
Детали машин и основы конструктирования
.pdf41
гами или брусками, притирами и другим специальным инструментом. Выбор инструмента и, следовательно, оборудования определяется видом материала, формой обрабатываемых поверхностей, потребным их качеством и точностью и, не в последнюю очередь, производственными возможностями. Это может быть слесарная обработка, точение, фрезерование, сверление, зенкерование, развертывание, протягивание, шлифование, хонингование, суперфиниш, притирка, полирование и иные виды обработки. В зависимости от точности и качества поверхности различают следующую обработку:
•обдирочная. Точность обработки составляет 16...17 квалитет, шероховатость поверхностей
– более Ra80 (Rz320). Применяют для обработки грубых поковок и отливок как подготовительная операция;
•черновая. Точность обработки составляет 12...14 квалитет, шероховатость поверхностей – Ra20...80 (Rz80...320). Применяют для обработки деталей с невысокими требованиями по точности и качеству поверхностей;
•получистовая. Точность обработки составляет 9...12 квалитет, шероховатость поверхностей – Ra 6,3...32 (Rz20...125). Применяют для обработки деталей со средними требованиями к точности форм и расположения поверхностей;
•чистовая. Точность обработки составляет 4...8 квалитет, шероховатость поверхностей – до Ra 0,1 и зависит от вида обработки. Так, при обработке режущим инструментом (зенкерование, чистовое фрезерование и точение) характеристики ниже по сравнению с абразивной обработкой (шлифование). Чистовая обработка обеспечивает высокие требования к точности форм и расположения поверхностей и часто является окончательной;
•тонкая. Служит для получения особо точных размеров, чистоты поверхности и высоких требований к отклонениям форм и расположения поверхностей деталей. Выполняется с целью обеспечения как заданной точности, так и иных требований, например, повышенного
сопротивления усталостной прочности.
Механическая обработка позволяет удовлетворить разнообразным требованиям к качеству деталей, но связана с разрушением поверхностного слоя. Это не всегда допустимо, так как ведет к образованию в новом поверхностном слое сети микротрещин, вызывающих концентрацию напряжений, снижение антикоррозионных свойств материала и т.п. Обработке могут подвергаться материалы, твердость которых меньше твердости инструмента. Но, с другой стороны, плохо обрабатываются и вязко-пластичные материалы, “засаливающие” шлифовальные круги, налипающие на инструмент.
Механическая обработка без снятия поверхностного слоя. Производится обкатывани-
ем поверхности роликами и шариками, накатыванием резьбы, зубьев и рифлений, дробеструйной обработкой, чеканкой и т.п. Обычно, это – завершающие операции и выполняются после чистовой обработки. Такая обработка существенно повышает поверхностную прочность, твердость и износостойкость деталей, а также чистоту обработанной поверхности. Точность обработки повышается незначительно. Обработке подвергаются материалы, допускающие пластическую деформацию в холодном состоянии.
Электрофизическая и электрохимическая обработка. Достаточно трудоемка, но позво-
ляет обрабатывать особо прочные и твердые материалы и детали сложной формы. Подвергаемые обработке материалы должны быть токопроводящими.
Существуют и другие виды обработки, основанные на новейших технологиях. Как правило, они – узкоспециализированные по материалам и оборудованию.
Обрабатываемость дает конструкции право на существование. По этой причине каждое конструкторское решение должно быть увязано с технологией, т.е. четко указан способ получения каждой поверхности детали и подтверждена допустимость его применения для выбранного материала.
Упрочняемость.
Упрочняемость – обобщенное название, под которым подразумевается возможность
42
улучшения или изменения механических (прочность), физических (например, коэрцитивная сила) и химических (например, коррозионная стойкость) свойств материала всей или части детали. Это позволяет более полно использовать свойства материалов, хотя и требует специального оборудования и заметно увеличивает стоимость изделия. Упрочняемость достигается методами термической (ТО) и химико-термической (ХТО) обработки и обычно проводится для металлов.
Термообработка включает следующие наиболее распространенные виды:
•отжиг, т.е. нагрев до определенной, свойственной конкретному материалу температуры с последующим медленным охлаждением с целью получения равновесной (устойчивой) структуры. Используется для уменьшения твердости материала и повышения его обрабатываемости, снятия внутренних напряжений, достижения однородности структуры. Длительность отжига составляет 10...20 часов;
•нормализация, т.е. нагрев с последующим охлаждением на спокойном воздухе. Операция аналогична отжигу, но выполняется за более короткий срок. Структура материала не успевает полностью прийти в равновесное состояние. Механические характеристики – несколько повышенные по сравнению с отжигом;
•закалка, т.е. нагрев и последующее быстрое охлаждение с целью получения неравновесной структуры материала. Обеспечивает высокие механические характеристики (прочность и твердость), но повышает и хрупкость материала. В зависимости от глубины зоны прокаливаемости закалку подразделяют на объемную (деталь или ее часть закаливаются практически по всему сечению) и поверхностную (закаливается до большой твердости поверхностный слой при, обычно, вязкой сердцевине);
•улучшение, т.е. закалка с последующим высоким отпуском (нагрев до температуры ниже закалочной с последующим охлаждением). Снижает хрупкость закаленного материала. Получаемые механические характеристики выше, чем при нормализации, но ниже, чем при закалке;
•старение, т.е. естественное или специально вызываемое изменение свойств материалов со временем, связанное с перестройкой структуры материала в более устойчивое состояние.
Повышает прочность материала, но, в тоже время, и его хрупкость.
Не все материалы допускают термообработку. Кроме того, термообработка связана с нагревом деталей, что вызывает их коробление и необходимость чистовой обработки ответственных поверхностей.
Химико-термическая обработка связана с насыщением поверхностных слоев деталей различными элементами. Это улучшает такие свойства, как поверхностная твердость, прочность, износостойкость и коррозионная стойкость. Обработка экономит дорогостоящие материалы, позволяя получить требуемые высокие характеристики у обычных материалов, сокращает номенклатуру используемых в конструкции материалов. Наиболее распространены следующие виды химико-термической обработки:
•цементация, т.е. науглероживание поверхностного слоя глубиной от 0,5 до 2мм. Сопровождается последующей закалкой. Повышает твердость, износостойкость и предел выносливости. Процесс обработки достаточно трудоемкий и длительный, причем время обработки возрастает с увеличением глубины насыщения. При цементации возможно коробление детали, но достаточность толщины слоя насыщения допускает чистовую доводку;
•азотирование, т.е. насыщение поверхностного слоя азотом. Толщина слоя незначительна, и незначительно коробление. При насыщении происходит небольшое увеличение размеров детали вследствие набухания поверхностного слоя. Обеспечивает очень высокую поверхностную твердость, снижает чувствительность детали в месте обработки к концентрации напряжений (прочностное азотирование), либо повышает коррозионную стойкость (антикоррозионное азотирование). Однако поверхностный слой весьма хрупок и не выдерживает больших контактных и ударных нагрузок. Процесс очень длительный и дорогой;
43
•цианирование, т.е. насыщение поверхностного слоя одновременно углеродом и азотом в расплавленных солях цианистых соединений (дорогих и ядовитых). Сопровождается последующей закалкой. Толщина слоя до 0,3мм. Обработанные поверхности обладают высокой твердостью, прочностью и износостойкостью, но слегка коробятся и не допускают большого контактного давления;
•нитроцементация, т.е. насыщение поверхностного слоя углеродом и азотом в газовых средах. Сопровождается последующей закалкой. Толщина слоя может достигать 1мм. Обеспечивает свойства материала, как и после цианирования.
Существует ряд других способов обработки, связанные с насыщением поверхностного слоя алюминием (алитирование), серой (сульфидирование), бором (борирование), хромом (хромирование), титаном и т.п. Диффузионная обработка применяется для повышения коррозионной стойкости, жаростойкости, износостойкости и твердости. Выбор способа, прежде всего, зависит от имеющегося оборудования, отпущенного времени и средств.
Соединяемость.
Как правило, изделие состоит из нескольких деталей. Возможность их взаимного соединения и способы соединения зависят и от свойств материала, из которого эти детали изготовлены. Необходимо учитывать следующие основные факторы:
•чувствительность материала к концентрации напряжений, что важно при выполнении отверстий (например, под болты), пазов и т.п.;
•поверхностная контактная прочность при нормальном давлении и сдвиге (определяет допустимое давление по соединяемым поверхностям);
•допустимость нагрева или охлаждения. Характеризуется диапазоном рабочих температур, скоростью нагрева или охлаждения, порогом хладноломкости. Учитывается при тепловой сборке, сварке, работе в специальных условиях;
•адгезионные свойства, обеспечивающие свариваемость, паяемость и склеиваемость деталей из однородных и разнородных материалов;
•химическая совместимость материалов контактирующих поверхностей деталей. Проявляется в возможности образования парой материалов в условиях эксплуатации или хранения гальванических элементов и, как следствие, появления электрохимической коррозии.
Обеспечение экономических требований к конструкции.
Экономические требования определяют целесообразность использования того или иного материала. Они неразрывно связаны с функциональными и технологическими требованиями и учитывают следующие основные затраты:
•затраты на материал с учетом функциональной эффективности от его применения в изделии;
•затраты на изготовление детали заданной формы, с требуемыми точностью размеров и качеством поверхностей, физико-механическими и физико-химическими свойствами. Связано с таким понятием, как обрабатываемость материала. Обычно эти затраты составляют наибольшую долю в общей стоимости изделий;
•затраты на сборку изделия (косвенно определяются массо-габаритными характеристиками деталей и узлов изделия);
•затраты на обеспечение сохраняемости изделия, т.е. неизменяемости его характеристик и свойств составляющих его материалов при длительном хранении и транспортировке (затраты на предохранение от климатических воздействий, вибраций и толчков при перевозке и т.п.).
Понятие экономичности, как и технологичности, – относительное. Так, на стоимость ма-
териалов влияют его доступность, затраты на транспортировку, конъюнктура и т.п. Выбор способа изготовления и сборки определяется имеющимся оборудованием, квалификацией работников и т.п. И то, что может быть осуществимо на одном предприятии, не всегда реализуемо на другом. По этим причинам конструирование и, в том числе, выбор материала деталей, должны всегда быть привязаны к конкретной ситуации и производству.

44
6.Конструкционные материалы
Вкачестве конструкционных материалов применяют вещества, главным образом, в твердом состоянии. Их классификация возможна по разным признакам: естественные и искусственные, органические и неорганические и т.п. На рис. 6.1 приведена общепринятая классификация, основанная на совокупности признаков. Здесь все конструкционные материалы разбиты на три группы – металлы, неметаллы и составные материалы.
Металлы, в свою очередь, подразделяются еще на три основные группы (рис. 6.2):
•черные. Это сплавы на основе железа, они наиболее распространены, доступны и дешевы, обладают хорошими технологическими и прочностными свойствами;
•цветные. Эти металлы дороже, но их тепло- и электропроводность, антифрикционные свойства выше;
•легкие (хотя и относятся к цветным, но в силу особых механических характеристик их стоит выделить в отдельную группу). Металлы этой группы в среднем дороже черных, но они имеют значительно меньший удельный вес и, как следствие, повышенные удельные показатели прочности и жесткости.
Конструкционные
материалы
|
металлы |
|
|
|
неметаллы |
|
|
составные |
|
|
|
|
|
|
|
|
|
материалы |
|
|
|
|
|
|
|
|
|
|
|
|
|
|
|
|
|
|
|
|
|
|
см.рис.8 |
|
|
- пластмассы: |
|
- биметаллы |
|||
|
|
|
|
термореактивные, |
|
- композиты |
|||
|
|
|
|
термопластичные |
|
- покрытия: |
|||
|
|
|
|
- резины |
|
металлические, |
|||
|
|
|
|
- другие |
|
неметаллические, |
|||
|
|
|
|
|
|
|
|
химические, |
|
|
|
|
|
|
|
|
|||
|
|
|
|
|
|
|
|
электрохимические |
|
|
|
|
|
|
|
|
|
|
|
Рис. 6.1. Основные группы конструкционных материалов
Материалы составляют физическую основу любого изделия. Естественно, что их описание обязательно присутствует в документации на проектируемую систему. Наиболее грамотно описание представлять в следующем виде: указывается название (марка) материала и наименование документа, определяющего предельные значения физических, механических, химических и других характеристик, состав, условия изготовления, контроля и т.д. Поскольку на практике материал часто поступает к потребителю в форме полуфабриката (проката, отливки), то также необходимо приводить сведения о его состоянии и виде заготовки, указывать регламентирующие их документы.
Например, сталь 45 ГОСТ 1050-88. Здесь сталь 45 – номинальный параметр (наименование – сталь, марка – 45), ГОСТ 1050-88 – документ (в данном случае – стандарт), регламентирующий предельные отклонения свойств и характеристик.
6.1 Группа черных металлов
Группа черных металлов подразделяется на чугуны и стали. К чугунам принято относить сплавы железа с углеродом, когда содержание углерода превышает 2,14%. При меньшем содержании углерода такие сплавы относят к сталям.
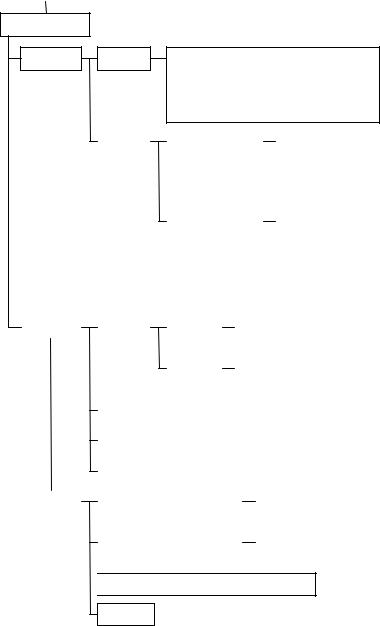
45
металлы
черные |
чугуны |
- серые, ГОСТ 1412-85 |
-высокопрочные, ГОСТ 7293-85
-ковкие, ГОСТ 1215-79
-жаростойкие, ГОСТ 7769-82
-антифрикционные, ГОСТ 1585-85
|
|
стали |
|
|
углеродистые |
|
|
- обыкновенные, ГОСТ 380-88 |
||||||
|
|
|
|
|
|
|
|
|
|
|
|
- качественные конструкцион- |
||
|
|
|
|
|
|
|
|
|
|
|
|
|||
|
|
|
|
|
|
|
|
|
|
|
|
ные, ГОСТ 1050-88 |
||
|
|
|
|
|
|
|
|
|
|
|
|
- литейные, ГОСТ 977-88 |
||
|
|
|
|
|
|
|
|
|
|
|
|
- автоматные, ГОСТ 1414-75 |
||
|
|
|
|
|
|
|
|
|
|
|
|
|
|
|
|
|
|
|
|
легированные, |
|
- качественные, |
|||||||
|
|
|
|
|
ГОСТ 4543-71 |
|
|
высококачественные, |
||||||
|
|
|
|
|
|
|
|
|
|
|
|
особовысококачественные |
||
|
|
|
|
|
|
|
|
|
|
|
|
- низколегированные, |
||
|
|
|
|
|
|
|
|
|
|
|
|
среднелегированные, |
||
|
|
|
|
|
|
|
|
|
|
|
|
высоколегированные |
||
|
|
|
|
|
|
|
|
|
|
|
|
- литейные |
||
|
|
|
|
|
|
|
|
|
|
|
|
|
||
цветные |
|
медные |
|
|
бронзы |
|
- оловянистые, ГОСТ 613-79 |
|||||||
|
|
сплавы |
|
|
|
|
- безоловянистые, ГОСТ 493-79 |
|||||||
|
|
|
|
|
|
|||||||||
|
|
|
|
|
|
|
|
|
|
|
|
|
||
|
|
|
|
|
|
|
|
|
|
|
|
|
||
|
|
|
|
|
латуни |
|
- литейные, ГОСТ 17711-93 |
|||||||
|
|
|
|
|
|
|
- деформируемые, ГОСТ 15527-70 |
|||||||
|
|
|
|
|
|
|
||||||||
|
|
|
|
|
|
|
|
|
|
|
||||
|
|
|
|
|
|
|
|
|
|
|||||
|
|
цинковые сплавы, ГОСТ 21437-75 |
|
|
||||||||||
|
|
|
|
|
|
|
|
|
|
|
|
|||
|
|
|
|
|
|
|
|
|
|
|
||||
|
|
баббиты, ГОСТ 1320-74 |
|
|
|
|
|
|
||||||
|
|
|
|
|
|
|
|
|
|
|
|
|
|
|
|
|
|
|
|
|
|
|
|
|
|
|
|
|
|
|
|
другие |
|
|
|
|
|
|
|
|
|
|
|
|
|
|
|
|
|
|
|
|
|||||||
|
|
|
|
|
|
|
||||||||
легкие |
|
алюминиевые сплавы |
|
|
|
- литейные, ГОСТ 2685-75 |
||||||||
|
|
|
|
|
|
|
|
|
|
- деформируемые, ГОСТ 8617-75 |
||||
|
|
|
|
|
|
|
|
|
|
|||||
|
|
|
|
|
|
|
|
|||||||
|
|
магниевые сплавы |
|
|
|
- литейные |
|
|||||||
|
|
|
|
|
|
|
|
|
|
- деформируемые |
|
|||
|
|
|
|
|
|
|
|
|
|
|
||||
|
|
|
|
|
|
|
|
|
|
|
|
|
|
|
титановые сплавы, ГОСТ 19807-74
другие
Рис. 6.2. Основные виды металлов
6.1.1 Чугуны
Чугуны, по сравнению со сталями, дешевле, имеют повышенные литейные свойства, но плохо свариваются, обладают меньшей прочностью, жесткостью и пластичностью. Так, модуль упругости чугуна Е=(0,6...1,6) 105 МПа, что в 1,2...3 раза ниже, чем у сталей, и при этом не является константой. Потери на внутреннее трение (гистерезис) в 5...20 раз выше, чем у сталей, что обеспечивает эффективное гашение возникающей в деталях машин вибрации.
Главной особенностью внутреннего строения чугунов является наличие включений свободного углерода в виде графита (рис. 6.3). Фактически каждое такое включение нарушает сплошность металлической основы чугуна, то есть играет роль микротрещины. В связи с этим форма графитовых включений оказывает очень сильное влияние на свойства чугуна: если включения имеют форму пластинок, то есть являются плоскими трещинами с острыми краями, то металлическая основа оказывается сильно поврежденной, а чугун в целом имеет низкую прочность и является хрупким. Если же форма включений близка к сферической, то они нарушают сплошность металла значительно меньше, поэтому и механические свойства такого чугуна заметно выше.

46
Присутствие в структуре чугуна графитных включений обеспечивает придание ему специфических свойств: нечувствительность к концентрации напряжений, устойчивость к коррозии в водной среде и на воздухе, высокие демпфирующие свойства, низкий коэффициент трения. В зависимости от внутреннего строения, состава и технологии получения чугуны подразделяются на серые, высокопрочные, ковкие, антифрикционные и жаростойкие.
Рис. 6.3. Форма графитных включений в чугунах различных типов
Серые чугуны, ГОСТ 1412-85. Самые дешевые и доступные, имеют хорошие литейные свойства и обрабатываемость. Основная особенность – наличие в структуре свободного углерода в виде достаточно крупных пластинок графита. Заготовки деталей из этого материала, как правило, получают отливкой, причем прочностные свойства чугуна с уменьшением скорости охлаждения отливки (в деталях большой массы и с толстыми стенками) понижаются. Модуль упругости материала составляет Е=(0,6...1,2) 105 МПа, плотность ρ =6,8...7,2 г/см3.
Серые чугуны маркируются буквами СЧ и двумя цифрами, показывающими среднюю величину предела прочности на растяжение в кГс (МПа 10) – от СЧ00 (в этой марке прочность не регламентирована) до СЧ45. Так, предел прочности СЧ15 равен σв ≈150 МПа. С ростом прочности, т.е. значащих цифр, твердость чугуна также возрастает приблизительно с 160НВ до 260НВ, но литейные свойства ухудшаются.
Потери на внутреннее трение у серых чугунов по сравнению с остальными марками чугунов – наибольшие. А наличие графитовых включений придает серому чугуну антифрикционные свойства.
С целью повышения прочности, износостойкости, коррозионной стойкости, снятия внутренних напряжений и других свойств серые чугуны модифицируют (легируют), т.е. добавляют в жидкий чугун небольшое количество присадок.
Высокопрочные чугуны, ГОСТ 7293-85. Получают легированием магнием или добавлением других специальных присадок и/или дополнительной термообработкой. Магний играет роль модификатора, то есть обеспечивает графитным включениям форму, близкую к шаровидной, благодаря чему механические свойства такого чугуна приближаются к свойствам углеродистых сталей, но литейные свойства выше (но ниже, чем у серых чугунов). Чугуны хорошо обрабатываются и упрочняются. Модуль упругости составляет Е=(1,6...1,9) 105 МПа,
твердость – 150НВ...360НВ, удельная ударная вязкость (при температуре 200С) аkcu – до
0,6 Мдж/м2.
47
Высокопрочные чугуны маркируются буквами ВЧ и числом, соответствующим среднему значению предела прочности на растяжение в кГс (МПа 10), например, ВЧ50. Основные марки чугунов лежат в пределах от ВЧ38 до ВЧ120.
Ковкие чугуны, ГОСТ1215-79. Очень трудоемки в изготовлении, но по сравнению с серыми чугунами имеют повышенные прочность, износостойкость и пластичность. Форма графитовых включений – хлопьевидная. Запаса пластичности недостаточно для обработки ковкого чугуна давлением и заготовку также получают отливкой. Модуль упругости чугуна Е=(1,6...1,9) 105 МПа, твердость – 100...250НВ.
Ковкий чугун маркируются буквами КЧ, двумя цифрами, соответствующих среднему значению предела прочности на растяжение в кГс (МПа 10), и числом, показывающим относительное удлинение δ . Например, КЧ45-6, его характеристики – σв ≈ 450 МПа и δ = 6%.
Жаростойкие чугуны, ГОСТ 7769-82. Получают легированием и специальной термообработкой. Сохраняют хорошие механические свойства и сопротивление окислению при температурах 500...1100 С. Обозначаются первыми буквами названия ЖЧ и видом и процентным содержанием легирующих добавок (обозначение добавок: С – кремний, Х – хром, Ю – алюминий, а буква Ш указывает на шаровидную форму графита, повышающую его прочность). Например, ЖЧЮ2ХШ, что означает – чугун жаростойкий, содержащий 2% алюминия, менее 1% хрома (в этом случае число процентного содержания отсутствует), графит шаровидной формы.
Антифрикционные чугуны, ГОСТ 1585-85. Получают в результате целенаправленной модификации серого, ковкого или высокопрочного чугунов. Дешевле многих металлических антифрикционных материалов, но требуют повышенной точности монтажа опорного узла и обильной смазки, не допускают больших скоростей скольжения. Обозначаются первыми буквами названия и порядковым номером в установленном ГОСТом перечне марок. Например, АЧС-1 – антифрикционный серый чугун, АЧВ-2 – антифрикционный высокопрочный чугун.
6.1.2 Стали
По химическому составу стали подразделяют на углеродистые и легированные. Введение легирующих добавок повышает стоимость сталей, но и улучшает механические, физические и химические свойства, что в итоге обеспечивает экономическую эффективность их применения в изделии. Стоит отметить, что модуль упругости у разных сталей практически одинаков и равен Е=(1,95...2,1) 105 МПа, плотность ρ ≈7,8 г/см3.
Общей для всех типов сталей является зависимость их механических свойств от содержания углерода: чем больше в стали углерода, тем сталь более прочная, твердая, но одновременно более хрупкая.
Углеродистые стали подразделяют на стали обыкновенного качества, качественные конструкционные и инструментальные. Отдельно, по технологическим свойствам также выделяют стали литейные (в конце обозначения ставится буква Л), автоматные и высококачественные (в конце обозначения ставится буква А).
Стали обыкновенного качества, ГОСТ 380-88. Это – наиболее дешевые стали, очень пластичные, хорошо свариваемые, но не подвергающиеся термообработке (в основном, из-за нестабильности химического состава), имеют невысокую прочность. Стали, в основном, по-
ставляются в виде проката. Удельная ударная вязкость (при температуре 200С) аkcu – до
1,0 Мдж/м2.
Стали этой марки обозначаются буквами Ст и номером в порядке возрастания прочности (от 0 до 6). Начиная с 4, номер уже соответствует среднему значению предела прочности в МПа, деленному на 100. С ростом номера марки пластичность падает. Стали поставляются трех видов:
•группа А, с гарантированными механическими свойствами;
•группа Б, с гарантированным химическим составом. В этом случае в начало обозначения
48
марки добавляется буква, указывающая на способ производства: М – мартеновский, К – конверторный. Например, МСт3, Кст4;
•группа В, с гарантированными механическими свойствами и химическим составом. В обозначении этих сталей добавляется буква В, например, Вст3.
Вобозначении также могут присутствовать буквы, характеризующие особенности производства: кп – сталь кипящая, не подвергнутая раскислению (наиболее дешевая, менее качественная), пс – полуспокойная, сп – спокойная, – и порядковый номер категории. Например, Ст3кп (первая категория не указывается), Ст3кп2.
Стали качественные конструкционные, ГОСТ 1050-88. Обладают более высокими ме-
ханическими характеристиками, допускают термическую и химико-термическую обработку. Стали маркируют двузначным числом (от 08 до 85), соответствующим среднему содержанию углерода в сотых долях процента. В ряде высокоуглеродистых сталей в обозначение входит буква Г, указывающая на содержание около 1% марганца. Примеры маркировок – сталь 08, сталь 45, сталь 65, сталь 65Г, сталь 20А (сталь высококачественная). Марганцовистые стали имеют повышенную прочность и износостойкость.
Прочность и твердость сталей зависят от марки и способа упрочнения. В состоянии поставки (обычно, это – отожженные или нормализованные стали) по мере возрастания доли углерода твердость повышается от 130НВ до 300НВ, увеличивается и прочность. Удельная
ударная вязкость (при температуре 200С) аkcu – до 0,6 Мдж/м2.
Литейные стали, ГОСТ 977-88. По составу соответствуют качественным конструкционным сталям, но имеют повышенные литейные свойства и предназначаются для получения заготовок литьем. Их механические характеристики несколько хуже, сложнее они и в обработке. В конце обозначения таких сталей указывается буква Л, например, сталь 35Л.
Автоматные стали, ГОСТ 1414-75. Обладают повышенной обрабатываемостью резанием, обеспечивают хорошее качество поверхности. Стали допускают термообработку, но плохо свариваются, имеют пониженные механические свойства, склонны к коррозии. Обозначение таких сталей начинается с буквы А. Например, А12.
Легированные стали, ГОСТ 4543-71. Введение легирующих элементов производят с целью улучшения или получения новых свойств, таких как прочность, коррозионная стойкость, износостойкость, жаропрочность, намагничиваемость, термостабильность и т.д. Удельная ударная вязкость (при температуре 200С) аkcu – до 2,0 Мдж/м2. Эффективность применения легированных сталей возрастает при использовании их в сочетании с термообработкой (для повышения механических характеристик).
В соответствии со стандартом в обозначении легированных сталей справа дополнительно приводится набор букв и чисел. Буквы указывают на название легирующего элемента: А (но если не крайняя справа или слева) – азот, Б – ниобий, В – вольфрам, Г – марганец, Д – медь, К
– кобальт, М – молибден, Н – никель, П – фосфор, Р – бор, С – кремний, Т – титан, Ф – ванадий, Х – хром, Ц – цирконий, Ч – редкоземельный металл, Ю – алюминий. Цифры после буквы показывают примерное процентное содержание данного легирующего элемента. Если же содержание менее 1% , то число отсутствует. Например, стали 40Х, 30ХН2ВФ. Возможны отступления в точности соблюдения маркировки.
Некоторые легированные стали, как и стали качественные конструкционные, выделены в особые группы:
•литейные легированные стали. В конце марки справа ставится буква Л, например, 40ХЛ;
•высококачественные стали. В конце марки справа ставится буква А, например, 20ХГСА;
•шарикоподшипниковые, особовысококачественные стали. В начале марки слева ставится буква Ш. Содержание легирующего элемента здесь приводится в десятых долях процента. Например, ШХ15 (содержание хрома порядка 1,5%);
•автоматные стали. В начале марки слева ставится буква А, например, А40Г;
•магнитные высококоэрцитивные стали. В начале марки слева ставится буква Е.
•и т.д.
49
Легированные стали сложнее обрабатываются, хуже свариваются. Их стоимость выше и зависит от содержания, вида и числа легирующих элементов.
По количеству добавок стали подразделяют на низколегированные (суммарное содержание легирующих добавок до 2,5%), среднелегированные и высоколегированные (суммарное содержание легирующих добавок свыше 10%). Низколегированные стали более доступны и относительно дешевые, позволяют получить достаточно высокие механические характеристики. Выбор конкретной марки легированной стали следует проводить, ориентируясь на возможность достижения особых свойств, которыми должна обладать изготовленная из нее деталь, а также наличие соответствующих экономических и производственных ресурсов пред- приятия-изготовителя продукции. Некоторые сравнительные характеристики разных материалов приведены ниже.
Для всестороннего обоснования выбора подходящей марки стали рекомендуем обратиться как к общемашиностроительным справочникам, так и к специальной литературе.
6.2Сплавы тяжелых цветных металлов
Вконструкциях наиболее распространены медные и цинковые сплавы и баббиты.
6.2.1 Медные сплавы
По сравнению с чистой медью медные сплавы имеют улучшенные конструкционные свойства, а потому и более распространены. Обладают высокими антифрикционными и декоративными свойствами, теплопроводностью, хорошо обрабатываются, но дороги. Сплавы подразделяются на бронзы и латуни.
Бронзы. Маркируются буквами Бр и буквенным обозначением дополнительных компонентов с последующими цифрами через тире, показывающими среднее содержание этих компонентов в процентах. Основные компоненты и их обозначение: олово (О), алюминий (А), бериллий (Б), железо (Ж), кремний (К), марганец (Мц), никель (Н), свинец (С), цинк (Ц), фосфор (Ф). В зависимости от их содержания бронзы подразделяют на оловянистые и безоловянистые
– свинцовистые, алюминиевые, бериллиевые и другие. Исключение олова в безоловянистых бронзах (за исключением бериллиевой бронзы) преследует цель удешевления этого материала.
Оловянистые бронзы, ГОСТ 613-79 и другие стандарты и нормативные документы. Основным и обязательным компонентом является олово. Например, БрОФ10-1, содержащая 10% олова и 1% фосфора. Бронзы хорошо отливаются (заготовки получают литьем), но плохо обрабатываются давлением. Благодаря олову имеют высокие антифрикционные свойства. Устойчивы к коррозии в атмосферных условиях, пресной и морской воде. Твердость бронз порядка НВ70...100, модуль упругости Е=(6...10) 104 МПа, теплопроводность
(0,06...0,12) Вт/(м 0С).
Алюминиевые бронзы, ГОСТ 18175-78. Например, БрАЖ9-4. Относительно дешевые, имеют повышенные механические свойства (твердость порядка 80НВ...120НВ) и химическую стойкость. Антифрикционные свойства хуже и, при этом, необходима повышенные точность и качество обработки поверхностей подвижно сопряженных деталей.
Свинцовистые бронзы. Высококачественный антифрикционный материал, но очень мягкие (НВ 40...60) и в конструкциях применяется в виде покрытий на твердую основу. Пример обозначения марки – БрС30.
Бериллиевые бронзы. Очень дороги, но обладают наибольшей среди бронз и латуней прочностью (в 1,5...2 раза выше, чем у алюминиевых бронз), термостабильностью, химической стойкостью, хорошо свариваются и обрабатываются резанием. У этих бронз практически отсутствует гистерезис. Пример обозначения марки – БрБ2.
По своим свойствам к бериллиевым бронзам близки кремнистые бронзы, например, БрКМц3-1.
Латуни. Сплавы меди с цинком. По способам обработки подразделяются на литейные (ГОСТ 17711-93) и деформируемые (ГОСТ 15527-70, обрабатываемые давлением). По составу
50
латуни разделяются на двойные (простые сплавы, содержащие приблизительно 2/3 меди и 1/3 цинка) и сложные (дополнительно содержат добавки свинца, железа, марганца, алюминия и олова). Двойные латуни маркируют буквой Л и цифрой, показывающей среднее процентное содержание меди. Например, Л62, состоящая из 62% меди и 38% цинка. В маркировку сложных латуней входят обозначения компонентов и их среднее процентное содержание. Например, латунь ЛАЖМц66-6-3-2, содержащая около 66% меди, 6% алюминия, 3% железа, 2% марганца, остальное – цинк.
Увеличение содержания цинка уменьшает стоимость латуни (цинк дешевле меди), повышает прочность и обрабатываемость резанием, но снижает пластичность и коррозионную стойкость. С ростом напряженного состояния увеличивается чувствительность латуней к коррозионному разрушению. Введение добавок целенаправленно улучшает отдельные свойства сложных латуней: обрабатываемость и антифрикционные свойства (свинец), прочность и коррозионную стойкость (марганец, олово и алюминий), литейные свойства (алюминий) и т.д. Считается, что латуни с повышенным содержанием меди имеют более красивый и благородный цвет.
6.2.2 Цинковые сплавы Цинковые сплавы, ГОСТ 21437-75, достаточно дешевые, обладают неплохими анти-
фрикционными свойствами. Сплавы маркируются буквой Ц и обозначением с процентным содержанием компонентов. Например, сплав ЦАМ10-5, содержащий 10% алюминия, 5% меди, остальное – цинк.
6.2.3 Баббиты Баббиты, ГОСТ 1320-74, – сплавы на основе олова и свинца, очень мягкие (НВ 15...30).
Они имеют низкие температуру плавления (300...400 оС) и коэффициент трения, хорошую износостойкость и прирабатываемость. Баббиты используют как антифрикционный материал, но в виде заливки на твердую основу, причем чем тоньше слой заливки, тем выше сопротивление усталости.
Баббиты маркируют буквой Б и числом, указывающим процентное содержание олова. При наличии дополнительных или заменяющих олово компонентов вместо числа приводится буквенное обозначение компонентов: Н – никель, Т – теллур, К – кальций, С – сурьма. Баббиты подразделяются на следующие виды:
•высокооловянистые (оловяносурьмяные), например, Б89. Обладают отличными антифрикционными свойствами, но и очень дорогие. Теплопроводность (0,03...0,042) Вт/(м 0С);
•низкооловянистые ( свинцовооловянистые), например, Б16, БН. Более дешевы, но и антифрикционные и технологические свойства ниже. Теплопроводность (0,012...0,024) Вт/(м 0С);
•безоловянистые (свинцовые), например, БК1. По своим свойствам аналогичны низкооловянистым.
6.2.4 Серебро
Из других цветных металлов отметим серебро. Оно обладает хорошими антифрикционными свойствами и высоким сопротивлением усталости в паре с деталями с высокой твердостью поверхности (HRC>50). Теплопроводность (0,36...0,42) Вт/(м 0С), модуль упругости Е=8,2 104 МПа, твердость НВ25...35 (в отожженом состоянии).
6.3Легкие сплавы цветных металлов
Клегким сплавам цветных металлов относят металлические материалы с удельной массой не более 5 г/см3. Это – прежде всего алюминиевые, магниевые и титановые материалы и сплавы на их основе.
6.3.1 Алюминиевые сплавы
Алюминиевые сплавы имеют плотность 2,6...2,9 г/см3, модуль упругости Е=(7...7,5) 104 МПа, твердость НВ 60...130, небольшую прочность, которая заметно падает с ростом температуры (предельная величина рабочей температуры составляет 200...250 оС). Технически чистый алюминий имеет высокую пластичность и коррозионную стойкость (бла-