
- •ВВЕДЕНИЕ
- •1. РОЛЬ, НАЗНАЧЕНИЕ И ОСОБЕННОСТИ ПРОИЗВОДСТВЕННЫХ ПРЕДПРИЯТИЙ ДОРОЖНОГО ХОЗЯЙСТВА
- •1.1. Общие сведения о производственных предприятиях дорожного хозяйства
- •1.3. Организация контроля качества продукции производственных предприятий дорожного хозяйства
- •2. КАРЬЕРЫ НЕРУДНЫХ СТРОИТЕЛЬНЫХ МАТЕРИАЛОВ
- •2.1. Классификация карьеров
- •2.2. Изыскания месторождений полезных ископаемых
- •2.3. Разработка горных пород
- •2.4. Выемка и погрузка горной породы
- •3.1. Классификация асфальтобетонных заводов
- •3.2. Технологические процессы на АБЗ
- •3.6. Транспорт производственных предприятий
- •4. ЦЕМЕНТОБЕТОННЫЕ ЗАВОДЫ
- •4.1. Назначение и классификация цементобетонных заводов
- •4.2. Приготовление цементобетонной смеси
- •4.4. Проектирование генеральных планов ЦБЗ
- •5. СКЛАДСКОЕ ХОЗЯЙСТВО ПРОИЗВОДСТВЕННЫХ ПРЕДПРИЯТИЙ
- •5.1. Организация материально-технического снабжения производственных предприятий дорожно-строительными материалами
- •5.3. Назначение складов и их классификация
- •5.4. Организация складских работ и технико-экономические показатели работы склада
- •5.6. Основные требования к складской переработке каменных материалов
- •5.7. Транспортирование каменных материалов и погрузочно-разгрузочные работы на складах
- •5.10. Транспортирование порошкообразных материалов и погрузочно-разгрузочные работы на складах
- •5.12. Основные требования к складской переработке органических вяжущих
- •5.14. Технологические схемы и компоновка складов органических вяжущих
- •5.15. Примеры технологических расчетов
- •6.1. Классификация заводов и полигонов
- •6.2. Технология изготовления изделий и конструкций
- •6.3. Способы производства железобетонных изделий
- •7. БИТУМНЫЕ И ЭМУЛЬСИОННЫЕ БАЗЫ
- •7.1. Назначение и размещение битумных баз
- •7.2. Технологические процессы подготовки органических вяжущих
- •7.4. Основные технологические операции при получении эмульсии
- •7.6. Охрана труда при приготовлении битумных эмульсий
- •8. ТРЕБОВАНИЯ БЕЗОПАСНОСТИ НА ПРОИЗВОДСТВЕННЫХ БАЗАХ И ЗАВОДАХ
- •8.1. Общие требования
- •8.2. Охрана труда
- •8.3. Требования безопасности на битумных и эмульсионных базах
- •8.5. Техника безопасности при эксплуатации ЦБЗ
- •8.6. Охрана труда на полигонах и заводах
- •Библиографический список
- •Приложение 1
- •Приложение 2
- •Приложение 3
- •Приложение 4
- •Приложение 5
- •Приложение 6
- •Приложение 7
- •Приложение 8
- •Приложение 9
- •Приложение 10
- •Приложение 11
- •Приложение 13

Место размещения АБЗ выбирают с учетом его назначения и минимального времени транспортирования горячих смесей. При температуре воздуха +10 ºС время транспортирования горячих смесей не должно быть более 1,5 ч.
С |
|
и |
|
б |
|
Критерием оптимальногоАсфальтобетонныйразмещения БЗ при строительстве авто- |
|
Рис. 3.5. |
завод О О «Кредмаш» |
мобильных дорог является наличиеДподъездных дорог и минимум затрат на доставку исходных материалов на завод и готовой асфальтобетонной смеси на дорогу с учетом расходов на строительство и перебазирование АБЗ.
Кроме этого, необходимо учитывать наличиеИжелезнодорожных станций, наличие в районе строительства карьеров щебня и песка, источников получения вяжущих и минерального порошка, возможность подключения к источникам электроэнергии от высоковольтных линий, газа, а также вблизости городов и поселков.
3.2. Технологические процессы на АБЗ
Технологический процесс работы АБЗ состоит из следующих операций: выгрузка из транспортных средств и хранение материала; транспортировка материала; сушка, дозирование и перемешивание компонентов смеси; выдача готовой продукции; хранение готовых смесей на временных складах.
43
Типичный АБЗ должен иметь следующие цехи: складской, транспортный, битумный, смесительный и энергетический. На территории завода могут размещаться здания: контора, лаборатория, механические мастерские, склад ГСМ, склад запасных частей, столовая, медпункт, агитпункт, душевые, туалетные, гардеробные.
Стехнолог ю , как прав ло, повышают себестоимость продукции. Лучшим вариантом сч тается, когда материалы, необходимые для приготовления смеси, доставляют на завод в готовом виде.
Иногда на АБЗ устраивают цехи для дополнительного домола или приготовления минерального порошка, для дробления щебня, сортировки
и обогащения гравия, приготовления поверхностно-активных добавок, цветного асфальтобетона, битумной эмульсии и др. Наличие таких цехов во всех случаях д ктуется местными условиями, но все они осложняют
Эконом чески оправданным о ычно бывает расположение на терри-
рентабельность бетона должны отвечатьАтре ованиям ГОСТ 9128–13 [17].
тории АБЗ цеха по приготовлению асфальтобетонных плит (плит
СибАДИ). Свойства эт х плит регламентируются ТУ 65.233–78 [16]. На-
этого цеха позволяет значительно повысить фондоотдачу, а также |
|
личие |
|
повысить |
предприятия. |
Свойства пр |
готавливаемых асфальтобетонных смесей и асфальто- |
Для улучшения качества асфальтобетонных смесей дорожники на собственных битумных азах готовят полимербитумные вяжущие путем введения в битум поверхностно-активных веществ (ПАВ) и активаторов. Приготовленные на АБЗ асфальтобетонные смеси с использованием ПАВ значительно повышают качество асфальтобетонныхДпокрытий.
Свойства и качество вводимых в асфальтобетонную смесь ПАВ должны отвечать требованиям ГОСТ 9128–13 и другим действующим нормативным документам.
Асфальтобетонную смесь на АБЗ приготавливают в автоматизированных установках циклического или непрерывногоИдействия с гравитационным или принудительным смешением материалов.
Материалы (щебень и песок) поступают со складов в бункеры агрегата питания. Предварительно дозируются. Количество бункеров определяется количеством сит сортировочного агрегата. Бункеры оснащены дозаторами непрерывного действия.
При возможности выбора в первую очередь применяют асфальтосмесительные установки циклического действия, затем непрерывного с принудительным перемешиванием и в последнюю очередь асфальтосмесительные установки непрерывного действия с гравитационным перемешиванием.
Достоинства башенной технологии с принудительным перемешива-
нием: простота, малая погрешность дозирования, возможность регулиро-
44
вания качества смеси, изменение длительности перемешивания, возможности введения ПАВ в процессе перемешивания под давлением 0,2–0,25 МПа через форсунки, возможность быстро перейти от выпуска одного состава смеси к другому.
Основные недостатки – большая металлоемкость и энергоемкость, невысокая надежность из-за большого числа агрегатов, малый срок службы деталей лопастного смесителя.
Далее материал поступает в сушильный барабан. Сушильный бара-
бан устанавл вается |
под углом от 2 до 8º и вращается на опорных колон- |
|
ках. Внутри барабана размещено несколько видов лопастей. Они при вра- |
||
щении барабана подн мают материал (щебень и песок) и сбрасывают его в |
||
поток горяч |
х газов. Материал в процессе сушки перемещается от верхне- |
|
С |
|
|
го загрузочного торца к нижнему (подгрузочному торцу) за счет наклона, |
||
газы дв жутся навстречу движению материала (противопоточная |
||
сушка). Про сход т |
ыстрый нагрев материала. Песчаные частицы нагре- |
|
ваются быстрее, чем зерна ще ня. |
||
Сушка |
нагрев каменных материалов должны обеспечить не только |
|
горячие |
||
заданную температуру, но и полное удаление влаги. |
||
Из суш льного |
ара ана горячие материалы поступают по ссыпному |
лотку в горячийбАэлеватор и поднимаются в распределительный агрегат. Грохот разделяет горячие материалы по фракциям (по количеству сит), далее материалы поступают в расходные емкости. Отсеки снабжены автоматическими управляемыми затворами, которые подают материал в дозатор. Отдозированные материалы поступают в смеситель. Параллельно с этим происходит объемное дозирование битумаД.
Для нагрева и обезвоживания битума применяют битумоплавильное оборудование непрерывного и периодического действия. В установках непрерывного действия с газовым или электрическим подогревом обезвоживание происходит в тонком слое. Установки периодического действия состоят из нескольких битумоплавильных котлов.ИВ них вязкий битум готовят по двухступенчатому циклу: в одних котлах битум нагревают до 110–120 ºС и при необходимости выпаривают воду, затем перекачивают с помощью битумных насосов в другие расходные котлы, где нагревают битум до рабочей температуры (130–150 ºС).
Компоненты асфальтобетонной смеси дозируются по массе; исключение допускается для битума и добавок ПАВ, дозирование которых ведется по объему. Для предварительного дозирования минеральных материалов (до поступления в сушильный барабан) используют агрегаты питания. Точность предварительного дозирования минеральных материалов ±5%. При работе с очень влажными материалами вводят поправку на их влажность. Допускаемая погрешность при дозировании составляющих асфальтобетонной смеси не должна превышать: для щебня, песка и мине-
45
рального порошка, применяемых для приготовления асфальтобетонов I и II марок ±3%; применяемых для приготовления асфальтобетонов III марки ±5% от массы соответствующего компонента; для битума независимо от марки асфальтобетона ±1,5% от их массы.
Особое внимание уделяется режимам перемешивания асфальтобетонной смеси в смесителях циклического и непрерывного действия. Режим перемешивания минеральных материалов с битумом играет основную роль в процессе приготовления смеси. Тщательно перемешанная смесь характеризуется равномерным распределением всех ее компонентов и полным обволакиван ем поверхности частиц битумом. Продолжительность переме-
шиван я зав с т от т па смесительной установки и вида приготавливае- |
||
мой смеси. Она колеблется от 20 до 60 с в смесителях отечественного про- |
||
С |
|
в смесителях зарубежных фирм в |
. Время перемешивания |
||
1,5 раза меньше. |
|
|
Повышен е качества смеси |
увеличение производительности тех- |
|
нологического оборудования могут быть обеспечены интенсификацией |
||
процесса перемеш ван |
, применением П В, активаторов, совершенство- |
|
изводства |
|
|
ванием способа введен я вяжущих. Способ введения битума оказывает |
||
существенное вл ян е на перемешивание и качество смеси. Принцип ин- |
||
тенсификации |
на сокращении длительности или увеличении |
базируется скорости перемешиванияА.
В целях совершенствования технологии приготовления асфальтобетонной смеси целесоо разно широко применять активаторы – цемент, известь, сланцевую смолу и др. Введение этих материалов способствует созданию активной свежеобразованнойДповерхности, имеющей в начальный период большую энергию, что обусловливает высокую адгезию с вяжущими материалами [9].
Сушка каменных материалов должна обеспечить их обезвоживание и равномерный нагрев до рабочей температуры (220–250 ºС). Недогрев материалов ухудшает их обволакивание вяжущимИи увеличивает неоднородность смеси. Перегрев увеличивает расход энергии и способствует образованию у каменных материалов микротрещин, а соприкосновение вяжущего с перегретым камнем вызывает пережог вяжущего и потерю вяжущих свойств.
Эффективность сушки зависит от равномерности и скорости подачи в барабан каменных материалов и газов, условий сгорания газов, скорости вращения барабана, теплоемкости и влажности материала.
Подача жидкого топлива осуществляется по трубопроводам к форсункам, где происходит его сгорание. Подача топлива регулируется насосом (жидкого) или давлением (газообразного). В настоящее время для распыления жидкого топлива используют воздух, подаваемый вентиляторами низкого давления, использование для этой цели пара менее эффективно.
46
Различные комплекты машин комплектуются разными сушильными барабанами, их диаметр составляет от 0,68 до 2,2 м, длина – от 2,7 до 11 м, окружная скорость вращения – 0,6–0,8 м/с.
Обычно емкость барабана не достаточна для эффективного сгорания топлива, образуется дым, что ухудшает КПД установки, снижает нагрев
Сматериалов, ухудшает санитарные условия.
Особенность приготовления асфальтобетонной смеси в смесителе непрерывного действия (см. рис. 3.2) состоит в том, что смешение материалов (щебня, песка, м нерального порошка и битума) производится в
сушильно-смес тельном барабане. сушильномтрого фракц онные материалы транспортером или фронтальным погрузч ком подаются в бункер-дозатор и агрегат питания, в котором
осуществляется весовое дозирование с учетом влажности поступающих
материалов. Отдоз рованные материалы сборным транспортером подают-
ся в льнобарабане-смес тельный ара ан. Отличие этого барабана в том, что у него дл на в 1,5–2 раза ольше. Движение материалов и горячих газов в
осуществляется в одном направлении (поточная суш-
ка). Матер алы просуш ваются до рабочей температуры и переходят во вторую смес тельную камеру. Битум поступает в начальную зону барабана и при вращении его смешиваетсяАс нагретым минеральным материалом. Сюда же подается отдозированный минеральный порошок и битум. Готовая смесь поступает в промежуточный бункер и далее скиповым подъемником в накопительный ункер.
Битум проходит те же стадии из битумохранилища, поступает в битумоплавильню, где нагревается доД130–160 ºС, далее через битумный дозатор поступает в смесительное отделение. ымовые газы, проходя через смесительное отделение, отдают часть уносимой пыли битумным пленкам, из-за чего выброс уменьшается до 10 и более раз. Очистка от пыли состоит из сухой ступени газоочистки, дымососа, мокрой системы газоочистки.
Достоинства этой технологии: уменьшениеИколичества агрегатов, снижение металлоемкости и энергоемкости, простота и надежность работы оборудования, уменьшение количества пыли [15].
Недостатки: интенсивное старение битума из-за контакта с выбрасываемыми газами, окисление битума, испарение его маслянистых фракций, высокая опасность воспламенения битума.
Агрегаты питания обеспечивают дозирование минеральных материалов.
Пылегазоочистительные установки служат для обезвреживания пы-
ли и газов, образующихся на АБЗ и засоряющих прилегающий воздушный бассейн, что является особенно недопустимо в городских условиях.
47
Основными источниками пыли в смесительном цехе являются:
1) сушильный барабан, дымовые газы которого содержат значительное количество остатков несгоревшего топлива (сажи), а также пыли от щебня и песка;
2) минеральный порошок (от соприкосновения горячего песка и Сщебня с влажным минеральным порошком происходит интенсивное выде-
ление пара, который уносит с собой большое количество мелких частиц); 3) отходы, образующиеся от грохотов, труб, элеваторов уносятся в
атмосферу.
Основными мерами борьбы с пылеобразованием служат: активаца) гермет ческое уплотнение очагов пылеобразования кожухами с прокладками;
б) отсос запыленного воздуха от очагов пылеобразования, особенно
от суш льного бара ана, мешалки и грохота, с последующей пылеочист-
кой этого) обработкаявоздуха). ; м нерального порошка органическими вяжущими (его При отсосе запыленного воздуха рекомендуются следующие вели-
чины разрежен я: 0,1–0,15 кг/м3 – у сит вибрационных, винтовых конвейе-
ров и бункеров; 0,2 кг/Ам3 – у мешалки, в местах падения минералов на ленточный транспортер, ковшовых элеваторов.
Эксплуатация смесительных установок с входящими в их комплект одним или двумя циклонами не отвечает санитарным нормам очистки, поэтому в настоящее время внедряют 2–3– ступенчатые установки для очистки воздуха. Сухие циклоны не гарантируютДочистку газов от мельчайших частиц (менее 10 мкм), поэтому их ставят на первой или второй ступени очистки. Гораздо более эффективны циклоны с мокрым улавливанием, внутренняя часть которых омывается водой или пенными реагентами. В настоящее время рекомендуется групповая (батарейная) установка ци-
клонов (по 2–8 шт.) малого диаметра. И Промышленностью выпускаются следующие типы циклонов, наибо-
лее подходящих для АБЗ: ЦН-15 (диаметр от 100 до 700 мм); ЦН-24 (диаметр 500 и 1000 мм) и ЦН-11 (диаметр 100 и 800 мм). Самый лучший результат дает батарейная установка циклонов ЦН-11.[4].
В настоящее время довольно широкое распространение получают комплекты АБЗ, оборудованные ходовым пневмоколесным приспособлением. Эти установки являются мобильными и свободно могут перемещаться к строящейся дороге. Производительность передвижных смесителей не велика (ДС-14 – 3 т/ч; ДС-4 – 6,5 т/ч) и они довольно редко применяются в городском дорожном строительстве. Модели асфальтосмесительного оборудования отечественного производства представлены в табл. 3.1 [19].
48

|
|
|
|
|
|
|
|
Таблица 3.1 |
|
|
|
Асфальтосмесители и комплекты автоматизированного оборудования |
|||||||
|
|
|
|
|
|
|
|
||
|
Модель |
|
Оборудование |
|
Технические данные |
|
|||
|
|
и его назначение |
|
|
|||||
|
|
|
|
|
|
|
|||
|
ДС-14 (Д-386) |
Для приготовления горячих сме- |
Производительность 3 т/ч, |
|
|||||
|
|
|
|
сей при ремонте покрытий, пере- |
скорость передвижения 2 км/ч |
|
|||
|
|
|
|
движной, периодического дейст- |
|
|
|||
|
|
|
|
вия |
|
|
|
|
|
|
-4 ( |
-288) |
|
Непрерывного действия, назначе- |
Производительность до 6,5 т/ч |
|
|||
|
|
|
|
н е то же |
|
|
|
|
|
|
-35 ( -597) |
Сборно-разборный, периодическо- |
Производительность до 25 т/ч, |
|
|||||
|
горячих |
|
|
емкость мешалки до 600 кг |
|
||||
|
|
|
|
го действ я, автоматизированный |
|
||||
|
-5 ( |
-325 А) |
То же |
|
|
|
Производительность до 30 т/ч, |
|
|
ДС |
|
|
|
емкость мешалки до 600 кг |
|
||||
|
Д-508 (Д-508-2) |
Комплект о орудования для при- |
Производительность до 25 т/ч |
|
|||||
|
|
|
|
готовлен я |
|
смесей, |
ба- |
|
|
|
|
|
бА |
|
|
||||
|
|
|
|
шенный |
|
|
|
|
|
|
Д-617 |
|
|
То же |
|
|
|
Производительность до 50 т/ч |
|
|
Д-617-1 |
|
Смес тель с мешалками периоди- |
То же |
|
||||
|
|
|
|
ческого действия, партерный |
|
|
|
||
|
Д-617-2 |
|
То же с мешалкой периодического |
То же |
|
||||
|
|
|
|
действ я, |
ашенный |
|
|
|
|
|
Д-645-2 |
|
То же |
|
|
|
Производительность до 100 т/ч |
|
|
|
Д-645-3 |
|
То же с мешалкой непрерывного |
То же |
|
||||
|
|
|
|
действия, партерный |
|
|
|
|
|
|
ДС-117-2 |
|
Смеситель |
непрерывного дейст- |
Производительность до 250 т/ч |
|
|||
|
|
|
|
вия, партерный |
|
|
|
|
|
|
|
|
|
|
|
Д |
|||
|
|
3.3. Особенности приготовления на |
БЗ холодных |
||||||
|
|
асфальтобетонных смесей и черного щебня |
|||||||
|
|
|
|
|
|
|
|
И |
|
|
|
Технологическая схема приготовления горячих, холодных асфальто- |
бетонных смесей и черного щебня принципиально не отличается от приготовления горячей смеси. Различаются они главным образом температурными режимами [20].
Температуры приготовления холодных смесей должны быть в пределах 90–110 ºС (в зависимости от марки битума), а с применением ПАД – 70–100 ºС. Обычно холодные смеси имеют максимальный размер зерен – 10–15 мм. Меньшая температура приготовления и малый размер зерен определяют некоторые специфические свойства приготовления этих смесей.
Холодные смеси требуют особенно тщательного перемешивания, поэтому готовят их обычно в установках с принудительным перемешиванием, а время перемешивания достигает 180–240 с [19].
При приготовлении холодных смесей особенно эффективно применять активированные материалы (минеральный порошок, битум и пр.).
49
Холодные смеси обычно перед употреблением некоторое время находятся на складе (от 4 до 8 месяцев), поэтому одной из особенностей технологии приготовления холодных смесей является обработка их для уменьшения слёживаемости. Это возможно достигнуть тремя способами: понижением температуры смеси перед подачей на склад до 25–30 ºС; добавлением химических веществ; перемешиванием смеси на площадке хранения.
Охлаждение смеси достигается двумя способами: принудительным продуван ем с помощью вентилятора либо естественным охлаждением
смеси в процессе ее транспортировки на склад.
Иногда для уменьшения слёживаемости смеси в процессе ее приго- |
|
товлен я в нее вводятся специальные добавки в виде водных растворов со- |
|
С |
|
апстока (3–5%), сульф дно-спиртовая барда (ссб) (10%) с хлорным желе- |
|
зом (10%) др. (в % по массе смеси). Растворы вводят в мешалку после |
|
окончан я перемеш |
я минеральных материалов с битумом и произво- |
дят дополн тельное в течение 6–10 с.
перемешивание В некоторыхбАслучаях слёживаемость холодной смеси на площадке
может быть знач тельно снижена периодическим перемешиванием (перелопачиван ем) с помощью погрузчиков, экскаваторов и пр.
Использование эмульсий для приготовления черного щебня и холодного асфальтобетона накладывает свои отпечатки на технологию приготовления смесей.
Применение эмульсий дает ряд преимуществ. Вследствие большей подвижности эмульсий минеральные материалы лучше обволакиваются вяжущим, что позволяет снизить расходДвяжущего и уменьшить время перемешивания. Минеральную часть перемешивают с эмульсией в холодном состоянии, что исключает затраты времени и средств на просушку вяжущего и подогрев минеральных материалов. ля приготовления асфальтобетонов на эмульсиях, необходимы влажные (2–3% по массе) и чистые материалы, при этом возможно увеличенное содержаниеИмелких фракций.
В то же время асфальтобетонам и черному щебню (холодным) на эмульсиях присущ ряд недостатков. Эти смеси, особенно на быстрорастворимых эмульсиях, нельзя длительное время хранить на складах. Прочность слоев дорожных одежд с применением холодных смесей ниже прочности асфальтобетонов на горячих смесях. Для покрытий такого типа характерен длительный набор прочности – период формирования после уплотнения.
Приготовление черных смесей с эмульсиями включает те же технологические процессы, которые необходимы при использовании битумов, кроме приготовления минеральных материалов. Смешение материалов можно производить в смесителях принудительного и свободного перемешивания. Чтобы улучшить прилипание вяжущего и уменьшить слёживаемость материалов, минеральные материалы можно обрабатывать известью
50
(0,2–0,7% по массе). Наилучший эффект достигается при обработке каменных материалов двумя эмульсиями. Технологическая последовательность при этом такова. Щебень или смесь перемешивают с известью 15– 20 с, затем в мешалку подают обратную эмульсию и опять перемешивают 1–2 мин. Если в смесь добавляют минеральный порошок, то его увлажняют (10–20% по массе), подают в мешалку и снова перемешивают, затем подают прямую эмульсию и все опять перемешивают не более 15–30 с.
Поверхностно-активные добавки вводят в мешалку до подачи битума или вместе с н м.
и |
|
3.4. Особенности приготовления смесей и работы на АБЗ |
|
Св холодный пер од года |
|
Для повышен я производительности АБЗ и снижения себестоимости |
|
работу |
АБЗ и в холодный период го- |
продукц целесоо разно продлевать |
да.
В холодный пер од года (т.е. при температуре менее +5 ºС) заводы могут готов ть холодные смеси. При этом технологическая схема приготовлен я матер ала прАнципиально не отличается от летних условий работ. Добавляются лишь технологические операции, направленные на уменьшение теплопотерь.
Хранению материалов в холодный период года следует уделять особое внимание. Органические вяжущие нужно хранить только в хорошо за-
крытых хранилищах. МинеральныйДпорошок должен быть сухим, лучше
применять активированные минеральные порошки. Сушат минеральный порошок в сушильных барабанах, что сопряжено с большими его потерями. В щебне и песке не должно быть мерзлых комьев. ля этого площадку очищают от снега и обеспечивают хороший водоотвод. Поверхность шта-
беля лучше укрывать брезентом или полиэтиленовойИпленкой, в противном случае каменные материалы приходится подогревать в штабеле или
рыхлить. Наилучший эффект дает хранение каменных материалов в закрытых или полузакрытых складах.
Транспортировку материала организуют с минимальными теплопотерями. Все транспортные конвейеры закрывают кожухами, при необходимости устраивают теплоизоляцию. Особенно тщательно теплоизолируют битумопроводы и горячий элеватор. Машины, подаваемые под погрузку, должны иметь систему обогрева кузова выхлопными газами.
Сушка материалов производится обычным способом, но продолжительность ее увеличивается на 20–30%, поэтому для поддержания производительности завода на заданном уровне необходимо предусматривать бóльшую производительность сушильных линий. Сушильные барабаны целесообразно также теплоизолировать.
51
Перемешивание материалов более продолжительно, увеличение достигает 30–80%. Для улучшения качества материалов и ускорения перемешивания применяют различные ПАД – известь (1–2% по массе каменных материалов), ферросоапсток (0,5–0,7%) и др. Мешалку целесообразно утеплить изоляционными материалами.
СВыгрузка готовой смеси малыми порциями (0,5–1,0 т) в автомобиль связана с большими теплопотерями. Чтобы избежать их под мешалкой, устраивают утепленный накопительный бункер емкостью, соответствующей емкости транспортных средств, используемых для доставки смеси. Это исключает простои транспорта.
ПриВ холодный пер од года целесообразна работа АБЗ в три смены, т.к. при работе в 1–2 смены каждый раз перед началом работы требуется затратить 1–2 часа на подогрев тру опроводов, насосов и пр.
исроков стробАтельства, конструкции асфальтобетоного покрытия, наличия материалов, комплекса местных условий (грунтово-гидрологических, климатических), подъездных путей, источников снабжения водой, электроэнергией, топливом и пр. Завод должен обеспечивать строительство высококачественными смесями и в нужном количестве.
Проектируя АБЗ, решают следующие основные вопросы: выбор месторасположения завода; определениеДобъемов работ по выпуску асфальтобетоной смеси – производительность завода и необходимое количество материалов для приготовления асфальтобетона; разработка схемы технологического процесса; подбор оборудования и механизмов; разработка средств механизации и автоматизации основных технологических процессов; проектирование складского хозяйства; расчетИтребуемых энергоресурсов; разработка генерального плана завода; разработка основных положений по строительству завода; расчет необходимого количества работников; составление калькуляции стоимости смеси и сметно-финансового расчета; разработка основных мероприятий по охране труда, технике безопасности
ипротивопожарной технике; определение основных техникоэкономических показателей завода [21].
Разработка генерального плана завода. Разработке генерального плана предшествует определение размеров всех зданий и сооружений. На стационарных заводах устраивают здания капитального типа, на временных – сборно-разборные.
На генеральном плане указывают расположение смесительнодозированного цеха, плавильной установки, склада минеральных материа-
52
лов, битумохранилища, лаборатории, конторы, транспортных путей, коммуникаций энергохозяйства и др.
При разработке генеральных планов АБЗ необходимо учесть ряд рекомендаций.
Площадь завода должна быть минимальной и компактной, вместе с этим давать возможность удобно расположить всё оборудование и допускать некоторое расширение завода.
Основным принципом проектирования генерального плана является рациональное расположение оборудования, при котором в полной мере соблюдается пр нятая технологическая схема с наименьшими затратами на
переработку сырья |
транспортировку материалов. Поэтому движение ма- |
териалов от одного агрегата к другому должно быть прямоточным, по |
|
С |
ез дополнительных перегрузок. Встречных потоков |
кратчайшему |
грузов надо збегать, т.к. они ухудшают условия эксплуатации завода.
возможно бл же к |
смес тельному цеху, что уменьшает стоимость транс- |
|
портных галерей. |
О ычно |
в щебне на АБЗ больше в |
пути
1,5–1,7 раза, чем потре ность в песке, поэтому склады щебня располагают ближе к смес телю, а склады песка – дальше.
кладыпотребностьще ня, песка, минерального порошка должны находиться
При проектированииАтранспортных путей целесообразно избегать встречного движения автомо илей, предусматривая кольцевое или сквозное движение. Ширина проездов предусматривается не менее 5,5 м при двухстороннем движении и не менее 3,5 м при одностороннем. Минимальные радиусы разворота автомобилей принимают 15–20 м. Выезд с территории АБЗ должен быть оборудованДвесами. Перед смесителем предусматривают площадку не менее 500–600 м2 для маневрирования и кратковременной стоянки автомобилей. Все транспортные пути и площадки должны иметь твердое покрытие [20].
Битумоплавильня обычно располагается ближе к смесителю. Это необходимо для минимизации потерь тепла приготовленнымИбитумом.
Административный и санитарно-бытовой блок целесообразно отделять от промышленного блока.
Принципиальное решение всего генерального плана в значительной мере зависит от компоновки смесителей, особенно если их несколько.
Раздельная и кольцевая схемы расположения смесителей требуют большей территории и несколько усложняют транспортирование компонентов смеси. Зато при этих схемах упрощается вывозка готовой смеси. Прямолинейная схема установки более рациональна при наличии двух смесителей, она более компактна. Еще более компактна параллельная схема, однако при такой компоновке значительно ухудшаются условия работы автотранспорта. Выбор оптимальной схемы зависит от многих факто-
53
ров: площади, отведенной под завод; типа смесителей; конструкции складов и пр.
Большое значение имеет максимальное использование длины тупика, вдоль которого обычно расположены склады щебня, песка, минерального порошка, вяжущих. Эти склады можно размещать на одной или обеих сторонах тупика в зависимости от конкретных местных условий.
Территория АБЗ обязательно ограждается. Необходимо, чтобы на территории завода была зеленая зона.
При разработке генерального плана сравнивают несколько сопоставимых вар антов, выб рают лучший из них на основе техникоэконом ческого сравнен я и вычерчивают в масштабе 1:500.
Генеральный план производственного предприятия – это проект рас- |
|||
С |
|
|
|
положен я всех здан й, сооружений, технического, энергетического и |
|||
вспомогательного о |
|
, инженерных сетей, транспортных путей |
|
орудования |
|
||
и т.д., обеспеч вающ |
х наи олее лагоприятные условия производствен- |
||
ного процесса на предпр ятии, рациональное экономическое использова- |
|||
ние терр тор |
на |
ольшую эффективность капитальных вложений. |
|
На АБЗ должны |
ыть склады материалов для хранения следующих |
||
запасов, обеспеч вающ е максимальную производительность завода: |
|||
- песка –15-дневный запас; |
|
||
- битума – месячный запас; |
- минеральногобАпорошка – 15-дневный запас; - гидрофобизирующих до авок – 3-месячный запас.
Склады должны быть запроектированы таким образом, чтобы обеспечить раздельное хранение щебняДразличных фракций и песка, исключающее снижение качества и загрязнения окружающей среды. Методы выгрузки битума, его хранения в битумохранилищах должны исключить возможность его обводнения. На основе обобщения проектной практики установлено, что основными принципами проектирования генеральных планов предприятий являются [22]: И
- размещение предприятий в промышленных узлах населенных мест на базе кооперирования с другими предприятиями;
- создание условий для расширения производства; - размещение складских помещений с учетом минимальных транс-
портных затрат; - размещение зданий и сооружений с минимальными разрывами;
-благоустройство территории;
-комплексное решение по трассировке и способах прокладки инженерных сетей;
-применение прогрессивных видов транспорта.
При проектировании генерального плана все производственные здания и сооружения группируются в соответствующие зоны с учетом сани-
54

тарных и противопожарных требований, видов обслуживающего транспорта. Пример генерального плана прирельсового АБЗ представлен на рис. 3.6 [4].
Си
Рис. 3.6. ГенеральныйбАплан прирельсового БЗ: 1 – склад каменных материалов; 2 – отделение подачи каменных материалов; 3 – асфальтосмесительная установка; 4 – накопительный ункер готовой смеси; 5 – компрессорная установка; 6 – склад минерального порошка; 7 – склад мазута; 8 – битумохранилище; 9 – склад ГСМ; 10 – склад резиновой крошки; 11 – ремонтныеДмастерские; 12 – подрельсовый
бункер; 13 – стоянка для автотранспорта; 14 – административный корпус; 15 – весовая и пункт контроля; 16 – туалет; 17 – трансформаторная подстанция
По использованию площади предприятия делят на зоны: - предзаводскую; - производственную; - подсобную;
Предзаводская зона – заводоуправление, столовая, стоянка легкового транспорта.
- складскую. И
Производственная зона – смесительное отделение, компрессорная, цех, битумохранилище, битумоплавильня.
Подсобная зона – вспомогательные здания и сооружения, передвижные электростанции или трансформаторная подстанция, котельная, компрессорные и др.
Склады вместе с территорией, обслуживающие железнодорожные пути и автомобильные дороги, образуют складскую зону.
55
Производственная зона, как правило, является основой, вокруг которой размещаются объекты других зон. Производственная зона составляет 20–30% всей площади предприятия. Непосредственно к этой зоне прилегают подсобная и складская зоны. Площадь подсобной зоны составляет до 1,5%. Площадь предзаводской зоны – до 5% территории. Площадь под же-
Слезнодорожные пути – до 10% территории, а площадь под дороги – до 20%. Площадь, занятая под озеленение, может достигать до 15–20% и более.
Расстоян е между зданиями и сооружениями принимаются в соответ-
и сооружен ям с учетом ветров преобладающего направления и размеров -защ тных зон. Для АБЗ – 500 м.
ствии с прот вопожарными и санитарно-гигиеническими требованиями. санитарномес тельные установки, выделяющие пыль и газ в атмосферу, следует располагать по отношению к жилой застройке или к другим зданиям
В решен генерального плана следует предусматривать наглядное
количество план ровочных элементов, а также типов подъездов и дорог.
Расстоян е между зданиями и сооружениями составляет от 9 до 15–18 м в зав с мости от степени их огнестойкости. Расстояния между открытыми технолог ческ ми установками принимаются по технологическим нормам. Минимальная ширина тротуаров – 1,5 м. Графическое изображение генеральных планов должно соответствовать требованиям
ГОСТ 21.204–93 СПДС [23].
Территория, на которой располагается прирельсовый АБЗ (см.
рис. 3.6), должна быть благоустроена и иметь подъездные пути, водоотвод, |
|
дороги, тротуары, условия культурно-бытового обеспечения, ограду и ос- |
|
вещение. |
бА |
Покрытие на открытых площадкахДдля хранения щебня и песка, а также на основных проездах рекомендуется устраивать из монолитного бетона. На территории прирельсового АБЗ располагаются здания и сооружения для технического обслуживания и ремонта технологическогоИоборудования, ремонтно-механические мастерские.
В составе АБЗ должна быть предусмотрена лаборатория, которая может размещаться в административном здании либо в отдельном помещении. Лаборатория должна быть оснащена всеми необходимыми приборами и оборудованием для проведения контроля за качеством материалов, асфальтобетонных смесей и асфальтобетонов согласно ГОСТ 9128–13.
Основным оборудованием на АБЗ (см. рис. 3.6) является асфальтосмесительная установка, кроме этого, на территории АБЗ размещается административный корпус, компрессорная установка, силосные склады минерального порошка, битумохранилище, склады ГСМ, ремонтные мастерские, весовая, туалет, трансформаторная подстанция и др.
56

В случае, когда железная дорога находится на большом расстоянии от строящейся автомобильной дороги, все материалы транспортируются автотранспортом, проектируют притрассовые АБЗ с использованием асфальтосмесительных установок мобильного типа (рис. 3.7) [4].
СибАДИ2Рис. 3.7. Генеральный план притрассового БЗ: 1 – склад каменных материалов; 2 – отделение подачи каменных материалов; 3 – смеситель; 4 – расходный бункер
цемента; 5 – кабина обслуживания и управления; 6 – емкости с битумом; 7 – отделение приготовления добавок; 8 – контора с лабораторией; 9 – спортивная площадка;
10 – материально-технический склад; 11 – резервуары противопожарные; 12 – ремонт- но-механическая мастерская; 13 – площадка для открытых ремонтных работ;
14 – бытовые помещения; 15 – баня; 16 – столовая; 17 – трансформаторная подстанция; 18 – туалет; 19 – артезианская скважина; 20 – передвижная компрессорная установка; 21 – отделение лаборатории; 22 – весовая с автоматическими весами грузоподъемностью 30 т; 23 – канализационные очистные сооружения; 24 – склад ГСМ;
На территории притрассового АБЗ располагаются склады каменных материалов песка. Подача каменных материалов в расходные бункера осуществляется одноковшовыми фронтальными погрузчиками. Минеральный порошок хранится в металлических расходных силосных складах. Минеральный порошок транспортируется пневмотранспортом по трубам, для этого используется передвижная компрессорная установка. Битум хранится в металлических цистернах емкостью 100 т и более. Битумное хозяйство должно быть обеспечено оборудованием для перекачки битума, его нагрева до рабочей температуры и битумовозами.
57
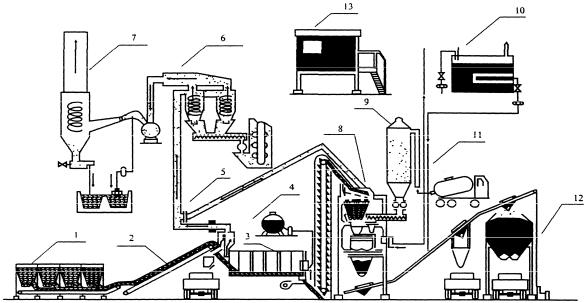
В состав притрассового АБЗ входят внутризаводские дороги, передвижные электростанции, передвижные компрессорные станции (прил. 7), склады различных материалов, весовая, бытовые помещения, баня, склады Г М, ремонтные мастерские и т.д.
Основным технологическим оборудованием на АБЗ являются ас- Сфальтосмесительные установки, которые обеспечивают основные техноло-
гические операции по приготовлению асфальтобетонных смесей. Асфальтобетонные установки классифицируются по основным кон-
структ вным технолог ческим показателям, производительности, прин-
ципу действ я смес теля, конструктивной компоновке оборудования и аг- стикирегатов, моб льности.
По про звод тельности различают асфальтосмесительные установки
12, 25, 32, 50, 100, 200, 250, 400 т/ч.
В Росс про зводителями асфальтосмесительных установок являются ОАО «бАСаста», «Центросвяр» и УралНИТИ. Технические характери-
асфальтосмес тельных установок приведены в прил. 6 [4].
В асфальтосмес тельной установке ДС-185 (рис. 3.8) все процессы автомат з рованы.
Д
Рис. 3.8. Технологическая схема асфальтосмесительнойИустановки ДС-185 (Украина): 1 – агрегат питания; 2 – конвейер; 3 – сушильный агрегат; 4 – топливный бак; 5 – I ступень (предварительная) очистки дымовых газов; 6 – II ступень очистки дымовых газов; 7 – III ступень очистки дымовых газов (скруббер Вентури); 8 – смесительный агрегат; 9 – агрегат минерального порошка; 10 – нагреватель битума; 11 – система теплоносите-
ля; 12 – бункер готовой смеси; 13 – кабина оператора
Пульт управления расположен в кабине оператора.
Технические характеристики асфальтосмесительных установок зарубежного производства приведены в прил. 7[4].
58

Общий вид асфальтобетонного завода фирмы AMAN-160 производительностью 160 т/ч ( г. Омск ЗАО «Стройсервис») представлен на рис. 3.9, 3.10.
1994 г. на данном заводе выпущено более 1,5 млн т асфальтобе-
тонных смесей. |
|
|
|
С |
|
|
|
и |
Рис. 3.9. АБЗ фирмы AMAN |
||
|
|
производительностью 160 т/ч |
|
б |
(г. Омск, ЗАО «Стройсервис») |
||
|
|
||
|
АБЗ |
|
|
|
|
Рис. 3.10. Выпуск готовой |
|
|
Д |
||
|
|
асфальтобетонной смеси |
|
|
|
на |
фирмы AMAN |
|
|
(г. Омск, ЗАО «Стройсервис») |
Асфальтобетонный завод AMAN производительностьюИ160 т/ч полностью автоматизирован, его обслуживают 4 человека. На заводе выпускаются асфальтобетонные смеси типа А, щебеночно-мастичные асфальтобетонные смеси высокого качества. В настоящее время этот завод демонтирован и на его месте смонтирован асфальтобетонный завод AMAN производительностью 240 т/ч.
На АБЗ имеются склады каменных материалов с цехом по их переработке (рис. 3.11) и битумное хозяйство (рис. 3.12).
59

Си необходимо
Рис. 3.11. СкладыАкаменных материалов с цехом их переработки
Щебень складировать на площадке с твердым покрытием
с разделением по фракциям. Количество фракций щебня должно быть от трех до пяти. Расстояние от ще еночных складов до асфальтосмесительной установки должно быть минимальнымД.
Фронтальными погрузчиками каждая фракция щебня транспортируется и перегружается в бункер -дозаторы.
Песок также фронтальными погрузчиками со склада песка транспор-
тируют и перегружают его в бункер-дозатор.
Битум транспортируют по трубам от битумохранилищаИи битумоплавильни к смесительному отделению с помощью шестеренчатых битумных насосов.
60

СРис. 3.12. Битумное хозяйство
Б тум доставляют на завод автогудронатором или битумовозом и перекачивают в металлические емкости (битумохранилища). С помощью трубопроводов и итумных насосов эти емкости соединены между собой, таким образом битум можно перекачивать из одной емкости в другую. Все трубопроводы сна жены паровой рубашкой, за счет которой сохраняется
температура транспортируемого битума. Рабочая температура битума, по- |
||||||
даваемого от битумоплавильни до асфальтосмесителя, должна соответст- |
||||||
|
бА |
|
|
|||
вовать требованиям, представленным в табл. 3.2 [17]. |
|
|
||||
|
|
|
|
|
Таблица 3.2 |
|
|
|
Рабочая температура битума |
|
|
||
|
|
|
Д |
|
||
ид смеси |
Температура смеси, °С, в зависимости от показателя битумов |
|
||||
|
|
|
|
|
|
|
|
Глубина проникания иглы при 25 °С, 0,1 мм |
|
|
|||
|
|
|
|
|||
|
|
|
|
|
|
|
|
40-60 |
61-90 |
91-130 |
131-200 |
201-300 |
|
Горячая |
|
|
|
И |
|
|
От 150 |
От 145 |
От 140 |
От 130 |
От 120 |
|
|
до 160 |
до 155 |
до 150 |
до 140 |
до 130 |
|
|
|
|
|
|
|
|
|
61