения, принимается на 1 м2 площади помещения; cosφ – коэффициент мощности, зависящий от количества и загрузки потребителей; k1, k2, k3, k4 – коэффициенты спроса.
Расчет потребности в воде. Суммарная потребность воды за смену на заводе
С |
Q qx qб qo qпр qn , |
|
(3.4) |
|
||||||
|
|
|
|
|||||||
где qх |
– сменная |
потребность воды |
на хозяйственные |
нужды, |
||||||
qх = 0,025 м3/см на 1 чел.; qб – потребность воды на бытовые нужды, |
||||||||||
qб = 0,06 м3/см на 1 чел.; qо – потребность воды на охлаждение компрес- |
||||||||||
При |
|
|
|
|
|
|
|
|||
сорной, qо = 1,5 м3/ч; |
qпр – потребность воды на производственные нужды, |
|||||||||
qпр = 20 |
м3/см; qп – |
|
потребность воды на тушение возможного пожара. |
|||||||
|
|
|
|
|
|
3 |
/с, qп = 0,005∙3∙3600 = |
|
3 |
. |
Время тушен я 3 ч при расходе воды 0,005 м |
54 м |
|||||||||
|
расчете потре ности в воде необходимо учитывать неравномер- |
|||||||||
ность её |
|
я, коэффициент неравномерности потребления воды |
||||||||
|
потреблен |
|
|
|
|
|||||
составляет: |
|
|
|
|
|
|
|
|
|
|
- на хозяйственные нужды – 3; |
|
|
|
|
|
|||||
- бытовые нужды – 1,3; |
|
|
|
|
|
|
|
|||
- охлажден е компрессорной – 1,2. |
|
|
|
|
||||||
|
|
|
А |
|
|
|
||||
При определении расхода воды на цементобетонном заводе необхо- |
||||||||||
димо дополнительно учитывать расход воды на приготовление бетонной |
||||||||||
|
|
|
3 |
|
3 |
смеси, и коэффициент неравномерно- |
||||
смеси qпригот., равный 0,2 м на 1 м |
|
|||||||||
сти потребления 1,3. |
|
|
|
|
|
|
|
|
|
|
Расход воды на асфальто етонном заводе зависит от количества ви- |
||||||||||
|
|
|
|
Д |
|
|
||||
дов выпускаемой продукции, применяемого оборудования, состава произ- |
||||||||||
водственных цехов и вспомогательных хозяйств. |
|
|
|
|||||||
Расход воды (л/с) [6] |
|
|
1,2 K Q |
|
|
|
||||
|
|
|
Qрасч |
|
|
3600 T |
, |
|
(3.5) |
|
|
|
|
|
|
|
И |
||||
|
|
|
|
|
|
|
где 1,2 – коэффициент, учитывающий неучтенные потери (утечка воды, неучтенные личные потребности и т.д.); К – коэффициент неравномерности потребления воды в течение смены, равный 1,1–1,6; Т – продолжительность смены, ч.
Вода на асфальтобетонном заводе расходуется на хозяйственные нужды, для пожарных целей, для работы обеспыливающих устройств, питания паровых котлов, изготовления битумных эмульсий, поливки территории завода и т.д.
Для каждой из вышеуказанных целей производится специальный расчет воды. Диаметр труб (м) водопроводной сети определяется по формуле [6]
64

|
d |
|
|
4Qрасч |
, |
(3.6) |
|
|
|
v 1000 |
|||
|
|
|
|
|
|
|
где v – скорость движения воды в трубе, равная 1,0–1,5 м/с; Qрасч |
– потреб- |
|||||
ность в воде, л/смену. |
|
|
|
|
|
|
С |
|
|
|
|
|
|
уммарная потребность в сжатом воздухе на асфальтобетонном |
||||||
заводе |
V V1 |
V2 V3 |
V4 , |
(3.7) |
||
где V1 – расход сжатого воздуха на распыление топлива у форсунок; |
||||||
ских |
|
|
|
|
V3 – то же |
|
V2 – то же на пневмат ческий транспорт минерального порошка; |
||||||
на работу пневмат ческ х инструментов; V4 – то же на работу автоматиче- |
||||||
систем управлен я. |
|
|
|
|
|
|
Расход сжатого воздуха на распыление топлива у форсунки |
(3.9) |
|||||
бАq v , |
||||||
|
|
n |
|
|
|
|
|
V1 n v1 qф k , |
(3.8) |
||||
|
|
1 |
|
|
|
|
где n – кол чество форсунок различного типа; v1 – удельный расход воздуха на распылен е топлива форсункой (ориентировочно принимается 0,7–1,0 м3/кг топлива); qф – расход топлива форсунками за 1 ч работы; k – коэффициент одновременности, равный при работе двух форсунок 1,0;
трех – 0,9; четырех – 0,85; пяти – 0,82.
Расход сжатого воздуха на пневматический транспорт минерального
порошка |
|
Д |
|||
|
в |
π d 2 |
р |
|
|
|
|
4 |
|
|
|
где vр – рабочая скорость воздуха, м/с, vр = 9–25 м/с; d – внутренний диа- |
|||||
метр трубопровода, м. |
|
|
|
И |
|
Расход сжатого воздуха на работу пневматических инструментов |
|||||
|
|
n |
|
|
|
|
V3 nn |
vм k , |
|
(3.10) |
|
|
|
1 |
|
|
|
где nn – количество инструментов того или иного типа; vм – |
расход возду- |
ха каждым механизмом, берётся из технической характеристики механизма, м3/мин; k – коэффициент одновременности работы для данного типа механизмов.
Расход сжатого воздуха для работы автоматических систем управления V4 определяется с учетом технических характеристик потребителей.
65

Расчетный суммарный расход сжатого воздуха, м3/мин, |
|
||||
|
Vр V Кп.в, |
|
|
(3.11) |
|
kп.в – коэффициент, учитывающий потери воздуха в компрессоре и возду- |
|||||
ховоде, равный 1,4–1,7. |
|
|
|
|
|
С |
|
|
|
|
|
По полученному требуемому расходу сжатого воздуха выбирается |
|||||
количество компрессоров. Характеристики стационарных и передвижных |
|||||
компрессорных станц й приведены в работе [4, прил. 8]. |
|
||||
Д аметр воздуховодов (см) приближенно можно определить по фор- |
|||||
муле |
|
|
|
|
|
|
dтр |
3,18 |
|
|
(3.12) |
|
Vв , |
|
|||
где Vв – кол чество воздуха, проходящего по рассчитываемому участку |
|||||
трубопровода, м3/м н. |
|
|
|
|
|
бА1 1 |
|
||||
Суммарная потре ность в паре на асфальтобетонном заводе |
|
||||
иP P P P P P , |
(3.13) |
||||
1 |
2 |
3 |
4 |
5 |
|
где P1 – расход пара на слив |
итума из железнодорожных цистерн; P2 – то |
же на нагрев вяжущего в итумохранилищах; P3 – то же на обогрев трубопроводов; P4 – то же на распыление топлива в форсунках; P5 – то же на отопление.
Расход пара на нагрев итума в битумохранилище, |
приямке, в же- |
||||
лезнодорожном вагоне определяется по формулам |
|
|
|||
|
Д |
(3.14) |
|||
|
P |
Q |
q; |
|
|
|
P2 |
Q2 |
q, |
|
(3.15) |
где Q1, Q2 – расход тепла на нагрев вяжущего; q – теплосодержание пара, |
|||||
ккал/кг. |
|
|
И |
||
|
|
|
|
|
|
Суммарный расход пара на распыление топлива, кг/ч, |
|
|
|||
|
P4 |
q П qТ , |
(3.16 ) |
где q – удельный расход пара, подаваемого через форсунку на 1 кг израсходованного топлива, кг (при тепловых расчетах сушильных барабанов принимается q = 0,6 кг); П– суммарная производительность асфаль-
тосмесительных установок; qТ – удельный расход топлива на 1 т приготавливаемой асфальтобетонной смеси, кг (в среднем qТ = 8 кг/т).
Расход пара на обогрев трубопровода определяется из расчета, что потери тепла на 1 м битумопровода диаметром 75–100 мм равны
66

150 ккал/ч. Тогда суммарные потери тепла за 1 ч при длине трубопровода L составляют
Q3 = 150 ∙ L ккал/ч, |
(3.17) |
а расход пара, кг, будет |
|
P3 Q3 q, |
(3.18) |
С |
|
где q – теплосодержание 1 кг пара, ккал/кг. |
|
Расход пара на отопление зависит от температуры наружного возду- |
|
ха, количества и объема производственных и бытовых помещений, харак- |
тера про зводственного процесса и количества рабочих.
Зная суммарную потребность пара на асфальтобетонных заводах, |
|||||
коэффициент |
|
|
|
||
выбирают необход мую поверхность нагрева котла Fк: |
|
||||
|
F |
|
P kз Kn |
, |
(3.19) |
|
к |
|
q |
|
|
где Fк – |
бА |
пара, кг/ч; |
|||
поверхность нагрева |
котла, м2; Р – потребность |
||||
kз – коэфф |
ент запаса, учитывающий неравномерность потребления па- |
||||
ра, равный 1,2; Kn – |
|
, учитывающий потери пара при подаче |
его от котельной до мест потре ления, равный 1,1–1,2; q – производительность котла – съем пара с 1 м2 площади нагрева (q ≈15–40 кг/м2∙ч).
По установленному значению Fк выбирают тип и количество котлов.
3.8. Контроль качества исходных материалов асфальтобетонных смесей и асфальто етонов
Асфальтобетонная смесь – рациональноДподобранная, приготовленная путем смешения в нагретом состоянии смесь, состоящая из щебня, песка, минерального порошка, битума и различных добавок (поверхност- но-активных добавок, активаторов и др.).
Асфальтобетон – уплотненная при рациональном температурном режиме до требуемой плотности асфальтобетоннаяИсмесь.
Асфальтобетонные смеси и асфальтобетон должны удовлетворять требованиям ГОСТ 9128–13[17].
Согласно ГОСТ 9128–13, асфальтобетонные смеси подразделяются на щебеночные, гравийные и песчаные.
В зависимости от вязкости применяемого битума и температуры при укладке асфальтобетонные смеси делятся на горячие и холодные.
Горячие асфальтобетонные смеси приготавливают с использованием вязких битумов марок: БНД 40/60, БНД 60/90, БНД 130/200, БНД 200/300, БН 40/60, БН 60/90, БН 90/130, согласно ГОСТ 22245 [24], укладываемых при температуре на менее 120 °С; холодные асфальтобетонные смеси приготавливают с использованием жидких битумов СГ 70/130, СГ 130/200,
67
МГ 70/130, МГ 130/200, МГО 70/130, МГО 130/200, согласно ГОСТ 11955 [25], укладываемых при температуре смеси не ниже 5 °С.
Выбор марки битума зависит от дорожно-климатической зоны района строительства, в которой будет использоваться приготовленная ас-
|
фальтобетонная смесь. |
|
|
|
|
|
|
|
С |
|
|
|
|
|
|
|
|
|
В зависимости от наибольшего размера минеральных зерен горячие |
|||||||
|
смеси и асфальтобетоны подразделяют: |
|
|
|
||||
|
на крупнозернистые – размер зерен |
до 40 мм; |
|
|
||||
|
мелкозерн стые – |
-«- |
|
|
до 20 мм; |
|
|
|
|
песчаные – |
|
-«- |
|
|
до 10 мм. |
|
|
|
мости |
|
|
|
|
|
||
|
По вел ч не остаточной пористости асфальтобетоны подразделяют |
|||||||
|
на виды: |
|
|
|
|
|
|
|
|
высокоплотные – остаточной пористостью 1,0–2,5%; |
|
|
|||||
|
плотные – |
|
|
-«- |
2,5–5,0%; |
|
|
|
|
б |
5,0–10%; |
|
|
||||
|
пор стые – |
|
|
-«- |
|
|
||
|
высокопор стые – |
|
-«- |
свыше 10%. |
|
|
||
|
В зав с |
от процентного содержания щебня асфальтобетонные |
||||||
|
смеси подразделяют на т пы: |
|
|
|
|
|
||
|
А – многоще ен стые – |
50–60%; |
|
|
|
|||
|
Б – среднеще енистые – |
40–50%; |
|
|
|
|||
|
В – малоще енистые – |
30–40%; |
|
|
|
|||
|
Г – песчаные |
из отсевов дробления; |
|
|
|
|||
|
Д – песчаные |
из природного песка. |
|
|
|
|||
|
В зависимости от физико-механических показателей асфальтобетоны |
|||||||
|
|
|
|
Д |
||||
|
подразделяют на марки (табл. 3.3). |
|
|
|
||||
|
|
А |
Таблица 3.3 |
|||||
|
Марки асфальтобетонных смесей в зависимости от видов |
|
|
|||||
|
|
|
и типов асфальтобетонов |
|
|
|||
|
Виды и типы асфальтобетонов |
|
|
Марки |
|
|
||
|
Горячие высокоплотные |
|
|
|
|
I |
|
|
|
Плотные типов: |
|
|
|
|
|
|
|
|
А |
|
|
|
|
I, II |
|
|
|
Б, Г |
|
|
|
|
I, II, III |
|
|
|
В, Д |
|
|
|
|
II, III |
|
|
|
Пористые и высокопористые |
|
|
|
I, II |
|
|
|
|
Требования к асфальтобетонным смесям и асфальтобетонам. |
|||||||
|
Асфальтобетонные смеси приготавливают на асфальтобетонныхИзаводах |
|||||||
|
(АБЗ) в соответствии с требованиями ГОСТ 9128–13 по техническому рег- |
|||||||
|
ламенту, утвержденному предприятием-изготовителем. |
|
|
|||||
|
Зерновой состав минеральной части смесей и асфальтобетонов должен |
|||||||
|
соответствовать требованиям ГОСТ 9128–13 для нижних слоев покрытий и |
|||||||
|
оснований (см.табл. |
3.4), |
для |
верхних слоев |
покрытий (табл. |
3.4, 3.5). |
|
68
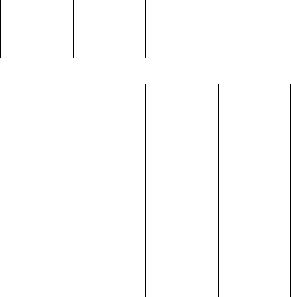
С |
|
Зерновой состав минеральной части |
|
|
|
Таблица 3.4 |
|||||||||||
|
|
|
|
|
|
|
|
||||||||||
|
|
|
|
|
|
|
|
|
|
||||||||
|
|
|
|
|
|
|
|
|
|
|
|
|
|
|
|
|
|
Вид и тип сме- |
|
|
|
|
|
|
|
Размер зерен, мм, мельче |
|
|
|
|
|
||||
сей и асфальто- |
|
|
|
|
|
|
|
|
|
|
|
|
|
|
|
|
|
40 |
20 |
|
15 |
|
10 |
|
5 |
|
2,5 |
1,25 |
|
0,63 |
0,315 |
0,16 |
|
0,071 |
|
бетонов |
|
|
|
|
|
|
|||||||||||
|
|
|
|
|
|
|
|
|
|
|
|
|
|
|
|
|
|
|
|
|
|
|
|
|
|
|
|
|
|
|
|
|
|
|
|
Плотные типов: |
|
|
|
|
|
|
Непрерывные зерновые составы |
|
|
|
|
|
|||||
|
|
|
|
|
|
|
|
|
|
|
|||||||
А |
90-100 |
66-90 |
б |
|
28-38 |
20-28 |
|
14-20 |
10-16 |
6-12 |
|
4-10 |
|||||
56-70 |
|
48-62 |
40-50 |
|
|
|
|||||||||||
Б |
90-100 |
и76-90 68-80 60-72 |
50-60 |
|
38-48 |
28-37 |
|
20-28 |
14-22 |
10-16 |
|
6-12 |
|||||
|
|
|
|
|
|
|
Прерывистые зерновые составы |
|
|
|
|
|
|||||
А |
90-100 |
66-90 |
56-70 |
|
А |
20-50 |
|
14-50 |
10-28 |
6-16 |
|
4-10 |
|||||
|
48-62 |
40-50 |
|
28-50 |
|
|
|||||||||||
Б |
90-100 |
76-90 |
68-80 |
|
60-72 |
50-60 |
|
38-60 |
28-60 |
|
20-60 |
14-34 |
10-20 |
|
6-12 |
||
Пористые |
90-100 |
75-100 |
64-100 |
52-88 |
40-60 |
|
28-60 |
16-60 |
|
10-60 |
8-37 |
5-20 |
|
2-8 |
|||
|
|
(90-100) |
|
|
|
|
|
Д |
|
|
|
|
|
|
|||
Высокопористые |
90-100 |
55-75 |
35-64 |
|
22-52 |
|
|
2-8 |
1-5 |
|
1-4 |
||||||
|
15-40 |
|
10-28 |
5-16 |
|
3-10 |
|
||||||||||
щебеночные |
|
(90-100) |
|
|
|
|
|
|
|
|
|
|
|
|
|
|
|
|
|
|
|
|
|
|
|
|
|
|
|
|
|
|
|
|
|
Высокопористые |
- |
- |
|
- |
|
- |
70-100 |
|
64-100 |
41-100 |
|
25-85 |
17-72 |
10-45 |
|
4-10 |
|
песчаные |
|
|
|
|
|
||||||||||||
|
|
|
|
|
|
|
|
|
|
|
|
|
|
|
|
|
|
|
|
|
|
|
|
|
|
|
|
|
|
|
|
|
|
||
|
|
|
|
|
|
|
|
|
|
И |
|
|
Примечания: 1. В скобках указаны требования к зерновым составам минеральной части асфальтобетонных смесей при ограничении проектной документацией крупности применяемого щебня.
2. При приемосдаточных испытаниях допускается определять зерновые составы смесей по контрольным ситам в соответствии с показателями, выделенными полужирным шрифтом.
69

|
|
|
|
|
|
|
|
|
|
|
|
|
|
|
Таблица 3.5 |
|
|
|
Зерновой состав минеральной части асфальтобетонных смесей |
|
|
|
|
||||||||||
|
|
|
|
|
|
|
|
|
|
|
|
|
|
|
|
|
Вид и тип смесей |
и |
|
Размер зерен, мм, мельче |
|
|
|
|
|
|
|||||||
|
|
|
|
|
|
|
|
|
|
|
|
|||||
и асфальтобето- |
|
|
|
|
|
|
|
|
|
|
|
|
|
|
|
|
20 |
15 |
|
10 |
5 |
|
|
2,5 |
1,25 |
|
0,63 |
|
0,315 |
0,16 |
|
0,071 |
|
|
|
|
|
|
|
|
||||||||||
Снов |
|
|
|
|
|
|
|
|
|
|
|
|
|
|
||
Горячие: |
|
|
|
|
|
|
|
|
|
|
|
|
|
|
|
|
- высокоплотные |
90-100 |
70-100 |
|
56-100 |
30-50 |
|
24-50 |
18-50 |
|
13-50 |
|
12-50 |
11-28 |
|
10-16 |
|
|
|
(90-100) |
б |
|
|
|
|
|
|
|
|
|
||||
|
|
|
(90-100) |
|
|
|
|
|
|
|
|
|
|
|
|
|
- плотные типов: |
|
|
|
|
|
Непрерывные зерновые составы |
|
|
|
|
||||||
А |
90-100 |
75-100 |
|
62-100 |
40-50 |
|
28-38 |
20-28 |
|
14-20 |
|
10-16 |
6-12 |
|
4-10 |
|
|
|
(90-100) |
|
(90-100) |
|
|
|
|
|
|
|
|
|
|
|
|
Б |
90-100 |
80-100 |
|
70-100 |
50-60 |
|
38-48 |
28-37 |
|
20-28 |
|
14-22 |
10-16 |
|
6-12 |
|
В |
90-100 |
85-100 |
|
75-100 |
60-70 |
|
48-60 |
37-50 |
|
28-40 |
|
20-30 |
13-20 |
|
8-14 |
|
Г |
- |
- |
|
100 |
70-100 |
|
56-82 |
42-65 |
|
30-50 |
|
20-36 |
15-25 |
|
8-16 |
|
Д |
- |
- |
|
100 |
70-100 |
|
60-93 |
42-85 |
|
30-75 |
|
20-55 |
15-33 |
|
10-16 |
|
|
|
|
|
|
|
Прерывистые зерновые составы |
|
|
|
|
||||||
А |
|
|
|
|
|
|
|
|
|
|
|
|
|
|||
90-100 |
75-100 |
|
62-100 |
40-50 |
|
28-50 |
20-50 |
|
14-50 |
|
10-28 |
6-16 |
|
4-10 |
||
Б |
90-100 |
80-100 |
|
70-100 |
50-60 |
|
38-60 |
28-60 |
|
20-60 |
|
14-34 |
10-20 |
|
6-12 |
|
|
|
|
|
|
А |
|
|
|
|
|
|
|
||||
Холодные |
|
|
|
|
|
|
|
|
|
|
|
|
||||
типов: |
|
|
|
|
|
|
|
|
|
|
|
|
|
|
|
|
Бх |
90-100 |
85-100 |
|
70-100 |
50-60 |
33-46 |
21-38 |
|
15-30 |
|
10-22 |
9-16 |
|
8-12 |
||
Вх |
90-100 |
85-100 |
|
75-100 |
60-70 |
48-60 |
38-50 |
|
30-40 |
|
23-32 |
17-24 |
|
12-17 |
||
Гх и Дх |
- |
- |
|
100 |
70-100 |
62-82 |
40-68 |
|
25-55 |
|
18-43 |
14-30 |
|
12-20 |
||
|
|
|
|
|
|
|
|
|
И |
|
|
Примечания: 1. В скобках указаны требования к зерновымДсоставам минеральной части асфальтобетонных смесей при ограничении проектной документацией крупности применяемого щебня.
2. При приемосдаточных испытаниях допускается определять зерновые составы смесей по контрольным ситам соответствии с показателями, выделенными полужирным шрифтом.
70

Графически зерновой состав представлен на рис.3.13
|
100 |
0,9 |
|
Кривые сбега |
|
|
|
|
|
|
|
|
|
|
|
|
|
|
% |
|
|
|
|
Подобранный |
состав |
|
|
|
|
|
|
|
|
|
|||
|
|
|
|
|
|
|
|
|
|
|
|
|
|
|||||
, |
|
|
|
|
|
асфальтобетонной смеси |
|
|
|
|
|
|
|
|||||
проходы |
|
|
|
|
|
|
|
|
|
|
|
|
||||||
|
|
|
|
|
|
|
|
|
|
|
|
|
|
|
|
|
|
|
С |
|
|
|
|
|
|
|
|
|
|
|
|
|
|
|
|||
Полные |
50 |
0,6 |
|
|
|
|
|
|
|
|
|
|
|
|
|
|
|
|
и |
|
|
|
|
|
|
|
|
|
|
|
|
|
|
||||
|
0 |
|
|
|
|
|
|
|
|
|
|
|
|
|
|
|
|
|
|
|
20 |
15 |
10 |
5 |
2,5 |
1,25 |
0,63 |
0,315 |
0,14 |
0,071 |
|||||||
|
|
бА |
|
|
|
|
|
|
||||||||||
|
|
Р |
|
Размеры сит, мм |
|
|
|
|
|
|
|
|
|
|
|
|
||
|
|
с. 3.13. Зерновой состав асфальтобетонных смесей |
|
|
|
|
Ф з ко-механ ческие показатели асфальтобетонов должны соответ-
ствовать ГОСТ 9128–13: [17].
Rсж50 : 0,9–1,6 для I марки; 0,8–1,5 для II марки; 0,8–1,2 для III марки;
Rсж20 : 2,5 для I марки; 2,2 для II марки; 2,0 для III марки;
Rсж0 : не более 9–13 для I марки; не более 10–13 для II марки; не бо-
лее 10–13 для III марки.
Чем больше прочность асфальтобетонаДпри сжатии Rсж, тем материал менее трещиностоек. Поэтому необходимо стремиться к увеличению прочности асфальтобетона при растяжении.
Водостойкость: для плотных асфальтобетонов не менее 0,85–0,95 для
I марки; 0,8–0,85 для II марки; 0,7–0,75 для III марки.
Трещиностойкость асфальтобетона характеризуется прочностью на растяжение при 0 °С в зависимости от марок не менее 3–4 МПа и не более
5,5–6,5 МПа. И
Чем больше модуль упругости Еу, тем больше величина температурных напряжений и тем менее трещиностоек асфальтобетон.
Таким образом, чем больше показатель R/E асфальтобетона, тем выше его трещиностойкость.
Показателем сдвигоустойчивости асфальтобетонных покрытий является прочность асфальтобетонных образцов при одноосном сжатии при температуре 50 ºС. В зависимости от дорожно-климатических зон эта прочность должна быть 0,8–1,6 МПа.
71
Требования к материалам
Щебень и гравий. Для приготовления асфальтобетонных смесей применяют щебень из плотных горных пород, который по зерновому составу, прочности и содержанию пыли и глины должен соответствовать требованиям ГОСТ 8267 [26] и ГОСТ 3444 [27]. Для приготовления смесей
и асфальтобетонов применяют щебень фракций от 5 до 10 мм, 10–20 мм, 15–20 мм, 20–40 мм. Содержание лещадных фракций допускается не более 15–35% в зависимости от типа смеси (А, Б, В). Прочность щебня должна быть 600–1200 МПа (бóльшие значения – для I марки, меньшие – для II и III марок асфальтобетона).
По ст ран ю в полочном барабане щебень и гравий должны соот- |
|
ветствовать марке И-1 для I марки, И-2 и И-3 – для II марки, И-3 и И-4 – |
|
С |
|
для III |
асфальто етона. Меньшее значение истираемости – для сме- |
сей с больш |
содержан ем ще ня. |
марки
Бóльшие значениябА600–1000 –для марки I, меньшие для II марки –400–800 и для III марки – 400–600. Содержание глинистых частиц в песке должно быть менее 0,5% для I и II марок и не более 1% для III марки. Для асфальтобетонных смесей пригоден песок с Мкр>2, т.е. среднезернистые или крупнозернистые пески. Применение мелкозернистых песков должно быть обосновано специально проведенными исследованиями или ранее выполненными рекомендациями.
Допускается пр менение ще ня из шлаков черной и цветной металлургии с содержан ем пыли и глины не более 3%, в том числе глины не
более 0,5%.
Пески. Пр меняют пески природные, отвечающие требованиям ГОСТ 8736 [28]. Марка по прочности песков должна быть 400–1000.
Минеральный порошок. Для Дприготовления асфальтобетонных смесей используют минеральные порошки, отвечающие требованиям ГОСТ Р 52.129–2003 [29]. Допускается применять для пористого и высокопористого асфальтобетонов отходы промышленности – молотые металлургические шлаки, золы-уноса ТЭЦ, пыль цементных заводов. При этом частиц менее 0,071 мм должно быть более 60%, пористость – 40–45%, со-
держание СаO+MgO – не более 3%, содержание водорастворимых соеди- |
||||
нений – не более 6%. Лучше для минерального порошка использовать тон- |
||||
комолотые известняки и доломиты. |
|
|||
|
Битумы. Для приготовления асфальтобетонныхИсмесей необходимо |
|||
применять битумы, удовлетворяющие ГОСТ 22245 [24] – вязкие битумы и |
||||
ГОСТ 11955 [25] – жидкие битумы, а также модифицированные, полимер- |
||||
но-битумные вяжущие и другие битумы и битумные вяжущие с улучшен- |
||||
ными |
свойствами. |
Для |
приготовления |
щебеночно-мастичных |
асфальтобетонных смесей применяются полимербитумное вяжущее ГОСТ Р 52056–2013 [30]. Рекомендуемую марку битума для приготовле-
72
ния асфальтобетонных смесей при устройстве верхних слоев покрытий автомобильных дорог и взлетно-посадочных полос аэродромов назначают в зависимости от дорожно-климатической зоны, видов и марок асфальтобетонов. Ориентировочное содержание битума в смесях представлено в табл. 3.10.
Контроль качества. При входном контроле устанавливают соот- СибАДИветствие качества исходных материалов (щебня, песка, минерального порошка и битума) в каждой поступающей на АБЗ партии действующим
стандартам.
Операц онный контроль осуществляют не реже 1 раза в 10 смен с определен ем следующ х показателей: зерновой состав щебня (гравия), песка и м нерального порошка.
одержан е пылеватых и глинистых частиц в щебне и песке не должно превышать 3%.
При контроле качества итума отбирают пробы из каждого рабочего котла и б тумоплав льных установок один раз в смену.
Проверяют температуру нагрева битума через каждые 3–4 часа в котлах б тумоплав льнях.
В процессе пр готовления асфальтобетонной смеси контролируют соблюдение установленного времени перемешивания для каждого вида смеси и температуру смеси на выходе из смесителя.
При автоматизированных асфальтосмесителях контроль температуры и времени перемешивания осуществляется автоматически.
При приемочном контроле готовой смеси в лаборатории контролируют: температуру готовой смеси, зерновой состав, содержание битума, водонасыщение, набухание, пределы прочности при сжатии при температурах 20 и 50 ºС, коэффициент водостойкости и др.
Температура асфальтобетонной смеси в зависимости от применяемого битума должна соответствовать значениям, приведенным в табл. 3.6.
|
|
|
|
|
|
|
|
Таблица 3.6 |
||
|
Температура асфальтобетонной смеси при отгрузке потребителю |
|
||||||||
|
|
|
|
|
|
|
|
|
|
|
|
|
|
Температура смеси, %, в зависимости от вязкости битума |
|
||||||
|
|
|
|
|
|
|
|
Условная вязкость |
||
Вид |
|
Глубина проникания иглы при 25 º , 0,1 мм |
по вискозиметру с |
|||||||
|
|
|
|
|
||||||
|
|
|
|
|
|
|
|
при 60 ºС, с |
||
|
|
40–60 |
|
61–90 |
91–130 |
131–200 |
201–300 |
70–130 |
|
121–200 |
Горячая |
|
От 150 |
|
От 145 |
От 140 |
От 130 |
От 120 |
- |
|
От 110 |
|
|
до 160 |
|
до 155 |
до 150 |
до 140 |
до 130 |
|
до 120 |
|
|
|
|
|
|
||||||
Холодная |
- |
|
- |
- |
- |
- |
От 80 |
|
От 100 |
|
|
|
|
до 100 |
|
до 120 |
|||||
|
|
|
|
|
|
|
|
|
смеси отверстием 5 мм
73

Показатели физико-механических свойств должны соответствовать требованиям, предъявляемым ГОСТ 9128–13 к данному виду, типу и марке асфальтобетонной смеси и асфальтобетона (табл. 3.7) [17].
Таблица 3.7
Физико-механические свойства асфальтобетонной смеси и асфальтобетона
С |
|
|
|
Марки асфальтобетонов |
|
|
|
|||||||
|
|
|
|
|
|
|
|
|
||||||
|
Показатель |
|
|
I |
|
|
II |
|
|
|
III |
|
|
|
|
|
|
|
Дорожно-климатические зоны |
|
|
|
|||||||
|
|
|
|
|
|
|
|
|
||||||
|
|
|
I |
|
II,III |
IV,V |
I |
II,III |
IV,V |
I |
II,III |
IV,V |
|
|
|
1 |
|
2 |
|
3 |
4 |
5 |
6 |
|
7 |
8 |
9 |
10 |
|
|
Предел |
при сжа- |
- |
|
- |
- |
1,1 |
1,2 |
|
1,3 |
1,0 |
1,1 |
1,2 |
|
|
прочностиВ |
|
|
|
||||||||||
|
тии при температуре 50 ºС, |
|
|
|
|
|
|
|
|
|
|
|
|
|
|
МПа, не менее, для асфаль- |
|
|
|
|
|
|
|
|
|
|
|
|
|
|
тобетонов: |
|
|
|
|
|
|
|
|
|
|
|
|
|
|
- высокоплотных |
|
1,0 |
|
1,1 |
1,2 |
- |
- |
|
- |
- |
- |
- |
|
|
- плотных т пов: |
|
|
|
|
|
|
|
|
|
|
|
|
|
|
А |
|
0,9 |
|
1,0 |
1,1 |
0,8 |
0,9 |
|
1,0 |
- |
- |
- |
|
|
Б |
|
1,0 |
|
1,2 |
1,3 |
0,9 |
1,0 |
|
1,2 |
0,8 |
0,9 |
1,1 |
|
|
Г |
|
1,1 |
|
1,3 |
1,6 |
1,0 |
1,2 |
|
1,4 |
0,9 |
1,0 |
1,1 |
|
|
Д |
|
- |
|
- |
- |
1,1 |
1,3 |
|
1,5 |
1,0 |
1,1 |
1,2 |
|
|
Предел прочности при сжа- |
|
|
|
|
|
|
|
|
|
|
|
|
|
|
тии при температуре 20 ºС |
2,5 |
|
2,5 |
2,5 |
2,2 |
2,2 |
|
2,2 |
2,0 |
2,0 |
2,0 |
|
|
|
для асфальтобетонов всех |
|
|
|
||||||||||
|
|
|
|
|
|
|
|
|
|
|
|
|
||
|
типов, МПа, не менее |
|
|
|
|
|
|
|
|
|
|
|
|
|
|
Предел прочности при сжа- |
|
|
|
|
Д |
|
|
|
|||||
|
тии при температуре 0 ºС для |
|
|
|
|
|
|
|
||||||
|
9,0 |
|
11,0 |
13,0 |
10,0 |
12,0 |
13,0 |
10,0 |
12,0 |
13,0 |
|
|||
|
асфальтобетонов всех типов, |
|
|
|||||||||||
|
МПа, не болеебА |
|
|
|
|
|
||||||||
|
Водостойкость, не менее: |
|
|
|
|
|
|
|
|
|
|
|
|
|
|
- плотных асфальтобетонов |
0,95 |
|
0,90 |
0,85 |
0,90 |
0,85 |
0,80 |
0,85 |
0,75 |
0,70 |
|
||
|
- высокоплотных асфаль- |
0,95 |
|
0,95 |
0,90 |
- |
- |
|
- |
- |
- |
- |
|
|
|
|
|
|
|
|
|||||||||
|
тобетонов |
|
|
|
|
|
|
И |
|
|||||
|
|
|
|
|
|
|
|
|
|
|
|
|
|
|
|
- плотных асфальтобетонов |
|
|
|
|
|
|
|
|
|
|
|
|
|
|
при длительном водонасы- |
0,90 |
|
0,85 |
0,75 |
0,85 |
0,75 |
0,70 |
0,75 |
0,65 |
0,60 |
|
||
|
щении |
|
|
|
|
|
|
|
|
|
|
|
|
|
|
- высокоплотных асфаль- |
|
|
|
|
|
|
|
|
|
|
|
|
|
|
тобетонов при длительном |
0,95 |
|
0,90 |
0,85 |
- |
- |
|
- |
- |
- |
- |
|
|
|
водонасыщении |
|
|
|
|
|
|
|
|
|
|
|
|
|
|
Сдвигоустойчивость по: |
|
|
|
|
|
|
|
|
|
|
|
|
|
|
- коэффициенту внутрен- |
|
|
|
|
|
|
|
|
|
|
|
|
|
|
него трения, не менее, для |
|
|
|
|
|
|
|
|
|
|
|
|
|
|
асфальтобетонов типов: |
|
|
|
|
|
|
|
|
|
|
|
|
|
|
высокоплотных |
0,88 |
|
0,89 |
0,91 |
- |
- |
|
- |
- |
- |
- |
|
|
|
А |
|
0,86 |
|
0,87 |
0,89 |
0,86 |
0,87 |
0,89 |
- |
- |
- |
|
|
|
Б |
|
0,80 |
|
0,81 |
0,83 |
0,80 |
0,81 |
0,83 |
0,79 |
0,80 |
0,81 |
|
|
|
В |
|
- |
|
- |
- |
0,74 |
0,76 |
0,78 |
0,73 |
0,75 |
0,77 |
|
|
|
Г |
|
0,78 |
|
0,80 |
0,82 |
0,78 |
0,80 |
0,82 |
0,76 |
0,78 |
0,80 |
|
74

Окончание табл. 3.7
|
|
1 |
2 |
|
3 |
4 |
5 |
6 |
7 |
8 |
9 |
10 |
|
|
Д |
- |
|
- |
- |
0,64 |
0,65 |
0,70 |
0,62 |
0,64 |
0,66 |
|
-сцеплению при сдвиге при |
|
|
|
|
|
|
|
|
|
|
|
|
температуре 50 ºС, МПа, не |
|
|
|
|
|
|
|
|
|
|
|
|
менее, для асфальтобетонов |
|
|
|
|
|
|
|
|
|
|
|
С |
|
|
|
|
|
|
|
|
|
|
||
|
типов: |
|
|
|
|
|
|
|
|
|
|
|
|
|
высокоплотных |
0,25 |
|
0,27 |
0,30 |
- |
- |
- |
- |
- |
- |
|
|
А |
0,23 |
|
0,25 |
0,26 |
0,22 |
0,24 |
0,25 |
- |
- |
- |
|
|
Б |
0,32 |
|
0,37 |
0,38 |
0,31 |
0,35 |
0,36 |
0,29 |
0,34 |
0,36 |
|
|
В |
- |
|
- |
- |
0,37 |
0,42 |
0,44 |
0,36 |
0,40 |
0,42 |
|
|
Г |
0,34 |
|
0,37 |
0,38 |
0,33 |
0,36 |
0,37 |
0,32 |
0,35 |
0,36 |
|
прочности |
- |
|
- |
- |
0,47 |
0,54 |
0,55 |
0,45 |
0,48 |
0,50 |
|
|
|
Д |
|
|||||||||
|
Трещиностьйкость по преде- |
|
|
|
|
|
|
|
|
|
|
|
|
лу |
на растяжен е |
|
|
|
|
|
|
|
|
|
|
|
при расколе при температуре |
|
|
|
|
|
|
|
|
|
|
|
0 º |
и скорости деформ ро- |
|
|
|
|
|
|
|
|
|
|
|
|
вания 50 мм/м н для асфаль- |
|
|
|
|
|
|
|
|
|
|
|
|
тобетонов всех т пов, МПа: |
|
|
|
|
|
|
|
|
|
|
|
|
- не менее |
3,0 |
|
3,5 |
4,0 |
2,5 |
3,0 |
3,5 |
2,0 |
2,5 |
3,0 |
|
|
- не более |
5,5 |
|
6,0 |
6,5 |
6,0 |
6,5 |
7,0 |
6,5 |
7,0 |
7,5 |
Примечан я: 1. Для крупнозернистых асфальтобетонов показатели сдвигоустойчивости и трещиностойкости не нормируются.
2. Показатели физико-механических свойств асфальтобетонов, применяемых в конкретных условиях эксплуатации, могут уточняться в проектной документации на строительство.
|
Показатели физико-механических свойств щебеночно-мастичных |
|||||
асфальтобетонов должны соответствовать требованиям ГОСТ 31015–2002 |
||||||
[30]. |
бА |
|||||
|
Водонасыщение высокоплотных и плотных асфальтобетонов из го- |
|||||
рячих смесей должно соответствовать указанному в табл. 3.8. |
||||||
|
|
|
|
|
Таблица 3.8 |
|
|
|
|
|
И |
||
|
Водонасыщение высокоплотных и плотных асфальтобетонов |
|||||
|
Д |
|
||||
Вид и тип асфальтобетонов |
Образцы, отформованные |
Вырубки и керны готового |
||||
|
|
для смеси |
|
покрытия, не более |
|
|
Высокоплотный |
От 1,0 (0,5) |
до 2,5 |
|
3,0 |
|
|
Плотные типов: |
|
|
|
|
|
|
|
А |
От 2,0 (1,5) |
до 5,0 |
|
5,0 |
|
|
Б, В и Г |
От 1,5 (1,0) |
до 4,0 |
|
4,5 |
|
|
Д |
От 1,0 (0,5) |
до 4,0 |
|
4,0 |
|
Примечания: 1. В скобках приведены значения водонасыщения для образцов из пере формованных вырубок и кернов.
2. Показатели водонасыщения асфальтобетонов, применяемых в конкретных до- рожно-климатических условиях, могут уточняться в проектной документации на строительство.
75
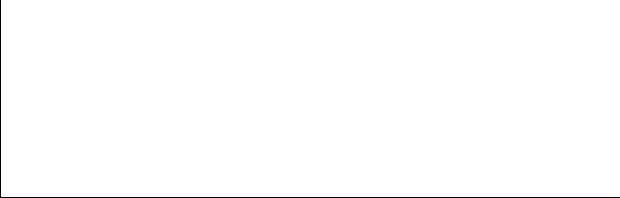
Пористость минеральной части асфальтобетонов из горячих смесей
|
должна быть, %: |
|
|
|
|
- высокоплотных . . . . . . . . . . . |
не более 16; |
|
|
|
- плотных типов: |
|
|
|
|
А и Б . . . . . . . . . . . . . . . . . . |
от 14 до 19; |
|
|
С |
не более 22; |
|
|
|
|
В, Г и Д . . . . . . . . . . . . . . . . |
|
|
|
|
- пористых . . . . . . . . . . . . . . . . . |
не более 23; |
|
|
|
- выокопористых щебеночных |
не менее 19; |
|
|
|
- выокопор стых песчаных . . . |
не более 28; |
|
|
|
Показатели ф з ко-механических свойств пористых и высокопорис- |
|||
|
тых асфальтобетонов з горячих смесей должны соответствовать значени- |
|||
|
ям, указанным в табл. 3.9. |
|
|
Таблица 3.9 |
|
|
|
|
|
|
Физ ко-механ ческ е свойства пористых высокопористых асфальтобетонов |
|||
|
|
|
|
|
|
Показатель |
|
Марки |
|
|
|
I |
II |
|
|
прочности |
|||
|
Предел при сжат при температуре |
0,7 |
0,5 |
|
|
50 ºС, МПа, не менее |
|
|
|
|
Водостойкость, не менее |
|
0,7 |
0,6 |
|
Водостойкость при дл тельном водонасыщении, |
0,6 |
0,5 |
|
|
не менее |
|
||
|
|
|
|
|
|
Водонасыщение, % по о ъему, для: |
|
|
|
|
- пористых |
Св. 4,0 до 10,0 |
Св. 4,0 до 10,0 |
|
|
- выокопористых |
Св. 10,0 до 18,0 |
Св. 10,0 до 18,0 |
сти при сжатии при температуре 50 ºС и показатели водостойкости не нормируются. 2. Для вырубок и кернов нижние пределы водонасыщения не нормируются.
бА Примечания: 1. Для крупнозернистыхДасфальтобетонов значение предела прочно-
Периодический контроль производят не реже 1 раза в 6 месяцев и при изменении исходных материалов.
Особенности подбора составов. СоставИасфальтобетонной смеси подбирается по заданию в соответствии с проектом производства работ и техническим проектом. В задании указываются тип смеси, его марка, крупность, в каком конструктивном слое и в какой КЗ он будет использоваться. Подбор смеси осуществляют в лаборатории, подбирают грансостав минеральной части, количество битума (назначается от 4 до 9%), в зависимости от вида, плотности смеси и типа асфальтобетона (табл. 3.10).
76

|
|
|
|
Таблица 3.10 |
|
|
Ориентировочное содержание битума в смесях |
||||
|
|
|
|
|
|
|
|
Вид смеси |
Содержание битума, % по массе |
||
|
1. Горячие: |
|
|
|
|
|
- высокоплотные |
|
4,0-6,0 |
|
|
|
- плотные типов: |
|
|
|
|
|
А |
|
|
4,5-6,0 |
|
|
Б |
|
|
5,0-6,5 |
|
|
В |
|
|
6,0-7,0 |
|
|
Г |
Д |
|
6,0-9,0 |
|
|
- пор стые |
|
3,5-5,5 |
|
|
|
и |
|
2,5-4,5 |
|
|
|
- высокопор стые щебеночные |
|
|
||
|
- высокопор стые песчаные |
|
4,0-6,0 |
|
|
С |
|
|
|
||
|
2. Холодные т пов: |
|
3,5-5,5 |
|
|
|
Бх |
|
|
|
|
|
Вх |
|
|
4,0-6,0 |
|
|
б |
|
4,5-6,5 |
|
|
|
Гх |
Дх |
|
|
|
|
- высокопор стые ще еночные |
|
2,5-4,0 |
|
Свойства смесей ла ораторного и заводского приготовления зачас-
тую разл чны, поэтому при приготовлении асфальтобетонных смесей учи- |
|
АБЗ |
|
тывают отличия между ними с целью получения смесей высокого качест- |
|
ва. По зерновому составу имеются отклонения по |
от средних значе- |
ний по проценту частиц, проходящих через каждое сито. В лабораторных условиях все составляющие минеральной части рассеиваются по ситам, а затем перемешиваются, поэтому в лаборатории смесь имеет более точный зерновой состав, чем заводской. Д
В лаборатории при подборе составов используют сухой заполнитель. На АБЗ в сушильном барабане влажность щебня и песка можно снизить примерно до 0,1% по массе, но иногда она достигает 0,5% и более. В лаборатории материал разогревают более равномерно, на АБЗ в зависимости от применяемых обеспыливающих установок все пылевидныеИчастицы улавливаются или частично улавливаются, поэтому и по содержанию минерального порошка будет разница между лабораторным составом и заводским.
Таким образом, тип и оборудование, используемые на АБЗ, значительно влияют на качество приготовляемой асфальтобетонной смеси.
В процессе приготовления и применения асфальтобетонных смесей происходит старение битума, интенсивность которого зависит от температуры нагрева каменных материалов и битума, продолжительности перемешивания, толщины битумной пленки на поверхности каменных материалов и температурного режима асфальтобетонной смеси до конца её уплотнения. В лабораторных условиях смесь перемешивается за несколько минут, в заводских – 30–180 с, в течение 2–3 ч осуществляют изготовление
77
образцов из смеси, которые после этого остывают в комнатных условиях; на АБЗ асфальтобетонная смесь может в течение нескольких часов находиться в термосах бункеров накопителей, после чего транспортируется на дорогу, где ещё в течение 2–3 часов укладывается и уплотняется.
Таким образом, время нахождения смеси в лабораторных условиях и в заводских условиях значительно различается, что существенно отражается на старении битума и искажает данные, полученные в лаборатории и в покрытии. Время на уплотнение на дороге и в лаборатории несравнимо (несколько часов 3 м нуты). За это время происходит остывание смеси,
тогда как в лаборатор |
при формовании образцов температура постоянна. |
|
Так |
м образом, |
состав смеси, подобранный в лаборатории, следует |
рассматр вать в качестве необходимого для первоочередного определения |
||
С |
|
|
содержан |
я б тума. Этот состав следует корректировать с учетом реаль- |
ныхзаданияуслов й пр готовления, хранения, транспортирования, укладки и уп-
3.ПредставитьбАтехнологическую схему приготовления асфальтобетонных смесей
васфальтосмесительной установке циклического действия башенного типа.
4.Представить технологическую схему приготовления асфальтобетонных смесей
васфальтосмесительной установке непрерывного действия партерного типа.
5.Каковы преимущества и недостатки смесительных установок башенного и партерного типов?
6.Какова точность дозирования всехДсоставляющих асфальтобетонной смеси по
весу?
7.Какое максимальное отклонение по температуре нагрева щебня и песка в сушильном барабане?
8.Какова должна быть температура асфальтобетонной смеси на выходе из смесителя для горячих асфальтобетонных смесей?
9.Какое должно быть время перемешивания асфальтобетонныхИсмесей и от чего оно зависит?
10.От чего зависит время транспортировки горячих асфальтобетонных смесей от АБЗ до дороги?
11.Какова температура приготовления холодных асфальтобетонных смесей?
12.Для каких целей используется пар на АБЗ?
13.Для каких целей используется сжатый воздух на АБЗ?
14.Какова должна быть температура нагрева битума для горячих асфальтобетонных смесей?
15.Какие основные принципы заложены при проектировании генеральных планов
АБЗ?
16.Какие основные цеха на АБЗ?
17.На какие зоны делят площадь производственного предприятия?
18.Какие виды транспорта на асфальтобетонных заводах вы знаете?
78