
Детали машин и основы конструктирования
.pdf
71
ской статистики установлено, что среднее значение результатов наблюдения х имеет в n раз меньшую дисперсию, чем дисперсия результата наблюдения. Поэтому за результат измерения принимается средний размер результатов наблюдений
х = (Σхi)/n.
Каждый результат наблюдения будет иметь случайную погрешность относительно сред-
него размера хi – х. Стандартной оценкой случайной погрешности является среднее квадратическое отклонение
Sx = |
∑(xi − x)2 |
. |
|
n −1 |
|||
|
|
Значения х при повторении n кратных измерений будут изменяться. Значит, результат измерения будет иметь среднее квадратичное отклонение
Sx = Snx .
Случайная погрешность результата измерения оценивается доверительным интервалом, определяемым некоторым числом (tрк ) средних квадратических отклонений ( Sx )
∆сл = ±tрк |
Sx |
|
n |
||
|
tрк называют коэффициентом Стьюдента, который зависит от доверительной вероятности Р и числа степеней свободы k=n–1.
Ряд значений tрк для доверительной вероятности Р=0,95 приведен в следующей таблице. Обычно число измерений не превышает 7.
n-1 |
1 |
2 |
3 |
4 |
5 |
6 |
9 |
20 |
50 |
∞ |
tрк |
12,7 |
4,30 |
3,18 |
2,78 |
2,57 |
2,45 |
2,26 |
2,09 |
2,01 |
1,96 |
Результат измерения записывается следующим образом
L = Lд + θ ±tрк Snx , Р=0,95, n=…
Например, L = (32,987±0,002) мм при Р=0,95, n=5 означает, что действительный размер получен на основании 5 наблюдений, равен 32,987 мм, а случайная погрешность с доверительной вероятностью 95% не будет больше 2 мкм. С вероятностью 5% она может превысить это значение.
Условие годности размера.
Условие годности действительного размера при контроле нормированного размера определяется следующим неравенством
dmin ≤ Lд ≤ dmax ,
где dmin , dmax – наибольший и наименьший предельные размеры, задающие допуск разме-
ра.
Так как Lд содержит погрешность, то при контроле возможны ошибки: 1-го рода – бракование в действительности годной детали, 2-го рода – приемка негодной, не соответствующей условию годности.
Рассмотрим пример: контролируется валик 40-0,1 (dmin=39,9 и dmax =40,0) штангенциркулем с погрешностью 0,05 мм.
Первый случай. Пусть размер изготовлен 40,00 мм и, следовательно, должен быть «годен». При измерении получили Lд = 40,05 (∆и = +0,05, погрешность штангенциркуля «увеличила» размер детали) и деталь будет забракована, так как Lд > dmax .
Второй случай. Деталь изготовлена с размером 39,85 мм, т.е. дефектная (брак неисправимый). При измерении получили Lд = 39,9 (∆и = +0,05) и деталь будет принята.
72
Таких ошибок при контроле партии размеров с допуском Т=0,1 с погрешностью измерения ∆и = 0,05 может быть много. В результате контроля в ящике с «годными» деталями будут лежать и детали «негодные», а в ящике «брак» часть деталей окажется годными, если их проверить более точным средством измерения.
Изделие, у которого хотя бы один параметр не соответствует заданным, называют дефектным (браком, бракованным изделием). При этом брак подразделяется на исправимый и неисправимый (окончательный). К исправимому браку относят изделия, технически допускающие исправление дефекта. Если устранить дефекты технически невозможно, то такое изделие относят к неисправимому браку.
Так, если диаметр реального вала (рис.1) будет больше наибольшего предельного размера, то такой вал при контроле будет забракован. Однако очевидно, что этот вал допускает доработку (обточку, дошлифовку), т.е. уменьшение диаметра до требуемых значений. Следовательно, этот брак является исправимым.
Если же диаметр вала будет меньше наименьшего предельного размера, то обычной доработкой его не увеличить. Следовательно, такой брак – неисправимый.
Контроль абсолютно всех параметров изделия и всей технической системы в целом очень затруднен и не всегда нужен. Поэтому понятие брака чаще трактуют с функциональноэкономических позиций:
•бракованным считается изделие, у которого хотя бы один функционально важный действительный параметр не соответствует заданному параметру. Помимо функциональных могут отслеживаться некоторые вспомогательные параметры, существенно влияющие на потребительские свойства изделия;
•если исправить дефект экономически нецелесообразно, т.е. расходы по исправлению будут превышать потери от брака, то такой брак считают неисправимым.
Спонятием годности связано с понятие точности, т.е. степени соответствия полученных результатов потребным. Чем выше задается точность нормируемых параметров, тем сложнее создать удовлетворяющее им годное изделие. А чем выше оказывается точность действительных параметров, тем проще изготовить годное изделие.
Изделие может иметь точные параметры, но при этом быть негодным, если заключения о точности и годности проводятся для разных групп параметров.
7.4 Геометрические параметры технических систем
Понятие “геометрический параметр” включает не только количественные характеристики (размеры), но и форму поверхностей и профилей, взаимное расположение поверхностей и осей. Эти параметры, как и всякие другие, могут выступать в виде номинальных, нормированных и действительных.
Для удобства геометрические параметры разбиты на группы. Принцип их разбиения можно пояснить посредством гармонического анализа.
Допустим, нужно изготовить цилиндрический вал. Номинальный профиль его сечения – правильная окружность. Но после изготовления реальный профиль будет иметь вид неровной замкнутой кривой, причем, если посмотреть на нее под увеличением, то увидим еще более изломанную линию. Функцию отклонения радиуса реального профиля Rдейст.= f (ϕ) от номиналь-
ного профиля ∆R = Rдейст. – Rном. = f (ϕ) можно разложить в ряд Фурье по угловой координате ϕ. Сопоставление отдельных гармонических составляющих позволяет ввести следующую классификацию геометрических параметров и их отклонений:
•гармоника нулевого порядка характеризует отклонение размера. Ей соответствует нулевой член ряда, являющийся средним значением функции отклонений за период. Для вала – это разность среднего действительного и номинального радиусов;
•гармоника первого порядка характеризует отклонение расположения поверхностей. Это – эксцентриситет, т.е. смещение расположения геометрического центра действительного
73
профиля по отношению к центру номинального профиля;
•гармоники со второго по седьмой порядок характеризуют отклонения формы. Для поперечного сечения вала они соответствуют его отклонению от круглости: овальность (второй член ряда Фурье), огранка (третий, четвертый и др. члены ряда);
•гармоники восьмого и больших порядков характеризуют волнистость поверхности;
•гармоники высоких частот характеризуют шероховатость поверхности.
Волнистость поверхности занимает промежуточное положение между отклонениями формы и шероховатостью. Часто ее отдельно не рассматривают, а соответствующие ей отклонения распределяют между этими характеристиками.
Витоге, геометрическая точность деталей определяется следующими признаками:
•точность размера элемента поверхности (линейные и угловые),
•точность расположения поверхностей или осей,
•точность формы поверхности элемента,
•волнистость поверхности,
•шероховатость поверхности.
Нормирование точности линейных размеров.
Численные значения отклонений размеров регламентируются международной системой допусков и посадок ISO. На ее основе созданы отечественные стандарты на отклонения линейных размеров и угловые размеры. Применение стандартных отклонений и размеров повышает конкурентоспособность изделий, в том числе их технологичность и ремонтопригодность, улучшает читаемость документации. Но в особых случаях допустимо отступление от требований стандартов:
•если для требуемых отклонений (например, из условия наилучшего функционирования) невозможно подобрать стандартный допуск, а изменить их нельзя;
•при отсутствии необходимого инструмента или оборудования;
•детали и узлы изготавливаются в единичных экземплярах, с применением пригоночных операций.
Отклонения размеров.
Согласно стандартам размеры указывают в виде номинального значения и предельных от него отклонений. Отметим, что в машиностроении линейные размеры и их отклонения приводятся в миллиметрах, и в этом случае их размерность не указывается и определяется по умолчанию. Номинальные величины размеров рекомендуют выбирать из рядов нормальных линейных значений и углов.
Линейные размеры, по способу измерения, разбиты на три группы:
•наружные размеры (охватываемые) элементов деталей. Контрольно-измерительный инструмент контактирует с такими элементами снаружи. Наружные размеры обозначают строчными буквами, например, d (от слова dimension). На такие элементы в ИСО установлен термин “вал”;
•внутренние размеры (охватывающие) элементов деталей. Они охватывают рабочие поверхности измерительного инструмента. Внутренние размеры обозначают прописными буквами, например, D. На такие элементы в ИСО установлен термин “отверстие”;
•размеры элементов деталей, не относящиеся ни к наружным, ни к внутренним. Это – так называемые прочие элементы поверхностей.
Вдальнейшем элементы типа “вал” или “отверстие” будем называть просто валами или отверстиями.
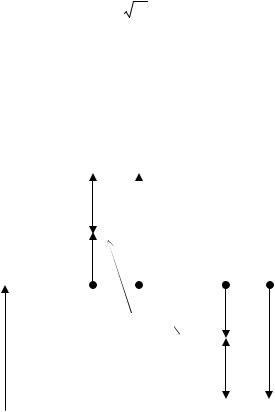
74
Стандартами устанавливаются следующие числовые значения отклонений и определяемые ими положения допусков (поля допусков):
-для угловых размеров - симметричные, например, 30° ± 20′. Форма записи отклонений – численная,
-для линейных размеров - 21 вариант положений. Форма записи отклонений допускается численная и посредством условного обозначения (за исключением размеров прочих элементов поверхностей). Запись отклонений посредством условного обозначения (шифром) включает латинскую букву и целое число.
Из предельных отклонений одно является основным, его значение задается стандартом, а другое определяется значением допуска IT, зависящего от размера и точности изготовления
(рис. 7. 4).
На рис. 7.5, 7.6 показаны расположение стандартных основных отклонений и их обозначение для отверстий и валов. Все поля допусков упорядочено расположены относительно номинального значения, и каждому положению соответствует своя буква основного отклонения.
Цепочка полей (A...ZC – для отверстий, a...zc – для валов) условно начинается в “теле” детали, т.е. выше линии номинального размера (иначе называемая “нулевой линией”) для отверстия и ниже – для вала, а заканчивается за пределами детали. Двойными буквами, например, cd и CD, обозначены дополнительно введенные для нужд часовой промышленности и ряда других отраслей по шесть промежуточных расположений.
Номинальные размеры в стандартах разбиты на интервалы. Для каждого из них задано значение основного отклонения – нижнего предельного отклонения для полей допусков A...H
иk...zc и верхнего предельного отклонения для полей допусков K...ZC и a...h (для основных отклонений K, M, N это значение при различных квалитетах может меняться).
Стандартом установлено десять степеней точности на угловые размеры (1...10) и двадцать
– на линейные (01, 0, 1, 2,..., 18). Число, обозначающее степень точности линейного размера, называется квалитетом. Чем выше квалитет, тем грубее выполнен размер, больше его допуск
ирассеяние действительных значений размеров (рис.7), но стоимость изготовления – ниже. Для квалитетов 5-17 размер допуска Т определяется через число единиц допуска k и еди-
ницу допуска i (мкм), т.е. T=k·i, где i = 0.453 D + 0.001D , где D (мм) – среднее геометрическое между крайними значениями диапазона размеров, имеющих одинаковый допуск, а стандартные величины чисел единиц допуска k приведены на рис.7.
Таким образом, в условном обозначении полей допусков буква характеризует положение поля допуска, а квалитет (также как и номинальный размер) – точность (величину допуска). Например, 50n6, 90H8. Числовые значения допусков и основные отклонения размеров приведены в соответствующих справочных материалах.
|
|
|
|
IT |
|
|
Для k…zc, A…H: |
|
||
|
|
|
|
|
|
|
||||
|
|
|
|
|
|
es (ES)=ei (EI)+IT |
|
|||
|
|
|
|
|
|
|
|
|
|
|
|
|
|
|
ei, EI |
|
|
|
|
||
|
|
|
|
|
|
|
|
|
|
|
|
|
|
|
Основные |
|
|
es, ES |
|
||
|
|
|
|
отклонения |
|
|
||||
|
|
|
|
|
|
|
|
|||
D |
|
|
|
|
|
|
Для a…h, K…ZC: |
|||
|
|
|
|
|
|
IT |
|
|||
|
|
|
|
|
|
|
|
|
||
|
|
|
|
|
|
|
|
|
ei (EI)=es (ES)+IT |
|
|
|
|
|
|
|
|
|
|
|
|
|
|
|
|
|
|
|
|
|
|
|
Рис.7.4 – Построение полей допусков и определение предельных отклонений

75
A
А
Отверстия
B
C
CD
D
E EF
F FG
G H
0 |
Js |
|
ZC
|
|
|
|
|
|
|
|
|
|
|
|
|
|
|
|
|
|
нулевая линия |
|||||||||||||||||||
|
|
|
|
|
|
|
|
|
|
|
|
|
|
|
(линия номинального |
||||||||||||||||||||||
|
|
|
|
|
|
|
|
|
|
|
|
|
|
|
|||||||||||||||||||||||
|
|
|
|
|
|
|
|
|
|
|
|
|
|
|
|||||||||||||||||||||||
|
|
|
|
|
|
|
|
|
|
|
|
|
|
|
|
|
|
|
|
|
|
|
размера) |
||||||||||||||
|
|
|
|
|
|
|
|
|
|
|
|
|
|
|
|
|
|
|
|
|
|
|
|||||||||||||||
K M |
|
|
|
|
|
|
|
|
|
|
|
|
|
|
|
|
|
|
|
|
|
|
|
|
|
|
|
|
|
|
|
|
|
|
|
||
|
|
N |
|
P |
|
|
|
|
|
|
|
|
|
|
|
|
|
|
|
|
|
|
|
|
|
|
|
|
|
|
|
|
|
|
|||
|
|
|
R |
|
|
|
|
|
|
|
|
|
|
|
|
|
|
|
|
|
|
|
|
|
|
|
|
|
|
|
|||||||
|
|
|
|
|
|
|
|
S |
|
|
|
|
|
|
|
|
|
|
|
|
|
|
|
|
|
|
|
|
|
|
|
|
|
||||
|
|
|
|
|
|
|
|
|
|
|
|
|
|
|
|
|
|
|
|
|
|
|
|
|
|
|
|
|
|
|
|
|
|
|
|
||
|
|
|
|
|
|
|
|
|
|
|
T |
|
|
|
|
|
|
|
|
|
|
|
|
|
|
|
|
|
|
|
|
|
|
||||
|
|
|
|
|
|
|
|
|
|
|
|
|
|
|
|
|
|
|
|
|
|
|
|
|
|
|
|
|
|
|
|
|
|
||||
|
|
|
|
|
|
|
|
|
|
|
|
U |
|
|
|
|
|
|
|
|
|
|
|
|
|
|
|
|
|
|
|
||||||
|
|
|
|
|
|
|
|
|
|
|
|
|
|
|
|
|
|
|
|
|
|
|
|
|
|
|
|
|
|
|
|
||||||
|
|
|
|
|
|
|
|
|
|
|
|
|
|
|
|
|
V |
|
|
|
|
|
|
|
|
|
|
|
|
|
|
|
|
||||
|
|
|
|
|
|
|
|
|
|
|
|
|
|
|
|
|
|
|
|
|
|
|
|
|
|
|
|
|
|
|
|
|
|||||
|
|
|
|
|
|
|
|
|
|
|
|
|
|
|
|
|
|
|
X |
|
|
|
|
|
|
|
|
|
|
|
|
|
|
||||
|
|
|
|
|
|
|
|
|
|
|
|
|
|
|
|
|
|
|
|
|
|
|
|
|
|
|
|
|
|
|
|||||||
|
|
|
|
|
|
|
|
|
|
|
|
|
|
|
|
|
|
|
|
|
|
|
|
Y |
|
|
|
|
|
|
|
|
|
|
|
||
|
|
|
|
|
|
|
|
|
|
|
|
|
|
|
|
|
|
|
|
|
|
|
|
|
|
|
|
|
|
|
|
|
|
|
|
||
|
|
|
|
|
|
|
|
|
|
|
|
|
|
|
|
|
|
|
|
|
|
|
|
|
|
|
|
|
Z |
|
|
|
|
|
|
|
|
|
|
|
|
|
|
|
|
|
|
|
|
|
|
|
|
|
|
|
|
|
|
|
|
|
|
|
|
|
|
|
|
|
|
|
|
|
|
|
|
|
|
|
|
|
|
|
|
|
|
|
|
|
|
|
|
|
|
|
|
|
|
|
|
|
|
|
|
ZA |
|
|
|
|
|
||
|
|
|
|
|
|
|
|
|
|
|
|
|
|
|
|
|
|
|
|
|
|
|
|
|
|
|
|
|
|
|
|
|
|
|
|||
|
|
|
|
|
|
|
|
|
|
|
|
|
|
|
|
|
|
|
|
|
|
|
|
|
|
|
|
|
|
|
|
|
|
|
|||
|
|
|
|
|
|
|
|
|
|
|
|
|
|
|
|
|
|
|
|
|
|
|
|
|
|
|
|
|
|
|
|
ZB |
|
|
|
||
|
|
|
|
|
|
|
|
|
|
|
|
|
|
|
|
|
|
|
|
|
|
|
|
|
|
|
|
|
|
|
|
|
|
|
|||
|
|
|
|
|
|
|
|
|
|
|
|
|
|
|
|
|
|
|
|
|
|
|
|
|
|
|
|
|
|
|
|
|
|
|
|
|
|
|
|
|
|
|
|
|
|
|
|
|
|
|
|
|
|
|
|
|
|
|
|
|
|
|
|
|
|
|
|
|
|
|
|
ZC |
|
Рис.7.5 – Относительные положения и обозначения стандартных основных отклонений для отверстий
|
|
|
|
|
|
|
|
|
|
|
|
|
|
|
|
|
|
|
|
|
|
|
|
|
|
|
|
|
|
|
|
|
|
|
|
|
|
|
|
|
|
|
|
|
|
|
|
|
|
|
|
|
|
|
|
|
|
|
|
|
|
|
|
|
|
|
|
|
|
|
zc |
|||
|
|
|
|
|
|
|
|
|
|
|
|
|
|
|
|
|
|
|
|
|
|
|
|
|
|
|
|
|
|
|
|
|
|
|
|
|
|
|
|
|
|
|
|
|
|
|
|
|
|
|
|
|
|
|
|
|
|
|
|
|
|
|
|
|
|
|
|
|
|
|
|
|
|
|
|
|
|
|
|
|
|
|
|
|
|
|
|
|
|
|
|
|
|
|
|
|
|
|
|
|
|
|
|
|
|
|
|
|
|
|
|
|
|
|
|
|
|
|
|
|
|
|
|
|
|
|
|
|
|
|
|
|
|
|
|
|
|
|
|
|
|
|
|
zb |
|
|
|||
|
|
|
|
|
|
|
|
|
|
|
|
|
|
|
|
|
|
|
Валы |
|
|
|
|
|
|
|
|
|
|
|
|
|
|
|
|
|
|
|
|
|
|
|
|
|
|
|
|
|
|
|
|
|
|
|
|
|
|
|
|
|
||||||||||||||
|
|
|
|
|
|
|
|
|
|
|
|
|
|
|
|
|
|
|
|
|
|
|
|
|
|
|
|
|
|
|
|
|
|
|
|
|
|
|
|
|
|
|
|
|
|
|
za |
|
|
|
|
|
|
|||||||||||||||||||||
|
|
|
|
|
|
|
|
|
|
|
|
|
|
|
|
|
|
|
|
|
|
|
|
|
|
|
|
|
|
|
|
|
|
|
|
|
|
|
|
|
|
|
|
|
|
|
|
|||||||||||||||||||||||||||
|
|
|
|
|
|
|
|
|
|
|
|
|
|
|
|
|
|
|
|
|
|
|
|
|
|
|
|
|
|
|
|
|
|
|
|
|
|
|
|
|
|
|
||||||||||||||||||||||||||||||||
|
|
|
|
|
|
|
|
|
|
|
|
|
|
|
|
|
|
|
|
|
|
|
|
|
|
|
|
|
|
|
|
|
|
|
|
|
|
|
|
|
|
|
|
|
|
|
|
|
|
|
|
|
|
|
|
|
|
|
|
|
|
|
|
|
z |
|
|
|
|
|
|
|
|
|
|
|
|
|
|
|
|
|
|
|
|
|
|
|
|
|
|
|
|
|
|
|
|
|
|
|
|
|
|
|
|
|
|
|
|
|
|
|
|
|
|
|
|
|
|
|
|
|
|
|
|
|
|
|
|
|
|
|
|
|
|
|
|
|
|
|
|
|
|
|
|
|
|
|
|
|
|
|
|
|
|
|
|
|
|
|
|
|
|
|
|
|
|
|
|
|
|
|
|
|
|
|
|
|
|
|
|
|
|
|
|
|
|
|
|
|
|
|
|
|
|
|
|
|
|
|
|
|
|
|
|
|
|
|
|
|
|
|
|
|
|
|
|
|
|
|
|
|
|
|
|
|
|
|
|
|
|
|
|
|
|
|
|
|
|
|
|
|
|
|
|
|
|
|
|
|
|
|
|
|
|
|
|
|
|
|
|
|
|
|
|
|
|
|
|
|
|
|
|
|
|
|
|
|
|
|
|
|
|
|
|
|
|
y |
|
|
|
|
|
|
|
|
|
|
|
|
|
|
|
|
|
|
|
|
|
|
|
|
|
|
|
|
|
|
|
|
|
|
|
|
|
|
|
|
|
|
|
|
|
|
|
|
|
|
|
|
|
|
|
|
|
|
|
|
|
|
|
|
|
|
|
|
|
|
x |
|
|
|
|
|
|
|
|
|
|
|
|
|
||
|
|
|
|
|
|
|
|
|
|
|
|
|
|
|
|
|
|
|
|
|
|
|
|
|
|
|
|
|
|
|
|
|
|
|
|
|
|
|
|
|
|
|
|
|
|
|
|
|
|
|
|
|
|
|
|
|
|
|
|
|
|
|
|
|
|
|
|
|
|
|||||
|
|
|
|
|
|
|
|
|
|
|
|
|
|
|
|
|
|
|
|
|
|
|
|
|
|
|
|
|
|
|
|
|
|
|
|
|
|
|
|
|
|
|
|
|
|
|
|
|
|
|
|
|
|
|
|
v |
|
|
|
|
|
|
|
|
|
|
|
|
|
|
|
|||
|
|
|
|
|
|
|
|
|
|
|
|
|
|
|
|
|
|
|
|
|
|
|
|
|
|
|
|
|
|
|
|
|
|
|
|
|
|
|
|
|
|
|
|
|
r s |
|
|
|
t |
|
u |
|
|
|
|
|
|
|
|
|
|
|
|
|
|
|
|
|
|
|
|
|||
|
|
|
|
|
|
|
|
|
|
|
|
|
|
|
|
|
|
|
|
|
|
|
|
|
|
|
|
|
|
|
|
|
|
|
|
|
|
|
|
|
|
|
|
|
|
|
|
|
|
|
|
|
|
|
|
|
|
|
|
|
|
|
|
|
|
|
|
|
||||||
|
|
|
|
|
|
|
|
|
|
|
|
|
|
|
|
|
|
|
|
|
|
|
|
|
|
|
|
|
|
|
|
|
|
k m |
|
n |
|
p |
|
|
|
|
|
|
|
|
|
|
|
|
|
|
|
|
|
|
|
|
|
|
|
|
|
|
|
|
|
|
|
|||||
|
|
|
|
|
|
|
|
|
|
|
|
|
|
|
|
|
|
|
|
|
|
|
|
|
|
|
|
|
|
|
|
|
|
|
|
|
|
|
|
|
|
|
|
|
|
|
|
|
|
|
|
|
|
|
|
|
|
|
|
|
|
|
|
|
|
|||||||||
|
|
|
|
|
|
|
|
|
|
|
|
|
|
|
|
|
|
|
|
|
|
|
|
|
|
|
|
|
|
|
|
|
|
|
|
|
|
|
|
|
|
|
|
|
|
|
|
|
|
|
|
|
|
|
|
|
|
|
|
|
|
|
|
|
|
|
|
|
|
|
|
|
|
|
|
|
|
|
|
|
|
|
|
|
|
|
|
|
|
|
|
|
|
|
|
|
|
|
|
|
|
|
|
|
|
|
|
|
|
|
|
|
|
|
|
|
|
|
|
|
|
|
|
|
|
|
|
|
|
|
|
|
|
|
|
|
|
|
|
|
|
|
|
|
|
|
|
|
|
|
|
|
|
|
|
|
|
|
|
|
|
|
|
|
|
|
|
|
|
|
|
|
|
|
|
|
|
|
|
|
|
|
|
|
|
|
|
|
|
|
|
|
|
|
|
|
|
|
|
|
|
|
|
|
|
|
|
|
|
|
|
|
|
|
|
|
|
|
|
|
|
|
|
|
|
|
|
|
|
|
|
|
|
|
|
|
|
|
|
|
|
|
|
|
|
|
|
|
|
|
|
|
|
|
|
|
|
|
|
|
|
|
|
|
|
|
|
|
|
|
|
|
|
|
|
|
|
|
|
|
|
|
|
|
|
|
|
|
|
|
|
|
|
|
|
|
|
|
|
0 |
|
|
|
|
|
|
|
|
|
|
|
|
|
|
|
|
|
|
|
|
|
|
|
|
|
|
|
|
|
|
|
|
|
|
|
|
|
|
|
|
|
|
|
|
|
|
|
|
|
|
|
|
|
|
|
|
нулевая линия |
|||||||||||||||||
|
|
|
|
|
|
|
|
|
|
|
|
|
|
|
|
|
|
|
|
|
|
|
|
|
|
|
|
|
|
js |
|
|
|
|
|
|
|
|
|
|
|
|
|
|
|
|
|
|
|
|
|
|||||||||||||||||||||||
|
|
|
|
|
|
|
|
|
|
|
|
|
|
|
|
|
|
|
|
|
|
|
|
|
|
|
g |
|
h |
|
|
|
|
|
|
|
|
|
|
|
|
|
|
|
|
|
|
|
|
|
|
|
|
|
|
|
|
|
|
|
|
|
|
|
|
|
|
|
||||||
|
|
|
|
|
|
|
|
|
|
|
|
|
|
|
|
|
|
|
|
|
|
f |
|
fg |
|
|
|
|
|
|
|
|
|
|
|
|
|
|
|
|
|
|
|
|
|
|
|
|
|
|
|
|
|
|
|
|
|
|
|
|
|
|||||||||||||
|
|
|
|
|
|
|
|
|
|
|
|
|
|
|
|
|
|
|
|
ef |
|
|
|
|
|
|
|
|
|
|
|
|
|
|
|
|
|
|
|
|
|
|
|
|
|
|
|
|
|
|
|
|
|
|
|
|
|
|
|
|
|
|||||||||||||
|
|
|
|
|
|
|
|
|
|
|
|
|
|
|
|
e |
|
|
|
|
|
|
|
|
|
|
|
|
|
|
|
|
|
|
|
|
|
|
|
|
|
|
|
|
|
|
|
|
zc |
|||||||||||||||||||||||||
|
|
|
|
|
|
|
|
|
|
|
|
|
|
|
|
|
|
|
|
|
|
|
|
|
|
|
|
|
|
|
|
|
|
|
|
|
|
|
|
|
|
|
|
|||||||||||||||||||||||||||||||
|
|
|
|
|
|
|
|
|
|
|
|
|
|
|
|
|
|
|
|
|
|
|
|
|
|
|
|
|
|
|
|
|
|
|
||||||||||||||||||||||||||||||||||||||||
|
|
|
|
|
|
|
|
|
|
|
|
|
d |
|
|
|
|
|
|
|
|
|
|
|
|
|
|
|
|
|
|
|
|
|
|
|
|
|
|
|
|
|
|
|
|
|
|
|
|
|
|
|
|
|
|
|
|
|
|
|
|
|||||||||||||
|
|
|
|
|
|
|
|
|
|
|
|
|
|
|
|
|
|
|
|
|
|
|
|
|
|
|
|
|
|
|
|
|
|
|
|
|
|
|
|
|
|
|
|
|
|
|
|
|
|
|
|
|
||||||||||||||||||||||
|
|
|
|
|
|
|
|
|
|
|
|
|
|
|
|
|
|
|
|
|
|
|
|
|
|
|
|
|
|
|
|
|
|
|
|
|
|
|
|
|
|
|
|
|
|
|
|
|
|
|
|
|
|
|
|
|
|
|
|
|
|
|
|
|
|
|
|
|
|
|
|
|
|
|
|
|
|
|
|
|
|
|
|
cd |
|
|
|
|
|
|
|
|
|
|
|
|
|
|
|
|
|
|
|
|
|
|
|
|
|
|
|
|
|
|
|
|
|
|
|
|
|
|
|
|
|||||||||||||||||||||||||
|
|
|
|
|
|
|
|
|
|
|
|
|
|
|
|
|
|
|
|
|
|
|
|
|
|
|
|
|
|
|
|
|
|
|
|
|
|
|
|
|
|
|
|
|
|
|
|
|
|
|
|
|
|
|
|
|
|
|
|
|
a |
|||||||||||||
|
|
|
|
|
|
|
|
|
|
|
|
|
|
|
|
|
|
|
|
|
|
|
|
|
|
|
|
|
|
|
|
|
|
|
|
|
|
|
|
|
|
|
|
|
|
|
|
|
|
|
|
|
|
|
|
|
|
|
|
|
||||||||||||||
|
|
|
|
|
|
|
c |
|
|
|
|
|
|
|
|
|
|
|
|
|
|
|
|
|
|
|
|
|
|
|
|
|
|
|||||||||||||||||||||||||||||||||||||||||
|
|
|
|
|
|
|
|
|
|
|
|
|
|
|
|
|
|
|
|
|
|
|
|
|
|
|
|
|
|
|
|
|
|
|
|
|
|
|
|
|
|
|
|
|
|
|
|
|
|
|
|
|
|
|
|
|
|
|
|
|
|
|
|
|
|
|
|
|
|
|
|
|
|
|
|
|
|
|
|
|
|
|
|
|
|
|
|
|
|
|
|
|
|
|
|
|
|
|
|
|
|
|
|
|
|
|
|
|
|
|
|
|
|
|
|
|
|
|
|
|
|
|
|
|
|
|
|
|
|
|
|
|
|
|
|
|
|
|
|
|
|
|
|
|
|
|
|
|
|
|
|
|
|
b |
|
|
|
|
|
|
|
|
|
|
|
|
|
|
|
|
|
|
|
|
|
|
|
|
|
|
|
|
|
|
|
|
|
|
|
|
|
|
|
|
||||||||||||||||||||||||||||||
|
|
|
|
|
|
|
|
|
|
|
|
|
|
|
|
|
|
|
|
|
|
|
|
|
|
|
|
|
|
|
|
|
|
|
|
|
|
|
|
|
|
|
|
|
|
|
|
|
|
|
|
|
|
|
|
|
|
|
|
|
|
|
|
|
|
|
|
|
|
|
|
|
|
|
|
|
|
|
|
|
|
|
|
|
|
|
|
|
|
|
|
|
|
|
|
|
|
|
|
|
|
|
|
|
|
|
|
|
|
|
|
|
|
|
|
|
|
|
|
|
|
|
|
|
|
|
|
|
|
|
|
|
|
|
|
|
|
|
|
|
|
|
|
|
|
|
|
|
|
a
Рис. 7.6 – Относительные положения и обозначения стандартных основных отклонений для валов

76
|
|
|
|
|
|
|
|
|
|
|
|
|
|
|
IT14 |
|
|
k |
|
|
|
|
|
|
|
|
|
|
|
|
|
|
|
|
|
|
400 |
||
|
|
|
|
|
|
|
|
|
|
|
|
|
|
|
|
|
|
|
|
|
|
|
|
T= k i |
|
|
|
|
|
|
|
|
IT13 |
|
|
|
250 |
||
|
|
|
|
|
|
|
|
|
|
|
|
|
|
|
|
|
|||
|
|
|
|
k – число единиц допуска |
|
|
IT12 |
|
|
|
|
160 |
|||||||
|
|
|
|
i – единица допуска |
|
|
|
|
|
|
|
||||||||
|
|
|
|
|
|
|
|
|
|
|
|
|
|
||||||
|
|
|
|
|
|
|
|
|
|
|
|
|
|
|
|
|
|
|
100 |
|
|
|
|
|
|
|
|
|
|
|
|
|
|
|
|
|
|
|
64 |
|
|
|
|
|
|
7 |
10 |
16 |
25 |
|
|
|
|
|
|
|
|
|
40 |
|
|
|
|
|
|
|
|
|
|
|
|
|
|
|
|
||||
01 |
0 |
1 |
2 |
3 |
4 |
5 |
6 |
7 |
8 |
9 |
10 |
11 |
12 |
13 |
14 |
15 |
16 |
17 |
18 |
|
|
|
|
|
|
|
|
|
|
квалитеты |
|
|
|
|
|
|
|
||
|
|
|
|
|
|
|
|
Рис.7.7 – Ряды точности |
|
|
|
|
|
Отметим, что в технике при характеристике окружностей предпочитают пользоваться диаметральными размерами, поскольку они проще контролируются и измеряются. Радиусы требуют указания центра окружности (оси цилиндра), который является математической абстракцией, и проставляются только в особых случаях. Например, записи размера 50n6 равнозначна численная запись 50 ++00,,033017 , что означает: номинальный размер (в данном случае –
диаметр) – 50мм, допуск по 6 квалитету точности, расположение поля допуска соответствует n (несколько выше номинального размера, рис.6), размер относится к “валу” (прописная буква), значение допуска шестого квалитета на данный размер IT6=0,016мм (установлено по справочнику или расчетом IT=0,033 – 0,017). Отметим, что какое бы другое от a до zc поле допуска не
было взято, при неизменных номинальном размере и квалитете значение их допуска будет постоянно. Другой пример, 90H8 (иначе – 90+0,054), что означает: допуск на отверстие номи-
нальным диаметром 90мм по 8 квалитету точности, расположенный по H и величиной IT8= 0,054мм. Данный размер выполнен на 2 квалитета грубее, чем рассмотренный выше размер вала. В практических расчетах обычно принимают нормальный закон распределения действительных значений размеров, как случайных величин, внутри допуска. Но он может отличаться от нормального, что, в первую очередь, зависит от условий изготовления.
Запись условным обозначением полей допусков (шифром) предпочтительна в конструкторской документации: облегчается качественный анализ (сравнение точности и взаимного расположения допусков различных размеров), не требуется помнить или постоянно обращаться к справочнику для отыскания значений всевозможных отклонений. При необходимости на рабочих чертежах установлена совместная запись – условным обозначением и, в скобках, предельными отклонениями (численная), например, 18H8 (+0,027). В технологической документации предпочтительна численная форма записи.
Основная форма записи нестандартных размеров и предельных отклонений – численная. В отдельных случаях, когда технологически сложно выдержать размеры, либо их точность предопределяются используемым инструментом, указывают только номинальный размер с ссылкой на условия, регламентирующие предельные отклонения. Например, 20* с пояс-
няющей ссылкой типа “ *Размеры обеспечиваются инструментом”.
Из всего многообразия возможных полей допусков стандартом рекомендовано применение только определенной их части: предпочтительные и рекомендуемые. Применение нерекомендуемых полей допусков экономически нецелесообразно, так как требует специального инструмента, требующего индивидуального изготовления.
77
. Сопряжения деталей Как правило, изделие состоит из нескольких деталей. По одним из своих поверхностей де-
тали соприкасаются между собой (это – сопрягаемые поверхности), а по другим контакт отсутствует (это – свободные поверхности). Различают следующие сопряжения:
•гладкие цилиндрические и конические;
•плоские;
•резьбовые и винтовые;
•зубчатые эвольвентные и циклоидальные;
•шлицевые;
•сферические.
Наиболее часто при сборке одна деталь входит в другую, а сопряжение происходит по цилиндрическим или плоским поверхностям, одна из которых – охватывающая, а другая – охватываемая. Например, сопряжение вала и втулки, паза и призматического бруса.
При сборке реальной пары деталей, в зависимости от соотношения действительных размеров возможны только два характера сопряжений – зазор или натяг:
•сопряжение с натягом, когда размер вала больше размера отверстия, и при сборке вал запрессовывается во втулку;
•сопряжение с зазором, когда размер вала меньше размера отверстия, и при сборке вал свободно входит во втулку.
Разность между размерами отверстия и вала соответствует величинам:
•зазора S = D – d, если D>d,
•натяга N = d – D, если d>D (в расчетах натяг могут рассматривать и как “отрицательный” зазор).
Партия готовых деталей или проектируемая деталь характеризуются нормируемыми значениями параметров. В этом случае характер возможного сопряжения определяется соотношением допустимых предельных размеров вала (охватываемой поверхности) и отверстия (охватывающей поверхности). Для удобства записи параметров сопряжения номинальные размеры сопрягаемых деталей принимают равными, т.е. d=D. О характере сопряжения также можно судить по взаимному расположению их полей допусков. Очевидны три случая взаимного расположения полей допусков, которые обуславливают три типа посадок – посадки с зазором, натягом и переходные.
Посадки с зазором. Образуются, когда в сопряжении любой допустимый размер вала меньше любого допустимого размера отверстия и, следовательно, поле допуска на вал лежит ниже поля допуска на отверстие. По схеме на рис. 7.11 (на примере поля допуска отверстия H7) – это поля допусков a...h на вал. Посадка характеризуется (рис. 7.8) наибольшим возможным зазором
Smax = Dmax – dmin =ES – ei
и наименьшим возможным зазором
Smin = Dmin – dmax =EI – es.
Аналогично понятию допуска размера введено понятие допуска посадки. Допуск посадки с зазором TS равен величине диапазона изменения возможных значений зазоров, т.е.
TS = Smax – Smin = TD + Td.
Посадка обозначается в виде дроби, в числителе которой указывается допуск на отверстие, а в знаменателе – на вал. Допустимы численная запись и запись условным обозначением (шифром).
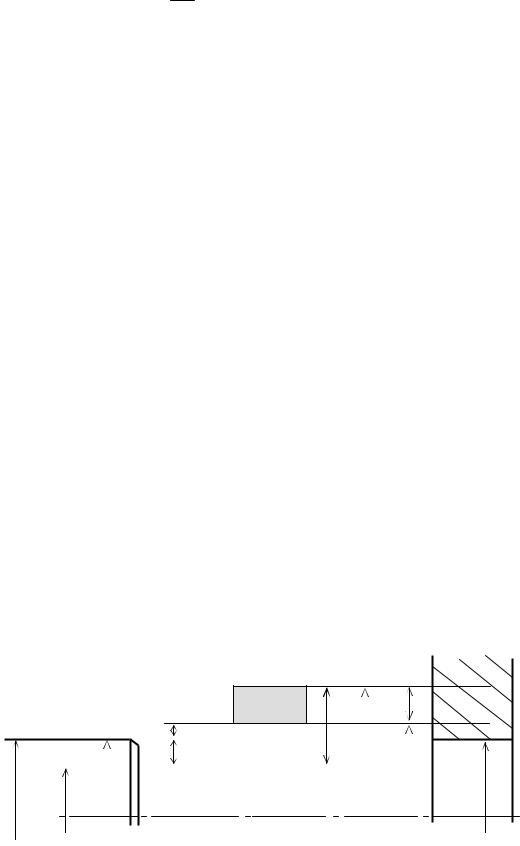
78
Например, запись шифром – 40 Hd 99 или, в более компактном виде, – 40H9/d9 (допуск на
|
+0,062 |
|
отверстие – H9, на вал – d9), и аналогичная им численная запись – 40 |
|
. Эти тождествен- |
|
||
|
−0,080 |
|
|
−0,142 |
ные записи означают: номинальный размер сопрягаемых поверхностей деталей равен 40мм, допуск посадки TS=0,124мм, минимальный зазор Smin = 0,08мм, максимальный зазор
Smax = 0,204мм.
Посадки с натягом. Образуются, когда в сопряжении любой допустимый размер вала больше любого допустимого размера отверстия и, следовательно, поле допуска на вал лежит выше поля допуска на отверстие. По схеме на рис.11 (на примере поля допуска отверстия H7)
– это посадки с одним из полей допусков p...z на вал. Отметим, что схема на рисунке представляет наиболее вероятный, но частный случай расположения полей допусков. Так, при уменьшении точности обработки отверстия и, значит, увеличении допуска, его поле может начать пересекаться с перечисленными полями допусков на вал, и тип посадки изменится.
Посадка характеризуется (рис. 7.9) наибольшим возможным натягом
Nmax = dmax – Dmin =es – EI
и наименьшим возможным натягом
Nmin = dmin – Dmax =ei – ES.
Допуск посадки с натягом TN равен величине интервала изменения возможных значений натягов, т.е.
TN = Nmax – Nmin = TD + Td.
|
+ 0,033 |
|
|
Пример посадки с натягом – 30H8/x8, или иначе – 30 |
|
. Здесь допуск посадки с натя- |
|
+ 0,097 |
|||
|
|
||
|
+ 0,064 |
|
гом TN=0,066мм, минимальный натяг Nmin = 0,031мм, максимальный натяг – Nmax = 0,097мм. Переходные посадки. Возникают, когда в сопряжении поля допусков на отверстие и вал перекрываются, и при сборке могут появляются как зазоры, так и натяги. О конкретном характере сопряжения можно судить только с какой-то вероятностью. Часто используют оценочную характеристику – более или менее вероятен в сопряжении зазор или натяг. По схеме на рис.11 (на примере поля допуска отверстия H7) – это посадки с одним из полей допусков js ... n на
вал. Переходная посадка характеризуется (рис. 7.10) наибольшим возможным натягом
Nmax = dmax – Dmin =es – EI
F8 |
TD |
|
Smin |
||
|
|
Td |
h7 |
Smax |
|
|
|
|
|
|
|
|
|
|
|
d |
dmin |
dmax |
Dmax Dmin |
D |
|
|
Рис.7.8 – Пример посадки с зазором в системе вала |
|

79
и наибольшим возможным зазором
Smax = Dmax – dmin.=ES – ei .
Допуск переходной посадки TNS равен величине интервала изменения сопряжения от наибольшего значения натяга до наибольшего значения зазора, т.е.
TNS = Smax – (–Nmax)= Smax + Nmax = TD + Td.
|
+ 0,030 |
|
|
Пример переходной посадки: 70H7/k6, или же – 70 |
|
. Здесь допуск посадки |
|
+ 0,021 |
|||
|
|
||
|
+ 0,002 |
|
TSN=0,049мм, максимальный зазор Smax =0,028мм, максимальный натяг – Nmax =0,021мм.
Различный тип посадки можно получить тремя способами:
•изменением положения поля допуска вала относительно фиксированного положения поля допуска отверстия. Это – посадка в системе отверстия. В качестве фиксированного, иначе
– основного, поля допуска отверстия принимают H (но могут быть исключения, например, при посадке наружных колец стандартных подшипников качения). Примеры посадок, приведенные на рис. 7.8, 7.9, даны в системе отверстия;
•изменением положения поля допуска отверстия относительно фиксированного положения поля допуска вала. Это – посадка в системе вала, а в качестве фиксированного, основного, поля допуска вала принимают h. Пример посадки приведен на рис. 7.8;
•изменением относительного положения полей допусков как вала, так и отверстия, но при этом их поля не являются основными, т.е. не соответствуют по расположению полям допусков h, H. Это – комбинированные посадки.
Выбор той или иной системы позволяет сократить множество вариантов возможных посадок и, следовательно, – необходимый станочный и инструментальный парк. Наиболее распространена система отверстия. Она используется, например, когда обработка внутренних (охватывающих) поверхностей затруднительна, либо для этого нужен дорогой специализированный инструмент, например, протяжки, сверла, зенкеры и т.п., которые настроены на фиксированный размер, и необходимость обработки другого, как по номинальному размеру, так и допуску отверстия уже требует другой инструмент. Система вала предпочтительна, когда сложно или крайне невыгодно обрабатывать охватываемые поверхности (валы), такие, например, как наружные кольца стандартных подшипников качения (их дополнительная обработка не только весьма трудоемка, но при этом подшипник становится нестандартным изделием, что усложняет ремонт), детали из тонкой проволоки. Комбинированные посадки назначают в особых случаях, например, в посадках шпонок.
С целью дальнейшего сокращения разнообразия посадок стандартом рекомендована к применению только часть их возможного количества, образуемые на основе рекомендуемых и предпочтительных полей допусков.
Td |
|
s6 |
|
|
|
|
Nmin |
|
|
|
|
|
|
|
|
|
|
|
|
|
|
|
|
|
|
|
|
|
|
|
|
|
Nmax |
H7 |
|
TD |
|
||
|
|
|
|
|
|
|
|
|
|
D
d
dmax dmin |
Dmax Dmin |
Рис.7.9 – Пример посадки с натягом в системе отверстия

80
|
|
|
|
|
Smax |
|
|
|||
Td |
|
n6 |
|
|
|
|||||
|
|
|
|
|
|
|||||
|
|
|
|
|
H7 |
TD |
|
|||
|
|
|
|
|
|
|
|
|
||
|
|
|
Nmax |
|
||||||
|
|
|
|
|
||||||
|
|
|
|
|
|
|||||
|
|
|
|
|
|
|
|
|
|
|
D
d
dmax dmin Dmax Dmin
Рис. 7.10 – Пример переходной посадки в системе отверстия
Если поверхности не сопрягаемые, а свободные, то их точность, пусть и косвенно, тоже должна гарантировать точность функциональных параметров. При отсутствии специальных указаний назначают 12, 14, 16 и 17 квалитеты, которые приблизительно соответствуют “точным”, “средним”, “грубым” и “очень грубым” требованиям к изделию.
Поле допуска на свободные размеры выбирают следующим:
•на охватывающие поверхности (отверстия) – H;
•на охватываемые поверхности (валы) – h;
•на размеры поверхностей, которые не относятся ни к охватываемым, ни к охватывающим – симметричное расположение отклонений (плюс-минус половина величины допуска на данный размер, например, ± IT14/2).
Обычно отклонения таких размеров на чертежах не проставляют, а указывают в технических требованиях.
Величины допусков свободных размеров могут назначать в соответствии с российским (национальным) стандартом с допуском t, см. табл. ниже.
|
|
|
|
|
Smax |
|
|
s6 |
t6 |
u7 |
|
|
|
|
|
|
r6 |
Nmax |
|||
|
|
|
|
|
Nmax |
p6 |
|
|
||
|
|
|
|
|
n6 |
|
|
|
|
Nmin |
|
H7 |
|
|
|
m6 |
|
|
|
|
|
|
|
|
|
|
k6 |
|
|
|
|
|
|
|
|
|
|
js6 |
|
|
|
|
|
|
Smin |
|
f7 |
g6 |
h6 |
|
|
|
|
|
Smax |
e8 |
|
|
|
|
|
|
|||
d9 |
|
|
|
|
|
|
|
|
||
|
|
|
|
|
|
|
|
|
|
|
|
c11 |
|
|
|
|
|
|
|
|
|
b11 |
|
|
|
|
|
|
|
|
|
|
a11 |
|
|
посадки с |
переходные |
посадки с |
|
|
||||
|
|
|
|||
|
|
|
зазором |
посадки |
натягом |
Рис.7.11 – Примеры посадок в системе отверстия (на основе рекомендуемых и предпочтительных полей допусков)