
Тонкопленочные солнечные элементы
.pdf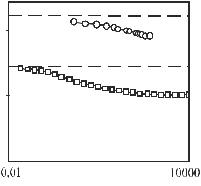
правило, максимальный стабилизированный КПД одинарного СЭ получают при толщине i-слоя 200 нм. Однако это уменьшает и оптическое поглоще-
ние структуры. В связи с этим необходимо применять отражающие слои на тыльной стороне и каскадную структуру солнечного элемента. Использование каскадныхструктур дает, с однойстороны, возможность уменьшения толщины
отдельных p–i–n-элементов и, таким обра- |
|
10 |
|
|
|
|
|
|
|
|
|
|
|
|
|
|
|
|
|
|
|
|
|
|
|
|
|
|||
зом, обеспечивает большую стабильность, |
|
|
|
|
|
|
|
|
|
|
|
|
|
|
|
|
|
|
|
|
|
|
|
|
|
|
||||
|
2 |
|
|
|
|
|
|
|
|
|
|
|
|
|
|
|
|
|
|
|
|
|
|
|
|
|
|
|
|
|
|
|
|
|
|
|
|
|
|
|
|
|
|
|
|
|
|
|
|
|
|
|
|
|
|
|
|
|
|
||
|
2 |
|
|
|
|
|
|
|
|
|
|
|
|
|
|
|
|
|
|
|
|
|
|
|
|
|
|
|
|
|
а с другой стороны — высокое значение эф- |
/мВтсм/см |
|
|
|
|
|
|
|
|
|
|
|
|
|
|
|
|
|
|
|
|
|
|
|
|
|
|
|
|
|
|
|
|
|
|
|
|
|
|
|
|
|
Трехкаскад СЭ |
|
|||||||||||||||||
|
|
|
|
|
|
|
|
|
|
|
|
|
||||||||||||||||||
|
|
|
|
|
|
|
|
|
|
|
Трехкаскадный |
СЭ |
|
|||||||||||||||||
фективности за счет большой толщины всей |
,МощностьМощность, |
|
|
|
|
|
|
|
|
|
|
|
|
|
|
|
|
|
|
|
|
|
|
|
|
|
|
|
|
|
структуры. Необходимо также иметь в виду, |
|
5 |
|
|
|
|
|
|
|
|
|
|
|
|
|
|
|
|
|
|
|
|
|
|
|
|
|
|||
|
|
|
|
|
|
|
|
|
|
|
Однокаскадный |
Э |
|
|||||||||||||||||
|
|
|
|
|
|
|
|
|
|
|
|
|
|
|||||||||||||||||
что согласование токов в каскадных СЭ |
|
|
|
|
|
|
|
|
|
|
|
ОднокаскадныйСЭ |
|
|||||||||||||||||
|
|
|
|
|
|
|
|
|
|
|
|
|
|
|
|
|
|
|
|
|
|
|
|
|
|
|
|
|
||
предполагает минимальную толщину i-слоя |
|
|
|
|
|
|
|
|
|
|
|
|
|
|
|
|
|
|
|
|
|
|
|
|
|
|
|
|
||
|
0 |
|
|
|
|
|
|
|
|
|
|
|
|
|
|
|
|
|
|
|
|
|
|
|
|
|
||||
|
|
|
|
|
|
|
|
|
|
|
|
|
|
|
|
|
|
|
|
|
||||||||||
в верхней p–i–n-структуре. Как отмечалось |
|
|
|
0,01 |
|
0,1 |
|
1 |
|
10 |
|
100 |
|
1000 |
|
10000 |
||||||||||||||
|
|
|
|
|
|
|
|
|
||||||||||||||||||||||
|
|
|
|
|
|
|
|
|
||||||||||||||||||||||
|
|
|
|
|
|
|
|
|
|
|
Время |
|
освещения |
|
, час |
|
|
|
|
|||||||||||
|
|
|
|
|
|
|
|
|
|
|
|
|
|
|||||||||||||||||
ранее, в этом случае и деградация этого |
|
|
|
|
|
|
|
|
|
Время освещения, ч |
|
|
||||||||||||||||||
|
|
|
|
|
|
Рис. 8.2. Зависимость |
||||||||||||||||||||||||
p–i–n-элемента будет минимальной. В то же |
|
|
|
|
|
|
||||||||||||||||||||||||
вырабатываемой СЭ мощности |
||||||||||||||||||||||||||||||
время эта p–i–n-структура является фильт- |
||||||||||||||||||||||||||||||
|
|
|
|
от времени эксплуатации |
ром для нижележащих структур, отсекающим часть падающего излучения. Снижение интенсивности падающего на нижние p–i–n-элементы излучения,
в свою очередь, уменьшает деградацию этих элементов. Зависимость вырабатываемой СЭ мощности от времени (рис. 8.2) эксплуатации показывает,
что после 1000 ч освещения вырабатываемая солнечным элементом с одним p–n-переходом мощность снижается на 30 %, а для СЭ с тремя переходами снижение составляет 15 %.
Применение структур на основе a-Si:H/c-Si открывает широкие воз-
можности для повышения стабильности СБ. В таких гетероструктурах практически отсутствует деградация свойств с течением времени под ос-
вещением, что является перспективным с точки зрения их использования не только для наземных, но и космических целей.
131
9. ПРОИЗВОДСТВО МОДУЛЕЙ СЭ НА ОСНОВЕ
НЕУПОРЯДОЧЕННЫХ ПОЛУПРОВОДНИКОВ
Характеристики промышленно выпускаемых модулей, как правило, ху-
же СЭ, получаемых в лабораториях. Это связано, прежде всего, с тем, что СЭ, получаемые в лабораториях, имеют меньшие площади, более высокое качест-
во TCO, полупроводников, высокую однородность слоев, низкие потери при герметизации, затенении, шунтах.
9.1. Рулонная технология изготовления модулей СЭ
При переходе от научно-исследовательских и опытно-конструкторских работ к крупномасштабному поточному производству ключевыми момента-
ми являются однородность осаждения на больших площадях, скорость осаждения, используемые газы, выход годных, воспроизводимость, возмож-
ность автоматизации. Примером поточного производства СЭ на подложке из нержавеющей стали является рулонная технология, разработанная в Energy Conversion Devices, Inc. (ECD).
Суть технологии заключается в том, что формирование СЭ осуществ-
ляется на стальной лист, который до начала процесса свернут в рулон, во время процессов постепенно разворачивается на входе в установку, а после окончания сворачивается на выходе из нее. Стальной лист имеет толщину 125 мкм, ширину 0,35 м и длину 750 м. Производство можно разделить на две части: осаждение и сборка.
Осаждение, в свою очередь, состоит из четырех этапов, в каждом из которых задействованы рулонные установки:
1)очистка подложки;
2)осаждение заднего отражающего слоя;
3)осаждение a-Si:H и с-Si:H;
4)осаждение верхнего слоя ITO.
Установка для очистки включает модуль для ультразвуковой отмывки в специальных моющих растворах, обработку щетками, ванны с деионизованной водой, камеру для инфракрасной сушки. Очищенный стальной лист скручивается на выходе вместе с защитным листом. Далее стальной лист протягивается через несколько модулей с магнетронами при постоянном токе для осаждения Al или Ag слоев в качестве отражателя и ZnO в качестве буферного слоя. Осаждение осуществляется на нагретую подложку, что обеспечивает формирование текстурированных слоев для усиления отражения
132
света. Далее рулон подается в установку для ВЧ ПХО (осаждения девяти слоев) для формирования структуры n–i–p/n–i–p/n–i–p (температура осаждения
250–300 С), а также буферных слоев с обоих сторон слоя a-SiGe:H. Осаждение всех слоев производится последовательно, но за один проход рулона. Для уменьшения дефектов в пленке за счет попадания частиц нанесение слоев осуществляется снизу. Скорость подачи стального листа составляет
30 см/мин. Камеры изолируются друг от друга динамически с помощью газового затвора для предотвращения загрязнения, однако при этом стальной лист непрерывно движется. После осаждения полупроводниковой структуры рулон загружается в установку для нанесения слоя TCO. Используется либо реактивное испарение индия в атмосфере кислорода, либо распыление мишени оксид индия–оксид олова в атмосфере Ar.
Вторая часть производства — сборка — включает следующие этапы. Вначале рулон со сформированной структурой солнечного элемента разре-
зается на отдельные листы необходимого размера. Далее по периметру листа наносится травящая паста, которая активируется в конвейерной печи для удаления ITO. Выбранные образцы проходят контроль качества. Затем СЭ поступают на операцию устранения шунтов. Для этой цели в электроли-
те производят окисление TCO до диэлектрика в области образования шунта. Изготовление СЭ завершается формированием проводящей сетки с помо-
щью углеродной пасты или медного провода, покрытого углеродной пастой. Отдельные солнечные элементы соединяются между собой, изготавливают модули, которые покрывают прозрачным герметизирующим слоем этилвенилэтилена и устанавливают на несущие конструкции.
Рулонное производство является крупномасштабным и при этом простым и гибким. Стальной лист со сформированной структурой СЭ может быть разрезан на любые размеры от малых, необходимых, например, для зарядных устройств, до больших, предназначенных для установки на крышах зданий. Стабилизированный КПД модулей, получаемых по этой технологии, составляет 8 %. Вместо стального листа может использоваться гибкая кап-
тоновая подложка.
Важным аспектом производства солнечных батарей на основе a-Si:H
является соблюдение техники безопасности. Несмотря на то, что в конечном продукте нет токсичных веществ, в производственном процессе ис-
пользуются токсичные, огнеопасные и взрывоопасные газы — моногерман, фосфин, триметилбор, моносилан, водород и т. д.
133

9.2. Изготовление модулей СЭ на стеклянной подложке
Для промышленного производства модулей из СЭ на основе аморфных полупроводников могут использоваться стеклянные подложки (тол-
щина 3 мм, ширина 0,5 м, длина 1 м), на которые наносится текстурированный слой TCO (SnO2) с помощью химического осаждения из газовой фазы при атмосферном давлении. После этого слой TCO скрайбируется на полосы шириной порядка 9 мм, и подложки загружаются в установку плазмохими-
ческого осаждения для нанесения слоев полупроводников (шесть слоев для формирования структуры p–i–n/p–i–n в случае тандемного солнечного эле-
мента a-Si:H/a-SiGe:H). Далее осаждается буферный слой ZnO и проводится следующее лазерное скрайбирование вблизи линий первого скрайбирования.
Свет
Стекло SnOSnO2
a-S:Hi/a-SiGe:H
ЭВЭЭВЭ
Стекло Контакт
Солнечный фотоэлемент на стеклянной подложке
При этом мощность лазера подбирается таким образом, чтобы удалялись слои ZnO и полупроводников, но оставался слой SnO2. Далее осаждается Al
в качестве заднего отражающего и контактного слоя и проводится третье скрайбирование вблизи второго, завершающее последовательное соединение соседних элементов на подложке, которое позволяет снизить потери на сопротивлении за счет увеличения выходного напряжения и уменьшения тока СЭ. Формирование соединения отдельных элементов проще осуществлять на стеклянной подложке, чем на стальной. Четвертое лазерное скрайбирование по периметру изолирует активную область от краев подложки. Формирование панели заканчивается спайкой с другой стеклянной пластиной с помощью этилвенилэтилена (ЭВЭ) как показано на рисунке.
9.3. СЭ на гибкой основе
Интересным с практической точки зрения является формирование фо-
тоэлектрических преобразователей на гибкой основе. Такие СЭ имеют существенно меньший вес, чем обычные, и легко монтируются фактически на любой поверхности. Они могут повторять поверхность зданий и крыш, а благодаря малому весу отпадает необходимость в усилении несущих кон-
134
струкций. Подобная технология может найти применение при создании специальной ткани со сформированным фотоэлектрическим преобразователем, которая может быть использована при изготовлении парусов, одеж-
ды. Из такого материала можно изготавливать сумки и чехлы, например, для сотовых телефонов, плееров и т. д.
Большой интерес к подобной технологии проявляют представители военной прмышленности. В современных условиях в армии используется ог-
ромное количество электронных устройств, каждое из которых требует обеспечения электричеством. Использование СЭ позволяет решить эту проблему.
Легкие солнечные элементы на гибкой основе могут быть расположены на крыше тентов, на рюкзаках, из них может быть изготовлена даже униформа.
В настоящее время разрабатывается технология, предусматривающая использование в качестве основы пластиковой подложки, а в качестве ра-
бочего слоя — аморфного полупроводника. На обе стороны гибкой пластиковой подложки наносятся слои металлов, один из которых — металличе-
ский электрод, а другой — задний электрод. Эти слои предотвращают газовыделение из подложки и предохраняют слои полупроводников от деграда-
ции. Слои на основе a-Si:H осаждаются на металлический электрод, после чего наносится слой прозрачного проводящего электрода на основе оксидов индия и олова. В сформированных СЭ имеются два типа отверстий: одни обеспечивают электрический контакт между прозрачным проводящим элек-
тродом и задним электродом, а другие — между металлическим и задним электродами. ITO имеет относительно высокое удельное сопротивление, что приводит к увеличению последовательного сопротивления СЭ. Первый тип отверстий позволяет снизить это сопротивление и увеличить эффективность сбора носителей. Лазерное скрайбирование по обеим сторонам подложки дает возможность сформировать отдельные элементы, последовательно соеди-
ненные между собой. По такой технологии были сформированы модули на гибкой подложке размером 40 80 см2 на основе тандемных СЭ с i-слоями из a-Si:H. Выходное напряжение модуля составило 200 В, КПД — 10,5 %.
Формирование подобных СЭ возможно с использованием рулонной технологии.
Оригинальная технология изготовления гибких фотоэлектрических преобразователей предложена канадской компанией «Spheral Solar» (Cambridge, Ontario). Основу таких солнечных элементов составляет множество кремниевых бусинок, расположенных между двумя тонкими пленками алюминие-
135
вой фольги, запечатываемых в пластик. Каждая отдельная бусинка пред-
ставляет собой крошечный СЭ, поглощающий солнечный свет и преобразующий его в электричество. Слои алюминиевой фольги придают всей структуре необходимую прочность и служат электрическими контактами.
Для изготовления бусинок используется кремний из отходов электрон-
ной промышленности. Его расплавляют и кристаллизуют в сферы диаметром примерно один миллиметр. Далее кремниевые сферы легируются бором для получения p-типа проводимости, а в приповерхностный слой проводится диффузия фосфора, в результате чего формируется p–n-переход.
Изготовленные таким образом кремниевые шарики помещаются на перфорированный лист алюминия, который создает контакт с поверхностью,
имеющей n-тип проводимости. Далее некоторая часть поверхности сферы стравливается до ядра р-типа проводимости. Второй слой алюминиевой фольги создает контакт к ядру р-типа. После этого вся структура герметизируется с помощью пластика. Неровная поверхность сфер позволяет увели-
чить площадь, поглощающую свет. Для фотоэлектрического преобразователя с подобной структурой получено значение КПД = 11 %, что сравнимо с эф-
фективностью преобразования обычных СЭ и значительно превосходит КПД изготавливаемых в настоящее время солнечных элементов на гибкой основе. Такой материал можно размещать на поверхности любой формы и покрывать любые строения и конструкции.
136

10. ТОНКОПЛЕНОЧНЫЕ СОЛНЕЧНЫЕ МОДУЛИ
НА ОСНОВЕ АМОРФНОГО И МИКРОКРИСТАЛЛИЧЕСКОГО
КРЕМНИЯ ПО ТЕХНОЛОГИИ И НА ОБОРУДОВАНИИ
ФИРМЫ «OERLIKON SOLAR»
Как уже отмечалось во введении, проблемой традиционной солнечной фотоэнергетики является высокая стоимость монокристаллических кремниевых солнечных батарей — основного материала на рынке солнечной энергетики.
Стоимость СБ их эффективность влияют на стоимость электроэнергии,
вырабатываемой солнечными электростанциями. Соотношение стоимости «солнечной» и «сетевой» электроэнергии определяет географию экономиче-
ски эффективной эксплуатации солнечных электростанций в странах с развитыми электросетями. Именно превышение стоимости «солнечной» электроэнергии над «сетевой» (без учёта специальных стимулирующих тарифов для возобновляемой энергетики) в развитых странах сдерживает активное распространение солнечной энергетики. Решить задачу удешевления «сол-
нечной» электроэнергии возможно путём если перейти на более дешевые тонкопленочные технологии изготовления солнечных элементов.
|
|
|
|
|
|
|
|
c-Si (average CE) |
c-Si |
|||
|
|
|
|
|
|
|
||||||
|
|
|
|
|
|
|
|
|
|
|
|
• основная технология получения СЭ (первое поколение) |
$3.50 |
|
|
|
|
|
|
|
c-Si (hi CE / low |
cost) |
|||
|
|
|
|
|
|
|
||||||
|
|
|
|
|
|
|
||||||
|
|
|
|
|
|
|
|
|
|
|
|
• высокая стоимость производства солнечных модулей |
|
|
|
|
|
|
|
|
c-Si (high CE) |
|
|
||
$3.00 |
|
|
|
|
|
|
|
|
• в перспективе займет свою нишу применения |
|||
|
|
|
|
|
|
|
uc-Si |
|
|
|||
|
|
|
|
|
|
|
|
|
a-Si и mc-Si |
|||
|
|
|
|
|
|
|
|
a-Si |
|
|
||
$2.50 |
|
|
|
|
|
|
|
CIGS |
|
|
• начало производства (второе поколение) |
|
|
|
|
|
|
|
|
||||||
|
|
|
|
|
||||||||
|
|
|
|
|
|
|
• низкая стоимость при производстве солнечных модулей |
|||||
$2.00 |
|
|
|
|
|
|
|
CdTe |
|
|
||
|
|
|
|
|
|
|
|
|
CuInSe2/Cu (In1−xGax)Se2 |
|||
|
|
|
|
|
|
|
|
|
|
$1.50 |
• находится на стадии внедрения в производство |
• наилучший материал для СЭ на гибкой подложке |
|
$1.00 |
• недостаток-дефицит In |
CdTe |
|
$0.50 |
• возможность использования простых методов |
получения, пригодных для промышленного внедрения |
|
$0.00 |
• выпускается в ограниченных объемах |
• недостаток-токсичность Сd, и ограниченность ресурсов |
|
2006 2008 2010 2012 2014 2016 |
Cd и Te в мире |
Рис. 10.1. Стоимость 1 Вт энергии в солнечном модуле, получаемая при использовании различных материалов
Перспективным путём решения этих проблем является применение гете-
роструктурных каскадных фотоэлектрических преобразователей на основе аморфногогидрогенизированногокремния исплавов на его основе(рис. 10.1).
137
Открытие в 1976 г. возможности легирования аморфного кремния a-Si:H, полученного в плазме тлеющего разряда, положило начало использованию его исключительных фотопроводимых свойств, связанных с сильным поглощением в области длин волн, соответствующих видимой части спектра. Открытие технологических путей получения тонких пленок этого материала и других аморфных гидрогенизированных полупроводников дало мощный толчок развитию новой, крайне необходимой технологии в области возобновляемой энергетики — технологии создания дешевыхсолнечныхэлементов.
Объем рынка солнечных элементов на сегодняшний день составляет порядка 1 ГВт. На долю тонкопленочных солнечных элементов приходится 15% и наблюдается более быстрый рост в этом сегменте рынка, что прежде всего связано с решением основной проблемы стоящей перед технологами — повышение эффективности преобразователей солнечной энергии и снижения стоимости солнечных модулей. Возьмем для сравнения кристаллический кремний — основной материал современной солнечной энергетики, понимая, что его стоимость определяет энергозатратный процесс получения этого материала и его долю в самом солнечном элементе. При таком подходе трудно ожидать снижение удельной стоимости солнечных модулей менее 2,5 дол./Вт.
Эволюция основных технологических принципов производства тонкопленочных кремниевых элементов (низкозатратные технологические процессы, дешевые подложки, другой дизайн модулей и т.д) уже сегодня обеспечивает в лабораторных условиях эффективность сравнимую с элементами на основе поликристаллического кремния, а темпы снижения себестоимости тонкопленочных солнечных модулей значительно выше, чем модулей на основе кристаллического кремния [7]. В настоящее время реальной задачей тонкопленочной фотовольтаики является достижение цены порядка 0,5–0,65 дол./Вт. Использование таких материалов как аморфный карбид кремния a-Si:C, аморфных кремнийгерманиевых сплавов a-SiGe:H, наноструктурированного и микрокристаллического кремния вместе с успехами в технологии управления типом их проводимости и созданием p–n-переходов на основе новых структур позволяет снять некоторые фундаментальные ограничения, связанные с оптическими и электрофизическими свойствами прежнихматериалов, и открывают возможность решения проблем обусловленных увеличением эффективности солнечныхэлементов при одновременномснижении ихстоимости.
По прогнозам экспертов к 2030 г. солнечная фотоэнергетика превратится в большой экономический сектор во всем мире. В Европе фотоволь-
таика станет мощной индустрией со значительным экспортным потенциа-
138
лом. Предполагается, что в ЕС появится от 200 до 400 тыс. рабочих мест
при годовом производстве 20–30 ГВт.
10.1. Сравнительный анализ существующих на сегодняшний день
тонкопленочных технологий для преобразования
солнечной энергии в электроэнергию
В связи с тем, что основной материал солнечной энергетики — кремний — непрямозонный полупроводник и его коэффициент поглощения не-
высок, для эффективного поглощения солнечного света толщина изготавливаемых солнечных элементов должна составлять сотни микрон. Это оп-
ределяет наряду с затратным процессом получения кремния и его значительный расход, а значит, и высокую стоимость солнечных модулей. Значи-
тельно снизить расход используемого материала и его стоимость позволяет применение тонкопленочной технологии на основе материалов с высоким коэффициентом поглощения таких, как: CdTe,Cu(In,Ga)Se, которые приме-
няются в виде поликристаллических пленок. К числу этих материалов относится и аморфный гидрогенизированный кремний. Но прежде чем оста-
новиться на изложении технологии получения солнечных модулей на его основе, рассмотрим их достоинства и недостатки.
Тонкопленочная нанотехнология CdTe. В Европе в этой области очень активна одна компания («First Solar», www.firstsolar.com).
Преимущества:
• Высокий стабильный КПД (производственная эффективность солнеч-
ного модуля порядка 10 %).
•Небольшие производственные издержки, результатом чего является очень низкая стоимость солнечных модулей.
Недостатки:
•Большая трудность контроля и воспроизведения процессов (низкий выход). Одновременно приходится контролировать два компонента — Cd и
Te, а также их надлежащий состав.
•Теллур Te: редкоземельный металл, примерно в десять раз более редкий, чем In. Существует проблема гарантии поставок.
•Кадмий Cd: тяжелый металл. Необходимо учитывать аспекты окружающей среды. СЭ в конце срока их службы необходимо специально утилизировать на свалках тяжелых металлов (дорогостоящая конечная процедура возврата и переработки СЭ, при которой затраты должен будет
139
принимать на себя изготовитель данных модулей). Ситуация выхода из строя СЭ в процессе эксплуатации: при разбитии стекла Cd может абсорбироваться и загрязнить почву. Таким образом, требуются дополнительные дорогостоящие затраты на монтаж модулей.
• Полосовая конструкция модуля на единой подложке затрудняет обеспечение зазоров между отдельными полосами.
Тонкопленочная технология диселинида меди и индия CuInSe2 (CIS) и Cu(In1–xGax)Se2 (CIGS) В этой областиработают примерно 20 компаний (в ос-
новном немецкие и из США). Пример — «Würth Solar» (www.wuerthsolar.com) или же«Avancis»(www.avancis.com).
Преимущества:
•Высокий стабильный КПД (производственная эффективность модуля порядка 11–13 %).
•Технология получения слоев CuInSe2 проста и заключается в последо-
вательном осаждении термическим испарением тонких слоев Ga, Se и Cu на поверхность подложки и последующего быстрого термического отжига.
Недостатки:
•Чрезвычайная трудность контроля и воспроизведения процессов (низкий выход годных элементов).
•Необходимость тщательного проектирование полос и зазоров в модуле, которое трудно воспроизвести.
Высокотемпературный процесс осаждения. Для формирования CIS и CIGS используется целый ряд методов (испарение, распыление, газовый транспорт, пульверизация с последующим пиролизом, электрохимическое осаждение, трафаретная печать), которые можно разделить по методу селинизации:
•методов, в которых Se вносится в слой одновременно с другими элементами соединения;
•методов, в которых взаимодействие с Se производится в результате осаждения слоев других элементов соединенения.
В том и другом случае используется либо осаждение на подложку, нагретую до температуры 400–500 °С, либо отжиг сформированного слоя при этих температурах. В ходе реакции образуется слойCIS толщиной 1,5–2 мм.
•Индий и галлий: редкоземельные металлы. Для производства тонко-
пленочных солнечных элементов CIS, способных генерировать 1 ГВт электроэнергии, требуется приблизительно 50 метрических тонн индия. Гарантиро-
ванные ресурсы поставки индия порядка 2400 т. Проблема гарантиипоставок.
140