
Детали машин и основы конструктирования
.pdf
161
(мелкосерийное производство и в глухих отверстиях), а на валах – фрезерованием дисковой или пальцевой фрезами. Обработка дисковой фрезой производительнее, но длина паза возрас-
а) б)
в)
Рис.8.50 – Шпоночное соединение с призматической шпонкой на конической поверхности (а,б) и с торцевой шпонкой (в)
тает на длину участка врезания инструмента (рис. 8.49б). В таких пазах устанавливают шпонки с плоскими торцами (для увеличения их полезной длины). Кроме того, в осевом направлении шпонки ни во что не упираются, что требует их дополнительной осевой фиксации посадкой или иным способом. Выполнение паза пальцевой фрезой менее производительно, но длина паза максимально приближена к длине шпонки, а его форма – форме шпонки с кругленными торцами.
Вшпоночном соединении сложно обеспечить полную взаимозаменяемость, часто применяется ручная пригонка.
Взависимости от способа изготовления пазов размеры шпоночного соединения наносятся по разному, особенно размер, характеризующий глубину паза.
Обычно в соединении ставят одну шпонку. Установка нескольких шпонок (редко более трех) не достаточно эффективна, поскольку теоретическое повышение нагрузочной способности (пропорционально числу шпонок) снижается из-за ослабления поперечного сечения вала, увеличения концентрации напряжений и неравномерности распределения нагрузки между шпонками (возникает статически неопределимая система).
При установке шпонок необходимо проверять условие последующей собираемости деталей на валу и вхождения получившегося узла в подшипниковые гнезда. Это связано с тем, что шпонка увеличивает диаметральный размер соответствующего участка вала, что может нарушить принцип монотонности изменения диаметров валов и помешать последующему надеванию деталей или продвижению собранного вала сквозь отверстия при монтаже.
Более технологичны сегментные шпонки (рис. 8.51). Пазы под них на валах изготавливают дисковыми фрезами вертикальной подачей, а шпонки нарезают из круглого проката. Соединение стандартизировано (ГОСТ 24071), легко собирается и разбирается, расположение шпонки устойчивое. Однако глубокий шпоночный паз существенно снижает прочность вала. Соединение сегментной шпонкой характеризуется шириной шпонки b, диаметром заготовки d
ивысотой сегмента h.
Основными видами отказов ненапряженного шпоночного соединения являются:
•обмятие рабочих поверхностей пазов или шпонки (граней той детали, прочность которой ниже);
•срез шпонки в плоскости стыка деталей. Поскольку размеры стандартной шпонки назнача-

162
ются из условия прочности на срез, то проверка таких шпонок на данное условие обычно не производится.
Рис.8.51 – Шпоночное соединение с сегментной шпонкой
Шпоночные соединения с силовым замыканием звеньев полностью фиксируют детали
(в осевом и окружном направлениях) благодаря силе трения. Она создается вследствие расклинивания соединяемых деталей шпонкой клиновой формы (рис. 8.52). Такое соединение, даже при отсутствии рабочей нагрузки (а это могут быть крутящий момент Т и осевая сила Fa), внутренне уже напряжено, что повышает общий уровень напряжений в деталях. По этой причине клиновое соединение еще называют напряженным.
Контакт шпонки с валом и втулкой осуществляется по верхней и нижней граням, а по боковым – существует зазор (они неработающие). Сила вдавливания шпонки F должна создать такое давление между соединяемыми деталями, чтобы возникшая сила трения могла воспринять внешнюю нагрузку. Отсутствие зазора по верхним граням и его наличие по боковым служит графическим признаком силового соединения.
Верхняя грань шпонки обычно выполняется с уклоном 1:100, что позволяет развивать большое распорное усилие.
Различают три вида клиновых шпонок:
•клиновые шпонки, устанавливаемые в пазах (рис. 8.52а);
•фрикционные шпонки (рис. 8.52б). Здесь форма нижней грани шпонки соответствует форме цилиндрической поверхности соединяемых деталей, паз на валу отсутствует. Это позволяет легко менять положение сажаемой на вал детали;
•тангенциальное клиновое соединение (рис. 8.52 в). Здесь натяг создается в касательном на-
правлении и при обязательной установке двух пар шпонок. Угол между шпонками обычно принимают около 120о.
Рис. 8.52 – Шпоночное соединение с клиновыми шпонками
Клиновое соединение удобно в единичном производстве, просто при сборке (но сложен его демонтаж). Сборка соединения требует внимательности, так как неконтролируемость или превышение усилия вдавливания шпонки может создать значительные напряжения в деталях
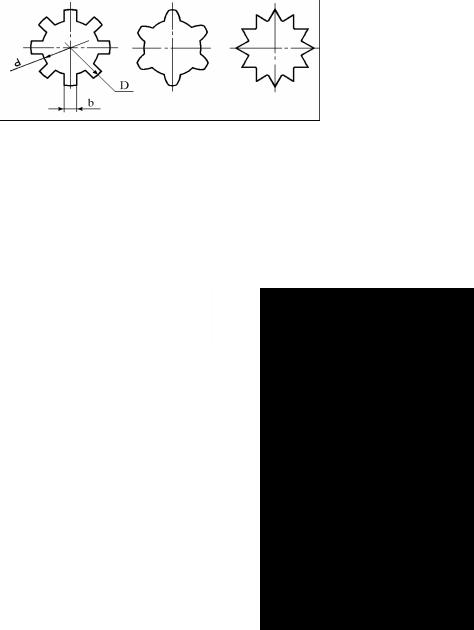
163
и вызвать разрыв втулки. Клиновые шпонки нарушают центровку соединяемых деталей (из-за расклинивания), хотя, при необходимости, позволяют выбирать радиальные зазоры.
8.5.2 Шлицевые соединения
Шлицевое соединение относится к разъемным и обеспечивает фиксацию соосно расположенных деталей в окружном направлении. Соединение представляет собой вал с выступамишлицами, располагающимися вдоль образующей, и втулку с пазами, в которые заходят шлицы. Шлицевое соединение можно рассматривать как многошпоночное, в котором шпонки выполнены заодно с валом. Шлицевое соединение – статически неопределимая система, и потому требует повышенной точности обработки.
Наиболее распространены прямоугольный, эвольвентный и треугольный профили шлицов (рис. 8.53). На валах шлицы изготавливают фрезерованием или строганием с последующим шлифованием. Пазы во втулках получают протягиванием (при серийном производстве) или строганием (при единичном производстве и в глухих отверстиях, производительность и получаемая точность при этом способе ниже).
а) б) в)
Рис.8.53 – Профили шлицов: а – прямоугольный, б – эвольвентный, в – треугольный
Прямобочное шлицевое соединение (боковые грани шлицов параллельны) – стандартизировано (ГОСТ 1139). Оно характеризуется внутренним d и наружным D диаметрами (по валу), числом шлицов z и их шириной b. Возможны три серии соединений: легкая, средняя и тяжелая,– различающиеся числом и размерами шлицов. Утяжеление серии повышает нагрузочную способность, но и увеличивает размеры соединения и трудоемкость его изготовления.
Взаимное центрирование шлицевого вала и втулки возможно тремя способами:
•по внутреннему диаметру шлицевого вала (рис. 8.54а). Способ допускает выполнение до-
|
водочных операций и поэтому, в частности, |
|
|
применяется при твердости соединяемых дета- |
а) |
• |
лей HRC>45; |
|
по наружному диаметру шлицевого вала (рис. |
|
|
|
8.54б). Обеспечивает высокую точность цен- |
|
|
трирования, но при точной обработке пазов |
б) |
• |
втулки (например, протягиванием); |
|
по боковым граням (рис. 8.54в). Применяют |
|
|
|
при высоких требованиях к окружным зазорам |
|
|
и прямолинейности боковых граней, при воз- |
|
|
можном изменении радиальных размеров со- |
в) |
|
пряжения (например, при температурной де- |
|
|
формации) и необходимости радиальной под- |
|
|
вижности соединяемых деталей (например, |
|
|
плавающее в радиальном направлении закреп- |
|
|
ление звеньев передач, соответствующее шар- |
Рис. 8.54 – Способы центрирования пря- |
|
нирному их соединению). |
мобочных шлицевых соединений |
|
|

164
а) б)
в)
Рис.8.55 – Изображение прямобочного шлицевого соединения на чертеже
На рис. 8.55 приведено графическое изображение прямобочного шлицевого соединения: вала (а), втулки (б) и в сборе (в). При продольном сечении шлицы не штрихуются. Буквенное обозначение соединения указывает (читая слева направо):
•способ центрирования: d – по внутреннему диаметру, D – по наружному диаметру, b – по боковым граням (в примере на рисунке это – d);
•через тире – количество шлицов (в примере равное 6);
•внутренний диаметр. При центрировании по этому диаметру также приводятся допуски для вала и втулки (в примере, для соединения в сборе – 28 H7/g6), в противном случае допуски не указываются и назначаются как на свободный размер;
•наружный диаметр с допусками для вала и втулки (в примере, для соединения в сборе –
34 H12/a11);
•ширину шлица с допусками для вала и втулки (в примере, для соединения в сборе –
7 D9/k7).
Посадки выбираются по рекомендациям в зависимости от условий работы.
Шлицевое соединение, по сравнению со шпоночным, имеет значительно большую нагрузочную способность, а вал – также и прочность. Детали хорошо центрируются. Недостатком является повышенная трудоемкость изготовления, однако не существенная в серийном производстве.
Эвольвентное шлицевое соединение (ГОСТ 6033) представляет собой эвольвентную зубчатую передачу с внутренним зацеплением и передаточным числом равным единице. Отличие заключается в том, что профильный угол берут равным αo =30о и уменьшенную высоту зуба. Это соединение более технологично и обладает повышенной прочностью, но поскольку фасонные отверстия очень сложно шлифовать, то применяется при твердости
втулки HRC<40.
Треугольное шлицевое соединение при-
меняют при стесненных диаметральных габаритах и, в основном, для увеличения сцепления между валом и втулкой при посадке. Мелкие шлицы на валах накатывают.
Все из перечисленных видов шлицевых Рис.8.56 – Торцевое шлицевое соединение соединений нуждаются в осевой фиксации.

165
При нарезании шлицов на валах (рис. 8.55а) они могут заканчиваться сбегом (его размер обеспечивается инструментом) или проточкой. В последнем случае рабочая длина шлицом меньше, но создается осевой упор втулки в буртик вала.
При соединении встык соосно расположенных деталей используют торцевые шлицы, нарезаемые на торцах деталей. Часто такой вид соединения называется кулачковым, а шлицы – кулачками. Торцевые шлицы могут иметь различную форму. Один из вариантов с образующими шлицов, сходящимися в центре, показан на рис. 8.56. Шлицы по окружности могут располагаться не только равномерно, но и выполняться в виде одиночных выступов, сопряженных со впадиной на торце другой детали.
Торцевое соединение компактно, но шлицы нагружаются неравномерно, необходимо осевое стопорение, особенно если боковые грани шлицов наклонены и возможно появление осевой распорной силы.
8.5.3 Профильные соединения
Профильное соединение относится к разъемным. Оно обеспечивает фиксацию в окруж-
ном направлении соосно расположенных |
|
деталей благодаря некруглой форме попе- |
|
речного сечения сопрягаемых поверхно- |
|
стей. Многообразие таких форм неограни- |
|
ченно (так, шлицевое соединение можно |
|
рассматривать как один из вариантов), но |
а) |
наибольшее распространение получили |
|
призматические и профильные с выпук- |
|
лым контуром формы. |
|
Основные виды форм поперечного се- |
|
чения деталей в призматических соедине-
ниях показаны на рис. 8.57а. Здесь нагрузка (крутящий момент Т) передается либо лысками (z =1, 2), либо плоскими гранями рабочих поверхностей (z>2). В соединениях с лысками центровка деталей осуществляется по цилиндрической поверхности, а
в многогранных – по граням. Плоские поверхности на валах фрезеруют или строгают, а в точных соединениях – дополнительно шлифуют. Отверстия строгают либо обрабатывают протягиванием (при серийном производстве).
Призматические соединения обладают средней нагрузочной способностью. Они сложны в обработке, особенно если рабочие поверхности должны иметь высокую твердость. Из-за возникновения радиальных распорных сил существенна деформация деталей. Такие соединения удобны на концевых участках валов, как показано на рис. 8.57б при z =2 (здесь осевая фиксация создается затяжкой гайки и упором втулки в буртик вала. Чтобы гарантировать такой упор либо на валу должна быть проточка, либо во втулке – фаска или расточка).
Рабочие поверхности профильных соединений образованы циклоидальными кривыми. Они технологичны и позволяют вести точную обработку при высокой их твердости. Соединение, по сравнению с призматическим, имеет пониженную нагрузочную способность. На рис. 8.58 показано три вида профильных соединений.
Основным видом отказа соединений является обмятие рабочих поверхностей деталей (вала или втулки, той у которой ниже прочность). Также, из-за действия распорных сил, необходима проверка втулки на прочность и жесткость.

166
8.5.4 Штифтовые соединения
Штифтовое соединение относится к разъемным. Оно осуществляется посредством штифта, вставляемого в отверстие, которое проходит сквозь соединяемые детали. Стандартизированы штифты конической и цилиндрической форм.
Конические штифты благодаря самоторможению хорошо фиксируются в отверстии (но если угол наклона конуса меньше угла трения) и удобны при разборке. Цилиндрические штифты в отверстии фиксируются посредством натяга либо иным способом (например, стопорными кольцами, изготовлением прорези на конце штифта и последующем расклинивании паза и т.п.). Они сложнее удаляются из отверстия, особенно если оно глухое.
Различают три способа установки штифтов: в осевом, радиальном и тангенциальном направлениях.
При осевой установке штифтов их располагают в плоскости стыка соединяемых деталей, вдоль образующей (рис. 8.59а). Соединение фиксирует детали в окружном направлении и изза сложности выемки штифта часто относят к неразъемным. Отверстие под штифт сверлится (и развертывается, для получения требуемой точности посадки) “по месту”, в собранном узле. При этом доступ инструмента к плоскости стыка должен быть удобным, а твердость материалов соединяемых деталей во избежание увода сверла – примерно одинаковой. Соединение аналогично шпоночному, но более технологично и создает меньшую концентрацию напряжений. С другой стороны, нагрузочная способность штифтового соединения меньше, а круглая форма штифтов создает распорную силу, нарушающую центровку деталей (при свободной их посадке).
При радиальной установке штифтов их располагают в отверстии, пронизывающем соединяемые детали радиально. Соединение обеспечивает полную фиксацию деталей. Штифты могут располагаться в сквозном (рис. 8.59) или глухом (рис. 8.59в) радиальном отверстии, либо, при сложности радиального подвода инструмента, – наклонно (рис. 8.59г). Соединение – простое, но требует совместной обработки деталей, создает сильную концентрацию напряжений и заметно ослабляет прочность вала, а потому имеет невысокую нагрузочную способность.
При тангенциальной установке штифтов их располагают в поперечном сечении по хорде. По свойствам это соединение аналогично соединению радиальными штифтами, но обладает более низкой нагрузочной способностью.
Для повышения нагрузочной способности в соединении могут устанавливать несколько штифтов.
При соединении по плоским поверхностям стыка штифты могут использоваться как направляющие. При этом они не должны быть силовым элементом и передавать нагрузки.
Отказы штифтового соединения связаны с обмятием рабочих поверхностей штифтов и соединяемых де-
талей и/или со срезом штиф- а) та по поверхности стыка этих деталей.
б) |
в) |
г) |
Рис.8.59 – Штифтовые соединения с осевой (а), радиальной (б,в) и наклонной (г) установкой штифтов
167
8.5.5 Фрикционные соединения
Фрикционные соединения обеспечивают полную фиксацию соосно расположенных деталей посредством сил трения (силовое замыкание). По способу создания контактного давления (натяга), приводящего к появлению сил трения, соединения подразделяются на прессовые по цилиндрической и конической поверхностям и клеммные.
Цилиндрическое соединение с натягом. Характеризуется номинальным диаметром d посадочной поверхности, длиной участка контакта l, величиной натяга и коэффициентом трения. На свойства соединения также влияет величина шероховатости сопрягаемых поверхностей.
Наименьшая величина натяга определяется из условия передачи внешней нагрузки для неблагоприятного сочетания величин параметров, имеющих разброс. Наибольшая величина натяга ограничивается прочностью и допустимой деформацией деталей, и прежде всего – втулки. Предпочтительны небольшие величины натяга и повышенная точность изготовления сопрягаемых поверхностей, поскольку при повышенных натягах:
•увеличивается вероятность наступление отказа вследствие разрушения деталей или недопустимой их деформации (например, заклинивание подшипника при его запрессовке);
•усложняется процесс сборки соединения и снижается вероятность последующей его разборки без повреждения. По этой причине соединение с натягом часто относят к неразъемным;
•уменьшается эффективность использования натяга из-за падения величины коэффициента трения вследствие обмятия микронеровностей при сборке;
•разброс величины натяга (допуск сопряжения), равный сумме допусков на сопрягаемые детали, ведет к существенному разбросу величины нагрузочной способности и прочностных свойств. С другой стороны, допуск сопряжения должен быть ограничен предельно допус-
тимыми величинами натяга.
На степень сцепления деталей в соединении влияют температурная деформация (но нужно учитывать разность в коэффициентах линейной температурной деформации вала и втулки) и действие дополнительных внешних сил, таких как, например, центробежных.
Сборка соединения осуществляется запрессовкой или тепловой сборкой.
При тепловой сборке за счет предварительной температурной деформации (уменьшения диаметра вала и увеличения диаметра отверстия втулки) уменьшают начальный натяг, в пределе – до получения зазора. Для этого, например, используют охлаждение вала в твердой углекислоте или жидком азоте и нагрев втулки (детали с отверстием) в печи или в горячем масле. При выборе температуры нагрева или охлаждения учитывают, чтобы физикомеханические свойства материала при этом не изменялись. Тепловая сборка не требует больших усилий запрессовки, в меньшей степени сминаются микронеровности.
Для облегчения запрессовки предусматривают направляющие конусы или посадочные пояски (подробнее – в разделе “Валы”). При одновременной посадке по нескольким поверхностям необходима предварительная взаимная центровка. При запрессовке в глухие отверстия следует обеспечить выход воздуха, иначе возможен разрыв втулки.
Для улучшения свойств прессового соединения (особенно при большой величине натяга) применяют сборку гидропрессованием: к контактирующим поверхностям изнутри по каналам под давлением подают жидкость, которая распирает детали и облегчает сборку.
Детали, соединенные посредством натяга, впоследствии недопустимо подвергать термообработке. В точных узлах после сборки выполняют чистовую обработку, либо начальную форму деталей делают такой, чтобы после сборки деформированные поверхности детали приняли нужную форму.
Осевое положение детали при запрессовке контролируют упором в буртик вала, либо совпадением торцев вала и отверстия детали, либо съемными дистанционными кольцами.
Цилиндрическое прессовое соединение просто в изготовлении, хорошо центрирует дета-

168
ли. К недостаткам относится большое рассеяние параметров, характеризующих нагрузочную способность и прочность (прежде всего из-за рассеяния размеров деталей и величины коэффициента трения), сложность сборки и разборки.
Основными видами отказов прессового соединения являются разрушение или недопустимая деформация соединяемых деталей, нарушение сцепления, что, однако, вызывается нерасчетными условиями работы и сборки. При циклическом нагружении соединения у торца втулки из-за неравномерной по длине деформации появляется участок проскальзывания, вызывающий фреттинг-коррозию и понижение усталостной прочности вала.
Соединение с натягом по конической поверхности. Здесь величина натяга, а следова-
тельно, и нагрузочная способность создается благодаря расклинивающему эффекту и регулируется посредством усилия запрессовки. Соединение просто собирается и разбирается, поэтому относится к разъемным. Посадка втулки на вал создается запрессовкой (рис. 8.60а, редко разбираемые соединения), либо затяжкой, например, гайкой (рис. 8.60б).
Соединение характеризуется углом конуса 2α или углом наклона α . Их малая величина позволяет создать большой натяг, обеспечивает хорошее самоторможение, но увеличивает неопределенность осевого положения втулки относительно вала, повышает опасность наступления разрушения при случайном превышении предельной величины усилия запрессовки.
При сборке величина натяга оценивается по величине силы запрессовки или крутящего момента на гайке, либо по осевому положению детали.
При невозможности изготовления конической сопрягаемой поверхности деталей или не-
а) б)
Рис.8.60 – Соединение с натягом по конической поверхности
обходимости перемещения втулки вдоль вала применяют соединение посредством промежуточных конических колец. Для улучшения плотности обхвата контактирующих поверхностей и легкости перемещении втулки в процессе монтажа промежуточное кольцо могут выполнять разрезным, т.е. цианговым (рис. 8.61).
Клеммные соединения. Здесь натяг создается стягиванием разрезной втулки, например, клеммными болтами (рис. 8.62). Соединение – разъемное, имеет невысокую нагрузочную способность, но просто при сборке и в эксплуатации.
|
|
|
|
|
|
Рис. 8.61 – Цианговое соединение |
|
Рис. 8.62 – Клеммное соединение |

169
8.5.6 Сварные соединения
Сварное соединение обеспечивает полную взаимную фиксацию деталей. Соединение – неразъемное и основано на использовании сил молекулярного сцепления. Сварка ведется с нагревом деталей. По характеру осуществления соединения к сварке близко клеевое соединение. Его достоинство – отсутствие необходимости в нагреве.
Применение сварных конструкций позволяет в наибольшей мере снизить материалоемкость сборных изделий. Сварка технологична и особенно эффективна в единичном и мелкосерийном производстве. К недостаткам сварных конструкций относятся коробление соединяемых элементов вследствие местного нагрева шва и последующего неравномерного его остывания, нестабильность качества шва, возникновение концентрации напряжений в шве (но ее можно заметно уменьшить последующей механико-термической обработкой шва). Сварные конструкции ответственного назначения нуждаются в последующей термической и чистовой механической обработках.
Число видов сварки достаточно велико. Их выбор зависит от вида и марки материала, размеров и формы деталей, уровня требований к качеству шва и других условий. Основной характеристикой соединения служит суммарная длина сварного шва.
В зависимости от взаимного расположения соединяемых деталей различают четыре вида сварных соединений (ГОСТ 5264):
•стыковые соединения. В месте соединения детали лежат в одной плоскости (рис. 8.63а). По стандарту соединение обозначается буквой С и устанавливается 25 их разновидностей (С1...С25), различающихся формой подготовки кромок (наличие отбортовки, скоса кромок с одной или двух сторон и т.д.);
•угловые соединения. Здесь кромки поверхностей соединяемых деталей перпендикулярны или наклонены друг другу (рис. 8.63 б). Соединение обозначается буквой У и устанавливается 15 их разновидностей (У1...У15);
•тавровые соединения. Плоскость одной соединяемой детали соприкасается торцем с плоскостью другой детали и перпендикулярна или наклонна к ней (рис. 8.63 в). Соединение обозначается буквой Т и устанавливается 16 их разновидностей (Т1...Т16);
•нахлесточные соединения (внахлест). Поверхности деталей частично накладываются друг на друга (рис. 8.63г). Соединение обозначается буквой Н и устанавливается 8 их разновидностей (Н1...Н8).
Сварная деталь является сборочной единицей, и на чертеже ее элементы штрихуются в разных направлениях. На сборочном чертеже изделия или чертеже его общего вида все элементы сварной детали уже штрихуются в одном направлении. Обозначение сварного соединения (ГОСТ 2.312) приводят на линии-выноске, которую проводят от линии шва. Для лицевого шва обозначение располагают над полкой (рис. 8.64а), а для шва с оборотной к изображенной на чертеже стороны – под полкой (рис. 8.64б). В состав обозначения входят (соответственно представленным на рисунке номерам прямоугольников):
а) б)
в) г)
Рис.8.63 – Виды сварных соединений: а – стыковое, б – угловое, в – тавровое, г – внахлест

1. |
Знаки шва по замкнутой линии (О) и шва, выпол- |
|
|
|
|
|
|
|
|
|
|
|
|
|
|
|
|
|
|
|
170 |
|
||||
|
|
|
|
|
|
|
|
|
|
|
|
|
|
|
|
|
|
|
|
|
|
|
|
|||
няемого по монтажному чертежу (T). |
|
|
|
|
|
|
|
|
|
|
|
|
|
|
|
|
|
|
|
|
|
|
|
|
||
2. |
Обозначение стандарта на типы и конструктивные |
|
|
|
|
|
|
|
|
|
|
|
|
|
|
|
|
|
|
|
|
|
|
|
|
|
|
|
|
|
2 |
|
|
3 |
|
|
4 |
|
|
5 |
|
|
6 |
|
|
|
|||||||
элементы швов. Например, ГОСТ 5264 на швы, выполнен- |
|
|
|
|
|
|
|
|
|
|
|
|
|
|
|
|||||||||||
а) |
|
1 |
|
|
|
|
|
|
|
|
|
|
|
|||||||||||||
|
|
|
|
|
|
|
|
|
|
|
|
|
|
|
|
|
|
|
|
|
|
|||||
ные ручной дуговой сваркой. |
|
|
|
|
|
|
|
|
|
|
|
|
|
|
|
|
|
|
|
|
|
|
|
|||
|
|
|
|
|
|
|
|
|
|
|
|
|
|
|
|
|
|
|
|
|
|
|
||||
3. |
Буквенно-цифровое обозначение вида шва. |
|
|
|
|
|
|
|
|
|
|
|
|
|
|
|
|
|
|
|
|
|
|
|
|
|
4. |
Знак |\ и размер катета шва (только для угловых |
|
|
|
|
|
|
1 |
|
|
|
|
|
|
|
|
|
|
|
|
|
|
|
|
|
|
швов). |
|
|
б) |
|
|
|
2 |
|
|
3 |
|
|
4 |
|
|
5 |
|
6 |
||||||||
5. |
Вспомогательные знаки: |
|
|
|
|
|
|
|
|
|
|
|
|
|
|
|
||||||||||
|
|
|
|
|
|
|
|
|
|
|
|
|
|
|
|
|
|
|
|
|
|
|
|
|||
|
|
|
|
|
|
|
|
|
|
|
|
|
|
|
|
|
|
|
|
|
|
|
|
|||
|
/ – шов прерывистый или точечный с цепным распо- |
|
|
Рис.8.64 – Обозначения сварных |
||||||||||||||||||||||
ложением; |
|
|
|
|
|
|
|
|
соединений |
|
|
|
|
|
||||||||||||
|
Z – шов прерывистый или точечный с шахматным рас- |
|
|
|
|
|
|
|
|
|
|
|
|
|
|
|
|
|
|
|
|
|
|
|
|
|
положением; |
|
|
|
|
|
|
|
|
|
|
|
|
|
|
|
|
|
|
|
|
|
|
|
|
||
|
– шов по незамкнутой линии. |
|
|
|
|
|
|
|
|
|
|
|
|
|
|
|
|
|
|
|
|
|
|
|
|
|
6. |
Вспомогательные знаки: |
|
|
|
|
|
|
|
|
|
|
|
|
|
|
|
|
|
|
|
|
|
|
|
|
|
|
o |
– усиление шва; |
|
|
|
|
|
|
|
|
|
|
|
|
|
|
|
|
|
|
|
|
|
|
|
|
ω – наплывы и неровности шва обработать с плавным переходом к основному металлу. На рис. 8.65 показан пример обозначения сварного углового соединения, которому соот-
ветствует упрощенное изображение, приведенное на рис. 8.63б.
Основными видами отказа сварных соединений являются разрушение шва, прочность которого, особенно при циклическом нагружении, меньше прочности основного материала.
ГОСТ 5264-69 У4 – 6
Рис. 8.65 – Пример изображения углового сварного соединения
8.5.7 Заклепочные соединения
Заклепочное соединение относится к неразъемным. Детали крепятся посредством стержня с головками на концах (заклепкой). Первоначально одна из головок отсутствует, и заклепка свободно вставляется в отверстие, предварительно просверленное в соединяемых деталях. После расклепывания выступающего конца стержня происходит плотное прижатие деталей друг к другу. Заклепочные соединения стали широко применяться с 30-х годов 18 века.
Заклепки позволяют создать прочное компактное соединение двух и более деталей, выполненных из любых материалов. Соединение обладает хорошей стабильностью свойств. К недостаткам относятся высокая трудоемкость сборки: все отверстия в деталях должны выполняться в сборе, необходимо клепальное оборудование. При этом большое число отверстий под заклепки ослабляет конструкцию и создает значительную концентрацию напряжений.
Различают следующие виды заклепок:
•стержневые с полукруглыми (рис. 8.66а), потайными и полупотайными головками, применяемые для силовых соединений. В зависимости от условий работы возможно выполнение “прочного” соединения (в силовых конструкциях, например, рамах), либо “прочноплотного” соединения (восприятие внешних усилий и обеспечение герметичности соединения, например, в резервуарах);
•пистонные (рис. 8.66б), применяемые для крепления мягких материалов;