
- •ВВЕДЕНИЕ
- •1. РОЛЬ, НАЗНАЧЕНИЕ И ОСОБЕННОСТИ ПРОИЗВОДСТВЕННЫХ ПРЕДПРИЯТИЙ ДОРОЖНОГО ХОЗЯЙСТВА
- •1.1. Общие сведения о производственных предприятиях дорожного хозяйства
- •1.3. Организация контроля качества продукции производственных предприятий дорожного хозяйства
- •2. КАРЬЕРЫ НЕРУДНЫХ СТРОИТЕЛЬНЫХ МАТЕРИАЛОВ
- •2.1. Классификация карьеров
- •2.2. Изыскания месторождений полезных ископаемых
- •2.3. Разработка горных пород
- •2.4. Выемка и погрузка горной породы
- •3.1. Классификация асфальтобетонных заводов
- •3.2. Технологические процессы на АБЗ
- •3.6. Транспорт производственных предприятий
- •4. ЦЕМЕНТОБЕТОННЫЕ ЗАВОДЫ
- •4.1. Назначение и классификация цементобетонных заводов
- •4.2. Приготовление цементобетонной смеси
- •4.4. Проектирование генеральных планов ЦБЗ
- •5. СКЛАДСКОЕ ХОЗЯЙСТВО ПРОИЗВОДСТВЕННЫХ ПРЕДПРИЯТИЙ
- •5.1. Организация материально-технического снабжения производственных предприятий дорожно-строительными материалами
- •5.3. Назначение складов и их классификация
- •5.4. Организация складских работ и технико-экономические показатели работы склада
- •5.6. Основные требования к складской переработке каменных материалов
- •5.7. Транспортирование каменных материалов и погрузочно-разгрузочные работы на складах
- •5.10. Транспортирование порошкообразных материалов и погрузочно-разгрузочные работы на складах
- •5.12. Основные требования к складской переработке органических вяжущих
- •5.14. Технологические схемы и компоновка складов органических вяжущих
- •5.15. Примеры технологических расчетов
- •6.1. Классификация заводов и полигонов
- •6.2. Технология изготовления изделий и конструкций
- •6.3. Способы производства железобетонных изделий
- •7. БИТУМНЫЕ И ЭМУЛЬСИОННЫЕ БАЗЫ
- •7.1. Назначение и размещение битумных баз
- •7.2. Технологические процессы подготовки органических вяжущих
- •7.4. Основные технологические операции при получении эмульсии
- •7.6. Охрана труда при приготовлении битумных эмульсий
- •8. ТРЕБОВАНИЯ БЕЗОПАСНОСТИ НА ПРОИЗВОДСТВЕННЫХ БАЗАХ И ЗАВОДАХ
- •8.1. Общие требования
- •8.2. Охрана труда
- •8.3. Требования безопасности на битумных и эмульсионных базах
- •8.5. Техника безопасности при эксплуатации ЦБЗ
- •8.6. Охрана труда на полигонах и заводах
- •Библиографический список
- •Приложение 1
- •Приложение 2
- •Приложение 3
- •Приложение 4
- •Приложение 5
- •Приложение 6
- •Приложение 7
- •Приложение 8
- •Приложение 9
- •Приложение 10
- •Приложение 11
- •Приложение 13

С |
|
|
Рис |
||
. 6.3. Технолог |
ческая схема изготовления труб методом центрифугирования: |
|
1 – накоп тельный |
ункер |
етонной смеси; 2 – ленточный питатель; 3 – центрифуга; |
обра |
||
4 – траверса; 5 – стенд; |
6 – консольные съемники; 7 – форма на посту тепловой |
|
обработки; 8 – пост раз орки, чистки, смазки; 9 – установка для испытания труб; |
||
10 – станок для зготовлен я фиксаторов арматуры; 11 – стенд для сборки двойных |
||
|
|
арматурных каркасов |
|
А |
|
Давление может |
ыть нормальным (пропаривание) и повышенным |
|
(автоклавная |
отка). При тепловой обработке используют автоматизи- |
|
рованное регулирование температуры по времени. |
||
|
|
Д |
6.3. Способы производства железобетонных изделий
На заводах железобетонных изделий применяют следующие способы: поточно-агрегатный, поточно-конвейерный и стендовый. Первые два обычно применяют на заводах, стендовый – на полигонах.
Поточно-агрегатный способ. При поточно-агрегатном способе производства форму и формуемое изделие передаютИпо потоку от одного технологического поста к другому с помощью кранового оборудования (рис. 6.4). При этом способе формы от одного поста к другому передаются с помощью кранового оборудования с определенным интервалом, зависящим от длительности соответствующей операции. Последовательность изготовления изделий следующая: форма очищается, смазывается, передается на пост формовки, устанавливают арматурные каркасы, заполняют форму смесью, подают на вибростолы, виброуплотняют, затем подают в пропарочные камеры и на пост распалубки и далее на склад готовой продукции.
145

СибАДИРис. 6.4. Технолог ческая схема изготовления железобетонных изделий поточноагрегатным спосо ом: а – зона хранения заполнителей бетонной смеси; б – зона приготовления бетонной смеси; в – зона изготовления арматурных каркасов; г – зона
формирования и о ра отки ЖБИ; д – зона хранения и выдачи готовых изделий; 1 – пост разгрузки заполнителей; 2 – приемные бункеры; 3 – накопительные бункеры;
4 – пост разгрузки; 5 – транспортерная галерея; 6 – пневмоподача цемента; 7 – бетоносмесительный цех; 8 – оборудование для производства арматурных каркасов и элементов; 9 – агрегат для термического напряжения арматуры; 10 – пост армирования; 11 – самоходный бетоноукладчик; 12– агрегат для формования изделий; 13 – зона выдержки изделий; 14 – промежуточный склад; 15 – транспортирование ЖБИ;
16 – подъем и транспортирование изделий; 17 – самоходная тележка; 18 – склад готовых ЖБИ
Этот способ позволяет легко перестраиваться на выпуск новых видов продукции, допускает высокий уровень механизации, не требует больших
затрат на организацию производства.
Конвейерный способ. При конвейерном способе технологический процесс расчленен на элементарные процессы, которые одновременно выполняют на отдельных рабочих местах. Форму изделие непрерывно перемещают от одного рабочего места к другому, каждое из которых обслуживает закрепленное звено (рис. 6.5).
Организуется на заводах большой мощности при массовом выпуске однотипных изделий, к примеру, дорожных плит. При этом способе формуемые изделия и формы перемещаются от поста к посту в строгой последовательности и с определенной заданной скоростью передвижения [32].
146

укладки |
|
Рис. 6.5. Конвейерная технология изготовления железобетонных изделий: I – зоны |
|
Схранен я матер алов; II – зона приготовления цементобетонной смеси; III – зона |
|
изготовлен я арматурных каркасов; IV – зона изготовления изделий; 1 – пост |
|
разгрузки каменных материалов; 2 – приемные бункеры; 3 – аккумулирующие |
|
бА |
|
бункеры; 4 – транспортерная галерея; 5 – расходные бункеры; 6 – смесительное |
|
отделен е; 7 – с лосный склад цемента; 8 – вагон-цементовоз; 9 – пропарочные |
|
камеры; 10 – пост |
термоизоляционного слоя; 11 – пост доводки изделий; |
12 – пост формован я |
здел й; 13 – пост укладки арматурных каркасов; 14 – смазка |
форм; 15 – оч стка форм; 16 – передаточная тележка; 17 – пост распалубки; 18 – пост контроля
Отформованное изделие подается в камеры пропаривания тоннельного типа, откуда изделие подается на склад. Технологическая последовательность следующая: установка ортовой оснастки, очистка и смазка поддонов и бортовой оснастки, навивка проволочной или установка стержневой аппаратуры и закладных деталей, укладка в формы вагонетки бетонной смеси, уплотнение бетонной смеси и отделка поверхности, контрольный осмотр, подача в тоннельные пропарочные камеры, тепловлажностная обработка, распалубливание изделий, передача изделий на склад готовой продукции, а формы вагонеток на конвейер.
Стендовый способ. Технологическая схема изготовления изделий |
|
Д |
|
стендовым способом представлена на рис. 6.6. |
И |
Стендовый способ применяют на полигонах. Производственный процесс изготовления железобетонных изделий выполняется в следующей последовательности: подготовка форм, укладка арматуры, укладка и уплотнение бетонной смеси, тепловлажностная обработка, распалубливание, передача изделий на склад готовой продукции. Обычно формовочная площадка стенда представляет собой бетонную или железобетонную плиту h=12–20 см. По размерам стенды подразделяются на короткие и длинные (короткие – до 30 м, длинные – 70–120 м и более). Формы изготавливают из металла, бетона и железобетона. Укладка смеси в формы производится ленточным бетонораздатчиком. Тепловлажностная обработка производит-
147

ся на месте путем подогрева различными способами. Применяют для ускорения твердения бетона быстротвердеющие цементы.
С |
|
|
|
и |
а |
б |
|
|
|
||
д |
|
г |
в |
|
|
|
|
ных элементовработки; г – зона формования о изделий; д – зона хранения и выдачи |
|||
|
А |
|
Рис. 6.6. Технологическая схема изготовления конструкций на стендах: а – зона хранения и обработки сырья; – зона приготовления бетона; в – зона изготовления арматур-
конструкций; 1 – пост разгрузки заполнителей; 2, 8 – приемные бункеры; 3 – склады каменных материалов; 4 – транспортерная галерея; 5 – расходные бункеры; 6 – пост приготовления бетона; 7 – пост разгрузки цемента; 9 – склад цемента; 10 – стенд; 11 – склад готовойДпродукции
По поточно-агрегатной схеме изготавливают плиты для дорожных покрытий, трубы, кольца, тумбы ограждений, сигнальные или километровые столбы, элементы укрепления откосов и обочин и т.д. Конвейерный способ применяют для массового производстваИизделий и конструкций, чаще для изготовления преднапряженных плит.
Преимущества конвейерной технологии – высокая механизация и автоматизация, высокая производительность.
Недостатки – трудность перехода на другие виды изделий. Мощность полигонов 5–15 тыс. м3 в год. Полигоны могут быть обо-
рудованы технологическими схемами: с башенным, портальным, автомобильным, козловым, мостовым кранами. Достоинствами стендового способа являются простота оборудования и его универсальность, недостатком – низкая производительность, т.е. низкий съем продукции с единицы площади.
Рассмотрим некоторые технологические операции более подробно.
148
Транспортирование бетонной смеси. Производят ленточными транспортерами, самоходными бетонораздатчиками, автосамосвалами, пневмотранспортом и вибротранспортерами.
Изготовление арматурных каркасов на заводах ЖБИ производят в специальных арматурных цехах.
Сстоит в укладке бетонной смеси в очищенные и покрытые смазкой формы с арматурным каркасом, распределении смеси, ее уплотнении и отделке лицевой поверхности зделия.
мазывают формы, чтобы не происходило прилипания изделия к
форме, специальными эмульсиями (эмульсолом).
Заполнение форм цементобетонной смесью производят только после
проверки установки закрепления арматуры и закладных |
деталей. |
Формован е железобетонных изделий. Процесс |
формования со- |
Формы разделяют на две основные группы: изделия с ненапрягаемой
ный способбетоннойуплотнения – это ви ропрокат на специальных вибропрокатных станах. Для изготовления изделий небольших размеров (тротуарных
арматурой предвар тельно-напряженные железобетонные изделия.
Бетонную смесь укладывают в формы специальными бетоноукла-
маш нами (при малых о ъемах вручную). |
|
дочными |
|
Уплотнен |
смеси в основном производят вибрационным способом |
глубинными, поверхностными ви раторами. Для более эффективного уп- |
|
лотнения |
смеси применяют вибропригруз. Наиболее эффектив- |
Различают следующиеАосновные способы виброобработки изделий: а) поверхностный – при котором колебательные импульсы на смесь передаются через поверхность виброформы – через стенки и днище опа-
плит) применяют ви роштампование.
лубки; б) глубинный – колебательные импульсы передаются через глубин-
ные вибраторы, погружаемые в смесь;
вибропрессование, вибропрокат и виброштампованиеИ.
в) объемный – колебательные импульсы передаются всему объему |
|
смеси. |
Д |
Виброформование с дополнительным механическим воздействием – |
Вибропрессование применяется для особо жестких смесей. Давление прессования находится в пределах 0,05–0,15 кгс/см2 за счет дополнительного пригруза. Вибропрессование может производиться после вибрирования с последующим прессованием в форме.
Вибропрокат осуществляется движущимися виброкатками или вибровалками. Существует несколько разновидностей вибропроката: одноступенчатый (на вибропрокатных станках Н.Я. Козлова) и многоступенчатый, который осуществляется на поточных линиях в три стадии:
1) укладка смеси в форму и предварительное формование изделий;
149
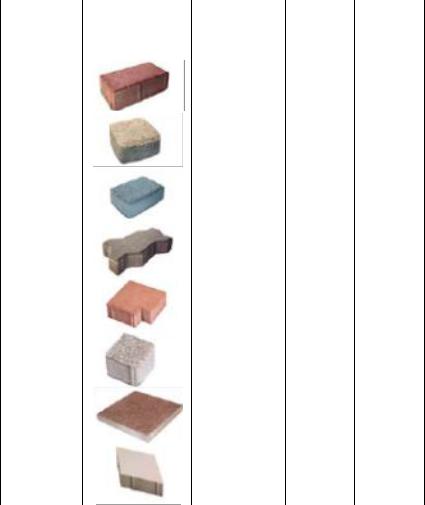
2) силовой вибропрокат при помощи семи последовательно расположенных виброваликов;
3) калибровка изделий, т.е. придание изделию необходимой толщины, выглаживание поверхности.
Частота колебания валиков – 3000 кол./мин, амплитуда первого– 0,8 мм, последнего – 0,25 мм, последний выглаживающий.
иловой вибропрокат обеспечивает повышенную плотность изделий (Ку до 0,99), обеспечивает повышенную прочность и долговечность.
В броштампован е осуществляется на специальных стендах рабочим органом, которым является виброштамп.
Номенклатура выпускаемых изделий (тротуарных плит), изготовлен-
|
ных с помощью в броштампования, представлена в табл. 6.1. |
|
|
|
|
||||||||
С |
Номенклатура выпускаемых изделий |
|
Таблица 6.1 |
||||||||||
|
|
|
|
|
|||||||||
|
|
|
|
|
|
|
|
|
|||||
|
|
|
|
|
|
|
|
|
|
|
|
|
|
|
|
|
|
|
|
|
|
|
Кол-во |
|
Кол-во |
||
|
|
е |
Арт кул |
Внешний вид |
Размер, мм |
|
Вес, кг |
|
шт. в |
|
|
шт. на |
|
|
Наименован |
|
|
|
|
1 м2 |
|
поддоне |
|
||||
|
Брусчатка |
|
1П.6 |
|
197х97х60 |
|
2,9 |
|
50 |
|
|
540 |
|
|
|
1П.8 |
|
197х97х80 |
|
3,8 |
|
50 |
|
|
432 |
|
|
|
|
|
|
|
|
|
|
|
|||||
|
|
|
|
|
|
|
|
|
|
|
|
|
|
|
Классика-1 |
|
1К.6 |
|
115х115х60 |
|
1,7 |
|
75 |
|
|
640 |
|
|
|
1К.6 |
|
115х115х80 |
|
2,3 |
|
75 |
|
|
640 |
|
|
|
|
|
|
|
|
|
|
|
|||||
|
|
|
|
|
|
|
|
|
|
|
|
|
|
|
Классика-2 |
|
1П.6 |
|
172х115х60 |
|
2,7 |
|
50 |
|
|
448 |
|
|
|
бА |
|
|
|
|
|
|
|
||||
|
Волна UNI |
|
1Ф.6 |
|
240х130х60 |
|
3,6 |
|
38 |
|
|
400 |
|
|
|
|
|
|
|
|
|
|
|
|
|
|
|
|
Execk |
|
3Ф.6 |
|
199х197х80 |
|
7 |
|
25 |
|
|
240 |
|
|
|
|
|
Д |
|
|
|
||||||
|
Квадрат |
|
2К.8 |
|
97х97х80 |
1,8 |
|
106 |
|
|
864 |
|
|
|
|
|
|
|
|
|
|
|
|
|
|
|
|
|
Большой |
|
3К.5 |
|
397х397х60 |
19 |
|
12 |
|
|
72 |
|
|
|
квадрат |
|
|
|
|
|
|
||||||
|
|
|
|
|
И |
|
|||||||
|
|
|
|
|
|
|
|||||||
|
Ромб |
|
2Ф.8 |
|
295х170х80 |
6,2 |
|
29 |
|
|
200 |
|
|
|
|
|
|
|
|
|
|
|
|
|
|
|
|
Виброштамп погружается в смесь, придает заданные размеры изделию, после чего извлекается и изделие подвергают термообработке.
150
Тепловлажностная обработка изделий. При естественном тверде-
нии в нормальных условиях изделия набирают марочную прочность в 28-суточном возрасте. Для ускорения процесса твердения бетона, уменьшения времени оборачиваемости форм, увеличения производительности заводов прибегают к различным приемам сокращения срока твердения изделий.
Это достигается применением тепловлажностной обработки изделий, применением БТУ, повышением активности цемента и различных ускорителей тверден я. На более эффективным из перечисленных способов яв-
ляется тепловлажностная обработка железобетонных изделий.
лие
Технолог ческ й процесс тепловлажностной обработки изделий за-
ключается в воздейств |
на него горячей и влажной среды |
парами при |
С |
|
|
температуре 80–100 ºС. Процесс твердения ускоряется в 10–20 раз за счет |
||
ускорен я процессов г дролиза и гидратации цемента. |
|
|
Тепловлажностная |
о ра отка обеспечивает набор |
прочности |
бетона > 70%бАот R28. Затем в процессе дальнейшего выдерживания изденаб рает марочную прочность.
Как е отр цательные моменты происходят при тепловой обработке? При форс рованном воздействии температуры создаются большие температурные градиенты по толщине изделия. В результате их действия наблюдается усиленная миграция влаги вначале во внутренние слои (т.к. t направлен к наружным слоям), затем перераспределение по всему объему (при изотермическом прогреве изделия) и миграция влаги к на-
Врезультате усиленной миграцииДвлаги материал может иметь повышенную пористость. В таком случае он будетИобладать пониженными МРЗ, воздействием, а значит, прочностью и долговечностью.
Всвязи с этим бетонное изделие должно выдерживать некоторое время до пропаривания, затем плавно повышать температуру, осуществлять изотермический прогрев и плавное снижение температуры.
Автоматизация процесса тепловой обработки обеспечивает заданные точность и стабильность регулирования температуры по установленному режиму, непрерывный контроль технологического процесса с соответствующей сигнализацией.
Таким образом, продолжительность полного цикла тепло-
влажностной обработки изделия при автоматизированном контроле будет складываться:ружным слоям.
τ = τ1 + τ2 + τ3 + τ4 + τ5, |
(6.1) |
151
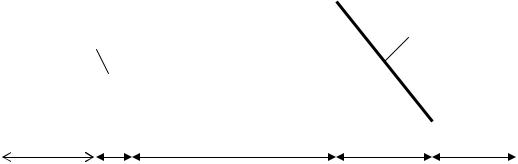
где τ1 – период предварительной выдержки сформованных изделий до тепловлажностной обработки, τ1 = 1,5–3,5 ч; τ2 – период нагрева изделий. Это время определяется допустимыми (критическими) скоростями нагрева во избежание температурных деформаций смеси. Период τ2 зависит от пластичности смеси, массивности изделий. Скорость подъема температуры не должна превышать 35–40 град/ч для жестких смесей и 20–25 град/ч для пластичных смесей; τ3 – период изотермического нагрева зависит от жесткости смеси и величины температуры изотермического прогрева, размеров и формы здел й, τ3 = 6–12 ч; τ4 – период охлаждения изделия. Период τ4 должен быть так м, чтобы резкое снижение температуры не повлекло об-
разован я температурных напряжений. Скорость охлаждения смесей: же- |
|||||||||||
стких – 50–60 град/ч, пластичных – 30–35 град/ч; τ5 – период выдержива- |
|||||||||||
С |
|
|
|
|
|
|
|||||
издел й после пропаривания и охлаждения до tв. |
|
|
|
||||||||
Допуст мая скорость остывания изделия 8–10 град/ч. |
|||||||||||
|
|
|
|
|
|
Изотермический |
|
|
|
|
|
ния |
|
|
|
|
|
||||||
|
|
|
|
|
|
|
прогрев |
|
Снижение |
||
|
Подъем |
|
|
|
|
|
|||||
|
|
|
|
|
|
температуры |
|||||
|
температуры |
|
|
|
|
|
|||||
|
|
|
|
|
|
|
|
|
|||
Предварительная |
|
|
|
|
|
|
Остывание |
||||
|
выдержка |
|
2–3 |
|
ч |
|
6–12 ч |
2–3 ч |
|
|
|
|
|
|
|
|
|
|
|
||||
|
1,5–3,5 ч |
|
|
|
|
|
|
|
|
|
|
|
|
|
|
|
|
|
|
|
|||
|
бА |
|
|
|
|||||||
Рис. 6.7. Продолжительность полного цикла тепловлажностной обработки |
Рекомендуемые режимы пропариванияДбетонных и железобетонных изделий приведены в прил. 12. И
Способы тепловлажностной обработки классифицируют по следующим признакам:
По источнику тепла – пропаривание:
а) при повышенной температуре более 100 ºС; б) при пониженной температуре менее 100 ºС.
Электронагрев, прогрев различными жидкостями (водой, маслом), методом горячего формования.
По способу передачи тепла – непосредственное соприкосновение изделия с теплоносителем, нагрев через поверхность (контактный), излучением, токами высокой частоты.
По давлению среды – при нормальном давлении (автоклавы).
По режиму работы – периодический, непериодический.
152
Наиболее распространенный способ – пропаривание при нормальном давлении при температуре 80–100 ºС.
Пропаривание осуществляют в камерах ямочного, ячеистого или тоннельного типа – однорядные и многорядные.
Автоклавный нагрев заключается в пропаривании изделий из желе-
С3 3
зобетона при повышенных температурах (175–193 ºС), насыщенных паром, под давлением 9–13 атм.
Автоклавы представляют собой герметически закрывающиеся камеры длиной 20–30 м, внутри которых изделия перемещаются на вагонетках
по рельсам. |
|
|
Реж м пропар ван я в автоклаве: |
|
|
τ1 – 2–4 ч; |
τ2 – 3–4 ч; τ3 – 4–5 ч; τ4 – 2–3 ч; τ5 – 1–2 ч. Итого 12–18 ч. |
|
Расход пара на 1м етона составляет 300–330 кг/м . |
||
Электронагрев заключается в пропускании через изделие переменно- |
||
го тока преобразован его в тепловую энергию. |
||
и |
|
|
6.4. Контроль качества, |
|
|
пр емка |
хранен е с орных конструкций |
|
Качество изготовления |
изделий контролируется на |
железобетонных всех этапах производстваА. Вопросами качества занимаются лаборатории и
ОТК. При приемке поступающих материалов проверяют наличие паспортов на сталь, песок, цемент, ще ень.
щей партии, отбирают пробу 20 кг и проводят испытания (сроки схватывания, НГ, активность). Если арматура поступает в мотках, отбирают пробу по два образца от 10% мотков. Контролируют дозировку материалов при приготовлении смесей. При весовой дозировке отклонения не должны пре-
вышать +2%. Контролируют время перемешиванияИсмесей с помощью установленных реле времени. Проверяют качество готовой цементобетонной
В лаборатории проводят контрольныеДиспытания каждой поступаю-
смеси (Rсж, Rиз, удобоукладываемость). Проверяют качество установленной арматуры, правильность сборки форм, закладных деталей, толщину защитного слоя и т.д. Контролируют степень уплотнения электрическим, механическим или радиометрическим методами. В процессе пропаривания контролируют температуру и режимы термообработки с помощью автоматических программных регуляторов.
Каждое изделие, отправляемое потребителю, имеет индивидуальный паспорт, в котором указываются не только основные технические характеристики, но и правила складирования, транспортировки, строповки и т.д.
153