
- •ВВЕДЕНИЕ
- •1.2. Классификация современных автомобилей
- •1.3. Требования к современным автомобилям
- •1.5. Анализ компоновочных схем автомобилей
- •1.6. Компоновка легковых автомобилей
- •1.7. Виды кузовов
- •1.8. Весовые и геометрические параметры автомобилей
- •1.9. Основные понятия о надежности и долговечности
- •ГЛАВА 2. ОПРЕДЕЛЕНИЕ НАПРЯЖЕНИЙ
- •2.2. Тензомост
- •2.3. Расчетные методы определения напряжений
- •2.4. Типы расчетов
- •ГЛАВА 3. СЦЕПЛЕНИЕ
- •3.1. Общие положения
- •3.3. Сцепление с диафрагменной пружиной
- •3.5. Подбор и проверка параметров сцепления
- •3.6. Расчет деталей сцепления на прочность
- •4.2. Бесступенчатые трансмиссии
- •4.3. Механическая коробка передач
- •4.4. Работа инерционного синхронизатора
- •4.5. Основы расчета КП
- •ГЛАВА 5. КАРДАННАЯ ПЕРЕДАЧА
- •5.1. Общие положения
- •5.2. Кинематика асинхронного карданного шарнира Гука
- •5.4. Расчет на прочность деталей карданной передачи
- •6.1. Главная передача (ГП)
- •6.2. Дифференциал. Принцип работы, блокировка
- •6.4. Основы расчета дифференциала
- •7.3. Балки мостов
- •7.4. Основы расчета балок мостов
- •8.2. Упругая характеристика подвески
- •10.3. Расчет тормозного привода
- •ЗАДАНИЯ ДЛЯ САМОКОНТРОЛЯ
- •Библиографический список
1.8.Весовые и геометрические параметры автомобилей
1.Сухая масса (сухой вес) – масса законченной конструкции автомобиля без запасного колеса, запасного инструмента и принадлежностей (ЗИП), нестандартного оборудования и заправки больших заправочных емкостей (бензобак, система охлаждения).
2.Снаряженная (собственная) масса (вес) – масса автомобиля, подготовленного к конкретным условиям эксплуатации без водителя, пассажиров, груза и багажа.
3.Полная масса (вес) – масса снаряженного и груженого номинальной нагрузкой автомобиля с водителем, пассажирами и багажом.
4.Номинальная грузоподъемность – максимальное значение груза, которое обеспечивает расчетное значение напряжений деталей
иузлов автомобиля, его эксплуатационныеИхарактеристики, планируемую долговечность.
Удельная масса узлов и агрегатов автомобиля в процентах от его собственной массы: Д
- Двигатель: 12–16% - Сцепление: 0,5–0,7% А
- Коробка передач: 2,5–5% - Карданная передачаб: 1–1.5% - Ведущие мосты: 10–16% - Ведомые мостыи: 5–9%
- Все колеса в сборе с ш нами: 7–20% - Рама: 10С–15% - Кабина: 5–14%
- Бортовая платформа: 11–16%.
Габариты автомобиля должны иметь минимальные размеры, к тому же не превышающие по ширине 2,5 м; по высоте – 3,8 м с возможностью понижения до 3,1 м для транспортировки по железной дороге.
По длине одиночный двухосный автомобиль не должен превышать 11 м, трехосный – 13 м, седельный тягач – 15 м, тягач с двухосным прицепом – 18 м, тягач с двумя прицепами – 24 м, городской сочлененный автобус – 16 м.
1.9.Основные понятия о надежности и долговечности
Надежность – свойство сохранять эксплуатационные показатели в заданных пределах в течение требуемого промежутка времени или определенного пробега [2, с. 17].
17
Обеспечить 100% надежности невозможно, так как она зависит от множества случайных факторов (условия эксплуатации, разброс характеристик материалов, условия хранения и т.д.). Численно надежность характеризуется вероятностью безотказной работы за уста-
новленное время или пробег автомобиля |
|||||
|
P |
= P |
= |
N0−∑ni |
, |
|
|
||||
|
(t) |
(s) |
|
N0 |
|
где P(t) |
|
|
|
||
– вероятность безотказной работы по времени; P(s) – вероят- |
|||||
ность |
безотказной работы по пробегу; N0 – количество деталей; |
||||
∑ni – |
количество деталей, отказавших за то же время. |
||||
Вероятность безотказной работы зависит от характера соедине- |
ния элементов в конструкции. При последовательном соединении вероятность безотказной работы всей системы определится путем перемножения вероятностей безотказной работы отдельных деталей
|
|
|
Pсист = P1 |
|
n |
|
|
|
|
P2 P3 = ∏Pi . |
|||
|
|
|
|
|
|
i =1 |
|
Вероятность безотказной работы всейИсистемы оказывается все- |
|||||
гда ниже вероятности безотказной работы самого ненадежного звена |
||||||
|
P1 = 0,9 |
|
|
|
|
Д |
|
P2 = 0,9 |
|
|
|
|
|
|
|
|
|
А |
||
|
P3 = 0,1 |
|
|
|
||
|
Pсист = 0,9 ∙ 0,9 ∙ 0,1 = 0,081. |
|
||||
|
|
|
|
б |
|
|
|
При параллельном соед нении вероятность безотказной работы |
|||||
резко возрастает |
иn |
|
||||
|
|
|
Pсист |
=1 |
−∏(1− Pi ), |
|
тогда |
|
С |
|
i=1 |
|
|
Р1 =0,9 |
|
|
|
|||
|
|
|
|
|||
|
P2 =0,1 |
|
|
|
|
|
Pсист = 1– (1 – 0,9) ∙ (1 – 0,1) = 0,91.
Работоспособность – такое состояние механизма, при котором он в данный момент соответствует всем требованиям, устанавливаемым в отношении его основных параметров.
Прочность – способность деталей сопротивляться всем видам разрушения или изменения форм под воздействием окружающей среды и нагрузок, изменяющихся в определенных пределах.
18
а) Статическая прочность – способность сопротивляться разрушению от максимальных кратковременных нагрузок (появляются в условиях тяжелой эксплуатации и ударных воздействий).
б) Усталостная прочность (выносливость) – способность сопротивляться разрушению под влиянием многократно повторяющихся, в том числе очень малых нагрузок.
Износостойкость – способность противостоять изменению размеров, форм и массы.
Усталость – процесс постепенного развития повреждений от суммы повторяющихся нагрузок.
Предельный износ – величина износа, не позволяющая дальше эксплуатировать деталь в данных условиях.
Коррозия – поверхностное разрушение от электрохимического |
|
воздействия внешней среды. |
И |
|
|
Старение – общее изменение свойств детали от химических и |
|
Д |
|
физических воздействий внешней среды. |
|
Долговечность – свойство сохранять работоспособность с возможными остановками на ТО и ремонт (до разрушения или другого предельного состояния). А
Срок службы – календарная продолжительность эксплуатации или пробег до капитальногобремонта.
Ремонтопригодность – приспособленность детали (механизма) к проведению операцийиТО и ремонта.
Отказ – событ е, заканч вающееся полной или частичной утратой работоспособностиС.
Нагрузочный реж м – совокупность нагрузок, которые испытывает деталь или механизм во время эксплуатации в данных условиях.
Расчетно-нагрузочный режим – величина нагрузок, которые принимают в основу расчета на прочность путем обобщения нагрузочных режимов для различных условий эксплуатации.
ГЛАВА 2. ОПРЕДЕЛЕНИЕ НАПРЯЖЕНИЙ
2.1. Диаграмма напряжений σ = f (ε), предельные
напряжения, коэффициент запаса прочности
Если взять стальной цилиндрический стержень (рис.13) длиной L, зажать его по краям в гидравлическую разрывную машину и начать растягивать силой F, стержень будет деформироваться (удлиняться), оказывая внутреннее сопротивление растяжению, пропорционально
19
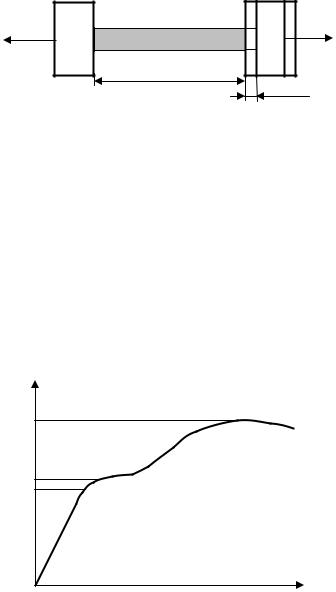
напрягая свою структуру. Внутреннее напряжение в материале обозначается буквой σ (сигма, размерность в мегапаскалях, т.е. МПа).
F |
|
|
|
|
|
|
F |
|
|
|
|
|
|
L |
|
L |
|
|
|
|
|
|
|
|
|
|
|
|
|
Рис. 13. Растяжение стержня |
|
||||
Деформируясь, |
стержень удлинится на величину |
L. Величина, |
||||||
равная отношению деформации L к начальному размеру L, называ- |
||||||||
ется относительной деформацией ε |
|
|
|
|||||
|
|
|
|
ε = |
∆L . |
|
|
|
|
|
|
|
|
L |
Д |
|
|
Вначале внутреннее напряжение в металле растет прямо про- |
||||||||
порционально деформации по линейному закону (рис.14). В этой зоне |
||||||||
|
|
|
|
А |
|
|
||
металл работает хорошо и готов работать долгоИ, если не превышать |
||||||||
напряжение σу– предел упругости (предел пропорциональности). |
||||||||
σТ |
|
|
б |
|
|
|
||
σВσ |
|
|
|
|
|
|
|
|
|
и |
|
|
|
|
|
||
С |
|
|
|
|
|
|
||
σУ |
|
|
|
|
|
|
|
|
0 |
|
|
|
|
|
ε |
|
|
Рис. 14. Диаграмма внутреннего напряжения металла |
Если еще увеличить деформацию, то напряжение превысит предел упругости и образец попадет в зону необратимого искажения внутренней структуры (пластическая деформация). Вернуться к прежней форме поврежденный образец уже не сможет, даже при полностью снятой нагрузке (он будет длиннее, чем был). Эта зона называется зоной текучести, а предельное напряжение – пределом текучести σТ . Попадать в эту зону в эксплуатации нельзя, иначе деталь при-
20
дется заменить. При дальнейшем растяжении происходит мгновенный процесс разрушения (стержень лопается поперек). Внутреннее напряжение перед моментом разрушения подскакивает до максимальной величины. Остановить разрушение в этой зоне уже невозможно, и поэтому максимальное напряжение σВ называется времен-
ным напряжением или пределом прочности.
В первой зоне (упругой) наблюдается линейная зависимость между деформацией и напряжением. Поэтому, точно замерив деформацию ε и зная коэффициент пропорциональности (Е-модуль упругости первого рода), можно определить напряжение внутри материала по формуле
σ = ε Е.
Коэффициент Е – справочная величина (для сталей, например, он равен 2∙105 МПа). Таким образом, определив напряжение в материале, можно сравнить его с σТ (σу ,σТ ,σВ – также справочные дан-
ные для любого материала) и сделать вывод, как близко от опасной зоны работает деталь. Так поступают при испытании новых конст-
рукций. |
И |
|
|
Пример: деталь изготовлена из стали марки Ст 15 с пределом |
текучести σТ =240 МПа. После экспериментального замера при мак- |
||||||
|
|
|
|
Д |
и подсчета по формуле |
|
симальной нагрузке величины деформации ε |
||||||
оказалось: σ = ε Е |
= 170 МПа. |
|
|
|
||
Превышение |
σТ над σ |
А |
σТ |
= 240 =1,4 , то есть |
||
составляет всего |
||||||
|
|
б |
|
σ |
170 |
|
остается маленьк й запас прочности (40%). Отношение предельного |
||||||
напряжения к максимальноидопускаемому в эксплуатации (оно пи- |
||||||
шется в квадратных скобках |
[σ] и называется допускаемым) опреде- |
|||||
ляет коэффициент запаса прочности КЗ |
|
|
||||
С |
|
КЗ = |
σТ . |
|
(2.1) |
|
|
|
|
|
[σ] |
|
|
В нашем случае КЗ = 1,4.
Вывод можно сделать такой: следует изготовить деталь из более прочной стали (рис.15), например, Ст 45 (σТ1 =340 МПа). Тогда
коэффициент запаса будет равен КЗ = 340/170 = 2. Графическое выражение сказанному представлено на рис.15.
21
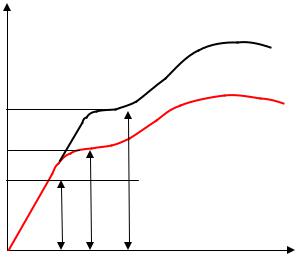
|
σ мПа |
|
|
|
Ст 45 |
|
|
|
|
|
|
|
340 |
|
|
|
Ст 15 |
|
240 |
|
|
|
|
|
170 |
|
σТ1 |
|
|
|
|
[σ]σТ |
|
|
|
|
0 |
|
|
|
ε |
|
Рис. 15. Увеличение коэффициента запаса прочности |
||||
|
|
|
|
Д |
|
|
Представленные выше характеристики напряжений характерны |
||||
для упругопластических материалов, к которым относятся большин- |
|||||
|
|
А |
Ии малолегированных ста- |
||
ство среднеуглеродистых нелегированных |
|||||
лей. |
|
б |
|
|
|
|
У хрупких – зона текучести практически отсутствует (рис.16). |
||||
Эти материалы работают в линейной зоне до разрушения, то есть до |
|||||
предела прочности. Поэтому коэффициент запаса прочности у таких |
|||||
материалов определяется по пределу прочности |
|||||
|
С |
Кз = |
σВ |
|
|
|
[σ]. |
|
(2.2) |
||
|
Выражение (2.1)иили (2.2) является основополагающим. |
||||
1. Задав коэффициент запаса прочности КЗ |
и материал σТ (σВ ), мож- |
||||
но определить размеры детали, входящие в формулу допускаемого |
|||||
напряжения [σ]. |
|
|
|
|
2.Задав коэффициент запаса прочности КЗ и рассчитав допускаемое напряжение [σ], можно подобрать по таблице материал σТ (σВ ).
3.Задав материал σТ (σВ ) и размеры детали, входящие в формулу до- [σ], определить, с каким коэффициентом за-
паса КЗ будет работать деталь.
К хрупким материалам относятся чугуны, высокоуглеродистые нелегированные и легированные стали с упрочнением (закалка, цементация, азотирование).
Графически в этом случае будет, как на рис.16.
22

σ |
|
|
|
|
σВ |
|
|
|
|
[σ] |
|
|
|
КЗ≈2,3 |
0 |
|
|
|
ε |
|
|
|
|
|
Рис. 16. Диаграмма для хрупких металлов |
||||
У пластических материалов, наоборот, зона текучести распро- |
||||
|
|
|
|
И |
страняется практически на всю характеристику и поэтому из предель- |
||||
ных напряжений также выделен только предел прочности (рис.17). |
||||
|
|
|
Д |
|
К пластическим материалам относятся малоуглеродистые не- |
||||
легированные стали и цветные металлы. |
|
|||
σ |
|
А |
|
|
б |
|
|
||
σВ |
|
|
||
и |
|
|
|
|
С |
|
|
|
|
[σ] |
|
|
|
|
|
|
|
|
КЗ≈1,64 |
0 |
|
|
|
ε |
|
|
|
|
|
Рис. 17. Диаграмма для мягких металлов |
23